ITE College West School of Engineering Diploma in Mechanical System Engineering Risk Control and Management Textbook PDF
Document Details
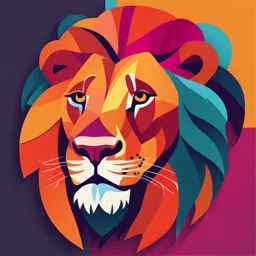
Uploaded by WillingZombie5275
ITE College West
2024
Lee Heng Keong
Tags
Related
- BME520 Biomedical Device Design & Troubleshooting Chapter 3 PDF
- ITE College West School of Engineering Mechanical System Engineering Diploma - Risk Control and Management PDF
- ITE College West School of Engineering Diploma in Mechanical System Engineering Risk Control and Management PDF
- Risk Control and Management Textbook PDF
- Gift of Fire, Ch 8 Errors, Failures & Risks PDF
- Compass Health AI SOP: Usability Engineering (PDF)
Summary
This textbook details Risk Control and Management for ITE College West's Mechanical System Engineering Diploma. The book covers risk management procedures, hazard management, implementing control measures, and emergency preparedness.
Full Transcript
School of Engineering Diploma in Mechanical System Engineering Risk Control and Management ME 73007 Documentation History Version No. Prepared by Effective date 1.0 Lee Heng Keong April 2024 Module: ME73007 / Ris...
School of Engineering Diploma in Mechanical System Engineering Risk Control and Management ME 73007 Documentation History Version No. Prepared by Effective date 1.0 Lee Heng Keong April 2024 Module: ME73007 / Risk Control and Management CONTENTS Topics Page 1 Conduct Risk Assessment 1.1 Risk management process 1 1.2 Hazards identification 9 1.3 Evaluate risk level of hazards 17 1.4 Hierarchy of control measure 20 1.5 Implementing control process 22 2 Implement risk management plan & control 2.1 Coordinate WSH Management Programme 25 2.2 Coordinate WSH training 32 2.3 Coordinate management review 36 2.4 Legal compliance for WSH management system 38 3 Respond to emergency situations and crisis 3.1 Emergency preparedness and response plan 42 (EPRP) 3.2 Prepare for the emergency response team 48 3.3 Inspection of response equipment and review of 51 response plan 1. Conduct Risk Assessment 1.1 Risk management process 1.1 Risk management process 1.1A Guiding principles of WSH framework 1.2 Hazards identification 1.1B Features of WSH Act 1.1C WSH coverage 1.3 Evaluate risk level of hazards 1.1D Preparation work 1.4 Hierarchy of control measure 1.1E Risk assessment 1.1F Risk evaluation 1.5 Implementing control process 1.1G Risk control 1.1H Implementation 1 2 Page 1 1 Conduct Risk Assessment 1.1A Guiding principles of WSH framework 1.1A Guiding principles of WSH framework Workplace Safety Health (WSH) requirement: Risk management : The WSH Act is an essential part of the new framework to cultivate good safety habits in all individuals so as to engender a strong safety culture Risk management is the process of identifying, in our workplace. It requires stakeholders to take evaluating and controlling risks at workplaces. It has reasonably practicable measures to ensure the been mandated under the Workplace Safety and safety and health of workers and other people that Health framework to foster a proactive accident are affected by the work being carried out. prevention culture 3 4 1.1A Guiding principles of WSH framework 1.1A Guiding principles of WSH framework Guiding principles of WSH framework : Component of risk management : a) Reducing risks at source by requiring all stakeholders to Preparation eliminate or minimise the risks they create; Risk Assessment (RA) b) Instilling greater ownership of safety and health outcomes by industry; and Implementation (includes specific communication c) Preventing accidents through higher penalties for poor of the hazards identified and their controls) safety management Record keeping 5 6 Page 2 1 Conduct Risk Assessment 1.1A Guiding principles of WSH framework 1.1B Features of WSH Act Key features of WSH framework : Component of risk assessment : i. it places the responsibility for workplace safety on all stakeholders along lines of control at the workplace; Hazard identification ii. it focuses on Workplace Safety & Health systems and Risk evaluation outcomes, rather than merely on compliance; Risk controls iii. it facilitates effective enforcement through the issuance of remedial orders; iv. it imposes higher penalties for non-compliance and risky 7 8 behaviour. 1.1C WSH Coverage 1.1D Preparation Work 1.1D Formation of Risk Management/ Risk Assessment Teams WSH coverage : 1.1D.1 Appointment of RM Team a) All workplaces, unless exempted by the WSH Act; b) Responsibilities of stakeholders; The Employer shall appoint a RM Team Leader (“RM Leader”) & Appoint RM Team members (“RM Members”). c) Hazardous substances; d) Machinery & equipment. The RM Team shall be responsible for the overall RM direction and RM activities of the Workplace. 9 10 Page 3 1 Conduct Risk Assessment 1.1D Preparation Work 1.1D Preparation Work 1.1D.1 Appointment of RM Team continue… 1.1D.2 RM Team Leader This RM Team can also function as a RA Team. RM Team appointed by the Employer shall: The RM Team Leader should have direct access to the Employer or shall be at least a senior member of the Have a thorough knowledge of the work to be assessed; and Workplace. The RM Team Leader shall be competent for Be multi-disciplinary, diverse with representation from major stake-holders of all the Workplace Operating functions the task. Having attended a RM course conducted by a MOM Approved Training Provider or equivalent is The employer shall ensure that the RM Leader is competent for sufficient demonstration of the fact. The Employer shall the task. Having attended a RM course conducted by a MOM appoint a RM Team Leader (“RM Leader”). Approved Training Provider or equivalent is sufficient demonstration of the fact. 11 12 1.1D Preparation Work 1.1D Preparation Work 1.1D.4 RA (Risk Assessment) Teams 1.1D.3 RM Team Member RA Teams are responsible for conducting RAs within the RM team members may be appointed from scope defined by the RM Team. If an organisation requires management staff, process or facility engineers, only one team, then the functions of the RM and RA teams technical personnel, supervisors, production may be combined within the RM Team. operators, maintenance staff and WSH personnel if available. Teams should have representatives from both the management and non-management levels. 