RWF Draft PDF
Document Details
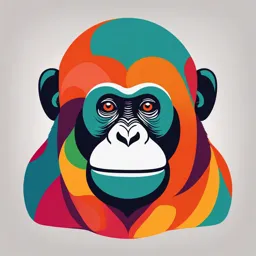
Uploaded by ImaginativePeachTree
Dayananda Sagar College of Engineering
Archana. A, Divyashree. S, Padmashree. S, Soundarya. S
Tags
Summary
This document is an internship report on the manufacturing of wheels and axles at the Rail Wheel Factory (RWF) in Bangalore, India. The report details the various processes involved, including melting, molding, finishing, and testing. It describes the materials used and the specifications for the products.
Full Transcript
1 INTERNSHIP REPORT On Rail Wheels and Axle Manufacturing Submitted by the Students of Bachelor of Engineering In Industrial Engineering and Management...
1 INTERNSHIP REPORT On Rail Wheels and Axle Manufacturing Submitted by the Students of Bachelor of Engineering In Industrial Engineering and Management Dayananda Sagar College of Engineering Internship Carried Out At Rail Wheel Factory Yelahanka, Bangalore Submitted by : Archana. A 1DS13IM001 Divyashree. S 1DS13IM010 Padmashree. S 1DS13IM027 Soundarya. S 1DS13IM046 2 Acknowledgment Our experience during the internship wouldn’t have been complete without the help of several people. It gives us a great sense of pleasure in acknowledging the support and help of the officers, supervisors, operators and the staff of Rail wheel factory. We wish to thank, first and foremost, Mr. S.N.Sarkar/Dy CME-TQM/ Principal/TTC, who gave us a chance to visit the prestigious rail wheel factory. We consider it an honor to have interned under Mr. T.Suresha/SSE/TTC/Electrical, Mr.M.G Sunil/SSE/TTC/Mechanical, Mr.D. Sanjeev Rao/SSE/TTC/Mechanical for sharing their literature and invaluable assistance and support. With immense gratitude we wish to thank Dr. C.P.S. Prakash (Principal of DSCE, Bangalore) and our Head of the Department, Dr. H. Ramakrishna, who helped us to get an opportunity to intern in this prestigious factory. We would also like to thank the operators in shop floor of RWF who helped us to complete our training and guided us with great spirit. Lastly, we extend our gratitude to our families for their support without whom it would have only remained a dream and we also thank all those who have directly and indirectly helped us to complete this internship successfully. 3 Abstract Indian Railways is an Indian state-owned enterprise, owned and operated by the Government of India through the Ministry of Railways. It is one of the world's largest railway networks comprising 115,000 km of track over a route of 65,808 km and 7,112 stations. Till early 1980s Indian Railways was importing about 55% of requirement of wheels and axles. Indigenous capacity was available only at Tata Iron & Steel Company [TISCO] and Durgapur Steel Plant [DSP]. The TISCO plant was technically not capable of meeting the changing requirement of wheels and axles for the new designs of rolling stock and production was discontinued. DSP was only able to partially meet Indian Railways’ needs. In the early 1970s the Railway Ministry felt the necessity for setting up a new specialized Production Unit for manufacture of rolling stock wheels and axles as import substitute. This report concentrates on the procedure carried out in the manufacturing of wheels, axles and wheel sets. Since each wheel and axle undergoes testing, the parameters considered for testing and methods of testing will also be focused on. The materials that are used either directly (making of wheels and axles) and indirectly (protective gear, chemicals for testing, etc.) is summarized. 4 Table of Contents Sl.no Topic Page no 1. Introduction 5-7 2. Wheel Shop 8-27 Melting 10-15 Molding shop 15-23 Finishing 24-27 Cope and Drag 28-29 preparation 3. Consumables used in 31-33 Wheel Shop 4. Specification in Wheel 34-35 Shop 5. Axle Shop 36-55 Forging 39-46 Machining 46-53 Assembly 54-55 6. Consumables used in Axle 56 Shop 7. M Lab 57-76 8. EMMS 77-80 9. Spectro Lab 81-83 10. Conclusion 84 11. Bibliography 85 5 Introduction Rail Wheel Factory (RWF) is a manufacturing unit of Indian Railways, producing wheels, axles and wheel sets of railroad wagons, coaches and locomotives for the use of Indian Railways and overseas customers is situated at Yelahanka, Bangalore in the Indian state of Karnataka. The RWF was founded in the year 1984. It was formerly known as Wheel and Axle plant but since it came under the Indian railway ministry board, it was renamed Rail wheel Factory afterwards. The unit was started by C. K. Jaffer Sharief, the then Railway Minister, who got this project to Bangalore. It was commissioned to manufacture wheels and axles for the Indian Railways. This factory uses cast steel technology in the manufacturing of wheels which utilizes scrap steel collected from Railways' own workshops as raw material. The products that are manufactured at RWF are wheels, Axles and wheel sets. They are engineered with little scrap for human errors. It has a planned capacity to manufacture of about 2,00,000 wheels of different sizes, 1,00,000 axles and to assemble 70,000 wheel sets. It was the first unit of Indian Railways to receive ISO 9001:2008 accreditation. 6 RWF is successfully meeting the requirement of wheels of wagon builders and loose wheels. A wheel is cast every 1.5 minutes. Wheels are cast by controlled pressure pouring process. The technology for this was obtained from M/s. Griffin Wheel Co., USA. In this process, the raw material used is scrap which consist old used Wheel sets, axles, parts of Rail bogie etc; that are rejected as unfit for use by the Railways. The scrap steel is melted in Electric Arc furnace. The correct chemistry of molten metal steel is ensured through a Spectrometer. The wheels are eventually cast in the graphite moulds, which are pre-heated and sprayed. After allowing for a pre-determined setting time, the mould is split and the risers are automatically separated from the cast wheel. The wheel then undergoes the process of heat treatment, Cleaning, Magnaglo testing, Ultrasonic testing, Peening and various stages of inspection. The wheel produced by this process requires no machining except the precision boring of central hole (hub) where the axle has to be fitted. RWF produces an axle every five minutes. The Plant converts steel blooms to axles through a series of forging, heat treatment and machining processes. Blooms cut to the required sizes are heated in Rotary Hearth Furnace up to 1200 degree C. These are carried to the precision Long Forging machine where the hammers convert billets into the required shapes through CNC. The Forging Machine having multiple hammers is used to get required sizes of forgings. After end cutting, the rough forged axles are subjected to heat treatment in normalizing and tempering furnaces. Rail Wheel Factory is having two axle machining lines which are CNC machines to convert these forgings to the axle. RWF converts BOX N, Coaching and Container Axles to wheel sets. Loco axles are 7 generally sent in rough turned condition to the Production Units and Railways workshops for converting to wheel sets. RWF is having a highly automated wheel set assembly complex supplied by M/s. Simmons Machine Tool Corporation, USA. Wheel seat sizes of machined axles are measured and wheels received from wheel shop are bored according to this size. The precision borers ensure that the final bores have required interference with the individual axles. After boring, the wheels are carried through automated conveyors to the assembly complex along with axles and wheels are pressed one after another. The force required in pressing the wheels is recorded automatically to ensure that the pressing force is within the laid down limits. Every product of RWF is manufactured to customer’s requirements and each product is inspected and tested to ensure a longer life and reliability. Since most machining process is automated, it leaves very little room for human error. 8 Wheel Shop Scrap Scr Charging Melting Spectro-Analysis Controlled Cooling Mould Split Pouring in Hot Wheel Kiln Sprue Wash & Hub Cutting Heat Treatment Stamping Shot Blasting Apex Grinding Hub Cooling & Cooling Magnaglo and Hardness testing Cope and Drag Ultrasound Testing grinding Inspection & Stock Shot Peening and Warpage Hub Boring 9 Wheel Shop The Wheel Shop is the first unit of RWF. The wheels enable the train to move along the rails of the track. On an average, a wheel weighs about 500 kgs. The RWF produces eight different types of wheels having different composition, requirements and dimensions. The wheel shop recycles metals from the scrap yard and adds required resources to obtain the right composition for producing wheels. Later the melt is used for moulding to obtain the basic geometry of wheel. It undergoes various machining, finishing processes and inspection tests to conform to customers’ requirements. The Wheel Shop comprises of mainly three divisions: 1) Melting 2) Moulding 3) Finishing (WFPS) 10 MELTING Scrap conditioning : Scraps are the basic additions to manufacture the wheels. They may be: Rejected wheels Rejected axles Used axles and worn out wheels Chips formed during machining processes The scraps are divided into three types – machine chips, light metals and heavy metals. This sectioning is important because during the initial melting process in the electric arc furnace, the distribution of heat is not uniform. The bucket charging distribution is such that from bottom to top; heavy, light and machine chips. This arrangement will prevent major fire spewing, scrap bridging, and scrap collapse when the arc is setup. 