OGTS – MO6 - 01 & 02 & 03 Basic Health and Safety in Maintenance Workshops PDF
Document Details
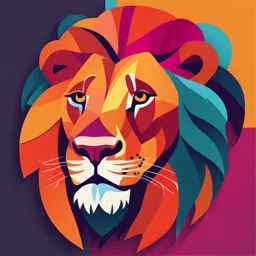
Uploaded by HardWorkingFoxglove
Tilenga Academy
2024
OGTS
Christine Arupo Maloba
Tags
Summary
This document provides health and safety guidelines for maintenance workshops in the oil and gas industry. It covers topics such as safe manual handling techniques, types of injuries, and causes of injury. The information is aimed at professional workers in the industry.
Full Transcript
BASIC HEALTH AND SAFETY IN MAINTENANCE WORKSHOPS OGTS – M06 – 01 & 02 & 03 BY: Christine Arupo Maloba 22 July 2024 | 2 Acknowledgement This training material has been prepared by UPIK-HSE and Dietsmann lect...
BASIC HEALTH AND SAFETY IN MAINTENANCE WORKSHOPS OGTS – M06 – 01 & 02 & 03 BY: Christine Arupo Maloba 22 July 2024 | 2 Acknowledgement This training material has been prepared by UPIK-HSE and Dietsmann lecturers covering OGTS-M06: 01, 02, 03 for the Tilenga Academy in accordance with OPITO curriculum and industry best practices. 24 June 2019 / ‹#› LEARNING OUTCOMES Describe safe working practices for a O1 maintenance workshop Create a basic risk assessment for O2 workshop maintenance tasks Demonstrate safe working practices in O3 a maintenance workshop 24 June 2019 / ‹#› SESSION OBJECTIVES P1.1 Describe safe working practices for working in a maintenance workshop P1.2 Describe the operation of safety documentation and procedures P1.3 Identify relevant emergency requirements for a maintenance workshop P2.1 Identify potential hazards in a workshop environment P2.2 Describe the associated risks and implications for people, equipment and the environment P2.3 Describe measures that could be taken to minimise the risks P2.4 Carry out and record a risk assessment for a maintenance workshop P3.1 Communicate and work effectively as part of a team for maintenance tasks 24 June 2019 / ‹#› SESSION OBJECTIVES cont’d P3.2 Take part in a tool box talk P3.3 Use correct manual handling techniques for maintenance tasks P3.4 Select and use the correct personal protection equipment for maintenance tasks P3.5 Maintain the workspace in a clean and tidy manner and dispose of waste 24 June 2019 / ‹#› Describe safe working practices for working in a maintenance workshop 7 INTRODUCTION TO MANUAL HANDLING Definition: Manual handling is any task where people physically move, handle or shift materials and objects. 8 Manual handling Examples of manual handling include: lifting boxes on or off storage racks or shelves; pushing furniture or tools; pulling an object into a better position carrying a package; sliding an object out from the floor; 9 Types of injuries Damage to the spine, back muscles and ligaments Amputations Abdominal hernia Muscle strains Crushed limbs and joint wear 22 July 2024 | 10 Manuel handling INDICATE: Correct method Incorrect method 22 July 2024 | 11 Manual handling Risks for your back Short term: acute back injury from unique event (i.e. lifting too heavy, or in bad position) Long term: chronic fragility/vulnerability of column invalidity from back pain great impact on your personal, professional and social life 12 Causes of injuries Overexertion - handling a load beyond the body’s capability. Repetitive actions - continually repeating certain movements or maintaining a body position for long periods. Poor workplace layout - encourages unsafe work postures and unnecessary manual handling. Incorrect technique - incorrect body positions and movements. 13 Reducing Manual handling Some ways to reduce manual handling tasks are by: planning your work area getting help from someone to carry heavy objects; using mechanical aids, such as hand trolleys, to move objects finding the best possible position 14 Safe manual lifting Size up the load to make sure it is not too heavy or too large. Assess the load to check contents will not move. Adopt a stable footing. Bend your knees and reach down to the load. Keep your back straight as you lower yourself. Grip the load with both hands. Brace your stomach and buttock muscles. Slowly push up with your legs and keep your back straight. Never bend at the waist, always bend at the knees - it makes the job ten times easier on your back. 15 16 Carrying load When carrying a load: keep the load close to your body; keep the load at no more than waist to chest height; and take short steps. If a load is too heavy or too large for you to lift and carry on your own, use a mechanical aid, or get someone else to assist you. 17 Carrying load To use a four-wheeled lifting aids, such as Carts and Platform Trucks: Push, rather than pull, the cart. Be aware of traffic in front of you. Allow an adequate stopping distance At the destination, secure the cart so it won’t roll 18 Pushing or pulling loads When pushing a load you should: place your feet apart with one well behind the other; lean forward; gradually apply your body weight; and push forward with your rear foot to set the load in motion. When pulling a load you should: place your feet apart with one well behind the other; lay back into the line of pull; gradually apply your body weight; and push backward with your front foot to set the load in motion. 22 July 2024 | 19 The Individual, Strength Is your strength height & fitness appropriate to the task? Everyone’s different! 22 July 2024 | 20 The Individual, Strength Have you been trained for the task? If you need training or information, ask your Supervisor 22 July 2024 | 21 The Load, Shape Do I need someone to help me lift? Ask for help, check the weight by tipping it and communicate clearly then check that everyone involved feels comfortable carrying the load 22 July 2024 | 22 The Load, Hazards Do not carry large objects that will obstruct your view It is important that your field of vision is clear when lifting lowering and carrying Look out for sharp edges 22 July 2024 | 23 The Environment, Layout Is the lighting good Can the workplace be reorganized? Obstructions should be cleared to provide enough space for correct positioning of the load 22 July 2024 | 24 The Environment, Ground condition Is the floor uneven, slippery or unstable? Check the floor for hazards such as, oil, steps or spillage 22 July 2024 | 25 The Environment, Temperature Perspiration on hands can reduce grip Hand gloves should be used to ensure better grip 22 July 2024 | 26 Whatever you are lifting or moving: Use appropriate personal protective equipment Take special precautions when handling chemicals and hazardous materials 24 June 2019 / ‹#› WORKING AT HEIGHTS 24 June 2019 / ‹#› INTRODUCTION TO WORKING AT HEIGHT SAFELY Working at height remains one of the biggest causes of fatalities and major injuries during maintenance works. Common cases include falls from ladders and through fragile surfaces. 'Work at height' means work in any place where, if there were no precautions in place, a person could fall a distance liable to cause personal injury (i.e. a fall through a fragile roof). Employers can take simple, practical measures to reduce the risk of any of their workers falling while working at height. 24 June 2019 / ‹#› Video https://youtu.be/00f0A1ppnRo 24 June 2019 / ‹#› Scaffolding Awareness Scaffolding is a temporary work platform used for working at heights. 24 June 2019 / ‹#› Generally, Height is defined as anything greater than 1.8m. Any work done beyond 1.5m is work at heights (newly revised) Falling from height remains the single greatest cause of severe injury and or death in the construction and Refining industry. Single most expensive cost related injury. 24 June 2019 / ‹#› Here is a simple equation for determining the required distance: - Lanyard Length – The length of the lanyard or retractable device connected to the harness anchorage point. - Deceleration Distance – The distance between the start of the fall to when the fall arrest system engages. OSHA limits this distance to 3.5 feet or less. - Work Height – The height where the work is taking place. - Safety Factor – Additional safety distance below the worker. The height and weight of the worker should also be considered when determining fall clearance. 