Mineral Processing (PMY 121) Study Theme 8 PDF
Document Details
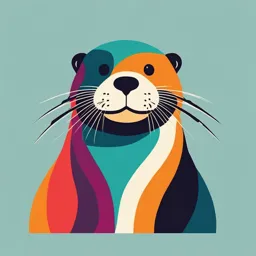
Uploaded by CostEffectiveChrysoprase8477
University of Pretoria
2024
University of Pretoria
Ms Jennifer van der Walt
Tags
Related
Summary
This document provides an outline of the various stages and processes involved in mineral processing, including comminution, crushing, grinding, and different types of separation techniques. It is part of a course on introduction to mining at the university of pretoria.
Full Transcript
07/10/2024 PMY 121: Introduction to Mining Study Theme 8: Introduction to Mineral Processing Ms Jennifer van der Walt Theme Outline 1 Mineral processing overview 2 Mineral processing flow sh...
07/10/2024 PMY 121: Introduction to Mining Study Theme 8: Introduction to Mineral Processing Ms Jennifer van der Walt Theme Outline 1 Mineral processing overview 2 Mineral processing flow sheet. 3 Comminution 4 Separation 5 Mineral processing summary 2 2 1 07/10/2024 Mineral processing overview ▪ Mineral processing involves processing of mineral resources to enhance its potential value for the benefits of end users. ▪ Mineral processing begins when an ore is delivered from a mine, to a processing facility as run-off-mine (ROM) (as already discussed in Theme1). ▪ Mineral processing is needed because run-off-mine ores are not consistent in their composition of constituents, they can be poor in grade, too coarse and unstable in size (Varies from fine sizes to big boulders ~1.5 m) ▪ Mineral processing are basically done using physical or mechanical processes and chemical effect. 3 3 Mineral processing overview ▪ Mineral processing consists of two unit operations: ❑ Comminution: Involves size reductions and liberation of valuable minerals from gangue minerals through crushing and grinding. https://www.youtube.com/watch?v=9p5WBDwu3x0 ❑ Separation/ Size screening: Is the process of separating the valuable mineral we want to concentrate from the worthless material known as gangue. ▪ Mineral processing can be performed with or without water as a medium. ❑ Mineral process performed with water is called wet process e.g. coal washing. ❑ Mineral process performed without water is called dry process e.g. cement rocks and aggregates for construction. 4 4 2 07/10/2024 Typical mineral processing flow sheet 5 5 Comminution ▪ Comminution is the process of reducing raw ore into a closer size range, and it is mostly done in two stages, namely crushing and grinding. ▪ In mineral processing, Comminution process is to done to achieve two major objectives: ❑ The objective of mineral liberation. Liberation is the major process to unlock (liberate) valuable minerals in the run off mine ore into more independent particles. ❑ The objective of size reduction. Crushing and grinding/ milling is done to reduce mineral particle sizes to an optimum size. 6 6 3 07/10/2024 This happens when particle size goes beyond 1.5 m. 7 7 Comminution - Crushing ▪ Crushing represents the first mechanical stage in the process of Comminution. ▪ Crushing is done to liberate valuable minerals from the gangue material and to provide optimum particle sizes required in the downstream separation and concentration processes. ▪ It is a dry process, and is mostly performed in three stages: ❑ Primary crushing ❑ Secondary crushing ❑ Tertiary crushing 8 8 4 07/10/2024 Comminution - Crushing ▪ Primary crusher – Jaw crusher ▪ Animation (https://www.911metallurgist.com/blog/jaw-crusher- animation) 9 9 Comminution - Crushing ▪ Primary crusher – Gyratory crusher ▪ https://www.youtube.com/watch?v=Kw_u3AVrudE&ab_channel=AP SRATHORE ▪ Animation 10 10 5 07/10/2024 Comminution - Crushing ▪ Secondary crushers – Cone crusher ▪ Animation (http://www.engineeringintro.com/all-about-construction- equipments/cone-crusher/) 11 11 Comminution - Crushing ▪ Secondary crusher – Impact crusher ▪ Animation (http://www.ami-crushers.com/stock-equipment/impact- crushers/) 12 12 6 07/10/2024 Comminution - Crushing ▪ Secondary crusher – roller crusher 13 13 Comminution – Grinding/Milling ▪ Grinding/milling is the last stage in the process of Comminution. ▪ Particles are reduced in sizes, through a combination of abrasion and impact. ▪ It is performed either as a dry or a wet process. ▪ There are two common milling setups: ❑ Autogenous