Shop Practices PDF
Document Details
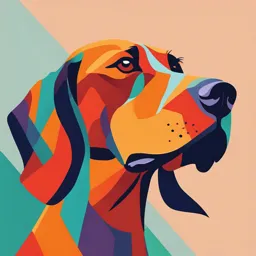
Uploaded by LowRiskBigBen2669
Gilbert M. Mendoza, ECE, ME
Tags
Summary
This document provides a detailed overview of shop practices, specifically focusing on technical drawings and measurement methods. The information covers important concepts such as linear measurement and various tools utilized in shops to complete tasks.
Full Transcript
PRINCIPLES OF LINEAR MEASUREMENT ❑ Scribers Scribers are marking tools that have sharp, needle- ❑ The US Customary, or Inch, System...
PRINCIPLES OF LINEAR MEASUREMENT ❑ Scribers Scribers are marking tools that have sharp, needle- ❑ The US Customary, or Inch, System like points made of hardened steel. The points are o The inch is divided into common fractions of ½”, like a pencil to scratch, or scribe, lines on metal. ¼”, 1/8”, 1/32”, and 1/64”. The bent end is used to scratch lines in places o These fractions of an inch may be measured where the straight end cannot reach. directly from steel rule. ❑ Dividers o Steel rules are also made with decimal fractions Dividers are two-legged steel instruments with of an inch such as 1/10” and 1/100”. hardened points. The greatest distance that can be ❑ SI Metric System opened between the two points measures the size. o The SI Metric system is a base ten, or decimal ❑ Trammels system. Its units of measurement are related to A large circle or an arc may be scribed with a tool each other by powers of ten Each of the main called a trammel. unit can be changed to a unit of more convenient It is sometimes called a beam compass or beam size, when desired, by multiplying or divided by trammel, and may also be used to measure distances powers of ten. in the same way that dividers are used. ❑ Outside Calipers LAYOUT WORKS An outside caliper is a two-legged steel instrument ❑ Layout work is the marking of lines, circles, and arcs on with its legs bent inward. metal surfaces. It is the transferring of information from Its size measured by the greatest distance it can a working drawing to metal surfaces to show the location be opened. and amount of metal to be cut away. It is used to measure the outside diameters of round ❑ The tools used for doing layout work are called layout objects and to measure widths and thicknesses of tools. materials. ❑ Layout tools are used by many skilled metalworkers: die- The distance between the legs is measured with a makers, diesinkers, gage makers, inspectors, layout rule. workers, machinists, metal patternmakers, sheet ❑ Inside Calipers metalworkers, structural steel workers, and tool makers. An inside caliper is a two-legged steel instrument with its legs bent outward. LAYOUT TOOLS It is used to measure the diameter of holes or to measure spaces. ❑ Surface Plate The distance between the two legs is measured on A surface plate is a large iron or granite plate with the rule. a very flat surface. ❑ Fine measurements with Calipers It provides an accurately flat surface on which to Fine measurements with calipers depend upon the place the workpiece. sense of touch, or feel, in the fingertips. Precision layout tools can be used to accurately ❑ Transferring a Measurement from One Caliper to Another mark the layout lines needed on the workpiece. To transfer a measurement from an inside caliper ❑ Steel Rules to an outside caliper, or vice versa, hold the caliper Steel rules are made in many lengths, widths, and which already has the measurement in one hand and thicknesses. the one to be set in the other hand. Adjust caliper The most commonly used steel rule is 6” long but to be set to the size of the one that already has lengths to 4’ are common. the correct measurement. A thin, springly rule called a flexible steel rule is ❑ Hermaphrodite Calipers used to measure curves. The hermaphrodite caliper has one pointed leg like ❑ Combination Set a divider and one bent leg. The combination set is the most commonly used set It is used to find the center on the end of a round of layout tools. bar, and to scribe lines parallel to the edge of a The set includes a square or combination head, workpiece. center head, bevel protractor, spirit level, steel ❑ Punches rule, and scriber. Prick punch is a sharply pointed tool of hardened The combination square is the most often used part steel. of the combination set. It is used to accurately define points to be center- Center head, because it forms a right or 90o angle, punched as well as to put small punch marks on is used to extend a line around a corner. layout lines so they will last longer. The bevel protractor is divided into degrees and Center punch looks like a prick punch. It is usually with rule fastened to it, any angle can be measured. larger than the prick punch and has a 90o point. A spirit level is usually fitted into the bevel The center punch is used to make prick punch marks protractor and the head of the combination square larger at the centers of the holes that are to be to help in leveling the work or setting it at an angle. drilled. ❑ Solid Steel Square ❑ Machinist’s Hammer This square has a fixed blade. The head of a machinist’s hammer has a ball-shaped It is more accurately square than the combination peen; thus, it is called a ball-peen hammer. square, which, if its sliding parts are worn, any become inaccurate. MACHINE DESIGN AND SHOP PRACTICES ENGR. GILBERT M. MENDOZA, ECE, ME 08/03/2024 ❑ Surface Gage ❑ Vernier Measuring Tools The surface gage has a heavy, flat carrying a Linear vernier measuring tools make measurements spindle that may be set at any angle. Clamped to accurately to one-thousandth of an inch. the spindle is a scriber, which may also be set at Vernier Caliper, like micrometer, is used for outside any angle or any height. The adjusting screw is used and inside measurements. It is made in standard for fine setting of the scriber. The height of the lengths of 6” [150 mm], 12”, 36”, and 48” [150, 300, point of the scriber may be measured with a rule. 600, 900, and 1200 mm]. Surface gage is used either to scribe or layout lines Vernier Height Gage, equipped with a straight or or to measure heights. The V-shaped grooves at offset scriber, is often used for precision layout one end and at the bottom make it useful on or work; and used with a dial indicator for inspecting against round work. completed work. Its standard sizes are: 12”, 18”, and ❑ Vernier height Gage 24” [300, 460, and 600 mm] Vernier height gage is used for the same kinds of Vernier Depth Gage, like the depth micrometer, is layout work as the surface gage. used for measuring hole and slot depths and the It is a precision layout tool that utilizes beam distance between parallel surfaces. graduations and a special movable scale called Vernier Gear Tooth Caliper is used for measuring vernier or vernier scale. the accuracy of gear teeth; it is also used to Vernier height gage can provide positioning of the measure some form cutters and threading tools. scriber to an accuracy of one-thousandth of an inch. Vernier Bevel protractor is a precision tool used ❑ Angle Plate for layout and measurement of precise angles. Angle plate has two surfaces at an accurate 90o, a right angle, to aeach other. It is often necessary to HANDSAWING clamp a workpiece to an angle plate to work with it. ❑ Parallel Clamp ❑ Hand Sawing Parallel clamp, also called toolmaker’s calmp, is Hand Hacksaw – is a basic tool in almost every often used to hold parts together or to hold the toolbox, and is used for cutting small pieces of work against an angle plate while laying it out. unhardened metals that cannot be cut in a more ❑ V-Blocks efficient