FSO Supervision, Automation & Control System Manual (PERENCO) 2023 PDF
Document Details
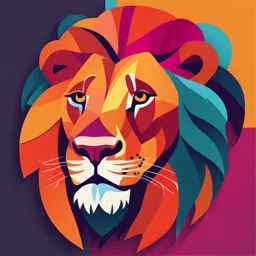
Uploaded by InvincibleWilliamsite5041
2023
Tags
Summary
This is a manual for FSO Supervision, Automation & Control System, specifically for the Campos Basin, Pargo Cluster, Vermelho and Carapeba Fields. It details various aspects of the oil and gas production system, including responsibilities, safety precautions, and system descriptions. The document is a technical manual.
Full Transcript
CAMPOS BASIN OIL & GAS PROUCTION SYSTEM – CAMPOS BASIN, PARGO CLUSTER, PARGO, VERMELHO AND CARAPEBA FIELDS FSO Supervision, Automation & Control System Manual Document number: OPS-FSO-MAN-004 11 January 2023 Revision 04 ...
CAMPOS BASIN OIL & GAS PROUCTION SYSTEM – CAMPOS BASIN, PARGO CLUSTER, PARGO, VERMELHO AND CARAPEBA FIELDS FSO Supervision, Automation & Control System Manual Document number: OPS-FSO-MAN-004 11 January 2023 Revision 04 Supervision, Automation & Control System Document number: OPS-FSO-MAN-004 Date: 11/01/2023 Revision: 04 Revision: Revision Date Last alteration Prepared Revised Approved - Combination of this manual and the 04 11/01/23 old OPS-FSO-MAN-005 FSO Automation QIJI B.JUPAIN B.ROBERT & Control System manual Review few wording and small technical FSOPG DEP DELAHOUSSE 03 03/10/22 QIJI details on document OIM Philippe FSOPG DEP DELAHOUSSE 02 01/07/22 - Updated per Rev 1 internal comment QIJI OIM Philippe - Completed Section 5.2 to Section 8 FSOPG DEP DELAHOUSSE 01 06/05/22 - Updated Section 1 to Section 5.1 with QIJI OIM Philippe latest project and Vendor provided information FSOPG DEP DELAHOUSSE 00 07/01/22 - Document creation QIJI OIM Philippe Uncontrolled copy. This document has no value if printed Page 2 | 56 Supervision, Automation & Control System Document number: OPS-FSO-MAN-004 Date: 11/01/2023 Revision: 04 Table of Contents 1 INTRODUCTION........................................................................................................................ 5 1.1 Project information........................................................................................................................ 5 1.2 Responsibilities.............................................................................................................................. 5 1.2.1 Operations Manager................................................................................................................. 5 1.2.2 OIM........................................................................................................................................... 5 1.2.3 Cargo Supervisor....................................................................................................................... 6 1.2.4 Maintenance Supervisor........................................................................................................... 6 1.2.5 HSE Officer................................................................................................................................ 6 1.3 System function............................................................................................................................. 7 2 SAFETY PRECAUTIONS.............................................................................................................. 7 2.1 Safety precautions......................................................................................................................... 7 2.2 System & operational hazards....................................................................................................... 7 3 REFERENCE DOCUMENTS.......................................................................................................... 8 4 ABBREVIATIONS AND DEFINITIONS......................................................................................... 10 5 SYSTEM DESCRIPTION............................................................................................................ 14 5.1 Overview...................................................................................................................................... 14 5.2 Main items of equipment............................................................................................................ 17 5.2.1 Design parameters.................................................................................................................. 20 5.2.2 Operating parameters............................................................................................................. 20 5.3 Associated items.......................................................................................................................... 26 6 CONTROL AND SAFEGUARDING.............................................................................................. 27 6.1 Philosophy.................................................................................................................................... 27 6.2 System protection devices........................................................................................................... 36 6.3 System trips................................................................................................................................. 37 7 OPERATING PROCEDURES...................................................................................................... 40 7.1 Pre-start checks........................................................................................................................... 40 7.1.1 Valve position check list.......................................................................................................... 40 7.1.2 Instrument check list............................................................................................................... 41 7.2 System start-up............................................................................................................................ 42 7.3 System shutdown......................................................................................................................... 42 7.3.1 Normal shutdown................................................................................................................... 42 7.3.2 Emergency shutdown............................................................................................................. 42 Uncontrolled copy. This document has no value if printed Page 3 | 56 Supervision, Automation & Control System Document number: OPS-FSO-MAN-004 Date: 11/01/2023 Revision: 04 7.4 Routine checks............................................................................................................................. 42 7.5 Troubleshooting........................................................................................................................... 43 7.6 Maintenance – preparation for, performance and reinstatement............................................. 44 8 APPENDIXES........................................................................................................................... 44 Uncontrolled copy. This document has no value if printed Page 4 | 56 Supervision, Automation & Control System Document number: OPS-FSO-MAN-004 Date: 11/01/2023 Revision: 04 1 INTRODUCTION 1.1 Project information FSO Pargo is located 83 km off the coast of Cabo de São Tomé (North Coast of the State of Rio de Janeiro), with a water depth of 93 meters deep. The FSO Pargo, converted from an existing Aframax- type tanker, has a single-point anchoring system with external turret, which allows the vessel to freely align with the resulting surface ocean circulation, minimizing mechanical stresses on the hull. The main features of the Ship are listed below. Ship Type: Aframax with double hull. Total Length = 260.41 m including external Turret and Helideck Length between Perpendiculars = 234.00 m Moulded Breadth = 42.00 m Moulded Depth = 21.00 m Maximum draft = 14.9 m Oil storage capacity is 115,604m3 (727,124.8bbls) @98% 1.2 Responsibilities 1.2.1 Operations Manager The Operations Manager has the overall responsibility and accountability for the safe and efficient operation of the FSO. The Operations Manager liaises with governmental and statutory organization and ensures that the Company complies with all its statutory, national, and international obligations. The Operations Manager implements and manages the Company’s HSE MS & Policy for the FSO operation, ensures it is being effectively implemented by all personnel. He/she maintain a continuous performance review of the FSO operations and take corrective action whenever deficiencies are identified and obtain all necessary technical and professional support for the FSO operation in liaison with Production Management Office, consultants, manufacturers, vendors, and contractors. 