13 14 Page 4 1 Conduct Risk Assessment 1.1D Preparation Work 1.1D Preparation Work 1.1D.4 RA (Risk Assessment) Teams continue… 1.1D.5 Scoping of RA (Risk Assessment) The RA team should include personnel who are involved with Scoping is the step of identifying a convenient unit (or the work, including contractors and suppliers. If available, it should include persons who are familiar with the design and "Boundary") for assessing and controlling risks at the development of the site, machine or process. Workplace. It may be as simple as dividing a Workplace or project into its distinct parts (e.g., divisions, Where RA experience or expertise is lacking, a WSH Officer, departments, functional areas or work activities), and WSH Auditor or Approved Risk Consultant who is trained and then sub-dividing each part into self- contained jobs or has experience in conducting RA should be engaged to assist areas, each representing the unit for the RA. the RM/ RA leader in the conduct of the RA. 15 16 1.1D Preparation Work 1.1D Preparation Work 1.1D.5 Scoping of RA (Risk Assessment) continue… 1.1D.6 Inventory of Work Activity RM Team (the primary team responsible for the overall RM For the identified departments, functional areas and direction and activities of the company) shall determine the work activities to be assessed, the “Inventory of Work boundaries of the RA (e.g., department, functional area or Activities” form should be used. Information to be work activity within the Workplace). included: Department, Activity or Trade Assessed; Risk Assessment for each identified department, functional Location; area or work activity should be scoped to provide focus to Process; and the Assessment. Work activity 17 18 Page 5 1 Conduct Risk Assessment 1.1D Preparation Work 1.1D Preparation Work 1.1D.6 Inventory of Work Activity continue… 1.1D.7 Gathering Information Other information to be included in the form: Once the extent of the RA is determined, relevant information Department or activity to be assessed in “Department, Activity should be gathered. These sources of information may or Trade Assessed”. include, but not limited to: The Location, Process and Work Activity. Workplace layout plan List of Work Activity in sequential steps. Process or work flowchart List of work activities in the process For Trade-based RA: List of chemicals, machinery and/ or tools used State the trade being assessed in “Department, Activity or Records of past incidents and accidents Trade Assessed”. Where the Location or Process is not applicable, state “N/A” in Relevant legislation, CPs or specifications these columns. Observations and interviews 19 20 Complete Work Activity List. WSH Inspection Records 1.1D Preparation Work 1.1D Preparation Work 1.1D.7 Gathering Information continue… Form team Details of existing risk controls Preparation Gather relevant information Identify tasks of each process Health and safety audit reports Hazard identification Feedback from employees, clients, suppliers or other Risk Assessment Risk evaluation stakeholders Risk control SWPs Obtain Employer or Management approval Other information such as safety data sheets (SDS), Implement control measures Implementation Communicate the hazards identified and their controls manufacturer’s instruction manual Audit or regular inspection Copies of any relevant previous Ras Must be available upon request Record-keeping Kept of at least three years Medical condition (e.g., allergy) of workers in the workplace or activity being assessed 21 Review Review RA on regular basis 22 Page 6 1 Conduct Risk Assessment 1.1E Risk Assessment 1.1E Risk Assessment 1.1E Requirement 1.1E Requirement continue… The steps in RA are Hazard Identification, Risk Evaluation As part of a continual review process, this CP recommends that and Risk Control. workplace hazards be reviewed monthly till: The hazard reaches the green zone (“Low Risk”) or When the steps from “Hazard Identification” to “Risk The risks of the hazard are residual in nature (“Residual Risk”); All reasonable practicable measures have been taken to control Control” have been recorded in the RA form for hazard, that hazard. the same steps from “Hazard Identification” to “Risk Control” are to be repeated till all the “Work Activity” The RM Team is to determine which hazards are to be reviewed from the “Inventory of Work Activities” has been monthly. All RA entries must be reviewed and, if necessary, revised assessed. at least once within three years. 23 24 1.1E Risk Assessment 1.1E Risk Assessment 1.1E.1 Hazard Identification 1.1E.1.1 Process Hazard Identification The RA Team Leader is to determine the most List the “Work Activity” from the “Inventory of Work appropriate way(s) of identifying the hazards. These may Activities” (see attached form) in the “Risk Assessment include brainstorming, systematic process reviews, Form” (See attached) Process Hazard Analysis and Job Observations and Job Identify the hazard and record it in the “Hazard” Safety Analysis (JSA). When identifying hazards, the RA Should there be more than one hazard for the work Team is to consider if the hazards could cause harm activities, different hazards should be recorded in beyond their immediate area of the work. separate lines. 25 26 Page 7 1 Conduct Risk Assessment 1.1E Risk Assessment 1.1F Risk Evaluation 1.1E.1.1 Process Hazard Identification continue… Various Risk Evaluation methods and matrices The following categories of hazards should be considered: practiced and preferred by workplaces. When o Physical (e.g., fire, noise, ergonomics, heat, radiation and Hazard Identification is complete, proceed with manual handling) Risk Evaluation procedure. The choice of matrices, o Mechanical (e.g., moving parts, rotating parts) the numeric 5x5 Risk Matrix is recommended. o Electrical (e.g., voltage, current, static charge, magnetic fields) Adoption of Trade based Risk assessment or Activity o Chemical (e.g., flammables, toxics, corrosives, reactive materials) based Risk Assessment while computing Risk, o Biological (e.g., blood-borne pathogens, virus) likelihood and severity of the hazards are to be o Others (e.g., hazards peculiar to the industry) 27 evaluated. 