24 June 2019 / ‹#› https://youtu.be/qFhLaP4xZ1A 24 June 2019 / ‹#› 24 June 2019 / ‹#› CONFINED SPACES CONFINED SPACES 22 July 2024 | 37 DEFINITION OF CONFINED SPACES Confined space is space that: Is large enough & so configured that employee can bodily enter & perform assigned work Has limited or restricted means for entry or exit (i.e. tanks, vessels, silos, pits, vaults or hoppers) Is not designed for continuous employee occupancy 22 July 2024 | 38 ISSUES OF CONFINED SPACES The accidents related to work within a confined space are most of the time serious accidents or fatalities Most of these fatalities were related to a deficiency in oxygen or to a presence of toxic gasses or flammables 60% of these victims were workers who tried to rescue without having the necessary knowledge and equipment 22 July 2024 | 39 EXAMPLES OF CONFINED SPACES For example the following locations could be confined spaces: A reservoir, a silo, a tank, a bunker, a chamber, a dome, a pit, a sewer, a pipe, a chimney, manhole, wagon or tanker truck, etc. 22 July 2024 | 40 EXAMPLES OF CONFINED SPACES Boiler tanks… Pipe chases… Crawl spaces… Manholes… Pits... 22 July 2024 | 41 22 July 2024 | 42 EMPLOYER’S RESPONSIBILITIES The employer has the responsibility to draw up an inventory of all his confined spaces and to do the risk assessment, by a qualified person, to issue the safety work procedure which should be strictly followed He has also to assure that the workers have the knowledge, an adequate training or experience in order to perform the work safely Moreover, he has to provide them with the appropriate work and personal protective equipment which should be in good overall conditions 22 July 2024 | 43 OXYGEN DEFICIENCY The air normally contains 21% of oxygen. When the concentration in oxygen is less than 19.5% in the air, it is forbidden to enter a confined space 22 July 2024 | 44 THROUGH THE DISPLACEMENT OF OXYGEN BY OTHER GASSES Many gasses, mainly inert gases (argon, nitrogen, carbon dioxide, etc.), the gasses used in the portable fire extinguishers, and refrigeration gasses, can displace the oxygen 22 July 2024 | 45 EFFECTS OF OXYGEN CONCENTRATIONS ON HUMAN BODY ✓ 23,5 %: Atmosphere rich in oxygen. Superior limit from which it is forbidden to enter ✓ 21,0 % : Normal oxygen concentration ✓ 19,5 % : Minimum concentration to enter in a confined space without a respirator self-rescue apparatus or with an air supply respirator ✓ 12 % to 16 %: Spasmodic breathing, anxiety, abnormal fatigue when doing some movements, insufficient concentration to keep a flame in ignition ✓ 10 % à 11 %: Acceleration in breathing and heart rate, euphoria, headaches. ✓ 6 % à 10 %: Nauseas and vomiting, inability of moving freely, possibility of loss of consciousness and collapse while being conscious ✓ Less than 6 %: Breathing failure followed by heart failure, death in a few minutes 22 July 2024 | 46 OXYGEN A. The Oxygen: IN A NORMAL ATMOSPHERE OXYGEN CONTENT IS 21% An atmosphere which is rich in oxygen ( 23,5% and higher), increases material flammability levels. It is strictly forbidden to enter a confined space containing more than 23,5% of oxygen 22 July 2024 | 47 OXYGEN ENRICHED ATMOSPHERES Enriched Oxygen levels cause flammable and combustible materials to burn violently when ignited. ▪ Hair, clothing, materials, etc. ▪ Oil-soaked clothing and materials. Never use pure oxygen to purge/vent equipment. Never store or place compressed tanks in a confined space. 22 July 2024 | 48 TOXIC SUBSTANCES ATMOSPHERES The deficient natural ventilation and the low air volume of many confined spaces lead workers to be exposed to important concentrations of contaminants A toxic atmosphere contains gasses, vapors or smoke well-known to have noxious (harmful) effects on human body. The toxic effect is independent from the oxygen concentration 22 July 2024 | 49 IF POSSIBLE,TRY TO AVOID ENTERING IN CONFINED SPACES? The first question to ask when elaborating a Contingency Plan in confined spaces is the following: Could we avoid entering in confined spaces? There are all sorts of methods allowing to achieve the same results without entering in a confined space. For instance, the use of cameras and Robotic equipment. Robotics for industrial cleaning in confined spaces and Suction Excavators (youtube.com) 22 July 2024 | 50 ROBOTICS FOR INDUSTRIAL USE 22 July 2024 | 51 QUALIFIED PERSONS: The Attendant Individual stationed outside one or more permit spaces who monitors authorized entrants & performs all attendant’s duties assigned in employer’s permit space program 22 July 2024 | 52 The Attendant Duties of Attendants ◼ Know hazards that may be faced during entry ◼ Aware of possible behavioral effects of hazard exposure in authorized entrants ◼ Continuously maintain accurate count of authorized entrants ◼ Remain outside permit space during entry operations until relieved by another attendant 22 July 2024 | 53 The Attendant Duties of Attendants ◼ Communicate with authorized entrants ◼ Monitor activities inside & outside space ◼ Summon rescue & other emergency services ◼ Perform non-entry rescues as specified by employer's rescue procedure ◼ Perform no duties that might interfere with primary duty to monitor & protect authorized entrants 22 July 2024 | 54 The Attendant The attendant should not enter in the confined space to make the rescue if all the conditions mentioned below are not respected: He is also trained to enter in the confined space to make the rescue. He has the personal protective equipment required. He is replaced by another attendant. 22 July 2024 | 55 AUTHORIZED ENTRANT Duties of Authorized Entrants ❑ Know hazards that may be faced during entry, including information on mode, signs or symptoms & consequences of exposure ❑ Properly use equipment and trained ❑ Communicate with attendant as necessary to enable attendant to monitor entrant status & enable attendant to alert entrants of need to evacuate space 22 July 2024 | 56 Personal protective equipment Do not enter a confined space without hands-on training in use of equipment 22 July 2024 | 57 RESPIRATORY PROTECTION Breathing apparatus are not required when atmospheric conditions in the confined space are compatible with the following criteria: ❑ Oxygen concentration higher than 19,5% and lower than 23,5%, ❑ Gas or flammable vapors concentration lower than 10% of the Lower Explosive Limit (L.E.L.), 22 July 2024 | 58 If the atmospheric conditions do not correspond to the standards previously mentioned. The area should be considered as being hazardous or as an area representing an immediate danger for the health and life. A special equipment should then be used. (Robotic Equipment) The respiratory protection choice is done by a gradual elimination of the inappropriate respirators according to the current conditions. 22 July 2024 | 59 Supplied Air Respirators During Confined space rescue, conventional SCBA’s size often makes it difficult to use SCBA small enough to pass through narrow openings may limit duration of its air supply to impractical levels 22 July 2024 | 60 I MUST Ensure a safety watcher is present and communication devices are working The safety watcher continuously monitors the in/out movement during the task The safety watcher communicates with the workers in the confined space In the case of an emergency, the safety watcher calls the rescue team Read and understand the emergency plan Everyone involved in a confined space task must know precisely what to do in an emergency Emergency and rescue devices should be available whenever work is carried out in a confined space 22 July 2024 | 61 I MUST NOT Enter a confined space without authorization / confined space permit No authorization / permit = No entry to a confined space Confined space intervention = Special permit Work in a confined space on my own The worker and the watcher must be in constant permanent contact 22 July 2024 | 62 SAFE PRACTICES Working inside a tank 22 July 2024 | 63 22 July 2024 | 64 Safety isolation procedures 24 June 2019 / ‹#› Introduction 24 June 2019 / ‹#› Isolation When working on an electrical installation, maintenance, inspection, it’s vital that you disconnect the equipment from the live supply and test whether any current is running through it before making a start on the task at hand. In the electrical trade, this process is referred to as safe isolation. 24 June 2019 / ‹#› Once you’ve disconnected an installation from the rest of the circuit and checked that no current is flowing through it, the system is said to be “dead” (as opposed to “live”). At this point, you can safely start investigating and fixing the installation. We isolate systems from the rest of the circuit prior to working on them primarily for safety purposes: if part of the installation is still live (i.e. connected to the mains supply), then you and other people on site run the risk of receiving an electric shock and serious burns 24 June 2019 / ‹#› Energy Sources 24 June 2019 / ‹#› Lockout /Tagout (LO/TO) Lockout: Use to hold an energy isolating device in the safe position and prevents the energizing of an equipment. Tagout: Use along with lockout devices as an additional warning or information. This tag can only be removed by the person originally installing it or a qualified electrician. 