11 Charging of scrap: It can be simply defined as addition of scrap along with materials such as lime stone, calcined lime and coke/graphite to the furnace. Brief procedure The electrodes are raised and an electromagnet via an EOT (Electric Overhead Traveling) crane transfers machine chips and some lights scraps into the furnace. Bucket charging of scraps in the required order is done. The bucket opens from the bottom. The heavier metals are on the top, then the light and the machine chips. Charge approximately 9000 to 1200 kgs calcined lime and 200 to 250 kgs coke/graphite. Melting of scrap: The furnace used for melting is an electric arc furnace. RWF wheel shop contains three electric arc furnaces named A, B and C. They operate the same way and only in C; its tap hole order differs from A and B. The capacity of each furnace is 20-23 Metric Tons. 12 The three electrode electric arc furnace heats charged material by means of an electric arc. It consists of a refractory-lined vessel (Alumina bricks), usually water-cooled in larger sizes, covered with a retractable roof, and through which one or more graphite electrodes enters the furnace. The furnace is primarily split into three sections: The shell, which consists of the sidewalls and lower steel "bowl" The hearth, which consists of the refractory that lines the lower bowl The roof, which may be refractory-lined or water-cooled, and can be shaped as a section of a sphere, or as a frustum (conical section). The roof also supports the refractory delta in its center, through which one or more graphite electrodes enter. Brief procedure The electrodes are lowered. On supplying the necessary current and voltage an arc is struck between the electrodes and the charge for 45 to 55 minutes. The gap between the electrodes and the charge is maintained by regulating the movements of the electrodes so that the arc remains between them. After 45 to 55 minutes oxygen lancing pipe is used for cutting of scrap through the slag door. The temperature during this procedure is 1650 to 1700 °C. The slag is formed which floats on the surface of the melt. This prevents oxidation, refines the metal and protects the furnace roof from excessive heat. Removal of slag: During the Oxygen lancing, slag is eliminated through the slag door. Brief procedure Dolomite is spread over the cleaned slag door. Remove full slag before the temperature is 1630 °C. 13 If it is sluggish, shovel in 55 to 65 kgs of Fluorspar on the slag. Ferro-manganese is used for slag reducing at around 1650 °C and 150 kgs of slag reducing mixture is also used. Spectro – analysis: The testing of sample that has to be further used or subjected for wheel manufacture is done at the spectro lab. The sample (solidified metal) for testing is obtained from the electric arc furnace to determine the composition of various metal constituents within the required range. Carburisation/Decarburisation: A sample of melt is taken for testing a percentage composition of C (Carbon), Si (Silica) and Mn (Manganese). These may differ from the fixed required percentage. Addition of materials to bring the composition to the fixed percentages may either be done by carburization or decarburization. Brief procedure CARBURISATION, if the carbon content is founded to be lesser, required amount of Graphite is added when the electrodes are just inside the bath at 1640 °C and the sample is taken. DECARBURISATION, if the carbon content is more, slag coated Oxygen lancing pipe is introduced to reduce Carbon content; based/depending on carbon to be reduced Oxygen is supplied. The controlling content for this process are Ferro-manganese, Silica-manganese and Ferro-silicon. Mix the bath thoroughly. After 3-4 minutes of arcing, take another sample for testing. Tapping: It is the process of pouring the melt from the furnace into the ladle (melt carrying container) by tilting the base of the furnace. 14 Brief procedure The ladle is prepared for tapping process and brought to the furnace through EOT crane. Add required amount of Ferro-silicon, Ferro-manganese or Silicon-manganese into the ladle after the ladle preparation. The tapping temperature should be between 1660 °C to 1720 °C. The base of the furnace is tilted and tapping of the metal starts. The ladle is adjusted so that the metal stream falls at the center of the ladle and not on the side walls. Tapping is completed within 3 to 4 minutes to avoid temperature loss. After tapping, the ladle is carried to the JMP (John Mohr Pit). 15 For 20 MT of liquid metal Item to be added Elements to increase Quantity of Ferro Aim to achieve allow to add for increase of element Graphite powder Carbon 2kgs for 0.01% to 60-62 for Box-N incr. 50-52 BG coach 70-72 CH-36 Wheel Ferro-silicon Silicon 140 kgs without 50-55 drain metal. 130 kgs with drain metal. Ferro-Manganese Manganese(Normally 3 kgs for 0.01% to 70-75(ladle) in furnace) incr. 30-45(furnace) Silicon-Manganese Manganese 3 kgs for 0.01% to 70-75 incr. MOULDING ROOM 16 John Mohr Pit(JMP): After the melt is poured into the ladle, it is carried to the JMP. The wheel shop has two John Mohr pits. The main purpose of JMP is for temperature measurement and maintenance and finalizing the melt composition. Brief procedure Wait till the temperature is lesser than 1610 °C. When the temperature is around 1560 to 1610 °C, immerse the Aluminum stars. The Aluminum stars are used to prevent change in composition of the melt. A sample is taken for testing, this acts as the final analysis for the required/fixed composition. Ladle insulation material is sprinkled into the ladle to maintain temperature. The ladle is taken for insertion of the ceramic pipe. *NOTE: The ceramic pouring tube is fixed on a cover and it takes around 1 day for preparation because it has to withstand high temperatures of the melt. This is done in a Pouring Tube Section. The roof is lifted and lowered 2 to 3 times for the pouring tube to get accustomed to the heat. This process prevents cracking of the pouring tube. Casting process: The casting process uses controlled pressure pouring process through which the melt rises in the ceramic pipe and fills the cavity of the approximate desired shape. This technique contains cope and drag system. They are made up of Graphite material. 17 Brief procedure The ladle containing the molten metal placed in JMP is brought into the place of pouring and Ladle Insulation Material powder is sprayed into molten metal to prevent temperature loss. The cope and drag assembly is placed on the covering of the ladle which contains a center circular hole. This hole houses the ingate through which molten metal gets into the cope-drag assembly. The liquid metal with high air pressure comes out of the ladle through the ingate. A sensor prevents overflow of melt i.e.; graphite stopper plunges the bottom of the drag and prevents the further flow of liquid metal from ladle into cavity. It also prevents the liquid metal flowing back to the ladle from the cavity. An asbestos gasket is used as a sealant between drag and pouring tube to prevent bleeding of liquid metal and also airation. One gasket is used for each cast wheel. Once the mould is prepared it is subjected to 9 to 10 minutes of solidification. Solidification may be defined as allowing the metal to cool and solidify. After solidification, the cope and drag assembly is split and the cast wheel is obtained. 18 The cope is clamped and lifted gently. Sometimes, wheel sticks to the cope so the crane moves up and down over the drag controlled by the operator. The wheel is placed in hot wheel kiln where it is subjected to controlled air cooling. The cycle time is 32 minutes and 33 wheels can be accommodated. The cope and drag are sent back separately for cleaning and preparation. *NOTE: The pouring of each wheel takes about 80seconds. For one heat 32 to 33 wheels can be casted. And a cope-drag assembly can be used for 20 to 25 wheels. Once the metal is poured paddy husk is added to the assembly through riser holes to prevent sudden drop in temperature of molten metal which otherwise would produce cracks/flaws in the surface of wheels. The important parameters are pouring time, metal initial and final temperature, pouring rate splitting time, wheels offloaded and riser weight. 19 Sprue washing: In casting, a sprue is a channel or passage through which a molten material is introduced into a mould. It contains a little part of the runner and riser which is not removed during splitting. These must be removed before the further cleaning of the wheel takes place. Brief procedure After the controlled air cooling, the wheel coming out of the kiln is at a temperature of about 400 to 500 °C. After sprue washing, the wheels are stamped where the wheel and heat numbers are stamped using a stamping machine. This is called stamping. Hub cutting: The center portion of the wheel where the axle fits in is called the hub. To produce this hub of required diameter, hub cutting is carried out. The mixture of oxygen and LPG gas flame coming out of the nozzle at high pressure and velocity is used for hub cutting. Brief procedure The hole is initially cut for a diameter lesser than the required during this process using hub cutting machine. The average hub diameter is 188mm for BOX-N. The part of the stopper pipe inserted during casting remains inside the cast wheel after being cut at both the edges. This is called pilot hole. The hole is initially cleaned using pneumatic air. The gas flame is directed to the pilot hole and moved along the radius and finally moved in a circular shape. 20 A Go-No Go gauge is used for checking its correctness. If found right, reload otherwise reject the wheel. *NOTE: If the hub cutters are under breakdown, wait till the temperature is lesser than 265°C , load them into normalizing. The temperature for hub cutting is between 265-400°C. The quality parameters are dimensional range of hub cut, details of hub not fallen/ pilot hole block, non-conforming wheels, O2 + LPG. Normalizing: Normalizing is defined as a heat treatment process to heat the metal above the critical temperature, holding for a period of time long enough for transformation to occur and air cooling. In general, it is to bring or return to a normal or standard condition or state. Normalizing helps to maintain proper grain size. Brief procedure: The wheels after hub cutting are sent into the rotary hearth furnace for normalizing process. The rotary hearth furnace used for normalizing has 7 zones. First three zones are called as heating zones where the outer layer of the wheel and a few inner layers get heated. 