way. Blocks of steel with V-shaped grooves are used to ❑ Parts of Hand hacksaw hold round work for laying-out. Parts of hand hacksaw are: frame, handle, prongs, V-blocks are usually made in matched pairs and come tightening screw and wing nut, and blade. with clamps to hold the work-piece in 90o V-grooves. ❑ Hacksaw Blades ❑ Micrometers Blades are made of thin high-grade steel that has Micrometers, called “mikes” for short, are been hardened and tempered. instruments that make very fine measurements. The Flexible blades are quality blades with hardened full name is micrometer caliper. teeth and a softer back that makes them springly Micrometers in English unit measure in thousandths and less likely to break. of an inch (1/1000”) or as fine as one thousandth of ❑ Sizes of Hacksaw an inch (1/10000”). Hacksaw blades are made in 8”, 10”, and 12” [200, Micrometers in SI system measure either to one 250, and 300 mm] lengths. hundredth of a millimeter (1/100 mm) or to two Blade length is the distance between the centers of thousandth of a millimeter (2/1000 mm). the holes at each end. ❑ Parts of a Micrometer Blades are usually ½” [12.7 mm] wide and 0.025” A micrometer has a frame, sleeve, thimble, spindle, [0.64 mm] thick. and anvil. ❑ Hacksaw Blade Material The opening between the anvil and the spindle is Blade materials include carbon steel, molybdenum made smaller or larger by turning the thimble. The alloy steel, tungsten alloy steel, and tungsten high- size os the opening is read on the sleeve and the speed steel. thimble. The lock nut locks the spindle so that it High-speed steels are the hardest materials used will not turn. for making hacksaw blades. ❑ Kinds of Micrometers ❑ Hacksaw blade pitch Inside Micrometer is used to measure the diameters 14 teeth per inch [1.8 mm pitch] – used for cutting of openings soft steel, aluminum, brass, bronze, copper alloys, Depth Micrometer is used to measure the depth of and other materials 1” [25 mm] or more in thickness. holes, grooves, and slots 18 teeth per inch [1.4 mm pitch] – used for cutting Screw Thread Micrometer is used to measure the machine steel, angle iron, drill rod, tool steel, pitch diameter of screw threads. aluminum, copper alloys, and other materials ¼” to Precise measurements with micrometers depend on 1” [6 to 25 mm] in thickness; also used for general- the user’s sense of touch or feel. purpose work. Sizes of Outside micrometer 24 teeth per inch [1 mm pitch] – used for cutting o 1” [25 mm] micrometer measures from 0” materials 1/16” to ¼” [1.6 to 6 mm] thickness, iron to 2” [0” – 25 mm] pipe, metal conduits, light angle iron, etc. o 2” [50 mm] micrometer measures from 32 teeth per inch [0.8 mm pitch] – used for cutting 1” to 2” [25 – 50 mm] materials up to 1/16” [1.6 mm] thickness, sheet metals, thin-wall tubing, and thin angles or channels. MACHINE DESIGN AND SHOP PRACTICES ENGR. GILBERT M. MENDOZA, ECE, ME 08/03/2024 ❑ Hacksaw blade Set COLD CHISELS Set of saw teeth refers to the way the teeth are ❑ Cold chisels are used to cut cold metal, hence the name; bent to one side or the other to provide a kerf (the and are made of tough alloy tool steel and are available cut made by the saw) that is wider than the in a number of sizes and shapes. thickness of the saw. ❑ Kinds of Clod Chisel The wider saw kerf prevents the saw blade from Flat chisel – one that has a wide cutting edge; used binding by providing clearance. for flat surfaces, cutting sheet metal, cutting bars Two kinds of Blade Set and rivets, and other cutting jobs; it is the most o Raker Set - is a set that has one tooth bent commonly used chisel. to the right, one to left, and one straight Cape Chisel – one that has a narrow cutting edge tooth in between; this pattern is repeated and is used for cutting narrow grooves; its cutting the length of the blade. It is used for 14 and edge is wider than the rest of the chisel to keep 18 teeth per inch blades. the chisel from sticking in the groove. o Waver Set – is a set that has several teeth Diamond-Point Chisel – one that has a cutting edge bent to the right and several teeth bent to shaped like a diamond and is used to cut V-shaped the left, alternately. It is used for 24 and grooves and square inside corners. 32 teeth per inch blades. Round-Nose Chisel – one that has a rounded cutting ❑ Putting Blade in Frame edge and is used for cutting round corners and When putting a new blade in the hand hacksaw, place grooves. it so that the teeth of the blade point away from ❑ Sizes of Cold Chisels the handle. Fasten one end of the blade to the hook Cold chisels range in size from ¼” [6.35 mm] to 1” at one end of the frame and the other end of the [25 mm] in diameter; lengths vary from 4” [100 mm] blade to the hook at the opposite end of the frame. to 8” [200 mm]. Tighten the blade securely; a loose blade makes a ❑ Angle of the Cold Chisel Cutting Edge crooked cut and is likely to bend or break. The cutting edge is a wedge that cuts into the metal. ❑ Holding Metal for Sawing The cutting edge angle on most cold chisels is from The work should be held tightly in the vise. Put the 50o to 75o. The angle on a specific chisel to be used part to be sawed near the vise jaws so that the depends upon the kind of metal to be cut. The softer pressure of cutting does not bend the work-piece the metal, the nearer the angle should be to 50o. or cause it to chatter. For cutting hard metal, the cutting angle should be Chattering is a rattling noise made when the work- greater, or more blunt. For most work, it should be piece or cutting tool vibrates, or springs back and about 60o. forth, during the work. It makes hacksawing very ❑ Head of Cold Chisel inefficient. The head of the cold chisel should be tapered a When possible, position the work-piece so that at little and rounded. least two saw teeth always contact the work-piece. After a cold chisel has been used for some time, This is necessary to avoid stripping (breaking) of the head becomes flattened like a mushroom with the saw teeth. rough, ragged edges; this mushroom head is Sawing thin metal. If the metal to be cut is thinner dangerous. One of the ragged edges may fly off and than the space between the two saw teeth, clamp injure someone when it is struck with the hammer. it between two thicker pieces of metal or hardwood. The mushroom head should be ground on the grinding Sawing through all three pieces at the same time is wheel. the safe way. If there is a layout in one side of the ❑ Holding the Chisel thin metal, use a C-clamp to fasten the metal so For small, fine work, hold the chisel with the fingers. that the layout can be seen. For larger chisels loosely around the middle, so that Making Long Saw cuts. Saw cuts in along work-piece the shock of the hammer blows is not transferred can be made by turning the blade at a right angle directly to the hand. to the saw frame ❑ Goggles Used in Chisel Work ❑ Holding and Using a Hand hacksaw When using chisel, wear goggles to protect eyes Grasp the handle with the dominant had (right hand from flying chips. is dominant if right-handed). Use the other hand to Make sure that the chips fly against a wall, or set grip the other end of the saw frame. up some kind of a shield to protect other workers. The Cutting Stroke. “Press down on the forward ❑ How to Start a Cut stroke and lift a little on the return stroke, because Position the chisel so that its point will bite into the blade cuts only on the forward stroke”. Tighten the metal. the blade after a few strokes because it will stretch when it gets warm. Make about 40 cutting Keep eyes on the cutting edge of the chisel