mill (AG) ❑ Semi Autogenous mill (SAG) 14 14 7 07/10/2024 Comminution – Grinding/Milling ▪ Autogenous mill (AG) - Employs ore as a grinding medium 15 15 Comminution – Grinding/Milling ▪ Semi Autogenous mill (SAG) - Employs steel balls and aluminium rods as grinding medium 16 16 8 07/10/2024 Separation - Screening Screening: Is a mechanical separation of particles according to size. ▪ To enable undersized material to bypass the crushing or grinding circuit and to retain oversized particles for further size reduction, ▪ To provide an optimum particle size material for efficient processing in the downstream separation and concentration systems, and ▪ To prepare product that meets particle size specifications required for the market place. 17 17 Screening - Types There are three different types of screening mechanism, namely: ▪ Grizzly ▪ Revolving screens e.g. trommel ▪ Moving screens e.g. Vibrating screens and Gyratory screens 18 18 9 07/10/2024 Screening - Grizzly ▪ Grizzly - Rough screening of coarse materials 19 19 Screening - Revolving Screens ▪ Revolving Screen (Trommel) - Undersize material falls through the screening surface while the oversize is conveyed by the rotating motion down the incline to the discharge end. 20 20 10 07/10/2024 Screening - Moving Screens ▪ Vibrating screens ▪ Video (https://www.youtube.com/watch?v=k8N4VRuO6qw) 21 21 Screening - Moving Screens ▪ Gyratory screen ▪ Video (https://www.youtube.com/watch?v=NLazpvpUF4c) 22 22 11 07/10/2024 Separation - Physical separation ▪ Physical separation represents separation that is conducted on the basis of mineral properties. ▪ It does not affect the chemical nature of minerals, examples are as follows: ❑ Gravity separation processes e.g. spirals, shaking tables and jigs. ❑ Dense medium separation processes e.g. dense medium cyclones. ❑ Magnetic separation processes e.g. wet high intensity magnetic separators (WHIMS) ❑ Electrostatic separation processes e.g. high tension (HT) roll separators 23 23 Gravity separation - Spirals ▪ Spiral concentrators: Separates using combined effect of centrifugal force, differential settling and heavy particle migration. 24 24 12 07/10/2024 Gravity separation – Shaking Tables ▪ Shaking tables: is a mine selecting machine for fine materials working by gravity. ▪ Water is added to the top of the table, perpendicular to its motion. The heaviest and coarsest particles move to far end of the table while the lightest and finest particles tend to wash over the riffles and to the bottom edge. ▪ Video: https://www.youtube.com/watch?v=vZPuf- feiqc 25 25 Gravity separation - Jigging ▪ Jigging: The jigging action of the machine causes denser particles to preferentially trickle down faster and are removed from the bottom of the unit. ▪ Animation (https://www.youtube.com/watch?v=dauNWfbEBkM) 26 26 13 07/10/2024 Dense Medium Separation – DMS Cyclones ▪ DMS: Separation based on specific gravity of the valuable mineral relative to the gangue and the carrying medium such as water. Particles with a higher specific gravity can be separated from particles with a lower specific gravity. ▪ Animation (http://www.parnabymarketing.co.uk/water-only-cyclone-plant.html) 27 27 Magnetic Separation - WHIMS ▪ Magnetic separation: Separation based upon natural or induced differences in magnetic susceptibility of the minerals within the ore. ▪ Magnetic roller separates magnetic minerals from non-magnetic minerals. 28 28 14 07/10/2024 Electrostatic Separation – HT Separation ▪ High tension separation (HT): Separations made using a corona discharge device to sort solid pieces by means of utilizing forces acting on charged or polarized bodies in an electric field. ▪ Separation is effected by adjusting the electric and coacting forces, such as gravity or centrifugal force. 29 29 Other Separation systems ▪ Pyrometallurgy: represents high temperature processing e.g. Smelting, converting and roasting ▪ Hydrometallurgy: represents aqueous solution processing e.g. Leaching, digestion, solvent extraction and precipitation. ▪ Electrometallurgy: Process of recoverying or refining of metal using electrical power e.g. electro wining and electro refining. 30 30 15 07/10/2024 Mineral processing - Summary 31 31 Questions? #UPMiningMatters "Educating and leading mining engineers to become Imagineers" 16