1.2.2 OIM The Master / Offshore Installation Manager (OIM) is in overall command and responsible for the safe management of the offshore facility and personnel in accordance with statutory requirements and the company's safety and performance standards. The Master / OIM is ultimately responsible for the safe operation of the unit and for prevention of pollution or damage to the environment. The Master / OIM is empowered in all situations with overriding authority to act decisively and according to his / her best judgment to prevent injury to crew members, other persons and to protect the rig and other vessels property and marine environment from damage. The Master / OIM manages all activities on or about the installation and assures Client's program is accomplished within parameters set by Client. The Master / OIM promotes and ensures that all Company Policies and Procedures are communicated and understood by all personnel on board the installation. Uncontrolled copy. This document has no value if printed Page 5 | 56 Supervision, Automation & Control System Document number: OPS-FSO-MAN-004 Date: 11/01/2023 Revision: 04 1.2.3 Cargo Supervisor The Cargo supervisor is responsible for the safe and proper execution of all marine and cargo operations. The supervisor ensures floater documentation register is up to date, maintains cargo documentation are updated, carry out watch duty during operations, supervise / operate the ballast control systems to always maintain vessel stability, participate in bunkering, lifting, cargo transfer, cargo loading and offloading operations. The Cargo supervisor supervises deck operations, checks all navigation equipment and instruments, maintains firefighting and life-saving equipment, updates the planned maintenance system as directed, checks the GMDSS equipment and ensures that mandatory provisions related to its operation (as specified in the radio regulations) are adhered. He/she also perform duties on the helideck and boat landing, where required, perform functions as identified in the vessel emergency preparedness manual, intervenes and reports in case of unsafe act, unsafe working conditions, near misses and incidents/accidents. 1.2.4 Maintenance Supervisor The maintenance supervisor drives forward the maintenance activity required to minimize risk, makes sure that maintenance of Safety Critical Equipment is executed, and deviations (if any) are reported, and risk assessed, makes sure the planning of maintenance activities and the scope of work of each activity are well described and continuously reviewed and updated, ensures that activities are properly prepared and expedited relentlessly in order to get the job done. This is measured through the amount of unexpected maintenance required and the completion of tasks according to plan. The maintenance supervisor ensures that maintenance activities are carried out according to the management system. He/she also ensures that maintenance "clear and checkable records" are accurate, complete, and up-to-date, actively participate in task risk assessments and daily basis inspects worksite under his/her responsibility. The measure of his/her effectiveness in this will be the amount of rework and the data quality (accuracy, completeness) of the maintenance management system. 1.2.5 HSE Officer The HSE officer supervises operations technical safety engineer for FSO operations, operations HSE (Environment, Health and Safety) engineer for FSO operations and acts as the environmental advisor for offshore operations. The HSE officer provides HSE advise to the Field Asset team and lead in the implementation of company's HSE policy to ensure that FSO operations in the field are conducted safely and in accordance with regulatory requirements and best industry practice. The HSE Officer ensures that corporate policies on HSE and Asset Integrity have specific implementation strategies and plans in place for the FSO Operations, ensure that the FSO HSE/Safety Case requirements are maintained current, the register of Risk Assessments and Major Hazards for FSO Operations and related offshore support activities including those for Sub Sea systems. He/she is responsible for HSE Management system procedures related to FSO Major Hazards, HSE training resources and program including FSO emergency response drills and exercises, development of inspection & audit programmes of all offshore assets, including support vessels, coordination and input Uncontrolled copy. This document has no value if printed Page 6 | 56 Supervision, Automation & Control System Document number: OPS-FSO-MAN-004 Date: 11/01/2023 Revision: 04 into HAZOP studies for FSO processing facilities, ensures that proper functional HSE/safety specifications are set for all HSE Critical equipment in relation to FSO major hazards, ensure that all safety related programmes/ procedures and systems are conducted on all departmental and contracted assets. He/she also liaises with Operations Manager/ FSO Managers / Contractors HSE Managers regarding HSE matters on the unit. 1.3 System function The supervision, automation & control systems are designed to enable users to check and monitor real time data of the various machineries and its performance through a dedicated command centre/space. This is very helpful in making quick and informed decisions pertaining to the safety of the FSO. Since all the data are located at various parts of the FSO, it will be easily accessible to the users through the control system. 2 SAFETY PRECAUTIONS 2.1 Safety precautions This manual is developed by PERENCO to ensure safe and efficient marine operations and cargo transfer onboard FSO PARGO. The manual provides background and technical details that includes but not limited to information related to statutory compliances, local regulations, procedures, recommended practices, ships acceptance procedures and procedures for ship-ship operations. Responsibility for the safe conduct of operations rests jointly with the Master and the crew. However, primary responsibility for the safe conduct of operations onboard the ship rests with the Master. Full co-operation is sought from the Master and crew for the common interests on the safety of people, environmental protection, safeguarding the assets and operations efficiency while FSO PARGO is in service. Manual in reading does not supersede any legislative requirements and it is the responsibility of the Ship’s Master to verify that the latest information regarding the regulations of both local and international regulatory bodies is abiding. Manual in reading does not supersede any commercial or contractual obligation. 2.2 System & operational hazards Most safety precautions are a matter of common sense and good housekeeping. A more detailed hazard and precautions can be found in the various manuals available onboard. The following basic rules must be followed at all times: 1. Never continue to operate any machine or equipment which appears to be unsafe and always report such conditions immediately. 2. Make it a point to test all safety equipment regularly. 3. Never ignore any unusual or suspicious circumstances no matter how trivial. Small symptoms often appear before a major failure occurs. 