so that strokes per minute. it can reset after each hammer blow if needed. ❑ Cutting Curved Lines Use light hammer blows until the chisel point has Cutting curved lines is done with a jeweler’s saw. dug into the metal then make the blows heavier to speed up the cutting. Jeweler’s saw blades have fine teeth and are very ❑ Shearing hard in order to cut metal. The blades are 5” [127 mm] long and with from 32 to 76 teeth per inch [0.08 A vise and a flat chisel, used together, can be made to 0.03 mm pitch] to act like a pair of scissors or shears for cutting o Unlike hacksaw blades, the teeth of the sheet metal. ❑ Cutting Rods and Rivets blades should point toward, not away from, the handle. Nicking it on opposite sides with the flat chisel, and o The cutting stroke is downward. then bending it until it breaks may roughly cut a small rod or bar. MACHINE DESIGN AND SHOP PRACTICES ENGR. GILBERT M. MENDOZA, ECE, ME 08/03/2024 FILES AND FILING Jewelry’s Files are small files used for fine work; ❑ Files are hardened pieces of tool steel with slanting rows and are made in lengths of 4” to 6” [100 to 150 mm] of teeth; and are used to cut, smooth, or fit metal parts. and sold in sets of various shapes. ❑ Parts of File Rifflers are files made, specially, for tool die, and Tang – is the pointed part of the file that fits into mold work; and are bent in various shapes to allow the handle. filing in hand-to-reach places. Point – is the end opposite the tang. Rotary files, or burrs, are made for use in electric or air-powered tools. Heel – is the end of the file next to the handle. ❑ Choosing the Right File Face – is the broad surface of the file that does Select the size, kind, and coarseness of file the cutting according to: Edge – is the narrow side of the file. If it has no ▪ Size of the work-piece teeth, it is called a safe edge. ▪ Amount of metal to be removed For safety all files with tangs should be fitted with ▪ Smoothness of the finish desired. handles. ❑ Holding Work for Filing Ordinary file handles are made of hardwood. The The work piece should be held tightly in a vise or metal ring on the file handle is called a ferrule. It otherwise fastened so it cannot move. keeps the handle from splitting when the tang is If in a vise, the part to be filed should be near the driven in. vise jaws to keep it from chattering. Large files should have large handles, and small file ❑ Using a File should have small handles. Very small file usually Do not use a file without a handle. are made with smooth, knurled (ridged) metal handle. Cross-filing. In cross-filing, the file is held naturally ❑ Shapes of Files. Files are made in hundreds of shapes. at about 45o angle to the work piece surface. Make Blunt file is one that has the same width and the file cut by moving it back and forth in a sawing thickness from the heel to the point. motion. Tapered file is one that is thinner or narrower at Draw-filing. Draw-filing produces a smooth flat the point. surface. (A mill file or a smooth single-cut file is The most commonly used shapes are as follows: recommended for this purpose.) Place the file at 90o warding, mill, flat, hand, pillar, square, round or rat- to the longest dimension of the surface to be filed. tail, half round, three-square, and knife. Grasp it firmly at both ends with the thumbs close ❑ Cuts of Files to the work piece. Keep the file at 90o while pushing Single-Cut File - is the one that has a single row it back and forth across the work piece. of cuts across the face of the file; the teeth are like the edge of a chisel. ❑ Checking the Accuracy of Surfaces During Filing Double-Cut File – is a cut that has two sets of cuts Filing flat surfaces should be tested often with the crossing each other, which give the teeth the form straight edge of steel rule or square. The work is of sharp points; these files cut faster but not as flat if no light can be seen between the smoothly as the single-cut file. straightedge and the surface. Rasp-Cut File – one with teeth that are not Test square corners often with a square. Use the connected and are formed by raising small parts of bevel protractor to test all other angles. the surface with a punch. This file is used in for ❑ Filing Cast Iron shaping wood and other soft materials. Before filing a cast iron surface that has not been Curved-Cut File – is one that is widely used into machined, remove the scale by tapping the work- bodywork; the widely spaced, curved teeth prevent piece surface with a large flat cold chisel. The file clogging when filing soft metals and plastic body will be ruined in few strokes if file the scale. fillers. Do not touch the filed part of cat iron with fingers ❑ Coarseness of Files or hand.. Single-cut and double-cut files are further Scale is a hardened layer, mostly iron oxide that classified by the coarseness or spacing between the always forms on iron castings. rows of teeth. ❑ Cleaning Files The six kinds of coarseness or spacing are as Keep the file free from chips and filings by brushing follows: rough, coarse, bastard, second-cut, it with wire brush called a file card. smooth, and dead smooth. Rough files are files with widest spacing between teeth. THREADS AND THREAD CUTTING Dead smooth files are files with closest spacing ❑ Screw thread is a ridge of uniform shape that winds at between teeth. a constant angle around the surface of a cylinder or a The files most often used are the bastard, second- cone. cut, and smooth. ❑ External threads – are threads on bolts and screws. The rough, coarse, and dead smooth files are used ❑ Internal threads - are thread on the inside of a hole. only on special jobs. ❑ Hands of Threads: ❑ Storing Files Right-hand thread – is the one in which the nut is Good care will save the cutting edges of the files screwed clockwise onto a bolt. and make them last longer. Left-hand thread – is the one in which the nut is Hanging files is a good is idea of storing files that screwed counterclockwise onto a bolt. prevents files from rubbing or hitting each other. ❑ Other Kinds of Files MACHINE DESIGN AND SHOP PRACTICES ENGR. GILBERT M. MENDOZA, ECE, ME 08/03/2024 ❑ Uses of Screw Threads on both the external and the internal threads for Used on fastener such as bolts, nuts, and screws. most applications. Used to change rotary (turning) motion to straight- Formulas for an external unifies Form: line motion. Pitch = p = ❑ Screw Thread Terms (Definitions adapted from ANSI) Number of threads per inch ANSI – American national Standard institute 0.61343 Major Diameter – the largest diameter of a straight Depth = D = 0.61343 x p = Number ofthreads per inch external thread. The nominal, or basic, size is similar p to the major diameter, and is used for general Flat at crest = F = identification, such as, identifying the thread size as 8 ¼” or ½” diameter. Common Tread Series in Unified Screw Treads: Minor diameter – the smallest diameter on a straight o Unified national Coarse Thread (UNC) – adopted external or internal thread. from the NC thread Pitch diameter – the diameter of an imaginary o Unified national Fine Thread (UNF) – adopted cylinder that passes through the thread profile from the NF thread where the width of the thread and width of the o Unified National Extra-Fine Thread (UN-EF) – groove are equal. adopted from the NEF thread Pitch – the distance from a point on one screw o Other less-common series, such as the 8-thread thread, measured parallel to the thread axis. The series (8UN), the 12-thread series (12UN), and pitch of a thread is a measure of the size of the the 16-thread series (16UN) thread. Six classes of Unified