Pre-start Up Checks/Inspections PDF
Document Details
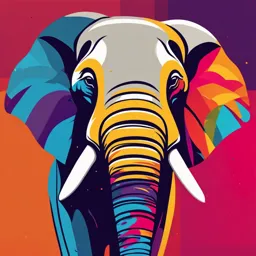
Uploaded by NeatLeibniz
Tags
Summary
This document details pre-start-up checks/inspections, covering their benefits for safety and finances in oil and gas industries. The importance of standard operating procedures (SOPs) in improving efficiency and safety is also highlighted. Key elements such as, visual inspections, equipment checks, and safety procedures are detailed with explanations of why they are important.
Full Transcript
1 Pre-start up checks/inspections Cont’d ✓Together, warning indicators and pre-start inspections provide a more complete picture of the safety and usability of an...
1 Pre-start up checks/inspections Cont’d ✓Together, warning indicators and pre-start inspections provide a more complete picture of the safety and usability of an item of equipment. ✓Therefore Pre-start up checks are helpful in this aspect. Pre- start up checks are most common in heavy industries like construction, oil and gas, mining and manufacturing. 2 Pre-start up checks/inspections Cont’d ✓A pre-start inspection is a quick review to ensure that a task or item of equipment is safe to use. The operator uses a checklist to perform a standardized routine inspection prior to using the equipment. ✓The idea behind a pre-start up check is that the best way to avoid issues is to be proactive, to take the time to inspect equipment or situations prior to them beginning. ✓A few basic checks on known risks and problematic areas can drastically reduce risk and potential consequence. 3 Pre-start up checks/inspections Cont’d ✓A pre-start checklist normally covers the exterior and interior condition of the equipment as well as operational aspects including mechanical and electrical systems, fluid levels and safety devices such as alarms, fire extinguishers and emergency eye wash. ✓The intent of a pre-start checklist inspection is to identify defects and safety hazards prior to operation. 4 Major elements of Pre-start up checks/inspections In order to ensure that the task or equipment is used safely, certain things should be included in a pre-start check/inspection, such as: ✓ Reviewing Standard Operating Procedures (SOPs) or other instructions ✓ Ensuring that workers understand the task to be performed (Tool box talks) ✓ Inspecting equipment for mechanical faults or damage. 5 Stages of pre-start up checks/inspections Undertaking a pre-start check on your equipment before you start a days work, happens in three stages. Step 1 - Visual inspections of important features prior to starting the machine. E.g. 1. All blinds removed 2. All instruments reconnected 3. All control valves stroked 4. All modified process lines and equipment are as per approved piping and instrument diagrams (P&IDs) 6 Step 1 - Visual inspections of important features prior to starting the machine, examples cont’d 5. All drawings marked up to reflect the “as-built” status 6. Operator training for modifications in progress 7. Maintenance training for modifications in progress 8. Start-up spares available 9. Physical check inside all vessels before boxing up 10. Correct thermal insulation reinstated where required 7 Stages of pre-start up checks/inspections Cont’d Step 2 - Visual & function tests while the machine is turned on but stationary. E.g. 1. All pressure testing complete and documented 2. All relief valves reinstalled with documented testing completed 3. Supply line including shut off valves of fuel (Gas and oil) is functioning well Step 3 - Testing the machine’s functioning during a short drive 8 Safety benefits of pre-start up checks/inspections 1. Identification of faults and defects before equipment use 2. Decreased likelihood or severity of injury from catastrophic equipment failures 3. Well-maintained equipment in safe-operating condition 4. A workplace culture of safety 9 Financial benefits of pre-start up checks/inspections 1. Reduced WHS (Work health and safety) operating costs—minimising risks and hazards decreases workplace injury associated costs 2. Decreased repair costs—minor repairs are made so major repairs are avoided 3. Reduced unplanned downtimes—equipment keep working 4. Fewer costly on-site and off-site repairs for equipment that break down during operation 5. More on time deliveries for the logistics sector 10 Standard operating procedures (SOPs) ❑A Standard operating procedure (SOP) is a written document composed of step-by-step instructions used to safely execute a routine operational task in a consistent manner. ✓Organizations of all types use SOPs to achieve efficiency, uniform performance, quality control, and regulatory compliance. ✓Standard Operating Procedures (SOPs) are important for the safe and effective operation of industrial plants and oil & gas facilities. ✓SOPs may be used for little other than operator training. 11 Importance of SOPs 1. Good operating procedures tell workers how to perform tasks the best way. 2. They eliminate unnecessary steps, movements, and equipment, allowing tasks to be completed with confidence. 3. Without effective procedures, workers may spend time and effort performing pointless steps and questioning if the published document in front of them should be trusted. 4. SOPs ensure that compliance standards are met. 12 Importance of SOPs Cont’d 4. They help to train new employees more efficiently. 5. SOPs prevent manufacturing failures. 6. Meet production requirements. 7. Guarantee employee safety. 8. Enforce best practices. 9. Adhere to a schedule. 13 Categories of SOPs ❑Technical SOPs – These detail how to perform and complete tasks. ✓ They are often in the form of a repeating work order, a preventative maintenance work order, or an inspection. ❑Management SOPs – These detail how all other SOPs are created, updated, distributed, and overseen. ✓ This may sound silly, but companies often need SOPs to manage their SOPs. ✓ Essentially, management SOPs outline the processes and procedures to define, document, and implement standard operating procedures. 14 Elements of SOPs ❑Regardless of type, standard operating procedures generally include the same information. An SOP must include: 1. Title page – typically consists of the title, procedure number, relevant department, publication date, and signatures. 2. Table of Contents – should give the reader the names of all the document’s sections, sub-sections, and associated page numbers. 15 Elements of SOPs Cont’d 3. Procedure (s) – consists of multiple sub-sections, which in total, should give all the necessary information about the described procedure(s) a) Scope – defines who the procedure is for (e.g. department, team), its purpose, limits, inputs/outputs, etc. b) Terminology – explains language, including acronyms and phrases the reader may not know 16 Elements of SOPs Cont’d c) Procedure Description – describes the procedure and each of its steps in detail and order from start to finish. d) Supplementary Information – gives additional details needed to complete each step (necessary decisions, possible obstacles, “what if” scenarios, troubleshooting tips, etc.) e) Health & Safety Warnings – warns employees about potential hazards, should be attached to individual steps, as well as compiled in a separate sub-section. 17 Elements of SOPs Cont’d f) Needed Equipment & Supplies – lists everything the reader will need to successfully complete the procedure 4. Metrics – defines metrics to track with this procedure to monitor and evaluate process efficiency over time (production volume, machinery downtime, etc.) 18 Steady state conditions ❑In systems theory, a system or a process is in a steady state if the variables (called state variables) which define the behavior of the system or the process are unchanging in time in spite of ongoing processes that strive to change them. ✓In continuous time, this means that for those properties p of the system, the partial derivative with respect to time is zero and remains so: 19 Steady state conditions Cont’d Consider a system in which a beaker half-filled with water and the thermostat of the hot plate is set at 50°C. If we observe the change in the temperature of water present in a beaker, the temperature of the water reaches 47°C and stops increasing. The reason is that the beaker is an open system. ✓ The heat travels from the hot plate to the beaker and from the beaker to the surrounding. ✓ Therefore, overall heat change in the two systems becomes equal. ✓ This condition is called the steady-state condition in thermodynamics.