Spray Finishing and Touch-Ups Notes - Summer Semester 2024 PDF
Document Details
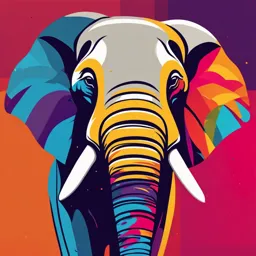
Uploaded by AttractiveJaguar
2024
Tags
Related
Summary
These notes cover the subject of spray finishing and touch-ups, focusing on the theoretical aspects of the summer semester 2024 program. The document details various topics such as equipment, viscosity, film thickness, and the different types of sprayable finishes.
Full Transcript
Spray Finishing and Touch-Ups SUMMER SEMESTER 2024 Overview Equipment, materials, and techniques for Spray Finishing Two Parts ○ Theory portion ○ Practical portion Theory Topics Air compressors Film thickness...
Spray Finishing and Touch-Ups SUMMER SEMESTER 2024 Overview Equipment, materials, and techniques for Spray Finishing Two Parts ○ Theory portion ○ Practical portion Theory Topics Air compressors Film thickness Spray booths Types of finishes Spray systems Lacquer finish defects Respirators Rubbing a finish Viscosity Shading stains and toners Viscosity Viscosity - a liquid’s body or thickness, a measure of its internal resistance to flow Varies with the type of liquid Varies with temperature of the liquid Any reference to a specific viscosity measurement must be accompanied by a corresponding temperature specification to be meaningful Measuring Viscosity Flow Rate – Most common measurement used to determine viscosity in finishing Viscosity cup used Time to empty the cup through a hole in the bottom of cup is an indication of viscosity 1 Viscosity Cups Different viscosity cups are available Different types ○ Ford ○ Fisher ○ Zahn Within a type, cups are numbers (#1, #2, …) based on dimensions #2 Zahn Cup and #4 Ford cup most common Viscosity conversion charts are available to convert a reading from one type of viscosity cup to that for another type of cup. Importance of Viscosity TE (Transfer Efficiency) Speed of application Quality of finish ○ Viscosity too high → Orange Peel ○ Viscosity too low → Runs, Gritty finish Always measure viscosity after each batch of material is mixed. Adjusting Viscosity To Decrease Viscosity Add the appropriate thinner / reducer as specified in the TDS Do not exceed the maximum dilution stated in the TDS or you may alter the chemistry of the product Consider selecting a larger size Fluid Tip / Fluid Needle / Air Cap rather than thinning the material too much To Increase viscosity Add some finish that has not been thinned Consider selecting a smaller Fluid Tip / Fluid Needle / Air Cap 2 Film Thickness Finishes can be divided into two groups: Penetrating ○ “Non-film-building” ○ Does not cure hard ○ Cannot be built up in layers to a measurable thickness Film ○ Finish Substance + Solvent – Applied as a liquid and dry/cure into a solid ○ Cures hard ○ Can be built up in layers to (almost) any thickness Wet Film Thickness (WFT) Thickness of a coating immediately after it is applied Includes solvent Measured using a WFTG (Wet Film Thickness Gauge) Dry Film Thickness (DFT) Thickness of an applied and dried/cured coating No solvent Measured using a DFTG (Dry Film Thickness Gauge) or manually ○ DFT (1 coat) = WFT (1 coat) x % Solid Content Measurements Measured in ‘mil’ or ‘thousandths of an inch’ 1 mil = 0.001” Recommended dry film thickness depends on product Sprayable Finishes 3 Definitions Solvent – a substance (usually a liquid) that dissolves a solute, resulting in a solution Drying – the process of a solvent being removed from a solution by evaporation, a physical change Reversible by adding solvent back to the dried material Evaporative finishes Curing – a chemical reaction, typically due to exposure to oxygen or a catalyst Cured processes are generally not reversible by adding the original solvent back to the dried material Reactive finishes Burn In – the property of a finish that allows a coat of finish to melt into and chemically bond to the last coat that was applied Results in a single thick layer of finish rather than multiple thin layers of finish mechanically bonded to each other Less chance of ghosting when rubbing out a finish Flash Off – when the liquid in a finish evaporates and the finish stops flowing Film finishes Finish substance + Solvent + Catalyst (sometimes) Coats the wood / sits on the surface Measurable thickness of finish Thicker coating → Better protection from scratches, water, and humidity exchange Practical limits to film thickness → Too thick may result in cracks as a result of expansion and contraction of wood Can be less ‘natural’ looking than penetrating finishes Chemistry: ○ Evaporative finish 4 ○ Reactive finish ○ Evaporative/Reactive ○ Coalescing finish Types of Sprayable Finishes Varnish Reactive finish → Cures A combination of oils, resins, and