21 The next four zones are called soaking zones wherein the heat spreads uniformly including the core of the wheel. The temperature maintained in the furnace is between 890 to 960 °C. The fuel used in rotary hearth furnace is high speed diesel. Each wheel remains in the furnace for a duration of 90 minutes and 45 wheels in 2rows can accommodated inside the furnace. The outer and inner walls of the furnace remain stationary whereas the hearth inside rotates with the help of rack and pinion gear. The temperature of the wheel coming out of the furnace is greater than 800 °C. *NOTE: The quality parameters are normalizing furnace zone temperature, heat and wheel number, time in and out of normalizing furnace. Specifications of blowers used for normalizing Direction Flow Rated De-rated Motor of static static discharge pressure pressure Combustion V belt 6000 CFM 1300mm 1070mm 75 HP; air blower driven; LTV WG WG 1450 RPM Combustion V belt 5701 CFM 1083mm 890mm 60 HP; air blower driven;RTV WG WG 1450 RPM Dilution air Direct 2500 CFM 240mm 195mm 7.5 HP blower driven;LTV WG WG 2 pole Automising Direct 1206 CFM 1088mm 895mm 15 HP air blower driven;RTV WG WG 2 pole Nose cooling Direct 3300 CFM 176mm 145mm 7.5 HP air blower driven;RTV WG WG 4 pole 3 Air blower, V belt 400m /min 650mm 535mm 100 HP induced driven, WG WG 4 pole draught direct driven; RTH 22 Quenching: It is a stage of material processing through which a metal is quickly brought down to lower temperature from a high temperature by rapid cooling. During the movement of the train the outer portion of the wheel called the rim is in contact with the rail and hence it is this portion that is subjected to more wear and tear. Therefore, to increase the hardness of the rim, rim quenching is performed. Water is the medium for quenching. Brief procedure The wheels coming out from the normalizing furnace are subjected to rim quenching wherein high pressure jet of water with 2.5 to 3.5 kg/cm2 pressure is made to fall only on the rim portion of the wheel for about five minutes. This increases the hardness of the rim portion up to a depth of 5 to 8mm. The temperature of the water for rim quenching is 18 to 35 °C. Tempering : Since the wheels are manufactured by casting process, there are chances of internal stresses being introduced in the interior of the wheel. These stresses are very dangerous and may also damage the wheel during working. In order to remove these stresses from the wheel, they are sent into the draw furnace where the wheel undergoes tempering process. Brief procedure Each wheel once entered the draw furnace remains inside for around 2.5 hours. The draw furnace in RWF is run using high speed diesel and has a capacity of 80 wheels. 23 Hub cooling: During the assembly of the wheels with axles there are chances of crack formation in the hub portion. Hence, this portion needs to be hardened. This hardening of the hub portion is done by quenching process. This stage contains a conveyor belt that’s consists 3 hub coolers. Brief procedure The wheels coming out of draw furnace is subjected to hub cooling in three regions – upper, middle and the inner portion of the hub is cooled separately. The time taken in each of the region is 45 seconds. High jet of water having a pressure of 2.5 kg/cm2 is sprayed on the interior of the hub during this process. The hub portion becomes harder hence reducing the chance of crack. The wheel after hub quenching has a rough surface and is air- cooled. The wheels need not be air-cooled separately, they are sent into stack yard for cooling for about 60 minutes. 24 Wheel Final Process Shop The finishing in the wheel shop happens in the Wheel Final Process Shop (WFPS). The wheels stored in the stack yard have a rough uneven surface. These wheels need to be cleaned and finished before its usage. This cleaning, finishing, and certain test is conducted in this cleaning shop. Apex grinding: Since the wheels are casted in cope and drag assembly, there is extra material along the parting line. To eliminate the extra material, apex grinding is performed. Cleaning: The surface of the wheel may contain dirt, ashes and even dust particles formed during storing; also the wheels contain scales formed during heat treatment process. To remove the unwanted dust and obtain a clean surfaced wheel, cleaning is performed. Brief procedure It contains three roto blasts through which high velocity starch are made to strike the surface of the wheel. 25 Due to the impact of these particles, the surface dust present on the wheels gets removed due to the abrasive action. Hence the surface cleaned wheel is obtained after the cleaning process. Magnaglo testing: This is a fluorescent magnetic particle inspection method. This test is conducted for detecting surface cracks. Brief procedure The cleaned wheels enter a dark room. Magnaglo powder uses water as a suspension medium. This is poured on the wheel. The black light (with wavelength of 365 nm) is switched on and the magnaglo fluoresces bright yellow-green. The operator checks for fine surface and sub-surface discontinuities. A crack can be detected when the magnetic particles accumulate around it and it glows bright. The operator uses radium chalks to indicate cracks. Further on, these will be grinded. Ultrasound testing: Ultrasound testing (UT) is a family of non-destructive testing techniques based on the propagation of ultrasonic waves in the object or material tested. This test is performed to detect interior defects/flaws. Brief procedure The wheel is directed for ultrasound testing. The wheel spins with its bottom in water. The sensors underwater emit a pulse waves with center frequencies ranging from 0.1 to 15 MHz 26 A probe sends a sound wave into a test material. There are two indications, one from the initial pulse of the probe, and the second due to the back wall echo. A defect creates a third indication and simultaneously reduces the amplitude of the back wall indication. The operator will indicate the flaw code and place. The wheel undergoes Brinell hardness test and the values will be displayed on a digital screen. Warpage testing: The wheels during casting and heat treatment process remains at high temperature. During this temperature there are chances of wheel undergoing little bending. But this bending of wheels above certain limits is undesirable for the working of the wheel. Warpaging is a process in which these bends are detected and if it exceeds the limit, they will be rejected. Brief procedure Receive wheel for warpage measurement. Pass wheel for warpage if warpage reading is lesser than 1.0mm for all wheels. The warpaging includes the balancing of wheels from which the defects relating to the shape of the wheels can be detected. If the detected defects in the shape like bending of wheels etc. are more than the limiting value, wheels are rejected. SHOT PEENING: Shot peening is a cold working process used to produce a compressive residual stress layer and modify mechanical properties of metals and composites. It entails impacting a surface with shot with force sufficient to 27 create plastic deformation. This process uses steels shots for peening cast iron wheels of hardness 255 to 363 BHN. Brief procedure Steel shots are made to strike on the wheel at high speeds. In case there are any cracks, the steel shots strike the cracks at high velocities and fill the gap and help remove the defects. Each wheel undergoes this process for 1 minute on an average. Hub bore machining: This is a rough boring operation carried before it is sent to the assembly shop. During hub boring, the center hole generated is of a smaller diameter than required. The hole needs to be enlarged to fit in the axle. This is done by hub boring machining. Brief procedure A square shaped carbide insert is used for boring. A hole of 3mm lesser than the diameter of the axle wheel seat is produced during this process. 28 COPE AND DRAG PREPARATION IN MOULDING ROOM Cleaning stage: After splitting the cope and drag, they are sent separately for their preparation. The cope and drag are first sent to their respective tilting machines where loose particles of dust fall out as they rotate. An operator uses compressed air at high pressure to blow out the remaining dust. The receiving temperature for blowing compressed air is 245-325°C. Cope baking: The cope is coated with resin and baked in an oven. After cope baking, the cope is cleaned by sand blasting. Cope spraying: Fused Silica Powder are mixed with additives of CMC and Veegum powder to prepare mould spray. This spray is used for coating the mould which serves as an emulsion stabilizer, suspending agent and binder. Check adhesion with adhesion tester whose acceptable range is from 50-65 PSI. There are three spray guns. The quantity for BOX-N that is used for each region is as follows: Plate – 185ml Hub – 125ml Rim – 170ml Drag spraying: A spray mixture tank is used for mixing the fused silica powder along with additives to prepare the mould spray. 29 When the temperature is above 245°C, the drag enters the spray room and the cooling fan is put on. The baume value for spray quantity from the two spray guns range from 39 to 41. Spray tank pressure – 8 to 10 PSI Atomizing pressure – 40 to 65 PSI The drag is later sent to the MHO (Mould Holding Oven) waiting for pouring. Spray quantity for BOX-N Hub – 125 ml Plate – 175 ml Rim – 175 ml Stopper fitting: An operator assembles the parts of the stopper pipe before fixing it on to the cope. When the cope is received, the operator checks for the spray pattern. If satisfied the stopper pipe assembly fixes onto the cope. In the end, the operator fixes the stapple to avoid any slipping of stopper pipe. The cope is later sent to the oven to wait for pouring. 