SCBA Context Manual PDF
Document Details
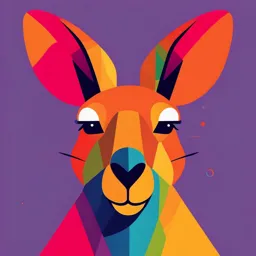
Uploaded by StatelyCliché
St. John's Fire District
2024
Tags
Related
- 202.021 On-Scene Cleaning Procedures for Personnel and PPE PDF
- St. John’s Fire District SCBA Context Manual PDF
- Bernalillo County Fire & Rescue Vehicle Fires Standard Operating Guidelines PDF
- Bernalillo County Fire & Rescue Air Management PDF
- Firefighter PPE and SCBA PDF
- Los Angeles City Fire Department Training Bulletin No. 195 PDF
Summary
This manual provides an overview of the MSA G1 self-contained breathing apparatus (SCBA), including its components, safety regulations, and operational procedures.
Full Transcript
Self-Contained Breathing Apparatus Context Manual VERSION 1 UPDATED June 1, 2024 Table of Contents Introduction 3 Reference Procedures...
Self-Contained Breathing Apparatus Context Manual VERSION 1 UPDATED June 1, 2024 Table of Contents Introduction 3 Reference Procedures 4 MSA G1 4 Safety Regulations 4 Components 4 Facepiece 4 Regulator (also referred to as Demand Valve) 5 G1 Heads-Up Display (HUD) 5 G1 Pressure Reducer 6 G1 Power Module 6 G1 Control Module 6 PASS Device 7 G1 Speaker Module 7 Cylinder Valve Assembly 8 Primary Low Pressure Warning Device (Bell) 8 G1 Carrier and Harness Assembly 8 Cylinder 9 Rapid Intervention Team/Universal Air Connection (RIT/UAC) 9 Donning 10 Start-up Sequence 11 Primary Screen 11 HUD Pressure Status 12 SCBA Unit Identifier 13 Operational Check 14 Primary Screen 19 SCBA Unit Identifier 19 Cleaning Disinfection 19 SCBA Identification 21 2 Introduction Respiratory Protection is vital to the health and safety of re ghters. The inherent hazards associated with re ghting and all-hazards mitigation requires the use of Self-contained Breathing Apparatus (SCBA). The human respiratory system is a sensitive and delicate group of organs The lungs and respiratory tract are probably more vulnerable to injury than any other part of the body. Standard Operating Procedures at all incidents include not entering any structure or atmosphere that is charged with smoke or re gases, or any other suspected respiratory hazard, unless one is equipped with an SCBA. The most appropriate approach to take at all incidents is to assume that any smoke and gases that are present are hazardous to all humans, including victims, bystanders and re ghters. An atmosphere should be considered hazardous when any one of the following is present: High heat Smoke Toxic gases Oxygen de ciency Suspected hazardous material release Moreover, modern buildings are constructed with materials, which release toxic chemicals as they burn. Failure to use an SCBA in hazardous atmospheres greatly increases the chance that re ghters will be unnecessarily exposed to inhaled poisons and deadly levels of carbon monoxide and other toxic gases. Additionally, proper use of an SCBA will protect the user from inhaling dangerously high levels of heat associated with re ghting, which have the potential to damage the lungs and respiratory tract. If there is any doubt whether an SCBA is required, re ghters should always err on the side of safety. All St. John’s Fire District re ghters shall receive training and be pro cient in the proper use of the MSA G1 SCBA. Fire ghters must be able to demonstrate pro ciency in all aspects of SCBA use, including donning and dof ng, performing a face piece Fit Check, Pak-Alert sensor module operation, emergency operations, maintenance and testing procedures and proper cleaning procedures. Additionally, re ghters should be able to demonstrate a thorough knowledge of the unit’s speci cations. 3 fi fi fi fi fi fi fi fi fi fi fi fi fi fi fi fi fi fi fi fi fi fi fi Reference Procedures Respiratory Protection Air Management Standard Operating Guideline 203.09 Safe Structural Firefighting MSA G1 The MSA G1 - referred to hereafter as SCBA - is a pressure-demand self-contained breathing apparatus (SCBA) operating independent of the ambient air for use in atmospheres immediately dangerous to life or health. Breathable air is supplied to the user from a compressed air cylinder via a pressure reducer, a regulator and a facepiece. The exhalation air is released directly into the ambient atmosphere. Safety Regulations The MSA G1 SCBA complies with the National Institute for Occupational Safety and Healthy (NIOSH) regulation under 42 CFR Part 84 for open circuit