Sustainable Development of Bio-Bricks Using Agricultural Waste PDF
Document Details
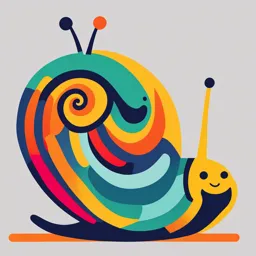
Uploaded by CuteOrphism
D. Y. Patil Technical Campus
2024
Radha Ajay Powar, Abhishek Baburao Patil, Aditya Sambhaji Kalake, Kiran Anil Chalake
Tags
Summary
This research explores the utilization of sugarcane trash for creating bio-bricks as a sustainable and cost-effective building material in India. It details the bio-brick production process, highlighting the potential to reduce air pollution connected to agricultural waste burning, and examines the properties of these bio-bricks.
Full Transcript
ISSN (Online) 2581-9429 IJARSCT International Journal of Advanced Research in Science, Communication and Technology (IJARSCT) International Open-Access, Double-Blind, Peer-Reviewed...
ISSN (Online) 2581-9429 IJARSCT International Journal of Advanced Research in Science, Communication and Technology (IJARSCT) International Open-Access, Double-Blind, Peer-Reviewed, Refereed, Multidisciplinary Online Journal Impact Factor: 7.53 Volume 4, Issue 5, April 2024 Sustainable Development of Bio- Bricks using Agricultural Waste Radha Ajay Powar1, Abhishek Baburao Patil2, Aditya Sambhaji Kalake3, Kiran Anil Chalake4 Assistant Professor, Department of Civil Engineering1 UG Students, Department of Civil Engineering2 D. Y. Patil Technical Campus, Talsande, Kolhapur, India Abstract: This paper endeavour the utilization of Agricultural waste ( Sugarcane trash ) for making Bio Bricks and other construction materials to reduce burning and disposal problems of Agricultural waste. India is an developing country and population of India goes on increasingthat puts huge burden of burn clay bricks. Burnt clay brick produced huge amount of greenhouse gas. Bio brick is one such material that haspotential to be sustainable and cost effective solution. Bio brick is an economic and environment efficient construction material and it has also carbon negative footprints. Sugarcane trash burning is a significant source of pollution in India, especially after the harvesting season. Bio- bricks was developed as an alternative and sustainable building material that is made up of agricultural waste. And at the same time will also lead to the reduction of air pollution and create new jobs at the grassroots level. The use of Sugarcane trash in construction materials is one of new way to deal with disposal and burning. India is home to some of the most polluted cities of the world in terms of its air quality. Data shows that around 20 out of the 30 most polluted cities of the world are in India. So the research highlight to provides green building material through Agricultural waste for sustainable development of Bio Bricks. Some additional work in this project can be done which will help environment with decreasing Air pollution by reducing of sugarcane trash burning. Bio-bricks can be developed as a carbon- negative, sustainable and economically viable material for construction. With the right kind of product development and incentives, it can diversify into numerous products satisfying the needs of an ecologically sensitive future. Keywords: sustainable development, lime binder, gypsum, fly ash, stone dust bio brick, agricultural waste, burning of agricultural waste I. INTRODUCTION India is an agricultural country, more than 50%of Indians make a living from farming. India's arable land area of 1,597,000 km2 (394.6 million acres) is the second largest in the world, after the United States. Its gross irrigated crop area of 826,000 km2 (215.6 million acres) is the largest in the world. India generates about 350 million tonnes of agricultural waste every year.In India, 220 million tonnes (MT) of cane are produced annually. At the rate of 10-20 per cent of cane harvested, about 22-44 MT of cane trash can be generated annually. Recycling this trash can greatly enhance the productivity of sugarcane fields and prevent deterioration of soil health. Indian farmers set fire in harvested farm fields to remove the crop stubble/residues as it is the most cost effective way of clearing the field for the next crop.The main adverse effects of crop residue burning include the emission of greenhouse gases (GHGs) that contributes to the global warming, increased levels of particulate matter (PM) and smog that cause health hazards, loss of biodiversity of agricultural