Tread Series o For inch base thread, pitch is equal to o Classes 1A, 2A, and 3A – external threads 1 divided by the number of threads per o Classes 1B, 2B, and 3b – internal threads inch. ❑ Other common thread forms o For metric threads, pitch is expressed Square Thread – is formed like square; the depth in millimeters. and width of the groove are equal; the height and o The pitch of a thread may be width of each ridge between the grooves are also determined with a steel rule or with a equal; the groove and ridge form two squares. screw pitch gage. Acme Thread – is usually used on the lead screw of Lead – the distance a thread moves along its axis a lathe; used on many other kinds of machine tools; in one revolution. On a single thread, the lead and angle of thread is 29o. pitch are equal or the same. On double-thread, the Pipe thread – used for assembling pipes and pipe lead is equal to twice the pitch. One triple thread, fittings. the lead is equal to three times the pitch. American National Standard Taper Pipe thread (NPT) Lead or helix angle – angle made by the helix of a – used for pipefitting jobs that require a low- thread at the pitch diameter measured in a plane pressure seal against liquid or gas leakage. The NPT perpendicular to the axis of the thread. threads are tapered ¾” per foot [62.48 mm per Multiple-thread – a thread having the same thread meter] on the diameter. The angle between the sides form produced with two or more helical grooves, of the thread is 60o. such as a double or triple thread. American National Standard Railing Joint Taper Pipe Crest – the top surface that joints the two sides (NPTR) – make a rigid, mechanical, tapered thread of a thread. joint for use in railing construction. Root – the bottom surface that joins the two sides American National standard Dryseal Taper Pipe of adjacent threads. Threads (NPTF) – are used in applications that Side or Flank – the surface that connects the crest require a gas or liquid tight thread joint without the with the root on either side of a thread. use of pipe compound or sealant. Four forms of Clearance – the distance between the crest of a Dryseal threads: thread and the root of a mating thread, measured o NPTF – dryseal standard pipe thread perpendicular to the thread axis. o PTF-SAE short – dryseal SAE short taper Height of thread – sometimes called single depth of pipe thread thread, - the distance between the major and minor o NPSF – dryseal standard fuel internal diameters of the thread, measured perpendicular to straight pipe thread theaxis of the thread. o NPSI – dryseal standard intermediate ❑ Development of Screw Threads in USA internal standard pipe thread Profile or form is the cross-sectional shape of a ❑ Types of American National Standard Straight Pipe screw thread. Threads (NPS): In 1924, the thread profile was named the American NPSC thread – used in pipe couplings National Form Thread and was much the same as the NPSM thread – designated for use in free-fitting United States Standard Form. mechanical joints. In 1911, the National Fine Thread was established. NPSL thread – is for use in loose-fitting mechanical ❑ Unified Screw Threads joints with locknuts. The Unified Screw Thread generally has rounded roots NPSH thread – is for loose-fitting mechanical joints and may have either rounded or flat crest. These are in hose couplings. the main difference from the American national Thread form. American industries use flat crest, while the English prefer rounded crests. The rounded root is optional MACHINE DESIGN AND SHOP PRACTICES ENGR. GILBERT M. MENDOZA, ECE, ME 08/03/2024 ❑ ISO Metric threads continue to cut the thread. Back up the die a In 1949, the International Standard Organization (ISO0 half-turn every two or three threads to break recommended worldwide adoption of three series of and clean away the chips. This help keep chips metric threads, that are based on the same 60- from clogging the die and roughing up the thread. degree thread form adopted for the ISO Inch (Unified) Threading to shoulder. A shoulder is a ridge of threads. The three series are the following: metal that extends from the base around the body o ISO Metric coarse pitch – commonly used on of the work piece. When full threads are needed fasteners as close to a shoulder as possible, first cut the o ISO Metric fine pitch – used mostly on threads in the usual manner as described above. precision tools and instruments o ISO metric constant pitch – used mainly on machine parts, but also used on all spark ❑ Cutting fluids for threading plugs. When threading steel, use sulfurized mineral oil ISO Metric and ISO Inch threads have the same thread or one of the commercial cutting fluids made form but not interchangeable because of differences especially for threading steel. in diameters and pitches. Special threading fluids are also available for Classes of ISO Metric threads aluminum. o the three classes are: fine, medium, and ❑ External thread measurements coarse. External threads must be cut to the correct depth to produce the proper fit or class of thread. If the pitch diameter is too large, the thread fits EXTERNAL THREADING WITH DIES too tightly. If it is too small, it fits too loosely. How to determine the fit or class of external ❑ Treading Dies screw: Treading Dies. Threading die is a tool for cutting o By testing how the threaded piece fits in a external threads on a round rod, such as those on a standard mating nut or threaded hole. bolt. o By measuring the pitch diameter either with Rethreading dies – are square or hexagonal in shape a thread micrometer or using the three-wire that can be turned with an ordinary wrench; used only method with a plain micrometer. for rethreading of damaged threads. o With a thread ring gage Left-hand dies – used to cut left-hand threads. o With a thread-roll snap gage. Screw plate – a set of threading tools that includes dies, taps, and the tools needed to use them. Diestock – a tool for holding and turning a threading die; and are made in several sizes to fit dies of INTERNAL THREADING WITH TAPS different diameters. ❑ Taps – is a tool for cutting internal threads. ❑ Sizes of Threading Dies It has threads like a bolt with two, three or four The diameter and pitch of the thread that is flutes (grooves) cut across the threads; the produced are stamped on each die, together with edges of the thread formed by the flute are the the kind of the thread. cutting edges; the shank end of the tap is square Example: ¼-20 UNC means that the die will cut a so that it can be turned with a wrench. Unified national Coarse thread with a major Taps are made from carbon steel or high-speed diameter of ¼” and 20 threads per inch steel and are hardened and tempered. A die marked M8 x 1.25 is a metric die that will A set of taps includes a taper tap, a plug tap, cut a thread with a major diameter of 8 mm and and a bottoming tap. a pitch of 1.25 mm. Taper tap has about six threads tapered at the ❑ How to cut a thread with a die and Diestock end so that it will start easily; the taper also Bevel the end of the end to threaded. (Bevel makes it easier to keep the tap straight ad the means to slant or taper the edge) this makes it cut is begun. The threads are cut gradually as easier for the die to start the thread. the tap is turned into the hole. Hold the rod tightly in a machinist’s vise so that Plug tap has three or four threads tapered at it cannot turn. the end and is used as a starting tap on easily Adjust the die to fit a standard bolt, that is, a cut metals. bolt with threads of the same size want to make. Bottoming tap has full threads