solvents Can be sprayed but not recommended Pros ○ Very good heat, wear, water, humidity, and chemical resistance ○ Brushes easily with long open time ○ Can be sprayed* Cons ○ Long open time → Slow drying resulting in dust problems and runs Sticky spray booth if sprayed* ○ Amber/Yellow tint initially becoming deeper over time ○ Difficult to rub out ○ Invisible repairs are difficult Shellac Evaporative finish Natural resin secreted by the lac beetle Can be sprayed but spray cup needs to be compatible Pros ○ Dries rapidly → Minimal dust problems ○ Good rubbing properties ○ Good repair qualities ○ Does not darken much with age ○ Excellent sealing properties Bonds well over oil, wax, and resins Blocks odors (ie. smoke, animal urine) 5 Excellent barrier to silicone Cons ○ Weak resistance to heat, water, and chemicals ○ Moderate resistance to wear ○ Short shelf life in liquid form Non-catalyzed Lacquer Evaporate finish Nitrocellulose with various resins added to reduce brittleness Replaced by catalyzed lacquer in many applications Typically sprayed Pros ○ Very fast drying ○ Excellent clarity and depth ○ Excellent rubbing properties ○ Excellent repair characteristics Cons ○ Fast drying can lead to ‘blush’ ○ High solvent content → solvent is toxic, flammable, and air polluting ○ Amber/Yellow tint initially becoming deeper over time ○ Only moderate heat, wear, water, and chemical resistance ○ Susceptible to surface contamination (fisheyes) CAB-Acrylic Lacquer Similar to Nitrocellulose Lacquer Evaporative finish Made of Cellulose Acetate Butyrate (CAB) combined with Acrylic 6 Commonly referred to as: ○ “CAB-Acrylic Lacquer” ○ “CAB” ○ “Acrylic” ○ “Water-white Lacquer” Refers to the colour, not the solvent Main Advantage: Non-Yellowing Cons: ○ Reduced water resistance ○ More expensive Conversion or Catalyzed Finishes Finishes composed of 2* parts Once mixed, a chemical reaction begins and the finish cures Curing time can vary from minutes/hours to even week/months Includes: ○ Catalyzed Lacquer Post-cat Pre-cat ○ Conversion varnish ○ Epoxy finish ○ Two-part polyurethane ○ Polyester finish Catalyzed Lacquer Post-Catalyzed Lacquer “Post-Cat” Acid catalyst added by user prior to application Reactive finish Nitrocellulose lacquer combined with a varnish Shelf life of many years Pot life: 6-24 hrs 7 Pre-Catalyzed Lacquer “Pre-Cat” Same as post-cat, but a weaker acid catalyst is added at the factory → Less hassle Reactive stage is very slow → Categorized as evaporative/reactive finish Can be redissolved with solvent prior to curing Less durable than post-cat Shelf/Pot life of 6-12 months Waterborne Lacquer Coalescing finish Solvent-based finish that is dispersed in water ○ Contains very little solvent compared to solvent-based finished → ‘Low VOC’ ○ Uses glycol ether as the solvent ○ Does not contain enough solvent to burn in their liquid state → negligible risk of explosion Water is typically used as the thinner ‘New and Improved” products being introduced constantly Less resistant to heat and chemicals compared to catalyzed lacquers Can be clear, tinted, or a solid color Some waterborne finishes provided with a separate ‘crosslinker’ or ‘hardener’ for increased durability that must be added by the user → ‘2K’ Spray booth requirements are far less stringent than for solvent based products Spray mask still required when spraying Film Finish Sheen Specular Reflection A type of surface reflection often described as “mirror-like” The incident light is reflected into a single outgoing direction The opposite of “Specular Reflection” is “Diffuse Reflection” ○ Smooth vs. Rough Sheen – the level of ‘shiny-ness’ 8 Descriptive terms ○ “Semi-gloss” ○ “Satin” ○ “Eggshell” ○ “Rubbed effect” ○ “Matte” ○ “Flat” ○ “Dead Flat” Numerical → Scale of 1-100 ○ Ex. Gloss: 90 → 90% of reflected light is specular To Control Sheen 1. Rub the last coat with abrasive compounds Produces very fine scratches in the surface Scratches scatter the reflected light 2. Use a finish that has a flattening agent included Silica particles Scatters reflected light Scattering light will reduce the transparency of a finish → Matt finishes are not as clear as gloss finishes. Lacquer Spraying Defects Quality Affecting Factors Surface Preparation (sanding grit, visible defects, etc.) Air pressure Pattern knob setting Fluid knob setting Selected air cap set Fluid viscosity Speed of application 9 Distance between gun and piece Air humidity Air temperature Air movement through spray booth Type of finish Orange Peel Finish is pebbly and resembles an orange peel Possible Causes Droplets are too large/thick → Finish does not flow out before dying ○ Viscosity is too high ○ Low air pressure Possible Solutions Add