self- contained breathing apparatus, the National Fire Protection Association (NFPA) Standard 1981 on Open-Circuit Self-Contained Breathing Apparatus (SCBA) for Emergency Services and the NFPA Standard 1982 on Personal Alert Safety Systems (PASS). Components The MSA G1 - referred to hereafter as SCBA - is a pressure-demand self-contained breathing apparatus (SCBA) operating independent of the ambient air for use in atmospheres immediately dangerous to life or health. Breathable air is supplied to the user from a compressed air cylinder via a pressure reducer, a regulator and a facepiece. The exhalation air is released directly into the ambient atmosphere. Facepiece The facepiece provides breathable air from the regulator past an inhalation valve to the inside of the lens (to minimize lens fogging) and then through the check valves into the nosecup. Exhaled air is directed out of the exhalation valve by the nosecup directly to ambient air. The face seal provides a snug, comfortable fit, and tight seal. The facepiece is equipped with a mechanical speech diaphragm that enhances speech communication. The HUD is provided inside the facepiece through light pipes from the regulator. 4 When in safe atmospheres with no regulator attached, ambient air can be inhaled directly through an opening to facilitate breathing and speaking with minimal resistance. The facepiece provides NFPA compliant heat protection of 500° up to 5 minutes. The SCBA Facepiece is individually assigned and issued as a piece of Personal Protective Equipment. Regulator (also referred to as Demand Valve) The mask-mounted G1 Regulator is a pressure-demand regulator, which maintains a positive pressure in the facepiece while the SCBA is in use. The positive pressure regulator reduces the pressure coming from the pressure reducer further to provide breathable air to the user. The regulator is connected to the facepiece with a fixed position Push-To-Connect (PTC) connection. The Regulator serves as the second stage and is activated by first sharp inhale and capable of providing a minimum of 350 LPM. The regulator includes a bypass valve with a large and easily accessible bypass (red) knob and an electronic module that provides functionality for Heads-Up Display (HUD) and electronic voice communications. The bypass valve offers variable flow up to 120 liters when fully opened with four turns. The microphones are activated when the regulator is connected to the facepiece and the user begins breathing. Inhalation noise is not amplified by the system. The District’s SCBA utilizes a continuous hose to provide an uninterrupted connection from the pressure reducer to the regulator. G1 Heads-Up Display (HUD) The HUD is integrated into the regulator and projects light into the facepiece. The HUD allows users to see the cylinder pressure and alarm status while wearing the SCBA. The HUD receives the information on the SCBA and power from the power module. The HUD consists of 7 LEDs which are separated on the left and right sides to improve visibility and clarity. 5 G1 Pressure Reducer The pressure reducer reduces the cylinder pressure to an intermediate pressure of 115 PSI, which is in turn further reduced by the regulator to a pressure that is respirable by the user. The pressure reducer incorporates a fail safe design which ensures air flow to the user in the event of a malfunction within the pressure reducer. The relief valve activates at 200-250 PSI. The pressure reducer connects to the cylinder valve assembly with a handwheel assembly. The pressure reducer incorporates an intermediate pressure relief valve, and a cylinder connector with a sintered filter to capture particulates. The pressure reducer connects to the cylinder by a Quick Connect fitting. To disconnect, twist 1/4 turn and pull away from the cylinder valve assembly male quick-connect adapter. Push directly in to lock into place. A Safety Pin activates when the cylinder is turned on to prevent accidental disconnection. G1 Power Module The power module serves as the power supply and provides all of the information for the control module, regulator and speaker module. The power module is connected to the backplate. It connects to the rechargeable battery module, emits audible PASS alarms and pre-alarms and has 4 buddy lights. The rechargeable battery module contains non replaceable lithium-ion cells. The system