NEBOSH Oil & Gas Manual PDF
Document Details
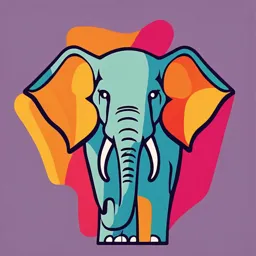
Uploaded by SoulfulTranscendental
University of the Philippines
NEBOSH
Tags
Related
- Health and Safety in Oil and Gas Processing Operations PDF
- Pedoman Process Safety & Asset Integrity Management Systems (PSAIMS) PDF
- API RP 580 2023 PDF - Elements of a Risk-Based Inspection Program
- HSOH 4100 - International Technical Certificate in Oil and Gas Operational Safety PDF
- Icarus-ORM Academy Oil & Gas Industry Process Hazards Guidebook 2021 PDF
- Hanwei HRLD Series Handheld Laser Methane Detectors PDF
Summary
This document is an introduction to Oil and Gas operational safety. It outlines expected learning outcomes, definitions of safety, and introduces the importance of health and safety training in the oil and gas industry, using examples of major safety incidents. The document also introduces concepts such as risk assessment, incident investigation, and hazard identification.
Full Transcript
TABLE OF CONTENTS Table of Contents i List of Abbreviations iii SECTION 1: Introduction 1 Expected Learning Outcomes 1 Definition of SAFETY 3 SECTION 2: HSE Management (Learning...
TABLE OF CONTENTS Table of Contents i List of Abbreviations iii SECTION 1: Introduction 1 Expected Learning Outcomes 1 Definition of SAFETY 3 SECTION 2: HSE Management (Learning From Incidents/Accidents) 4 I. Incident Investigation 8 II. Root Cause Analysis 18 III. Hazard Identification 28 IV. Risk Assessment 53 V. Documented Evidence 73 SECTION 3: Hydrocarbon Process Safety 79 I. Contractor Management 79 II. Process Safety Management 86 III. Permit - to - Work System 103 IV. Shift Handover 112 V. Plant Operations and Maintenance 117 VI. Start - up and Shutdown 132 SECTION 4: Inherent Safer Design Principle 144 I. Failure Models 144 II. Other Types of Failures 156 III. Safety Critical Equipment Controls 162 i IV. Safe Containment Principles 178 V. Fire Hazards 200 VI. Furnace and Boiler Operations 209 SECTION 5: Fire Protection and Emergency Response 217 I. Leak and Fire Detection Systems 217 II. Emergency Response 238 SECTION 6: Logistics and Transport Operations 260 I. Marine Transport 260 II. Land Transport 279 ii List of Abbreviations ABBI Above, Below, Behind, Inside ACGIH American Conference of Government and Industrial Hygienists ADR European Agreement Concerning the International Carriage of Dangerous Goods by Road ( AccordEuropeeneRelatif au Transport International des Merchandises Dangereuses par Route) AFFF Aqueous Film Forming Foam ALARP As Low As Reasonably Practicable AMA Advanced Medical Aid Ar Argon ATEX Atmosphere Explosives. Also, the name of commonly given to European directives for controlling explosive atmospheres BA Breathing Apparatus BLEVE Boiling Liquid Expanding Vapour Explosion B-O-P Blowout Preventer BOSIET Basic Offshore Safety Induction and Emergency Training CCR Central Control Room CCTV Closed Circuit Television CFD Computational Fluid Dynamics CNS Central Nervous System CO2 Carbon dioxide COMAH Control of Major Accidents Hazards COSC Combined Operations Safety Case CRO Control Room Operator CUI Corrosion Under Insulation CVCE Confined Vapour Cloud Explosion DCR Design and Construction Regulations DNA Deoxyreibonucleic Acid DP Dynamic Positioning DPI Dye Penetration Inspection DSEAR Danger Substances and Explosive Atmospheres Regulations DSV Diving Support Vessel DTLG Decommissioning Technical Liaison Group EBS Emergency Breathing System ECC Emergency Command and Control EER Evacuation, Escape and Rescue ELD Engineering Line Diagram ELSA Emergency Life Support Apparatus ERP Emergency Response Procedure ERRV Emergency Response and Rescue Vessel ESD Emergency Shutdown ESDV Emergency Shutdown Valve EU European Union F&G Fire and Gas FMEA Failure Mode and Effect Analysis FMECA Failure Modes and Effects Criticality Analysis iii FPS Floating Production System FPSO Floating Production Storage and Offloading unit FRC Fast rescue Craft GPA General Platform Alarm GPS Global Positioning System GRP Glass Reinforced Plastic GZ Drum Gas Zone Drum H2S Hydrogen sulphide HAZID Hazard Identification Study HAZOP Hazard and Operability Study HDPE High Density Polyethylene HIPPS High Integrity Pressure Protection System HLV Heavy Lift Vessel HP High Pressure HQ Headquarters HSE Health and Safety Executive HVAC Heat, Ventilation and Air Conditioning IDLH Immediately Dangerous to Life or Health IGC Code International code for the construction and equipment of ships carrying liquified gases in bulk IGG Inert Gas Generator ILO International Labour Office IMO International Maritime Organization KW Kilowatt kWm2 Kilowatt per square metre LEL Lower Explosive Limit LNG Liquid Natural Gas LOTO Lock Out, Tag Out LP Low Pressure LPG Liquefied Petroleum Gas LPI Liquid Penetration Inspection LSA Low Specific Activity MAPP Major Accident Prevention Policy MCRC Maximum Continuous Rating MEDIVAC Medical Evacuation MIG Manual Inert Gas MOB Man Overboard MODU Mobile Offshore Drilling Unit Mpa Mega Pascal MPGF Multipoint Ground Flare MPI Magnetic Particle Inspection MSDS Material Safety Data Sheet N Nitrogen NDT Non - Destructive Testing NORM Naturally Occurring Radioactive Materials NSMC North Sea Medical Centre NUI Normally Unmanned Installation OBM Oil Based Mud iv OIM Offshore Installation Manager OSCR Offshore Installations (Safety Case) Regulations 2005 OSHA Occupational Safety and Health Administration P&A Plugging and Abandonment (of wells) P&ID Piping and Instrument Diagram P&V Pressure and Vacuum relief valve PAPA Prepare to abandon Platform Alarm PFEER Prevention of Fire, Explosion and Emergency Response PFP Passive Fire Protection pH Power of hydrogen, i. e. a measure of how acidic a substance is PHA Process Hazard Analysis PIG Pipeline Inspection Gauge POB Personnel On Board PPE Personal Protective Equipment ppm Parts Per Million PSIC Protective Systems Isolation Certificate PSM Process Safety Management PSV Platform Support Vessel PT Penetrant Testing PTW Permit To Work RBM Risk Based Management RID European Regulations Concerning the International Carriage of Dangerous Goods by Rail (RéglementConcernat le Transport International Ferroviare des Merchandises Dangereuses par Chemin de Fer) ROSOV Remotely Operated Shut - Off Valve ROV Remotely Operated Vehicle RPE Respiratory Protective Vehicle RT Radiography Testing RTU Remote Terminal Unit SALM Single Anchor Leg Mooring SAR Search and Rescue SBM Single Buoy Mooring SBM Synthetic Based Mud SBV Standby Vessel SCC Stress Corrosion Cracking SCE Safety Critical Elements SIL Safety Integrity Level SIMOPS Simultaneous Operations SMART Specific, Measurable, Achievable, Realistic and with Timescales SMS Safety management System SOLAS Safety of Life at Sea SOLAS Specific Off - label Approvals SPM Single Point Mooring SRB Sulphate Reducing Bacteria SSCV Semi - Submersible Crane Vessel SSIV Subsea Isolation Valve STEL Short Term Exposure Limit TDS Total Dissolved Solids v TEMPSC Totally Enclosed Motor Propelled Survival Craft TIG Tungsten Inert Gas TLP Tension Leg Platform TLV Time Limit Valve TMT Tube Metal Temperature TR Temporary Refuge Tremcard Transport Emergency Card TWA Time Weighted Average UEL Upper Explosive Limit UKOOA United Kingdom Offshore Operators Association UN United Nations UNECE United Nations Economic Commission for Europe UVCE Unconfined Vapour Cloud Explosion VCF Vapour Cloud Fire VCT Vocational Training Certificate VDU Visual Display Unit VESDA Very Early Smoke Detection Apparatus VLSSCV Very Large Semi - Submersible Crane Vessel WBM Water Based Mud vi SECTION 1: Introduction SECTION 1 Introduction EXPECTED LEARNING OUTCOMES The syllabus set by NEBOSH (The National Examination Board in Occupational Safety and Health) for the International Technical Certificate in Oil and Gas Operational Safety is broken down into individual sections, which have been translated into 5 sections within this course. Each section has a clear learning outcome and command words are used in the learning outcome to indicate what is required of the student in relation to each item of content. Examination questions are set by NEBOSH to discover not only how much of a subject a student knows but also the associated skills that they are expected to demonstrate. Marks are then based on how effectively these skills are demonstrated. Command words are the guides in the question as to what assessment skill is being targeted by the question. These skills are generally knowledge, comprehension and application. KNOWLEDGE Knowledge requires an ability to recall or remember facts without necessarily understanding them. Command words used in knowledge based questions include identify. - Identify is asking for an answer, which selects and names a subject. For example ‘IDENTIFY three types of non-destructive testing of welds’. - Give is asking for an answer without an explanation. For example ‘GIVE an example of … ’; ‘GIVE the meaning of … ’. Introduction to Oil and Gas Operational Safety 1 SECTION 1: Introduction COMPREHENSION Comprehension requires an ability to understand and interpret learned information. Command words used in comprehension - based questions include outline. - Outline is asking for an answer, which supplies the principle features or different parts of a subject or issue. An exhaustive description is not required. What is sought is a brief summary of the major aspects of whatever is stated in the question. - Describe is asking for a detailed written account of the distinctive features of a subject. The account should be factual without any attempt to explain. APPLICATION Application is the skill of being able to take knowledge and apply it in different contexts and circumstances in order to understand why and where problems and issues arise. Command words used to assess the skill of application include explain. - Explain – This is asking for the reasoning behind, or an account of, a subject. The command word is testing the candidate’s ability to know or understand why or how something happens. INTRODUCTION The importance of effective health and safety training in the oil and gas industry is highlighted by extensively reported examples of major process safety incidents including: Deepwater Horizon oil - rig explosion in the Gulf of Mexico (2010) Buncefield oil storage depot explosion (2005) Piper Alpha oil platform explosion (1988) BP Texas City Refinery explosion (2005) 2 Introduction to Oil and Gas Operational