4. Never underestimate the fire hazard of petroleum products, whether fuel oil or cargo vapour. Uncontrolled copy. This document has no value if printed Page 7 | 56 Supervision, Automation & Control System Document number: OPS-FSO-MAN-004 Date: 11/01/2023 Revision: 04 5. Never start a machine remotely without checking visually first if the machine can be operated satisfactorily. All machineries and equipment onboard are to be operated and handled only by qualified & trained personnel only. Proper PPE and permits are to be used before any work is to be carried out. 3 REFERENCE DOCUMENTS Document Number Document Title FSOPAR-BR-PAR-00-DOR-PH-H-103 FSO Pargo– Control And Shutdown Philosophy E-71 Onboard Test Procedure of Electric Equipment E-32B Instruction Manual for Control Console (ECC&BCC) E-33B Instructions Manual for E-R Alarm & Monitoring System B-13 Machinery Particulars & Maker List M-01 Machinery Arrangement B-01 Final Specification E-73 Onboard Test Procedure for E-R Machinery Control System E-31 Vendor Drawing of Group Control Panel O9 Diagram of gauge and control system E-33A Vendor Drawing of E-R Alarm & Monitoring Systems E-38 Vendor Drawing of Bridge Control Console Uncontrolled copy. This document has no value if printed Page 8 | 56 Supervision, Automation & Control System Document number: OPS-FSO-MAN-004 Date: 11/01/2023 Revision: 04 E-32A Vendor Drawing of Engine Control Console E-42A Vendor Drawing of Fire Detection System FSOPAR-BR-PAR-00-ODS-DW-J-031 ODS System Block Diagram General FSOPAR-BR-PAR-00-ODS-IM-J-003 ODS Operating Manual Metering Control Panel PG1158-00-E02.001 ODS System block Diagram FSOPAR-BR-PAR-00-DDW-DW-O-004 Hose reel arrangement drawing FSOPAR-BR-PAR-00-DDW-DW-Q-005 Arrangement drawing – Hose reel hydraulic tubing FSOPAR-BR-PAR-00-DDW-PI-Q-004 Extension of deck machinery hydraulic system for hose reel FSOPAR-BR-PAR-00-INC-IM-O-001 FSO PARGO Hose Reel O&M Manual FSOPAR-BR-PAR-00-INC-PI-O-001 FSO PARGO Hose reel hydraulic circuit & service connection details FSOPAR-BR-PAR-00-INC-SP-O-001 FSO PARGO Hose reel functional specification FSOPAR-BR-PAR-00-DDW-ES-N-002 Rev.02 Heli deck lighting single line diagram FSOPAR-BR-PAR-00-MAM-DW-N-001 Electrical Drawings Local Control Panel & HPU FSOPAR-BR-PAR-00-MAM-IM-O-001 Installation, Operating and Maintenance Manual Uncontrolled copy. This document has no value if printed Page 9 | 56 Supervision, Automation & Control System Document number: OPS-FSO-MAN-004 Date: 11/01/2023 Revision: 04 4 ABBREVIATIONS AND DEFINITIONS Oil tanker for the transport of crude oil DWT from 80,000 to 120,000 Aframax MT ANP National Petroleum Agency. API American Petroleum Institute. BCSS Underwater submerged centrifugal pump BDV Blow down valve Wise Basement / Sewer Port side Left side of a ship, deck, etc. Starboard side Right side of a ship, deck, etc. Safety Briefings Security meetings Basic Sediments and Water. Sediment and water content present in BSW the oil produced. Bureau Veritas Company responsible for the Classification of the Vessel Height of a vessel that lies below the waterline, during operation or in Draft transit. ECR Engine Control Room CCR Cargo Control Room Peak tanks Water ballast tank (1 forward and 1 aft) CIS – Control & Interlock Control System: It is based on the use of Programmable Interconnected System Logic Controllers (PLCs) to perform control and interlock functions. Uncontrolled copy. This document has no value if printed Page 10 | 56 Supervision, Automation & Control System Document number: OPS-FSO-MAN-004 Date: 11/01/2023 Revision: 04 PLC Programmable Logic Controller. COW Crude oil used for Washing Dampers Vent hatches Decks Different levels of a unit (Main deck, Upper deck, Bridge deck…) Demister Filter type PPE Personal Protective Equipment. ESD - Emergency Shut Security Outage System Down FLARE Torch / Gas burner of the platform. Flowline Underwater lines (Floating, Storage and Offloading) Floating production, storage and FSO transfer unit. Helipad - Demarcated area, intended for the landing and takeoff of Helideck helicopters. Helipad Area of the unit intended for the transit of aircraft (helicopters). Brazilian Institute of the Environment and Renewable Natural IBAMA Resources. ICSS – Integrated Control Integrated Control and Security System & Safety System H2S Hydrogen Sulfide HMI Human Machine Interface Uncontrolled copy. This document has no value if printed Page 11 | 56 Supervision, Automation & Control System Document number: OPS-FSO-MAN-004 Date: 11/01/2023 Revision: 04 ISGOTT International Safety Guide for Oil Tankers and Terminals Astronomical water (LDA) - Vertical distance of a reference level, specified in relation to a slide, at the bottom of "DATUM" of the tide. the sea Flexible oil transfer pipe (off-loading) to the relieving ship or to an Hose FSO. Equipment located in the ocean bed whose objective is the equalization of the different pressures of the flows of each of the Manifold wells, before sending them to the production lines. Similarly, this equipment controls the flow of wells. MBL – maximum Minimum Value of Material Break load. breaking load. MCA Meters of water column. No-Breaks Uninterrupted Power Source OCIMF Oil Companies International Marine Forum. Product transfer operation between the vessel storer and the Offloading relieving vessel. Offshore Relating to genuinely oceanic activities. OIM Offshore Installation Manager PA/GA Public Address and General Alarm Pipeline End Manifold - equipment that allows the connection of PLEM multiple lines. Pipeline End Termination: Structure installed at the end of the subsea ducts in order to allow the connection of this duct with the riser – or PLET other stretch of subsea duct – and that has a valve system to control the flow of products in circulation. Uncontrolled copy. This document has no value if printed Page 12 | 56 Supervision, Automation & Control System Document number: OPS-FSO-MAN-004 Date: 11/01/2023 Revision: 04 PMS Power management System PPM Particle per Million PSD – Process Shut Process stoppage system Down Flexible line stretch, or steel duct, used to overcome the water slide, Riser thus being suspended between the seabed and the platform and assuming appropriate geometries for each project. Header Distributor ROV Remotely Operated Vehicle. SCR Remote Control Room Scrubber Separator Glass SDV – Shut down valve Emergency valve System composed of flow lines and underwater structures, among Submarine System which stand out the Christmas trees. Slop Residue Geometric configuration of the riser characterized by two stretches with accentuated curvatures, the first from the PLET with the Steep Wave installation of several buoys to obtain fluctuation, and the second without fluctuation until the connection with the platform. Stripping Remove / Empty Rotating chamber installed on the center line and at the top of the Turret that aims to allow the transfer of products (process and Swivel do Turret utilities), energy and signals between the geostatic part and the rotating part of the Turret. The number of functions depends on the design and use of the converted or built tank ship. Uncontrolled copy. This document has no value if printed Page 13 | 56 Supervision, Automation & Control System Document number: OPS-FSO-MAN-004 Date: 11/01/2023 Revision: 04 Arrangement of cable mooring between two ships, on the bow with bow or stern with stern. Specifically for this document, it is the Tandem (mooring) mooring arrangement between the bow of a conventional oil tanker and the stern of the FSO. Cylindrical structure anchored composed of a bearing system that allows a Tanker, attached to this structure, rotate freely to align with Turret the resulting environmental forces. It can be of the internal and external type, when it is installed on the hull of the ship and in a structure designed outside the hull of the ship respectively. UPS (Uninterrupted Power Supply) Uninterrupted Power System USD Unit Shut Down - System or equipment stop VMS Vessel management System. XV – Shut off Closing valve 5 SYSTEM DESCRIPTION 5.1 Overview Control and Supervision System for legacy systems (systems that were existing in the donor vessel Minerva Nike) are left as is where is and the same systems are used in the FSO Pargo. Please see Minerva Nike document O9 Diagram of gauge and control system. In addition, new conversion items installed such as Helideck, Offloading, Mooring, QRH, Laboratory, Metering have their own supervision and remote monitoring system. In all cases, it is not possible to control the “conversion” systems through the existing Kongsberg Datachief and all controls are local or on a dedicated panel provided by respective suppliers. For more details, please refer to Section 6 of respective manuals listed below in Table 1. Uncontrolled copy. This document has no value if printed Page 14 | 56 Supervision, Automation & Control System Document number: OPS-FSO-MAN-004 Date: 11/01/2023 Revision: 04 Table 1 - Conversion Equipment/System Manuals Name of Equipment Operating Manuals Metering Control System Refer to OPS-FSO-MAN-016 Aluminium Helideck and Refer to & OPS-FSO-MAN-019 Helicopter Monitoring system Offloading Hose Reel Refer to OPS-FSO-MAN-015 Quick Release hook control Refer to Installation Operation Maintenance Manual FSOPAR-BR-PAR- panel 00-MAM-IM-O-001 