Lab Animal Safety & Handling Procedures PDF
Document Details
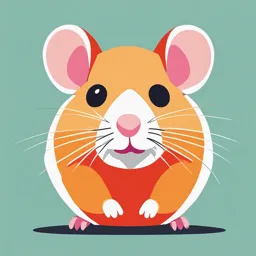
Uploaded by RenewedReasoning
Delaware Valley University
Tags
Related
- Lab Animals and Disease Control in Healthcare Settings - Lecture 8 Part 2 PDF
- Lab Animal Disease Coccidiosis PDF
- Veterinary Clinical Pathology Lab Manual PDF Fall 2024
- Lab Safety Rules and Management PDF
- Benha University Veterinary Medicine Practical Courses List PDF 2024
- Introduction to Animal Science Lab Animal 1 PDF
Summary
This document covers various aspects of lab animal safety, including safety and oversight, waste removal systems, types of waste, disposal methods, and zoonotic diseases. It also addresses the potential for allergic reactions to lab animals and the various measures to prevent exposure and transmission.
Full Transcript
Safety & Oversight Employee Safety Prevent Exposure Prevent Sickness Prevent Injury Environmental Safety Prevent Contamination Prevent Pollution Animal Safety Safety & Oversight Government Federal State ...
Safety & Oversight Employee Safety Prevent Exposure Prevent Sickness Prevent Injury Environmental Safety Prevent Contamination Prevent Pollution Animal Safety Safety & Oversight Government Federal State Local Employer Department This Photo by Unknown Author is licensed under CC BY How Does it Goes Out Waste Removal System 1: Duct Transport System How it Works: Ducted from Dump Station directly to dumpster at a loading dock to transport dirty bedding with urine and feces away with minimal manual labor Positives: Ergonomics, Allergen Reduction Negatives: Damage, Live Animals This Photo by Unknown Author is licensed under CC BY-NC-ND How Does it Goes Out Waste Removal System 2: Manual Transport System How it Works: Traditional System of dirty bedding with urine and feces dumped into trash bags then manually hauled to a dumpster Positives: Greater control if need to retrieve something Negatives: Allergen control, risk of injury What Goes Out? 1. Animal Wastes 2. Biohazardous Agents 3. Chemical Hazard Agents 4. Animal Carcasses 5. Sharps Animal Wastes w/o Hazards Removal Typical: General Garbage Possible: Special Labeling, Tracking with or without special bags Disposal Method: Duct and/or manual Biohazardous Agent Waste Disposal Removal: Dictated disposal methods to ensure safety Disposal Method: Manual Transport System Only Autoclave Decontamination Process with special disposal Packaging Method Red bags within specific boxes Must be labeled for disposal by licensed vendor Chemical Hazardous Waste Disposal Removal: Dictated disposal methods to ensure safety Tying or Taping Bags: Why does it matter? Disposal Method: Manual Transport System Only Decontamination by Disinfectant w processing NEVER Autoclave Chemical Waste Packaging Method: Yellow Bags within Same Boxes as Haz Waste Labeled for Disposal by Licensed Vendor Animal Carcass Disposal Removal Dismemberment Prior to Packaging Use of Special Drums Based on Animal Weight Special Labeling/Tracking of Waste Disposal Method: Manual Transport ONLY Packaging Method: Within Same Boxes as Haz Waste Labeled for Disposal by Licensed Vendor Sharps Waste Disposal Removal What goes in a sharps container???? Recapping Rules Disposal Method Manual Transport only NEVER Autoclave Sharps Containers Packaging Method: Within Same Boxes as Haz Waste Labeled for Disposal by Licensed Vendor What is ‘Disposal by Licensed Vendor’? Vendor is Licensed by Government to Incinerate Wastes Tracking System for Pickup, Receiving at Site, Disposal, and Confirmation of Incineration Zoonoses A disease which can be transmitted to humans from animals Common Zoonoses Tetanus: Bites, Scratches Multiple Species: Rabies, Cryptosporidiosis Herpes B Tularemia/Rabbit Fever Coronaviruses/SARS Hoof Stock:, Campylobacteriosis, E. coli, Qfever, Mad cow Disease Bartonella henselae/Cat Scratch Fever Major Things we can Give NHPs 2 Things we can pass along 1. Measles 2. TB How to Prevent: Health Surveillance program for all people with access to animals Major Zoonotic Risk with Macaques NHPs Herpes B is naturally carried and can test negative No vaccination to protect workers Transmission Bitten or scratched by an infected monkey Get an infected monkey's tissue or fluid on your broken skin or orifice Needle stick by a contaminated syringe Scratch or cut on a contaminated cage or other sharp-edged surface Exposure to the brain (especially), spinal cord, or skull of an infected monkey Prevention: Thoroughly wash the wound or area on your body that had contact with the monkey and gently scrub with soap, detergent, or iodine for 15-45 minutes and report to OHS/ER Mortality Rate: 80% if untreated (last report 2021 China) What are LAA? Definition: Allergic Reactions Related to Animal Proteins in Skin, Saliva, Urine, Feces 11-44% Rate of Allergy Response 2 Ways Exposure Occurs 1. Inhalation 2. Direct Contact 6 Common Lab Animal Sources 1.Mice 2.Rats 3.Rabbits 4.Cats 5.Guinea pigs 6.Dogs 4 Ways to Prevent LAA Exposure 1. Work Uniform Do Not Take Work Home, Possible Options 2. PPE 3. Ventilated Work Stations: HEPA filters with ‘Air Curtains’ to Contain Allergens (Synonyms: Hood, BSC, Cabinet, Laminar Flow, Pass Thru, etc.) 4. Hygienic Behavior Remove Uniform and/or PPE, Wash Hands with Soap and Water If Leaving Area and not available, use Hand Sanitizer PPE Definition: Physical barrier acting as protection from