Safety SECTION 1: Introduction Definition of SAFETY Safety is usually defined as ‘freedom from accidents or the condition of being safe from pain, injury or loss’. However, a more functional definition is ‘control of accidental loss’. This definition relates to injury, illness, and damage to anything in the occupational or external environment. It includes both preventing accidents and keeping losses to a minimum when accidents do occur. It also relates to the function of control in the management system. Loss prevention in the Oil & Gas, Chemical and Petrochemical industries involve: Identification and assessment of major hazards Control of hazards by containment, substitution, improved maintenance Control of process by utilizing automatic control, relief system, interlock, alarm Limitation of loss when accident happens By successfully completing this course we trust that you will: Have gained an understanding how to manage operational risks effectively within the oil and gas industry Be able to implement this knowledge within your own working environment to prevent process-related accidents that: Endanger health or life safety Damage plant and equipment (capital assets) Harm environmental quality Introduction to Oil and Gas Operational Safety 3 SECTION 2: HSE Management (Learning From Incidents/Accidents) SECTION 2 HSE MANAGEMENT (Learning from Incidents/Accidents) Is it not true that when we hear SAFETY, the things that immediately spring to mind are the incidents that either influenced our own lives or had a negative impact on our working place? In other words, the things that we normally don't want to hear from! Learning from Incidents Safety and reliability of Complementary methods modern chemical processing (other than standard codes plants are mainly related to and practices), which are continuous plant operation, process orientated, are equipment reliability and plant required as a basis to ensure design integrity. adequate design. It is important to Moreover, the recognise the need to importance of formal eliminate potential problems identification and elimination as early as possible during the of safety, reliability and design stage of any project by operating problems has been the use of proper procedures, accentuated by economic codes and practices. pressures for larger processing units and equipment and However, with advancing operations to function in closer technology and new production proximity to known hazardous processes, it is not always conditions. practical or possible to stay abreast of developments. 4 INTRODUCTION TO OIL AND GAS OPERATIONAL SAFETY SECTION 2: HSE Management (Learning From Incidents/Accidents) Incident Recalls Some major incidents/accidents from the past… 1.) Flixborough England (1974) Flixborough, England, June 1, 1974: "It was a still, warm, sunlit afternoon. One moment the teacups were tinkling and the kettles whistling. The next moment, a blast of nightmarish intensity as the giant plant blew up and blotted out the sun."--Humberside Police Report Nypro Chemical Works in Flixborough, UK on June 1, 1974 Cyclohexane vapour cloud ignited Blast equivalent to 15 tons of TNT 28 were killed CAUSE: Faulty temporary piping design poorly qualified design team Accident let to the Control of Industrial Major Accident (CIMAH) Regulations - now superseded by COMAH. 2.) Mexico City (1984) Mexico City (1984) LPG Explosion 300 fatalities mostly offsite $20M direct damages 3.) Bhopal (1984) Bhopal, India. Union Carbide. 23. December 1984 Run-away chemical reaction occurred when a large amount of water entered into the MIC storage tank #610. Workers informed supervisor who took no action until too late. 40 tons of methyl-isocyanate spread for 2 hours 8km down Introduction to Oil and Gas Operational Safety 5 SECTION 2: HSE Management (Learning From Incidents/Accidents) wind over the city of 900,000 inhabitants. More than 2,000 victims died and 11,000 disabled with many more affected even up to today. Probable Cause: Management Failures. Resulted in several governments passing legislation that required better accounting and disclosure of chemical inventories. 4. Piper Alpha (1988) 6 July 1988 The production platform Piper Alpha was destroyed by an explosion and fire, initiated by a condensate leak in the gas compression module 165 of the 226 people on board died (together with 2 rescuers) Total cost of incident (excluding business interruption): ₤1,165 billion Probable Cause: Deficient analysis of the hazards present and poor plant design; inadequate maintenance and safety procedures. This incident lead to the formation of the Safety Case Regulations, which came into force in 1992. 6 INTRODUCTION TO OIL AND GAS OPERATIONAL SAFETY SECTION 2: HSE Management (Learning From Incidents/Accidents) 5.) BP Texas City Refinery (2005) On 23 March 2005 an explosion and subsequent fire caused major damage at BP’s largest refinery (USA’s third largest). The explosion was the result of an Unconfined Vapour Cloud Explosion from a release of Benzene/Heptane from a Raffinate Splitter on a 180 m3/hr Isomerisation Unit. The unit was being started up after a 2 weeks shutdown for reactor repairs. 12 months earlier an explosion on start-up had also occurred with no injuries. Learning from Incidents Why Should We Invest in Safety? If you think safety is expensive, try an accident...! We have had terrible accidents in the past! The legal costs and damage to the company's reputation are mostly irrecoverable. Training is one way to help people become more aware and knowledgeable about safety. Introduction to Oil and Gas Operational Safety 7 SECTION 2: HSE Management (Learning From Incidents/Accidents) Deepwater Horizon Oil Rig 21 April 2010 The drilling rig, owned by Transocean, was destroyed after an explosion and fire that followed a blow-out from the BP Macondo well 41 miles offshore Louisiana in 5000 ft water. 11 People were killed and 17 injured Extensive damage to the environment Costs to BP alone already amounts to $56 billion including the clean-up, response, settlements with victims, criminal penalties and civil charges. I. INCIDENT INVESTIGATION Two reasons why accidents and incidents should be investigated: Firstly, to determine the root cause Secondly, so that information forthcoming from the investigation can be used to prevent them from happening again Legal reasons for investigating accidents and incidents: To demonstrate that the company is meeting its legal requirement to investigate accidents and incidents Persons who have been affected by an accident may consider taking legal action against the company as a result. Consequently, employers should make available information regarding the circumstances appertaining to the accident, which result from any investigation. If needs be, the company can demonstrate to the judicial courts their commitment and positive attitude to health and safety by providing evidence of a thorough investigation of an 8 INTRODUCTION TO OIL AND GAS OPERATIONAL SAFETY SECTION 2: HSE Management (Learning From Incidents/Accidents) accident which subsequently allowed them to take steps to put in place measures to prevent any future recurrence. Financial Reasons for Investigating Accidents and Incidents: Information forthcoming from an accident investigation provided to an insurance company may well assist in the event of a claim. Investigating dangerous incidents and rectifying the cause, such as an escape of flammable vapour, could prevent a recurrence with potential catastrophic results, thus averting the cost of repairs and replacement and lost revenue, as well as potentially saving lives and preventing injuries. Other Reasons for Investigating Accidents and Incidents The information and insights gained from the investigation of accidents and incidents are invaluable. The following are examples of the kinds of things to be expected when a thorough investigation is conducted: How and why an accident/ or faults, for example, incident happened opening a flow valve too quickly might cause pressure What working practices and to build up beyond a safe procedures actually are – working pressure in a these may differ from what pipeline, resulting in an they should be (e.g. escape of flammable product employees may take from a flange unacceptable risks to make their work easier or faster) An investigation can highlight weaknesses in existing risk How exposure to conditions control measures and allow (e.g. noise, cold, heat) or employers to review and substances (e.g. chemicals, supplement them in order to radiation, gases) may affect prevent accidents/ incidents the health of employees in the future. Lessons learned in one department of an Weaknesses or faults in organization can be used in production systems whereby other departments, thus a certain scenario of events benefitting the organization will expose these weaknesses as a whole Introduction to Oil and Gas Operational Safety 9 SECTION 2: HSE Management (Learning From Incidents/Accidents) Benefits from Investigating Accidents and Incidents: The outcomes of an taken against the investigation can result company; increased in the company putting insurance premiums; measures in place to and loss of business due prevent the recurrence to a bad reputation, of similar accidents or resulting in lost orders. incidents in the future. The company can avoid The development of a business losses if they health and safety culture take heed of the within the company. outcome of an Following an investigation by investigation, any preventing further measures, which are put accidents or incidents. in place as a result of the findings will be more The benefits of remedial readily accepted by the action can be measured workforce, especially if in the number of they were involved in the potential lives saved as decision-making process. well as the potential savings of the cost of Managerial skills will be repairs and replacement developed during any and lost revenue. Other investigation and these costs saved might can be used in other include the cost of legal departments within the action, which might be organization. 