Laboratory Control Panel Refer to OPS-FSO-MAN-018 & Operation manual FSOPAR-BR-PAR-00- TLS-IM-F-001 External Turret Refer to OPS-FSO-MAN-013 Supervision systems enable real-time monitoring of FSO operational parameters from the ER & Cargo Control room (Cargo load/discharge control, Power generation, SW ballast management, Steam generation, Fire & Gas detection, etc.) and helps assign an immediate response in case of deviation of parameters above the set points according to the safety matrix approved by the classifier company. In addition, the stop of individual equipment can be generated automatically through automation systems, depending on their safety matrices, or manually by operators through local shutdown buttons. Uncontrolled copy. This document has no value if printed Page 15 | 56 Supervision, Automation & Control System Document number: OPS-FSO-MAN-004 Date: 11/01/2023 Revision: 04 Figure 1 - DATACHIEF C20 ALARM & MONITORING SYSTEM Cargo operations on FSO PARGO are automated, monitored, supervised, and operated from the Control Room. The volume of the tanks is monitored by the Loadmaster program, which is integrated into the PLC panels. This allows the operator to control pumps start/stop, valves opening/closing for cargo loading & discharge, SW ballast management, FW & Fuel bunkering to be done remotely and automatically. As safety measures, there are pressure, temperature, ullage, and volume information of all tanks in the Control Room. There is high pressure, low pressure, ullage, high- & low-level alarms fitted for all tanks and also sensors. In addition to emergency stop buttons provided at key areas. For the ER side, the more detailed performance and data on the main engines and diesel engines can be monitored thru the KYMA-PFS system installed in the ER control room. FSO Pargo has the following main automation systems: Table 2 – Main automation systems on FSO Pargo System Equipment Ballast tank gas detection system Salwico SW 2020 KVC-41 / 3 Load control system Load Master software Uncontrolled copy. This document has no value if printed Page 16 | 56 Supervision, Automation & Control System Document number: OPS-FSO-MAN-004 Date: 11/01/2023 Revision: 04 Datachief C-20, ER Deadman alarm Machine space control system system, Bridge watch monitoring system Fire detection system Consilium CS 3004 The Donor vessel marine automation system consists of machinery control & monitoring system and cargo control & monitoring system. The main purpose of the system is to give ship's engineers and/or officers all the basic alarms and status information to maintain safe and efficient operation of the machinery and cargo equipment. The schematics of all control systems inherited from Donor vessel is provided in the Appendix below, details can be found in O9 Diagram of gauge and control system Marine automation systems have capabilities of providing requirements such as: Alarm and monitoring Tank level indication Engine/ auxiliary/generator control Remote diagnostics System integration according to clients' preference Cost Efficiency Saving labour costs through unmanned operation Improved maintenance by self-diagnostic features Integration of engineer calling system Extension alarm system and fire alarm indication Flexibility Easy configuration of signals and functions Open platform for interfacing to external systems Modular design for easy adoption/extension Cargo alarm system whether as integrated or stand-alone solution If necessary, the FSO commander can trigger the closure of the PPG-1A oil receiving subsea valve through a dedicated panel or abandon the ship through the general alarm system (PA/GA) following the FSO's emergency procedures. 5.2 Main items of equipment Machinery Space On FSO Pargo the engine control room is equipped with various automation and control system such as Datachief C20 system, ER Deadman alarm system, Bridge watch monitoring system, Boiler management system, Fire detection System (including water mist system) and Power Management System. The Datachief C20 system provides the user with all the various systems and its parameters linked to it. This allows the user to remotely monitor the systems and make necessary adjustments manually or automatically. There are various types of sensors and control PLCs located and integrated into the systems to achieve this. Some examples of these are: Auto start/stop of diesel engines to meet power and safety requirement of the FSO Uncontrolled copy. This document has no value if printed Page 17 | 56 Supervision, Automation & Control System Document number: OPS-FSO-MAN-004 Date: 11/01/2023 Revision: 04 Monitoring and level alarms of all the fuel, water, and waste tanks in ER Boiler firing management to maintain its pressure and steam consumption demands Automatic top up of feed water levels in the boiler in relation with boiler water level alarms Automatic activation of the steam dumping system when there is a variation of steam loads on the boiler. Opening & closing of various pneumatic/hydraulic valves in ER Automatic operation for auxiliary machineries (Purifier, OWS, air compressors etc.) Visual & Audible alarm systems The fire detection system on board is automatically linked to the start/stop of emergency machineries. For example, the water mist system pumps and sprinklers are activated when both the smoke and heat detectors are activated together at key areas in the ER. Figure 2 – DataChief20 Components Uncontrolled copy. This document has no value if printed Page 18 | 56 Supervision, Automation & Control System Document number: OPS-FSO-MAN-004 Date: 11/01/2023 Revision: 04 Figure 3 – DataChief C20 Alarm & Monitoring System External Cable Diagram Cargo Operation The cargo operation on the FSO Pargo is monitored from the Cargo Control Room (CCR). It is equipped with the Loadmaster program to monitor cargo and ballast operations. This system allows users to receive or discharge cargo and at the same time maintain the stability of the FSO by adjusting the ballast system. There are various types of sensors, control PLCs located and integrated into the systems to achieve this. Some examples of these are: Starting/Stopping of cargo pumps Starting/Stopping of ballast pumps Operating suction & discharge valves for cargo & ballast tanks Monitoring tank pressures with high/low alarms Monitoring cargo & ballast tank levels with high/low alarms Automatic venting of tanks Emergency stops for cargo operations Accurate flow readings for cargo load/discharge Integrated safety systems such as fire detection system, H2S detection system, gas detection systems etc. Visual & audible alarms system Uncontrolled copy. This document has no value if printed Page 19 | 56 Supervision, Automation & Control System Document number: OPS-FSO-MAN-004 Date: 11/01/2023 Revision: 04 5.2.1 Design parameters Supervision systems are designed based on the capability to ensure monitoring can be executed remotely and there is no need of constant manning. Sensors and indications are the primary source of information provider for the supervision and control system. Sensors fitted must be in a close loop with the indication system for the operator to be able to receive information and initialised inputs based on the situation. The outputs of supervision vision must be in the form of alarms fitted as a triggering mechanism. The FSO CCR and ECR will be manned 24hours in a day. It is possible that the ECR is minimally manned during the night shifts when there are no major operations carried out. The watchkeeping personal will be able to take quick response to wards any issues or emergencies. If not addressed, the alarms will be escalated to duty engineers’ cabin and subsequently to the bridge after the designated time. Automatic control, remote operation and central supervision is so designed that the propulsion plant is operated with unmanned engine room under normal conditions at open water except starting up and finishing of the plant. One (1) control room is arranged in the engine room, where the control console of main engine and the main switchboard is installed. The main engine is remotely operated from wheelhouse and engine control room. The machine side control of main engine is provided for emergency use. The instrument gauge and alarm are arranged in good order for safety operation and easy maintenance. Automatic combustion control and equipment concerned with boiler is arranged adjacent to the boiler. Automatic