24 June 2019 / ‹#› Therefore, Lockout/Tag-out refers to a safety procedure which is used in industry settings to ensure that dangerous machines are properly shut off and not started up again prior to the completion of maintenance or servicing work. It protects the employees from the unexpected energization or release of hazardous energy during service or maintenance activities 24 June 2019 / ‹#› Lockout devices Lock with one key and tag Chains Flanges Pipe blank or bling 24 June 2019 / ‹#› Tag out devices Tags are always attached to the lock or energy isolation devices Serves as a communication device TAG STAGES: DONOT OPERATE and securely fastened. 24 June 2019 / ‹#› The process of tagging out a system involves attaching information tag or indicator (usually a standardized label) that includes the following information: Why the lockout/tag out is required (repair, maintenance, etc.). Time and date of application of the lock/tag. The name of the authorized person who attached the tag and lock to the system. Note: ONLY the authorized individual who placed the lock and tag onto the system is the one who is permitted to remove them. This procedure helps make sure the system cannot be started up without the authorized individual's knowledge. 24 June 2019 / ‹#› Isolation procedure Preparation Equipment shout down Equipment isolation Application of LO/TO device Release the stored energy Verification 24 June 2019 / ‹#› Isolation procedure cont’d An isolation procedure is a set of predetermined steps that should be followed when workers are required to perform tasks such as inspection, maintenance, cleaning, repair and construction. Before any task is preformed at the plant, it must be shut down and its energy sources locked out and tagged as part of the Isolation procedure to ensure the safety of those doing the work. Example of energy sources that need to be locked out and tagged are; electricity, hydraulic pressure, compressed air or gas, kinetic spring tension and moving parts. 24 June 2019 / ‹#› Isolation procedure Preparation Identify and isolate hazardous energy sources and understand how to use the equipment Equipment shout down Stop buttons and follow shut down procedure of the equipment properly. Equipment isolation Install devices to isolate hazardous energy sources 24 June 2019 / ‹#› Apply Locks and Tags If something can be locked, it MUST be locked, if it cant be locked then it MUST be tagged Release the stored energy Guard against the residual energy Verification Try activating start button to ensure everything is off, check interlock, and be sure area is clear. No response means isolation is verified. Return controls to the safe position (off). 24 June 2019 / ‹#› Generally; Shut down the machinery and equipment Identify all energy sources and other hazards Identify all isolation points Isolate all energy sources ( in the case of electrical equipment , whole current isolation, such as the main isolator should be used instead of control isolation by the way of the stop button on a control panel) Control or de-energise all stored energy Lock-out all isolation points using multi-padlock hasps and danger tags Danger tag machinery controls, energy sources and other hazards 24 June 2019 / ‹#› Importance of the lockout procedure To Isolate all forms of potentially hazardous energy to ensure that accidental release of hazardous energy does not occur. To Control all other hazards to those doing the work To Ensure that entry to a restricted area is tightly controlled To ensure safety for all. 24 June 2019 / ‹#› Different locks/tags used in tagout procedure Yellow = Affected worker places his yellow (if he is not the person who locked out the simple equipment) lock on the Multilock hasp (1 or 2 lock points) or the lockbox (Multiple lockout points)prior to working on the equipment. 24 June 2019 / ‹#› Red= Authorised worker locks out the equipment with the red locks in combination with an isolation tag attached to each lock and also attaches the red lock and personal danger tag which personalizes the lock to secure the lockbox. For simple lockouts the trained affected worker also uses the red lock in combination with their Personal danger tag to lock out the equipment. 24 June 2019 / ‹#› Purple = When a lock out crosses over a shift a transition purple lock is placed on the lockbox by the authorised worker. He then removes his own red lock and PDT. He hands the key of the purple lock over to the next authorised worker coming on or places the key in a designated secure location in the workshop. The next authorised worker coming on then checks the machine and place a red lock with his PDT on the lockbox when he is satisfied that the equipment has been locked out correctly and then removes the purple lock. 24 June 2019 / ‹#› Orange = A contractor working as an Affected worker places his orange lock on the Multilock hasp (1 or 2 lock points) or the lockbox (Multiple lockout points) prior to working on the equipment. It is the responsibility of the need manager/designate to ensure that the contractor puts his lock & isolation tag on the lockbox or multilock hasp. 24 June 2019 / ‹#› Keyed Alike padlocks= In some case these locks are keyed alike in that one key opens numerous locks however this key is unique to these set of locks. These are used in complex lockouts where numerous sources of energy need to be locked out at any one time. 24 June 2019 / ‹#› Caddy = A caddy is used to carry locks to their destination. It is especially useful for keyed alike locks where (X) amount of locks are required to lock out a specific machine. There is only (X) amount of holes punched in the caddy to reflect the amount of locks required for that lock out. The one key used to open these locks is attached to the caddy. A Caddy can carry up to a maximum of 12 locks. 24 June 2019 / ‹#› Tags Personal Danger Tags (PDT) Each authorised and affected worker must be issued with at least one PDT. Most will be issued with 4-5 depending on their area and job. A PDT is a personally issued tag, with information about the owner which personalizes the lock it is attached to. It also has on the rear of the tag the 12 step process which must be followed each time a lock out occurs. Each PDT is unique and will clearly identify the owner of that tag. 24 June 2019 / ‹#› The PDT in combination with a red lock (Authorised Worker) which is applied to the lockbox or multilock hasp indicates that this person has locked out the machine. The PDT in combination with a yellow lock (Affected Worker) which is applied to the lockbox or multilock hasp indicates that this person is working on the machine. The PDT in combination with an orange lock (contractor) which is applied to the lockbox or multilock hasp indicates that this person is working on the machine. 24 June 2019 / ‹#› Isolation Tag An Isolation tag is applied to each lock-out point of the equipment accompanied by a red lock, to indicate that isolation point has been isolated and is not operational. The isolation tags are only used when a lock box is used. The PDT is applied directly to the isolation points where there are 2 or less isolation points. An isolation tag is also attached to the transition lock by the authorised worker when attaching the lock to the lockbox detailing the time and date the transition lock was applied and by whom and also from which shift it is being transitioned to and from. Periodic contractors who have not been issued with a PDT will use an isolation tag recording their name, date, their contact # and their company and attach it to the orange lock which they have attached to the lockbox. 24 June 2019 / ‹#› Lock-Out Box A lock-out box is used to store keys to multiple equipment locks, used when a machine has multiple energy sources. The lock-out box is then locked with the lock and PDT of each person who will work on the machine regardless of the work being carried out. 24 June 2019 / ‹#› Multi-padlock Hasp A Multi-Padlock Hasp is used so that a number of workers may apply their locks and personal danger tags (PDT) to the isolation points of a simple machine. This is usually used in combination with a red lock & PDT when there are 2 or less isolation points on the equipment. If another person is working on the equipment he/she will place a yellow lock and PDT on each hasp or in the case of a contractor an orange lock & PDT/isolation tag. 24 June 2019 / ‹#› https://youtu.be/CV6BDf40yZg 24 June 2019 / ‹#› Use of Machine Guards Machine guards are protective devices that cover moving pieces of machinery that may pose a danger to workers. Moving machine parts present a hazard to machine operators and flying debris can affect anyone in the vicinity of a machine As a result, industrial machines are required by law to have guards that protect workers from the risk of injury while they are at work. 24 June 2019 / ‹#› Use of Machine Guards If at any time, the guard has to be removed in order for maintenance to take place, all systems should be completely powered down to ensure that injuries cannot take place while the guard is not in position. 