Plant Operations vs Control Room Operations PDF
Document Details
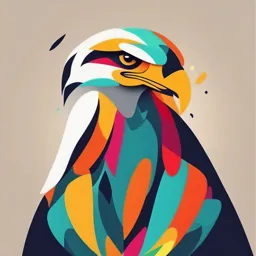
Uploaded by InvulnerableSanDiego
Tags
Related
- Unit A-5 Introduction to Plant Operations and the Environment PDF
- VOC System Control Philosophy Process Description PDF
- Los Angeles City Fire Department Earthquake Emergency Operational Plan PDF
- Nuclear Power Plant Operation Lecture PDF
- NOP-OP-1002 Conduct of Operations R21 PDF
- Duties of the Control Technician - Training Material PDF
Summary
This document covers plant operations versus control room operations in an oil and gas training setting. It explains the roles of control room operators and process variables. It also details different types of instruments used in process control.
Full Transcript
1 Plant operations vs Control room operations Cont’d ❑A plant is a place where industrial processes take place. ❑A control room is a room from which a system, network , or piece of equipment is controlled. ...
1 Plant operations vs Control room operations Cont’d ❑A plant is a place where industrial processes take place. ❑A control room is a room from which a system, network , or piece of equipment is controlled. 2 Control room operations The necessary control and monitoring of processing operations is managed from the control room, which is a dedicated structure where operators perform plant operations monitor and control using sophisticated and automatic control systems in a safe and efficient manner. ✓ They are spaces where vital information is collected for the efficient operation of the plant and from where operators are able to manage the most important equipment in the plant. 3 Control room operations Cont’d ✓ All the important systems and apparatus send signals to the control room, allowing the operator to efficiently carry out their work. ✓ This allows machinery located around the plant to be managed and, if necessary, operated, from one place. 4 Typical roles of control room operators 1. Monitor Plant Operations From the control room, Control Room Operators monitor all plant operations on screens and computers. They watch closely to identify any abnormal operating and equipment conditions. 2. Fix Problems When something abnormal is detected, the Control Room Operators troubleshoots and repairs the electrical and mechanical equipment to get everything back on track to minimize safety risks and economic losses. 5 Typical roles of control room operators Cont’d 3. Track and Log Operational Systems The Control Room Operators is responsible for tracking and recording the status of the operational system using applicable journals and control system tools. 4. Make Recommendations From their vantage point, Control Room Operators are in a great position to identify and recommend changes to improve overall plant reliability, performance and output. 6 Typical roles of control room operators Cont’d 5. Monitor Emissions An important duty of the Control Room Operator is to monitor the operations of emissions control equipment and adjust it to meet State and Federal permits. 7 Process variables, measurements and alarms A process variable is a physical or chemical quantity that is usually measured and controlled in an operation such as oil processing plant. ✓Common process variables are flow, level, pressure, temperature, turbidity, chlorine, and oxygen levels. ✓Instruments are used to monitor and control a process to keep the process variables within a correct limit. 8 Measurements An analog instrument is the one which shows the results of measurement either in the form of a wave or by the deflection of a pointer on an analog scale. A digital instrument is the type of measuring instrument which represents the output in the form of digits on a screen (LCD or LED). Inferred measurement is an approach to get data on something you can't measure directly by taking what you can measure and inferring what you want to know from that. 9 Measurement and control ✓Sensors are the first element in a process control loop. They actually measure the value of the process variable. ✓Indicators (I) are human readable devices that display information about a process. ✓Transmitters (T) convert a reading from a sensor into a standard signal and transmits it to a controller. ✓Controllers (c) are devices that receive data from the measurement instrument, compares data with programmed set point and signals control element to take corrective action. 10 Measurement and control Cont’d ✓Recorders (R) are devices that records the output of a measurement device. ✓Alarms (A) are devices responsible for alerting plant operators about an upset condition of the process variable. Alarms typically consist of sound and light outputs that attract attention of the plant operator. 11 Measurement and control Cont’d Water in the vessel is heated by the The process variable is level. You heat exchanger. Measuring the can change the level by closing or temperature the steam flow to the opening the control valve. If you exchanger is controlled. Temperature close the valve, the level increases. changes when the amount of steam If you open the valve, the level is changed. The process variable is decreases. called Temperature. 12 Process Switches and Alarms ◦ Another type of instrument commonly seen in measurement and control systems is the process switches. ◦ Usually, switches are used to activate alarms to alert human operators to take special action or can be used to trip or initiate interlocks. 13 Process Switches and Alarms Cont’d The “PSH” (pressure switch, high) activates when the air pressure inside the vessel reaches its high control point. The “PSL” (pressure switch, low) activates when the air pressure inside the vessel drops down to its low control point. Both switches feed discrete (on/off) electrical signals to a logic control device (symbolized by the diamond) which then controls the starting and stopping of the electric motor-driven air compressor. Another switch in this system labeled “PSHH” (pressure switch, high-high) activates only if the air pressure inside the vessel exceeds a level beyond the high shut-off point of the high pressure control switch (PSH). 14 Effective communication ❑ Communication is simply the act of transferring information from one place, person or group to another. Every communication involves (at least) one sender, a message and a recipient. Good communication is an essential tool in achieving productivity and maintaining strong working relationships at all levels of an organization. 