notifies the user when the batteries need to be recharged by emitting an audible tone from the power module, displaying an empty battery icon on the display of the control module, and by a flashing yellow LED on the HUD. The power module is also equipped with a RIT light, which activates when low pressure alarm occurs, to make it easier to see the UAC in the dark. The power module has a data logging feature that records information about the SCBA while the control module is turned on. The power module contains an internal real time clock. G1 Control Module The G1 control module is the user’s interface with the SCBA and PASS device. The control module is assembled to the high pressure air source and to the power module by a pneumatics and electronic hose assembly. It is equipped with an analog gauge as well as a graphical display to provide vital information: Time Remain (Estimated) numeric cylinder 6 pressure, battery status, and alarms. When the control module is being read by the user, no buddy lights on the control module will flash and a white gauge light will illuminate, to enable the user to read the gauge and display. The integrated PASS motion sensor is housed within the control module. The ALARM button of the control module activates the full PASS alarm with or without air pressure. PASS Device The PASS device on the G1 SCBA is made up of three components: Battery Module Power Module Control Module The PASS device provides the user the ability to monitor movement through a motion sensor. The PASS device will go into pre-alarm with 20 seconds of being motionless. When a user remains motionless for 30 seconds, the PASS device goes into full alarm to alert those around the user. The PASS device also monitors cylinder pressure and battery status. G1 Speaker Module The speaker module amplifies and clarifies the speech from the facepiece during use. When inhaling, the breathing sound will not be amplified. The speaker module is turned OFF when the complete SCBA is turned OFF and can also be activated/ deactivated with its button. Pressing of the button is acknowledged by a beep. Battery The MSA G1 power supply is powered by a rechargeable Lithium Ion battery. All lights, communication, and controls are powered by this source. The battery provides 6-8 hrs of continuous use with all features active. Battery status can be checked without powering on SCBA. Press and hold both or one green button for 3-5 seconds. Change the battery when the battery power is yellow, indicating two hours remain. Batteries take between 4-6 hours to fully charge. The removal tool is located on the shoulder. 7 Cylinder Valve Assembly The cylinder valve assembly includes a large pressure gauge with a photoluminescent face. The handwheel for the cylinder valve assembly non- locking handwheel. The cylinder valve assembly includes a pressure-relief device to vent pressure safely if the cylinder is over pressurized. Primary Low Pressure Warning Device (Bell) The pressure reducer includes a bell alarm for low pressure that actuates at 35 percent of the SCBA’s rated service pressure during use. This will activated at approximately 1575 PSI and 16 minutes of remaining service. G1 Carrier and Harness Assembly The harness and carrier assembly consists of: Backplate (houses the power module, battery module, and pressure reducer) Cylinder band with latch to hold the cylinder Shoulder pads Adjustable pull straps Lumbar pad Waist belt Regulator Keeper Backplate The carrier and harness assembly includes an ergonomic backplate. The backplate includes large handles to facilitate handling and storage. The hop handle of the back plate has a drag rating of 1000 lbs. The side handles are rated to 500 lbs. Cylinder Band The metal cylinder band and latch securely retain the cylinder and provide a rigid opening to enhance cylinder installation and removal. Shoulder Pads The shoulder pads provide weight distribution across the shoulder, friction pad to prevent slippage of the straps, increased visibility with retroreflective material, and steel buckles for a secure fit. The tunnels on these pads are released using snap buttons to ease in swapping or repair of components. The inside and outside of the shoulder straps are identifiable by print/stitching. A facepiece clip can also be attached to either shoulder strap. Lumbar Pad 8 The adjustable lumbar pad provides the user three