controllers and control valves are provided on principal systems for safety operation and easy maintenance. When the measuring value of the system is high or low from the predetermined value, a buzzer sound and the alarm indication to flicker for the operator's attention. An engine officer calling alarm system is fitted to each engine officer's cabin to call a watch-keeper for watches or in emergency. The alarms must have suitable audible/visible alarms throughout the engine room as well as the control room. 5.2.2 Operating parameters Item Operating Parameter All instruments are of suitable construction for maximum operating value and is of graduations in metric units. Temperature sensor for remote reading and supervision is of the electric analogue type. Thermometers and temperature sensor for monitoring of fluid temperature only is equipped with pockets of suitable materials Instrument or is element exchangeable type. Local pressure gauges are of the Bourdon type with body of brass or SUS. Three-way test valve is provided for pressure switches and transmitters. Uncontrolled copy. This document has no value if printed Page 20 | 56 Supervision, Automation & Control System Document number: OPS-FSO-MAN-004 Date: 11/01/2023 Revision: 04 Remote level indication for settling tank, service tanks and M.D.O. storage tanks is of air purge type and the repeated indicating signal is used for local level indication and pressure indication is of the pneumatic * pressure transmitter type. In general, local control loops for temperature, pressure and level control is of the pneumatic cylinder type or diaphragm type, but for some minor purposes, wax Control Valves type or self-contained type valves may be used. All pneumatic control loops to have air filter regulators. Remote Valve Control System 1. This system is used for remotely controlling deck valves, from the CCR, by using high pressure hydraulic to operate the valves. Signal from the CCR will be sent to a control cabinet, and it will further transmit a signal to the hydraulic solenoid 2. These valves include cargo valves, ballast valves, engine room sea chest valves Cargo Control etc, where the valves are of big size. Console Cargo Pumping System 1. This system is the control of the cargo operated pump turbine (COPT) from the CCR, includes starting, stopping, sudden trips or alarms. 2. The signal will be given from the CCR, then to the COPT group board and transmit the signal to the cargo pump. Alarms will be triggered to the COPT group board and shown at the CCR. This equipment is operated on AC 220 V, 3 phase, 60 Hz and 24V DC power and installed in the Engine Control Room for remote control of the main and auxiliary engines in the engine room, continuous monitoring of their pressure and temperatures and alarming of any fault condition thereof. The provisions are provided with necessary control levers, push buttons and switches required for control and monitoring of operating conditions of the engines. This equipment is manufactured to the requirements Power Supply System Engine Control 1. The power source of ECR Console used in this vessel is AC 220V, 3 phases, 60 Hz Console from MSBD and DC 24 V from Battery charger. 2. In case of DC 24 V, there are two kinds. One is converted from AC 220V, 3 phase, and 60Hz by transformer and rectifier, which used to main control power. The other is stand-by power from battery charger, which used to console when the main DC 24V power be failed. 3. When AC 220V from MSBD or DC 24V from battery charger fails, the power failure alarm occurs and extended to cabin and public accommodation by monitoring system. Uncontrolled copy. This document has no value if printed Page 21 | 56 Supervision, Automation & Control System Document number: OPS-FSO-MAN-004 Date: 11/01/2023 Revision: 04 4. Fuses are provided in each branch feeders of AC and DC to protect each equipment or device. 5. Receptacles are provided on left and right side of console each one for the purpose of maintenance. 6. Regarding the detailed circuit, refer to the Drawings. Test Circuits 1. Lamp Test: When the test switch is set to the "LAMP" position, all lamps in the console will light up if they are all in good order. It is recommended to carry out this testing once every day for right monitoring operations. 2. Buzzer: Test When the test switch is set to the "BZ" position, buzzer in the console will ring if it is on good order. It is recommended to carry out this testing once every day for right monitoring operation. Alarm System 1. As soon as an abnormal condition occurs, the alarm status mark starts to flicker and buzzer to sound. 2. The abnormal condition disappears, but the alarm status mark is still flickering and the buzzer sounding. 3. The buzzer stops operating silences the buzzer, but the alarm status mark is still flickering. 4. The flicker reset operation erases the alarm status mark. 5. As soon as another abnormal condition occurs, the alarm status mark starts to flicker and the buzzer to sound. 6. The buzzer stop operation silences the buzzer, but the alarm status mark is still flickering. 7. The abnormal condition disappears, but the alarm status mark is still flickering. 8. The flicker-reset operation erased the alarm status mark. 9. As soon as still another abnormal condition occurs, the alarm status mark starts to flicker and the buzzer to sound. 10. The buzzer stop operation silences the buzzer but the alarm status mark continuous to flicker. 11. The flicker reset operation silences the buzzer status mark to indicate steadily. 12. As soon as the abnormal condition disappears the alarm status mark goes out. Engineer Calling System Uncontrolled copy. This document has no value if printed Page 22 | 56 Supervision, Automation & Control System Document number: OPS-FSO-MAN-004 Date: 11/01/2023 Revision: 04 1. Concept - This system is used to call other engineer to ECR when the engineer on working at local needs help or he found the abnormal condition of machinery. 2. Procedure - In ECR the selector switch must be indicated to calling position and push the "CALL" button, then calling signal will be informed to cabin or public room. Then the buzzer of calling box in room sound and the lamp light. - The engineer in cabin room or public room pushes the "ACCEPT" button on calling box to inform the acknowledgement then the buzzer sounding, and lamp lighting are stopped and the accept signal will be informed to ECR by lamp lighting on console. - The engineer in ECR push the "ACCEPT" button, then lamp light will be off. When calling action is finished, the position of selector switch must be positioned to "OFF". 3. Procedure - There is one more function in the system, which is that when the failure of extension alarm system take place, the alarm signal is informed to all room automatically regardless selector switch position. In this case, acknowledgement action is same as manual calling system Patrol Calling System This system is used to patrol engineer in local area in order to announce the machinery alarm or telephone signal and there are three positions. 1. Patrol Position When the engineer in the engine control room left to local area, the selector switch must be indicated to this position, hi this position, machinery alarm and telephone signal occurred in ECR are extended to air horns and strobe lights installed in local area in order to inform the engineer on patrol. 2. Call Position This position is used when other man wants to call the engineer on patrol or on working in local area. 3. Off position the engineer must change the selector switch to this position when he finished the patrol. If not, the lifetime of air horn and strobe light will be reduced due to long time operating till acknowledgement whenever alarm occur. Pressure Indicating System 1. Concept, as for the important points the individual meters should be installed on console to monitor easily by class regulation. 2. Operating The pressure is measured by 4-20mA exhausted from pressure transmitter at machinery side Main Engine Control System 1. Main engine control system is used for automatic remote control and protection of main ship's diesels. It permits to change direction and speed rotation of propeller directly from the bridge by navigators. The system Uncontrolled copy. This document has no value if printed Page 23 | 56 Supervision, Automation & Control System Document number: OPS-FSO-MAN-004 Date: 11/01/2023 Revision: 04 consists of the equipment installed on the bridge; engine control room (ECR) locally mounted near the engine. 