Operations Management PDF
Document Details
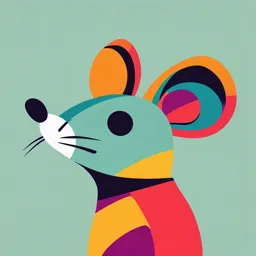
Uploaded by EloquentAmazonite
Tags
Summary
This document provides an overview of operations management, focusing on strategic decision-making, cost leadership, and differentiation. It examines various aspects such as globalisation, technology, quality issues, and performance objectives.
Full Transcript
**[Operations]** Managing the processes that transform and add value to inputs to create outputs of goods and services. ***Role of operations management*** ***Strategic role of operations management -- cost leadership, good/service differentiation*** **Strategic role =** focusing on decisions fo...
**[Operations]** Managing the processes that transform and add value to inputs to create outputs of goods and services. ***Role of operations management*** ***Strategic role of operations management -- cost leadership, good/service differentiation*** **Strategic role =** focusing on decisions for achieving long-term goals. The strategic goals are to improve: - Productivity - Efficiency - Quality of outputs. It involves operations managers contributing to the strategic direction of strategic plan of the business **Cost Leadership:** involves aiming to have the lowest costs or to be the most price-competitive in the market. This is gained by offering greater value by means of lower prices, grater quality or by providing greater benefits and service at no extra cost. Most businesses who aim to be cost leader will have a high degree of standardisation. Can keep cost down through: - Economies of scale in production and distribution - Access to cheaper raw materials - Exclusive access to a large source of low cost inputs - Developing an efficient scale of operationseconomies of scale - Using up-to-date technology in production - Controlling production and research costs. **Good/service differentiation:** involves differing products from competitors. Is can be achieved through: - Altering the quality - Faster delivery (efficiency) - Customisation - More features and applications on the physical appearance - Location of operations - Improving the service ***Goods and/or services in different industries*** **Goods** can either be: - Standardised (mass produced, uniform in quality, produced with a production focus) - Customised (varied according to the needs of the customer, produced with a market focus) - Can be reused - Hard to modify once manufactured - Perishable or non-perishable - Tangible product that requires factory/machinery and space - Less labour intensive than services - The manufacturing of goods has become automated with computer-aided design (CAD) and computer-aided manufacture (CAM). **Services** can be: - Standardised (e.g. fast food restaurant) - Customised (e.g. medical services, hairdressers) - They are intangible - Can only be used by the customer once - Easier to change and customise - More interaction with customers - Require more people and have an office-centred production ***Interdependence with other key business functions*** All key functions are interdependent and rely in each other for success. **Operations-** must supply a product that has the features and quality consumers want as well as being reliable in distributing the product to the market. **Marketing-** connects operations directly with the customer. Identifies the nature of consumers' desires and implements marketing strategies to encourage purchase of goods made in operations. **Finance-** required so production and distribution can take place. The finance manager creates budgets and makes funds available to purchase inputs, equipment and repairs. **Human Resources-** required for the hiring of employees to work in production. Ensures that there are enough employees with the appropriate skills. ***Influences on operations*** ***Globalisation, technology, quality expectations, cost-based competition, government policies, legal regulation, environmental sustainability*** **Globalisation:** - Able to reduce the cost of operations by pursuing a global web strategy (location of different parts of the production process in different areas) which will reduce labour costs - More abundance of raw materials, technology skills and low transport costs - Can also act as a threat to a business as other businesses who apply cost leadership can dominate the market - Able to reach new markets and provide franchises - Gives consumers the opportunity to purchase products from the business that provides the most value for money - Access to a global market for businesses to sell their outputs **Technology:** - Enables service-based businesses to penetrate global markets with the international distribution of information through the internet and smart phones - Can result in the development of new methods of production or new equipment that helps businesses perform functions more quickly and efficiently (lower cost) - Computer-aided design (CAM) and computer-aided manufacture (CAM) has impacted the number of employees needed within operations - It improves efficiency, logistics and reduces reliance on human labour **Quality expectations:** customer expectations and satisfaction with the product(s). Operations of the delivery of services can have a positive impact on customer satisfaction. Customers require world-class standards in products and after-sales support. Customers will have certain beliefs about: - Durability (how long the product lasts given a reasonable amount of use) - Reliability (how long the product functions without needing repairs or maintenance) - Fit for purpose (how well the product does what it is supposed to) **Cost-based competition:** A business can gain a price advantage over its competitors by using operational strategies that lower costs through: - Cheaper labour and resources - Outsourcingeconomies of