30 Consumables for Wheel Shop The consumables used in the wheel shop can be either used directly to manufacture the wheels (eg: Coke/Grahite, Ferro-silicon, etc.) or indirectly used to help manufacture the wheels Consumable Name: Asbestos Gasket Application/ Job requirement: Asbestos Gasket is used as a sealant between drag and pouring tube in casting of railway cast steel wheel to prevent bleeding of liquid steel. One asbestos gasket is used for casting each wheel. Consumable Name: Ingate Sleeves Application/ Job requirement: The Clay Graphite Tapered Ingate Sleeve shall be fired/baked in controlled reducing atmosphere. The kilns shall have control mechanism to achieve uniform heating at a controlled rate as established by the manufacturer’s firing schedule. The Clay Graphite Tapered Ingate Sleeves have to be encased in a suitable medium like graphite, calcined petroleum coke or similar during firing so as to avoid oxidation. During the mould assembly for casting steel railway wheels, the Clay Graphite Tapered Ingate Sleeve is required to be fixed in the graphite drag against the taper at a pressure of 52-56 kg/cm2 and ingate sleeve is retained in position using 31 ingate-retaining ring. As the mould is reused, after each casting the ingate is reamed using grinding stone for proper seating of the clay graphite stopper in the stopper seat. Consumable Name: Ceramic Pouring Tube Application/ Job requirement: The pouring tube is assembled with pressure Pouring Tank cover. The molten metal rises through the pouring Tube into the mould by means of controlled pressure (35psi max.) pouring technique. Consumable Name: Pouring Tube Glaze Application/ Job requirement: The pouring tube glaze is used as a coating applied to the ceramic pouring tube by dipping the tube in it to fill the pores of the tube and make the tube air tight. Consumable Name: Clay Graphite Stopper Application/ Job requirement: The Clay Graphite Stopper, made of clay graphite, is used to prevent the back flow of molten metal after pouring the metal into the mould. The stopper with pipe assembly is set with cope on the required height and used for the manufacture of cast steel wheels. Molten metal rises through the gap available between the stopper and mould box by means of pressure pouring technique. Once the metal rises to the required height of risers the Clay Graphite Stopper is pressed down for closing the molten metal incoming port by Pneumatic cylinders. Consumable Name: Calcined Lime Application/ Job requirement: This Calcined Lime is used as flux for making slag in the steel making process through Electric Arc Furnace melting practice. Consumable Name: Ferro Silicon Application/ Job requirement: Ferro Silicon is used as a ladle addition to the liquid Steel tapped from the Electric Arc Furnace. Final chemistry with respect to Silicon is achieved suitably for casting of Railway steel wheels. 32 Consumable Name: Silico Manganese Application/ Job requirement: Silico Manganese is used as a ladle addition to the liquid steel manufactured in Electric Arc Furnace steel making practice. Final chemistry with respect to Manganese and partly Silicon is achieved suitably for casting of Railway steel wheels. Consumable Name: Ferro Manganese Application/ Job requirement: Ferro Manganese is used as furnace addition in the making of steel from Electric Arc Furnaces for casting of Railway steel wheels. Consumable Name : Graphite Powder/ Granule Application/ Job requirement: Graphite Powder/Granules is used in the Electric arc Furnace at RWF, steel scrap is melted for casting of railway wheels. During the course of melting, Graphite Granules are added to maintain the carbon content in the steel. Consumable Name: Magnaglo Powder Application/ Job requirement: Magnaglo powder is a dry, free flowing, speckled brown and white magnetic powder which fluoresces bright yellow-green under black light (wave length of 365 nanometres). Magnaglo powder is intended for 33 use in high sensitivity wet method magnetic particle inspection using water as suspension vehicle. It is used to locate fine surface and sub-surface discontinuities such as cracks, inclusions, seams, shrinkage porosity, tears, laps flakes etc., in cast steel wheels for Rail road application. Consumable Name : Fused Silica Powder Application/ Job requirement: Fused Silica Powder is used for the preparation of spray for graphite moulds. It should serve as an emulsion stabilizer, suspending agent, film former, binder and organic gum modifier, when added with other additives of CMC and veegum to prepare mould spray. Consumable Name: Steel Shots Application/ Job requirement: The steel shots are used for cleaning and peening of the Cast steel wheels of hardness of 255 to 363 BHN. 34 Wheel Shop Specifications Average Wheels Cast Per Day 720 706 704 700 680 660 Average wheels cast per day 641 640 620 600 13-14 14-15 15-16 Average Heats Per Day 22.75 22.62 2013-2014 2014-2015 20.79 2015-2016 35 Good Wheels Per Day 670 656 660 650 640 630 616 620 610 Good Wheels Per Day 594 600 590 580 570 560 13-14 14-15 15-16 Wheel Rejection % 5.93 6.083 15-Apr 6.13 7.51 15-May 15-Jun 7.31 15-Jul 15-Aug 36 Axle Shop Billet Cutting Billet heating in Forging in LFM RHF Normalising Cooling on the End Cutting and Bed Hot Stamping of Axle no Air Cool R16 Polymer Tempering Axles Quenching for R43 Axles Machining Sampling for Air Cool mechanical & metallurgical test 37 Axle Shop The Axle shop is the second unit of RWF. An axle is a central shaft for a rotating wheel. RWF produces an axle every 5 minutes. Rail Wheel Factory is having three axle machining lines out of which 2 are CNC machines to convert these forgings to the axle. RWF converts BOX N, Coaching and Container Axles to wheel sets. Loco axles are generally sent in rough turned condition to the Production Units and Railways workshops for converting to wheel sets. RWF produces 16 Axels according to the requirement. The Plant converts steel blooms to axles through a series of forging, heat treatment and machining processes. Blooms cut to the required sizes are heated in Rotary Hearth Furnace up to 1200 degree Celsius. These are carried to the precision Long Forging machine where the hammers convert billets into the required shapes through computerized control program. The Forging Machine having multiple hammers is used to get required sizes of forgings. After end cutting, the rough forged axles are subjected to heat treatment in normalizing and tempering furnaces. It undergoes machining, finishing and inspection tests to satisfy the customer requirements. 38 The railway axle is a long, thick cylindrical rod made up of alloy steel and weighs about 500 kg. The axles mainly consist of 4 parts – body, wheel seat, dust guard and journal. Major portion of the axle is the body whose length is fixed and is equal the distance to be maintained between two parallel wheels. Hence, the length of the body which is the center portion of the axle varies for different types of axle. The portion of the axle where the wheels of the train is fixed is the wheel seat. The curved portion between the wheel seat and the journal is the dust guard. The two ends of the axle after the dust guard is journal. The journal is the main portion which is required in a perfect smooth finished surface state. The bearings of the train wheels occupy this place. The axle shop is divided into three portions and they are: Forging shop Machining shop Assembly shop 39 FORGING SHOP Billet cutting : The long bar with square cross section is called a bloom and they are cut into small length pieces by gas welding. The blooms are obtained from Durgapur (SAIL), Maharashtra (MUSCO) and Pune (Kalyani forging) steel plant. The billet cutting machine is an automated machine and it takes three minutes to cut a billet from a bloom. The fuel used is a mixture of Oxygen and LPG. According to the various cross section area, the axle are divided into the following types: Types Area(mm2) Materials used Locomotive axles 340 R43 BOX-N 300 R16 Coaching axles 287 R16 Brief procedure The bloom is carried in a conveyor to the billet cutting machine. The operator marks the points at which the flame cutting will take place. The marking depends on the type of axle to be manufactured. The machine is switch ON and the gas flame of O2 and LPG at a suitable pressure is directed on the work piece and cutting operation is performed. The cutting is based on length to weight ratio. 40 Heating : Heating of billets is done in Rotary Hearth Furnace (RHF). The billet after being cut must be heated so that it can be forged. The RHF having four furnaces namely – preheating zone, heating zone, soaking zone I and soaking zone II – is used for heating the billets to a temperature of 1200 °C. Zone Total no of burners Preheating 6 Heating 9 Soaking I 3 Soaking II 2 Total 20 Brief procedure A robot arm inserts the billet into the RHF. The billet enters the preheating zone where the heating process begins. The billet moves into the heating zone. This zone takes the longest time. 41 In the soaking zone I and II, the heat is spreads to the core of the work piece. The RHF has a capacity of 80 billets and the cycle time is 6.5 hours. *NOTE: Quality parameters of Billet Heating Zones Upto 250 sq per 272/287/300 340 sq/round with round (with sq/round (with tolerance tolerance) tolerance) Pre heating Zone 1100-1170 1150-1200 1170-1210 Heating Zone 1100-1170 1180-1200 1180-1210 Soaking zone I 1125-1170 1180-1200 1180-1210 Soaking zone II 1125-1170 1180-1200 1180-1210 Forging : Forging is a mechanism used to make or shape a metal object by heating in a fire furnace and hammering it to the required dimensions. The forging machine called Long forging machine consists of four hammers of about 800 tons capacity each with two motors subjected to the power supply of 400KW power. The hammers are placed diagonally to each other. The operation is brought about based on the set of instructions (program) given by the operator. 