Zoonoses, Exposures, and Allergens What can be considered PPE 1. Work Uniform (Scrubs, Shoes, Lab Jacket) 2. Disposable Items (Gloves, Gown, etc.) 3. Hearing/Eye/Face Protection (Safety Glasses/Shield, Ear Plugs, etc.) How are Standards are Determined OHS, EHS, Institutional Biosafety Committee (IBC), LAS Department Use Published Safety Data, Government Guidelines (CDC, laws, EPA, etc), Animal Health Levels PPE Uses in the Workplace 1. PPE for General Employee Safety 2. PPE for Maintaining Animal Health Status 3. PPE for ABSL- Levels 4. PPE for Chemical Hazards PPE for General Employee Safety 1. Preventing Development of LAA 2. Preventing Zoonoses Transmission 3. Employee Physical Safety PPE Use for Animal Health Status Goal: Keeping certain stuff in OR out and Maintain Approved Health Status Nomenclature Health Status Level PPE Level Gnotobiotic VERY High High Germ Free Barrier High MidLevel to High Specific Pathogen Free (SPF) High MidLevel to High Non-Barrier Low to Medium None to MidLevel Conventional Low to Medium None to MidLevel Quarantine Low High Stay Tuned to Learn more Soon! PPE for ABSL- Levels ABSL: Animal Biosafety Level Four Different ABSL- Levels: ABSL-1 to ABSL-4 Level determined by many factors & what PPE is required determined by the level Hazard & PPE Increases as Level Increases PPE for Chemical Hazards Method One: United States Four Health Variables Rated at Levels of 0-4 Hazard & PPE Increases as Level Increases Level determined by many factors & what PPE is required determined by the level PPE for Chemical Hazards Method One: United States Hazard & PPE Increases as Level Increases PPE for Chemical Hazards Method Two: Global Method Introduced Method in Mid-2000s to Globalize Chemical Labeling Official Title: Globally Harmonized System (GHS) Importance of Globalizing Chemical Hazard Labeling Level determined by many factors & what PPE is required determined by the level Hazard & PPE Increases with Lower Number PPE for Chemical Hazards Method Two: Global Method Hazard & PPE Increases with Lower Number Rating Physical Health Environmental 1 Unstable Mass Explosion Fatal if Swallowed, inhaled Very toxic to aquatic life with Extremely Flammable Severe skin burns long lasting effects 2 Flammable Toxic if swallowed, inhaled Toxic to aquatic life with long lasting effects 3 Pressurized canister, may Harmful if swallowed, inhaled Harmful to aquatic life with burst if heated Skin irritant long lasting effects 4 Combustible Liquid May be harmful if swallowed, inhaled May cause long lasting May intensify fire; oxidizer May irritate skin harmful effects to aquatic life Common Issues in Facilities UNAVOIDABLE REPEITIVE MOVEMENTS Task Hands/Wrists Elbows Shoulders Neck Back Legs Transferring rodents with forceps Handling containers, wire cages, cage lids Preparing, transferring, replenishing water bottles Rodent dosing Lifting feed bags Pushing, pulling, rotating full carts Six Ergonomic Considers in LAS & Application Other 39% Back Abdomen, Arm, Multiple 61% g Le Shoulder WMSDs Other 6 Common Issues 1. Lifting, Bending, Twisting 2. Pushing, Pulling 3. Reaching for Items High & Low 4. Repetitive Movements 5. Standing 6. Carrying Heavy Items Work Related Musculoskeletal Disorders (WMSDs) Classified as the “most widespread occupational health hazard facing our Nation today” by OSHA and occur by lifting, standing in one position too long, repetitive movements, twisting, poor posture, and more. In 2016, WMSDs accounted for 39% of all injuries causing lost work days and the majority of those involved the back. Staff may be out for a day or over a year and may even require surgery. 6 Common Issues 1. Lifting, Bending, Twisting 2. Pushing, Pulling 3. Reaching for Items High & Low 4. Repetitive Movements 5. Standing 6. Carrying Heavy Items How to Implement Ergonomics & Prevent Workplace Injuries 1. Techniques Training 2. Regular Evaluation of Current Practices 3. Consider Changes #1: Techniques Training Incorporate Injury Prevention & New Employee Ergonomics Into All Trainings Training Involve Subject Matter Experts (Ergonomic Specialists & EHS), Responding to Work Employee Department Management, Refresher Place Injuries Training Vendors, Staff, Grad Students Goal: Minimize Training Drift Safety Ergonomic Mandated Training Training #1 Techniques Training 3 Common Applications to Review New 1. Poor posture & Physical Condition Employee 2. Stress Training 3. Exceeding your physical abilities 5 Common Times to Train Responding Employee 1. New Employee Training to Work Place Refresher 2. Employee Refresher Training Training Injuries 3. Safety Mandated Training 4. Ergonomic Training 5. Responding to Work Place Injuries Safety Ergonomic Mandated Training Training What Does Techniques Training Mean? Examples #2: Regulation Evaluation of Current Practices Involve Subject Matter Experts (Ergonomic Specialists & EHS), Department Management, Vendors, Staff, Grad Students Trial & Document #2 Regulation Evaluation of Current 4 Steps in Evaluation Practices 1. Walk Through & Review Practices in Action 2. Research Alternatives 3. Trial & Document Alternatives 4. Make Change & Share with All Involved 4 Limitations 1. Cost 2. Program Support 3. Staff Support 4. Changes in Preferences over Time #3: Consider Changes in Techniques & Practices 4 Considerations 1. New Equipment 2. New Techniques 3. New Practices 4. Rotate Responsibilities Rotate Responsibilities