scale, global web strategy - Lowering quality - Using cheaper inputs **Government policies:** - Government policies are methods used by the government that encourage the operations function of a business to be more innovative and competitive. - A common way to support these innovative businesses is to provide monetary benefits such as a financial grant or tax concessions. - There has been a gradual reduction in 'protection' of Australian businesses forcing them to be more efficient in their operations and reduce costs. - Free trades, taxation, interest rates, government spending and environmental incentives. **Legal regulations:** - The aim of government regulation of a business is to promote safety and fair business conduct. - Many of the regulatory requirements exist at a local, state and federal level. - It is the legal responsibility of the operations manager to be aware of all the laws relevant to the operations function and ensure that the business complies with them. - Work Health and Safety (WHS), anti-discrimination, equal employment opportunity (EEO), local zoning, and GST collection. **Environmental sustainability:** - Ecological sustainability refers to the development and use of methods of production that allow resources to be used by producers today without limiting the ability of future generations to satisfy their needs and wants. - Consumers need to be aware of the cost and disposal of excessive packaging. - Society will have a positive attitude towards businesses that are environmentally friendly and good corporative citizens. - Involves the use of alternative resources, organic growing, recycling and packaging and catering for future generations. ***Corporate social responsibility*** ***-the difference between legal compliance and ethical responsibility*** ***-environmental sustainability and social responsibility*** **Corporate social responsibility** is a commitment by a business to operate ethically to protecting and contributing to the resources and interests of customers. It is how success and profitability is determined and how well it considers the interests of employees, consumers and the community. **Legal compliance** is mandatory and of greater importance than **ethical responsibility** as there are not specific laws the business would be breaking, yet unethical behaviours may lose customers. - Ethical behaviour involves making decisions that are not only legally correct but also morally correct. - For operations, a code of conduct will be concerned with: - minimising harm to the environment - reducing waste, recycling and reusing - producing value-for-money, quality products - improving customer service **Environmental sustainability** is about the present use not affecting the future use, looking after the environment for future generations. **Social responsibility** refers to the positive effect on the community- protecting interests of customers and wider society, e.g. initiatives/charity to community. - By pursuing environmentally sustainable goals a business will be contributing to a better quality of life for society. ***Operations processes*** ***Inputs*** ***-transformed resources (materials, information, customers)*** ***-transforming resources (human resources, facilities)*** Common direct inputs= labour, energy, raw materials, skills/knowledge, machinery and technology. **Transformed resources:** inputs that are changed or converted in the operations process to a finished good or service. - [Materials]- raw materials and intermediate goods (e.g. supplies, parts) used up in the operations - [Information]-influence and inform how inputs are used, where and which supplier to use and to keep control over material inputs. - [Customers]-their choices shape inputs. Customers can be changed in different ways, e.g. feel that value has been added to their lives after seeing a film or going on holidays. **Transforming resources:** resources that remain in the business and carry out the transformation process to add value to inputs. - [Human resources]-effectiveness of human resources determines the success of the transformation. The skill, knowledge, capabilities and labour of people is applied to materials to convert them into goods and services. - [Facilities]-plant, machinery, buildings, land, equipment and technology used in operations. ***Transformation processes*** ***-the influence of volume, variety, variation in demand and visibility (customer contact)*** ***-sequencing and scheduling -- Gantt charts, critical path analysis*** ***-technology, task design and process layout*** ***-monitoring, control and improvement*** The transformation processes are those activities that determine how value will be added. These processes can add value in four ways: - Physical altering of the physical inputs or the changes that happen to people - Transportation of goods or services, e.g. having them delivered to a more convenient location - Protection and safety from the environment; for example, protecting assets - Inspection by giving customers a better understanding of the good or service **The influence of volume:** - The actual number of products or services produced by the operation. - A business using mass production will produce a high volume with a high degree of process repetition. - A business with customization and low production will allow for lots of stoppages and adjustments. - When volume is the largest factor, there will be lots of capital facilities and technology, but less labour. Assembly lines using convey or belts will be common and organized. - Low volume= 5 star restaurant, high volume = fast food restaurant. **The influence of variety:** - Variety refers to the range of products made, number of different models and variations offered in the products or services. - A business producing a high volume product with low variety