42 Brief procedure: The billets from the Rotary hearth furnace at a temperature of about 1100 - 1150 degree Celsius are subjected to forging process. This is done to bring the billet. The forging process in axle shop is based on cams, which in turn is controlled by PLC (Program Logic Control) and CNC (Computer Numerically Controlled) for the control of movements and dimension specifications (measurements) respectively. It consists of two chuck head named A and B related to the movement of expansion and R which is used as a reference for diameters. The hydraulic pressure in the machine generates mechanical power to bring about the process. As a result the axles of required dimensions are obtained based on the requirement. Thus the forged axles of specified dimension are now subjected to End cutting process. *NOTE: The cycle time of the process ranges from 4.5-5 minutes per axle. 43 SPECIFICATIONS: 1.Force 800tons 2.Eccentric stroke(hammer 14mm length) 3.Stroke 270strokes/min 4.Hydraullic pressure 90-100bar 5.Lubricant pressure 5bar 6.Damping pressure 80bar 7.Ring space pressure 70-80bar End Cutting: The metal cutting process used in the removal of excess material at the ends to obtain metal component with required dimensions is termed as end cutting. During the forging process, the billet deforms to the required axle shape, and since at the ends the material is deformed and in an irregular shape, it needs to be eliminated. Thus, end cutting is done. Basic procedure: The forged axles after forging is subjected to end cutting process termed as Axle end cutting. High flame gas of oxygen and LPG mixture from the nozzle with a diameter of about 25mm at high pressure is forced on both the sides hence the removal of metal. The cycle time of the process is less than a minute due to high temperature of the forged axle. The high temperature axles are now subjected to normal Air cooling process, wherein the axles are arranged in an open area hence the cooling takes for about half an hour duration. 44 Heat Treatment: Normalising : It consists of heating steel about 40-50°C above its upper critical temperature and if necessary holding it at that temperature for a short time. Brief procedure: Once the axles are air cooled, they are sent into the normalizing furnace. These axles are placed on the base of the furnace and fire is set on the sides of the furnace. The fuel used is High Speed Diesel. Around 90 axles can be accommodated in the furnace. Normalizing furnace consists of three zones namely pre-heating, heating and soaking. The cooled axles regain their grain structure by the end of normalizing process. The type of structure obtained will depend largely on the thickness of cross section as this will affect the rate of cooling. Thin sections will give a much finer grain than thick sections. 45 Quenching : It is simply defined as sudden cooling of heated metal by dipping in cooling agent or spraying cooling agent in order to obtain the work piece in a stable state which induces certain properties like hardness etc to the work piece. Brief procedure: Not all types of axles require quenching. Only a few types of diesel axles are quenched in quenching agent. The quenching agent used is a mixture of polymer oil and water in the ratio 1:20. The quenching agent is present in a tank about 10 feet depth where quenching takes place. Quenching is done for about 25-30 minutes depending on the carbon content present in the material of the particular axle. It is done for 4 to 5 axles at a time. The axles which do not require quenching are sent directly to tempering furnace after normalizing. Diesel axles are sent into tempering furnace after quenching. Tempering : Tempering is a heat treatment technique applied to ferrous alloys, such as steel or cast iron, to achieve greater toughness by decreasing the hardness of the alloy. The reduction in hardness is usually accompanied by an increase in ductility, provides softness and machineability to the metal thereby decreasing the brittleness of the metal. 46 Brief procedure: Axles enter the tempering furnace where they are heated below their critical temperature in order to achieve softness so that they can be machined with ease. The tempering furnace also consists of three zones i.e.; pre- heating, heating and soaking. Heating is done at around 600 to 650°C. Around 118 axles can be placed in the tempering furnace. Tempering reduces internal stresses in the axles which may have induced during heating, forging or quenching. Those axles which have acquired the required composition and properties are sent to the axle machining shop for machining while others are sent back for re-heating. Sampling: After tempering, the axles are cooled for 24 hours and then taken for testing. The axle is taken for destructive testing where it is cross-sectioned and checked if it is suitable for operating and its other functions. Axle Machine Shop Station 1:End milling, centering and Cup turning : End milling can be defined as removal of metal with the help of rotating end mill. An end mill is a type of milling cutter, a cutting tool used in industrial milling applications. It is distinguished from the drill bit in its application, geometry, and manufacture. While a drill bit can only cut in the axial direction, a milling bit can generally cut in all directions, though some cannot cut axially. And end mill is a multi-point cutting tool. Because the forged axles undergo various hat treatment processes, it has excess length. This must be cut with little amount of tolerance for further machining. 47 Centering is the process of producing a center hole in the axle in order to hold the axle in further machining process. This is followed by cup turning where excess material is removed and smoother surface finish is done only at the ends. The centering tool and cup turning tool is made out of HCS. The tool life of centering tool is 200 axles. These operations are performed by CNC machines of Siemens technology. Brief procedure The end mill cutter has a number of inserts which does the actual cutting job. The axle is brought close to the end mill and machined. It consists of two chucks each powered by a motor. They remove 0.7 mm of material from each side. The inserts that are used for milling have four cutting edges and are made of Carbide. Each edge may be used for operating 60 axles. Then it is switched to another set of two chucks that is again powered by a motor (each). The same set of chucks performs both centering and cup turning. Centering is done for a hole diameter of 28mm (Box-N axle) Cup turning is done for a diameter of 148mm(Box-N axle) Ultrasound inspection : Ultrasound inspection is done to detect internal defects. This inspection is done from one face to another. After calibrating the ultra sound flow detector the couplant is applied to obtain proper coupling for conductance. On inspection, of the axle does not meet the conditions even after heat treatment, the axle is rejected. 48 Station 2: Rough turning: Turning is a machining process in which a cutting tool, typically a non-rotary tool bit, describes a helical tool path by moving more or less linearly while the work piece rotates. The tool used here is a single point cutting insert made of Carbide. They are called nest inserts. In order to remove the excess material and bring it to the required dimensions, rough turning is carried out. The exact shape of axle is brought to in this process and later machined to obtain a smoother surface finish. During this process the axle is fixed between the chucks and made to rotate at very high speeds. The carbide insert is fixed to a cassette and it is fitted into the tool holder. Hence the tool holder is more permanent and the cassettes are replaced. Each cassette has an L and R side. According to their function, they will be selected. There are five chucks used for this operation. 49 The rough turning operation also uses CNC technology. Brief procedure The axle is divided to four sections – 1, 2, 3 and 4. 1 and 4 for the body. 2 and 3 for journal. Rollers are used for long turning to avoid vibrations. After lifting rollers, channels 1 and 4 take place. Coolant is not used in this process since carbide inserts are used. 15 axles can be machined with the same insert for journals and 8 to 10 axles can be machined in case of longer lengths. Station 3 : Drilling, countersinking, Tapping and Recentering : After rough turning of the axle, threaded holes are drilled at the two end surfaces in order to fix the bearing to the axle. Drilling is a machining operation of producing a cylindrical hole in a solid work piece by means of a revolving tool called the drill bit. Drill bit is called as twist drill since it has sharp twisted edges formed around a cylindrical body. It is made up of HCS (High Carbon Steel). 