10 INTRODUCTION TO OIL AND GAS OPERATIONAL SAFETY SECTION 2: HSE Management (Learning From Incidents/Accidents) W. H. HEINRICH'S DOMINO THEORY "The occurrence of an injury invariably results from a completed sequence of factors, the last one of these being the accident itself. The accident in turn is invariably caused or permitted directly by the unsafe act of a person and/or a mechanical or physical hazard." (W.H. Heinrich, Industrial Accident Prevention, 1931) Injury / Damage Incident Cost Categorizing Incidents Accidents and incidents result in outcomes. An outcome is the effect of an unplanned, uncontrolled event and can range from a mere escape of vapour which causes no ill effects and disperses into the atmosphere, to a major incident with structural damage and a number of injuries. An outcome can result in one of the following: Injury Minor injury (an injury which does not involve time off work) Significant injury (one which is not ‘major’ but which results in the injured person being away from work OR being unable to carry out their full range of normal duties) Major injury (those which, can be regarded as a serious threat to a person’s health and/ or well-being) Dangerous Occurrence or Damage Only Near miss Introduction to Oil and Gas Operational Safety 11 SECTION 2: HSE Management (Learning From Incidents/Accidents) A Dangerous Occurrence or Damage Only is an event that happens which has not involved injury to anyone, but which could have done. The following list of examples is not meant to be exhaustive: A fire or explosion not Electrical short circuit or resulting in injury overload causing a discharge spark An escape of flammable or Failure of industrial toxic gas, vapour or fluid radiography or irradiation equipment to de-energize or The collapse, overturning or return to its safe position failure of load-bearing parts after the intended exposure of lifts and lifting equipment period Explosion, collapse or bursting of any closed vessel or associated pipework A near miss is any unplanned incident, accident or emergency, which did not result in an injury or major damage. An example would be materials falling from scaffolding and almost hitting an employee underneath. A near miss must be reported to determine the cause in order for changes to be made to prevent it happening again. It has been proven many times in the past that it is necessary to investigate near miss incidents as thoroughly as you would for major incidents. Depending on the Severity of the Accident, the Investigating Team should Consist of the following members: Individuals involved Supervisor (both Operations and Maintenance) Safety Supervisor Top Management for the area affected Outside consultants (if required for specialist information) 12 INTRODUCTION TO OIL AND GAS OPERATIONAL SAFETY SECTION 2: HSE Management (Learning From Incidents/Accidents) The investigating team will need to have information and training regarding: Their roles and responsibilities How to identify which events need to be reported How to complete documentation Accident book regulations and requirements and how to use it as a source of historical information Documents and forms relevant to the investigation – internal and external The dissemination of information and to whom Investigating Accidents/Incidents Follows a Generally Accepted Four-stage Process: Step one – gathering information & establish facts Step two – analysis of the information (immediate, underlying & root causes) Step three – identifying the required risk control measures (required corrective actions) Step four – formulation of the action plan and its implementation Step 1 – Gathering Information & Establish Facts The process of gathering the information should ensure that it: Explores all reasonable lines of enquiry Is timely – should be done as soon as possible after the event Is structured, setting out clearly what is known, what is not known and records the investigative process This is the stage to collect information about: Where it happened? When it happened? Who was involved (NOTE: NOT who was responsible!)? What was involved? What else contributed? Introduction to Oil and Gas Operational Safety 13 SECTION 2: HSE Management (Learning From Incidents/Accidents) (why don’t we include the question: Why did it happen?) Relevant information will include: Sketches, measurements and photographs Instrument readings, records and logged information Check sheets, permits-to-work and details of the environmental conditions at the time if relevant Opinions, experiences and observations as well as events which led up to the accident/ incident should also be recorded but, be sure to distinguish between facts and opinions. Gathering information include the following methods: 1.1 Observations 1.2 Interviews 1.3 Design data 1.4 Using photo’s and other environmental data 1.1 Observations Good observation skills should include: Knowledge of the workplace and procedures Being open minded Being impartial and objective Keeping a systematic record of observations The observer should: Take time to observe the whole scene Be alert to possible changes to the accident scene by those who may have a motive to correct unsafe practices Use the ABBI technique: look Above, Below, Behind, and Inside Be inquisitive and question employees to determine risks – their views can be a valuable source of insight Use all senses including smell, sight, touch and hearing Have an open mind and look for solutions 14 INTRODUCTION TO OIL AND GAS OPERATIONAL SAFETY SECTION 2: HSE Management (Learning From Incidents/Accidents) Identify, record and feedback good performance as well as bad 1.2 Interviews Use an interview style, which does not reflect a blame culture. Ask questions in a way, which does not make the person being interviewed feel intimidated or uncomfortable. Conduct the interview in familiar surroundings as this will be less intimidating. Encourage co-operation by allowing witnesses to speak openly in their own words without using technical jargon. Promote a positive attitude to finding the reasons for the incident to prevent a recurrence in the future rather than apportioning blame for the present one. Interview witnesses separately and in private to prevent them from influencing each other’s accounts. Include questions related to possible underlying, contributing factors such as training, work pressure and emotional state. Provide a summary of what the witness said in order that they can ensure that everything has been understood correctly and that the interviewer has not misinterpreted the account. Step 2 – Analysis Of The Information Any analysis of the information collected should: Be objective and unbiased Identify the sequence of events and conditions that led up to the event Identify the immediate causes Identify underlying causes, i.e. actions in the past that have allowed or caused undetected unsafe conditions/practices Introduction to Oil and Gas Operational Safety 15 SECTION 2: HSE Management (Learning From Incidents/Accidents) Identify root causes, i.e. organizational and management health and safety arrangements – supervision, monitoring, training, resources allocated to health and safety, etc. Evaluate all factors and information gathered during Step one. Analysis of this information should result in supplying reasons why the incident happened. It may also become clear what further information is still required (we shall look at Root Cause analysis in detail at the end of this section). By involving all members of the investigating team, differing opinions can be considered and a broad view of the results gained. The analysis should be conducted systematically to make sure nothing has been missed and that an unbiased outcome can be reached as to the immediate, underlying and root causes of the accident. If necessary, this is also the stage when specialist opinions and expert knowledge can be obtained. Step 3 – Identifying the Required Risk Control Measures Once the findings of the investigation have evolved, they will highlight failings in the existing control measures, which led to the incident. They may also determine which control measures should be implemented in order to prevent a future recurrence. Another outcome of an accident investigation is that it will prioritize the risk control measures to be implemented. Recommendations must be based on key contributory factors and underlying causes, and aimed at eliminating the risk of possible reoccurrence. Usually those control measures, which eliminate the risk by using engineering controls are more reliable than those controls which are reliant on people. 16 INTRODUCTION TO OIL AND GAS OPERATIONAL SAFETY SECTION 2: HSE Management (Learning From Incidents/Accidents) Hierarchy of Risk Control: Eliminate the risk altogether. Substitute the risk for something safer. Apply engineering controls such as cut-out devices, guards, etc. Apply administrative controls such as safe working practices. Use Personal Protective Equipment (PPE), but only as a last resort or in conjunction with other controls. Step 4 – Formulation and Implementation of Action Plans Involvement of senior management in the formulation of an action plan will be necessary, as this level of management is generally the decision-making level within an organization. The investigation team must recommend additional risk control measures, which have been determined as a result of the investigation. The action plan will determine which control measures should be implemented in the short term (usually to manage the existing risk) and others which will be long term measures to eliminate or reduce the risks to an acceptable level. The Action Plan should have SMART Objectives: Specific Measurable Achievable Realistic, and with Timescales Introduction to Oil and Gas Operational Safety 17 SECTION 2: HSE Management (Learning From Incidents/Accidents) Accident/Incident Report Forms Whatever the format, all accident/incident reports must state: What happened – the injuries, losses and costs. How it happened – the event itself. Why it happened – the causes: root, underlying and immediate. Recommendations – any action to be taken to remedy the situation and prevent any recurrences. An efficient recording system will: Ensure the information is correctly and accurately presented. Allow the data to be analysed easily in order to discover common causes or trends. Ensure data, which may be required for future reference is included. Identify issues, which may help prevent any recurrence of the accident. Report forms should be reviewed on a regular basis to ensure that any recommendations have been implemented. II. ROOT CAUSE ANALYSIS Causes of incidents can be categorized into three basic types: 1. Immediate causes are generally unsafe acts and/ or conditions. 