2. The set of Engine Remote Control equipment in ECR essentially consists of a panel fitted up with the various signalling, alarm and control facilities, in addition to the electronic modules (both logic and analog). Generator Engine Control System 1. Generator engine control system is used for automatic control of the generator and protection of the machinery which is used to power the ship. 2. The following system will be able to trigger alarms to the ECR from its fitted sensors on the generator. This will also provide an interlock for synchronizing the generators when parameters are achieved. Auxiliary and Composite Boiler Control System 1. This system enables the control of the boilers remotely, where it is starting of fuel pump or firing burners. 2. Alarms from the boiler will trigger to the ECR and have the tendency to trip the boilers when parameters are off range. 3. The controls of boiler valves remotely when signal is given to the cabinet and control of the solenoid cabinet therefore operating the valves. This equipment is operated on AC 220 V, 3 phase, 60 Hz and 24V DC power and installed in the wheelhouse for remote control of the main engine, satellite communication and for monitoring of steering gear condition. The provisions are provided with emergency stop push button to stop various fan or pump when fire and, with dimming control device to prevent from the light leakage to outside in night-time. Power Supply System 1. The power source of Bridge Console used in this vessel is AC 220V, 3 phases, 60 Hz from MSBD and DC 24 V from Battery charger. Bridge Console 2. In case of DC 24 V, there are two kinds. One is converted from AC 220V, 3 phase, and 60Hz by transformer and rectifier, which used to main control power The other is stand-by power from battery charger, which used to console when the main DC 24V power be failed. 3. When AC 220V from MSBD or DC 24V from battery charger is failed, the power failure alarm is occurred and extended to cabin and public accommodation by monitoring system. 4. Fuses are provided in each branch feeders of AC and DC to protect each equipment or device. Uncontrolled copy. This document has no value if printed Page 24 | 56 Supervision, Automation & Control System Document number: OPS-FSO-MAN-004 Date: 11/01/2023 Revision: 04 5. Receptacles are provided on left and right side of console each one for the purpose of maintenance. 6. Regarding the detailed circuit, refer to the Drawings. Alarm System of Bridge 1. Some alarms occurred in the machinery space will be transferred to W/H through monitoring system located in engine control room (ECR). This alarm will be detected in extension alarm panel installed on Bridge Console. This alarm is only group alarm, but it can be confirmed at ECR in detail. 2. While there are some independent alarms of W/H itself using by annunciator relay regardless monitoring system. When this alarm is occurred, the lamp lighting starts to flicker and buzzer to sound. Others in acknowledgement are same as monitoring system. Emergency Stop System 1. When fire occurred in the engine room or accommodation, pumps and fans must be stopped to prevent from fire enlargement. So, the remote push buttons are used for the purpose of control the related equipment. 2. How to use in that, when fire be taken place, push the appropriate push button after opening the cover which is named on EM'CY STOP S/W. When do release the emergency condition, turn the push button to arrow marked on the upper side of push button. Helicopter Monitoring System 1. The helideck monitoring system are designed to measure all weather conditions during helicopter landing and take-off operations in order to improve both flight and passenger safety. 2. This system consists of multiple sensors (visibility, wind, motion etc) that will be transmitted to the interface cabinet. 3. Fitted together is a 2.2 kVA UPS SEP 2200 in case of a black out in the power management system. Metering Control System 1. The metering system is designed to accurately measure the amount transferred product during transport from the FSO Pargo. 2. The metering skid consist of multiple metering runs, each with a turbine flowmeter and a temperature and pressure transmitter for temperature and pressure compensation 3. The metering skid is designed for a specific flow direction Uncontrolled copy. This document has no value if printed Page 25 | 56 Supervision, Automation & Control System Document number: OPS-FSO-MAN-004 Date: 11/01/2023 Revision: 04 5.3 Associated items Name of Equipment Model and Type Quantity Particulars E/R Alarm & Datachief-C20 Consisting 1 Refer to E-33B Instruction Manual Monitoring System of 2EA MCU, 2EA DPI for E-R Alarm & Monitoring Cabinet, 3EA CRT with System. This document describes keyboard and 2EA Printer in detail on the Datachief-C20’s specifications, maintenance, etc. Fire Detection Salwico CS3004 1 E-42A Vendor Drawing of Fire System Detection System, this document contains all the detail particulars for the Salwico CS3004 fire detection system Metering Control ODS 1 Refer to Operating manual System Metering Control Panel FSOPAR- BR-PAR-00-ODS-IM-J-003 Aluminium Helideck Helitecnica & Shore 1 Refer to Helideck Installation and Helicopter Connection Manual 00-HEL-IM-F-001 Monitoring system Offloading Hose Trelleborg 1 Refer to manual Installation Reel Operation Maintenance FSOPAR- BR-PAR-00-TRE-IM-Q-001 Quick Release hook Mampaey 1 Refer to Installation Operation control panel Maintenance Manual FSOPAR-BR- PAR-00-MAM-IM-O-001 Laboratory Control TLS Offshore Containers 1 Refer to Operation manual Panel FSOPAR-BR-PAR-00-TLS-IM-F-001 Inert Gas System KASHIWA CO. LTD 1 Refer to Operation Manual OPS- Control Panel FSO-MAN-023 Boiler Control Hyundai Heavy Ind. Co. Ltd 1 Refer to Operation Manual OPS- Console FSO-MAN-024 Uncontrolled copy. This document has no value if printed Page 26 | 56 Supervision, Automation & Control System Document number: OPS-FSO-MAN-004 Date: 11/01/2023 Revision: 04 6 CONTROL AND SAFEGUARDING 6.1 Philosophy Engine Control Console Early warning signals provide a further benefit for the continuous monitoring of propulsion components. These can indicate the overload stress on components and thus prevent an unexpected breakdown. Supervision systems help to achieve optimum operation without overloading can also prolong the operating life of components -giving. With each tank fitted with sensors, the operator can should be able to receive real time information such as levels, temperature, pressure, etc. With supervision and control systems, operators remotely control the FSOs substation and supervise the status of the vessel. In the FSO, it is important to control, management, monitor for power distribution system. Supervision and control systems can effectively reduce the possibility of accidents and the loss of finance. Through supervision and control system, the operator does not need to go to the site to check the status of the device. He can monitor and manage the device in the control room. Meanwhile, the tables, historical trends and reports will be generated rapidly and accurately. The system has run in the factory substation of oil refinery. The results are shown that the data is correct, and operation is easy. Full monitoring and alarm facilities are provided both in the machinery space and in the Engine Control Room (ECR). Sufficient facilities are also provided for machinery watch on the Bridge, and a Watch-calling subsystem enables engineers to be automatically called to the ECR when they are on watch-call duty in their quarters. Thus, both the machinery and the ECR may safely be left unmanned, while machinery watch is carried out on the Bridge The main purpose of the system is to give ship's officers all the basic alarms and status information they require to maintain safe and efficient operation of the machinery. The system is designed to meet the classification society's requirements for periodically unmanned engine room operation. The design conforms to all rules and regulations, and all modules are type approved. Cargo Operation and Bridge Watchkeeping Cargo alarms will sound either at the cargo control room or bridge. These alarms will usually be related to the machineries on deck, cargo tank level, ballast tank level and etc. During operations ongoing, the CCR will be manned, therefore