lands, and the deterioration of soil fertility Construction has become entirely dependent on concrete structures and fired clay bricks, whose manufacture leads to the emission of a massive amount of greenhouse gases. Moreover, despite their high compressive properties, their thermal properties are poor, leading to an increase in the micro-climate problem. The results of the growing construction industry will be like a bell of danger as conventional materials are responsible for producing a massive amount of greenhouse gas emissions and environmental pollution (clay, sand, cement, bricks, etc.)Changing conventional materials and reusing agricultural waste is essential to enhance air quality and reduce air pollution. Copyright to IJARSCT DOI: 10.48175/IJARSCT-17547 306 www.ijarsct.co.in ISSN (Online) 2581-9429 IJARSCT International Journal of Advanced Research in Science, Communication and Technology (IJARSCT) International Open-Access, Double-Blind, Peer-Reviewed, Refereed, Multidisciplinary Online Journal Impact Factor: 7.53 Volume 4, Issue 5, April 2024 The present paper explores the potential application of ‘agricultural waste’, like sugarcane trash as the ingredient for alternative sustainable construction materials in the form of bricks. Using Sugarcane trash can be modified bio brick to suit the local market and building construction styles. The application of Sugarcane trash as a construction material can result in the reduction of the usage of natural resources as well as of energy consumption. At the same time, it can add to the farmer’s income, who can sell the leftover instead of burning them, thereby reducing air pollution. To achieve this goal, the process of up-cycling (the process of converting waste materials into new products of better environmental value than in their previous use) (Oyenuga et al., 2017) can be used to convert the sugarcane trash into usable bricks by combining it with lime, stone dust and water. The paper is divided into two parts, the first part highlights the brick making industry and Burning of sugarcane trash and its adverse impact on environment. The second part of paper elaborates the process of making the bio-brick, its advantages, it’s probable uses in construction industries and direct benefits to the environment. Thus, through our research paper we want to explore the potential use and possibilities of bio bricks in construction industries 1.1 Brick making industry in India Following China, India is the second largest manufacturer of bricks across the globe. No wonder, this very building material holds so much of importance in the Indian architecture. India alone produces over 10 percent of the bricks which are globally produced and has about 1,40,000 brick-making enterprises, who account for 250 billion brick masonry units (Source). This industry also employs around 15 million workers and consumes annually over 35 million tons of coal. Today there are many other options available to choose from when it comes to building materials, but bricks have always been one obvious choice. This is industry is surely growing as the demand for Bricks never declines due to the fast-economic growth, urbanization, and prosperity. This blog aims to explain how this legendary building material – Bricks, are made. Yes, let’s simplify it for you – The Brick Making Process In India. 1.1.1 Brick Demand Following China, India is the second largest manufacturer of bricks across the globe. No wonder, this very building material holds so much of importance in the Indian architecture. India alone produces over 10 percent of the bricks which are globally produced and has about 1,40,000 brick-making enterprises, who account for 250 billion brick masonry units (Source). This industry also employs around 15 million workers and consumes annually over 35 million tons of coal. Today there are many other options available to choose from when it comes to building materials, but bricks have always been one obvious choice. This is industry is surely growing as the demand for Bricks never declines due to the fast-economic growth, urbanization, and prosperity. This blog aims to explain how this legendary building material – Bricks, are made. Yes, let’s simplify it for you – The Brick Making Process In India. 