Refrigeration and Air Conditioning Technician PDF
Document Details
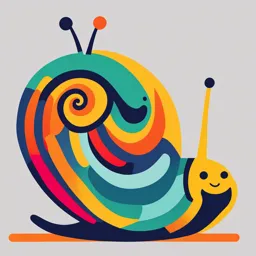
Uploaded by SupportiveSpruce
National Instructional Media Institute, Chennai
2020
null
null
Tags
Summary
This document is a training manual for Refrigeration and Air Conditioning Technicians at the National Instructional Media Institute, Chennai, India. It covers the trade theory for the 1st year of the NSQF Level 5 program in Capital Goods and Manufacturing.
Full Transcript
Refrigeration and Air Conditioning Technician NSQF LEVEL - 5 1st Year (Volume II of II) TRADE THEORY SECTOR: Capital Goods and Manufacturing DIRECTORATE GENERAL OF TRAINING MINISTRY OF SKILL DEVELOPMENT & ENTR...
Refrigeration and Air Conditioning Technician NSQF LEVEL - 5 1st Year (Volume II of II) TRADE THEORY SECTOR: Capital Goods and Manufacturing DIRECTORATE GENERAL OF TRAINING MINISTRY OF SKILL DEVELOPMENT & ENTREPRENEURSHIP GOVERNMENT OF INDIA NATIONAL INSTRUCTIONAL MEDIA INSTITUTE, CHENNAI Post Box No. 3142, CTI Campus, Guindy, Chennai - 600 032 (i) Sector : Capital Goods and Manufacturing Duration : 2 Years Trade : Refrigeration and Air Conditioning Technician - 1st year (Volume II of II) Trade Theory NSQF (Level - 5) Developed & Printed by National Instructional Media Institute Post Box No.3142 Guindy, Chennai - 600032 INDIA Email: [email protected] Website: www.nimi.gov.in Copyright © 2020 National Instructional Media Institute, Chennai First Edition : December 2020 Copies :1000 Rs.275/- (ii) FOREWORD The Government of India has set an ambitious target of imparting skills to 30 crores people, one out of every four Indians, by 2020 to help them secure jobs as part of the National Skills Development Policy. Industrial Training Institutes (ITIs) play a vital role in this process especially in terms of providing skilled manpower. Keeping this in mind, and for providing the current industry relevant skill training to Trainees, ITI syllabus has been recently updated with the help of Mentor Councils comprising various stakeholder's viz. Industries, Entrepreneurs, Academicians and representatives from ITIs. The National Instructional Media Institute (NIMI), Chennai, an autonomous body under Ministry of Skill Development & Entrepreneurship is entrusted with developing producing and disseminating Instructional Media Packages (IMPs) required for ITIs and other related institutions. The institute has now come up with instructional material to suit the revised curriculum for R&ACT 1st Year (Volume II of II) Trade Theory NSQF Level - 5 in Capital Goods & Manufacturing Sector under annual pattern. The NSQF Level - 5 Trade Theory will help the trainees to get an international equivalency standard where their skill proficiency and competency will be duly recognized across the globe and this will also increase the scope of recognition of prior learning. NSQF Level - 5 trainees will also get the opportunities to promote life long learning and skill development. I have no doubt that with NSQF Level - 5 the trainers and trainees of ITIs, and all stakeholders will derive maximum benefits from these IMPs and that NIMI's effort will go a long way in improving the quality of Vocational training in the country. The Executive Director & Staff of NIMI and members of Media Development Committee deserve appreciation for their contribution in bringing out this publication. Jai Hind Director General/ Addl.Secretary Ministry of Skill Development & Entrepreneurship, Government of India. New Delhi - 110 001 (iii) PREFACE The National Instructional Media Institute (NIMI) was established in 1986 at Chennai by then Directorate General of Employment and Training (D.G.E & T), Ministry of Labour and Employment, (now under Ministry of Skill Development and Entrepreneurship) Government of India, with technical assistance from the Govt. of the Federal Republic of Germany. The prime objective of this institute is to develop and provide instructional materials for various trades as per the prescribed syllabi under the Craftsman and Apprenticeship Training Schemes. The instructional materials are created keeping in mind, the main objective of Vocational Training under NCVT/NAC in India, which is to help an individual to master skills to do a job. The instructional materials are generated in the form of Instructional Media Packages (IMPs). An IMP consists of Theory book, Practical book, Test and Assignment book, Instructor Guide, Audio Visual Aid (Wall charts and Transparencies) and other support materials. The trade practical book consists of series of exercises to be completed by the trainees in the workshop. These exercises are designed to ensure that all the skills in the prescribed syllabus are covered. The trade theory book provides related theoretical knowledge required to enable the trainee to do a job. The test and assignments will enable the instructor to give assignments for the evaluation of the performance of a trainee. The wall charts and transparencies are unique, as they not only help the instructor to effectively present a topic but also help him to assess the trainee's understanding. The instructor guide enables the instructor to plan his schedule of instruction, plan the raw material requirements, day to day lessons and demonstrations. In order to perform the skills in a productive manner instructional videos are embedded in QR code of the exercise in this instructional material so as to integrate the skill learning with the procedural practical steps given in the exercise. The instructional videos will improve the quality of standard on practical training and will motivate the trainees to focus and perform the skill seamlessly. IMPs also deals with the complex skills required to be developed for effective team work. Necessary care has also been taken to include important skill areas of allied trades as prescribed in the syllabus. The availability of a complete Instructional Media Package in an institute helps both the trainer and management to impart effective training. The IMPs are the outcome of collective efforts of the staff members of NIMI and the members of the Media Development Committees specially drawn from Public and Private sector industries, various training institutes under the Directorate General of Training (DGT), Government and Private ITIs. NIMI would like to take this opportunity to convey sincere thanks to the Directors of Employment & Training of various State Governments, Training Departments of Industries both in the Public and Private sectors, Officers of DGT and DGT field institutes, proof readers, individual media developers and coordinators, but for whose active support NIMI would not have been able to bring out this materials. R. P. DHINGRA Chennai - 600 032 EXECUTIVE DIRECTOR (iv) ACKNOWLEDGEMENT National Instructional Media Institute (NIMI) sincerely acknowledges with thanks for the co-operation and contribution extended by the following Media Developers and their sponsoring organisations to bring out this Instructional Material (Trade Theory) for the trade of R&ACT 1st Year (Volume IIof II) NSQF (Level - 5) under Capital Goods & Manufacturing Sector for ITIs. MEDIA DEVELOPMENT COMMITTEE MEMBERS Shri. P. Senthil Kumar - TO, Govt ITI, Virudhu Nagar Shri. M. Ravichandran - ATO, Govt ITI, Tindivanam. Shri. P. Mohan - ATO, Govt ITI North Chennai - 32. NIMI CO-ORDINATORS Shri. Nirmalya nath - Deputy General Manager, NIMI, Chennai - 32. Shri. V. Gopalakrishnan - Assistant Manager, NIMI, Chennai - 32. NIMI records its appreciation for the Data Entry, CAD, DTP operators for their excellent and devoted services in the process of development of this Instructional Material. NIMI also acknowledges with thanks the invaluable efforts rendered by all other NIMI staff who have contributed towards the development of this Instructional Material. NIMI is also grateful to everyone who has