24 June 2019 / ‹#› Key points about machine guards Purpose: The fundamental purpose of machine guarding is to reduce the risk of injury to the machine operator or workers. Guards prevent access to areas that may cause harm, such as pinch points, shear points and points of operation 24 June 2019 / ‹#› Types of barriers Fixed Barriers: These are physical barriers that prevent direct contact with hazardous areas. They can be permanently fixed or removable. Presence-Sensing Devices: These automatically stop the machine when a person enters a danger zone. Automated Feeding and Ejection Mechanisms: These eliminate operator exposure to the point of operation while handling materials. Machine Location or Distance: This method removes the hazard from the operator’s work area Best practice Always use machine guards when operating or maintaining equipment. Ensure proper guard installation and check that they are secure. Regularly inspect guards for any damage or wear. Train employees on the importance of machine guarding and safe equipment operation with guards in place 7/22/2024 Safe work practices for a maintenance workshop Safe work practices are generally written methods outlining how to perform a task with minimum risk to people, equipment, materials, environment, and processes. Safe work practices should be developed as a result of completing a job safety analysis (JSA) or a hazard risk assessment (HRA) and should closely reflect the activities most common in the company's type or sector of construction. All safe work practices should be kept in a location central to the work being performed and readily available to the workforce. Some safe work practices will require specific job procedures, which clearly set out in a chronological order each step in a process as usually specified in the JSA. 24 June 2019 / ‹#› Safe work procedures are usually developed by management and workers as a result of a JSA/HRA, accident or incident investigation, and/or as a supplement to a safe work practice. Safe work procedures should be included in the company's "Worker Orientation" program. All workers should be aware of the fact that safe work procedures have been established, are in effect, are written down, and must be followed. 24 June 2019 / ‹#› Determine the overall task that requires a safe work procedure. Break down the task into its basic steps. Identify the hazards associated with each step, and ways to eliminate or minimize the risks to workers from these hazards. Write the safe work procedure, for example the list of actions that workers must do when performing the task. Example: fixing a blown bulb 24 June 2019 / ‹#› Basic steps Hazards Risk control measures Isolating the workplace Electrical shocks Wear appropriate PPE, follow the from any Work place safety procedures power(electricity) Removing the blown Trips and falls Use scaffoldings bulb and replacing it Appropriate PPE with a working bulb 24 June 2019 / ‹#› Safe work procedures are directions on how work is to be carried out safely and are required for all hazardous tasks performed at your workplace. They identify hazards and clarify what must be done (precautions) to eliminate or minimize risks. (Series of specific steps that guide a worker through a task from start to finish in a chronological order. Safe work procedures are designed to reduce the risk by minimizing potential exposure.) Hydrogen sulfide How Is Hydrogen Sulfide Formed? Hydrogen sulfide is formed when organic matter decays It is also generated as a common by product of industrial manufacturing processes It is formed under low oxygen conditions when sufficient amounts of sulfur and bacteria are present. It can be present places such as Oil and gas reservoirs, sewers and sewage processing facilities ,swamps, dark and damp places where bacteria is present 7/22/2024 Objectives: Introduce safety practices related to H2S Discuss methods of detection for H2S 7/22/2024 General safety Even though H2S has very strong odor, it’s warning properties are poor. Often times, employees think that just because they can’t smell H2S that it’s not present. If odor is detected, leave area until source is identified, controlled, and area made safe. 7/22/2024 7/22/2024 General safety cont’d If you don’t have proper respiratory protection, STAY OUT! Use warning signs to alert personnel. Use fencing to keep unauthorized personnel out. 7/22/2024 General safety –wind direction indicators Post wind direction indicators in areas where H2S is present or has potential to be present. Wind direction indicators give visual cue as to presence and direction of wind. 7/22/2024 Use wind direction indicators, such as… Windsocks Flags Banners Streamers Use H2S monitors and detectors 7/22/2024 General safety signs Signs to indicate the potential for or the presence of H2S Signs to prohibit smoking Signs to prohibit ignition sources Other signs as needed 7/22/2024 General Safety -Fences Fence off dangerous areas, including: Tanks, Open pits, Wellheads Install fences far enough away Post signs on fences 7/22/2024 Monitoring equipment Two basic types of monitoring equipment: Fixed Portable 7/22/2024 7/22/2024 Fixed monitoring equipment Used in permanent locations Can detect single or multiple gases Have reset alarm level Have audio and visual alarms 7/22/2024 7/22/2024 Portable monitoring equipment Two basic types of portable monitoring equipment: Electronic Non-electronic 7/22/2024 Portable electronic monitors Can be single gas or multi-gas Usually handheld, clipped to belt, or carried in shirt pocket (should be in the breathing zone) Some have LCD Some alarm only 7/22/2024 Portable electronic Diffusion type monitors have a sensor that allows gas to enter, then uses microprocessor to determine the amount of gas present 7/22/2024 7/22/2024 Portable electronic monitor ‘BW Clip4’ app 7/22/2024 Portable electronic-advantages Accurate Light weight “Go anywhere” Easy to Use Low Cost 7/22/2024 Portable electronic -disadvantages Monitors must be calibrated and tested Must order calibration gas Sensors expire Calibration gas expires Sensors can be “overloaded” 7/22/2024 Portable non-electronic Pump draws known amount of air through tube filled with reagent Reagent changes color Amount of color determines amount of gas present 7/22/2024 Portable non -electronic- advantages Relatively low cost No batteries Easy to use 7/22/2024 Portable non-electronic-advantages Accuracy is about + 25% Pumps can leak H2S can corrode the pump Have broken glass tubes 7/22/2024 Portable non-electronic - disadvantages Tubes expire Cannot mix pumps and tubes from different manufactures Colors may be hard to read 7/22/2024 https://youtu.be/ZkoKCvL_jwU https://youtu.be/5P-PoIUE6LI 7/22/2024 7/22/2024 24 June 2019 / ‹#› CONTROL OF SPILLAGES, USE OF SPILL KITS 24 June 2019 / ‹#› CHEMICAL SPILL KIT You can clean up minor chemical spills where there are no injuries, that do not pose any threat of a fire and for which you have the proper training and proper protective equipment. Chemical spill clean-up kits are helpful to have in the laboratory and other service areas which use chemicals. The kits are useful if you and your fellow workers know how to use them properly. Chemical absorbent pads or socks or neutralising powder can be used to quickly contain a spill. Use these items only if you are not in any danger. Often the best use of such a kit is to put the absorbent on the spill to contain the chemicals, then leave the room and secure the area until the proper authorities arrive to finish the clean-up. Emergency spill kit 24 June 2019 / ‹#› Is this an emergency? If you can clear up the leak on the spot it should not be regarded as an emergency. If you are not sure, consider it an emergency. The following are examples of spills and leaks that should be considered emergencies: Type of spill Amount Examples extremely flammable liquids 500 ml propylene oxide flammable liquids 750 ml toluene combustible liquids 750 ml mineral spirits toxic, volatile liquids 750 ml ammonia concentrated acids 4.5 litre sulphuric acid concentrated alkalis 