alarms of any kind will be accepted and acknowledged. At the bridge, for the watchkeepers during watch, a Bridge Navigational Watch & Alarm System (BNWAS) is fitted as a monitoring and alarm system which notifies other navigational officers or master if the officer on watch (OOW) does not respond. This system is similar to the dead man alarm in the engine room. In FSO function, the bridge will be minimally manned in accordance with Perenco Safe Manning philosophy. Uncontrolled copy. This document has no value if printed Page 27 | 56 Supervision, Automation & Control System Document number: OPS-FSO-MAN-004 Date: 11/01/2023 Revision: 04 Metering Control System The meter skids are designed to measure Crude Oil with a maximum design export flow rate of 3,000 m³/h at 10 bars inlet average pressure and 15 bars maximum. The total system flow will be distributed by the inlet header to a certain number of parallel metering unit on stream and one dedicated spare. Turbine meter system or equivalent will be considered. A custody transfer metering system is supplied for flow measurement of offloading with permissible expanded uncertainty for metering system as per OTSL R117/ Inmetro no. 64 Class 0.3. The system consists of three custody transfer flow meters in a 3 x 50% configuration. Each meter run will be provided with inlet valves, strainer, thermal relief valve, flow conditioner, helical turbine meter, pressure transmitter, temperature transmitter, balancing valve, prover connection valve and outlet valve. One automatic flow proportional sampling system, one BS&W analyzer and one density analyzer is provided on the common outlet header. A skid with three metering streams and prover is provided with integral power. The skid will be complete in all aspects, e.g., instrumentation, structural, piping, and other associated related works clearly defining in the tie in detail. Double block and bleed valves will be used to ensure positive isolation. Figure 4 - Metering Skid Connection A Metering Control System (MCS) is supplied for location in an air-conditioned safe area. The architecture designed by ODS Metering Systems consists of: o Metering Control Panel, including Flow Computers, Supervisory computer, PLC system, network equipment, etc. o Desk mounted HMI for operator interface, database management, meter validation, etc. Uncontrolled copy. This document has no value if printed Page 28 | 56 Supervision, Automation & Control System Document number: OPS-FSO-MAN-004 Date: 11/01/2023 Revision: 04 ODS has tried to minimize the number of components and interfaces of the metering control system without affecting the performance or operability of the system. Because of the number of metering signals, BS&W, density signals and required sample control we have designed the system with multi-stream flow computers and a PLC system. All measuring streams will be routed to the Metering Panel. The flow computers will be rack mounted on a swing frame panel with a see-through Perspex type door will be provided with a key lock to prevent non-authorized personnel access to the flow computers. The metering control panel consists of the following components: o Flow Computers Each meter stream will be connected with a flow computer rack, consisting of stream flow computers. There will be a dedicated flow computer for each flow meter, therefore a total of tree flow computers are included. The Flow-X/R stream flow module contains a fast microprocessor, adequate memory and all analogue and digital inputs and outputs to support a full single metering stream for both gas and liquid applications. o PLC system The PLC will be used for line-up and control of the valves. In addition, the PLC system will be used to collect the data from the automatic sampler; collect data from the BS&W analyzer; calculate station data, proportional flow control of the sampler; and manual initiation of verification for the Oil Offloading Runs. o HMI / supervisory system The HMI/Supervisory computer is the master control unit for co-ordination of the metering system functions. The supervisory computer is in the Meter Control Cabinet and the display will be stand-alone next to the cabinet. In the normal method of operation (Computer Automatic Mode) all the metering system functions are monitored and controlled from the HMI/Supervisory computer. The HMI Software Package includes alarm management, report generation and real time and historic trends. Helideck Monitoring System The Helideck Monitoring System (HMS) is used to analyze helideck motion during helicopter landings to improve safety in hostile weather conditions. The HMS sensor locations to be in accordance with Normam 27. The HMS monitors helideck attitude and vertical velocity, wind speed and direction, air temperature and barometric pressure and presents this information to indicate landing conditions. A complete panel is provided at the Wheelhouse to accommodate the lighting panel, fire alarms and is also supplied by a UPS in case a power failure occurs. The radio Room to be allocated as the space to install all necessary equipment for Helideck and Marine communication. The radio must be homologated by Anatel. The radio room must be equipped with two unities of VHF air band trans receiver and one unity of portable VHF air band. The HMS screen is installed in the Radio room to allow radio operator to inform the condition of Helideck to chopper. The HMS contains an air temperature sensor, wind sensor for speed Uncontrolled copy. This document has no value if printed Page 29 | 56 Supervision, Automation & Control System Document number: OPS-FSO-MAN-004 Date: 11/01/2023 Revision: 04 and direction, and MRU info (roll, pitch, and heave). The HMS screen must always show the images of Helideck. The camera is used to monitor and record all the approximation, landing and take-off choppers. The audio recording system is utilized to record all audios of the two VHF air Band Transceiver. The NVR has the capacity to keep records of audio and video for at least 90 days. Figure 5 - Helideck sensors fittings for HMS Uncontrolled copy. This document has no value if printed Page 30 | 56 Supervision, Automation & Control System Document number: OPS-FSO-MAN-004 Date: 11/01/2023 Revision: 04 Figure 6 - Lighting Panel board associated for Helideck Offloading Hose Reel The hose reel is installed on the aft deck of the FSO Pargo and is designed for the storage, pay- out and pay-in of the offloading hose. The hose reel drum is rigidly connected to the slew ring (via the spokes and drive-end hub), which is driven by four pinions. Each pinion is housed by a gearbox which is controlled by a hydraulic motor. The hose reel control system is used to control the hose reel operations for pay-in and pay-out of the hose. The hose reel equipment is controlled via manual operation of the joystick levers. The control console is used to control the movement of the hose reel. The hose reel is driven by 4 hydraulic motors which turn the slew ring. The motors can rotate the drum in the pay-in and pay-out directions, as well as stopping the hose with the disk brake each gearbox has. The movement is controlled by a joystick on the control console, and its speed increases as the joystick is moved further towards the up/down positions. The central position of the joystick is the neutral position where the hose reel has stopped rotating and the hydraulic motor brakes are applied. As the joystick is moved towards the neutral position each motor slows down, the rotation stops once the joystick reaches the central position and the hydraulic brakes are applied. Uncontrolled copy. This document has no value if printed Page 31 | 56 Supervision, Automation & Control System Document number: OPS-FSO-MAN-004 Date: 11/01/2023 Revision: 04 Figure 7 - The Console display The control console manages the movement of the hose reel spooler via a hydraulic cylinder, which is located under the drum at the back end of the spooler frame. The movement is controlled by a joystick on the control console, and it moves towards the idle/drive end as the joystick is moved towards the up/down positions. The spooler and hydraulic cylinder arrangement are configured so that the cylinder rod is fully retracted when the hose is completely paid out or paid in. Hydraulic power unit control panel is in Steering Gear room. Emergency Stop Function An emergency stop function is provided by a hydraulic isolation valve. When the valve