directly or indirectly helped in developing this Instructional Material. (v) INTRODUCTION TRADE THEORY The manual of trade theory consists of theoretical information for the Course of the R&ACT 1st Year (Volume II of II) Trade Theory NSQF Level - 5 in Capital Goods & Manufacturing. The contents are sequenced according to the practical exercise contained in NSQF LEVEL - 5 syllabus on Trade Theory attempt has been made to relate the theoretical aspects with the skill covered in each exercise to the extent possible. This correlation is maintained to help the trainees to develop the perceptional capabilities for performing the skills. Module 1 Compressor and Motors Module 2 Condenser, Expansion Valve and Evaporator Module 3 Refrigerant and Insulation Module 4 Window Air Conditioner Module 5 Split A/C Module 6 Multi Split A/C and Car Air Conditioning The trade theory has to be taught and learnt along with the corresponding exercise contained in the manual on trade practical. The indications about the corresponding practical exercises are given in every sheet of this manual. It will be preferable to teach/learn trade theory connected to each exercise at least one class before performing the related skills in the shop floor. The trade theory is to be treated as an integrated part of each exercise. The material is not for the purpose of self-learning and should be considered as supplementary to class room instruction. TRADE PRACTICAL The trade practical manual is intended to be used in practical workshop. It consists of a series of practical exercises to be completed by the trainees during the course. These exercises are designed to ensure that all the skills in compliance with NSQF LEVEL - 5 syllabus are covered. The manual is divided into Six modules. The skill training in the shop floor is planned through a series of practical exercises centered around some practical project. However, there are few instances where the individual exercise does not form a part of project. While developing the practical manual, a sincere effort was made to prepare each exercise which will be easy to understand and carry out even by below average trainee. However the development team accept that there is a scope for further improvement. NIMI looks forward to the suggestions from the experienced training faculty for improving the manual. (vi) CONTENTS Lesson No. Title of Lesson Learning Page No. Outcome Module 1 : Compressors and motors 2.1.84-86 Function of hermetic compressor 1 2.1.87 Gasket for compressor 3 2.1.88 Dome welding 4 2.1.89 - 91 Construction and working of principle of various compressors 7 2.1.92 - 95 Identification & application of different types of single phase motors 14 2.1.96 Types of motor used in RAC 17 2.1.97 Single phase motors types resistance/induction start, induction run motor 19 2.1.98 Capacitors, relays, over load protector, thermostat and selector switch 31 2.1.99 Description, construction functions of 3 I motors & starters 38 2.1.100 -101 3 phase squirrel cage induction motor - relation between slip, speed, rotor frequency, copper loss and torque 42 2.1.102 Test on induction motors 47 2.1.103 Three - phase, slip - ring induction motor 57 2.1.104 Maintain, service and troubleshoot in an AC three phase squirrel cage induction motor 63 2.1.105 - 107 Air conditioning units with inverter technology 74 Module 2 : Condenser, Expansion Valve and Evaporator 2.2.108 Air cooled condenser of domestic refrigerators 80 2.2.109 Air cooled condenser in Window Air conditioners 83 2.2.110 -111 Types of water cooled condenser 86 2.2.112 Pump down system in the split AC 88 2.2.113-114 Receiver, liquid line sight glass and strainer 90 2.2.115 Dehydrators (filter drier) 92 2.2.116-117 Capillary tube for the hermetic type compressor 93 2.2.118 Types of expansion valves 95 2.2.119 Evaporator in refrigerator 98 2.2.120 Evaporators in split AC 103 2.2.121 Methods of defrosting system 107 Module 3 : Refrigerant and Insulation 2.3.122-123 Refrigerant 109 2.3.124 Recovery of refrigerants 116 (vii) Lesson No. Title of Lesson Learning Page No. Outcome 2.3.125 Transfer of refrigerants 121 2.3.126 Hydro Fluoro Olefin (HFO) refrigerants 124 2.3.127-128 Cylinder & valves 125 2.3.129 Refrigeration System 129 2.3.130 Retrofitting of CFC filled domestic refrigerator with hydro carbon refrigerant 139 2.3.131-132 Retrofitting of CFC filled domestic refrigerator with HFC’s 141 2.3.133-135 Thermal insulation material 143 Module 4 : Window air conditioner 2.4.136 Mechanical & electrical components of window AC 146 2.4.137 Electric circuits of window AC 150 2.4.138 Electrical components of window AC 152 2.4.139 Window AC - Installation methods 155 2.4.140 Alternate leak detecting method and service valves in split AC 160 2.4.141-144 Factors effecting - system performance 168 Module 5 : Split AC 2.5.145-149 Mechanical & electrical components of window AC 171 2.5.150 Split air-conditioner outdoor unit (wall mounted) 182 2.5.151 Outdoor/indoor unit of split AC system (floor/ceiling mounted) 186 2.5.152 Ductable split AC 194 Module 6 : Multi Split AC and Car Air Conditioner 2.6.153 Multi-split AC systems 199 2.6.154 Basic working principle of inverter AC 225 2.6.155 Components of car AC 227 2.6.156 Components of car AC testing 231 2.6.157 Car AC compressor 234 2.6.158 Performance of car AC unit 242 2.6.159 Evacuation & gas charging of car AC 246 2.6.160-162 Car AC unit assembly sequence 254 (viii) LEARNING / ASSESSABLE OUTCOME On completion of this book you shall be able to S.No Learning Outcome Lesson No 1 Dismantle, repair and assemble hermetic, fixed and variable speed 2.1.84 - 91 compressor, and test performance. 2 Identify the terminals of sealed compressor and their wiring and measure 2.1.92 - 95 current, volts, watts and use of DOL starter with different types of motors. 3 Perform selection of Hermetic compressor for different appliances, 2.1.96 - 104 starting methods, testing controls &safety cut out used in sealed compressor. 4 Identify the components of control system of Inverter AC and wiring of 2.1.105 - 107 control system. 5 Perform servicing & de-scaling of condenser (internals & externals) used in 2.3.108 - 109 different appliances. 6 Perform Fitting & adjustment of drier, filter & refrigerant controls used in 2.3.110 - 118 different refrigeration system. 7 Perform servicing of different evaporator used in different appliances 2.3.119 - 121 8 Carry out Recovery and Recycling of Refrigerant used, alternative of CFC, 2.3.122 - 126 HFC re-cover, transfer & handing of gas cylinders. 9 Carry out Recovery and Recycling of Refrigerant used, alternative of CFC, 2.3.127 -130 HFC re-cover, transfer & handing of gas cylinders. Retrofit CFC/HFC machine with ozone friendly refrigerant with understanding of the compatibility. 10 Pack thermal insulation andprevent cooling leakage. 2.3.131 - 135 11 Install window AC, test Electrical & electronics components & Fault diagnosis & remedial measures. 2.4.136 - 144 12 Perform servicing of electrical& electronic control, test, Installation, wiring, 2.5.145 - 154 fault finding & remedial measures of different split AC. 13 Perform servicing of car AC. Fault diagnosis & remedial measures. 