Mobile Cranes (MOB) Diploma Workbook V1 2023 PDF
Document Details
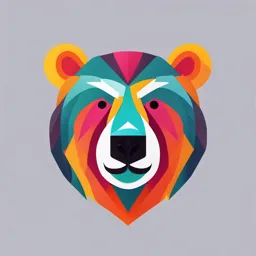
Uploaded by PromisingJadeite8923
null
2023
LEEA
Tags
Related
- Mobile Cranes (MOB) Diploma (Global) Workbook 2023 PDF
- Mobile Cranes Diploma (Global) Workbook 2023 PDF
- Mobile Cranes (MOB) Diploma (Global) Workbook 2023 PDF
- Mobile Cranes Diploma (Global) Workbook 2023 PDF
- Mobile Cranes (MOB) Diploma (Global) Workbook 2023 PDF
- Mobile Cranes Diploma (Global) Workbook - PDF
Summary
This workbook provides information about the Mobile Cranes (MOB) Diploma, a qualification for those involved in the testing, inspection, and examination of mobile cranes. It outlines learning outcomes, course scope, on-site procedures, requirements for testing, and essential equipment.
Full Transcript
Mobile Cranes (MOB) Diploma (Global) Workbook Lifting Equipment Engineers Association Lifting Standards Worldwide 1...
Mobile Cranes (MOB) Diploma (Global) Workbook Lifting Equipment Engineers Association Lifting Standards Worldwide 1 Page © LEEA MOB (GLOBAL) v1 2023 AW Welcome to the Mobile Cranes Diploma (MOB) 1. Introduction The LEEA Mobile Cranes Diploma qualification is essential for anyone engaged in the testing, inspection and examination of Mobile Cranes, and responsible for assessing their suitability to return to service following statutory examination. LEEA Diplomas are globally recognised as the industry-standard qualification for lifting equipment testers, inspectors, examiners, repairers and maintainers. 2. Learning outcomes Upon successful completion of this Diploma course, students will acquire the knowledge that will assist them to perform the 'thorough examination' of Mobile Cranes in service and validate or otherwise assess their fitness for a further period of service, applying conditions as may be necessary. Students will be able to refer to and extrapolate information from sources to support their analysis of lifting equipment suitability for continued service. 3. Scope of the MOB course a. Working On-site b. The Examiners’ Tools and Equipment c. Types of Mobile Crane d. Types of Examination e. Assessment Criteria f. Preparation for Thorough Examination g. Competency h. Rated Capacity Indicators and Rated Capacity Limiters (RCIs and RCLs) i. Load Testing of Mobile Cranes j. Thorough Examination – Mobile Crane Carrier/Chassis k. Thorough Examination - Mobile Telescoping Crane Structure l. Chain and Wire Rope Examination m. Rated Capacity Charts n. Load Indicators Notes: 2 Page © LEEA MOB (GLOBAL) v1 2023 AW 3a. Working on Site As a professional in the lifting equipment industry, there are high expectations of you to perform your role to mitigate risk and keep people safe. This is of paramount importance and should always be the priority focus of your work. Secondly, our stakeholders, customers and employers rightly expect the highest professional standards from all those working in such a high-risk industry. So, you are expected to be competent in your technical abilities, but moreover, as a professional you must also manage your standards of service, both internally to your employer, and externally to your customers and other stakeholders. Let us now look at LEEA’s vison statement: On successful completion of this training course and the associated end-point assessment, you will be awarded the LEEA Diploma in Mobile Cranes (Global), and where applicable, the LEEA TEAM Card. As a TEAM Card holder, there is an expectation that you will perform your role to the very best of your ability, meeting the requirements of a ‘competent person’ as defined by LEEA in its COPSULE. Our industry ‘end-users’ are actively encouraged to use LEEA member companies that employ qualified and competent individuals. They are assured that by using LEEA TEAM Card holders, they are putting their lifting equipment into safe hands and minimising their risks as duty holders and owners of such equipment. NOTES: 3 Page © LEEA MOB (GLOBAL) v1 2023 AW In order that we continue “raising standards in the lifting equipment industry”, each of us has our own part to play. As a lifting equipment examiner/inspector/tester, employed by a LEEA member company, you share this responsibility and have a particularly important role! During this section of the course, we will look at how we approach our work on a day-to-day basis. Our considerations must include: a. Pre-Job Information b. Representing your employer: your role as an ambassador c. Reporting and signing-in d. During the job e. Completing the job Notes: 4 Page © LEEA MOB (GLOBAL) v1 2023 AW So, before we consider travelling to the customer’s site, we should pause and think about the following: a) Pre-Job Information: 1. What task(s) am I expected to do at the site today? 2. Who am I to report to when I get there? 3. Do I have all the necessary paperwork and work instructions from my employer? 4. What equipment will I need to complete the task(s)? 5. How long is the task(s) expected to take 6. Any requirements for access machinery or scaffolding? 7. How to access the site, particularly access for test weights and adequacy of floors and passages? b) Representing your employer: 1. Are my vehicle and uniform/overalls clean? 2. Do I have appropriate footwear? 3. Is my PPE suitable for the task(s) expected of me? Do I have alternatives in case I have to change my method of work? 4. Has the risk assessment or JSA (job safety analysis) been completed, or do I have to conduct this alone when I arrive at the site? Will I simply have to review the existing RA/JSA? 5. Is there a method statement for the work? Has this been discussed and agreed? 