thinner/solvent to reduce viscosity Ensure sufficient air is available at the gun Change to a smaller air cap set Repair Sand smooth and respray Gritty Finish Once dry, the finish feels gritty/sandy. Material is drying in the air and landing on the piece. Small particles of dry finish sitting on the surface. Possible Causes Overspray is landing on piece Material is too thin and being over-atomized Gun is too far away from piece Possible Solutions 10 Orient piece in spray booth such that overspray is drawn across wet surface Thin product less Hold gun closer to piece Repair Cut back and respray If occurs in final coat → Rub with back of sandpaper to knock off dry particles of finish but not scratch finish Blush Milky white haze. Looks like a cloud floating in the finish. Possible Causes Moisture in air gets trapped in finish Fast drying finishes sprayed in humid conditions Water in airlines/spray equipment When air temp is close to dewpoint, cooling effect of expanding air and solvent evaporation can cause condensation as finish is sprayed Possible Solutions Add a retarder so that finish dries slower Wait for less humid conditions before spraying Spray, then turn off fan in spray booth to slow drying Heat air → Raise temp away from dewpoint ○ Run heater in makeup air unit Repair May disappear with time → Wait 24 hours Spray with retarder (or lacquer thinner) to re-dissolve finish allowing moisture to escape Spray another coat under better humidity conditions 11 Cut back and recoat Small Bubbles/Pin Holes Small bubbles develop over large pores in the wood. Possible Causes Finish dries before air trapped in large pores of wood can escape Possible Solutions Dust on several thin/dry coats before applying a wet coat Add a retarder to slow drying Pore fill wood before finishing Repair Difficult to repair Cut back finish and dust on a few thin/dry coats, then spray wet coat Strip and respray Fish Eyes Formation of small depressions in coating. Common when refinishing a piece. Possible Causes Surface contamination by silicone (possible from furniture polish) → Lacquer does not adhere to wood in some spots Possible Solutions Remove silicone from wood by washing with mineral spirits, TSP & water, or ammonia & water before finishing Seal in silicone with layer of shellac Seal in silicone by misting on two or three light coats of lacquer and then apply a wet coat 12 Lowering surface tension of finish with “Fish Eye Drops” → Can work but not recommended ○ Contains silicone and will contaminate gun Repair Sand smooth and respray Drips, Sags, and Runs Possible Causes Moving gun too slowly/stopping while holding trigger Spray gun too close to piece Not releasing trigger at end of stroke Aircap orientation incorrect for direction of gun movement Finish is too thin Repair Sand, chisel, or scrape off and respray Rubbing Out a Finish Common Flaws in a Film Finish Brush Marks Orange Peel Dust Nibs Roughness Uneven Sheen Wrong Sheen “Finishing The Finish” 2 Aspects 13 ○ 1. Level and smooth the finish ○ 2. Adjust the sheen Puts very fine scratches in the finish Finer scratches → Higher gloss Coarser scratches → Lower gloss Adjusting The Sheen Flattening agent in a finish can be used to determine sheen of a finish ○ Flattening paste must be evenly distributed for a uniform sheen ○ Can be difficult to perform “invisible” repairs A ruffed finish is usually easier to repair ○ To replicate the original sheen, simply use the same grit abrasive as the original finish Considerations for Rubbing a Finish 1. Type of Finish Hard, brittle finishes are easier to rub out that flexible finishes Easiest to rub out ○ Shellac ○ Lacquer Most difficult to rub out (to obtain an even sheen) ○ Varnish (including polyurethane) ○ Waterborne finishes 2. Thoroughness of Cure Finish must be fully cured Rubbing out to soon ○ Uneven scratch pattern → Splotchy or uneven sheen ○ Scratches may disappear as finish continues to cure When rubbing out a finish ○ Should produce a dry powder ○ Should not gum up or clog the abrasive → “Corning” 14 Many finishers rush this operation, rubbing out the finish within a few days of application, which compromises the results. 