1.1.2 Challenges Faced By The Brick Making Industry In India Despite the high demand for bricks in India, there are some challenges that the industry is facing. One of the main challenges is the availability of raw materials. While clay is abundant in many parts of India, the quality of the clay varies from region to region. This has led to a shortage of high-quality clay in some areas, which has affected the production of bricks. Another challenge facing the brick industry in India is the use of traditional brick kilns, which are known to be highly polluting. These kilns emit large amounts of particulate matter, carbon monoxide, and other pollutants, which have a negative impact on air quality and the health of those living in the surrounding areas. To address this issue, the government has been promoting the use of cleaner brick kiln technologies, such as the Vertical Shaft Brick Kiln (VSBK), which is more efficient and produces fewer emissions. The high demand for bricks in India has also led to a rise in the price of bricks in recent years. According to a report by the Brick Industry Association, the price of bricks in India increased by around 30% between 2016 and 2020. This increase in price has been attributed to several factors, including the rising cost of raw materials, increasing labor costs, and the use of more sustainable and Eco-friendly brick-making techniques. Copyright to IJARSCT DOI: 10.48175/IJARSCT-17547 307 www.ijarsct.co.in ISSN (Online) 2581-9429 IJARSCT International Journal of Advanced Research in Science, Communication and Technology (IJARSCT) International Open-Access, Double-Blind, Peer-Reviewed, Refereed, Multidisciplinary Online Journal Impact Factor: 7.53 Volume 4, Issue 5, April 2024 Despite these challenges, the demand for bricks in India is expected to continue to grow in the coming years. The government’s focus on infrastructure development and sustainable building practices, as well as the growth of the construction and manufacturing sectors, are all expected to contribute to this growth. 1.1.2 Pollution cause due to burnt clay brick Were found that most of the people around the bricks kiln was more concern about the soil and air pollution. People are suffering or facing breath problem, nasal problem, eye burning and other diseases. Brick kilns production of different toxic pollutant components for air pollution and human hazards. People are suffering with diseases like respiratory, nasal cognition, burning of eyes and loss of visibility, which accelerated many accidents on that particular area due to brick kilns. Some of the ash is carried by flue gases. It is possible to mix a part of the fuel in the powdered form with the clay during clay preparation. This fuel is referred as internal fuel as it is present inside the brick. As the brick is heated in the kiln, combustion of internal fuel takes place. However, in this case as the fuel particles are entrapped in the brick, the ash associated with them remains inside the brick and does not come out. This helps in reducing the pollution. Use of good quality agriculture soil in large quantities for brick making is also a grave area of concern. In geographical regions having thin topsoil, this result in reduction in the productivity of land and in extreme cases the land does not remain fit for agriculture use. To reduce this wastage some steps can be taken. At present only top surface (3 to 10 ft) is utilized for brick making, resulting in large surface area being affected due to digging of soil for brick making. So deep mining of clay can reduce the area affected due to dig of soil for brick making. All this mentioned measures would require mechanization of some of the processes in brick making. Development of suitable low cost machinery for making perforated/hollow products as well as support for popularizing these products on large scale are essential for reducing wastage of agriculture soil in brick making. The degradation of environment by bricks making process is very serious matter because Global health is most important for everyone. That there are bad effects of these bricks making process on soil, water, air, vegetation and human health. 1.2 Agricultural waste in India After China, India is the second biggest maker of agricultural waste. In India, 220 million tonnes (mt) of cane are produced annually. At the rate of 10-20 per cent of cane harvested, about 22-44 mt of cane trash can be generated annually. This sugarcane trash could not be use for cattle feed or any other purpose. Composting of this sugarcane trash is time consuming and labour required is more. The problems of labour and give fast and better way tosowing next crop indianfarmers burn this trash in agricultural sector. 