4.5 litre lye solution poisonous, reactive materials Any amount cyanides, sulphides oxidising agents 500 mg concentrated nitric acid leaks from gas cylinders uncontrolled oxygen, acetylene Table 1: Examples of spills and leaks that should be considered emergencies 24 June 2019 / ‹#› FIRST RESPONSE TO A CHEMICAL SPILL Move away from the immediate area: The first person to notice the spill or leak should move away from the immediate area of the spill in order to evaluate the situation without breathing in any fumes from the chemical. Check the wind direction to ensure that you move downwind of the spill. This may not be necessary if it is a small spill of a harmless chemical. Try to identify the spill: Do so without placing yourself at risk. This includes identifying: ▪ the type of material spilled (e.g., from the label); ▪ the size of the spill and whether the leak has stopped; ▪ whether two chemicals are involved in the leak and could react with each other; ▪ any unusual features such as foaming, odour, fire, etc. 24 June 2019 / ‹#› PROCEDURES TO HANDLE MINOR CHEMICAL SPILLS Tell everyone in the immediate area about the spill. Avoid breathing in vapours/fumes from spill. Put on protective equipment, including safety goggles, suitable gloves, and long- sleeved laboratory coat/overall. Confine spill to small area, i.e. stop it from spreading. Use appropriate materials to neutralise and absorb inorganic acids and bases. Clear up the chemical waste material, place in the appropriate container, and dispose as chemical waste. For other chemicals, absorb spill with vermiculite, dry sand, or absorbent pads. Clean spill area with water. 24 June 2019 / ‹#› PROCEDURES TO HANDLE MAJOR CHEMICAL SPILLS Attend to injured or contaminated persons and remove them from exposure. Alert people in the area to evacuate. If spilled material is flammable, turn off ignition and heat sources. Close doors to affected area. Call the emergency controller. Be prepared to tell the emergency controller the following: Your name and department/workplace What chemical(s) are involved How much was spilled Where the spill is located. 24 June 2019 / ‹#› CONTINUED Nature of any injuries What control measures have been taken Wait for spill clean-up personnel to arrive 24 June 2019 / ‹#› 24 June 2019 / ‹#› NOISE AWARENESS 24 June 2019 / ‹#› Noise Exposure At Work Contents: The effects of noise on hearing, Hearing protection – purpose, types and use, Purpose of Noise monitoring and how it’s done. 24 June 2019 / ‹#› What Exposure to Loud Noise Will Do Exposure to loud noise will inevitably cause hearing loss over time. Loud noise damages or destroys the nerves in the inner ear. Another effect can be “tinnitus” or permanent ringing in the ear. 24 June 2019 / ‹#› EFFECTS OF NOISE EXPOSURE When is Noise Too Loud? Noise is measured in units called “decibels” or “dBA” If two people 1 Meter apart must shout to be heard, the background noise is too loud (above 85 decibels). Noise above 140 decibels causes pain and immediate hearing loss. 24 June 2019 / ‹#› Effects of Noise Exposure Our ears can recover from short exposure to loud noise, but over time nerve damage will occur. The longer and louder the noise, the greater chance permanent damage will occur. There is really no such thing as “tough ears” or “getting used to it”. 24 June 2019 / ‹#› Effects of Noise Exposure Hearing loss from noise exposure is usually not noticed because it is so gradual. Usually a person loses the ability to hear higher pitches first. Often the first noticeable effect is difficulty in hearing speech. Scientific studies have shown that hearing loss can occur when 8-hour average noise exposure exceeds 85 decibels. 24 June 2019 / ‹#› Effects of Noise Exposure The table below shows noise levels and how long a person can be exposed without hearing protection before there is damage to the ear. Noise Level Allowable Exposure Time 80 decibels 8 hours 90 decibels 4 hours 100 decibels 1 hour 105 decibels 30 minutes 110 decibels 15 minutes 115 decibels 0 minutes 24 June 2019 / ‹#› Noise Levels Examples of Commonly Used Noisy Equipment Equipment Noise Level Back Hoe 85-95 decibels Chain Saw 110 decibels Front-end Loader 90-95 decibels Gunshot 140 decibels Jackhammer 112 decibels Lawn Mower 90 decibels Tractor 95-105 decibels Circular Saw 90-100 decibels 24 June 2019 / ‹#› Hearing Protection TYPES OF HEARING PROTECTION There are three types of hearing protection – ear muffs, earplugs and ear caps. Ear muffs and earplugs provide about equal protection, ear caps which are less common provide somewhat less protection. 24 June 2019 / ‹#› Hearing Protection – Ear Plugs Earplugs are made of foam, rubber or plastic and are either one-size-fits-all or in sizes small, medium and large. Some are disposable, some are reusable. They are lightweight, and require no maintenance. They are inserted into the ear canal. 24 June 2019 / ‹#› INSERTING FOAM EARPLUGS Earplug incorrectly inserted Earplug correctly inserted 24 June 2019 / ‹#› EAR MUFFS Ear muffs cover the whole ear and are preferred by some people. They have replaceable pads and some high-tech styles filter out specific noise pitches. They last longer than most plugs. 24 June 2019 / ‹#› Hearing Protection How can you hear anything with earmuffs on? Using earmuffs or plugs in noisy areas actually makes it easier to hear coworkers or machinery. They reduce overwhelming loud background noise. They are similar to dark glasses that reduce the sun’s glare making it easier to see. SOME FINAL WORDS 24 June 2019 / ‹#› ▪ Noise can cause serious permanent damage. ▪ This Damage is easy to avoid – use your PPE – and common sense! ▪ If you think you are being exposed to excessive noise – speak to your Supervisor or to your HSE Officer. 24 June 2019 / ‹#› P1.2 Describe the operation of safety documentation and procedures Safety documentation and procedures Safety documentation and procedures are crucial for maintain workplace safety and regulatory compliance, the following are some of the documentation and procedures every workplace must have. Policies and Procedures: These outline safety rules, expectations, and protocols within the organization. Standard Operating Procedures (SOPs): Detailed instructions on how to safely use hazardous equipment and perform specific tasks. Emergency Evacuation Plans: Clear guidelines for evacuating the workplace during emergencies. Risk Assessments: Assessments of potential hazards and risks in the workplace. Safety Data Sheets (SDS): Information about hazardous chemicals and substances Training Records: Documentation of safety training provided to employees. Incident Reports: Records of accidents, near misses, or injuries. Safety Inspections and Audits: Regular checks to identify safety issues. First Aid Procedures: Guidelines for providing first aid in emergencies. Lockout/Tagout (LOTO): Procedures to safely isolate and de-energize machinery or equipment during maintenance or repair. Confined Space Entry: Guidelines for working safely in confined spaces, including proper ventilation, communication, and rescue procedures. Fall Protection: Procedures for preventing falls from heights, including the use of harnesses, guardrails, and safety nets. Personal Protective Equipment (PPE): Guidelines on using and maintaining PPE such as helmets, gloves, goggles, and masks.. Fire Safety: Evacuation procedures, fire extinguishers usage, and emergency response plans. Chemical Handling and Storage: Proper procedures for handling, storing, and disposing of hazardous chemicals. Electrical Safety: Protocols for working with electrical equipment, grounding, and avoiding electrical hazards. Machine Guarding: Ensuring machinery has appropriate guards to prevent accidental contact with moving parts. Emergency Response: Procedures for handling medical emergencies, spills, or other critical incidents P1.3 Identify relevant emergency requirements for a maintenance workshop Emergency requirements for a maintenance workshop Minimum Light Levels: Adequate lighting is crucial for safety. Proper illumination helps prevent accidents and allows workers to navigate the workshop effectively. Ventilation: Proper ventilation helps maintain air quality, especially when dealing with chemicals, fumes, or exhaust. Good ventilation reduces health risks and ensures a safer environment. Ventilation: Proper ventilation helps maintain air quality, especially when dealing with chemicals, fumes, or exhaust. Good ventilation reduces health risks and ensures a safer environment. Disabled Access: Design the workshop to accommodate individuals with disabilities. Accessible ramps, doorways, and