2.6.155 - 162 (ix) SYLLABUS 1st Year (Volume II of II) Duration: Six Months Duration Reference Learning Professional Skills Professional Knowledge Outcome (Trade Practical) (Trade Theory) with Indicative hours P r o f e s s i o n a l Dismantle, repair and 84 Acquainting with hermetic Compressor Skill 50 hrs.; assemble hermetic, compressor of Refrigerator or window Function, construction, fixed and variable speed type AC. (02 hrs.) working,application of Professional compressor, and test 85 Cut the compressor and dismantle. compressor,(Fixed speed and Knowledge performance. (05 hrs.) variable speed compressor) like 14 hrs. 86 Identify different compressor and Reciprocating, rotary, scroll and Service it. (06 hrs.) inverter type. (07 hrs..) 87 Lap necessary parts and cut the gasket. (05 hrs.) 88 Assemble the compressor with the new gasket. (07 hrs.) 89.Dismantle rotary / wobble plate/ Study the construction & working swash plate/scroll compressor. (07 of reciprocating, rotary, scroll, hrs.) screw and centrifugal 90.Identify different parts of dismantled compressor, wobble & swash compressor. (08 hrs.) plate compressor. Compressor efficiency factors, wet 91. Rectify defects and repair accordingly. compression, oil, properties, (10 hrs.) lubrication methods. (07 hrs..) P r o f e s s i o n a l Identify the terminals of 92. Identify terminal sequence of hermetic AC motors and their types. Skill 50 hrs.; sealed compressor and compressor motor by using digital Advantages of AC motor over DC their wiring and multimeter and start by DOL starter motor. Revolving field theory. Professional measure current, volts, and measure starting current and Phase splitting theory. Capacitor Knowledge watts and use of DOL running current by using ammeter and method and inductor method 14 hrs. starter with different AVO meter. (12 hrs.) used to split the single phase. types of motors. 93. Identification of terminal sequence of Torque –starting torque and CSIR motor by using digital running torque. Split phase multimeter and start by DOL starter induction motors, working and measure starting current and principle and construction. running current by using Ammeter and Starting winding and running AVO meter. Direct start using winding. ammeter and voltmeter. (13 hrs.) Starting current and running current. Method of changing the direction of rotation (DOR).Capacitor starts induction run motor, working principle and construction. Centrifugal switch and its function. Starter and its necessity. DOL starter and the safety devices incorporated in it. Description of hermetic compressor motor. (07 hrs..) 94. Start CSR motor through DOL starter Capacitor starts capacitor run and measure starting current and motor, working principle and running current and changing of DOR. construction. Starting (07 hrs.) capacitor and running capacitor Shaded pole motors, working (x) 95. Start shaded pole motor through DOL principle and construction. starter and measure starting current Torque comparison among and running current and changing of various single-phase AC motors. DOR, dismantle motor identify parts Common faults, causes and andassemble. (18 hrs.) remedies in motors. (07 hrs..) Professional Perform selection 96. Select a hermetic compressor of any Motors Skill 50 hrs.; of Hermetic kind. (04 hrs.) Motors used in refrigeration And Air compressor for 97. Start the compressor motor by RSIR, conditioning system, types, Professional d i f f e r e n t CSIR, PSC & CSR method by using construction, working & their starting Knowledge appliances, different type relay, capacitors, OLP’s, methods. Function of Starting relay, 14 hrs. starting methods, etc. (10 hrs.) Capacitors, OLP’s.(07 hrs..) testing controls & 98. Check and Test different type relay, safety cut out Capacitors, OLP’s, find out fault, rectify used in sealed and install. (11 hrs.) compressor. 99. Identify the terminals of a Squirrel cage Production of rotating magnetic field induction motor. (06 hrs.) by three phase AC supply. Working 100.Start the motor through DOL starter principle of three phase induction and measure starting current, running motor. Terms such as torque, slip, current and show changing of DOR. rotor frequency and their relation. (05 hrs.) Construction of squirrel cage 101. Start the motor through Star Delta or induction motor. Importance of Auto transformer starter and measure phase sequence. Construction of starting current, running current and slip ring induction motor show changing of DOR. (04 hrs.) Comparison between SCIM and SRIM. Three phase motor starters 102. Familiarise with Slip-ring induction such as DOL starter, Star – Delta motor and identify it’s terminals. starter, Auto transformer starter and (04 hrs.) Rotor resistance starter. Common 103. Start the Slip-ring induction motor faults, causes and remedies in through Rotor resistance starter and three phase AC motors. (07 hrs..) measure starting current, running current and show changing of DOR. (03 hrs.) 104. Rectify fault through insulation test, continuity test, open circuit test and short circuit test. (03 hrs.) Professional Identify the 105. Explain control circuit of variable speed Working principle of inverter Skill 25 hrs.; components of air conditioners (Inverter ACs). (08 hrs.) technology, advantages of variable control system of 106. Identify components of control system speed technology over fixed speed. Professional Inverter AC and of Inverter ACs including printed circuit Working principle of control system Knowledge wiring of control board (PCB) NTC,PTC e.g. Power for inverter Air Conditioners (ACs). 7 hrs. system. PCB, Filter PCB, Heat sink reactor. Printed circuit board (PCB), (08 hrs.) including power PCB, filter PCB, 107. Wiring of the control system. (09 hrs.) heat sink and reactor. Wiring diagram. (07 hrs..) Professional Perform servicing 108. Familiarise with different types of Condenser Skill 75 hrs.; & de-scaling of condensers used in refrigerators, Bottle Function of condenser, types, condenser coolers, visible coolers, deep freezers, Construction of air-cooled Professional (internals & Window and Split AC. (05 hrs.) condenser. Effect of chocked Knowledge externals) used in 109. Clean, flush, service and leak test condenser. Advantages, de scaling 21 hrs. d i f f e r e n t different type of air-cooled condensers, of air-cooled condenser. Effects of appliances. micro channel condensers. Remove air fouling and bypass air in dust from fins in air cooled condenser, condenser. micro channel condensers. (10 hrs.) Perform Fitting & 110. Identify with different types of water- adjustment of drier, cooled condensers like Shell and filter & refrigerant Tube type, Tube within tube type, controls used in shell, coil & evaporative type, etc. (04 hrs.) (xi) different refrigeration 111. Identify different items necessary for Types of water-cooled system. de-scaling like diluted Hcl, Pump & condenser, application, and motor, hose, etc. (04 hrs.) advantages. Liquid receiver, 112. Dilute acid and water according to pump down, application, types, amount of scaling and perform de- function and working. scaling. (04 hrs.) Description of water-cooled 113. Fit the pump motor with condenser condenser. and start. Take safety measure on Drier concentration of acid which may Function of drier, types, damage tube. (10 hrs.) application and its advantage. 114. Identify drier and capillary tube used Description of desicants.(14 in different cooling machines. (03 hrs.) hrs..) 115. Replace drier and capillary tube at the time of gas charging according to manufacturer’s direction. (10 hrs.) 116. Install different diameter capillary tube Expansion Valve used in different type of cooling Expansion valve used in machines. (08 hrs.) domestic refrigeration and air 117. Install with different types of expansion conditioning systems. valves used in small cooling machines Capillaries, Automatic and and central plant like Automatic Thermostatic Ex. Valves, and expansion valve, Thermostatic electronic expansion valves. expansion valve, hand expansion valve, (07 hrs..) and electronic expansion valves, etc. (12 hrs.) 118. Test and adjust the expansion valves fitted with machines. (05 hrs.) Professional Perform servicing of 119. Identify and service different types of Evaporator Skill 25Hrs.; different evaporator evaporators like plate and tube type, Working principle, Function, types used in different Fin and tube type, etc. fitted in of evaporators used in refrigerator, Professional appliances refrigerators, Bottle coolers, water water coolers, bottle coolers, Knowledge 07 Hrs. cooler, Window and split AC. (08 hrs.) window and split A.C, Super 120. Perform leak test, flush to remove oil heating in evaporators, Function by dry nitrogen. (08 hrs.) of accumulator and types. 