1.2.1 Burning of agricultural waste However, current management strategies for crop residue, the major by-product of the agricultural sector, are deemed unsustainable and incompatible with this intensive production rate. Crop residue burning , is the most common way to manage the crop by-product, and it is the fourth largest contributor to biomass burning emissions globally (Andreae and Merlet, 2001; Sahu et al., 2021). In India, around 87.0 Mt of crop residue is burned annually, which is much larger than the entire agricultural waste production in other Asian countries like Bangladesh (72.0 Mt), Indonesia (55.0 Mt), and Myanmar (19.0 Mt) (Bhuvaneshwari et al., 2019; Datta et al., 2020; NPMCR, 2014; TERI, 2021). India is the world's second-largest contributor to carbonaceous aerosols, emitting 84.0 Tg.yr−1 (Grover and Chaudhry, 2019). CRB activities are the primary source of particulate matter (PM), sulfur dioxide (SO2), Nitrogen oxide (NOX), carbon monoxide (CO), black carbon (BC), and volatile organic compounds (VOCs) during the pre- and post-monsoon crop harvest (Grover and Chaudhry, 2019; Liu et al., 2022; Zhang et al., 2019). These emissions increase the risk of acute respiratory infection and other correlated diseases and deteriorate the living standards of agrarian states and their surrounding regions (Bikkina et al., 2019; Chakrabarti et al., 2019; Jethva et al., 2019; Ravindra et al., 2019). Recently, Crop residue burning was found to exacerbate negative health impacts associated with the COVID-19 pandemic (Chauhan et al., 2023). Copyright to IJARSCT DOI: 10.48175/IJARSCT-17547 308 www.ijarsct.co.in ISSN (Online) 2581-9429 IJARSCT International Journal of Advanced Research in Science, Communication and Technology (IJARSCT) International Open-Access, Double-Blind, Peer-Reviewed, Refereed, Multidisciplinary Online Journal Impact Factor: 7.53 Volume 4, Issue 5, April 2024 1.3 Need of sustainable development of bricks All this mentioned measures would require mechanization of some of the processes in brick making. Development of suitable low cost machinery for making perforated/hollow products as well as support for popularizing these products on large scale are essential for reducing wastage of agriculture soil in brick making. The degradation of environment by bricks making process is very serious matter because Global health is most important for everyone. That there are bad effects of these bricks making process on soil, water, air, vegetation and human health. The environment is degraded by the bricks making process and the result of this degradation is to be studies in various angles so that some remedial planning can be suggested. The bricks making process affects not only environment but also human health. The main adverse effects of crop residue burning include the emission of greenhouse gases (GHGs) that contributes to the global warming, increased levels of particulate matter (PM) and smog that cause health hazards, loss of biodiversity of agricultural lands, and the deterioration of soil fertility So sustainable development of bio bricks is solution for this two issue it’s air pollution due to burning of agro waste and pollution due to burn brick and alternative source to clay bricks. 2. Process of making bio brick Process of making bio bricks start with careful selection of dry agro waste. In kolhapurcity about more than 60-70% agricultural sector is used for sugarcane. Sugarcane trash are dried leaves that are left over in the field after the sugarcane is harvested. It available in large quantity. This is available in bulk quantity carefully chopped into small particles less than 15 mm. Lime slurry is prepared with adding water to lime stone this is also called as slaking of lime. When water is added to lime exothermic reaction takes place and heat is evolved. Carefully handle the slaked lime. Stone dust or fly ash mixed with lime slurry. Dry Sugarcane Trash Chopped into Preparation of Lime Slurryby Slaking of Lime Fine Pieces Less than 15mm Stoneadding water into it Mixing of Chopped Sugarcane Trash Mixture is poured in Mould in 3 Layers, Lime Slurry, Stone Dust