facilities are essential for inclusivity and safety. Space Requirements: Consider the number of occupants in the workshop. Ensure sufficient space for safe movement, equipment storage, and emergency response Remember, prioritizing safety in a maintenance workshop is essential for protecting workers and preventing accidents Who to contact in an emergency Main contents of a typical emergency response plan Emergency contacts Relevant strategy and procedures for response ie. Plant isolation Special procedures for dealing with particular circumstances Availability of resources /need for specialized equipment Details of offsite assistance available Emergency control center and locations of alternatives Training requirements for emergency planners Assembly point and alternatives How to review the plan and take care of new changes Operations risk evaluation Incident command structure and emergency response team members, their roles and obligations and their training requirements Details of alarm systems When to declare an emergency Internal notification protocols Identification of emergency responders Standard list of information required from the site of the incident Information to be released to the media Evacuation and abandonment procedures Critical factors considered for the successful response and evacuation of workers in an emergency Sufficient number of escape routes Presence of alternative means of escape in opposite directions from most situations Sufficient width of escape routes to accommodate the number of people, stretchers Reasonable travel distances between fire-resistant compartments Protection from the effects of fire, explosion and ingress of smoke Provision for manual call points to raise the alarm Provisions for firefighting equipment to aid escape Adequate lighting Provision of manual call points to raise the alarm Suitably located escape routes to enable persons to escape to safety Reasonable travel distances between fire resistant compartments Relevant signage in place Escape routes kept free from obstructions Availability of escape breathing apparatus Nonuse of elevators unless they are fire resistant Escape doors opening in the direction of travel where possible and never locked 24 June 2019 / ‹#› OGTS – M06 - 01 DESCRIBE THE PURPOSE OF SAFETY PROCEDURES/ DOCUMENTATION 24 June 2019 / ‹#› OGTS –M06 - 01 LEARNING OUTCOME Permit to work systems O1 24 June 2019 / ‹#› SESSION OBJECTIVES P2.1 Describe the purpose and types of permit to work systems P2.2 Describe the purpose of risk assessments 24 June 2019 / ‹#› Work - Permits 24 June 2019 / ‹#› 24 June 2019 / ‹#› 24 June 2019 / ‹#› PURPOSE OF PERMIT TO WORK This document and procedure emphasis on the PTW (Permit to Work) process as it should be applied within Total Energies. Therefore, the objective of this procedure is to: Ensure all the PTW phases are respected and correctly followed by all personnel involved; Define the roles and responsibilities in this process; Identify hazards linked to the work and evaluate the risk along the permit to work process; Ensure that precautions are recommended, implemented and maintained up to the end of the work; Coordinate the works, to avoid conflict of access or interferences of activities; Define the maximum validity period and the required complementary certificates for a permit to work. 24 June 2019 / ‹#› FIELD OF APPLICATION The provisions of this procedure apply to all TE´s sites, activities and operations. This procedure has to be transposed in a dedicated site instruction to provide methods for permit to works specific to certain contexts: work on sites without industrial operations (e.g. offices, living facilities, Logistic base…). In case of coexistence with a work permit between TE and a contractor (for example, supply vessel, barge and drilling platform), a "Bridging Document" is prepared to define the application areas of each system, and thus managing the interfaces between both parties, throughout the duration of the work. Notwithstanding the above indications, the Responsible for Safety and Environment on Site (RSES) Site Health, Safety Environment Manager. may decide at his sole discretion to cover any work by a PTW, if the RSES feels necessary to better control the risk of such work. 24 June 2019 / ‹#› Types of permit to work Depending on the type and complexity of the work, the work may be performed using one of the following forms: ▪ Standard Permit to work form; ▪ Routine permit form; (or simplified PTW); ▪ Or work that is authorized without PTW but via a Verbal instruction. Permit to work validity period. When the validity period of a PTW has expired, the work concerned cannot begin or be continued without a new permit to work A permit to work for cold work or hot work without naked flame shall expire 14 days after the opening date (within 24 hours after approval date) and may be reduced at RSES discretion. 24 June 2019 / ‹#› COLD PERMIT TO WORK The cold permit to work provisions apply by default to all types of works other than those covered by a more specific form and jobs not involving a naked flame, potential source of ignition (sparks etc.). 24 June 2019 / ‹#› HOT PERMIT TO WORK (A AND B) The Hot permit to work provisions apply when work involves actual or potential sources of ignition, namely: Jobs involving Naked flame spark or heat-producing sources (flame cutting, welding, grinding), unless used inside workshops or areas specifically designed for that purpose and not located in the vicinity of any hazardous area. The respective Hot permit is then rated as “Naked Flame” (Hot Permit to work A); Jobs involving “Non naked flame” Covers Other potential sources of ignition (hand tools, equipment not or no more intrinsically safe), located or used inside or nearby a hazardous area, and that cannot be isolated. The respective Hot permit is then rated as “Non naked flame” (Hot Permit to work B). 24 June 2019 / ‹#› ROUTINE PERMIT A simplified Permit to work, is used only for recurrent and low risk work that does not generate any co-activity or simultaneous operations. The routine permit shall be used: ▪ For regular or routine operating activities (carried out several times a year); ▪ For a duration of at least 7 days; ▪ To supported by approved procedures and routine job forms; ▪ Carried out by employees or contracted staff who are adequately trained and experienced, and are part of the permanent organization in place at the location (core team); ▪ Their risk assessment clearly shows that they do not involve unusual hazards or high rated risks; ▪ Supported by an approved Job Risk Assessment, as per procedure. 24 June 2019 / ‹#› WORK ON VERBAL INSTRUCTIONS : The min requirements for verbal authorization’re: ▪ Activities which are part of the regular operation of the installation and its equipment, in line with the design specifications and within the operating limits prescribed by the manufacturers; ▪ They are supported by suitable plans / schedules, procedures, instructions, checklists, and operating manuals; ▪ They are included on the list of the types of activities that may be carried out on verbal / written instructions. ▪ Inhibition / overriding of safety systems are not required to perform the activity; ▪ Activity is relatively simple to perform. NB: Any activity requiring isolation ▪ Activity is re-occurring on a regular base; cannot be executed under verbal instruction. ▪ Activities shall be performed by regular crew only; ▪ No electrical, process/mechanical or personal isolations required. 24 June 2019 / ‹#› COMPLEMENTARY PERMITS Specific operations require the use of complementary permits or specific authorizations in addition to any permit to work. Such as, but not limited to: ▪ Confined space entry permit; ▪ Electrical isolation sheet; ▪ Process / mechanical isolation; ▪ Critical lifts plans; ▪ Safety inhibit / override permit; ▪ In case of Simultaneous Operations, the permit to work ting system may be adapted as part of the SIMOPS dossier. 24 June 2019 / ‹#› P2-1 TO P2-4 HAZARD IDENTIFICATION &RISK ASSESSMENT 24 June 2019 / ‹#› HAZARD IDENTIFICATION RISK ASSESSMENTS Risk assessment in the context of a maintenance workshop involves identifying hazards, evaluating, and controlling potential hazards that could lead to accidents, injuries, or damage during maintenance activities. The goal is to ensure the safety and health of workers, as well as to protect equipment and the environment. 24 June 2019 / ‹#› PURPOSE OF RISK ASSESSMENTS To provide, by means of a consistent and systematic approach, a method to: - identify potential hazards, - Evaluate the potential Risk for personnel, the environment and the asset. - determine appropriate and sufficient control measures to reduce risks to an ALARP level, - develop an action plan to implement the compensatory measures. 