28 1.1F Risk Evaluation 1.1F Risk Evaluation Common standard matrix is as shown Common standard matrix is as shown continue… 29 30 Page 8 1 Conduct Risk Assessment 1.1F Risk Evaluation 1.1G Risk Control Based on the severity and likelihood identified for hazards, Risk Compare the existing controls against the Hierarchy of Control When then can be computed using the following table considering additional measures to reduce risk, the more effective measures in the Hierarchy of Control should be considered first. When Additional Control(s) have been decided, re-rate the Severity, Likelihood and RPN scores and record them in the “S”, “L” and “RPN” columns in the “Risk Control” section. The new risk control RPN shall not be HIGHER than the Risk Evaluation RPN. Preferably, the revised RPN should be within the Low Risk (Green) zone. However, an improvement in RPN is acceptable provided it is not within the High Risk (Red) zone. 31 32 1.1H Implementation 1.1H Implementation 1H.1 Communication A specific person should be identified to lead the Completed RA forms must be approved by the Manager of the area, implementation of the Additional Controls. The person’s function or activity where the risk is being assessed. While various forms and levels of communication are to take place throughout the name is to be recorded in the “Implementation Person” RM process, the specific communication of the hazards identified and column. The due-date for implementation is to be recorded their controls to the persons performing the activity. The Manager in the “due-date” column. The Implementation Person is to who oversees the area, function or activity where the WSH risks exist provide progress updates to the RA Team on a periodic shall ensure that all persons exposed to the risks are informed of: basis as determined by the RA Team Leader. The nature of risks; Any measures or SWP implemented; and The means to minimize or eliminate the risks. 33 34 Page 9 1 Conduct Risk Assessment 1.1H Implementation 1.2 Hazard Identification 1H.2 Record Keeping 1.2A Method of identification The Manager shall assist the employer to ensure that RA 1.2B Unsafe work condition records, including but not limited to RA forms and control measure records, are kept for at least three years. The 1.2C Unsafe work practices Manager shall assist the employer to ensure that the Risk Register is readily available for review by designated persons at the workplace and by regulatory agencies. 35 36 1.2A Method of identification 1.2A Method of identification Process of Hazard Identification The RA Team Leader is to determine the most appropriate 1. List the “Work Activity” from the “Inventory of Work way(s) of identifying the hazards. These may include Activities” (as in RA form) in the “Risk Assessment brainstorming, systematic process reviews, Process Hazard Form” (as in RA form) Analysis and Job Observations and Job Safety Analysis (JSA). 2. Identify the hazard and record it in the “Hazard” 3. Should there be more than one hazard for the work When identifying hazards, the RA Team is to consider if the activities, different hazards should be recorded in hazards could cause harm beyond their immediate area of separate lines. the work. 37 38 Page 10 1 Conduct Risk Assessment 1.2A Method of identification 1.2A Method of identification Process of Hazard Identification Process of Hazard Identification 4. The following categories of hazards should be considered: 4. The following categories of hazards should be 4.1 Physical (e.g., fire, noise, ergonomics, heat, radiation considered: and manual handling) 4.4 Chemical (e.g., flammables, toxics, 4.2 Mechanical (e.g., moving parts, rotating parts) corrosives, reactive materials) 4.3 Electrical (e.g., voltage, current, static charge, 4.5 Biological (e.g., blood-borne pathogens, virus) magnetic fields) 4.6 Others (e.g., hazards peculiar to the industry) 39 40 1.2B Unsafe work condition 1.2B Unsafe work condition Under the WSH Act Unsafe Condition Employees have a duty to keep his/her workplace 1. No access to extinguisher and colleagues safe Fire extinguishers are to be made available and Employers are required to ensure the safety and serviced regularly. The access to the fire health of everyone including non-employees visiting extinguisher and hose reel should not be blocked. the workplace. Suitable number of fire extinguishers is to be made available. No access to extinguisher is a Employers should maintain a safe work environment violation under fire safety act. 41 42 Page 11 1 Conduct Risk Assessment 1.2B Unsafe work condition 1.2B Unsafe work condition Unsafe Condition Unsafe Condition 2. Excessive Noise 2. Excessive Noise Workplace noise hazard is excessive noise generated by If you have to raise your voice when talking to a person work activities such as machineries, operations and who is 1 m away from you, the noise level is likely to be processes. Typical high noise works include hacking, above 85 dBA. use of pneumatic blower, grinding, compressor and Short, infrequent exposures to loud noise can cause generator. temporary hearing loss. Excessive noise is defined as an equivalent sound Prolonged exposures to excessive noise can cause pressure level of 85 dBA or more over an 8-hr work day. permanent hearing loss/noise-induced deafness (NID) 43 44 which is irreversible 1.2B Unsafe work condition 1.2B Unsafe work condition Unsafe Condition Unsafe Condition 3. Water on Floor 4. Defective Ladder A queen ladder is an A-frame ladder with extended stiles Slippery work surfaces are wet, oily, dusty or that form a barrier around the front half of the top plate. glazed). Wet surface causes slippery and This allows for an effective handhold. potential for slip and fall. Stepping onto the horizontal part of the extended portion to gain additional height is unsafe and must not be done. However, improper or unsafe use of ladders have resulted in falls and contributed to work fatalities and injuries. 45 46 Page 12 1 Conduct Risk Assessment 1.2B Unsafe work condition 1.2B Unsafe work condition Unsafe Condition Unsafe Condition 4. Defective Ladder 5. Missing Safety Devices Ensure that the ladder rests or bears upon surfaces that are Safety Devices include those devices that are meant for stable, level and firm. Ladders are often used in the the protection from harm. Typical safety devices include workplace as an equipment to gain access to higher areas. Guards, Interlocks, Black boxes in Cranes, EMO button in machines. Removing or altering these devices is serious crimes. 