Industrial Pharmacy II - Size Reduction Lecture Notes PDF
Document Details
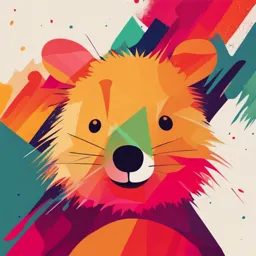
Uploaded by DextrousElation3938
Sinai University
Tags
Summary
This document provides a lecture overview of size reduction methods, including the mechanics of hammer mills, vibration mills, cutting mills, and end-runner mills. It covers the principles, benefits, and drawbacks of each method for reducing material size in a pharmaceutical setting.
Full Transcript
Industrial Pharmacy II nd 2 lecture size reduction SIZE REDUCTION METHOD Impact methods Size reduction range: 2- Hammer Mill It is an impact mill using a high-speed rotor to which are fixed a number of hammers. The material is fed at the top or center, thro...
Industrial Pharmacy II nd 2 lecture size reduction SIZE REDUCTION METHOD Impact methods Size reduction range: 2- Hammer Mill It is an impact mill using a high-speed rotor to which are fixed a number of hammers. The material is fed at the top or center, thrown out centrifugally, and ground by the impact of hammers or against the plates around the periphery. The hammer mill, which can be either the horizontal or vertical shaft type, is one of the most widely used mills in the pharmaceutical industry. Milling can be obtained by changing hammer speeds, and/or screen sizes and feed rates. 3 3 Parts Consists of a metal casing, enclosing a central shaft, to which 4 or more swinging hammers are attached. Lower part of the casing consists of a screen, through which material can pass and be collected in a suitable receiver. Construction & Working A hammer mill is essentially a steel drum containing a vertical or horizontal rotating shaft or drum on which hammers are mounted The hammers swing on the ends or are fixed to the central rotor The rotor rotates at a high speed inside the drum while material is fed into a feed hopper The material is put into the hopper which is connected to the drum The material is powdered to the desired size due to the fast rotation of hammers and is collected under the screen This is mainly operated at 1000 to 2500 rpm for the reduction of the large-sized particles High-speed rotor uses 10000 rpm speed 6 6 Uses Brittle material is best fractured by impact from blunt hammers Not suitable for fibrous material which is best reduced by cutting method. Principle of Operation: ❖ Impact between rapidly moving hammers mounted with joints. ❖The hammers swing out to a radial position when the shaft is rotated, the lower part of the casing consists of a screen through which material can escape. ❖When sufficiently size reduced, material is collected in a suitable receiver. ❖ The screen can be changed according to the particle size required. 8 8 Advantages of Hammer Mill: 1. It is capable of grinding many different types of materials. 2. The product size can be controlled by variations of rotor speed, hammer type, size, and shape of the mesh. 3. Operation is continuous. 4. No surfaces move against each other so that there is little contamination of the product with metal abraded from the mill. 5. Easy to set up or build and easy to clean. 7. Small space requirement. 8. May operate as a closed system to reduce dust and exposure to hazards 9 9 Disadvantages of Hammer Mill: 1. High speed of operation causes the generation of heat which may affect thermo labile materials or drugs containing gum, fat, or resin. 2. Hammer mills cannot be employed to mill sticky, fibrous, and very hard materials. 3. Potential screen clogging. 10 10 3. Vibration mill Alternative techniques: Vibration mills are filled to approximately 80% total volume with porcelain or steel balls. During milling the whole body of the mill is vibrated and size reduction occurs by repeated impaction. Comminuted particles fall through a screen at the base of the mill. SIZE REDUCTION METHOD Cutting methods Size reduction range: 4. Cutting Mill ▪ A cutter mill consists of a series of knives attached to a horizontal rotor which act against a series of stationary knives attached to the mill casing. 13 13 Principle of Operation: During milling, size reduction occurs by fracture of particles between the two sets of knives, which have a clearance of a few millimeters (cutting). A screen is fitted in the base of the mill casing and acts to retain material in the mill until a sufficient degree of size reduction has been reached. Uses: 1. used for fibrous material, wet and dry materials, and soft materials e.g. Liquorice roots, peels, etc. 2. not used for hard, abrasive materials. 14 14 SIZE REDUCTION METHOD Compression methods Size reduction range: 5. End Runner Principle Size reduction is done by crushing due to the heavy weight of the steel pestle. Shearing stress is also involved during the movement of mortar and pestle Construction It is considered a mechanical mortar pestle It consists of a steel mortar that is fixed to a plate The construction of mortar is connected to a horizontal shaft bearing a pulley so the plate with mortar can be rotated at high speed The pestle is dumbbell-shaped and the bottom of the pestle is flat Construction of the pestle is done in such a way that it can be raised from mortar for cleaning and emptying. Working The material to be ground is placed in the mortar. The mortar revolves at a high speed. The revolving mortar causes the pestle to revolve during this process, and size reduction is achieved Advantages End runner mill provides moderately fine powder. Wet grinding with very viscous materials such as ointments and paste is also possible Disadvantages Not suitable for the unbroken or slightly broken condition of drug End Runner Mill 6. Edge Runner Mill Principle The size reduction is done by crushing due to the heavy weight of the stone. Construction It consists of two heavy rollers and may weigh several tons. The roller move on a bed which is made up of granite or stone. Each roller has a central shaft and revolves on its axis. The rollers are mounted on a horizontal shaft and move around the bed Working The material to be ground is placed on the bed with the help of the scrapper in such a way that it comes in the path of the stone wheel These stones revolve on their own axis and at the same time travel around the shallow stone bed The material is ground for a definite period The powder is collected and passed through a sieve to get powder of the required size. It consists of a rotating pan or mortar made of cast iron or porcelain. A scraper is used to redirect the material into the grinding zone. Advantages Does not require attention during operation Disadvantages ▪ Hard to clean, ▪ Time-consuming, ▪ Not used for sticky materials Uses Grinding of hard material to a fine powder. Edge Runner Mill Edge Runner Mill 7. Single-Drive Roller Mill The roller mill has two cylindrical rolls of stone or metals mounted horizontally which are capable of rotation on their longitudinal axes. One of the rolls is driven directly while the second is rotated by friction when the material is drawn through the gap between the rolls. Comminution occurs by compression Used for cracking seeds prior to extraction of fixed oils. 24 24 SIZE REDUCTION METHOD Attrition methods Size reduction range: 8. Multiple Drive Roller Mill The material is sheared as it passes through the gap and is transferred from the slower to the faster roll, from which it is removed by a scraper. Comminution occurs by attrition Particle size can be controlled by: 1. The gap between the rollers 2. The speed differential between the rollers 3. The rate at which more grain is fed into the system Used for reducing & dispersing solids in semi-solid media 26 26 9. Colloidal mill 28 28 It consists of Rotor (rotating part) and a stator (fixed part). The distance between the rotor and stator (clearance) can be rendered – very small so can give very fine particles. The clearance can be regulated by means of a special micrometer adjusting device. Rotors & stators may be smooth or rough. It may be jacketed to be cooled & may be sterilized for handling sterile products. Used in the preparation of pharmaceutical suspensions & emulsions with particle sizes less than one micron. Size reduction is affected by attrition as it passes between the milling surfaces 29 29