24 June 2019 / ‹#› FIELD OF APPLICATION General case The provisions of this procedure are applicable to all sites and operations under the control of the Company (except otherwise stated in a specific instruction). They apply to jobs, which are considered to be safety critical in terms of risks that they may cause: - personnel injury, - environmental damages, - impact on safety critical element, - asset, material or production losses, 24 June 2019 / ‹#› Identify Hazards: Examine all activities, tools, equipment, and materials used in the workshop. Look for potential sources of harm such as moving machinery, electrical hazards, chemical exposure, ergonomic risks, and manual handling tasks. Assess Risks: Evaluate the likelihood and severity of harm from the identified hazards. Consider factors such as the frequency of exposure, number of workers exposed, and the potential consequences of an incident. Monitor and Review: Regularly check the effectiveness of control measures. Review and update the risk assessment periodically or when there are changes in the workshop activities, equipment, or after an incident. Documentation: Keep detailed records of the risk assessment process, findings, and actions taken. Ensure documentation is accessible to all relevant personnel. Determine Control Measures: Identify appropriate measures to eliminate or reduce the risks to an acceptable level. Control measures can include engineering controls (e.g., machine guards, ventilation), administrative controls (e.g., training, procedures), and personal protective equipment (PPE). Implement Control Measures: Put the identified control measures into practice. Ensure all workers are trained and understand the new procedures and controls. 24 June 2019 / ‹#› P2.1 identify potential hazards in workplace environment 24 June 2019 / ‹#› Hazard identification defined Hazard identification is the process of identifying potential hazards in the workplace that can cause harm to people, property, or the environment. This process involves recognizing situations or conditions that have the potential to cause injury and taking steps to prevent accidents or harm. Hazard identification is a critical step in the risk management process and is essential for creating a safe and healthy work environment. It involves identifying hazards associated with tasks, equipment, or the work environment, and then taking measures to control or eliminate these hazards to ensure the safety and well-being of employees. 24 June 2019 / ‹#› Methods of Hazard identification 1. Workplace Inspections: Regular inspections of the workplace can help identify any potential hazards or unsafe conditions. 2. Incident and Accident Investigation: Reviewing past incidents and accidents can help identify underlying hazards and prevent future occurrences. 3. Job Safety Analysis (JSA): Analyzing each step of a job to identify potential hazards and determine the best way to perform the task safely. 4. Safety Data Sheets (SDS): Reviewing SDS for chemicals and hazardous materials to understand their potential hazards and safe handling procedures. 5. Employee Reports: Encouraging employees to report any potential hazards they encounter in the workplace. 24 June 2019 / ‹#› Maintenance Hazards Maintenance hazards can include electrical hazards, such as working with live wires or faulty equipment, which can cause electrical shock or fires. Other hazards may include working at heights, handling heavy machinery and equipment, exposure to chemicals, and potential for slips, trips, and falls in the maintenance area/workshop. It's essential to identify and mitigate these hazards to ensure the safety of maintenance workers and those in the surrounding area. Common Hazards in Maintenance Workshops Mechanical Hazards: Moving parts of machinery can cause injuries such as cuts, entanglement, and crushing. Electrical Hazards: Working with or near electrical equipment can lead to electric shock or burns. Chemical Hazards: Exposure to hazardous substances (e.g., solvents, lubricants) can cause health issues. Ergonomic Hazards: Poorly designed workstations or repetitive tasks can lead to musculoskeletal disorders. Noise and Vibration: High levels of noise and vibration from tools and machinery can affect hearing and health. Fire and Explosion Hazards: Flammable materials and processes can pose fire risks Poor House keeping: cluttered materials, cables, tools P2.2 Describe the associated risk and implication for people equipment and environment. Risk and implication for people equipment and environment. 1. Mechanical Hazards Risks: Entanglement in moving parts. Implications for Equipment: Cuts or amputations from sharp edges or Damage to machinery. tools. Increased maintenance Crushing injuries from heavy machinery costs. or equipment Implications for the Implications for People: Environment: Serious injuries or fatalities. Potential oil or hydraulic fluid leaks from damaged Permanent disability. equipment 2.Electrical Hazards Risks: Electric shock or electrocution from exposed wires or faulty equipment. Electrical fires. Implications for People: Burns, cardiac arrest, or death. Implications for Equipment: Fire damage to electrical equipment. Downtime due to equipment failure. Implications for the Environment: Fire spreading to nearby areas, causing broader environmental damage. 3. Chemical Hazards Risks: Exposure to hazardous substances such as solvents, lubricants, or cleaning agents. Chemical burns or respiratory issues from inhalation. Implications for People: Acute health effects such as skin irritation or respiratory problems. Chronic health conditions from long-term exposure. Implications for Equipment: Corrosion or damage to equipment from chemical spills. Implications for the Environment: Contamination of air, water, or soil from chemical spills. 4. Ergonomic Hazards Risks: Strain from repetitive motions or awkward postures. Musculoskeletal disorders from lifting heavy objects improperly. Implications for People: Chronic pain or long-term disability. Reduced productivity due to discomfort or injury. Implications for Equipment: No direct impact, but improper handling of equipment can lead to damage. Implications for the Environment: Minimal direct impact, but inefficient work practices can lead to increased waste. 5.Noise Hazards Risks: Hearing loss from prolonged exposure to loud machinery. Implications for People: Permanent hearing damage or tinnitus. Increased stress or communication difficulties. Implications for Equipment: No direct impact. Implications for the Environment: Noise pollution affecting nearby areas. 6. Fire and Explosion Hazards Risks: Fires from flammable materials or faulty electrical systems. Explosions from pressurized equipment or volatile chemicals. Implications for People: Burns, injuries, or fatalities. Implications for Equipment: Complete destruction of machinery or tools. Implications for the Environment: Large-scale environmental damage from fire or chemical release. 7.Slippery or cluttered floors leading to accidents. Risks: Slips, Trips, and Falls Implications for People: Injuries such as fractures, sprains, or head trauma. Implications for Equipment: Damage to equipment from being dropped or struck during a fall Implications for the Environment: Potential spills of hazardous materials if containers are knocked over. 8. Confined Spaces Risks: Asphyxiation or toxic atmospheres in confined spaces. Implications for People: Suffocation or poisoning. Implications for Equipment: Challenges in equipment operation and maintenance in confined spaces. Implications for the Environment: Accumulation of hazardous gases or materials. P2.3 describe measures that can be taken to minimize risks in maintenance workshops When controlling hazards And minimizing risks, we focus on the hazard control hierarchy. The hazard control hierarchy is a systematic approach to minimizing or eliminating exposure to workplace hazards. It consists of several levels, each representing a different control measure. The hierarchy typically includes the following levels: 1. Elimination: This involves physically removing the hazard from the workplace. If the hazard is no longer present, there is no risk of exposure. 2. Substitution: This involves replacing the hazardous material, process, or equipment with a less hazardous alternative. This can help reduce the risk of harm to workers. 