47 48 1.2B Unsafe work condition 1.2C Unsafe work practices Unsafe Condition Under the Risk Management of WSH Regulation, when it is 6. Poor Housekeeping not reasonably practicable to eliminate risk, Safe Work Poor Housekeeping leads to trip, slips and falls, fire, pest Procedures are developed and implemented such that there breeding. is a reasonably practicable measures to minimise the risk Recognition and prompt correction of housekeeping and to control the risk. hazards is imperative to fire safety efforts. "Safe work procedure" means any procedure developed to Typical housekeeping issues involve thrash, food waste, carry out work safely. This includes any procedure which is oil/water/chemicals, stocks, welding and cutting materials to be taken to protect the safety and health of persons in not stored in its appropriate locations. the event of an emergency. 49 50 Page 13 1 Conduct Risk Assessment 1.2C Unsafe work practices 1.2C Unsafe work practices 1. Not Following Procedures Although most accidents are preventable, Unsafe Work Practices and Acts contribute to a sizeable number. Consequence of not following safe work practice can leads to accidents. It is the duty of the employee to follow safe work Example of an accident, a grinder was used to cut open practices and employer needs to take all reasonably the cover of a machine to replace its internal parts. practical measures to reduce the risk. Some of the During the cutting, a flash fire occurred, causing the unsafe work practices include employees not following cover of the machine to be blown off the machine. Main procedures, workplace not having procedures etc. cause – employee not following safe work practices 51 52 1.2C Unsafe work practices 1.2C Unsafe work practices 1. Not Following Procedures 1. Not Following Procedures A procedure is a step-by-step process for performing A safe work practice is a set of guidelines to help workers a task safely from beginning to end. perform a task that may not require a step-by-step procedure. Example: To reflect real life in the workplace, employees/ Not securing the guard before turning on a machine workers who actually do the job must be involved in Leaving large boxes in the way of staff in a corridor, or in developing the practices and procedures. front of the fire exit Trailing an electrical extension cord across the workspace Having written safe work practices and procedures is Not wearing a hard hat on a construction site. an essential component of an WSH-MS program. 53 54 Page 14 1 Conduct Risk Assessment 1.2C Unsafe work practices 1.2C Unsafe work practices 2. Unsafe Procedures 2. Unsafe Procedures Having the correct procedure is important. If the procedures are wrongly written, employees will Common Unsafe Work Practices are practices which follow unsafe practice and there is a potential for are prohibited during rehabilitation, maintenance, incidents or hazards paint stabilization and hazard reduction. 55 56 1.2C Unsafe work practices 1.2C Unsafe work practices 2. Unsafe Procedures 2. Unsafe Procedures Example, 24CFR 35.140 US-OSHA, Prohibited methods of paint removal. d. Heat guns operating above 1100 degrees Fahrenheit or charring the paint. The following methods shall not be used to remove paint that e. Dry sanding or dry scraping, except dry scraping in is, or may be, lead-based paint: conjunction with heat guns or within 1.0 ft. (0.30 m.) of a. Open flame burning or torching. electrical outlets, or when treating defective paint spots b. Machine sanding or grinding without a high-efficiency totalling no more than 2 sq. ft. (0.2 sq. m.) in any particulate air (HEPA) local exhaust control. one interior room or space, or totalling no more than 20 c. Abrasive blasting or sandblasting without HEPA local sq. ft. (2.0 sq. m.) on exterior surfaces. 57 58 exhaust control. Page 15 1 Conduct Risk Assessment 1.2C Unsafe work practices 1.2C Unsafe work practices 2. Unsafe Procedures 3. Coexistence of incompatible substances f. Paint stripping in a poorly ventilated space using a Incompatible refers to not suitable to be together. Co- volatile stripper that is a hazardous substance in existence of incompatible chemicals cases reaction, generation accordance with regulations of the Consumer Product of heat etc. Incompatible chemicals give an undesired chemical reaction Safety Commission at 16 CFR 1500.3, and/or a when mixed. This usually refers to substances that will react to hazardous chemical in accordance with the cause an imminent threat to health and safety through an Occupational Safety and Health Administration explosion, fire, and/or formation of toxic materials. The term regulations at 29 CFR 1910.1200 or 1926.59, as can also refer to an unwanted change in the physical or applicable to the work. 59 mechanical properties of the materials. 60 1.2C Unsafe work practices 1.2C Unsafe work practices 3. Coexistence of incompatible substances 3. Coexistence of incompatible substances Another examples of incompatibilities, the reaction of For example, in industry, a containers of bleach will alkali metals such as sodium or potassium metal with have a warning not to mix bleach and ammonia. water. In this case, the products are basic sodium or When mixed, these substances generate the toxic potassium hydroxide (which is corrosive), hydrogen gas gases chloramine (NH2Cl) and hydrazine (N2H4), (which is explosive) and a lot of heat (an exothermic which could cause serious injuries or death! reaction). The heat generated is so great that the hydrogen generated will usually ignite! 61 62 Page 16 1 Conduct Risk Assessment 1.2C Unsafe work practices 1.2C Unsafe work practices 3. Coexistence of incompatible substances 4. Unauthorized Operation Another examples of incompatibilities; There are many operations that requires authorisation. Improper storage and disposal of incompatible chemicals has Mandatory Permit to work system to be deployed for led to a number of accidents. all high risk activities like: Excavations Always properly identify and segregate chemicals and wastes to avoid the accidental mixing of incompatibles. Crane operations Lifting operations For example, Confined Space entry Do not store acids and bases in the same cabinet. Hot work and Do not store acid waste and organic waste in the same area. 63 64 Modification to life safety systems 1.2C Unsafe work practices 1.2C Unsafe work practices 5. Operation by Untrained Personnel 4. Unauthorized Operation Only authorised persons should be deployed for a Unauthorized operation leads to incidents and task. Ensure competent persons to carry out specific potential loss in productivity. task example like lifting. Only trained personnel are allowed to operate. Operations by untrained persons can lead to: Accidents Often the hazards are due untrained / unqualified Delayed productivity persons Confusion 65 Stress 66 Page 17 1 Conduct Risk Assessment 1.2C Unsafe work practices 1.3 Evaluate Risk Level of hazards 5. Operation by Untrained Personnel Competency and training requirements are spelt in WSHA. Employers are required to ensure that employees of all 1.3A Review of existing risk control measures levels i.e. workers, supervisors, managers, and WSH Personnel possess basic Workplace Safety and Health (WSH) 1.3B Evaluating risk level base on severity and competencies. likelihood of hazards As a minimum, workers are to be trained in safety orientation course, work at heights etc. Further, a training need analysis should be developed to ensure competencies are well managed 67 68 1.3A Reviewing of existing risk control measures 1.3A Reviewing of existing risk control measures The risk assessment should consider a range of a) identification or clarification of existing and potential control measures and provide a basis for the selection control measure options; b) evaluation of effects of control measures on risk levels; of control measures. The risk assessment process c) basis for selection or rejection of control measures and should provide the following in relation to control the associated justification of adequacy; and measures: d) basis for defining performance indicators for selected control measures 69 70 Page 18 1 Conduct Risk Assessment 1.3A Reviewing of existing risk control measures 1.3B Severity and likelihood of hazards Risk control measures that have been implemented and Severity of hazard are still effective in controlling the hazard is usually Level Severity Description 5 Catastrophic Death, fatal diseases or multiple major injuries. termed as existing control measures. The range of Serious injuries or life-threatening occupational diseases control measures that should be considered in the risk 4 Major (includes amputations, major fractures, multiple injuries, occupational cancers, acute poisoning, disabilities assessment and should evaluate the range of control and deafness, work-related upper limb disorders). measures in terms of viability and effectiveness to Moderate Injury or ill-health requiring medical treatment (includes 3 lacerations, burns, sprains, minor fractures, dermatitis and provide a basis for selection or rejection of each control work-related upper limb disorders). measure. Injury or ill-health requiring first-aid only (includes minor 2 Minor cuts and bruises, irritation, ill-health with temporary Examples of existing Risk Control Measures are: discomfort). 71 1 Negligible Negligible injury. 72 Safe Work Procedure, PPE, Training and Permits 1.3B Severity and likelihood of hazards 1.3B Severity and likelihood of hazards Likelihood of hazard Evaluating risk level based on severity and likelihood Level Likelihood Description Risk Prioritization Number (RPN) = Severity x Likelihood 5 Almost Certain Continual or repeating experience. Risk Prioritisation Number Likelihood Almost Rare Remote Occasional Frequent Certain Severity (1) (2) (3) (4) 4 Frequent Common occurrence. (5) Catastrophic 5 10 15 20 25 (5) 3 Occasional Possible or known to occur. Major (4) 4 8 12 16 20 2 Remote Not likely to occur under normal circumstances. Moderate (3) 3 6 9 12 15 Minor (2) 2 4 6 8 10 1 Rare Not expected to occur but still possible. 73 Negligible (1) 1 2 3 4 5 74 Page 19 1 Conduct Risk Assessment 1.3B Severity and likelihood of hazards 1.3B Severity and likelihood of hazards Assessing the existing and residual risks Assessing the existing and residual risks Risk Level Acceptability Recommended Actions of Risk Low Risk Acceptable - No additional risk control measures may be needed. After computing the risk levels for the workplace, it - Frequent review may be needed. is important to assess the levels. Risk levels for the Medium Tolerable - Risk level is reduced to as low as is practicable within a defined time Risk period. hazard in the yellow zone is “Medium Risk”, the - Interim risk control measures, such as administrative controls, may be implemented. hazard is in the green zone is Low Risk while the - Management attention is required. High Risk Unacceptable - High Risk level must be reduced to at least Medium Risk before work red zone indicates high risk. Additional control commences. - There should not be any interim risk control measures and risk measures are required to reduce the risk levels. control measures should not be overly dependent on personal protective equipment or appliances. If need be, the hazard should be Following table serve as guide in deciding on the eliminated before work commences. - Immediate management intervention is required before work 75 acceptability of risk. 76 commences. 1.3B Severity and likelihood of hazards 1.4 Hierarchy of control Measure Assessing the existing and residual risks Hierarchy of control measures is adopted to reduce Once all the risk controls are selected and their the risk levels. In determining the control measures, it residual risks highlighted, the RA Team needs to is often preferred to consider additional control identify the action officers and follow-up dates. measures in the order of hierarchy: In this way, the specific action officers to implement Elimination the controls can be clearly identified, and the Substitution follow-up dates will help to ensure timeliness in Engineering Control implementation. Administrative Control PPE 77 78 Page 20 1 Conduct Risk Assessment 1.4 Hierarchy of control Measure 1.4 Hierarchy of control Measure Elimination Elimination of risk refers to the total removal of the worker’s exposure to the hazards, effectively making all the identified possible accidents, incidents and ill health impossible. This should be attempted first as recommended in the hierarchy, and is a permanent solution. By definition, eliminating the hazard means physically removing it. It is the most effective hazard/risk control For example, if employees must work high above the ground, the hazard can be eliminated by moving the piece they are working on to ground level to eliminate the need to work at heights, using robots to replace humans to eliminate the danger of working in confined space 79 80 1.4 Hierarchy of control Measure 1.4 Hierarchy of control Measure Substitution Engineering Control This involves substituting a process or a product with a less hazardous process or product to mitigate the risk. Substitution, the These do not