2. Underlying causes are generally procedural failures. 3. Root causes are generally management system failures. Immediate and underlying causes are also sometimes referred to as contributing causes 18 INTRODUCTION TO OIL AND GAS OPERATIONAL SAFETY SECTION 2: HSE Management (Learning From Incidents/Accidents) 2.1 Immediate Cause The most obvious reason why an adverse event happens, e.g. the guard is missing; the employee slips; the pipe flange fails, etc. There may be several immediate causes identified in any one adverse event. Immediate causes are those, which are responsible for the accident and are often easy to recognize. 2.2 Underlying Cause The less obvious ‘system’ or ‘organizational’ reason for an adverse event happening, e.g. pre-start-up machinery checks are not carried out; safe working procedures are not adhered to; the hazard has not been adequately considered via a suitable and sufficient risk assessment; production process pressures are too great, etc. 2.3 Root Cause Root causes are generally management, planning or organizational failings. For example, we mentioned safe working procedures not being adhered to, as an underlying cause. This could be because of lack of training or poor supervision, both of which are classed as root causes. Other examples of root causes include: A lack of rules and/or working procedures Insufficient training A general lack of commitment to safety Insufficient supervision Poor plant, equipment and layout design Poor working conditions There are many techniques used in determining the true picture of immediate and root causes of an accident/incident. One of the easiest and most commonly used is by applying a questioning technique, which constantly asks the five ‘W’ questions previously mentioned. We also use ‘why?’ to question the answers obtained until the obvious cause is clear. ? Introduction to Oil and Gas Operational Safety 19 SECTION 2: HSE Management (Learning From Incidents/Accidents) WE THEN APPLY THE ANSWERS TO A PICTORIAL DIAGRAM TO GIVE A CAUSAL TREE OF THE EVENTS. CLASS EXERCISE Use the questioning technique to determine the root cause for the following accident. Joe is one of the control room operators on board a floating production storage and offloading (FPSO) platform. He had been asked to inspect a fire and gas sensor some distance away from his normal work post. He decided to take a shortcut through an area that housed steam pipes. Unauthorized employees are not normally allowed in this area as the steam in the pipes is under pressure and of high temperature. Scene of the accident As he was passing by the piping, one of the flanges of the steam pipes emitted a blast of steam, which scalded Joe’s hand and he suffered serious burns. Joe was a walking wounded casualty and took himself to the medical bay for treatment to burns. An investigation into the incident was started. 20 INTRODUCTION TO OIL AND GAS OPERATIONAL SAFETY SECTION 2: HSE Management (Learning From Incidents/Accidents) The causal tree developed from continuously asking the question ‘why?’ has given us a clear picture of what all the true causes of the accident were. This leaves us with a clear indication of the actions, which need to be taken if we want to ensure there is no repetition of any of the events leading up to the accident. Another useful “tool” that can be used for Root Cause analysis (RCA) is the ‘Fishbone Diagram’ – also known as the Cause & Effect Analysis. FISHBONE DIAGRAMS The Fishbone diagrams are useful to help identify the most likely ROOT CAUSES of a problem. They can also help teach a team to reach a common understanding of the problem. This tool can help focus problem solving and reduce subjective decision - making. Using a fishbone diagram while brainstorming possible causes helps you to focus on the various possibilities. Some useful categories: Introduction to Oil and Gas Operational Safety 21 SECTION 2: HSE Management (Learning From Incidents/Accidents) Example: The Washing Machine Problem Description “Machine is 2 weeks old. When doing the fourth load of clothes, I heard a loud noise and the machine stopped! It wouldn’t re-start.” Problem Verification Service technician checks the washing machine operation to test procedure. The machine does not operate. Investigate Why 22 INTRODUCTION TO OIL AND GAS OPERATIONAL SAFETY SECTION 2: HSE Management (Learning From Incidents/Accidents) Introduction to Oil and Gas Operational Safety 23 SECTION 2: HSE Management (Learning From Incidents/Accidents) 24 INTRODUCTION TO OIL AND GAS OPERATIONAL SAFETY SECTION 2: HSE Management (Learning From Incidents/Accidents) Tools Used in Root Cause Analysis Tools Used in Root Cause Analysis Introduction to Oil and Gas Operational Safety 25 SECTION 2: HSE Management (Learning From Incidents/Accidents) Fishbone Diagram WHEN IS IT USED? When the need exists to display and explore many possible causes of a specific problem or condition. This diagram allows the team to systematically analyze cause & effect relationships. It can also help with the identification of ROOT CAUSES. WHAT DOES IT LOOK LIKE? HOW IS IT DONE? 1. Name the effect; determine the specific problem to be analyzed. Draw the diagram with a process arrow to the effect and draw a box around it. 2. Decide what the major categories of the causes are (i.e., people, machines, measurement, materials, methods, environment, policies, etc.). 3. Label categories important to your situation. Make it work for you. 4. Brainstorm all possible causes and label each cause under the appropriate category. 5. Post the diagram where others can add causes to it (i.e., experts, affected people, process owners, etc..). 6. Analyze causes and eliminate trivial and/or frivolous ideas. 7. Rank causes and circle the most likely ones for further consideration and study. 8. Investigate the circled causes. Use other techniques to gather data and prioritize findings. 26 INTRODUCTION TO OIL AND GAS OPERATIONAL SAFETY SECTION 2: HSE Management (Learning From Incidents/Accidents) Summary Root Cause Analysis is a method to focus our efforts on the true “Root Causes” of escapes, so that we truly prevent their reoccurrence. Root Cause Analysis helps us reduce turn - backs and frustration, maintain customer satisfaction, and reduce costs significantly. Each problem is an opportunity. It contains the information needed to eliminate the problem. But to identify the root cause, we have to ask “Why?” over and over, until we reach it. Introduction to Oil and Gas Operational Safety 27 SECTION 2: HSE Management (Learning From Incidents/Accidents) III. HAZARD IDENTIFICATION Hazard Definition Anything which may cause harm, injury, or ill health. An inherent physical or chemical characteristic of a material, equipment or process that has the potential for causing harm to people, the environment or property. (AICHE Center for Chemical Process Safety). Hazard Identification Hazard identification is the first step in the risk management- process. Only people with a thorough knowledge of the area, process or machine under review should carry out a hazard identification survey. The task of identifying hazards should be broken up into clear and manageable sections, in a manner, which suits the organisation, the task itself, and the people doing the work. Useful Resources for Hazard Identification 1.) PREVIOUS ACCIDENT REPORTS Location Day of Week Machine Part of Body Persons Severity of Injury Age of Persons Occupation Time of Day 2.) PHYSICAL INSPECTION OF THE WORKPLACE A physical examination of the workplace requires an inquiring mind, lateral thinking, and the ability to be and remain open- minded. It is of little use to look at a particular area and, in a perfunctory manner, declare it to be hazard free. 28 INTRODUCTION TO OIL AND GAS OPERATIONAL SAFETY SECTION 2: HSE Management (Learning From Incidents/Accidents) 3.) BRAINSTORMING This is a process of conducting group meetings with people who are familiar with the operation of the area under review, recording all ideas and thoughts relating to possible hazards and then sorting the results into some sort of priority order. Brainstorming requires the ability to “think outside the box” (lateral thinking) in order to exhaust all possible ideas. 4.) KNOWLEDGE OF EMPLOYEES Employees should be encouraged to report any hazards they are aware of. Remember; it is only the person involved that actually has the facts of what really happened. The person on ground level is most of the times the most informed. By building a relationship of trust, management can obtain facts without a fear of blame. 5.) TRADE JOURNALS Trade journals are often a source of information regarding hazards encountered by others in the industry. They can be a source of useful inquiry, as members of the same industry would expect to encounter similar hazards. 6.) OSH PUBLICATIONS These publications can be of particular benefit as they concentrate on reporting issues relating to safety and health. 