to the end and is Mount the die in the diestock. Secure it with the used to cut full threads to the bottom of a hole. tightening screw. ❑ Tap Styles Place the tapered, or starting side, of the die on Hand taps – are straight-fluted, have three or the rod. four flutes, and have a cutting edge parallel to Hold the diestock with both hands near the die. the center line of the tap. Keep the die as square as possible with the rod. Gun taps – are straight-fluted, with two, three, Press down firmly and at the same time slowly or four flutes depending on the size of the tap. rotate the die clockwise. Larger die sizes require Cutting edges are ground at an angle to the more pressure to get the die started. After two centerline od the tap; the angular cutting edges or three threads have been cut, heavy pressure cause the chips to shoot ahead of the tap. Plug- on the die is no longer necessary. The die will type gun taps are designated for tapping open, continue to screw itself onto the rod as it or through, holes. Bottoming-type gun taps are rotated. designed for tapping blind holes (holes that go Shift the position of your hands to the ends of only part-way into work piece), producing fine the diestock, and add a little cutting fluid, and chips that can readily escape. MACHINE DESIGN AND SHOP PRACTICES ENGR. GILBERT M. MENDOZA, ECE, ME 08/03/2024 Helical-fluted taps, commonly known as spiral- Lubricate the tap with an appropriate cutting fluted taps – are designed to lift the chips out fluid. of the hole being tapped. o Tapping blind holes. A blind hole is one that o Low-angle spiral-fluted taps are best for goes only paart way into the workpiece. If tapping ductile materials like aluminum, full threads to the bottom of blind hole are copper, or die-cast metals. desired, run the plug tap in as far as it will o High-angle spiral-fluted taps work best on go. Clean out the hole now and then. In this tough metals, such as carbon and alloy way, the chips collecting in the bottom of steels; and are made with two, three, or the hole will not keep the tap from going to four flutes, depending on the tap diameter, the bottom. Then change to the bottoming and are available in plug and bottoming tap, and finish cutting the partially cut types. threads at the bottom of the hole. Serial taps – are usually made in sets of three; o Cutting fluids for tapping. Taps are very have one, two, or three identifying rings cut at hard and brittle and are easily broken. the end of the shank; and are designed for cutting Cutting fluids greatly reduce the strain on threads invery tough metals. the tap, and should be used when tapping Thread-forming taps have no cutting edges and most metals. therefore produce no chips; threads are formed ❑ Causes of Broken Taps by forcing the metal to flow around the threads A hole that has been drilled too small forces the tap on the tap; this produces a strong thread, to remove more metal than it is able to; therefore, because the grain of the metal is forced to follow it jams and breaks. the thread profile and the surface is somewhat A tap that is started at an angle to the hole sticks work-hardened. tight and then breaks. ❑ Sizes of Taps The tap wrench acts like a lever. With it, a great Taps are made the same sizes as bolts and twisting force can be put upon the tap. Misuse of screws; the major diameter, pitch, and kind of this force breaks many taps. Applying more pressure thread are stamped on the shank of the tap. to one side of the tap wrench than the other may Example: ¼ -20 UNC means that the outside also break the tap. diameter of the tap is ¼ inch, there are 20 Lack of cutting fluid where required will cause a tap threads per inch, and the thread is Unified to stick tight and break. National Coarse. Failure to back up the tap will cause the chips to Tap marked M6 x 1 is a metric tap with an outside crowd in front of the cutting edges or to pack tight diameter of 6 mm and a pitch of 1 mm. in the flutes of the tap. More force is then needed ❑ Tap size Limits to turn the tap, and this extra force is often more The size of the pitch diameter of a tap determines than the tap can stand. the depth and the fir of a tapped thread. Turning a tap after the bottom of hole is reached ❑ Internal thread measurement will cause it to break. Internal threads are checked for the correct fit ❑ Removing a Broken tap from a Hole or class of thread with thread plug gages. A broken tap is usually difficult to remove because ❑ Tap Drills the broken part is jammed tightly in the hole. Tap drill is the drill used to make the hole before A tap broken near the top of the hole may sometimes tapping. be removed by placing a dull Cape Chisel in the flute The tap drill should be a little larger than the of the tap and striking light blows with the hammer. diameter at the bottom, or root, of the thread, Apply penetrating oil first, then, work the broken known as the minor diameter. tap both clockwise and counterclockwise. ❑ How to cut internal threads with Tap A tap extractor is a tool designed to remove broken Drill the hole with the proper size tap drill. tap; it is made with slender steel fingers that fit Clamp the work piece in a vise with the hole in an into the flutes of the tap, so that a twisting force upright position. can be applied to remove the broken tap. Install a taper tap or a plug tap of the correct ❑ Thread Inserts size in a tap wrench. (the t-handle tap wrench is Thread Inserts are threaded steel bushings; used to used for holding small taps.) give new lining to holes with worn or damaged Insert the end of the tap in the hole, then grasp threads; also used to provide strong wear-resistant the tap wrench with both hands close to the tap. linings in low tensile strength metals, such as cast Press down firmly on the tap while turning it aluminum and magnesium. clockwise. Larger taps require mor pressure to get the tap started. It is very important that the tap be started FITS AND FITTINGS parallel with hole. If the hole is 90 degrees to ❑ In metalworking, fitting means preparing parts so they go the top of the work piece, a square or steel rule together correctly. can be used to check its alignment. A tap that is ❑ The term fit is used to describe how tight two mating started at an angle to the hole is forced to cut parts go together. The kind of fir that exists depends on a deeper and deeper thread on one side of the the tolerances and allowances that were called for in the hole as it gets deeper. This results in a broken design of the parts. tap. ❑ The sliding fir is a close fit between two parts with Once several threads have been cut, it is no enough clearance so that one can slide freely without longer necessary to press down on the top. wobbling. MACHINE DESIGN AND SHOP PRACTICES ENGR. GILBERT M. MENDOZA, ECE, ME 08/03/2024 ❑ Running fit is used where one part revolves inside on some larger screwdrivers are square; a wrench may another. A shaft running in a bearing, as in a drill press be used to turn such a screwdriver. spindle, must have a running fit. The fit must not be so An offset screwdriver has a bent handle; it is used tight that it keeps the shaft from turning, nor so loose where a straight screwdriver will not reach. that it wobbles from side-to-side. Phillips screwdriver is used for Phillip head screws. ❑ Location clearance fits (LC) are used in the assembly of ❑ Pliers are tools used for cutting small wire and for stationary parts where some clearance is permissible. Fits holding, twisting, turning, pulling, and pushing. may range from snug fits so medium amount clearance Slip-joint pliers, also