121. Demonstrate different type of Methods of defrosting. (07 hrs..) defrosting in different machines. (09 hrs.) Professional Carry out Recovery 122. Identify and explain different colour Refrigerant Skill 25Hrs.; and Recycling of code of different type refrigerant Classification of refrigerants, Refrigerant used, cylinder like HCFCs (HCFC-22, HCFC- nomenclature of refrigerants Professional alternative of CFC, 123). HFCs (HFC-134a, HFC-32, R- including chemical name and Knowledge HFC re-cover, transfer 410A, R-407C and R-404A) and low- formulas, hydro 07 Hrs. & handing of gas Global Warming Potential (GWP) chlorofluorocarbons (HCFCs), cylinders. refrigerants like ammonia, R-290, hydro fluorocarbons (HFCs) and HFC-32, blends of HFCs (R-410A, R- hydro fluoroolefins (HFOs), blends 404A, R-407C etc.) and hydro of HFCs and blends of HFCs/ fluoroolefins (HFOs: HFO-1234yf, HFOs. Climatic impact of HFO-1234ze, HFO-1233zd, HFO- refrigerants: Stratospheric ozone 1336mz), blends of HFCs and HFOs. depletion, global warming, (04 hrs.) mechanism of ozone depletion; 123. Identify unknown refrigerant by its idle the Montreal Protocol phase-out pressure using head pressure gauge. schedule of ozone depleting (04 hrs.) refrigerants (HCFCs) and high 124. Recover refrigerant from a faulty global warming refrigerants machine. (06 hrs.) (HFCs). Brief introduction of 125. Transfer / Recycle refrigerant from one Ozone Depleting Substances cylinder to another using ice. (06 hrs.) (Regulation and Control) Rules, 2000 and its amendments. (xii) 126. Measure pressure-temperature of Introduction of properties of refrigerants including HCFC-22, ammonia, refrigerants; environment R-290, HFC-32, HFC-134a, R-404A, R- related properties: Ozone 407C and R-410A, HFOs. Identify Depleting Potential (ODP), flammability and toxicity of A3 and A2L of GWP; ODP and GWP of refrigerants. (05 hrs.) various refrigerants, thermo chemical properties: flammability and toxicity of refrigerants, lower flammability limit (LFL) and upper flammability limit of A3 and A2L refrigerants. Thermo physical properties: pressure temperature of different refrigerants.(07 hrs..) Professional Carry out 127. Demonstrate safe handling of refrigeration Safe handling of flammable Skill 25Hrs.; Recovery and cylinders. (04 hrs.) refrigerants. Recycling of 128. Demonstrate handling of cylinder valves. Refrigerant leak detection Professional Refrigerant used, (03 hrs.) methods, evacuation and Knowledge alternative of 129. Good servicing practices onTest leak, charging of refrigerant, 07 Hrs. CFC, HFC re- evacuation and charge refrigerant in temperature glides of cover, transfer & refrigerator by weight in capillary system. refrigerant blends, procedure of handing of gas (10 hrs.) charging of refrigerant blends cylinders. 130. Recover CFC by recovery pump and especially the zeotropic Retrofit CFC/ cylinder on CFC filled domestic refrigerator. blends, hydrocarbon blends, HFC machine (08 hrs.) HFC blends (R-404A, R-407C, with ozone R-410A) and blends of HFC/ f r i e n d l y HFO. refrigerant with Retrofitting understanding of Changes of components & the compatibility. practices while retrofitting CFC appliances with HC Refrigerants. Properties of HCs (07 hrs..) Professional Pack thermal 131.Flush the system with dry nitrogen. Thermal Insulation Skill 25Hrs.; insulation Evacuate and charge hydrocarbons. (05 Function, types, andprevent hrs.) thermodynamic properties of Professional Knowledge cooling leakage. 132.Test and Use sealed component (Electrical) heat insulation materials used 07 Hrs. like thermostat, relay, overload protector in refrigeration and Air etc. (05 hrs.) Conditioning systems. 133. Identify insulating foam (polyurethane rigid Introduction of polyols and foam and polystyrene). (02 hrs.) foam blowing agents (HCFC- 134. Fill with insulation material like PUF and 141b, cyclopentane, water, glass wool. (07 hrs.) C02, methyl formate, HFO- 135. Pack insulation inside door panel and 1233zd (E), HFO-1336mzz adjust gasket to prevent air leak. (06 hrs.) (Z)). (07 hrs..) Installwindow AC, 136. Acquainting with electrical and mechanical Window Air Conditioner Professional Skill 50Hrs.; test Electrical & components used in window air-conditioner. Study of construction and electronics (05 hrs.) working principle of window Professional components & 137. Acquainting with electrical components like AC and its components; Knowledge Fault diagnosis & selector switch, thermostat switch, relay, electrical controls and wiring. 14 Hrs. remedial measures. starting capacitor, running capacitor, Installation, troubleshooting overload protector, remote and PCB control, and servicing. etc. (06 hrs.) Energy Efficiency Ratio (EER) 138. Demonstrate working of mechanical -Energy-efficiency labeling on components like compressor condenser, ACs.(07 hrs..) expansion valve (capillary) and evaporator. (05 hrs.) (xiii) 139. Trouble shooting, installation, tracing wiring circuit. (4 hrs..) 140. Leak testing, evacuation and gas charging. (05 hrs.) 141. Hands on practice on installation of window Installation of Window AC AC following step by step procedure. Advantages of proper (08 hrs.) installation of window AC with 142. Install gauge manifold in the system. emphasis on proper (04 hrs.) functioning and avoidance of 143. Show discharge pressure and sanction leakage of refrigerant. pressure during running time. (07 hrs.) Selection of installation 144. Check performance of different parameters location considering safety, i.e. pressure, temperature, pull down time, exclusive availability of power air flow and current drawn. (06 hrs.) point and obstruction-free air flow from condenser. Step by step procedure for proper installation, and proper inclination of AC cabinet backward/ outward for drainage of condensate. (07 hrs..) Professional Perform servicing Split AC Split AC Skill 100 of electrical& 145. Identify various components of split AC like Construction and working hrs.; electronic control, mounted, floor and ceiling mounted, duct principle, types, trouble Professional test, Installation, able and multi split AC. (04hrs.) shooting & care and Knowledge wiring, fault finding 146. Identify electrical circuits. (04hrs.) maintenance. 28 hrs. & remedial 147. Test different components and fault finding. Energy Efficiency Ratio (EER) measures of (03 hrs.) - Energy-efficiency labeling on different split AC. 148. Leak testing of the system, evacuation and ACs. gas charging. (03hrs.) Advantages of proper 149. Hands on practice on Installation and installation with emphasis on trouble shooting. (06hrs.) proper functioning and 150. Same as Split ACin the case of wall avoidance of leakage of mounted split AC. (16hrs.) refrigerant. Selection of location of indoor and outdoor units ensuring minimum distance between the units, away from flammable materials, if any, good air flow within the cooling space as well as over the condenser. Locate power supply point considering safety and exclusiveness. Step by step procedure forinstallation both for indoor and outdoor unit. Ensure convenient access for drainage of condensate from the cooling coil. Split AC (Wall Mounted) Construction and working principle, types, trouble shooting. Description of electrical components used in split A.C. Study the wiring circuit. (xiv) 151. Same as Split ACin the case of floor, SPLIT A.C (floor, Ceiling / Ceiling /Cassette mounted Split AC. Cassette mounted Split A.C) (16hrs.) Construction and working principle, types, trouble shooting. Description of electrical components used in split A.C. Study the wiring circuit. 