7.) CONTACTS A colleague or friend in another subsidiary of the company, or even a contact in a competitive company, could be a good source of information as they probably share similar safety problems. Introduction to Oil and Gas Operational Safety 29 SECTION 2: HSE Management (Learning From Incidents/Accidents) Industry Associations Safety and health is often brought up at industry association meetings or during informal discussions before or after meetings. Generally the company’s own safety staff is also associated with SHE organizations and attend regular seminars where valuable information is shared amongst members. LEARNING OUTCOME Explain the purpose of, and procedures for, investigating incidents and how the lessons learnt can be used to improve health and safety in the oil and gas industries. REVISION EXERCISE Write your answers to the questions below on a separate sheet of paper without referring to the information in this book in the first instance. Once you have answered all of the questions, you can refer back to the revision guide to compare your answers, and this will give you an indication oh how much knowledge you have been able to absorb or whether you need to revise this section further. Q1 Outline FIVE reasons for investigating accidents and incidents. Include in your answer at least one legal reason and two financial reasons Q2 Identify the kind of persons you would expect to be involved in a team set up to investigate an accident/incident Q3 Identify the FOUR stages in the process of investigating accidents and incidents. Q4 Identify SIX observational skills or techniques used in accident/incident investigations. Q5 Give SIX sources of information relating to accident/incident investigations. Q6 In relation to causes of accidents, explain what is meant by: (a) immediate causes (b) underlying causes (c) root causes Q7 Give the hierarchy of risk control. Q8 Lessons learnt from major incidents can be 30 INTRODUCTION TO OIL AND GAS OPERATIONAL SAFETY SECTION 2: HSE Management (Learning From Incidents/Accidents) disseminated both locally and more widely. Outline who might benefit from lessons learnt: (a) locally (b) more widely Risk A risk is defined as the combination of the likelihood that the identified harm/hazard will occur and the seriousness of such an occurrence: The chance (likelyhood, frequency or probability) that somebody could be harmed or some infrastructure could be damaged. This is accompanied by an indication of how serious (consequence or severity) the harm could be. Process Hazard Analysis PHA is a structured, systematic study of what might go wrong in a process, in a design, or in an ongoing operation, which might cause an accident. Unexpected conditions, contamination, operator error, equipment malfunction, instrument failure, inadequate procedures, and other possible variations are considered as possible causes for any unwanted scenarios (hazards). DEFINITION FOR SOME INHERENT HAZARDS 1.) Flash Point The flash point of a volatile liquid is the lowest temperature at which it can vaporize to form an ignitable mixture when mixed with air. Importance Consequently, storing a fluid at a temperature below its flash point is an effective way of preventing ignitable vapours from forming. 2.) Vapour Density Vapour density is the measurement of how dense a vapour is in comparison with air. Comparing a vapour’s density with air indicates whether the Introduction to Oil and Gas Operational Safety 31 SECTION 2: HSE Management (Learning From Incidents/Accidents) vapour will rise or fall if it is released into the atmosphere. Importance So, if we say air has a density of 1, then any vapour with a density below 1 will rise as it is lighter than air, and any vapour with a density above 1 will fall as it is heavier than air. 3.) Vapour Pressure The process of evaporation involves the molecules on the surface of a liquid. When the energy within these molecules is sufficient for those molecules to escape, they do so in the form of a vapour. This is known as vapour pressure. Importance The greater the vapour pressure, the faster this process takes place, which results in a greater concentration of vapour. A substance with a high vapour pressure at normal temperatures is often referred to as volatile. 4.) Flammability Vapour, which is flammable presents the risk of an explosion. However, some vapours are more flammable than others and, as such, are categorized to indicate the level of risk involved. The degree of flammability can be expressed as: Flammable (inflammable: This describes a product, which is easily ignitable and capable of burning rapidly, with a flash point below 100˚F (37.8˚C). Highly flammable: a product which has a flash point below 21˚C but which is not defined as extremely flammable. Extremely flammable: a product, which has a flash point lower than 0˚C and a boiling point of 35˚C or lower. 5.) Fire Triangle For a fire to start, there are three elements which have to be present: - a source of fuel - a source of heat or ignition - oxygen 32 INTRODUCTION TO OIL AND GAS OPERATIONAL SAFETY SECTION 2: HSE Management (Learning From Incidents/Accidents) This is known as the ‘fire triangle’. If any one of these elements is eliminated, then a fire cannot continue or start. 6.) Flammable Range Within the fire triangle where the source of fuel is a vapour, for it to burn it has to fall within a specific percentage range in comparison with air. If the mixture of flammable vapour and air has too much flammable vapour in it, the atmosphere will not burn (too rich). Conversely, if the mixture of flammable vapour and air has too little flammable vapour in it, the atmosphere will again not burn (too lean). The lower flammable limit (LFL) is the lowest concentration of a gas or vapour in air, which is capable of being ignited. The upper flammable limit (UFL) is the highest concentration of a gas or vapour in air, which is capable of being ignited. The percentage of flammable vapour which falls between these two parameters (not too rich to burn but also not too lean to burn) is known as the flammable range. Importance There is always a risk of fire and explosion in an area, which contains vapour within the flammable range. It is vital, therefore, to control the atmosphere to make sure that the flammable range is not reached. Purging (replacing) the air in storage tanks with nitrogen is such a control. This is because nitrogen is an inert gas (i.e. it will not burn). Introduction to Oil and Gas Operational Safety 33 SECTION 2: HSE Management (Learning From Incidents/Accidents) 7.) Toxicity Toxicity is used in two senses: a) To denote the capacity to cause harm to a living organism b) To indicate the adverse effects caused by a chemical This information must be available on the Material Safety Data Sheet (MSDS), which comes with any chemical. The following further descriptions may be used: Acute toxicity is a term which describes the effect a substance has had on a person after either a single exposure or from several exposures within a short space of time (e.g. 24 hours or less). Chronic toxicity is a term which describes the effects a substance has had on a person after many exposures over a longer period of time (e.g. months or years). 8.) Carcinogens A carcinogen is defined as any substance that can cause, or aggravate, cancer. They fall into two groups: 1. Genotoxic carcinogens are those which react with DNA directly or with macromolecules which then react with DNA. There are no safe thresholds of exposure to genotoxic carcinogens. 2. Non-genotoxic carcinogens do not react directly with DNA although they do cause cancer in other ways. There may be some threshold exposure limits for substances which fall within this group. 34 INTRODUCTION TO OIL AND GAS OPERATIONAL SAFETY SECTION 2: HSE Management (Learning From Incidents/Accidents) PROPERTIES AND HAZARDS OF VARIOUS GASES ASSOCIATED WITH THE OIL AND GAS INDUSTRY 1. Hydrogen Hydrogen is a gas, which is difficult to detect as it is odourless and colourless. It is lighter than air (with a density of 0.07 when compared with air) and so will rise when released. Hydrogen is a highly flammable gas when it is mixed with air (flammable range 4– 75 per cent) and it burns with an invisible flame. The only way to detect burning hydrogen is when it ignites something else which has a visible flame. 2. Hydrogen sulphide (H2S) It is a toxic, corrosive and flammable gas. It has a density of 1.39 when compared with air and tends to drift in low-lying areas such as pits, cellars, drains, etc. As such, it is difficult to disperse. It is toxic when inhaled because, when it enters the bloodstream, it combines with the hemoglobin in red blood cells, preventing the absorption of oxygen into the blood, thus rapidly causing asphyxiation. Although hydrogen sulphide has a foul odour, it very rapidly paralyses the sense of smell and can quickly overcome anyone exposed to it and asphyxiate them. Even very low concentrations of the gas can prove fatal. For this reason, it has a Time Weighted Average (TWA) of 8 hours at 5 ppm, or 15 minutes at 10 ppm. (International limits may vary, please get to know your company’s specific specifications for H2S). Introduction to Oil and Gas Operational Safety 35 SECTION 2: HSE Management (Learning From Incidents/Accidents) 3. Methane Methane is an odourless, colourless gas, which exists naturally in the substrate. It is lighter than air with a density of 0.717 compared with air. It is a flammable gas and, when mixed with air in concentrations between 5 and 15%, is explosive. Although methane is not toxic at low concentrations, it can cause asphyxiation if the level is high enough to reduce the amount of inhaled oxygen. Natural Gas Natural gas is a gas consisting primarily of methane. It is found associated with other fossil fuels, and usually also contains lesser concentrations of ethane, propane, butane, pentane, and higher molecular weight hydrocarbons. Impurities such as elemental sulphur, carbon dioxide (CO2), water, helium, nitrogen and sometimes mercury are also present in natural gas as it is received from the well head. NGL Natural gas liquids (NGL): propane, butanes and C5+ (which is the commonly used term for pentanes plus higher molecular weight hydrocarbons). 4. LNG Liquefied Natural Gas (LNG) is a colourless, odourless, highly flammable natural gas, which is made up of methane (85 – 95%), ethane, propane and butane. It is non-corrosive and non-toxic although, like methane, it can cause asphyxiation if the concentration is high enough when inhaled. Liquefied natural gas at -162˚C takes up about 1/600th the volume of natural gas in the gaseous state. 36 INTRODUCTION TO OIL AND GAS OPERATIONAL SAFETY SECTION 2: HSE Management (Learning From Incidents/Accidents) 5. Liquefied Petroleum Gas (LPG) (LPG) is a mixture of hydrocarbon gases (mainly propane and butane) which are highly flammable. It is used as fuel in heating and cooking appliances and motor vehicles, and also as an aerosol propellant and refrigerant. LPG is an odourless, colourless gas which has a density of 2.0 when compared with air and tends to drift in low lying areas such as pits, cellars, drains, etc. As such, it is difficult to disperse. Liquefied Petroleum Gas (LPG) expands at a rate of 250: 1 at atmospheric pressure when it changes from a liquid to a gas. Consequently, it can cause a massive vapour cloud from a relatively small amount of liquid when that liquid is released into the air. To store LPG effectively, it has to be converted from a gas to a liquid, which means it is stored at a temperature of between 0˚C and −44˚C. Consequently, any moisture which settle to the bottom of the tank storing the LPG will need to be drained off. Liquefied petroleum gas (LPG) is toxic and can cause: - Asphyxiation - Cold burns to the skin on contact - Brittle fracture to carbon steel on contact - Environmental damage - Fire and explosion 6. Nitrogen Nitrogen is the most abundant gas in the earth’s atmosphere, 78% by volume. It is a colourless, odourless, non-flammable gas, which is often used as a blanket gas in storage tanks and for purging equipment and processes of oxygen and hydrocarbons, thus eliminating the hazards of fire and explosion. The primary hazard associated with nitrogen is asphyxiation when it is used in confined spaces to displace oxygen. Introduction to Oil and Gas Operational Safety 37 SECTION 2: HSE Management (Learning From Incidents/Accidents) 7. Oxygen Oxygen is an odourless, colourless gas, which is present in the atmosphere at 21% by volume. It is vital for sustaining life as it is breathed in and absorbed into the bloodstream. It is considered to be a safe gas, but it can present the following hazards: 1. Asphyxiation – this is because the body is stimulated to breathe by the level of carbon dioxide (CO2) in the air and should a situation arise where oxygen is released into an area displacing the carbon dioxide, then the stimulus to breathe could cease, causing death by asphyxiation. 