known as combination pliers, are fits. used for gripping; can also cut small-size wire; the ❑ Location Interference fits (LN) are used where accuracy slip-joint makes it possible to grip large parts. of location and rigidity of mating parts are most Side-cutting pliers are especially useful for cutting important. These fits are used where a load from one wire and nails; used by electricians for cutting part must be transferred directly to another part without electric wires; the flat square jaws are useful for loss of motion. Force fits and shrink fits can satisfy this bending corners on thin metal. requirement. Round-nose pliers are used to bend small wire and ❑ Location transition fits (LT) are ranked between clearance thin metal, and to hold small parts. fits and interference fits; are used where accuracy of Long-nose pliers are used for handling small parts location is important and where a small amount of either where space is limited. clearance or interference is permissible between the ❑ Wrenches (Adjustable) mating parts. Adjustable-end Wrench is a strong tool used for ❑ Force fits are used where parts must be held together general work in the shop. Its jaws are pointed at very tightly. With these fits, parts can fastened together such an angle that it can be used in close corners almost as tightly as though they were made from one and unhandy places. piece.. Force fits are used to assemble gears, pulleys, Adjustable S-wrench is useful in many places where bearings, collars, and similar parts on shafts. a straight-handled wrench cannot be used. ❑ Shrink fits are classified under force fits, since they Monkey wrench is named after its inventor, Charles involve interference between mating parts. However, Moncky. It is used for tightening or loosening bolts where heavy driving or pressing forces are not practical and nuts, and can be set to fit many sizes. or possible, the parts are installed by shrinking one part Vise-grip wrench, also called Vise-grip pliers, is a onto the other. A pulley, gear, or collar may be fastened handy tool. It works in close places and the strong to a shft with a shrink fit. steel jaws lock to the work and will not slip; it acts ❑ Shims – are several layers of very thin metal often used like a vise, clamp, plier, pipe wrench, open-end to separate the two halves of plain bearing. wrench, or locking tool. Pipe wrench is used to hold or turn pipes or other round pieces of metal. SCRAPERS AND SCRAPING ❑ Wrenches (Non-adjustable) ❑ Scrapping is the process of shaving off small amounts of Box wrenches – have closed ends; the head of the metal using hand-held scraping tools. Scraping is most wrench goes completely around the nut or bolt head; often done to obtain precision alignment of machine parts; the handles are usually offset 15o, which provides it is also done to provide shallow pockets that will hold wrench (and user’s knuckles) clearances for nearby lubricants on flat surfaces, such as machine ways. obstacles. ❑ Machine surfaces usually are not perfectly true for a Socket wrenches are used to turn nuts and bolts number of reasons: that are in hard-to-reach places or below the File scratches or tool marks must be removed surface of the work. Set of Socket Wrenches: Metal may be unequal hardness or the metal may o Extension bars have been sprung out of true shape while being o Hinge handle, commonly called breaker bar – clamped for machining used for loosening difficult nuts and bolts The cutting tool may have worn or been sprung during o Reversible ratchet – used for normal the machining loosening and tightening ❑ Scrapers are made in several shapes and have cutting o Speed handle – used for rapid assembly or edges of hardened steel or tungsten carbide. disassembly of threaded parts Hook and flat scrapers are used for scrapping flat o Universal joint – used when the wrench surfaces handles cannot be positioned at right angles Half-round and three-cornered scrapers are used on to the nut or bolt centerline. curved surfaces. The three-cornered scraper is also Spanner wrenches – have hook or one or two pins useful for removing sharp edges, or burrs, from o Hook spanner wrenches are wrenches that around holes. fit into a slot o Pin spanner wrenches – are wrenches that fit into holes in threaded collars, and are ASSEMBLY TOOLS used to loosen or tighten them. Hexagonal wrenches are also called hex keys and ❑ Assembling means putting the parts of something Allen wrenches – are used with socket cap screws together. and socket set screw; are available in wide range of ❑ Screwdrivers are tools used to turn, or drive, screws; sizes, either singly or on set. made in may sizes and several shapes; the size is Torque wrenches are used when several bolts or nuts measured by the length of the blade, which is made of must all be tightened a uniform amount; also used to tool steel that is hardened and tempered. The screwdriver prevent over-tightening a single fastener. point for driving slotted screws should be correctly shaped; it must be fit the slot in the screw. The blades MACHINE DESIGN AND SHOP PRACTICES ENGR. GILBERT M. MENDOZA, ECE, ME 08/03/2024 Powered wrenches Set screws are made with square heads or are o Electric-and air-powered wrenches – enable headless. Both kinds are made with different points. workers to rapidly assemble and Setscrews are case-hardened are used to fasten disassemble parts with a minimum physical pulleys and collars on shaft. The headless setscrew effort; used for driving screws, tapping is made for safety. Screws with heads are dangerous threads, chipping, and riveting. on moving parts because the worker may be caught ❑ Punches and injured. There are two kinds of headless screws: Drift punch, sometimes called a tapered punch or screw with slot for a screwdriver, and the one with aligning punch, is smooth and has a tapered end; may hexagonal hole, known as a socket-head setscrew. be used to arrange holes in a straight line, to drive Wood screws are often used to fasten metal parts out pins, or to drive out rivets. to wood; made with flat, round, or oval heads. The Pin punch has a straight end and is used to drive heads are slotted or recessed so they can be turned out cotter pins and tapered pins. with screwdrivers. Wood screws are made of steel, Transfer punch is a pin punch with a point at its end brass, and aluminum. Steel wood screw come either like a center punch; used to transfer the location of bright or blued finish, or they are plated with the center of a hole on one part to another part. cadmium, nickel, or chromium to prevent rust or ❑ Arbor press – is a machine for pressing parts of corrosion. The diameter of wood screws and machine machinery together or forcing them apart, such as screws is measured on on the body under the head pressing a shaft in or out of a pulley or gear. with the American Standard Screw gage. ❑ Machinist’s Vise – is often used to clamp parts together Lag screws have either square or hexagonal heads while they arte being assembled. like bolts and are threaded like wood screws; used ❑ Clamps – are often used to temporarily hold parts for heavy work such as fastening a machine to a together while being assembled. wooden floor. C-clamps are shaped like the letter C; made in many Thumbscrews are screws with one or two wings or sizes and very useful general purpose clamps. with a knurled head; used where a screw must be Toolmaker’s parallel clamp have two parallel jaws, turned by the thumb and finger. which are opened or closed by two screws; are made ❑ Nuts in several sizes and are best suited for holding small Machine screw nut is