eliminate hazards, but rather isolate people second most effective hazard control, involves replacing something from hazards. Capital costs of engineered controls tend to that produces a hazard (similar to elimination) with something that does not produce a hazard. be higher than less effective controls in the hierarchy, however they may reduce future costs. Engineering controls For example, replacing lead based paint with acrylic paint. To be an are physical means that serve the workforce by reducing the effective control, the new product must not produce another likelihood of occurrence or severity of consequence of the hazard. Because airborne dust can be hazardous, if a product can mishap. be purchased with a larger particle size, the smaller product may effectively be substituted with the larger product 81 82 Page 21 1 Conduct Risk Assessment 1.4 Hierarchy of control Measure 1.4 Hierarchy of control Measure Engineering Control Administrative Control For example, a crew might build a work platform rather than Administrative controls are changes to the way people work. purchase, replace, and maintain fall arrest equipment. "Enclosure Examples of administrative controls include procedure changes, and isolation" creates a physical barrier between personnel and employee training, and installation of signs and warning labels hazards, such as using remotely controlled equipment. Fume (such as those in the Workplace Hazardous Materials hoods can remove airborne contaminants as a means of Information System).Administrative controls do not remove engineered control. Other examples include structural changes to hazards, but limit or prevent people's exposure to the hazards, the work environment or work processes, erecting a barrier to such as completing road construction at night when fewer interrupt the accident transmission path between the worker and people are driving. Documentation should emphasize all the the hazard (for example, machine guards, interlocks, and steps to be taken and the controls to be used in carrying out the 83 84 confined space ventilation). activity safely. 1.4 Hierarchy of control Measure 1.4 Hierarchy of control Measure Administrative Control Personal Protective Equipment For example, Permit-to-work systems, scheduling of Personal protective equipment (PPE) includes gloves, respirators, hard hats, safety glasses, high-visibility clothing, incompatible works, SWPs, Alarms, Buddy System and safety footwear. PPE is the least effective means of and Warning Labels. controlling hazards because of the high potential for damage to render PPE ineffective. Additionally, some PPE, such as respirators, increase physiological effort to complete a task and, therefore, may require medical examinations to ensure workers can use the PPE without risking their health. 85 86 Page 22 1 Conduct Risk Assessment 1.5 Implementing control process 1.5A Briefing & disseminating control processes Manager and RA Team Leader shall ensure employees are aware of the Risk Control Measures taken. 1.5A Briefing and disseminating control processes Briefing is to be carried out to affected employees of the nature of risk faced by the employee and a record of the briefing is to be maintained by 1.5B Implementation RATeam leader. While various forms and levels of communication are to take place 1.5C Report on status of implementation throughout the RM process, and require the specific communication of the hazards identified and their controls to the persons performing the activity. 1.5D Monitor effectiveness of control measures The Manager who oversees the area, function or activity where the WSH risks exist shall ensure that all persons exposed to the risks are informed of: 1.5E Review of control measures The nature of risks; Any measures or SWP implemented; and 1.5F Keeping and updating records 87 The means to minimize or eliminate the risks. 88 1.5B Implementation 1.5B Implementation As far as is practicable, the Manager is to implement the recommended risk control measures as soon as possible. The The Manager shall ensure that the plan is monitored Manager shall ensure that an action plan is prepared to regularly until all the measures are implemented. The implement the measures. Manager shall ensure that all persons exposed to the risks are informed of the nature of risks; and Any The plan should include a time line of implementation and responsible persons implementing the safety and health control additional control measures or SWP implemented. The measures. Manager shall ensure that regular inspections and process audits are carried out to ensure that risk control The Manager should provide adequate resources for the measures have been implemented and are functioning implementation of the RA plan with additional control measures The resources are to be evaluated against the risk levels 89 effectively. 90 Page 23 1 Conduct Risk Assessment 1.5C Report on status of implementation 1.5D Monitor effectiveness of control measures Additional Control Measures implemented should be reviewed Wherever there is an additional control measures periodically. The effectiveness of the control measure should be identified, Responsible Person and date of implementation evaluated and reviewed as whether the inherent risk has been to be identified. Implementation responsible Person shall reduced. report to the Manager, RA Team leader and employer on the status of implementing the control measures. Any additional control measures that has not been able to reduce the risk should be reviewed and revised with a new Should there be any change in the implementation implementation schedule. schedule; the RA leader shall notify Manager and The Manager shall ensure that regular inspections and process Employer. audits are carried out to ensure that risk control measures have 91 92 been implemented and are functioning effectively. 1.5E Review of control measures 1.5F Keeping and updating records Implementation schedule shall be reviewed periodically The Manager shall assist the employer to ensure that RA records, by the Manager and the RA team leader. including but not limited to RA forms and control measure records, are kept for at least three years. Resources committed for implementing control measures The Risk Register should be readily available for review by shall be reviewed by Manager and RA Team Leader. designated persons at the workplace and by regulatory agencies. Update the Risk Registry including additional control measures, Adjustments to the control measures shall be done upon safe work practices, communication records and trainings as mutual confirmation from all parties. when the changes occur or after an incident has happened. 