3. Choice of Abrasives Sandpaper ○ Used for cutting back / levelling ○ Eliminates irregularities Orange peel Brush marks Dust nibs ○ Using a sanding block will result in a more even surface ○ Liquid lubrication Without → Use stearated (dry lubricated) With → Use wet/dry sandpaper ○ Extra coats of finish may be required if you plan to cut back aggressively ○ Low spots will remain shiny Steel Wool (Real or Synthetic) ○ Used to put an even satin scratch pattern in the finish ○ Available as natural or synthetic ○ Finest natural steel wool is #0000 #0000 or #000 suitable for producing a satin finish ○ Use with a lubricant (ie. wool lube) ○ Synthetic Steel Wool Nylon fibers coated with abrasive powders Abrasiveness is due to the abrasive power glued to the fibers – Not to the fiber itself Abrasive power does wear off during use → Pad becomes less and less effective, similar to sandpaper Best for between coats of water-based finishes Rubbing Compounds ○ Very fine powders suspended in a paste or liquid ○ Can produce sheens higher than that produced by #0000 steel wool 15 ○ Types Pumice Finely ground lava Satin finish possible Rottenstone Finely ground limestone Gloss finish possible ○ Commercial preparations Various grits available ○ Mix with water or mineral oil ○ Worked with a pad Felt Burlap Wool 4. Lubricants Using lubricants… ○ Floats away grit and abraded material → Maintains the abrasive effectiveness ○ Holds down dust and steel wool particles ○ Reduces corning with sandpaper ○ Can reduce the size of scratches Choices ○ Mineral spirits or Naphtha ○ Liquid or paste wax ○ Oil ○ Water or soapy water ○ Commercial preparations 5. Rubbing Schedule Approach 1 ○ Level the surface with sandpaper before rubbing with steel wool or rubbing compounds to adjust sheen More time Higher quality finish 16 Risk of sand through or layering/ghosting increases Transition of coats may be visible with some finishes such as varnish and polyurethane Not usually an issue with finishes where layers burn into each other Approach 2 ○ Skip te leveling and begin with steel wool or rubbing compounds to adjust sheen Quicker Finish may still include imperfections 6. Cleaning Up Clean the surface well between each grit ○ Vacuum or blow off the dust ○ Wipe with tack cloth ○ Cloth dampened with mineral spirits ○ Wipe with the grain to avoid cross-grain scratches Clean off any sludge remaining from lubricants ○ Use naphtha/mineral spirits for sludge made with wax, oil, or mineral spirits ○ Use water for sludge made with water ○ Sludge remaining in scratches, pores, and recesses will dry opaque ○ May cause a haze of flat surfaces 7. Waxing and Polishing Often a good idea to apply paste wax to a rubbed surface to reduce wear Rubbed finishes show scratches more so than non-rubbed finishes ○ Ridges caused by rubbing are easily flattened Dark-colored paste wax can be used to advantage on dark woods Shading Stains, Toners, and Glazes Toning and Shading 17 Used to change the colour of a project after a finish has been applied A tinted finish is applied on top of the existing finish Both use the same materials – Difference is where it is applied on the project Toning Material applied everywhere Used to adjust/correct the colour of an entire project Shading Material only applied to specific parts of a project Used to adjust the colour of part of a project so it better matches the rest of the project ○ Sapwood/heartwood ○ Board with different natural colour Used to add colour for emphasis Shading Stains and Toners Availability ○ Premade ○ Mix your own Colorant + Solvent + Finish Use a lot of solvent and very little finish (lacquer) Finish simply acts as a binder so the colorant sticks to the finish already on the project Finish does not build film thickness Colourant options The selected colorant must be compatible with the top coat material ○ For Lacquer Solvent based pigment stain Universal-pigment colourant Oil-soluble dye 18 ○ For Water-Based Finishes Water-based pigment stain Universal-pigment colourant Water-soluble dye Shading and Toning Technique Always applied with a spray gun – Not wiped on ○ More even results ○ Better color transitions/blending when shading ○ Won’t disturb underlying clear coat Ensure the shading stain / toner is dilute ○ Less colourant is better than more colorant ○ Color change will be subtle and slow Many coats are used to slowly dark the color of the piece ○ Easy to spray another coat to make the project darker ○ Impossible to reverse the process without stripping DO NOT scuff sand the shading stain or toner – Must be top coated for protection Takes practice to achieve good results Repair of toned pieces can be very difficult Glazing Application and then manipulation of a colorant over a sealed surface Commercially available products → A very thick stain Glaze must be thick enough to stay where you put it Used to highlight/emphasize features ○ Gives depth to mouldings ○ Give a worn, dirty antique look ○ Can highlight pores Glazing Technique Sprayed on and rubbed off where it is not wanted ○ Use steel wool or ScotchBrite pads to remove 19 ○ Some alcohol-based glazes dry almost instantly – Excess can be removed with a rag soaked with alcohol Relatively forgiving → Reversible Glaze must be top coated for protection 20