3. Engineering Controls: These are physical changes to the workplace, such as installing barriers, ventilation systems, or noise enclosures, to isolate people from the hazard. 4. Administrative Controls: These controls involve changing the way people work, such as implementing policies, procedures, or training to minimize exposure to hazards. 5. Personal Protective Equipment (PPE): When hazards cannot be eliminated or substituted, PPE such as gloves, goggles, or respirators can be used to protect workers from exposure. 7/22/2024 P2.4 carry out and record a RA for a maintenance workshop 7/22/2024 Methods of Risk Assessment 1. Preliminary Hazard Analysis (PHA): This method involves identifying and evaluating potential hazards at the early stages of a project or process. 2. Failure Mode and Effects Analysis (FMEA): FMEA is a systematic approach to identifying and preventing potential failures within a system, product, or process. 3. Fault Tree Analysis (FTA): FTA is a deductive approach to analyze the ways in which an undesired event can occur. 4. Event Tree Analysis (ETA): ETA is a graphical technique used to determine the possible outcomes of a series of events. 5. Bow-Tie Analysis: This method visually represents the relationship between causes and consequences of a potential hazard, as well as the control measures in place to prevent the hazard from occurring. 6. HAZOP (Hazard and Operability Study): HAZOP is a structured and systematic examination of a process to identify potential hazards and operability problems. How to conduct a risk assessment in a maintenance workshop Step 1: Identify hazards - Identify and list all potential hazards that could cause harm or damage in the workplace, project, or process. Step 2: Identify who might be harmed and how - Consider who may be affected by the identified hazards and how they might be harmed. This includes employees, visitors, contractors, etc. Step 3: Evaluate and prioritize risks - Assess the likelihood and severity of the identified risks. Prioritize the risks based on the level of potential harm and the likelihood of occurrence. Step 4: Control measures - Develop and implement control measures to eliminate or reduce the risks. This may involve engineering controls, administrative controls, or the use of personal protective equipment (PPE). Step 5: Record findings - Document the findings of the risk assessment, including the identified hazards, the risks, and the control measures put in place to mitigate those risks. Step 6: Review and update - Regularly review and update the risk assessment, especially when there are changes in the workplace, processes, or regulations. 24 June 2019 / ‹#› Production Shortfall X < 2 kboe 2 kboe < X < 20 kboe 20 kboe < X < 200 kboe 200 kboe < X < 1 Mboe 1 Mboe < X < 10 Mboe X >10 Mboe (MAP) Long-term emission leading to negligible Long-term emission leading to very limited Long-term emission leading to significant Long-term emission leading to very significant Long-term emission leading to extremely Long-term emission leading to limited potential Chronic risks (SEES) potential harm to the environment and/or people potential harm to the environment and/or people harm to the environment and/or people off site potential harm to the environment and/or people potential harm to the environment and/or people significant potential harm to the environment off site off site off site off site and/or people off site ”Notices” in the national media + press agency Local media (written press, radio, TV). dispatch(es). Negative comments on social “Report” in the national media; Numerous Comments on local or national media websites. networks and/or intervention by national “Report” in international media; Negative comments on social networks and/or intervention by negative comments on social networks and/or Media No reaction. Information on social networks (Facebook, influencers with more than 500 followers on interventions by national influencers, in the local international influencers; Twitter, discussion forums, etc.) in the local Facebook or Twitter in the local language(s) or Reuse of the event by personalities (political, NGOs, etc.) followed by negative mobilization. language(s) or the Group’s official languages. language(s). the Group’s official languages (English and French). Severity scale from CR-GR-HSE-801 (Human, Env, Material & Media) Material X < €20 k €20 k < X < €200 k €200 k < X < €2 M €2 M < X < €10M €10 M < X < €100M X > €100M Severity scale for Production shortfall & probability scales from ex-CR EP HSE 102 Temporary exceedance of an emission Very localized pollution with minimal impact on Pollution of small area with limited impact on the Large-scale pollution in ecosystems of Pollution with massive and lasting Environmental standard; accidental spillage below the Group’s Pollution with significant environmental impact. consequences for vast ecosystems of high the environment. environment. recognized ecological interest. statistical reporting threshold. ecological interest. Internal: permanent disability or a fatality. Internal: multiple fatalities. Internal: numerous fatalities. Recordable incident without lost time, medical Recordable with lost time, including temporary Human First aid treatment including restricted work disability (without permanent disability) External: injuries among local populations. External: one fatality and/or numerous injuries External: multiple fatalities among local Transport or security related third party fatality. among local population. population. Severity of Consequence Production Shortfall Chronic risks (or Gain) (SEES) Human, Environmental, Material and Media Minor Moderate Serious Very Serious Catastrophic Disastrous 1 2 3 4 5 6 Incident almost inevitable under Very likely exposure Very Likely current conditions (or for gain) Certain fully successful modification to long-term Expected to occur several times during plant lifetime > 10-1 6 6 12 18 24 30 36 emission outcome Likelihood of Occurrence Incident probable with additional factors (or for gain) High likelihood of Likely exposure to Likely fully successful modification long-term emission Could occur several times during over plant lifetime 10-1 - 10-2 5 5 10 15 20 25 30 outcome Incident possible with additional Unlikely exposure to Could occur once for every 10 to 20 similar plants Unlikely factors (or for gain) Some uncertainty long-term emission over 20 to 30 years of plant lifetime 10-2 - 10-3 4 4 8 12 16 20 24 of successful modification outcome Combination of rare factors required One time per year for at least 1000 units. One time Very unlikely Very Unlikely to cause an incident (or for gain) for every 100 to 200 similar plants in the world over High uncertainty of successful exposure to long- 20 to 30 years of plant lifetime. Has already occurred 10-3 - 10-4 3 3 6 9 12 15 18 term emission modification outcome in the company but corrective action has been taken Extremely unlikely Has already occurred in the industry but corrective Extremely Freak combination of factors required to cause an incident exposure to long- action Unlikely 2 2 4 6 8 10 12 term emission has been taken 10-4 - 10-5 Event physically possible but has never or seldom Remote exposure to occurred over a period of 20 à 30 years for a large Remote No similar incident in industry long-term emission amount of sites (> few thousands, ex: wagons, < 10-5 1 1 2 3 4 5 6 process drums,…) Major Consequence Definitions: Risk Level 3 Broadly acceptable risk level Risk Level 2 Tolerable risk level if demonstrated to be ALARP Risk Level 1 First Priority, risk level to be obligatorily reduced to Level 2 or 3 24 June 2019 / ‹#› PERMIT TO WORK EXAMPLE OF RISK ASSESSMENT COMMENTS HAZARDS IDENTIFICATION LINKED TO THE JOB LOCATION GOLDEN RULES LINKED TO THE JOB q Classified Area : q 0 ; q 1; q 2; q Non Hazardous Work at height q Work on scaffold q Presence of: q Liquid HC; q Flammable material Manual handling q Use of hand tools q Presence of: q Gaseous HC; q Toxic gas q Presence of: q Open drain ; q Vent; q Sample point Lifting: Simple/Routine; Critical (Complicated/Complex) Work with chemicals / lubricants / paints / solvents q High temperature q Electrical works; q Instrum & ICSS works q Noisy area OTHER HAZARDS AND ASSOCIATED RISKS ADDITIONAL PRECAUTIONS AND PREVENTION MEASURES q Blasting; q Painting; q Dust emission q Automatic actuation of nearby equipment q Work on Rotating equipment / moving parts q Live electrical equipment close by; q Aerial power lines q Use of pressurized tools / hoses (Air, N2, Hydr., water…) q Interference with adjacent works q Use or handling of compressed gas (cylinders,…) q Underground network: q pipes; q cables; q culvert q Use of electri