positions for ideal comfort. The lumbar pad can be adjusted by one-hand and can be adjusted while worn. The lumbar pad also has a swivel feature to allow it to move with the user. Cylinder The District’s utilizes the low-profile Eclipse cylinder. The cylinder is visually distinguishable by its black color. Constructed of a seamless aluminum liner that is fully wound over entire surface (except for thick neck area) with high-strength carbon fiber filament impregnated with epoxy resin and a final over-wrap of fiberglass fibers. The District’s cylinder is 4500 PSI with a rated service time of 45 minutes. The cylinder has a weight of 13.5 lbs. and a diameter of 6.1 inches. The minimum pressure for the SCBA to be in service is 4050 PSI. Do NOT use cylinders that are not filled to the maximum working pressure. Do NOT put cylinders that are partially charged in storage. Rapid Intervention Team/Universal Air Connection (RIT/UAC) The pressure reducer is equipped with a Rapid Intervention Team/Universal Air Connection (RIT/UAC) fitting. The RIT/UAC fitting is for use by rapid intervention teams for emergency filling operations. The SCBA includes an automatically resetting pressure relief valve to vent excess pressure if the SCBA is over pressurized during an emergency filling operation. NOTE: The UAC is compatible with all SCBA manufacturers. 9 Donning Don SCBA by placing arms through the shoulders straps. Connect waist belt. Pull forward on the waist strap pull tabs to tighten the belt for a snug fit. Pull down on the shoulder pull straps to tighten the straps. Adjust as necessary. 10 Start-up Sequence When the PASS device goes out of sleep mode, it goes into a start-up sequence that provides information to the control module about the state of the SCBA for operation. The logo screen shows the MSA logo and a Unit and the Riding Position if assigned to the device, on the control module. The buddy lights on the power and control modules cycle through red, yellow, and green. The power module plays the start-up tone. During this process, the PASS device does a self-test to make sure the device is operating correctly. The self-test screen shows the results of the self-test. A successful self-test shows a Go icon to indicate the SCBA can be put into service. If maintenance is necessary, the overhaul reminder icon shows to indicate the SCBA should be removed from service after use. If the SCBA should not be used, a Hardware Alarm icon shows on the control module and a full alarm from the power module is activated. The PASS device will not continue to operate. Remove the SCBA from service. The primary screen shows and the SCBA can be used. Primary Screen The primary screen provides all critical information to the user. The District’s SCBA are configured with the primary screen to display a calculated remaining service time. The countdown timer displays the estimated rated service pressure until 35% remaining, corresponding with the Air Management Guideline. The actual time remaining may be less than the calculated time displayed. Increases in breathing rate may reduce remaining time more than expected. Use the time indicator as a general guide only. The time displayed is based on the continuation of the average breathing rate over the last three minutes. Increases in the breathing rate after checking the displayed time may result in less remaining time than anticipated. Secondary Screen The secondary screen can be accessed by pressing the green button once. The secondary screen displays the following information: 11 Temperature Gauge Bluetooth Connectivity Long Range Radio Icon Battery Status Pressure PRESSURE COLOR DISPLAY 50 - 100% Green 36 - 49 % Yellow 0 - 35% Red HUD Pressure Status The HUD provides the pressure and alarm status through light pipes into the facepiece. The pressure status shows on the user's right side. The alarm status shows on the user's left side. The pressure status indicators are divided into the following four segments, which are based on the percentage of the maximum pressure of the cylinder. Each segment is associated with a specific number and color of LEDs. SEGMENT PRESSURE RANGE HUD LED Segment 1 75 - 100% Segment 2 50 - 74% Segment 3 36 - 49 % Segment 4 0 - 35% 12 SCBA Unit Identifier The SCBA will be outfitted with a unit identifier that corresponds with the apparatus. The identifier assists in quick visual