Compass Health AI Supplier Evaluation and Monitoring SOP (PDF)
Document Details
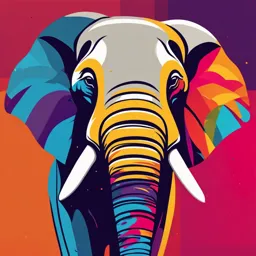
Uploaded by MajesticTroll
2024
Tenzin Yangzom, James Baskin
Tags
Summary
This document is a Standard Operating Procedure (SOP) for Compass Health AI, outlining the process for evaluating, selecting, and approving suppliers. The SOP covers supplier quality, product, and service requirements, and includes details on evaluating contractors and consultants. The document also describes the roles and responsibilities involved and the monitoring process.
Full Transcript
Compass Health AI SOP: Supplier Evaluation and Monitoring Approvals Author Position Role Signature Date DD-MMM-YYYY Tenzin Head of Author 02-Jan-2024 Yangzom QA/RA James Approver 02-Jan-2024 Baskin...
Compass Health AI SOP: Supplier Evaluation and Monitoring Approvals Author Position Role Signature Date DD-MMM-YYYY Tenzin Head of Author 02-Jan-2024 Yangzom QA/RA James Approver 02-Jan-2024 Baskin COO Document# QMS-SOP-0016 Revision History Version Date Description 1.0 03-Jan- Initial Release 2024 Document# QMS-SOP-0016 1 Introduction This document outlines the process and responsibilities for evaluation, selection, and approval of suppliers which can satisfy requirements for quality, product, and service. Compass HealthAI Inc. (“Compass”) evaluates its suppliers, and purchases only from those who can satisfy quality requirements. These supplier evaluations and maintenance audits are conducted by selected members of Top Management. Suppliers who meet requirements are entered on the Approved Supplier List by the Regulatory team. Quality Assurance - Regulatory Affairs (QA-RA) continually monitors supplier quality performance. Suppliers showing inadequate performance may be requested to implement corrective actions. If the corrective actions are not implemented and/or are not effective, the supplier is removed from the Approved Supplier List. Compass utilizes contractors and consultants in the product development process (e.g. contract engineering services, regulatory consultants). The skills and competence of these suppliers are evaluated by the hiring manager, and performance evaluation and monitoring are governed by the service contract between the consultant or contractor and Compass. These contractors and consultants are included on Compass’s organizational chart, and resource needs reviewed by Top Management during management review meetings. 1.1 Scope Supplier evaluation is performed for acquisition of any product or service that may affect quality of product delivered by Compass. Suppliers of products or services that do not affect quality are still listed, and identified as exempt from evaluation on the Approved Supplier List. Document# QMS-SOP-0016 2 Applicable and Reference Documents 2.1 Applicable Standards The following standards and regulations are intended to be met by this procedure: FDA QSR § 820.30 Design Controls ISO 13485:2016 Section 7.3. Design and Development ISO 13485:2016 Section 7.4. Purchasing TG(MD)R Sch1 P1 2, Sch3 P1 Cl1.4(5)(d)(ii) 2.2 Reference Documents Document Title Document # Supplier Evaluation and Re-evaluation Form QMS-FRM-0008 Approved Suppliers List CLR-REC-2000 SOP: Document Controls QMS-SOP-0002 SOP: Control of Records QMS-SOP-0003 SOP: Software Development Process QMS-SOP-0008 SOP: Risk Management QMS-SOP-0013 3 Acronyms and Definitions Table 1: Acronyms Document# QMS-SOP-0016 Acronym Description SOUP Software of Unknown Provenance QA-RA Quality Assurance Regulatory Affairs SOP Standard Operating Procedure QMS Quality Management System Table 2: Definitions Term Definition A person or company providing product or service. This may include Supplier persons unaware that they are providing product to Compass, such as creators of freely available software libraries. 4 Process Roles Role Description Originator The originator is the person desiring to select a supplier. Evaluates the originator’s determination and reviews QA-RA evidence of suitability, consulting with the originator, and any other Compass staff required in QA judgment, to perform an effective review. Document# QMS-SOP-0016 Adds suppliers to the Approved Suppliers List for supply of the specific products or services in question, once determined to be suitable Monitors the rates of non-conformance in delivered product or service from each supplier to determine if deficiency exists in the evidence provided for approval Approves the addition of the supplier to the Approved Management Suppliers List 5 Supplier Evaluation and Monitoring Process The objective of the Supplier Evaluation process is to select and effectively evaluate potential suppliers which may satisfy Compass’s requirements for specifications, quality, quantity, and standards. The Supplier Evaluation process proceeds at a high level according to Figure 1. Figure 1: Supplier Evaluation Process All suppliers of product or service to Compass shall be subject to this process. All suppliers shall be registered on the Approved Suppliers List (QMS-REC-0045). The process shall be separately completed for each product, or collection of products, and service to be procured from the supplier. A supplier is approved for specific products or services only. Any addition to the list of items to be provided shall be accompanied by re- evaluation in the context of the new items. 5.1 Initial Selection Personnel at Compass Health are responsible for selecting potential suppliers as need arises from design and development, management, and planning efforts. Document# QMS-SOP-0016 The personnel desiring to select a supplier (the Originator) shall initiate a Supplier Evaluation and Re-evaluation Form (QMS-FRM-0008). The Originator shall describe the product or service required from the supplier. The Originator shall make a declaration of freedom from conflict of interest on the Supplier Evaluation and Re-evaluation Form. The Originator shall make a determination, recorded on the form, whether the product or service in question may affect quality of products provided by Compass Health. If determination is made that quality of Compass’s products cannot be affected by the product or service being procured, QA-RA shall evaluate the Originator’s determination and, if in agreement, the supplier is added to the Approved Suppliers List for the product or service in question. Note: Suppliers include providers who may not be aware that