50 A countersink is a conical hole cut into a work piece. It is used to allow the dead center to support the axle for further machining processes. Tapping is the operation of producing internal threads in a previously drilled hole by means of a tool called tap. The tap had threads cut on its periphery and is hardened to improve its properties. The threads cut on the tap form the replica of the threads to be produced in the work piece. Brief procedure An overhead crane transfers the rough turned axle to station 3. Prior to the operation the pitch circle diameter (PCD) and the angle at which the holes are to be drilled is checked. The axle is subjected to drilling operation where the drill bit is held in the chuck of the machine and is rotated by a spindle at high speeds of 198 rpm. The drill bit is forced to move against the rigidly clamped axle. In the case of BOX-N axles three holes are drilled at an angle of 120o and 22.5 mm drill by the sharp cutting edges of the rotating drill bit. Excess material removed (i.e; chips) gets curled and escapes through the helical grooves provided in the drill bit. Countersinking is done with the help of a countersink tool of conical shape for the axles to be supported. To perform the tapping operation the tool held rigidly in the spindle is rotated at a speed of 90 rpm. The rotating tap is fed slowly in the hole of axle to cut the material and produce threads. During the tapping process, eight threads are formed for each inch. 51 Operations are carried out on both sides. A continuous supply of coolant is required in order to reduce the heat production and wash away the chips. Operation Speed Feed Depth of Coolant Insert Rev/min mm/min cut mm Drilling 198 50 72 Flood dia 27.5 coolant twist drill Countersinking 198 1 Flood Dia 28 coolant twist drill Tapping 90 52 Flood 1”, 8 (+0.5, -1.0) coolant threads CNC M/C tap. Station 4: Smooth turning : The rough finished axle is now given a good surface finish by turning operation. A carbide tool with Titanium coating (heat proofing) is fixed in the tool holder and is fed against the rotating work piece. Brief procedure Bypass the axles that have defects. The type of rejections maybe journal undersize, dust guard undersize, wheel set undersize and body undersize. The process consists of two channels. CH1: T1 Journal T3 Body T5 Wheel seat 52 CH2: T4 Journal T2 Body T6 Wheel seat The axle is rotated at a speed of 350 rpm and the operation is carried out at a feed rate of 0.66 mm/rev. The coolant used during the process is servo oil mixed with water. And the cycle time is 20 minutes. Change the inserts when required. Station 5 : Cylindrical grinding : Grinding is an abrasive machining process which uses a grinding wheel as a cutting tool to produce finished surface. The journal is the most important part of the axle since the bearing is seated on it. Hence, the journal is given a perfect finish. This is done by grinding. Brief procedure 53 Two grinding wheels are kept on both the ends at an angle of 45o to finish both the sides of the axles. They operate one after the other. The work piece (axle) comes near to the wheel and gets fixed. The high speed grinding wheel rotating at 1240 rpm approaches the axle due to which very fine material layer is removed from the axle due to the action of abrasive particles fixed on the grinding wheel. In the same manner the other side of the axle is also finished. The time taken for grinding one axle is 8 to 8.5 minutes. *NOTE : The tool used here is a diamond wheel dresser of 700 mm diameter. The depth of cut lies between 0.12 to 0.125 mm. Magnaglo testing : This is a fluorescent magnetic particle inspection method. This test is conducted for detecting surface cracks. Brief procedure The operator uses a pipe that consists of magnetic flux powder and carrier oil to wet the axle. The axle under the black light fluoresces bright yellow green. Due to accumulation of magnetic flux in cracks, they appear brighter. The magnetizing time before switching on the black light is 20 seconds. If the crack is lesser than 21.88 mm, the axle is passed otherwise it is rejected. Ultrasonic testing : Ultrasound testing (UT) is a family of non-destructive testing techniques based on the propagation of ultrasonic waves in the object or material tested. This test is performed to detect interior defects/flaws. 54 Brief procedure The axle is dipped in the water bath of volume 4000 ltrs. A transmitter moves above the axle along its axis. It is also called diametric probing. The frequency used is 5 MHz. The internal defects can be detected because of acoustic mismatch. This is due to difference in density. The results are displayed on a CRT screen. The time taken for ultrasound inspection is 5 to 6 minutes. Wheel Seat Measuring Station: Since the axle and wheel are brought separately from two shops, during assembly the type of fit maintained is interference fit. The wheel seat is measured with gauges to allow the wheel to be pressed on to it. Wheel Boring: The wheel boring in the Wheel shop is a rough finishing process. The wheel has to be bored for a smoother finishing and to the specification of the wheel seat. The wheel seat specifications are obtained from the measuring station. The manufactured wheels from the wheel shop for the particular axle is center bored to the measure axle’s wheel seat diameter by the vertical boring machine using Octagon shaped carbide tool. Wheel mounting : Wheel mounting is the process of pressing the two wheels onto the wheel seat of the axle using mounting press to form a wheel set. 55 Brief procedure After the smooth surface finish boring operation, the two wheels for the particular axle are sent for pressing. Boring of one wheel consumes 4 minutes. For BOX-N wheel set Bore diameter = 211.917 mm Wheel seat diameter = 212.32 mm The two wheels are hydraulically pressed so that the two wheels sit on the wheel seat of the axle by using pressing machine one wheel after the other. Castor oil/double boiled linseed oil is applied on the axle during pressing to reduce the pressure on the axle. The wheel set obtained is measured by various gauges. Example : offset gauge. The track gauge measurement and the offset measurement are done. The track gauge is important since the wheels sit on the track. Thus their measurement is essential. And the offset allows the bearing to sit properly. 56 In case the distance between the wheels is to be altered or any other minor corrections need to be done, it is corrected by DEMOUNTING machine. Good sets are rolled onto the inspection line. It is painted to prevent the surface of the axle from rusting and the journal is covered and then transported to place where rest of the body parts of the train is manufactured. Pressing tonnage for wheel sets Wheel set type Tonnage Range (metric) BOX-N 78 – 136 BGC 72 - 117.5 BLC 78 – 136 25 T 85 - 128 57 Consumables used in Axle shop The following consumables used in Rail Wheel Factory are essentially needed to be multi-sourced. The particulars given here under are indicative and are meant to help suppliers for developing and supplying the same to RWF. The axle consumables are: Consumable Name: Steel Blooms for forging Diesel/Electric loco and EMU Driving axles as per IRS R 43 and IRS R 16 Application/ Job requirement: The steel blooms shall be manufactured from steel made by basic electric arc furnace or any other process recommended as equivalent and approved by the purchasing railways. The steel must be degassed under vacuum. Hydrogen content in the liquid steel is determined by standard analysis method on LECO hydrogen analyzer. Hydrogen content of the steel is determined by the standard analysis method on LECO nitrogen analyzer. Consumable Name: Forging Hammer Application/ Job requirement: The forging hammers are used for forging different steel axles and armature shaft for railway use. Forging Hammers are made from DIN 56NiCrMoV7 steel quenched and tempered to 34 HRC. The reclamation process is described in the RWF specification for reclamation. Entire process followed for reclamation must be documented and be made available to inspecting officials. 58 M Lab Properties of materials Every material is known by its set of properties. A variety of tests are conducted to evaluate and compare the mechanical properties of different materials. Some of the popular tests conducted include the tensile test, Compression test, Shear test, Hardness test, Impact test, bending test and so on. Among all the tests tensile test gives maximum information about mechanical properties. MECHANICAL PROPERTIES Yield Strength: 59 It can be defined as the stress at which plastic deformation (yielding) begins without any appreciable increase in load. Yield strength, σy = Py /A0 N/m2 Where Py = load at yield point A0 = original area of cross section. Ductility: It is the ability of the material to undergo plastic deformation under tensile load. A material with high ductility undergoes severe plastic deformation before fracture takes place. Percentage elongation gives a measure of ductility. % elongation = (L – L0) / L0 * 100 Where L = length of specimen after the tensile test. L0 = original length. Malleability: It is the ability of the material to undergo plastic deformation under compressive load. Ultimate tensile strength: After the yield point the specimen undergoes continuous plastic deformation with increase in load. This load reaches a certain maximum value after which the specimen does not take any more load. At the point of ultimate load, the area of cross section of the specimen starts reducing and is known as Necking. Ultimate tensile strength, σu = Pu / A0 N/m 2 Where Pu = ultimate load A0 = original area of cross section 60 Fracture strength: After the ultimate load is reached, the load drops and at a particular load fracture takes place. The stress corresponding to this load where the actual failure takes place is known as Fracture strength of the material. 