or Fly As Each Layer Properly Compacted in homogeneous Mixture using wooden Dowel Copyright to IJARSCT DOI: 10.48175/IJARSCT-17547 309 www.ijarsct.co.in ISSN (Online) 2581-9429 IJARSCT International Journal of Advanced Research in Science, Communication and Technology (IJARSCT) International Open-Access, Double-Blind, Peer-Reviewed, Refereed, Multidisciplinary Online Journal Impact Factor: 7.53 Volume 4, Issue 5, April 2024 Chopped sugarcane trash is mixed with lime slurry and mixed through by machine or handupto homogeneous mixture observed. This mixture poured into mould in 3 layers, each layer are compacted by wooden dowel. the top surface is finished by trowel. This mould is kept for drying for 24 to 48 hours. Unmould the cube and dried in open air for 21 to 28 days. This process is repeated bye using lime binder. The cube is kept for drying for After unmould cubes are 24 hours and then unmould open dried for 28 days 3. Initial Testing Once we developed a sufficient number of Bio-Bricks, we went for initial testing to understand the fundamental properties and direction for future product development. After a month of air drying, these Bio-Bricks attained their final working strength, and they were ready for the basic physical test such as load-bearing test, thermal insulation test, fire retardant test and water absorption test. 3.1 Density Mass and volume of bio brick measured. Density can be measured by dividing the mass by volume. Bio Bricks Density in kg/ Sample No. 01 644.4 Sample No. 02 636 Sample No. 03 555 Sample No. 04 560.9 3.2 Load-Bearing Test 150mm X 150mm X 150mm size Bio-bricks were selected for the load-bearing test using a compression testing machine. Figure highlights the load-bearing test, and the result confirmed that these Bio-Bricks have very low load- bearing capacities and are not suitable for load-bearing constructions. But can be used as filler walls in frame structure and as a partition wall. Copyright to IJARSCT DOI: 10.48175/IJARSCT-17547 310 www.ijarsct.co.in ISSN (Online) 2581-9429 IJARSCT International Journal of Advanced Research in Science, Communication and Technology (IJARSCT) International Open-Access, Double-Blind, Peer-Reviewed, Refereed, Multidisciplinary Online Journal Impact Factor: 7.53 Volume 4, Issue 5, April 2024 3.3 Water Absorption Test Bio brick Load bearing in n/ Sample 1 0.59 Sample 2 0.54 Sample 3 0.49 Sample 4 0.45 The major component of Bio-Bricks being agro-waste, we wanted to check the effect of water absorption and stability of the block once soaked in water. For this experiment, we used a 150mm X 150mm X 50mm block which was left in a water container for around 24 hours. The Bio-Bricks were checked for deformation and cracks due to water absorption, and it was found to be stable after the period. For water absorption percent- age, the dry weight and the weight after 24- hour soaking was taken the difference of weight divided by the original weight multiplied by100 gave the percentage (Figure 11). Bio brick Water absorption in % Sample 1 51 Sample 2 45 Sample 3 42 Sample 4 44 3.4 Fire Retardant Test This test was vital as we were using a highly flammable material, i.e. dry agro-waste like wheat straw or paddy straw. We had to make sure that the final building material was resistant to fire and reduce the spread of fire. For this experiment, we used a very high-temperature flame of 800 °C using a blow torch and tried to burn from the corner of the Bio-Brick. But to our satisfaction, once the flame was removed after three minutes, the fire died within 5 seconds, and it did not spread to other parts of the block. Figure 10 highlights the sequence of the fire retardant test. Copyright to IJARSCT DOI: 10.48175/IJARSCT-17547 311 www.ijarsct.co.in ISSN (Online) 2581-9429 IJARSCT International Journal of Advanced Research in Science, Communication and Technology (IJARSCT) International Open-Access, Double-Blind, Peer-Reviewed, Refereed, Multidisciplinary Online Journal Impact Factor: 7.53 Volume 4, Issue 5, April 2024 Burned For 3 Minutes Flame Removed Fire died within 3sec. 3.5 Thermal insulation test For this test 150mm X 150mm X 50mm Bio-Brick was used. The idea of the test was to verify if these Bio-Bricks were able to act as thermal insulators and help in reducing thermal gain in buildings. This test was performed using a blow torch and heating one side of the brick