they are providing product to Compass. For example, creators of freely available software libraries or SOUP. 5.2 Evaluation If the product or service to be procured is determined to affect quality of Compass’s products, a full supplier evaluation shall be performed. The Originator requesting approval of the supplier shall detail the product or service being procured, including description of how the product may affect Compass product quality. The Originator shall detail any evidence has been amassed in favour of approval, as well as any evidence in favour of denying approval. Compass uses a class system for products or services provided by suppliers, for which three different rankings of classes warrant different requirement of evidence to be provided for such product approval. The three classes and the associated requirements of evidence are as follows: Class I Supplier Suppliers of products and services that are deemed to have very low risk or no risk of affecting the quality of Compass’s product. Thus, there is no evidence required to approve this class of product/services and a Supplier Evaluation and Re-evaluation Form does not need to be completed for Class I products/services. However, the supplier of the Class I product/service is still required to be included in the Approved Suppliers List (QMS-REC- 0045) and identified as “EXEMPT” from evaluation. Document# QMS-SOP-0016 Class II Supplier Suppliers of products or services that are deemed to have medium risk of potentially affecting the quality of Compass’s product. With this class of products/services, more diligence is required and consequently, evidence is required to approve such products/services. Evidence for approval of Class II product/services could include: reference to detailed technical discussion with the supplier, showing good understanding of the specifications proven establishment and good reputability of the supplier responsive bid to a request for proposal any other information supporting selection Critical Supplier This class of products and services possess a high risk of affecting Compass’s product. A critical supplier is a supplier of a product or service, the failure of which to meet specified requirements could cause unreasonable risk to the patient, clinician or others, or could cause a significant degradation in performance of Compass’s products. Any supplier who provides products or services that are customized and for which requirements are specified by Compass prior to procurement are considered critical suppliers. Hence, the following evidence must be present for approval of such supplier: provision of screening sample product meeting requirements quality system certification: Supplier compliance with ISO 9001, ISO 13485, or other applicable QMS Standard as evidenced by third party audit results, OR certification of material or service by a third party to an accepted Standard, OR A supplier audit Any other information supporting selection Accreditation bodies For Accreditation Bodies, including testing laboratories, recognized by Regulatory bodies in jurisdictions in which Compass's product(s) are cleared to sell in (ex. FDA, HC), a Supplier Evaluation/Re-evaluation Form is not required to be completed. However, the Accreditation Body must be included in the Approved Suppliers List (CLR-REC-2000) and Document# QMS-SOP-0016 identified as “EXEMPT” from evaluation. In the Approved Supplier List, the Regulator recognizing the Accreditation Body and the respective scope of accreditation must be clearly stated. The services/certification requested must be within the current scope of accreditation of the Accreditation Body. 5.3 Approval QA-RA shall review evidence of suitability, consulting with the originator, and any other Compass staff required in QA-RA judgment, to perform an effective review. Review shall include evaluation of the impact on the Risk Management for the affected Compass product(s). Results of the review shall be recorded on the Supplier Evaluation and Re-evaluation Form which shall be entered as a record according to SOP: Control of Records (QMS-SOP-0012). If the supplier is determined to be suitable, QA-RA shall add the supplier to the Approved Suppliers List for supply of the specific products or services in question. Management shall review and approve the addition of the supplier to the Approved Suppliers List 5.4 Monitoring Suppliers shall be subject to periodic review of performance in the provision of the products or services in question. Methods for supplier monitoring may include but not limited to incoming inspection reports, verification/validation reports, non-conformance reports, supplier corrective action reports, delivery times, SLAs, and etc. Non-conformances are evaluated in the context of sampling plans and allowable defects, and, if determined to be unsuitable, the supplier is removed from the Approved Suppliers List for such products. Supplier may be asked to perform corrective action via a supplier corrective action report to rectify the deficiency. Successful performance of such corrective action shall be evaluated to determine if the supplier is to be removed from the list. Document# QMS-SOP-0016 5.5 Supplier Re-Evaluation Supplier re-evaluation requirements are indicated on the Approved Supplier List. Results from supplier monitoring are used as inputs into supplier re-evaluation. The review shall be documented on the Supplier Evaluation and Re-evaluation Form and the date of re-evaluation date is documented on the Approved Suppliers List. If suppliers are determined to be unsuitable, the supplier is removed from the Approved Suppliers List. 6 Process Monitoring QA-RA shall periodically, at least once per year, monitor the rates of non-conformance in delivered product or service from each supplier to determine if deficiency exists in the evidence provided for approval. Deficiency may be in the form of incorrect evidence, or insufficient evidence to indicate control over quality of product or service. Results of the periodic review shall be made available to management at each Management Quality Review. 7 Quality Records Record type Description List of suppliers who have met all the requirements and have Approved Supplier List been approved by selected members of top management. Supplier Evaluation Initiated by the personnel desiring to select a Class II or Critical and Re-evaluation supplier. Form Document# QMS-SOP-0016