152. Same as Split ACin the case of Ductable SPLIT A.C ( Ducted ) split AC. (16hrs.) Study of the Duct able split AC, its Construction and working principle, types, trouble shooting. Description of electrical components used in split A.C. Study the wiring circuit. 153. Same as Split ACin the case of Multi Split MULTI SPLIT A.C AC. (16hrs.) Study the construction and working, various components, electrical circuits, testing components, fault detection, leak testing, evacuation, gas charging, Installation, trouble shooting. 154. Same as Split AC in the case of Inverter INVERTER SPLIT A.C. Split AC. (16hrs.) Study of construction and working principle of inverter AC and its components, electrical circuit and controls, installation, servicing, trouble shooting, fault detection, leak testing and gas charging. Concept of Indian Seasonal Energy Efficiency Ratio ISEER). Energy Efficiency leveling on inverter AC.(28hrs..) Professional Perform servicing 155. Identify various mechanical components CAR AIR CONDITIONING Skill 25 hrs.; of car AC. Fault used in car AC. (02 hrs.) Study various components, Professional diagnosis & 156. Identify various electrical components used electrical circuits and wiring Knowledge r e m e d i a l in electrical circuits in car AC. (02 hrs.) diagram, testing components, 7 hrs. measures. 157. Testing of system components & fault fault detection, leak testing, finding (03 hrs.) Study of good service practice, 158. Install gauge manifold to check suction evacuation, gas charging, and discharge pressure in charging time Installation, trouble shooting, and running time. (04 hrs.) Magnetic clutch operation, free 159. Leak testing using dry nitrogen, evacuation movement of flywheel and gas charging (HFC-134a, HFO-1234 (nonfunctioning of clutch), care yf and blends of HFCs and HFOs). (04 hrs.) and maintenance. (07 hrs..) 160. Installation and trouble shooting (03 hrs.) 161. Testing magnetic clutch, compressor overhauling, condenser cleaning and add refrigerant. (05 hrs.) 162. Regular maintenance. (02 hrs) In-plant training / Project work: Broad Area: a) Assemble a car A.C Cycle b) Assemble window AC / Split AC (xv) (xvi) CG&M Related Theory for Exercise 2.1.84 - 2.1.86 R&ACT - Compressor and Motors Function of hermetic compressor Objective: At the end of this lesson you shall be able to explain the necessity of part function. Usually hermetic or sealed type provides compact where it drops back to the sump. (Fig 1&2) assembly and will such require less place and noise The main parts of reciprocating compressor are head less. The unit is completely sealed in and tested at the plate valve plate and valves, piston, piston pin, factory, trouble is free with compressor motor assembly. connecting rod and crankshaft. The motor located above the compressor operates horizontally. This construction method permits operation of the compressor in oil, simplifying the lubricating problem. The suction intake is placed so that suction vapour must travel through the holes in the motor rotor in order to get to the top of the shell and then to the intake tube. Any oil or liquid refrigerant is separated from the vapour by centrifugal force due to rotation of the motor rotor as vapour passes up through the holes in the rotor. Consequently oil and liquid separation assured oil is eliminated and with it damages of valve breakage coil is picked up in a small slot on the end of the crankshaft which acts as centrifugal pump and the oil is forced into the power main bearing. From this point it follows the spiral groove in the bearing up to the crankcase where it lubricates the trust plate, connecting rod and piston coil is then pumped through a tube by vapour action up to a small reservoir beside the upper main bearing and is then fed into and spiraled up through the bearing from 1 The reciprocating compressor are available 1/8 HP to shaft and fix main bearing of the compressor and 15 HP capacity. It is Hermatically sealed type. tightended the eccentric lock nut. Hermatically sealed type The following precaution to be taken while assembling the compressor. In hermetic type there is no need for the shaft seal. The compressor and motor have a common shaft and are New gasket should be used assembled in a single body and the whole assembled is The marks should be match for proper fillings fixed in a steel shell, the joints of which are welded. The bolts should not be over tight To assemble the reciprocating compressor to check the parts and clean completely. Fix the connecting rod and Faulty parts should not be used piston with help of piston pin. Then piston in cylindrical and set the big end bearing of the connecting rod on the 2 CG&M: R&ACT (NSQF Level-5) - Related Theory for Exercise 2.1.84 - 2.1.86 CG&M Related Theory for Exercise 2.1.87 R&ACT - Compressor and Motors Gasket for compressor Objectives: At the end of this lesson you shall be able to know the need for lapping and polishing of valve plate, seal know the valve plate components and function know the causes for failure of valve plate explain the cutting gasket. In valve plate any scratch seat will leak the refrigerant Gasket is a packing to make leak proof joint. All the joints and the system efficiency will greatly reduced. of the compressor must be air tight and with stand the pressure and heat developed during the compression. The scratches on shaft seal will leak the refrigerant from the system. So lapping for these parts to remove Gasket are generally of cork, paper composition, lead, scratches and improve the system efficiency. asbestos rubber and aluminium. Mostly the lead and paper composition gasket are used in reciprocating Valve plate components & function compressor. Valve plate The size of the gasket depends upon the thickness of Suction valve plate the gasket and common sizes are used 1.6mm, 0.8mm Discharge valve plate and 0.4mm. Valve plate: Both suction valve plate and discharge reed When these are tightened by bolt in between two surface mounted on valve plate of joints these are previously closed and make leak proof joints. Suction valve plate: During suction stroke through suction valve plate vapour enter into the cylinder Following properties should be suitable in gasket Discharge reed valve: During compression stroke It should be compressible without expansion suction valve closed and discharge valve open to the It should be able to withstand high pressure and high condenser. temperature Causes for failure of valve plate It should be easily cut in proper size Uneven seatings due to the wear carbon deposit or It should be made from a material which should not damage. react chemically with air or refrigerant used in the Valve reeds which are distorted cracked or in any system. other way damaged. Wet compression, leads damaging valve plate. 