Chemistry 86: Metals and Metallurgy (Xavier University PDF)
Document Details
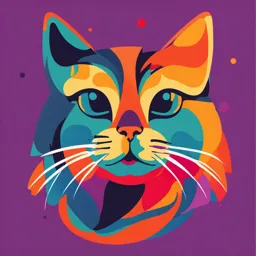
Uploaded by GloriousBamboo
Xavier University
Tags
Summary
These lecture notes cover the topic of Metals and Metallurgy in Chemistry 86. Chemistry for Engineers at Xavier University. The document explains the elemental abundance, compositional phases of the earth, different methods of isolating metals such as the Bayer process, and the extraction of different metals.
Full Transcript
Chemistry 86 Chemistry for Engineers Metals and Metallurgy 22-1 The Elements in Nature and Industry 22.1 How the Elements Occur in Nature 22.2 The Cycling of Elements Through the Environment 22.3 Metallurgy: Extracting a Metal from Its Ore 22.4 Tapping t...
Chemistry 86 Chemistry for Engineers Metals and Metallurgy 22-1 The Elements in Nature and Industry 22.1 How the Elements Occur in Nature 22.2 The Cycling of Elements Through the Environment 22.3 Metallurgy: Extracting a Metal from Its Ore 22.4 Tapping the Crust: Isolation and Uses of Selected Elements 22-2 Figure 22.1 The layered internal structure of Earth. The processes by which the Earth formed led to its differentiation into different layers. 22-3 Elemental Abundance The abundance of an element is the amount of that element in a particular region of the natural world. Elements are not equally abundant in all regions – abundances differ due to the differences in physical and chemical behavior of the elements. - The core of the Earth is rich in dense Group 8B(8) to 8B(10) metals. - The Earth’s crust has the largest share of nonmetals, metalloids, and light active metals. 22-4 Table 22.1 Cosmic and Terrestrial Abundances (Mass %) of Selected Elements. 22-5 Compositional Phases of the Earth As the Earth cooled to form its major layers, gravity and convection caused materials of different densities to separate, giving several phases. Fe was the major component of the core or iron phase. The outer silicate phase, containing oxygen combined with Si, Al, Mg, and some Fe, separated into the mantle and crust. The sulfide phase, with intermediate density, consisted mostly of iron sulfide mixed with parts of the other phases. 22-6 Figure 22.2 Geochemical differentiation of the elements. 22-7 Distribution of the Elements The distribution of the elements in the Earth’s layers was controlled by their chemical affinity for one of the three phases. Elements with low or high electronegativity (EN) tended to congregate in the silicate phase as ionic compounds. These included active metals and nonmetals. Metals with intermediate EN dissolved in the iron phase. Lower-melting transition metals, and many metals and metalloids in Groups 11 to 16, became concentrated in the sulfide phase. 22-8 Table 22.2 Abundances of Selected Elements in the Crust, Its Regions, and the Human Body as Representative of the Biosphere (Mass %) 22-9 Sources of the Elements O2, N2, and the noble gases (except He) are obtained from the atmosphere, where they occur as the free elements. A few elements occur naturally in their uncombined (native) state. These include S, carbon in coal, and unreactive metals. Most elements occur in ores, natural compounds or mixtures from which an element must be extracted. 22-10 Figure 22.4 Sources of the elements. 22-11 Metallurgy Metallurgy is the technology of metals, and is concerned with their extraction and utilization. Pyrometallurgy uses heat to obtain the metal. Electrometallurgy employs an electrochemical step. Hydrometallurgy relies on the metal’s aqueous solution chemistry Extraction of a pure element from its ore involves a series of steps, beginning with mining the ore. The mineral contains the element while the gangue is the portion of the ore with no commercial value. 22-12 Table 22.3 Common Mineral Sources of Some Elements Element Mineral, Formula Al Gibbsite (in bauxite), Al(OH)3 Ba Barite, BaSO4 Be Beryl, Be3Al2Si6O18 Ca Limestone, CaCO3 Fe Hematite, Fe2O3 Hg Cinnabar, HgS Na Halite, NaCl Pb Galena PbS Sn Cassiterite, SnO2 Zn Sphalerite, ZnS 22-13 Figure 22.9 Steps in metallurgy. Pretreating Converting Magnetic attraction (mineral to compound) Mining Cyclone separation Pyrometallurgy Flotation (roasting, etc.) Leaching Hydrometallurgy Refining Converting Electrorefining (compound to metal) Alloying Distillation Chemical redox Zone refining (smelting, etc.) Electrochemical redox 22-14 Pretreating Magnetic attraction Cyclone separation Flotation Leaching 22-15 Pretreating the Ore Magnetic attraction can be used to separate magnetic minerals from the gangue. Density separation exploits large differences in densities. Panning for gold relied on the density differences between gold and sand. Flotation uses an oil-detergent mixture to form a slurry, which is mixed rapidly with air to give an oily, mineral-rich froth that floats. Leaching involves the formation of a complex ion that is water soluble. 22-16 Magnetic separation In the separation of ores that have magnetic properties, the ore is ground and passed over a rotating drum. The drum has a magnet inside it which holds the magnetic ore particles as the waste falls outside the screen. The ore held on the drum can be released or scraped off. 22-17 22-18 Figure 22.10 The cyclone separator. Panning for gold also relies on density differences. The cyclone separator blows high-pressure air through the pulverized mixture to separate the particles. 22-19 Figure 22.11 The flotation process. The fine particles of ore are swirled around in large tanks with air blown in and flotation agents added. The particles attach to the bubbles and float to the surface where the froth is skimmed off. Flotation is a key step in copper recovery. Sulfide and non- 22-20 sulfide minerals as well as native metals are recovered by froth flotation. Leaching is a hydrometallurgical process that selectively extracts the metal, usually by forming a complex ion Leaching gold with a cyanide solution remains the most widely used hydrometallurgical process for the extraction of gold from ores and concentrates. Despite the difficulties and hazards of working with cyanide, no other process has yet been proven to be an economic viable alternative. Au + 8 NaCN + O2 + 2 H2O → 4 Na[Au(CN)2] + 4 NaOH 22-21 Converting (mineral to compound) Pyrometallurgy (roasting, etc.) Hydrometallurgy 22-22 Conversion of Minerals by Roasting Minerals are often converted to their oxides because oxides can be reduced easily. Δ CaCO3(s) CaO(s) + CO2(g) Metal sulfides are converted to oxides by roasting in air: Δ 2ZnS(s) + 3O2(g) 2ZnO(s) + 2SO2(g) Roasting is a process of strongly heating the ore to a high temperature in excess of air. Roasting is used for converting sulfide ores into oxides for the purification of metals. Volatile impurities along with moisture get removed. 22-23 Converting (compound to metal) Chemical redox (smelting, etc.) Electrochemical redox The next step converts the new mineral form (usually an oxide) to the free element by either chemical or electrochemical methods. 22-24 Conversion of Minerals by Chemical Redox Reduction with carbon is common. Heating an oxide with a reducing agent to obtain the metal is called smelting. ZnO(s) + C(s) → Zn(s) + CO(g) Oxides of less active metals are reduced with hydrogen instead of carbon. WO3(s) + H2(g) → W(s) + 3H2O(g) A more active metal may be used as the reducing agent. Cr2O3(s) + 2Al(s) → 2Cr(l) + Al2O3(s) H°