2. It is one element of the ‘fire triangle’, i.e. it allows a fire to burn. 3. It can oxidize metal, i.e. cause rusting. PROPERTIES AND HAZARDS OF ASSOCIATED PRODUCTS 1. Anti-foaming Agents and Anti-wetting Agents Anti-foaming and anti-wetting agents are used to prevent foam forming or to break down foam that has already been created in a process liquid during any production processes. Foam can have a detrimental effect on product quality and production efficiency by slowing down the process. Anti-wetting agents are coatings, which are applied to surfaces of vulnerable components, which are subject to moisture and subsequent corrosive activities. They are known as ‘hydrophobic’ coatings, meaning they repel moisture. 2. Micro-biocides Micro-biocides are used to protect against the harmful effects of bacteria, e.g. legionella, which can proliferate in air conditioning systems and humidifiers. They do this by destroying the bacteria if it is present or by preventing its formation. 38 INTRODUCTION TO OIL AND GAS OPERATIONAL SAFETY SECTION 2: HSE Management (Learning From Incidents/Accidents) They are also used as corrosion inhibitors on some metals, e.g. steel pipelines. Micro-biocides are classed as irritants to skin and eyes on contact, as well as being toxic if ingested. 3. Corrosion Preventatives Corrosion is a major hazard in the oil and gas industry. Preventing corrosive activity from causing damage to infrastructure is essential. Some corrosion preventatives come in the form of a water- displacing film which acts by spreading across the surface of metals, displacing water from cracks and crevices and forming a barrier to corrosive activity. Other types of preventatives are applied to metals; they then dry to a hard resin or waxy film, thus forming a barrier to corrosive activity. 4. Refrigerants Refrigerants are liquefied gas under pressure and pose a minimal risk provided they remain contained within their allotted systems. Problems arise when there is an escape or release of the refrigerant because it can displace oxygen in the atmosphere with the potential to provoke asphyxiation. To minimize the risk it is advisable to conduct regular safety checks on all equipment and systems, and have in place emergency procedures to deal with any unexpected release of the refrigerant. Data relating to the refrigerant will be contained in the Material Safety Data Sheet (MSDS), which is provided with the product. This should state the toxicity status of the product as well as the safe exposure limits which apply. The hazards associated with refrigerants are: 1. Injury from components or material ejected by the high pressure escape 2. Frostbite injury to skin or eyes where contact with refrigerant is made 3. Asphyxiation Introduction to Oil and Gas Operational Safety 39 SECTION 2: HSE Management (Learning From Incidents/Accidents) 4. Possible explosion or fire if the refrigerant is flammable 5. When certain refrigerant gases burn they can produce other gases which can be very toxic 6. Liquid refrigerants have a very high expansion rate when changing from a liquid to a gas, causing overpressure 7. Refrigerant gases are heavier than air and will slump if the gases are accidently released Good practices and safe working procedures when dealing with refrigerants are as follows: Having procedures in place to deal with any unexpected release of refrigerant, e.g. recovery procedures and equipment to contain the refrigerant. Never working in confined spaces where there is a risk that refrigerants may be released. This is because of the very real risk of asphyxiation. Providing ventilation equipment to deal with any potentially high concentrations of refrigerant. Ensuring that anyone who is exposed to refrigerant gas is immediately moved out of the affected area to a place where they can breathe fresh air and be given oxygen as necessary. They will also need to be medically examined. 5. Water and Steam Water is used for cooling and dilution in process operations as well as for fighting fires, cleaning and within air conditioning systems. It does, however, present hazards, including: Legionella, which proliferates in air conditioning systems. Regular testing and maintenance systems can control this. Leptospira, which can be found in water, which has its source in freshwater rivers or lakes. This can be transmitted to humans via broken skin or through the mucous membranes of the eyes, nose or mouth and, in extreme cases, can cause Weil’s disease, which can be fatal. Effective personal hygiene can control this. 40 INTRODUCTION TO OIL AND GAS OPERATIONAL SAFETY SECTION 2: HSE Management (Learning From Incidents/Accidents) Corrosion, which attacks steel. Controls for this include applying a protective coating to steel components or fitting sacrificial anodes within the system to provide cathodic protection. The build-up of an electrostatic charge within pipe-work resulting in a potential explosion if this is discharged. To avoid electrostatic charge build-up, the flow rate of water should be controlled at a suitable rate and the pipe-work should be bonded to earth. An increase in pressure within pipe-work and other components within a system. This may be caused by an increase in temperature during hydrostatic pressure testing, e.g. where there is exposure to direct sunlight. This may cause failure of the system with catastrophic effects. 6. Freezing Water Water expands when it freezes, and this can result in the failure (fracture) of pipework and/ or other components within a system. Under certain conditions, plugs of ice (hydrates) can form and these can block pipes and pumps as well as preventing the closure of valves which, in critical situations, can have catastrophic effects. Controls preventing this can be: Lagging pipes considered to be at risk of being damaged by freezing water Fitting steam trace lines Draining unused components 7. Sea Water Sea water contains living organisms which can proliferate and cause blockages, e.g. in the heads of sprinkler systems and heat exchangers. This can be avoided by the implementation of a regular maintenance programme to ensure all parts of a system are kept free from blockages, as well as using additives to kill any Introduction to Oil and Gas Operational Safety 41 SECTION 2: HSE Management (Learning From Incidents/Accidents) living organisms, which may be present. A dry riser would also be a useful control. 8. Steam Steam is used extensively in the oil and gas industry. It is used to power turbines and generate electricity, as well as serving as a source of heat and/ or energy to assist with many other operations and processes. It can also be used to protect systems from the risk of freezing (tracer lines) and to serve as a heating system for areas where personnel are housed. Steam has inherent risks as follows: It can cause thermal shock to a system if it is introduced into cold pipes or steam lines. It can cause failure of parts of a system if there is an uncontrolled expansion within it, e.g. jointed flanges could fail as they are some of the weakest points of the system. It can cause burns if anyone comes into contact with it. 9. Mercaptans These are substances containing sulphur, which are used to help detect natural gas by giving it an odour (natural gas in pure form is odourless). T-butyl mercaptan blends are typically used for this purpose as they smell of rotting cabbage, even in low concentrations in air. Most mercaptans are harmful and has the following hazards associated with it: It is harmful if inhaled. It is a respiratory irritant – chronic exposure may cause lung damage. It is a skin irritant. It is an eye irritant. It can depress the central nervous system. It has a flashpoint of − 18˚C. 42 INTRODUCTION TO OIL AND GAS OPERATIONAL SAFETY SECTION 2: HSE Management (Learning From Incidents/Accidents) 10. Drilling Muds (Drilling Fluid) When drilling operations are in progress, mud is pumped from the mud pits through the ‘drill string’ where it is sprayed onto the drill bit. This allows for the cooling and cleaning of the drill bit throughout its operation. It also allows the crushed rock cuttings, which have been drilled from the bore hole, to be carried to the surface where they are separated from the mud by the use of a ‘shale shaker’ or other equipment before the mud is returned to the mud pit to be reused. There may be natural gases or other flammable materials, which have combined with the mud during the drilling operation. These have the ability to be released from the mud anywhere within the system where the mud is flowing back to the pit. As a result of this there is risk of fire or explosion should these gases be exposed to a source of ignition. Control measures to prevent this include: - Safe working procedures - Monitoring sensors - Equipment and wiring which has been certified as explosion proof Introduction to Oil and Gas Operational Safety 43 SECTION 2: HSE Management (Learning From Incidents/Accidents) 11. Low Specific Activity (LSA) sludge The formations of rock and shale, which contain oil and gas deposits also contain Naturally Occurring Radioactive Materials (NORM). These include: - Uranium - Thorium - Radium - Lead-210 Sludges are a mixture of liquid and suspended material and therefore present a range of hazards, for example: - Skin irritant (possibly causing dermatitis) - Inhalation (fumes or dust from dried sludges) - Ingestion (poor hygiene, i.e. not washing, not cleaning up, eating at work site) - Radiation - Carcinogenic - Environmental (pollutant) - Absorption through the skin (dermatitis) Other Hazards Associated with Oil and Gas The types of major hazard (to people, the environment, and property) inherent in operations of industrial and other activities are generally derived from the energy of the “systems” in operation. The types of energy include: Kinetic energy (e.g. momentum of moving vehicles) Potential energy (e.g. energy of a falling load) Chemical energy (e.g. heat energy from combustion) Toxic energy Other types of loss include: Loss of business Financial loss Contractual loss (financial or performance) Legal liability 44 INTRODUCTION TO OIL AND GAS OPERATIONAL SAFETY SECTION 2: HSE Management (Learning From Incidents/Accidents) Many others, depending on the branch of engineering or the type of activity undertaken The Main Types of Hazardous Incident That May Occur in a Process Plant and Associated Storage, Warehousing and Transport Operation 1. Major fire 2. BLEVE or fireball 3. Flash fire 4. Vapor cloud explosion (confined or unconfined) 5. Dust explosion 6. Other types of explosion 7. Toxic gas escape 8. Toxic fumes from fires 9. Chronic toxic exposure in the workplace (not strictly covered by this course, but mentioned for completeness) 10. Damage to the environment from abnormal gaseous or liquid escape 11. Spiral to disaster – “domino” incidents 12. Major equipment breakdown 1. Major Fires Flammable Liquid Fires Liquefied Flammable Gas Fires Flammable Gas Fires Flammable Powder Fires Highly Reactive Material Fires 2. Pool Fire A pool fire is a fire burning above a horizontal and stable pool of vaporizing hydrocarbon fuel. Liquid spills will expand on a surface until they Introduction to Oil and Gas Operational Safety 45 SECTION 2: HSE Management (Learning From Incidents/Accidents) achieve a certain critical thickness. As the pool increases in area, the proportion of fuel burning off increases until it eventually matches the rate of input. 3. Jet Fire A jet or spray fire is a flame which is being fed by hydro- carbons continuously being released with significant momentum in a particular direction. They are caused by the release of gaseous, flashing liquid and liquid inventories. Jet fires develop rapidly, and the extreme heat they generate can result in structural failure if the flame impinges on critical members of the structure. The properties of jet fires depend on: - Fuel composition - Release geometry - Release conditions - Wind direction and ambient conditions - Release rate Assessment of the hazards of jet fires is made by analysis of the length of the jet flame relative to the distances of equipment, buildings, people, etc. Consideration is given to the extent to which the affected area is impinged on, as well as the necessity for Passive Fire Protection (PFP) and emergency depressurization, as well as other options in order to mitigate the hazard. 46 INTRODUCTION TO OIL AND GAS OPERATIONAL SAFETY SECTION 2: HSE Management (Learning From Incidents/Accidents) 4. BLEVE’s and Fire Balls Spherical fire resulting from sudden release of liquid/ vapour Short duration - typically 5 to 20 seconds e.g. BLEVE (Boiling- Liquid Expanding Vapour Explosion) Can use to represent escalations 5. Flash Fires (VCF) A cloud of gas or vapour ignites and burns - no overpressure generated. The vapour cloud can be caused by: Evaporation of spilled liquefied flammable gas Evaporation of spilled flammable liquid heated to a temperature close to or above its atmospheric-pressure boiling point A leak of flammable gas A large spill of volatile flammable liquid If such a cloud is ignited in the open air, the most likely result is a “flash fire” or fire ball as the gas or vapor burns quickly with a soft whoomph. It is unlikely to burn fast enough to produce a damaging pressure wave or shock wave – just a bang. Introduction to Oil and Gas Operational Safety 47 SECTION 2: HSE Management (Learning From Incidents/Accidents) Such a fire, though brief, can kill or seriously injure anyone within the burning cloud; note that the cloud expands while burning. The effects are confined almost entirely to the area covered by the burning cloud. Vapour Cloud Fires (VCF’s) are important for two reasons: 1. There is the possibility that they may escalate and cause secondary fires elsewhere. 2. It is highly probable that a steady fire will follow a VCF, i.e. a pool or jet fire or a combination of both. 6. Vapour Cloud Explosion (VCE) If a cloud of flammable vapor is ignited, it may burn as a flash fire without a blast wave, or it may explode with a damaging blast wave. The likelihood of an explosion is increased if one or more of the following conditions apply: Confinement, partial confinement, or obstructions in the vicinity Large amount of vapor Mixture close to the stoichiometric composition, where the amount of oxygen exactly matches the amount of fuel to be burned Turbulence in the burning cloud The vapor being of a material that normally burns with a high flame speed The effect of a vapor cloud explosion is physical damage due primarily to the blast wave. In a chemical plant, this damage usually starts leaks that result in very damaging fires. In adjacent residential areas, the damage may range from broken windows to more serious structural damage. 48 INTRODUCTION TO OIL AND GAS OPERATIONAL SAFETY SECTION 2: HSE Management (Learning From Incidents/Accidents) A vapor cloud explosion may fatally injure people by: Projecting missiles Throwing people violently against solid objects Collapsing buildings Enveloping them in the burning or exploding cloud 7. Dust Explosions A mixture of flammable or combustible dust in air can explode if ignited. Many historical dust explosions have been in the form of repeated explosions following an initial small explosion. The cause of this is that the first explosion shakes loose dust that has accumulated on beams, etc., allowing a second or third explosion to occur in quick succession. These later explosions can be more damaging than the first one. More than 30 people were killed in an explosion of wheat dust in a silo building. The damage radius of a dust explosion is usually limited to the building in which it occurs, and to a very short range outside. 8. Other Explosions On any installation there is a possibility of a wide variety of explosions, including: Unconfined explosions (overpressure generated by the presence of obstacles) Confined explosions (overpressure generated by a combination of confinement and obstacles) External explosions (associated with confined, vented explosions) Internal explosions (e.g. within a flare stack) Physical explosions (e.g. a failing pressure vessel) Solid phase explosions (e.g. those which are associated with the use of well completion explosives) Mist explosions Introduction to Oil and Gas Operational Safety 49 SECTION 2: HSE Management (Learning From Incidents/Accidents) Some highly reactive materials, such as: - Ethylene Oxide - Organic Peroxides - Calcium Hypochlorite can decompose explosively if heated For example, in poorly controlled storage conditions, or if they become contaminated. 9. Exposure to Toxic Gases In processing oil and gas, and in the manufacture of products widely used in the community, the process industry commonly handles toxic gases, including: Hydrogen Sulfide Hydrogen Fluoride Chlorine Hydrogen Chloride Vinyl Chloride Ammonia Carbon Monoxide Some commonplace and normally safe materials generate toxic fumes when burned: PVC, Polyurethane - fire in the event of a tire burning at a warehouse Carbon Monoxide, Hydrogen Chloride from burning plastics, etc. in the smoke from house fires Pesticides, Herbicides (unburned toxic material in smoke) vaporized by the heat from a large warehouse fire The smoke normally initially rises due to its temperature, taking the highest concentration of toxic or irritant materials away from people closest to the burning installation. When the smoke has dispersed to a lower concentration, and the temperature is thereby lowered, the smoke plume may spread downward, too, resulting in exposure of people on the ground at a distance. 50 INTRODUCTION TO OIL AND GAS OPERATIONAL SAFETY SECTION 2: HSE Management (Learning From Incidents/Accidents) 10. Toxic Liquid or Gas Release Causing Damage to the Environment There is rarely a significant hazard to people, unless it has the potential to find its way into the drinking water or the food chain. Example - a large escape of a corrosive material, such as a strong acid could flow onto a public roadway where people could walk into it without recognizing its hazard, and then be unable to get away. Example (very serious effects) - pesticide escaping from a processing plant into the factory’s storm water drains and thus into the external environment. In both such types of incident, forethought in the design stage and good operating practice and management can minimize both the potential (i.e., the hazard) and the risks. It is also extremely important to know the interaction and chemical reactions amongst various chemicals being disposed – on its own it may be harmless but when reacting with other chemicals it can become a deadly poison. Introduction to Oil and Gas Operational Safety 51 SECTION 2: HSE Management (Learning From Incidents/Accidents) LEARNING OUTCOME Explain the hazards inherent in oil and gas arising from the extraction, storage and processing of raw materials and products REVISION EXERCISE Write your answers to the questions below on a separate sheet of paper without referring to the information in this book in the first instance. Once you have answered all of the questions, you can refer back to the version guide to compare your answers and this will give you an indication of how much knowledge you have been able to absorb or whether you need to revise this section further. Q1 Outline the features of the following: (a) flash point (b) vapour density (c) vapour pressure Q2 Explain the difference between ‘flammable’, ‘highly flammable’, and ‘extremely flammable’. Q3 Explain what the ‘lower flammable limit’ and ‘upper flammable limit’ of a product is. Q4 Toxicity can be ‘acute’ or ‘chronic’. Explain the difference between the two terms. Q5 Some substances are described as ‘skin