3 CG&M Related Theory for Exercise 2.1.88 R&ACT - Compressor and Motors Dome welding Objectives: At the end of this lesson you shall be able to name all the parts and function of each explain leak test after dome welding. Compressor has the following parts: - Motor winding - Rotor - Connecting rod - Piston - Gudgin pin - Valve plate, valve reed, suction, discharge, retainer, spring, bolts - Terminal adapter - Crankshaft - Discharge muffler, suction muffler, - Compressor, top and bottom dome The figures of piston body, connecting rod, valve plate and reed are given in (Fig 1, Fig 2, Fig 3) and (Fig 4) respectively. In hermetic sealed compressor motor and compressor are directly connected in a shaft and fixed in a 2 piece dome(top and bottom) with support of suspension spring for stop noise and vibration. Both motor and compressor running in a same shaft so the (RPM) will be same for motor and compressor this will give more performance for sealed compressor than open type compressor. The total compressor inner body upto main bearing immersed in lubricating oil so in full speed motor bearing will not get wornout. The compressor stator has got two windings (starting winding and running winding). Running the rotor got fan blade. This blade spray cool gas on winding and total dome will get cool. 4 When assembling sealed compressor should not Pressure total compressor to be immersed in a water assembled in open. Air should be assembled in AC room tank for check minute leak. to avoid moisture entering in winding, compressor head After leak test, new oil to be charged after let out gas and dome. pressure, as recommended by manufacturer through After weld compressor dome for leak test the compressor charging pipe. recharge pipe, suction pipe all to be sealed and through Leak testing hermetic sealed compressor is shown in charging pipe with HP gauge 17.0 kg/cm2 gas to be (Fig 5). charged after charge. Oil to compressor Objectives: At the end of this lesson you shall be able to add oil to compressor lubrication lubricating oil properties methods of lubrication. Lubrication is the process by which the moving parts Some of the most important properties which refrigerant are kept lubricated by the film of oil. Since heat is oil should have generated in the moving parts, the oil film becomes – Viscosity (as recommended by manufacturer) heated and cooled by the oil level maintained in crankcase i.e., the oil should always be flowing in the – Low acidity bearings and moving parts, while the compressor is – Low flash point running. – Low pour point Lubricating oils for refrigeration compressors are a special grade oil. In a refrigeration compressor oil comes – Good dielectric strength in contact and mix with (such as in freon) the refrigerant. – Chemical stability So, it becomes necessary that the oil used in the – Miscibility with refrigerant refrigeration system should be selected to confirm to the special needs of the system. Recommended quantity of oil should be used. Viscosity Viscosity : Viscosity is the resistance to flow of fluide and is expressed is say bolt universal (SSU) Low acidity Oil have a certain amount of organic acidity it’s maintained below 0.05 Low flash point At operating pressure & temperature the oil should not be flashed i.e, it should not be ignited Pour point Pour point is property of lubricant at the temperature oil ceases to flow Dielectric strength It is property of oil to resist the flow of electricity. Chemical stability It is the property of oil, should be chemically stable or compatible with refrigerant & others materials Miscibility It should be well miscibility with refrigerant. CG&M: R&ACT (NSQF Level-5) - Related Theory for Exercise 2.1.88 5 Methods of lubrication splashes the oil on the rubbing surfaces and lubricates. This system is preferred for the compressors below The methods of lubrication used for refrigeration system 10kW capacity. are divided into two main groups: b Forced feed lubrication a Splash lubrication In the forced feed method, the oil is forced under b Forced feed lubrication pressure with the help of pump through the system and a Splash lubrication the oil comes back under gravity after performing the In Splash lubrication system, the crank case acts as a lubricating function into the sump located in the crank sump for lubricating oil. The crank-shaft and connecting case. This system is used for high capacity compressors. rod into oil sump. Each revolution of the crank-shaft Winding and pumping pressure in hermetic compressor Objective: At the end of this lesson you shall be able to check the winding in hermetic compressor. When a compressor does not run, it is most likely Checking of pumping in pressure in hermetic because of one of the following problem. compressor - The compressor motor is burnt out Volumetric efficiency of a compressor is the actual volume of refrigerant gas pumped divided by the - The compressor is mechanically struck calculated volume - There is no voltage to the compressor If the head pressure increases the amount pumped per In order to check compressor motor windings, stroke will decrease. This is because the compressed disconnect all wiring from the three compressor vapour in the clearance space will expand on the intake terminals. Using a multimeter measure the resistance stroke and freon vapour cannot move into the cylinder between each two pairs. If the power source is three until the pressure in the cylinder is lower than the phase, all three readings on the compressor windings pressure in the suction line. The higher the compressed should be equal. pressure the greater the compressed vapour in the If the compressor operates on single phase power, there clearance space will expand. should be one resistance reading that equals the sum Secondly if the low side pressure decreases it is more of the other two. Most resistance readings will fall within difficult for vapour to fill the cylinder and the amount the range of 1 to 20 ohms. A compressor with a failed pumped per stroke will decrease. motor will often have one or more of the reading equal Thirdly if the clearance pocket is enlarged the amount to zero (winding is shorted) or infinite resistance (winding pumped per stroke will decrease. The clearance space is open). is the space left in the cylinder when the piston is at the The compressor winding can also be grounded to the end of its pumping stroke T.D.C.(Top Dead Centre). casing. For this mark the resistance between each The efficiency of a compressor also depends on the size terminal and the casing. So make sure the probe on the of the valve openings. If the intake valve reduces the casing is touching bare metal. You may scrape away flow of low side vapour into the cylinder the cylinder will some paint. This resistance reading should be infinity. not be filled and the efficiency of the compressor will be If there is any movement at all on the meter, there is lowered. If the exhaust valve stick or if the line from the some continuity to ground and the compressor motor compressor to the condenser is pinched, this extra should be considered unserviceable. pressure in the cylinder will cut down the compressor’s If the compressor motor windings are not shorted, not pumping efficiency. open and not grounded then electrically the motor is all right. 6 CG&M: R&ACT (NSQF Level-5) - Related Theory for Exercise 2.1.88 CG&M Related Theory for Exercise 2.1.89 - 2.1.91 R&ACT - Compressor and Motors Construction and working of principle of various compressors Objectives: At the end of this lesson you shall be able to explain the construction and working of rotary compressor stationery blade type types of rotary compressor. Rotary compressor in that compressor in which gas is When motor or the roller rotate through the surface of compressed in rotary motion. Generally it is used in small the cylinder. Then low pressure gas enters into the sealed systems like refrigerator and Air conditioner. It is cylinder and compressed in to the outer dome. Hence also used in vacuum pump. oil and gas will separate. The oil will collect at the outer dome and compressed gas flows into the discharge line. The main parts of a stationery blade type rotary (Fig 1) compressor are rollar spring and discharge valve , dividing blade is fitted on the cylinder wall. The roller is Types of rotary compressor fixed on the shaft. The function of dividing blade is Stationery blade type rotary compressor separate low pressure and high pressure. The oil is filled in the outdome. The oil level is maintained below the Rotary blade type rotary compressor discharge tube. The shaft is connected to the motor. 