either square or hexagonal; the parts together. thread may be either coarse or fine. Stove, carriage, Toggle clamps are made in may sizes and types are and machine bolts are generally supplied with square widely used in special work holding fixtures. nuts. Spring clamps are useful where only light holding Jam nut is sometimes called a lock nut or check nut; power is needed; can only be quickly applied and thinner than an ordinary nut and is used as a lock released because of their spring action. to keep another nut from loosening by vibration. Although the jam nut is usually put on last, the thicker nut may be put on last to make use of the FASTENERS greater strength. Castle nut has slots cut into a top ring on metal. ❑ Fasteners are elements used to hold together metal parts The part that extend upward make it look like a in a form of bolts, screws, pins, and rivets. castle, hence the name. A cotter pin is slipped in a ❑ Bolts and screws – are made in many shapes and sizes. slot and through a hole in the bolt to lock the nut Carriage bolt – has a smooth, round head; a back, to the bolt and thus keep the nut from jarring off. round finish; and a coarse thread. It is usually used Castle nuts are usually used to hold wheel bearings to fasten a wooden part to metal. The square part and wheels in place. under the head sinks into the wood and keeps the Wing nuts have two thin, flat wings and are used bolt from turning while the nut is being tightened. where a nut has to turned with the thumb and Tap bolts are like machine bolts except that the forefinger. whole body is threaded. Self-locking nuts eliminate the need for lock Stove bolts are have either a round or flat head, washers, lock nuts, or cotter pins to keep the nut which is slotted so that the bolt can turned with a tightly in place. The self-locking feature is usually screwdriver; made with a coarse thread; used as provided either by one or more deformed threads, or general purpose fasteners where precision fits are with a plastic insert. unnecessary. ❑ Washers Cap screws are made with heads of several different Plain washers are used as bearing surfaces for bolts, shapes; usually finished all over and are made with nuts, screws, and rivets; protect the surface under either coarse or fine threads; used when it is not the fastener and spread the load over a greater convenient to get at both sides of the work with area. The size of the a washer is measured by the wrenches. The head of the cap screw presses against diameter of the bolt that it fits. the top piece and holds the part together. Lock washers are used to lock a nut or screw in Machine screws are made with heads of several place, thus preventing movement or loosening due to different shapes and are made with either coarse or vibration. The helical spring type lock washer looks fine threads; made of steel, stainless steel, or brass. like a coil from spring.; they are hardened and The smaller diameters are described by gage tempered, and are used under a screw or nut. numbers, 0 – 12. These sizes range from 0.060” to Tooth-type lock washers of hardened steel will 0.216”. the gage numbers are the same for both wedge into bearing surfaces to prevent bolts, nuts, machine screws and wood screws. Larger diameters or screw from turning or loosening due to vibration. are usually designated by their sizes: ¼”, 5/8”, and 3/8”. MACHINE DESIGN AND SHOP PRACTICES ENGR. GILBERT M. MENDOZA, ECE, ME 08/03/2024 Preassembled screw and washer assemblies called Blind rivets are rivets so named because they can be sems have a lock washer fitting loosely below the inserted and set from the same side of the work screw head. The expanded rolled thread diameter piece. prevents the washer from falling off; used for more rapid assembly on modern assembly lines. ❑ Pins are used to hold mechanical parts together or limit SOLDERING AND BRAZING the travel of moving parts. ❑ Soldering is a process of fastening metals together. Cotter pins, also called cotter keys, are made of soft Solder, a nonferrous metal, has a melting point lower steel wire; slipped through a hole in a bolt behind a than the metals to be joined. Soldering and brazing are castle nut; to keep the nut from turning. The heat different from welding. In welding, the pieces being joined of the cotter pin should fit into the slot of the nut; are melted and fused together. Soldering is commonly one leg should be bent over the end of the bolt and used by electronics technicians to older wire joints for the other leg should be bent over the side of the electric circuits. nut. Soft soldering is soldering with an alloy of lead and Tapered pin is often used for such purposes as tin. fastening a pulley or collar to shaft. The taper equal Soldering copper is a bar of copper, usually octagonal ½” per foot; made in lengths from 3/8” to 6”. The in cross-section. hole into which the pin fits is first drilled and then reamed with a taper-pin reamer, which has the same taper as the pin. WELDING Roll pins are pins made of sheet steel rolled into a ❑ A weld occurs when metal from pieces being joined flows tube; hardened and spring-tempered; slightly larger and blends together; this action may be caused by heat, than standard hole sizes so that they hold very pressure, or a combination of both. tightly when driven into the hole. ❑ Fusion weld when heat alone is used. ❑ Keys are used to keep pulleys and gears from moving on ❑ Pressure welding usually involves heating surfaces to a shafts. Half of the key fits into a keyway, which is a slot pliable, or plastic, state and then forcing the metal in the shaft, and the other half fits into a slot in the together with pressure. shaft, and the other half fits into a slot in the pulley or ❑ Welding Processes gear. Brazing is the joining of metals by melting a Square key is the one that is most used. nonferrous filler rod at a temperature above 800 F, Gib-head key is useful where it is necessary to but below the melting point of the metals being remove the key from one side of the pulley or gear. joined. A wedge may be used to back the key out of the Forge welding is pressure welding by heating and hole. hammering pieces together. Woodruff key is semicircular in shape and fits a Oxyacetylene welding is the most common form of matching semicircular pocket in the shaft. The key is gas welding; this welding uses oaxygen and acetylene thus trapped in position and cannot work its way gases to provide heat for welding and cutting. loose due to vibration. Shielded metal arc welding is a common form of arc ❑ Retaining Rings – are a relatively new type of fasthern; welding; the weld is shield by flux-coated welding seated in either internal grooves or in external grooves rods; the shielding prevents oxidation and produces with a special plier-like tool. Theself-locking types are a stronger weld. Welding heat is provided by an driven into place and do not require a groove. Retaining electric arc. rings provides a shoulder for holding, locking, or Resistance welding uses the heat generated by positioning parts of assemblies. electric current passing through a small area of the ❑ Self-threading screws used to cut or form their own metals being joined. Pressure forces the heated threads in soft steel, aluminum, and other soft metals; areas together until they have fused. Spot welding used for economical assembly of sheet metal and other is a common form of resistance welding. sheet materials such as plastic, plywood, asbestos, and Thermit welding processes use the intense heat of a fiber materials. chemical reaction to fuse metals. Drive screws are made of