identification. The identifier is secured to the carrier band. This identifier is designed to be complementary to the accountability system. RESOURCE IDENTIFIER Engine Aerial Rescue Tender , Squad Chiefs 13 Operational Check The District requires inspection of SCBA as part of the Daily check-off. SCBA will be inspected after use following proper cleaning and disinfection. DO NOT inspect the SCBA before cleaning if there is danger of contacting hazardous contaminants. All personnel shall inspect their assigned SCBA DAILY. This responsibility shall NOT be delegated. The SCBA Inspection consists of Visual Inspection and a Functional Test. If the SCBA fails any of the conditions listed in the Visual Inspection section or if the SCBA does not function properly for all tests outlined in the Functional Tests section, the SCBA must be removed from service. All Components 1. Inspect all components for deterioration, dirt, cracks, debris, tears, holes, stickiness, signs of heat or chemical related damage, or other visible signs of damage. 2. Inspect all straps (shoulder pads, pull straps, lumbar pad, waist straps, facepiece head harness) for tears, cuts, wear, abrasion, missing buckles or straps. 3. Perform all component specific inspections listed below. Facepiece 1. Inspect the lens for cracks, scratches, deformation, and color change. 2. Check the facepiece rubber for a tight seal and secure fit to the lens ring. 3. Ensure the exhalation valve is clean and operates easily. The valve must move off the seat and return when released (from inside the facepiece). 4. Inspect the facepiece inlet for damage. Ensure the inhalation valve is in place. 5. Inspect the nosecup to ensure the check valve are in place and the nosecup is secure to the component housing. Regulator 1. Ensure that moisture or debris is not present, especially inside the regulator and in the microphone ports. 2. Ensure the o-ring and seal ring are free of debris and not damaged or missing. 3. If the SCBA is equipped with a quick connect hose, inspect the rubber seal for deterioration, dirt, cracks, tears, or tackines. Inspect the quick connect fittings. Ensure that the openings are clear and free of debris and other contaminants. 14 Ensure that the quick connect fittings operate properly and are secured. Pressure Reducer 1. Turn the quick connect counterclockwise a quarter of a turn and pull away from cylinder valve to release. 2. Before installing ensure there is no dirt or debris on either the male or female end of the coupling. Ensure the adapter on the cylinder valve is tight. 3. Inspect the high pressure relief valve for damage. 4. Reattach handwheel to the cylinder valve. Push the quick connect coupling onto the cylinder valve adapter until an audible snap is heard. The handgrip will rapidly rotate approx. 45° counter-clockwise indicating that the valve is connected to the pressure regulator. 5. Ensure that the bell is properly aligned and that the screws are tight. The bell should not be able to be rotated or loose. Cylinder and Valve Assembly 1. Check the hydrostatic test date on the cylinder approval sticker located on the cylinder neck. 2. Ensure the needle and gauge face on the cylinder valve gauge are clearly visible and that the gauge stem is not bent. 3. Ensure the rubber boot is present on the cylinder valve. 4. NOTE: The cylinder shall have 4050 PSI or greater. Carrier Assembly 1. Operate the latch on the cylinder band to ensure that it opens and closes properly and that it holds the cylinder securely. 2. Unit Identifier is present. 3. Ensure that the lumbar pad is attached securely. 4. Ensure the power module and pressure reducer are secured to the backplate by the lower cover. Control Module 1. Check the displays for cracks and other visible damage. 2. Ensure the buttons are not damaged or missing. 3. Ensure the hose assembly is securely attached to the control module. 4. Ensure the needle and gauge face on the gauge are clearly visible and that the gauge stem is not bent. Power Module 15 1. Ensure that the power module and battery module are securely attached to the backplate. 2. Inspect the piezo emitters on both sides of the power module. (The emitter covers should not obstructed by dirt or debris.) Battery Module 1. Unlock the battery module with the battery removal tool. 2. Remove the battery module from the power module. 