will be capital intensive. - Low variety= car factory with small variations. High variety= financial advice. **The influence of variation in demand:** - amount of produce desired by customers - Variation can change according to time of day, season, holidays and time of year. - When there are steady levels with no variation, there will be high volume and capital costs. - Low variation= bread and milk. High variation = ice cream factory **The influence in visibility (customer contact):** - Operations will also be influenced by the degree to which customers can see the operations in action. - Service-based businesses will have a high level of visibility. Speed of operations will also be important as customers usually have a much lower tolerance for waiting. - High visibility= restaurant. Low visibility= beef producer. **Sequencing=** a plan showing the order in which activities occur **Scheduling=**used to plan the length of time activities take and the sequence of the use of resources **Gantt charts** records the number of tasks involved in each particular project and the estimated time needed for each task, good for long-term projects, easy to understand **Critical path analysis** a scheduling tool that allows manager to see shortest length of time to complete all tasks, precise in timing, good for short-term tasks **Technology:** It makes task more effective and efficient, high-tech or low-tech, less employees needed, increasingly important, cost is also relevant, allows more work to be done in a shorter time, machinery/manufacturing technology-robotics, CAD and CAM. **Task Design:** is how the task will be completed. It allows for ongoing analysis and adjustments in each activity to ensure continuous improvement in productivity. Classifying job activities, what needs to be done, making it easy for an employee to successfully complete tasks, job analysis, can be cone after a skills audit is conducted. **Process layout:** arrangement of machines in a sequence-grouped together by function/process they perform **Monitoring-** the systematic collection and analysis of information as a task progresses. These include: quality, speed, dependability, flexibility, customisation and costs. It is aimed at improving the efficiency and effectiveness of an operations process. The purpose of it is to see if resources have been allocated properly and are being used efficiently. **Control-** a function that aims at keeping the business's actual performance as close as possible to what was planned by making adjustments to the operation process. It is about assessing the performance of a business. **Improvement-** suggests that adjustments and readjustments may need to be made to day-to-day activities in the short term and even the entire operations process in the long term. There can be improvements in: quality, speed, dependability, flexibility and cost. ***Outputs*** ***-customer service*** ***-warranties*** **Outputs:** good or service provided/delivered to a customer, are the final products that a business offers to customers. **Customer service-** is a service provided to customers before, during and after a purchase. It is an intangible output that requires extensive contact with customers. Good customer service will increase customer satisfaction. How a business meets and exceeds the expectation of customers in all aspects of its operations, key in developing long-term relationships. **Warranties-** an assurance that a business stands by the quality claims of the products that they make and provide to the market. Agreement to fix defects in products, an assessment of warranty claims can help a business to adjust transformations processes to be more effective. ***Operations strategies*** ***Performance objectives -- quality, speed, dependability, flexibility, customisation, cost*** **Quality=** quality of service/conformity/design, can be measured in rate of returns and feedback. Good quality prevents costs by product recalls and repairs, dimensions of quality are: durability, performance, serviceability (convenient to repair) and aesthetics (does it look good). **Speed=** time it takes for production/operations process to respond to changes in the market demand, tested by analysing wait time and production speed, if the production is too fast the quality may suffer. **Dependability=** consistency and reliability of products, measured by warranty claims and complaints. **Flexibility=** how quickly processes adapt to market change, technology, ability to make changes to operations due to external factors. **Customisation=** creation of individualised products to meet specific customer needs. **Cost=** minimisation of expenses so that operations processes are conducted as cheaply as possible. ***New product or service design and development*** **New product:** design, development, launch and sales of new products allows a business to grow and maintain a competitive advantage, different approaches (customer approach/changes or innovation in technology). **Service design and development:** more complex, adding to the service offered to the customer, can be adding to variety/increase of choice, develop within cast structure. ***Supply chain management -- logistics, e-commerce, global sourcing*** **Supply chain management** is the stream of processes of moving goods from the customer order through the raw material stage, supply, production and distribution of products to the customer. Integrating and managing the flow of supplies throughout the inputs/transformation process/outputs to best meet the needs of customers, supplier rationalism/backwards vertical integration/cost minimisation/flexible responsive supply chain process **Logistics:** the transport of physical raw materials, inputs and the distribution of finished goods to markets. It involves the integration of