with flamefor about three minutes. And the temperature was measured on the both side of the block using anthermometer (Figure 9). The result shows that Bio-Bricks have excellent thermal insulation properties and can be used as insulation boards or panels. Burned for 3 minutes Take reading of burning side Take reading of apposite side – Percentage of therma lResistance of bio brick = 100 Bio brick Thermal Insulation in % Sample 1 24.9 Sample 2 23.6 Sample 3 22.8 Sample 4 19.8 Copyright to IJARSCT DOI: 10.48175/IJARSCT-17547 312 www.ijarsct.co.in ISSN (Online) 2581-9429 IJARSCT International Journal of Advanced Research in Science, Communication and Technology (IJARSCT) International Open-Access, Double-Blind, Peer-Reviewed, Refereed, Multidisciplinary Online Journal Impact Factor: 7.53 Volume 4, Issue 5, April 2024 III. CONCLUSION India is an Agricultural Country & is among second producer of Agricultural Waste in the World. It generates huge amount of Agricultural Waste that needs to disposed. At the same time demand of burnt bricks increases and it produce huge amount of Green House Gases.Based on study it can be conclude that manufacturing of Bio Bricks by Agricultural waste is best way to burning and compost Agricultural waste and it is more beneficial to environment as well as economy when compared to current methods of waste disposal of burning method into open Area. So as per researchBio-Bricks Lightweight, easy to assemble, and affordable. The Compressive Strength of Bio-Brick is very low so, we can use for non-bearing wall.The water absorption is more so, we can use for internal walls. They are easy to install and can be more affordable. They have thermal insulation and fire retardant. By using Agricultural waste in Bio Bricks reduce the burning and also decreases Air Pollution. REFERENCES. Asdrubali, F., D’Alessandro, F. and Schiavoni, S. (2015), “A review of unconventional sustainable building Insulation materials”, Sustainable Materials and Technologies, Elsevier B.V., Vol. 4, pp. 1–17. Armstrong, L. (2015), “Building a sustainable future: The hempcrete revolution”,Www.Cannabusiness.Com, Available at: http://www.cannabusiness.com/news/science-technology/building-a-sustainable-future- thehempcrete-revolution/ (accessed 4 August 2018).. Baig, M. (2010), “Biomass: Turning agricultural waste to green power in India”, Www.Abccarbon.Com Available at: http://abccarbon.com/biomass-turning-agricultural-waste-to-green-power-in-india/ (accessed 20 October 2018).. Zhou, Yi1, AmmarA. M.Al Talib2, Jonathan Yung Chun Ee3(2022), Recycling Of High Density Polyethylene Plastics (Hdpe) Reinforced With Coconut Fibers for Floor Tiles.. Baig, M. (2010), “Biomass: Turning agricultural waste to green power in India”, Www.Abccarbon.Com, available at: http://abccarbon.com/biomass-turning-agricultural-waste-to-green-power-in-india/ (accessed 20 October 2018). Ip, K. and Miller, A. (2012), “Life cycle greenhouse gas emissions of hemp-lime wall constructions in the UK”, Resources, Conservation and Recycling, Elsevier B.V., Vol. 69, pp. 1–9.. Jain, N., Bhatia, A. and Pathak, H. (2014), “Emission of air pollutants from crop residue burning in India”, Aerosol and Air Quality Research, Vol. 14 No. 1, pp. 422–430.. PHFI and CEH. (2017), “Air pollution and health in India : a review of the current evidence and opportunities for the future”, available at: https://www.ceh.org.in/wp-content/uploads/2017/10/Air-Pollution-and-Health- inIndia.. Awoyera, P. O., &Adesina, A. (2020). Plastic wastes to construction products: Status, limitations and future perspective.CaseStudies in Construction Materials, 12, e00330.. Rishav Singh1, Somnath Maity2, SanjirAlam Sk.3 (2022), Manufacturing of plastic tiles from waste plastic materials.. RUSHIKESH MODHE1, YOGESH LONDHE2, PROF. KASHINATH ZAMARE3, PROF.LAXMAN LAHAMGE4 (June 2022), Use Of Plastic Waste for Floor Tiles.. Singh, R. K., &Ruj, B. (2015). Plastic waste management and disposal techniques Indian scenario. International Journal of Plastics Technology, 19(2), 211- 226.. Bamigboye, G. O., Ngene, B. U., Ademola, D., &Jolayemi, J. K. (2019, December). Experimental study on the use of waste polyethylene terephthalate (PET) and river sand in roof tile production. In Journal of Physics: Conference Series (Vol. 1378, p. 042105). IOP Publishing. Copyright to IJARSCT DOI: 10.48175/IJARSCT-17547 313 www.ijarsct.co.in