93 94 Page 24 1 Conduct Risk Assessment 2. Implement risk management plan & control 2.1 Coordinate WSH management programme 2.1 Coordinate WSH Management Programme 2.1A Risk management programme 2.1B Hazardous chemical management programme 2.2 Coordinate WSH training 2.1C Contractor management programme 2.3 Coordinate management review 2.1D Coordinate WSH management system and programme 2.4 Legal compliance for WSH management system 2.1E Documentation of roles and responsibilities 2.1F Coordinate consultation process with stakeholders 2.1G Resource requirement for WSH management system and programme 1 2 Page 25 2.1A Risk management programme 2.1A Risk management programme 2 Implement risk management plan and controls Risk management programme Risk management programme is a process of identification of hazard, evaluation (i) Preparation of risk and implementing control measures, appointing the responsible At preparation stage, consideration on job scope, person and timeframe and then evaluating the effectiveness of the control layout and hazards of the jobsite. This information measures. shall be collected by the appointed Risk The main components of RM are: Assessment team and this team will determine the (i) Preparation extent of the RA. (ii) Risk Assessment (RA) (iii) Implementation (includes specific communication of the hazards identified and their controls) (iv) Record-keeping. 3 4 2.1A Risk management programme 2.1A Risk management programme (ii) RA (iii) Implementation Risk assessment should be conducted by a multidisciplinary team who Upon RA completion, the document will be endorsed by top management have a thorough knowledge of the works. The risk assessment team for the implementation action. Upon completion of implementation, should include contractors/suppliers personnel who are involved with the communication had to be done. work, whenever necessary. Implementation person should be have gone through RA training and The team leader should have undergone training in risk assessment. familiar with the hierarchy of control and have authority to implement the Alternatively, a safety consultant trained and has experience in job safety approved proposed actions. analysis and risk management could be engaged to assist in the conduct Once the implementation is done, the corrective & preventive measure of risk assessment. should be evaluated for the effectiveness of the implemented action. Team members should include management staff, process or facility Residual risk if left unattended should be communicated to all personnel engineers, technical personnel, supervisors, production operators, related to the work activities directly or indirectly. maintenance staff and safety personnel if available. 5 6 Page 26 2.1A Risk management programme 2.1B Hazardous chemical management programme 2 Implement risk management plan and controls (iv) Record-keeping MHCP The person in charge of the RM programme should The Management of Hazardous Chemicals Programme (MHCP) is to prevent and control chemical hazards at workplace, and ensure that RA records, including but not limited to RA safeguard the health and safety of persons against chemical forms and control measure records, are kept for at hazards within the workplace. least three years and Risk Register is readily The Management of Hazardous Chemicals Programme available for review by designated persons at the enhances chemical safety and prevents chemical-related workplace and by regulatory agencies. injuries, illnesses or diseases at the workplace. 7 8 2.1B Hazardous chemical management programme 2.1B Hazardous chemical management programme Key elements of MHCP MHCP (Management) 1. Policy & strategy 2. Selection & procurement 3. Register and Safety Data Sheet Management to have a policy statement stating support and 4. Labelling and Warning Signs commitment from top management to ensure the safe use of chemicals, 5. Storage and Transportation and the protection of employees against chemical hazards and a broad 6. Risk assessments and control strategy on managing hazardous chemicals. 7. Safe work procedures and Personal Protective Equipment 8. Workplace Monitoring and Surveillance Formulate emergency plan in respond to chemical accidents such as 9. Information and Training fires, explosions, spills, leaks or release of hazardous chemicals. First 10. Emergency planning & first-aid aid considerations to ensure that provisions for emergency treatment of 11. Waste disposal chemical poisoning or excessive exposure including facilities, first aider 12. Contract work (where applicable) and first aid treatment. 13. Programme review & audit 9 10 Page 27 2.1B Hazardous chemical management programme 2.1B Hazardous chemical management programme 2 Implement risk management plan and controls MHCP (Documentation) MHCP (Management) The organisation should keep an updated list of chemicals along with information such as Management shall ensure that a risk assessment (RA) is conducted for any work involving any hazardous chemical. SDS (Safety Data Sheet) Inventory (amount stored) Management should conduct annual review / audit of MHCP Supplier of chemical to ensure that it is relevant and up-to-dated. Location of the chemicals Name of persons who are at risk or liable to be exposed to 11 the chemicals 12 2.1B Hazardous chemical management programme 2.1B Hazardous chemical management programme MHCP (Operation) MHCP (Training) Develop a decision process on which chemical to buy or bring in at workplace by reviewing the SDS, consider properties such as: flash point, toxicity, health effects, permissible exposure level of the Workers should be trained to: chemical and Global Harmonised System (GHS) Hazard category. understand the information in SDS and on the labels Safe work procedures shall be developed covering the activities such as: follow safe handling procedures such that they dispensing, transferring, using and disposing of the hazardous chemicals. Safety and health precautions need to be taken in the course understand the risks of exposure of work, and the use of personal protective appliances. know of ways to protect themselves and proper use PPE should be properly selected, correctly used or comfortably fitted and of PPE. regularly maintained to ensure effective protection against the chemicals. 