is operated at the control console, the flow of hydraulic fluid is cut off from the hose reel system, the brakes are engaged, and the hose reel stops rotating. The hydraulic power for the hose reel and hose reel spooler is provided by the vessel hydraulic power system. Before commencing hose reel operations, reference should be made to the vessel operating procedures to ensure that adequate hydraulic pressure and power is available. Uncontrolled copy. This document has no value if printed Page 32 | 56 Supervision, Automation & Control System Document number: OPS-FSO-MAN-004 Date: 11/01/2023 Revision: 04 Figure 8 - Offloading Hose reel control panel and associated equipment Quick Release Hook Control Panel The system is designed to cast off the mooring lines of ships which are moored to the quayside and which, following completion of the loading / unloading activities, wish to put to sea and to ensure that these mooring lines can be safely cast off simultaneously. In both situations outlined above, the mooring hook in which the ship's mooring hawser has been placed is opened. The "Quick Release System" is used for casting off the ship's mooring lines and this action can be carried out remotely. Remote operation is carried out using a project-related remote control operating panel. Manual operation of the mooring hook always remains possible by using the release lever. The remote-control system can be used to load the mooring lines into the hooks. The mooring hooks are now executed with a hydraulic cylinder “L” and a proximity switch “H,” which indicate the ‘open’ or ‘closed’ position of the hooks. Safe monitoring with Mooring Load Monitoring System (MLMS) The Mooring Load Monitoring System in place enables us to keep a constant watch on the forces on the mooring lines. Immediate actions could be taken with possible slack or overload situations. Load information is displayed in real time, the alarms can be preset on Safe Working Load requirements. The retrieved data can be used to estimate the number of mooring lines required for safe mooring. Uncontrolled copy. This document has no value if printed Page 33 | 56 Supervision, Automation & Control System Document number: OPS-FSO-MAN-004 Date: 11/01/2023 Revision: 04 Remote Control System (RCS) In case of an emergency, the hooks can be released from a distance by remote control. With the Remote-Control System, the hooks can be released individually or simultaneously. Open or closed hook indications are transmitted to the remote-control panel. Figure 9 - QRH Control panel Figure 10 - Front view of the QRH Control panel Uncontrolled copy. This document has no value if printed Page 34 | 56 Supervision, Automation & Control System Document number: OPS-FSO-MAN-004 Date: 11/01/2023 Revision: 04 Laboratory Control Panel This control system internally centralized negative-pressure exhaust system, fire interlocking system and combustible gas interlocking alarm. Make sure to input correct power supply. Turn the Main Power switch from OFF to ON. All the other equipment starts and stop switches are placed at the panel itself, such as fan, lamp, and power to the socket. The container also has an in-build gas detector and fire detector. The container is equipped with the list of items below in Table 3. Table 3 – List on items in Container No. Item Description 1 Explosion -proof electrical control box BXK51 2 Explosion - proof-Fan 3&4 Explosion- proof beacon & lamp switch 5&6 YA-D300 series point type detector 7 Temperature sensitive fire detector 8 Smoke sensitive fire detector 9 Manual call point 10 Explosion-proof socket 11 &12 Explosion-proof lights 13 Explosion-proof junction box 14 Explosion-proof control unit system 15 Explosion -proof led light Uncontrolled copy. This document has no value if printed Page 35 | 56 Supervision, Automation & Control System Document number: OPS-FSO-MAN-004 Date: 11/01/2023 Revision: 04 16 Explosion -proof AC 17 Explosion -proof oblique flow fan 18 Explosion-proof connector 19 ROXTEC MCT Figure 11 - Laboratory Operating Panel 6.2 System protection devices All control systems are fitted with self-fault detection alarms that will warn operator of abnormal conditions. Power supply to control systems is supplied through AC 220V main supply with DC 24V back-up from battery which ensures constant power supply in the event of trip or black out. Uncontrolled copy. This document has no value if printed Page 36 | 56 Supervision, Automation & Control System Document number: OPS-FSO-MAN-004 Date: 11/01/2023 Revision: 04 Nautical instrument. Interior communication equipment, general battery charger and GMDSS equipment are connected to the power distribution panel which is fed from main switchboard and emergency switchboard respectively with automatic change over switch. One (1) battery switchboard is provided for charging and discharging of battery, and distributing DC 24V source to battery light, interior communication equipment and navigation equipment. For transient emergency illumination in positions of controls and monitoring, battery light to be provided and to be automatically switched on in the event of failure of normal A.C. power. The control system should not trip as it is responsible to keep a real time monitoring of the FSO condition and parameters to ensure operating range are kept at safe levels. In case of a trip to the control system, the control system should be reinitialised with proper adherence to the safety regulation of the control system to avoid over current that may be fatal to the system. Below alarm systems in the E/R Alarm and monitoring systems are key to alerting and reacting: o Bridge dead man alarm system o E/R dead man alarm system o E/R patrol alarm START A manual emergency trip switch with cover is provided in the E/R control console and bridge control console and fire control station. The Emergency trip system is independent of the remote-control system. Fail-safe functionality The most probable failures, for example loss of power or wire failure, shall result in the least critical of any possible new conditions where the normal user interface for the below listed safety functions is an operator station in an integrated system, a back-up means of operation/user interface is required. This applies to: — emergency shutdown systems (ESD) — fire and gas detection system — activation of relevant fire-fighting systems — other safety functions where a back-up means is required by the rules or standards. The back-up means of operation shall be independent of the normal user interface and its communication networks. Redundant Systems A redundant system shall, upon failure, have sufficient self-diagnostics to effectively ensure transfer of active execution to the standby unit. Power Distribution Essential control and monitoring systems shall be provided with two independent power supplies. This applies to both single and redundant control and monitoring systems. 6.3 System trips The control system should not trip as it is responsible to keep a real time monitoring of the FSO condition and parameters to ensure operating range are kept at safe levels. In case of a trip to the control system, the control system should be reinitialised with proper adherence to the safety regulation of the control system to avoid over current that may be fatal to the system. Uncontrolled copy. This document has no value if printed Page 37 | 56 Supervision, Automation & Control System Document number: OPS-FSO-MAN-004 Date: 11/01/2023 Revision: 04 Metering Control System Events (Stored in events log): Login information, Changing keypad values and Changes of state of alarms (all alarms) Critical alarms (shown in alarm log when active or when not acknowledged): Calculation Errors and Hardware failure errors (Tx failures etc) Non-Critical alarms (shown in alarm log when active or when not acknowledged): Limit alarms (High/Low) for Pressure and Temperature Turret and Mooring System System is fitted with Emergency Shut Down valve. Refer to FSOPAR-BR-PAR-00-DOR-DW-Z-004 Turret general arrangement drawing. Figure 12 – Turret General Arrangement Drawing Offloading System Alarm and trip for cargo pump/turbine as follows: o Over-speed trip o L.O. low pressure trip o L.O. high temperature alarm o L.O. tank low level alarm o High exhaust steam back pressure trip o Pump casing over-heat trip o Bulkhead stuffing box over-heat trip Uncontrolled copy. This document has no value if printed Page 38 | 56