7 In rotary blade type rotary compressor the dividing blade continues its rotation the volume of vapour enclosed is titled on the rollar. Minimum two blades or multiples between the blades decreases and its pressure of two. The rollar is fixed to the shaft and rollar rotated increases. As it rotates further high pressure vapour through the surface of the cylinder as shown in Fig 2. reaches the discharge port and then discharge valve As rotar rotates, rollar rotated through the surface of opens and vapour enters the condenser through the cylinder by centrifugal force. discharge line. When these blades again reach suction port the space between them is filled with low pressure The low pressure vapour coming through the suction vapour again and this cycle is repeating. line entres the space between two blades. As the rotar Parts of rotary compressor Objective: At the end of this lesson you shall be able to identify the parts of rotary compressor. Stationery blade type rotary compressor Discharge line Parts of stationery blade type rotary compressor are Blade given below (Fig 1) Parts of Rotary vane type rotary compressor (Fig 2) Rollar (impeller) Rollar Rotar shaft Vane Eccentric Cylinder Cylinder Suction port Housing Discharge Suction line 8 CG&M: R&ACT (NSQF Level-5) - Related Theory for Exercise 2.1.89 - 2.1.91 Rotary compressor (stationery blade type) Objective: At the end of this lesson you shall be able to details of rotary compressor. Before assembling the compressor check all parts for wear and tear. Inspect discharge reed for any scratches on them. Fix discharge reed in the valve plate at its proper place. Place the rotar in the rotar housing. Fit the shaft through the rotar and check for correct position. Assemble cylinder cover, blade and spring place the cylinder and shaft assembly in the dome. Tighten the both evenly with a torque wrench. Keep the compressor and motor in the dome.Weld the joint. Scroll type compressor Objective: At the end of this lesson you shall be able to explain scroll type compressor. Scroll compressor are orbital motion, positive 9 Lower bearing 10 Thrust washer displacement machines that compress with two inter 11 Magnet 12 Oil tube fitting, spiral shaped scroll members. (one is fixed and another is movable) 13 Shell 14 Rotor 15 Stator 16 Suction tube 17 Electric terminal 18 Terminal cover 19 Suction baffle 20 Slider block 21 Internal pressure relief valve 22 Discharge tube 23 Check valve Key components 1 Discharge plenum 2 Thermal valve 3 Fixed scroll 4 Orbiting scroll 5 Crankcase 6 Counterweight 7 Eccentric shaft 8 Lower bearing ring CG&M: R&ACT (NSQF Level-5) - Related Theory for Exercise 2.1.89 - 2.1.91 9 (Fig 1) Scroll compressor components between the fixed and orbiting scrolls. This fixed angular relation, coupled with the movement of the orbiting A cut away view of the scroll compressor with key scroll, is the basis for the formation of gas compression components labeled in shown in fig1. The motor stator pockets. is rigidly attached to the shell. The rotor is shrink-fit onto, the eccentric shaft. The shaft is supported by two As shown here, the compression process involves three bearings, one in the crankcase and the second below orbits of the orbiting scroll. In the first orbit, the scrolls the motor. ingest and trap-off two pockets of suction gas. During the second orbit, the two pockets of gas are Scroll compression process compressed to an intermediate pressure. In the final The diagram shown describes the scroll compression orbit, the two pockets reach discharge pressure and process. The two components shown are mating are simulateously opened to the discharge port. involute scrolls. One scroll is fixed in place and the other This simulataneous process of suction, intermediate scroll orbits within this fixed scroll. On e part that is not compression, and discharge leads to the smooth shown in this diagram but is essential to the operation continuous compression process of the scroll of the scroll is the anti-rotation coupling. This device compressor. maintains a fixed angular relation of 180 degrees Components of swash plate axial type compressor Objective: At the end of this lesson you shall be able to explain briefly about swash plate axial type compressor. Purpose: There are numerous types of compressors in The pistons are operated by a swash plate use today. Compressors may have from one to ten which moves the pistons back and forth in the cylinders and may or may not have provisions to retain cylinders as the shaft is rotated. There are 10 refrigerant oil. There is even a rotary and as scroll type separate cylinders, 5 at the front of the design. compressor and 5 at the near of the Regardless, all operate as the “pump” of the system to compressor. Reed valves are provided for keep the refrigerant circulating and to increase the each cylinder. (Fig 1) refrigerant pressure. 10 CG&M: R&ACT (NSQF Level-5) - Related Theory for Exercise 2.1.89 - 2.1.91 The swash plate is most frequently used in car air conditioning system, it has upto ten cylinders. A swash plate mounted at an angle on a shaft moves a number of double acting pistons backwards and forward axially. (Fig 2) This induces and compressors refrigerant. The induction and expulsion of refrigerant is controlled by metal plates with integral reed valves. The swash plate converts the rotary movement of the compressor shaft into the reciprocating movement of pistons. Swash plate compressors can be of either fixed or variable capacity. Construction and working of screw compressor Objective: At the end of this lesson you shall be able to construction and working of screw compressor. Rotary - screw compressor Less vibration and less urging due to continuous gas displacement via the sweeping motion of the rotors. A rotary - screw compressor uses rotors to compress larger volumes of gaseous refrigerant to a high pressure Better adjustments in cooling capacity without causing and temperature (shown in figure). The compression is unstable operation, which is sometimes as issue with performed by male and female rotors that reduce the centrifugal compressors. refrigerant gas volume as they rotate. Cool vapour Less sensitive to liquid slugging but long-term liquid refrigerant enters from the suction port, is forced by the slugging will impact the reliability of the compressor. meshing rotors through the threads as the screws rotate, and exits at the discharge port with high pressure and Limitations temperature. The rotary-screw compressor can be sub- Impractical to design to a capacity below 20 tons (70 classified by the quantity of screws (singles, twin and kW), due to the rotor processing technology. multi). The capacity can be adjusted through an inverter drive. Application Benefits Screw compressors have been development to complete with large reciprocating and small centrifugal Compared to the compressors discussed above, the compressors in both air conditioning and refrigeration rotary screw compressor has the following benefits. markets. It is used for commercial and industrial air Simpler structure, less components, larger capacity, and conditioning and refrigeration applications with a higher efficiency capacity range from 20 to 750 tons (70-2, 637 kW). CG&M: R&ACT (NSQF Level-5) - Related Theory for Exercise 2.1.89 - 2.1.91 11 Construction and working principle of centrifugal compressor Objective: At the end of this lesson you shall be able to construction and working of centrifugal compressor. Centrifugal compressor Compact structure and lighter weight per unit capacity. 