2 Fracture strength, σf = Pf / A0 N/m Where Pf = fracture load or breaking load A0 = original area of cross section Toughness: The toughness of a material is its ability to withstand both elastic and plastic deformation. In other words, it is the amount of energy a material can withstand before fracture takes place. IRON CARBON EQUILIBRIUM DIAGRAM A study of the constitution and structure of all steels and irons must first start with the Iron carbon equilibrium diagram. Iron is an allotropic metal which means that it can exist in more than one type of crystal structure depending upon temperature. Pure iron exists as BCC structure at room temperature and is called as FERRITE or α- IRON. At 912 degrees Celsius BCC Iron undergoes allotropic changes and becomes FCC structure which is retained till 1394 degree Celsius. FCC Iron is also known as AUSTENITE or γ – IRON. At 1394 degree Celsius it changes back once again to BCC structure called δ – FERRITE and this is retained till its melting point at 1538 degree Celsius. In Iron carbon equilibrium diagram, the left vertical axis represents 100% iron and all the allotropic changes of pure iron with temperature. The right vertical axis does not represent 100% carbon but instead represents only 6.67% C by weight. This is because a maximum amount of 6.67% C can only 61 be added to molten iron at which it becomes saturated. Iron when it contains exactly 6.67% C by weight forms a phase called CEMENTITE or IRON CARBIDE Fe3C. Description of phases in the Fe-c system All the phases that appear on the Fe-c equilibrium diagram are equilibrium phases that is, they are the phases obtained upon very slow cooling at equilibrium conditions. Following are the different equilibrium phases of Fe-C. 62 α – FERRITE: It is nothing but an interstitial solid solution of small amounts of carbon dissolved in BCC iron. The maximum solid solubility of carbon in iron is 0.025% at 727 degrees Celsius and 0.008% at room temperature. It is the softest among all phases of iron and carbon. AUSTENITE It is again an interstitial solid solution of carbon but in FCC iron. The maximum solid solubility is 2.1%C at 1148 degree Celsius. Austenite is not stable below 727 degrees Celsius and will not be normally present in the micro structure at room temperature. It has an FCC structure and it is not magnetic. δ – FERRITE It is also an interstitial solid solution of carbon now BCC iron because austenite changes its structure at 1394 degree Celsius from FCC to BCC. Maximum solid solubility of carbon in δ-iron is 0.1%C at 1495 degree Celsius. CEMENTITE It is also known as iron carbide and has a chemical formula Fe3C. It is considered as chemical compound because it contains fixed carbon percentage but is crystalline in nature. Cementite always contains 6.67%C by weight and has an orthorhombic crystal structure. It is the hardest structure that appears on Fe-C diagram. The presence of cementite greatly enhances the properties of steel. PEARLITE When austenite containing exactly 0.83%C is cooled very slowly to below 727 degrees Celsius, it transforms into pearlite. Pearlite is nothing but lamellar structure of α- ferrite and cementite. It is a fairly soft structure and 63 its hardness lies between that of α-ferrite and cementite. It has a finger print like appearance. LEDEBURITE It is the eutectic lamellar mixture of austenite (light phase) and cementite (dark phase). The eutectic reaction occurs at 4.33%C at 1148 degree Celsius. Austenite in the eutectic mixture of ledeburite is unstable below 727 degrees Celsius and hence transforms into α-ferrite and cementite. 64 M Lab M lab also known as Metallurgy lab is an integral part of the RWF. The main objective is to test the consumables and the specimens in order to ensure safety, quality and confirm that they meet the specifications. The M lab is divided into various sections: Machine shop Physical testing Chemical lab Refractory lab Tests can be carried out in two ways: Destructive tests Non-destructive tests DESTRUCTIVE TESTS Physical section will carry out various metallurgical tests on wheels and axles. After being destructively tested, the component of the specimen either breaks or remains no longer useful for further use. Ex. Tensile tests, Impact tests, etc. NON-DESTRUCTIVE TESTS 65 A component does not break in non-destructive testing and after testing it can be used for the purpose for which it is made. Ex. Magnetic particle inspection, Ultrasonic testing, etc. MACHINE SHOP Machine shop is generally used for preparation of specimens. Since destructive testing is done, wheel and axle has to be sectioned correctly to accommodate all tests. The machine shop contains a lathe machine, grinding machine and a drilling machine. Tasks that are performed by the operator in the machine shop are: Axle specimen is prepared. Cross section of the wheel is obtained from EMMS (Electrical Mechanical Machine Shop). Specimen for the Charpy test is prepared. The specimens from machine shop further go to physical testing to check for their physical parameters. PHYSICAL TESTING All tests in the physical testing are of destructive type. Since the wheels are produced by casting process, there is lot of stress induced during solidification of the molten metal. These are not good for working of wheels, hence to check the limiting stress, tests are carried out. 66 The axles undergo forging in the axle shop. Due to changing temperatures, stresses are developed. To test their limiting stress and grain structure, physical testing is necessary. Tests carried out are: Closure test Radial saw cut analysis technique is used to measure the bulk circumferential residual stress levels in rail road cast steel wheel. With this technique the opening or closure of the saw cut, at the flange tip is monitored as a function of the radial cut depth. Hardness test To a metallurgist, hardness is a material’s resistance to penetration. In general, an indenter is pressed into the surface of the material to be tested under a specific load for a definite time interval, and a measurement is made of the size or depth of the indentation. The greater the hardness of the metal, the greater resistance it has to deformation. In metallurgy hardness is defined as the ability of a material to resist plastic deformation. Hardness tests can be performed with the help of instruments such as : Brinell Hardness tester : This test is a type of indentation test. J.A. Brinell introduced the first standardized indentation- hardness test in 1900. The Brinell hardness test consists in indenting the metal surface with a 10-mm diameter 67 steel ball at a load range of 500-3000 kg, depending of hardness of particular materials. The Brinell hardness tester uses a steel ball for indentation. The hardness number is determined by its characteristics such as applied load, diameter of indenter, diameter of indentation, depth of the impression. Rockwell Hardness Tester : Rockwell hardness test is most preferably used and is generally accepted due to the speed, small size of indentation and ability to distinguish small hardness difference. The hardness is measured according to the depth of indentation under a constant load. The type of indenter used here is a diamond indenter. The acceptable HRC (Rockwell Hardness) are as follows: Wagon : 277 to 341 68 Coach : 255 to 321 Portable Hardness Tester: Conventional hardness testers, like Rockwell, Brinell or Vickers machines, require the test piece be brought to the testing device; but this is not always possible. Portable testing devices have been developed that permit in-situ hardness measurements thus offering quick and economical supplements to conventional, stationary testing machines. An ideal solution for metallic hardness measurements with conversions to HLD, HRC, HRB, HB, HV, and HS are available. There is no indentation in this hardness tester. Micro Hardness tester : Determination of hardness over very small areas for example individual constituents, phases, requires hardness testing machines in micro or sub-micro scales. Vickers hardness can also be measured in a micro scale, which is based on the same fundamental method as in a macro scale. The micro indenter (diamond-shape) is used for measuring in a small area, such as at the cross section of the heat-treated metal surface. 69 The micro hardness test is mainly for testing hardness of steel shots. Steel shots are used for finishing purposes. The acceptable hardness value is in the range of 375 to 550 HV. Tensile test In tensile testing, the ratio of maximum load to original cross sectional area is also called ultimate strength. This test gives an idea of material strength obtained by proper process adopted of steel making and its effective heat treatment done. Tests will be carried out by turning to the standard test method and breaking by using tensile testing machine. There are two tensile test machines - one of a 100 ton capacity and another of a 20 ton capacity. The important parameters that are considered are – Peak load Breaking load Maximum displacement Area Ultimate stress Elongation Reduction in area Yield stress Grain structure A very important feature of a metal is the average size of the grain. The size of the grain determines the properties of the metal. For example, smaller grain size increases tensile strength and tends to increase ductility. A larger grain size is preferred for improved high-temperature creep properties. Creep is the permanent deformation that increases with time under constant 70 load or stress. Creep becomes progressively easier with increasing temperature. Grain size are reported in terms of grains per unit are or volume average diameter or as grain size number derived from area measurements. This will be done by a metallurgical microscope with an image analyzer. This indicates the type of structure having the material and it reveals defects of the material like porosity, shrinkage etc. There are 8 different grain size distributions of Iron Carbon. The required range is 6 to 8. This is evaluated by measuring the grains per unit volume. 