3. Check the battery module for visible damage, ensure that the connection seal is in place and undamaged. 4. Reinsert the battery module and turn off the PASS device. Check that the Regulator and Facepiece Can Hold a Negative Pressure 1. Close the cylinder valve and purge any air from the system using the bypass knob or the purge cover on the regulator 2. Hold the facepiece against the face to create an effective seal. 3. Attach regulator to the facepiece and inhale until the facepiece begins to collapse against the face. 4. Hold breath for approximately 10 seconds. Negative pressure should be maintained and the facepiece should remain collapsed against the face for the entire 10 seconds. Check Function of the Control Module, Power Module, HUD, Speaker Module and Primary Low Pressure Warning Device 1. Ensure that the bypass knob is fully closed (clockwise). 2. Pressurize the system by opening the cylinder valve. 3. Observe the starting sequence of the LEDs on the regulator. 4. Listen for the power module to sound and for the primary low pressure warning alarm to sound briefly. 5. Ensure that the buddy lights are flashing green. 6. Ensure the pressure gauge and LCD display show the correct pressure. When testing the control module, check if the graphical display and the analog gauge are consistent within 5% (225 PSI) of the cylinder pressure; Both reset buttons on the control module have the same function. Use one when resetting the motion alarm and the other when testing the manual alarm. 16 Verify proper function of the HUD, control module, power module, and low pressure warning device by observing the control module gauge and display when the alarms sound. Perform this test with a full cylinder. 7. Allow the control module to remain motionless for approximately 20 seconds. Listen for the power module to sound repeated tones of the PASS pre-alarm. Verify that the buddy lights are flashing red. Verify that the red LED is flashing in the HUD. 8. Shake the control module to reset the alarm before the unit goes into full alarm. 9. Allow the control module to remain motionless until the full alarm sounds (30 seconds). Listen for the power module to sound the tones of the PASS full alarm. Verify that the buddy lights are flashing red. Verify that the red LED is displayed in the HUD. Verify that shaking the control module does not reset the full alarm. 10. Reset the PASS alarm by pressing the left reset button (green) on the side of the control module twice within approximately one second. 11. To check the manual activation of the PASS alarm, press and hold the alarm button on the front of the control module until the alarm activates. Listen for the power module to sound the tones of the PASS full alarm. Verify that the buddy lights are flashing red. Verify that the red LED is displayed in the HUD. 12. Reset the PASS alarm by pressing the right reset button (green) on the side of the control module two times within approximately one second. 13. Close the cylinder valve fully. 14. Don the facepiece or hold the facepiece against the face to create an effective seal. 15. Attach the regulator to the facepiece. 16. Ensure proper attachment by pulling on the regulator. 17. Inhale sharply to start air flow. 18. Breathe normally. Ensure proper regulator response. The regulator should NOT make any unusual sounds including whistling, chattering, or popping 19. Ensure that air flows freely. 20. Talk into the facepiece to ensure the speaker module is operating properly. 21. Press and hold the ON/OFF button on the speaker module until the audible tone sounds and the unit turns OFF. 22. The LED on the speaker module should be OFF. 17 23. Press and hold the on/off button on the speaker module until the audible tone sounds and the unit turns ON. 24. Push the regulator release buttons. 25. Ensure that air flow stops. 26. Remove the facepiece from the face. 27. Close the cylinder valve fully. 28. Slowly open the bypass valve on the regulator to vent the pressure until the control module pressure reading drops below approximately 1575 PSI. 29. A flashing red LED must display in HUD at the appropriate pressure. The primary low pressure warning device should be alarming, all of the buddy lights should be flashing red, and the pneumatic light should illuminate. 