13 14 Page 28 2.1B Hazardous chemical management programme 2.1B Hazardous chemical management programme 2 Implement risk management plan and controls MHCP (Storage - labelling) MHCP (Operation- storage) Prior to storage, areas of consideration: All packaged containers of hazardous chemical should i. properties of the chemicals be labelled. ii. any form of incompatibility iii. quantity amount permissible to store Warning signs or notices should be: iv. operational and environmental condition. (i) prominently displayed at areas where such Atmosphere in which toxic substances are given off shall be tested by a competent substances are used or handled, person at sufficient intervals. Exposure to toxic substances shall be within the PEL. (ii) specifying the nature of the danger of the hazardous chemical The relevant information can include in the transport documents, and by 15 placing or sticking placards on the transport units i.e. vehicles and containers. 16 2.1B Hazardous chemical management programme 2.1C Contractor management programme MHCP (Operation- waste storage) CMP (Contractor management programme) Waste labelling shall be done as per local or international standards. Contractor management programme outlines the requirements for Proper waste transport and disposal facilities, e.g. by licensed or toxic waste collectors shall be adopted. evaluating, selecting, coordinating, monitoring and communicating WSH expectations of contractors. It is a systematic contractor management process aiming to minimize safety and health risk to employees and general public. 17 18 Page 29 2.1C Contractor management programme 2.1C Contractor management programme 2 Implement risk management plan and controls Key elements of CMP (Contractor management programme) Key elements of CMP (Contractor management programme) a. Roles and Responsibilities i. Clients d. Project Implementation ii. Contractors i. Work Communication and Coordination ii. Information and Training b. Project Contracting iii. Management and Supervision i. Contractor Selection and Evaluation iv. Monitoring and Review ii. WSH Requirements in Contract c. Project Prerequisites e. Project Completion i. Pre-Work Coordination i. Post Contract Review ii. WSH Induction 19 f. RM Capability Building 20 iii. Risk Assessment 2.1D Coordinate WSH management system and 2.1E Documentation of roles and responsibilities programme Coordination among various stakeholders and implemented programme are necessary for the success of any system and Documentation of roles and responsibilities for every programme. Once WSH management system and programme individual at the workplace is necessary. Generally at are identified, consideration should be given to present the the workplace, each individual have some roles to play proposal to stakeholders. Stakeholders should be consulted on and assign the responsibilities. WSH roles, the key items such as objectives of the proposals, responsibilities and authorities of line management implementation plan, budget and resources. Priorities of the stakeholders need to be known and taken into consideration personnel are generally spelled out in safety policy. before the proposals by means of coordination. 21 22 Page 30 2.1E Documentation of roles and responsibilities 2.1E Documentation of roles and responsibilities 2 Implement risk management plan and controls Top management or its representative shall be appointed to overlook the Individual area of responsibilities to be spelled out: implementation of WSH management system and its programme. 1. Implement all Company's Environmental, health & safety The following line personnel roles, duties and responsibility are spelled management system, programme and procedures out: 1. Project director/General manager 2. Review and update the Company's EHS policy and other related 2. Project manager/Plant manager duties. 3. Site manager/Maintenance manager 3. Ensure the RA is carried out for all work activities, Safe Work Practices 4. Project engineer/Plant engineer are developed and followed & PTW system is developed, 5. WSH officer implemented and adhered to. 6. WSH coordinator 4. Investigate Incidents and enforce preventive measures. 7. WSH Representative 5. Implement WSH management programme and monitor the effect. 8. Site supervisor/Plant supervisor 6. Review OSH (Occupational Safety & Health) objectives and targets. 9. Site foreman 7. Implement emergency preparedness and response plan. 23 24 10. Safety and health committee member 2.1E Documentation of roles and responsibilities 2.1F Coordinate consultation process with stakeholders The assigned roles and WSH responsibilities should be effectively communicated to all the stakeholders whom they affect at all level. This should ensure that the stakeholders understand the scope and the interfaces between the various Consultation, is a process where stakeholders input on function. Communication to the stakeholders on roles, WSH responsibilities and matters affecting them is discussed and group awareness authorities may include: 1. One to one session. This is a briefing conducted by the superiors on one and understanding increase thus improving the efficiency, to one basis. transparency and involvement. Through the consultation 2. Description in appointment letter, spelling out the roles and responsibility. The letter is given to the employee when he joins the company and is different types of safety and health management acknowledged by the employee on his acceptance. programme are made known to stakeholders. 3. Site Job descriptions. Job description is given to the employee during the joining the company stating their role and responsibilities. 25 26 Page 31 2.1F Coordinate consultation process with 2.1G Resource requirement for WSH management stakeholders system and programme 2 Implement risk management plan and controls Consultation may take the form of: Resources need to be analysed before proposing and Employer/employee group committees implementing WSH management system. Resources need to Regular staff meetings with employees be considered are: Regular written communications such newsletters 1. Human resource One to one session 2. Budget 3. Material Site coordination meetings 4. Machines and equipment Feedback sessions on WSH management system 5. Trained operation and supervisory staff Surveys 6. Effect of production and progress