71 72 Charpy Impact test It is a test to determine the behavior of the material when subjected to higher rates of loading, usually in bending, tension or torsion. The loads that are suddenly applied to a structure are known as shock or impact load. These loads build up rapid stress and affect the resisting properties of material. The property of a material is associated with work required to cause rupture. In charpy test, the specimen is place d as ‘cantilever beam’. The specimens have U-shaped notch of 45°. The notch is located on tension side of specimen during impact loading. Depth of notch is generally taken as t.5 to t/3 where ‘t’ is thickness of the specimen. Specimen Charpy Impact test 73 Charpy Impact testing equipment 74 CHEMICAL LAB Chemical lab consists of analysis of various consumables to check for their parameters and compositions. Two types of analysis are conducted. They are: Wet analysis Instrumental analysis In Wet analysis, individual analysis of consumables is made by dissolving them either in water/acid or any liquid medium. It is a classical method which involves observation to analyze materials. Most of the analyzing is done in the liquid phase. Wet techniques often depend on the formation of a product of the chemical reaction that is easily detected and measured. Some tests are conducted by using certain reagents to indicate the presence of a specific chemical in an 75 unknown solution. Few tests are based on volumetric analysis for volume measurements. In Instrumental analysis, the consumables and specimens are tested using scientific instruments. It is used to measure the property of the analyte (material). The various types of instruments used in M-lab are: LECO Analyzer: It is an elemental carbon and sulfur analyzer that has a variable power combustion furnace, and has an enhanced IR cell design. It has available automation that makes it a valuable resource for any industrial environment requiring accurate analysis of carbon and/or sulfur. The unit gives fast analysis in less than a minute. Particle size analyzer: A particle size analyzer is used to test the size of the fused silica that is used in spraying the cope and drag. The particle size is important because if it does not conform to the required size, the silica might clog at the tip of the nozzle, hence making it difficult for spraying. A laser beam is used to count the particles and the size is measured. 76 XRF: Wavelength dispersive X-Ray fluorescence spectrometer is an instrument used for rapid quantitative elemental analysis of major and minor atomic elements, from beryllium (Be) through uranium (U), in a wide variety of sample types with minimal standards. It is a Micro analysis technique to analyze samples as small as 500 µm. The principle of working is based on Brooks’ law. It is the latest instrument, eliminating the necessity of chemical analysis, thus saving time. Mono quartz distillation unit Kinematic viscometer 77 Flame photometer Flash point apparatus Melting point apparatus Electro chemical Analyzer Flow length apparatus Viscometer Electrolytic Analyzer Centrifugal apparatus Muffle furnace REFRACTORY LAB Refractory means difficult to melt or work (resistant to heat). A refractory material is one that retains its strength at high temperatures. Refractories can be defined as "non-metallic materials having those chemical and physical properties that make them applicable for structures or as components of systems that are exposed to environments above 1,000 °F (811 K; 538 °C)”. Refractory materials are used in linings for furnaces, kilns, incinerators and reactors. They are also used to make crucibles and moulds for casting glass and metals. Refractory lab is an important part of the RWf since they use refractory consumables such as refractory castables and Alumina bricks. To ensure that they are heat resistant, tests are conducted in the Refractory lab. Refractory lab consists of Flue gas analyzer, permeter (Atomic clock permeability), muffle furnace, RVL machine. Flue gas analyzer: Flue gas is the gas exiting to the atmosphere via a flue, which is a pipe or channel for conveying exhaust gases from a fireplace, oven, furnace, boiler or steam generator. A device that monitors the composition of the flue gas of a boiler heating unit to 78 determine if the mixture of air and fuel is at the proper ratio for maximum heat output. Atomic clock permeability: Permeability is a property of foundry sand with respect to how well the sand can vent, i.e. how well gases pass through the sand. And in other words, permeability is the property by which we can know the ability of material to transmit fluid/gases. The permeability is commonly tested to see if it is correct for the casting conditions to find Permeability number permeter is used. Muffle furnace: A muffle furnace is front-loading box-type oven or kiln for high temperature. It is used in many research facilities to determine what proportion of a sample is non-combustible and non- volatile. 79 EMMS EMMS is an abbreviation for Electrical Mechanical Machine Shop. The preparation of specimen for testing, tools for machining, and cross section of wheels are done here. Operations such as grinding, turning, milling, and finishing are carried out. TOOLS Single point cutting tool: A single point cutting tool is a simplest type consisting of a single effective cutting edge that removes the excess material from the work piece. Lathe tool (chamfering tool, parting tool, facing tool, etc.), shaper tools (tools used in shaping machine), planer tools, boring tools etc are the examples of single point cutting tool. Multipoint cutting tool: A multipoint cutting tool has more than one cutting edge and includes milling cutters, drill bit, reamers, broachers, grinding wheel etc. 80 Chip removal process: When the cutting tool is forced to move against the work piece, the tool exerts a compressive force on the work piece. The material of the work piece is stressed beyond its yield point causing it to deform plastically and shear off. The sheared portion of the metal begins to flow along the cutting tool face in the form of small pieces called chips. Three different types of chips are formed, they are Continuous chips Continuous chips with built up edge Discontinuous chips TURNING (LATHE) Turning is a machining process used for the generation of external cylindrical and conical surfaces on a rotating work piece by means of a single point traversing cutting tool. The process is usually performed on a lathe, wherein a single point 81 cutting tool is fed against a rotating work piece. Both the work piece and the tool are held rigidly on the lathe. Turret lathe is used for the preparation of cope and drag mould. MILLING Milling is a manufacturing process in which the excess material from the work piece is removed by a rotating multi point cutting tool called milling cutter. In milling, the cutter is held in the spindle of the machine and made to rotate at suitable speeds. The work piece, which is held rigidly by a suitable device is fed slowly against the rotating cutter. As the work piece advances against the rotating cutter, each tooth of the cutter removes metal from the surface of the work piece to produce the desired shape. Milling machines are preferred for small and medium sized jobs and are used for producing flat, angular or curved surfaces for cutting threads, toothed gears, keyways, slots and wide variety of operations. 82 GRINDING Grinding is a process of removing excess material from the work piece by the mechanical action of abrasive particles that are held together by an adhesive, generally in the form of solid wheel. The wheel known as grinding wheel is rotated at high speeds, and when the surface of the rotating wheel is brought in contact with the work piece, material is removed in the form of fine chips. The depth of cut is obtained by downward movement of the grinding wheel. The process removes very little material in the form of fine chips when compared to that of turning, milling or drilling, and this makes it to be called a finishing process. Grinding is employed to produce a work piece of high accuracy and surface finish. 83 Spectro Lab The testing of sample that has to be further used or subjected for wheel manufacture is done at the spectro lab. The sample (solidified metal) for testing is obtained from the electric arc furnace to determine the composition of various metal constituents within the required range. The instrument or tester used for this purpose is ARL Metal Analyzer (M-402 optical emission spectrometer). ARL Metal Analyzer (M-402 optical emission spectrometer) PRINCIPLE: The principle of optical emission spectrometry involves applying electrical energy in the form of spark generated between an electrode (tungsten) and a metal sample, whereby the vaporized atoms are brought to a high energy state within a so called discharge plasma. WORKING: The polished sample is placed between two tungsten electrodes and an arc is struck. In doing so the electrons are excited. Inductively coupled plasma (ICP) is used as an excitation source. Optical emission refers to emission using spark discharge, direct current arc discharge or glow discharge for generating the excitation discharge. This method involves statistical processing of the spark pulse generated emission spectra obtained from spark discharges in an inert (argon) atmosphere. The excited atoms and ions in the discharge plasma create a unique emission spectrum specific to each element. Thus, a single element generates numerous characteristic emission spectral lines. Therefore the light generated by the discharge can be said to be a collection of the spectral lines generated by the elements in the sample. This light is split by a diffraction grating to extract the emission spectrum for the target elements. The intensity of each emission spectrum depends on the concentration of the element in the sample. Detectors (photo multiplier tubes) measure the presence or absence of the spectrum 84 extracted for each element and the intensity of the spectrum to perform qualitative and quantitative analysis of the elements. After detecting, the concentration of each element in the sample is displayed. The following element compositions are acquired: Carbon Manganese Silicon Phosphorous Sulphur Chromium Nickel Copper Molybdenum Aluminum Vanadium Lead Titanium Tin 85 The optical emission spectrometer offers rapid elemental analysis of solid metal samples, making it indispensable for quality control in steel making processes. It offers fast and accurate metal analysis. ADVANTAGES/BENEFITS: Stability, accuracy, precision and low detection limits. Robustness and reliability. Easy integration to increase productivity. HYDROGEN TESTING MACHINE: The presence of hydrogen and other supplementary gases is tested using this machine. The working principle is based on Wheatstone bridge. A Wheatstone bridge is an electrical circuit used to measure an unknown electrical resistance. It consists of four resistors where three resistors of known resistances are used to determine the unknown resistance. At the point of balance the ratio of the opposite resista