30. The alarms should continue until the air pressure is 200 psi or less. 31. When the system pressure falls below 200 psi, turn the control module off by pressing the reset button (green) two times within approximately one second. 32. Open the bypass valve slowly to release any remaining pressure in the system. 33. Close the bypass valve. 34. Stow SCBA 18 Primary Screen The primary screen provides all critical information to the user. The District’s SCBA are configured with the primary screen to display a calculated remaining service time. The countdown timer displays the estimated rated service pressure until 35% remaining, corresponding with the Air Management Guideline. The actual time remaining may be less than the calculated time displayed. Increases in breathing rate may reduce remaining time more than expected. Use time indicator as general guide only. The time displayed is based on the continuation of the average breathing rate over the last three minutes. Increases in the breathing rate after checking the displayed time may result in less remaining time than anticipated. SCBA Unit Identifier The SCBA will be outfitted with a unit identifier that corresponds with the apparatus. The identifier assists in quick visual identification. The identifier is secured to the carrier band. Cleaning Disinfection Facepiece 1. Remove the facepiece-mounted regulator from the facepiece. 2. Use the instructions on the label to prepare a solution of Confidence Plus Germicidal Cleaner in a bucket or sink. NOTE: The head harness can be cleaned as part of the facepiece or removed to be cleaned separately. 3. Submerge the facepiece in Confidence Plus Germicidal Cleaner for a minimum of 30 seconds. 4. Use a soft brush or sponge to clean the soiled facepiece. 5. Rinse the facepiece and components thoroughly in clean water that is not more than 110°F and is preferably running and draining. 6. To clean and rinse the pressure-demand exhalation valve, use a blunt object to push in on the stem and flush the valve with clean water. 7. Operate the exhalation valve manually to make sure it operates correctly. 8. Make sure there is no water, moisture, or dampness on or in the facepiece before returning it to service. 9. Do a negative pressure seal test before returning the face piece to service. 19 Harness and Cylinder If the SCBA is soiled (i.e. heavy smoke residue or dirt accumulation) use a sponge damp with mild soap solution or use a soft/medium bristle brush to remove deposits, in a well ventilated area. Put a cover on the regulator outlet to prevent water, dirt, or debris from going into the regulator. from the following components: Harness (straps and buckles) Carrier (band and latch assembly) Cylinder (handwheel, gauge, outlet connection) Pressure reducer (bell and coupling nut connection) Control module/power module/battery module/speaker module Cleaning Considerations Do NOT use cleaning substances that can or might attack any part of the SCBA such as bleach. Do NOT use alcohol, which can cause deterioration of rubber parts. Do NOT use cleaning products that contain hydrocarbons or solvents such as nitro-thinner. Do NOT use radiant heat such as the sun or radiators to dry cleaned parts. Do NOT use a pressure washer. Ensure components are thoroughly rinsed. Make sure there is no water, moisture, or dampness on or in the facepiece and regulator before returning the SCBA to service. Any moisture on or in the facepiece or regulator can freeze and result in a malfunction of the SCBA. 20 SCBA Identification The SCBA components will utilize an identification system to allow for inventory tracking and maintenance reporting. MASK Masks will have a metal disk affixed. The disk is embossed with a three digit number. Example: 101 CYLINDER Cylinders are identified by a series of letters and numbers, which correspond with the barcode. Example: AME1333 HARNESS 21 Maintenance Reporting Maintenance Reporting for saws utilizes a dual system that includes the generation of a Work Order Ticket and the application of an Out of Service Tag. The Work Order Ticket shall be generated in Vector. In conjunction with the Work Order Ticket, a physical out-of-service tag is to be af xed to the asset. The tag will notate: Date: Enter the date of reporting. SER. #: Enter the Inventory Identi cation Number. Example: AME133 Location: Enter the Station and Unit where the asset is assigned. Problem: Provide a provide a description of the problem. Signed by: Enter your name. 22 fi fi 23