IMS_11 Broaching (PDF)
Document Details
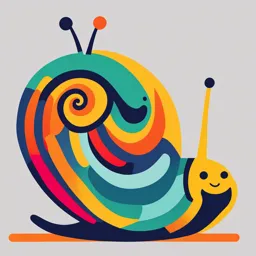
Uploaded by RetractablePansy5601
Technical University of Sofia
Tags
Related
- Maryland Medical Protocols for Emergency Medical Services PDF
- PDF The effectiveness of different mandibular advancement amounts in OSA patients: a systematic review and meta-regression analysis
- Huberman Lab Podcast: Breathing Science with Dr. Feldman PDF
- Yoga: Ancient Practices for Modern Wellbeing PDF
- Health Promoting Behavior PDF
- Breath: The New Science of a Lost Art (PDF) by James Nestor
Summary
This document is a chapter on broaching, a metal cutting technique. It discusses internal and external broaching methods, applications, and achievable accuracies. It also covers the influence of broaching on surface quality.
Full Transcript
CHAPTER 11 BROACHING 11.1 Definition Broaching is a metal cutting technique with a multi-edged tool in which the tool performs the cutting motion. This method functions without any feed motion due to the offset of the cutting teeth on the broac...
CHAPTER 11 BROACHING 11.1 Definition Broaching is a metal cutting technique with a multi-edged tool in which the tool performs the cutting motion. This method functions without any feed motion due to the offset of the cutting teeth on the broaching tool. The material is removed in one stroke (pulling or pushing) with the broaching tool, called the broach. 11.2 Broaching methods In broaching, two working procedures – internal- and external broaching - are distinguished 11.2.1 Internal broaching During internal broaching, the broaching tool is brought into the premachined opening of the workpiece. Working motion then begins, whereby the broach, equipped with many cutting blades, is pulled or pushed through. The broach contour (square, hexagon, etc.) is generated in the workpiece opening. Figure 11.1 elucidates the configuration of workpiece and tool during broaching. Figure 11.1 Broaching principle. 11.2.2 External broaching During external broaching, the broaching tool finishes a premachined outer workpiece contour, such as the opening of a forged open-end wrench. 11.3 Application of the broaching techniques 11.3.1 Internal broaching Internal broaching is applied to generate openings of different shapes. Thus, for example, serrations, taper bushings for splines, and spline profiles for movable gears are created with this method. Some typical examples are seen in Figure 11.2. As a rule, broaching is used if high accuracy to shape and size is demanded in addition to high surface quality. For this reason, broaching is sometimes used instead of reaming to generate holes. Broaching is an economical procedure since it is possible to produce very sophisticated geometries that require no further reworking very quickly and with a single stroke. The generation of a spline profile in internal broaching is illustrated in Figure 11.3. Chapter 11 1 Figure 11.2. Broaching profiles for internal broaching. Figure 11.3. Generation of an internal spline during internal broaching a - before; b and c – during; d – at the end of the broaching procedure. Figure 11.4. Broaching profiles to be produced by external broaching. Chapter 11 2 11.3.2 External broaching External broaching is the method used for the generation of external profiles. However, this method is also used for the manufacturing of shaped grooves, such as Christmas tree-shaped grooves (Figure 11.4c), in which the turbine blades are mounted in turbine wheels. External broaching is also applied for machining of external teeth (Figure 11.4b) and guiding surfaces (Figure 11.4d), as well as guide grooves and similar items. Figure 11.4 shows some typical workpieces for external broaching. 11.4 Achievable accuracy values 11.4.1 Accuracy to size The accuracy values that can definitely be achieved with internal- and external broaching range from IT 7 to IT 8. However, with more effort, it is also possible to achieve IT 6. 11.4.2 Surface quality The final finishing tooth that cuts in the offset at a depth of h = 0,01 mm has a substantial effect on surface quality. Furthermore, reserve teeth are included in internal broaching. These teeth improve the surface by regrooving and shaving. During the generation of profiled surfaces with all the teeth of a broaching tool or of straight surfaces by broaching tools with lateral offset, the surface is influenced by the minor cutting edges of these tools. The surface roughness values Rt that can be achieved during broaching of mild steels range from Rt = 6,3 to 25 µm High surface qualities can also be achieved in the case of easily broached free cutting steels and materials for casting. Acceptable broaching results may also be expected from case hardening- and tempering steels, if a homogeneous ferrite-, perlite distribution is available for normally annealed material. 11.5 Broaching tools Figure 11.5. Broach components l1 shank, a1 pilot, a2 cutting portion, a3 pilot, l2 rear support, L total length detail X see Figure 11.6. Chapter 11 3 11.5.1 Broach – blade geometry On broaches, rake angle and tool orthogonal clearance (Figure 11.6) have the same effect as on the turning tool. Rake face chamfers reinforce the wedge and only slightly diminish the positive properties of greater rake angles. Due to complicated grinding, broaches are generally made without any rake face chamfers. Flank wear lands with a land angle of the flank from 0° to 0,5º and a land width of 0,5 mm have only finishing- and calibrating teeth. Only small land angles of the flank with small land width are selected in order to maintain accuracy to size of the broach even in the case of repeated re- sharpening. Figure 11.6. Cutting edge geometry of a broach according to Figure 11.5, at the bottom right, cutting edges of a broach with inclined blades. Figure 11.7. Formation of the tooth space. 11.5.2. Broaches - design types A variety of broach forms is given in Figure 11.8. For difficult profile types, the external broach is composed of several cutting portions. Chapter 11 4 Figure 11.8. Broach types for internal- and external broaching. Chapter 11 5