irritants’. Explain what a ‘skin irritant’ is. Q6 Explain what is meant when a substance is said to have ‘carcinogenic properties’. Q7 Outline hazards associated with: (a) hydrogen gas (b) hydrogen sulphide (c) methane (d) Liquefied Petroleum Gas (LPG) (e) Liquefied Natural Gas (LNG) (f) nitrogen (g) oxygen (h) micro – biocides (i) refrigerants (j) steam (k) mercaptans Q8 Outline hazards and control measures associated with: (a) drilling muds (b) low specific activity sludges 52 INTRODUCTION TO OIL AND GAS OPERATIONAL SAFETY SECTION 2: HSE Management (Learning From Incidents/Accidents) IV. RISK ASSESSMENT Risk Assessment and Its Purpose Within the oil and gas industry there are inherent risks of accidents occurring at any stage of the process – from exploration through to the extraction, refining and final delivery of the product. These risks include fire, explosion, environmental contamination and injury to personnel. The oil and gas industry has a responsibility to identify those risks and put in place control measures to reduce them to a level that is as low as is reasonably practicable (ALARP). To put in place risk control measures it is important to identify those risks, the first step of which is to perform a risk assessment. There are a number of techniques available when assessing risks, including: A. The 5-step approach B. Qualitative assessment techniques C. Semi-quantitative assessment techniques D. Quantitative assessment techniques Introduction to Oil and Gas Operational Safety 53 SECTION 2: HSE Management (Learning From Incidents/Accidents) A. 5-Step Approach The 5-step approach to risk assessment include: Step 1: Identify the hazards. Step 2: Decide who might be harmed and how. Step 3: Evaluate the risks and decide on precautions. Step 4: Record the findings and implement them. Step 5: Review the assessment on a regular basis and update if necessary. Step 1: Identify the Hazards The first step is to work out how people could be harmed. In order to help identify the hazards the following procedure should be followed: Conduct a tour of the workplace and observe what could reasonably be expected to cause harm. Consult the workers or their representatives for their views and opinions. Consult the manufacturers’ instructions or data sheets. These will highlight hazards associated with machinery or substances. Consult the accident log and ill-health records. These can often indicate less obvious hazards as well as highlighting trends. 54 INTRODUCTION TO OIL AND GAS OPERATIONAL SAFETY SECTION 2: HSE Management (Learning From Incidents/Accidents) Step 2: Decide who might be harmed and how For each hazard, there has to be clear identification of the groups of people who might be harmed – this will help identify the best way of managing the risk (e.g. ‘people working in the boiler room’ or ‘passers-by’). In each case, identify how they might be harmed, i.e. what type of injury or ill health might occur. For example, workers lifting heavy equipment may be susceptible to back injuries. Step 3: Evaluate the risks and decide on precautions Having identified the hazards, the next step is to decide what action to take to reduce the risks associated with the hazards. In most countries the law requires employers to do everything ‘reasonably practicable’ (ALARP) to protect people from harm. When setting controls to minimize the risks to As Low As Reasonably Practicable (ALARP), the Hierarchy of Control should be used. When using the Hierarchy of Control, priority should be given to those control measures at the top of the list. - Elimination - Substitution - Engineering controls - Administrative controls - Personal Protective Equipment (PPE) Step 4: Record the findings and implement them The first step of implementation is to write down the results of the risk assessment and share the document with those staff members involved. A risk assessment is not expected to eliminate all risks, but it is expected to be suitable and sufficient. If the findings of the risk assessment conclude that there are a number of improvements to be made, it is appropriate to draw up a prioritized plan of action. In order for it to meet these criteria, the Risk Assessment will need to be able to show that: A proper check was made. Introduction to Oil and Gas Operational Safety 55 SECTION 2: HSE Management (Learning From Incidents/Accidents) All of those who might be affected were consulted. All the significant hazards were addressed. The recommended risk control measures are suitable and sufficient, and the remaining risk is low. All the staff or their representatives were involved in the process. Step 5: Review the risk assessment and update if necessary Few workplaces remain static. Inevitably, new equipment or variations in substances used and procedures undertaken will introduce new hazards to the workplace. Consequently, it’s sensible to review all control measures on an ongoing basis. B. Qualitative Risk Assessment A qualitative risk assessment is based on the conclusions reached by the assessor using his/her expert knowledge and experience to judge whether current risk control measures are effective and adequate, in order to ensure they reduce the risk to a level which is as low as is reasonably practicable, or if more measures need to be applied. It’s a way of identifying hazards emanating from specific activities, which might affect people or the environment. The assessor can develop an understanding of the risks involved and how serious they may be if realized, thus allowing him/her to prioritize the control measures in the order that they should be implemented. The use of a scale matrix may be helpful in this process. There are advantages in using the combined skills of a team of assessors. Getting a fuller, more rounded picture of the risks involved would result from having a pool of ideas and judgments rather than those of a single assessor. When making a qualitative judgment on the severity of a risk, two parameters are taken into consideration: These are the likelihood of an event occurring and the consequences or severity if the event does occur. 56 INTRODUCTION TO OIL AND GAS OPERATIONAL SAFETY SECTION 2: HSE Management (Learning From Incidents/Accidents) Severity can be assessed in terms of its effect on - Harm caused - Quality - Time - Inconvenience - Cost C. Semi-quantitative Risk Assessment Effective risk management uses well-founded decisions based on as broad a knowledge base as possible, i.e. the knowledge and experience of the assessor(s). It also requires a degree of consistency in making judgments. Under qualitative assessment techniques, both the likelihood and the severity of any event are subjective (i.e. a personal opinion). However, using a semi-quantitative approach involves putting a value on the likelihood and severity of an event. To do this effectively, a numerical value is applied to the degree of severity as well as the likelihood of a particular event occurring. When judging the risk of a particular activity, the risk assessor or risk assessment team agree the likelihood rating, e.g. 3, agree the consequence (severity) rating, e.g. 4, then multiply the likelihood (3) by the consequence (4) to get a rating of 3 × 4 = 12 (tolerable). This can be seen in the following matrix. The numerical value can then be used to prioritize the actions required, as shown in the grading on the right of the matrix. Introduction to Oil and Gas Operational Safety 57 SECTION 2: HSE Management (Learning From Incidents/Accidents) D. Quantitative Risk Assessment Quantitative risk assessment techniques provide the means to make a detailed assessment that will be based on quantitative considerations of event probabilities and consequences. The quantitative risk assessments involve using special quantitative tools and techniques in order to identify hazards, to give an estimate of the severity of the consequences and the likelihood of the hazards being realized. Historical data analysis is the basis for many quantitative risk assessments. Frequencies are simply calculated by combining accident experience and population exposure, typically measured in terms of installation-years: One example of a source of historical data which can be used as the basis for quantitative risk assessments is the Worldwide Offshore Accident Databank (WOAD). When a project is in the design stage, some risks and hazards can be ‘designed out’. 58 INTRODUCTION TO OIL AND GAS OPERATIONAL SAFETY SECTION 2: HSE Management (Learning From Incidents/Accidents) Unfortunately, the hydrocarbon inventory will always remain as a major hazard, as it’s the very reason the industry is there in the first place. Examples of modeling techniques are: 1. HAZID (Hazard Identification Study) 2. HAZOP (Hazard and Operability Study) 3. FMECA (Failure Modes and Effective Critical Analysis)/FMEA (Failure Modes and Effects Analysis) 1. HAZID (Hazard Identification Study) A Hazard Identification Study (HAZID) is a tool for identifying hazards. It is normally a qualitative risk assessment and is judgment based. It is usually undertaken by a team of people who will be selected because of their particular knowledge, experience or expertise The reasons for identifying hazards are two-fold: To compile a list of hazards, which can then be evaluated using further risk assessment techniques (failure case selection). To conduct a qualitative evaluation of how significant the hazards are and how to reduce the risks associated with them (hazard assessment). The following features are essential elements of a hazard identification study: The study should be creative and dynamic (lateral thinking). This will allow a wide scope of hazards to be considered. The study should take a structured approach so as to be comprehensive in its coverage of relevant hazards. The study should embrace historical data and previous experiences so that lessons learned can be acted upon. The scope of the study should be clearly defined. This is to ensure that those who read the study fully understand which hazards have been included and which have been excluded. Introduction to Oil and Gas Operational Safety 59 SECTION 2: HSE Management (Learning From Incidents/Accidents) Hazard checklists are an effective means of producing a comprehensive list of standard hazards, which can be used for hazard identification studies at the concept and design stages of a project to consider a wide range of issues related to safety. It