80% - 90% weight reduction and about 50% footprint A centrifugal compressor is also called a turbo or a radial reduction compared to the reciprocating compressors. compressor which compresses refrigerant to a high pressure and temperature by adding kinetic energy to Higher reliability and lower maintenance cost because the cool vapour refrigerant is forced to pass into and there are less components exposed to wear and tear. through the impeller, and the impeller forces the fluid to Less vibration due to continuous gas displacement. spin faster and faster. The high-speed refrigerant gas is then forced to pass through the diffuser where the Multiple energy resources can be used for driving the refrigerant gas volume expands as its speed decrease. compression, i.e. electrical motor, steam turbine, or gas This process converts the kinetic energy of the high- turbine. speed low pressure gas to low-speed higher-pressure Limitations gas. The higher the impeller speed, the higher the pressure. Unlike the reciprocating piston compressor Capital cost premium, but lower operation cost offsets that has different actions for every stroke (i.e. suction, the increased investment. compressor, discharge), centrifugal compressors Requirements for higher, quality material, higher perform these actions continuously and concurrently. precision machining, and higher quality manufacturing. The capacity can be adjusted through an inverter drive and inlet guide vane. Impractical to design to a capacity below 20 tons (70 kW) due to the impeller’s high rotation speed. Also, it’s A centrifugal compressor can also be sub-classified by difficult to manufacturing an impeller with small diameters the number of stages (single-stage, two-stage and multi- (e.g. not smaller than 200mm) due to processing stage) and lubricating method (splash lubricated, forced technology. lubricated, or oil-free). The oil-free type adopts friction- free magnetic bearings. As a result, there are no Larger unit capacity requires larger circuit breaker and mechanical wear surfaces, which enhances the wiring. efficiency, reliability, reduces the noise level, and the Surging more likely to occur under light load conditions. maintenance cost. Applications Benefits A centrifugal compressor is beat suited for large cooling Centrifugal compressor has the following benefits; applications above 200 tons (700 kW), and is the most Largest capacity which can be up to 10,000 tons (35,000 popular compressor type for commercial and industrial kW) per unit. air conditioning and refrigeration systems. It competes with screw compressors and large reciprocating Higher heat transfer coefficient in evaporator and compressors. condenser due to oil-free refrigerant. 12 CG&M: R&ACT (NSQF Level-5) - Related Theory for Exercise 2.1.89 - 2.1.91 Table 1 Shows a summary of characteristics of the five compressor Compressor types Cost per kW Efficiency Vibrations Manufacturing Input power accuracy per unit Positive Reciprocating Low Low High Easy Low-High displace Single-acting ment Rotary-Vane Medium Medium Moderate Difficult Low Rotary-Scroll Medium High Moderate Difficult Low Rotary-Screw High Very high Lowest Very difficult High Dynamic Centrifugal High Very high Lowest Very difficult High Construction and working principle of wobble plate compressor Objective: At the end of this lesson you shall be able to construction and working of wobble plate compressor. Wobble plate compressor A variable displacement compressor can change the angle of the wobble plate and piston stroke. This angle A variable displacement compressor can change the is changed by a control valve that senses evaporator angle of the wobble plate and piston stroke. This angle pressure, which in turn changes wobble chamber is changed by a control valve that senses evaporator pressure. When the evaporator cools and low-side pressure, which in turn changes wobble chamber pressure drops, the piston stroke of a variable pressure. Variable displacement A/C compressor are displacement compressor is reduced so that compressor controlled by either a “ MANUAL” or “ELECTRONIC” outlet matches the cooling load. Variable displacement control valve. The manual valve consists of a diaphragm A/C compressors are controlled by either an internal acted upon by compressor crankcase pressure. As the mechanical control valve or and electronic valve that is evaporator outlet temperature (pressure) rises and falls, pulse-width operated by a module. The manual valve the diaphragm causes the crankcase pressure to move option is shown here. the wobble plate in either direction. Increased wobble plate angle will increase compressor displacement and outlet and decreased wobble plate angle will decrease compressor displacement (output). MOST MANUAL VALVE VARIABLE DISPLACEMENT COMPRESSORS WILL HAVE AN ELECTRONIC CLUTCH. The electronic control valve does not have a diaphragm, but instead has a crankcase pressure control valve that is controlled by a computer (BCM or other module) based on inputs from various temperature and/or pressure sensors. It is duty-cycled to meet the needs of the outlet temperature of the evaporator. Most vehicles today use the electronic control valve. This is important to know when diagnosing a low pressure problem. The compressor may be completely capable of creating the required pressure, but the control valve or circuit is not responding to system demands. A simple pressure or temperature or other sensor could cause this problem. Never replace the compressor until all OEM diagnostic strategies are followed. CG&M: R&ACT (NSQF Level-5) - Related Theory for Exercise 2.1.89 - 2.1.91 13 CG&M Related Theory for Exercise 2.1.92 - 2.1.95 R&ACT - Compressor and Motors Identification & application of different types of single phase motors Objectives: At the end of this lesson you shall be able to description of single phase motor used in RAC fields different part of single phase motor function of different part application of the single phase motor different types of single phase motor speed/r.p.m of motors. Basically single phase motor driven by single phase shown in figure. So starting torque is very high due supply i.e., 200-240 volts. Mainly induction motor used to starting capacitor connected in series with the in RAC fields maximum. Induction motor receives its starting winding. When the rotor reaches 75% of its names because rotar has no outside source of supply. rated speed, centrifugal switch or rely disconnect the Rotating magnetic field creates in stator & that is why starting winding with the starting or relay disconnect rotor moves by electro magnetic induction. the starting winding with the starting capacitor. Then motor runs only running winding. This type Motor has two parts i.e., rotor & stator compressor motor mainly used in deep freezer. Static part is stator & revolving part is rotor. In stator two sets of winding is require to make it self starting namely, main or running winding and starting or auxilary winding. Main or running winding made of comparatively thick wire & starting or a auxilary winding made of thin wire, so that resistance of starting winding is more than running winding. Types of single phase motors commonly used; 1 Split phase motor (RSIR) 2 Capacitor start (CSIR) 3 Capacitor start & run (CSR) 4 Permanent capacitor or capacitor run induction motor (PSC) 5 Resistance start capacitor run motor (RSCR) 6 Shaded pole motor 1 Split phase motor (RSIR): Basically this motor is sused in small domestic freezer. Low starting torque is require to start the motor. When single phase supply is given to the stator, a rotating magnetic (field creates)in stator. The current flow in the running winding lags the current flow in the starting winding by approximately 30 electricals degrees. Since the current flowing in the two windings are 30 degree out of phase which each other the single phase is 3 Capacitor start & run motor (CSR): The split to give the effect of two phases and a rotating construction of the capacitor start run induction motor field is set up in the stator which produce starting is same as that of capacitor start induction motor torque. When the motor speed gained about 75% of with exception that a running capacitor is installed its rated speed centrifugal switch or relay disconnect in series with the starting winding as shown in figure. the starting winding then the motor runs continuously The operation of the capacitor start run induction by running winding only motor differs from that of the capacitor