15 Reasons for effective communication 1. Team building – Building effective teams is really all about how those team members communicate and collaborate together. By implementing effective strategies, such as those listed below, to boost communication you will go a long way toward building effective teams. This, in turn, will improve morale and employee satisfaction. 2. Gives everyone a voice – As mentioned above, employee satisfaction can rely a lot on their having a voice and being listened to, whether it be in regards to an idea they have had or about a complaint they need to make. Well established lines of communication should afford everyone, no matter their level, the ability to freely communicate with their peers, colleagues and superiors. 3. Innovation – Where employees are enabled to openly communicate ideas without fear of ridicule or retribution they are far more likely to bring their idea to the table. Innovation relies heavily on this and an organization which encourages communication is far more likely to be an innovative one. 16 Reasons for effective communication 4. Growth – Communication can be viewed both internally and externally. By being joined up internally and having strong lines of communication you are ensuring that the message you are delivering externally is consistent. Any growth project relies on strong communication and on all stakeholders, whether internal or external, being on the same wavelength. 5. Strong management – When managers are strong communicators, they are better able to manage their teams. The delegation of tasks, conflict management, motivation and relationship building (all key responsibilities of any manager) are all much easier when you are a strong communicator. Strong communication is not just the ability to speak to people but to empower them to speak to each other – facilitating strong communication channels is key. 17 Good communication involves… 1. Define goals and expectations – Managers need to deliver clear, achievable goals to both teams and individuals, outlining exactly what is required on any given project, and ensuring that all staff are aware of the objectives of the project, the department and the organisation as a whole. 2. Clearly deliver your message – Ensure your message is clear and accessible to your intended audience. To do this it is essential that you speak plainly and politely – getting your message across clearly without causing confusion or offence. 3. Choose your medium carefully – Once you’ve created your message you need to ensure it’s delivered in the best possible format. While face-to-face communication is by far the best way to build trust with employees, it is not always an option. Take time to decide whether information delivered in a printed copy would work better than an email or if a general memo will suffice. 18 Good communication involves… Cont’d 4. Keep everyone involved – Ensure that lines of communication are kept open at all times. Actively seek and encourage progress reports and project updates. This is particularly important when dealing with remote staff. 5. Listen and show empathy – Communication is a two-way process and no company or individual will survive long if it doesn’t listen and encourage dialogue with the other party. Listening shows respect and allows you to learn about any outstanding issues you may need to address as an employer. 19 Communication procedures A communication procedure describes the specific requirements and methods for the internal and external communication of quality-related issues, and the establishment of lines of communication with various parties that affect quality. ✓ Based on ISO 9001:2015, Clause 7.4 any communication procedure includes the following: 1. What is to be communicated. ❖ Quality-related issues including the quality policy, quality objectives, quality management system requirements, processes, customer requirements, organizational performance, customer satisfaction, purchase orders, specifications, drawings, requests for quotation, changes etc. 20 Communication procedures 2. When to communicate. ❖ Based upon the frequency, urgency/importance, significance, scheduled meetings, ad-hoc briefings, staff shift patterns. 3. Who to communicate with regarding relevant interested parties. ❖ External interested parties such as customers, suppliers, regulators, stakeholders, government agencies, local community, investors, external providers, media. ❖ Internal interested parties such as employees, employee representatives, contractors, unions. 21 Communication procedures 4. How communication occurs, what communication channels are used. ❖ Via scheduled, formal meetings, in formal briefings, notices, e-mails, telephone, text, intranet, internet, directives, management review, visual management, media campaigns, social media, quality alerts, bulletins, webinars, press releases, newsletters. 5. Who undertakes the communication ❖ Line Managers, Supervisors, team leaders, team members, employee representatives, public relations, marketing, external agencies. 22 Effective communication in a plant Effective communication in a plant can be performed via plant logs, use of radio, hand signals, etc ✓ Plant log records contain details about shift changeovers, equipment changes, production losses, and near misses that might occur during a shift etc. ✓ Hand signals can provide a standard method to communicate visually with equipment operators to keep other workers on the ground safe. 23 Effective communication in a plant ✓ Two-way radio communications will help to operate a safe manufacturing environment, with clarity and an enhanced focus on worker safety. 24 Safe working practices Safe work practices are ways of controlling hazards and doing jobs with a minimum of risk to people and property. ✓ Safe work practices are generalized statements of what you should or should not do in order to do a job or task safety. E.g. Electrical safety SWP, Hand tools SWP, SOPs 25 Safety in a workplace 1. Always Report Unsafe Conditions 2. Keep a clean workstation 3. Wear protective equipment 4. Take breaks 5. Don’t skip steps 6. Stay up to date with new procedures or protocols 7. Maintain proper posture 8. Offer guidance to new employees 24 June 2019 / ‹#› 1. To operate a given equipment, the following steps are followed; A. Toolbox talk B. Pre-start up check C. Start up D. Achieving steady state E. ………………………. F. Pre-shut down check G. Shut down H. ………………………. 2. Mention the five typical roles of a control room operator.