information, transportation, inventory, warehousing, materials handling and packaging. Computerisation can make the task faster/more efficient. The role of logistics is to ensure that operations have the right items at the right quantity and the right time at the right place. **E-commerce:** the use of internet to buy and sell goods and services. Alter operation process, e-procurement, managing supplies in an organised way, makes trading easier, cheaper access to global markets, privacy and security issues, and increased risk of purchasing unsatisfactory or faulty materials. **Global sourcing:** business acquires the inputs it needs for production across the borders of a number of countries. A business seeks to find the most cost effective location for manufacturing a product, even if the location is overseas, may be cheaper to purchase inputs from overseas than create them, keep control over complex supply chains, lower costs, loss of control over quality, reliability and costs, slower lead times. ***Outsourcing -- advantages and disadvantages*** **Outsourcing:** occurs where other businesses provide the raw materials and components, and also service inputs. **Advantages-** external provider specialised, lower costs, greater effectiveness, require less capital expenditure, can use employees of other business, may contribute to the speed, give the business flexibility to choose the suppliers it wants, requires less input from management, the business can focus on its core business. **Disadvantages-** if ineffective may be more expensive, not in control, if competitors are doing the same=less competitive advantage, dependent on other businesses, can involve a loss of jobs, can the security and confidentiality issues. ***Technology -- leading edge, established*** **Leading edge=** most advanced or innovative, is sometimes still being developed **Established=** developed and widely used ***Inventory management -- advantages and disadvantages of holding stock, LIFO (last-in-first-out), FIFO (first-in-first-out), JIT (just-in-time)*** **Inventory management** refers to the systems and processes that identify the quantity of goods or materials to be ordered and the timing of the delivery of those goods or materials. Inventory control has 3 aims: determine maximum and minimum stock, provide details of changes in inventory to trigger management decisions to reorder, strategies applied impact transformation process. [Advantages of holding stock:] consumer demand can be met, reduces lead times between order/delivery, storage of stock allows business to promote products in non-traditional/new markets, stock adds value to business, making products in bulk can reduce costs, dependability of delivery [Disadvantages of holding stock:] costs with storage, invested capital/labour/energy can be used elsewhere, if stock is unsold the business experiences a loss, increased management costs, goods may pass their expiry or use by date. **LIFO (last-in-first-out):** last goods produced are the first out or used and therefore each unity sold/used is the last one recorded, the newer stock is displayed for sale before products purchased at an earlier date. This endures that up-to-date stock is on display for customers. **FIFO (first-in-first-out):** first goods produced are the first ones sold/used, therefore the cost of each unit sold/used is first recorded, can be used if price of supplies/goods remain relatively stable, used when products have a used-by date. **JIT (just-in-time):** ensures exact amount of products or materials arrive only as they are needed, can save money as it eliminates inventories but require flexible operations/reliable suppliers. ***Quality management*** ***-control*** ***-assurance*** ***-improvement*** **Quality management:** involves setting performance objectives that clearly set quality as a foremost goal. **Quality Control-** involves checking transformed and transforming resources in all stages of the production processes, failure to meet pre-determined targets=corrective action **Quality Assurance-** involves monitoring and evaluation of the various processes of a project, service or facility to ensure that a minimum level of quality is being achieved by the production process. Assures set standards are met, pre-determined (universal) quality standards **Quality Improvement-** involves continuous improvement in all functional areas to reduce the rate at which mistakes occur. Ongoing commitment to improving goods/service and total quality management-quality is a commitment/responsibility of all staff ***Overcoming resistance to change -- financial costs, purchasing new equipment, redundancy payments, retraining, reorganising plant layout, inertia*** Major reasons for resistance to change are: **Financial costs-**purchasing new equipment, redundancy payments, retraining, reorganisation of plant layout **Inertia-** psychological resistance, fear of losing jobs/uncertainty. ***Global factors -- global sourcing, economies of scale, scanning and learning, research and development*** **Global sourcing:** refers to the process of acquiring raw materials, services and various parts that are needed to manufacture goods or services. A business may use a global web strategy. **Economies of scale:** occur when the amount of production increases and as a result of this increased output there is a decrease in the cost of production per unit of output. **Scanning and learning:** involves monitoring a business's internal and external environment so that it can gather, analyse and use information for tactical or strategic purposes. Scanning the global environment to identify and learn the critical global trends that may impact on the business. **Research and development:** helps business to creating ideas for new products or services that will give them a leading edge over other businesses.