hardened steel and have a Induction welding uses high-frequency current as the smooth round head, multiple threads, and a pilot-type source of heat. nose; these are driven into holes with a hammer. Inert gas is used in several processes to keep the ❑ Rivets and riveting weld free of scale, oxidation, or other impurities. Rivets are metal pins that look like bolts without threads; made of different metals such as soft iron OXYACETYLENE WELDING or steel, aluminum, copper, and brass; available in ❑ An oxyacetylene weld is a fusion weld. The heat is many different sizes and shapes of heads. produce by burning acetylene gas with oxygen gas, giving Riveting is the fastening of pieces of metal or other a temperature of about 6000 oF. material together with rivets. This process is used to hold pieces together permanently. Oxyacetylene Welding Equipment Tinner’s rivets are solid rivets used for riveting ❑ Oxyacetylene welding equipment. Oxyacetylene welding sheet metal; made of soft steel, either plain or requires the following special equipment: coated with tin. Cylinder of oxygen Rivet spacing. As a general rule, rivets should not Cylinder of acetylene be spaced closer together than three times the Special valves called regulators for the cylinders diameter of the rivet. MACHINE DESIGN AND SHOP PRACTICES ENGR. GILBERT M. MENDOZA, ECE, ME 08/03/2024 Hoses to carry the gases from the cylinders to the ❑ Wear protective clothing when using oxyacetylene torch equipment, it should include the following: Welding torch, sometimes called a blowpipe, and A cloth or leather cap various sizes of torch tips Welding goggles Lighter that can make a spark to ignite the mixture Coveralls of treated cotton or full-length apron. of gases Trousers without cuffs and a shirt with full-length A pair of tongs or pliers to handle pieces of hot sleeves metal Leather shoes ❑ Oxygen cylinders are usually taller and smaller in Gloves with cuffs that overall the sleeves diameter than acetylene cylinders, for the reason that a long, slender cylinder can better withstand high pressure. Starting-up Procedure for Oxyacetylene Welding When the tank is full, oxygen tank pressures reach 2200 ❑ Starting-up procedure for Oxyacetylene Welding psi (15.2 Mpa). The oxygen cylinder tank valve must be 1. Install the correct torch tip opened all the way when in use, and closed all the way 2. Check to see that the regulator keys are held when not in use. Because of the potentially explosive in place by only two or three threads. This will pressure of an oxygen cylinder, it is usually kept chained prevent the high-pressure gas from damaging to a cart. A ruptured oxygen cylinder can smash through the low-pressure gage when the tank valves are a concrete wall. opened. ❑ Acetylene cylinders are usually shorter and larger in 3. Open the oxygen tank valve all the way diameter than oxygen cylinders; low-pressure cylinders 4. Open the acetylene tank valve about ½ turn. that contain only about 250 psi(1.7 Mpa) when full. The Leave the wrench on the valve stem to allow tank valve should only be opened about ½ a turn so that quick shut-off of fuel if necessary. the fuel supply of gas be shut off quickly in an 5. Open the oxygen torch valve about ½ turn. Then emergency. screw in the oxygen regulator key until the ❑ The gas pressure regulator is a device on each cylinder desired pressure is obtained. Close the oxygen that delivers a constant supply of gas at a reduced torch valve. pressure to the welding torch. Regulator is necessary 6. Open the acetylene torch valve about ½ turn. because the welder works with only 1 to 10 psi of each Them screw in the acetylene regulator key until gas. The regulator attaches to the tank valve. Two the desired pressure is obtained. Close the pressure gages are attached to the regulator. The high- acetylene torch valve. The oxyacetylene torch pressure gage, which is nearest the tank valve, shows is ready for lighting. the tank pressure when the tank valve is open. Gas is released from the regulator key clockwise. The amount Lighting the Torch of pressure being released through the regulator is ❑ Lighting the Torch shown on the low-pressure gage, which is farther from Before lighting the torch, be sure the proper clothing the tank valve. WARNING: acetylene gas is unstable when is being worn. This includes goggles with colored compressed against itself above 15 psi, so never set the lenses. acetylene pressure regulator for more than 15 psi. A torch lighter, also called a spark lighter or friction ❑ Hoses used in welding are always color-coded. Red hoses lighter, is used to make a spark that will ignite the are always used to connect the torch to the acetylene acetylene gas. pressure regulator. Their fittings have left-hand threads Open the acetylene torch valve about a half turn. so that they cannot be connected to the oxygen Point the tip of the torch away from your body and regulator. Green hoses are always used to connect the away from the gas cylinders. Ignite the acetylene gas torch to the oxygen pressure regulator; their fittings with the torch lighter. Do not use matches or a have right-hand threads. cigarette lighter to light the torch. The acetylene will ❑ Welding torch mixes the gases from the oxygen and burn a dark orange color and may give off black soot. acetylene cylinders. It controls the flow of each gas to The acetylene valve is adjusted properly when the produce the size and type of flame needed. With the flame almost separates from the torch tip. welding torch, the welder can direct a maximum amount of Open the oxygen torch valves. Adjust each valve to heat to a small spot or area. obtain the desired size and kind of flame. ❑ The torch tips used in welding come in different sizes that can easily fit onto the welding torch. Each tip Adjusting the Flame provides the size and kind of flame needed to weld a ❑ Once the torch is lighted, the oxyacetylene flame can be certain thickness of metal. Sometimes the hole in the adjusted to: torch tip (called orifice) becomes partly clogged with a 1. A neutral flame – the proper mixture of oxygen small piece of carbon, dust, or dirt. The gases passing and acetylene for m ost welds through the tip make a hissing sound different from the 2. A carburizing flame – a low-temperature flame normal sound, and the flame may have an odd shape. When for torch brazing. This flame has too much this happens, it is important to use a special tip cleaner acetylene (or too little oxygen) for welding. to clean the tip. Do not try to use a piece of wire, wood, 3. An oxidizing flame – this flame has an excess of or a wire brush to open the hole, because the tip may be oxygen (or insufficient acetylene). It will not damaged. Clean the tip by inserting a tip cleaner of proper make a strong weld. It is always harmful. size in the hole in the torch tip. Shutting-down Procedure for Oxyacetylene Welding ❑ Shutting-down procedure for oxyacetylene welding 1. To put out the torch flame, close the acetylene torch valve. This sometimes results in a loud popping sound, which is normal. Protective Clothing for Oxyacetylene welding 2. Close the oxygen torch valve 3. Close the acetylene tank valve MACHINE DESIGN AND SHOP PRACTICES ENGR. GILBERT M. MENDOZA, ECE, ME 08/03/2024 4. Close the oxygen tank valve 5. Drain the acetylene line by opening the acetylene torch valve. When the acetylene gas pressure gages have both dropped to zero, close the acetylene torch valve. 6. Drain the oxygen line by opening torch valve. When the oxygen gas pressure gages have both dropped to zero, close the oxygen torch valve. 7. Unscrew the oxyge