6. Make sure you notify the customer of your arrival time on site c) Reporting and signing in: 1. Report to main reception and sign in officially 2. Meet with your designated contact 3. Information is to be exchanged about the work to be done and safety precautions to be adopted, both from the examiners and site personnel point of view 4. Agree a meeting time for when you have finished your work for a debrief 5. Discuss communication arrangements so that your whereabouts is known, and you can be contacted at all times to ensure you are safe and well whilst working on site d) During the job: NOTES: 5 Page © LEEA MOB (GLOBAL) v1 2023 AW Firstly, you must consider the basic requirements for the examination to be effective: 1. The area should be clean and clear of contaminants which may harm the examiner or the equipment 2. Adequate access to the equipment shall be provided 3. The equipment should be reasonably clean, and the examiner should have the means to clean local areas 4. The examiner should have visual aids and tools required for the examination, including adequate natural or artificial lighting e) Completing the job: 1. Did you carry out post-examination running checks on equipment, where necessary? Operational checks? 2. Has equipment been stowed in designated storage areas or parked in a safe area? 3. Have all barriers and signs been removed from cordoned areas? 4. Let equipment users know that you have finished your work and that the equipment has been returned to service 5. Complete your reports, identifying any issues and your recommendations; safety critical issues are your priority, and the owner of the equipment must be notified of these immediately. If the equipment is to be removed from service, ensure it is suitably quarantined and marked, “DO NOT USE” 6. Identify and detail any repairs that may need carrying out and a timescale in which this should be completed 6 7. Have your debrief meeting with the site contact to present your report summary Page 8. Ensure your customer is completely satisfied before you leave site © LEEA MOB (GLOBAL) v1 2023 AW IMPORTANT! LEEA Members represent the highest standards within our industry. You are an ambassador for your company and your profession; it is essential that your personal behaviours are exemplary, and your competencies are consistently maintained through our active participation in continuous professional development (CPD). Notes: 7 Page © LEEA MOB (GLOBAL) v1 2023 AW 3b. The examiners’ tools and equipment Tools The Mobile Crane examiner will require a selection of hand tools in the course of their work. The selection of tools will depend on the nature of the job. A broader perspective on tools required may include a spirit level, tyre pressure gauge, inclinometer and load cell. Notes: 8 Page © LEEA MOB (GLOBAL) v1 2023 AW Measuring Equipment Calibration of measuring equipment should be carried out in accordance with relevant standards, and this is verified by LEEA during compliance audits. Sheave gauges for measuring the wear in sheaves and pulleys: Vernier Gauge to measure rope and component wear to an accuracy of 0.1mm: An inclinometer can be used to measure and verify the boom angle. 9 Page © LEEA MOB (GLOBAL) v1 2023 AW A load cell can be used to verify the actual load being lifted by the crane under test conditions. Spirit levels are used to verify the crane level gauges. Notes: 10 Page © LEEA MOB (GLOBAL) v1 2023 AW Lighting It is very important that the Mobile Crane is situated in a well-lit area with either natural or artificial light so that defects can be identified. Torches or portable lighting stations may be required to help you. Notes: 11 Page © LEEA MOB (GLOBAL) v1 2023 AW Cleaning Materials The area where you are carrying out the inspection should be reasonably clean and free of contaminants that may affect the equipment you are inspecting. As an examiner you may not be able to see deterioration or damage that may be present due to excessive dust, oils and grease etc. It is therefore imperative to ascertain whether areas of the crane need cleaning prior to the examination taking place. It is recommended that you carry basic cleaning materials such as rags, a wire brush and PH neutral cleaning fluids in the event that you have to clean the components being inspected. Ensure any data sheets and chemical warnings are adhered to for the use of such products and your JSA/risk assessment reflects this. 12 Page © LEEA MOB (GLOBAL) v1 2023 AW 3c. Types of Mobile Cranes Rough Terrain Cranes This crane is ideal for rough terrain and is capable of ‘lift on rubber’ duties. When function testing lifting on rubber duties, it is advisable to have the outriggers extended and the jacks sufficiently clear of the ground to allow loading, as safety precautions in the event of the tyres failing. Lift on rubber means that the crane can lift and travel with a load. Crane manufacturer’s that allow “on rubber” lifts will provide a load rating chart specifically for this configuration. Notes: 13 Page © LEEA MOB (GLOBAL) v1 2023 AW Truck Mounted Cranes This type of crane may not have 360° duties or can have reduced duties in the front quadrant. However, if it is fitted with a 5th jack at the front end, the crane may be rated for 360° operation. Notes: 14 Page © LEEA MOB (GLOBAL) v1 2023 AW All-Terrain Cranes These cranes are designed to be used under different ground conditions. Some all-terrain cranes may be fitted with steering and travel functions in the upper cab, and therefore they can stow their jacks and outriggers from the upper cab. A steering wheel and brake pedal are also fitted to allow travel around the site to a new position. When examining this type of crane, it is essential that both sets of steering and braking systems are examined and work correctly. Notes: 15 Page © LEEA MOB (GLOBAL) v1 2023 AW City Cranes City cranes have a noticeably shorter boom with more sections than a normal mobile crane. This allows greater maneuverability whilst retaining overall boom length. It is all-wheel steering, and the boom is kept low to avoid overhead obstructions prevalent in urban areas. Notes: 16 Page © LEEA MOB (GLOBAL) v1 2023 AW Yard Cranes Yard cranes are designed for use in yards where it is not always convenient or possible to deploy outriggers, however they may have outriggers fitted and operate where a rough terrain crane is too large. The yard crane has free, on rubber capabilities and a strong platform on which light loads (e.g., pumps, motors, valves) can be transported. Notes: 17 Page © LEEA MOB (GLOBAL) v1 2023 AW Crawler Mounted Telescopic Cranes Telescoping cranes, mounted on tracks, are usually used for on-site work and can be examined in the same manner as wheeled cranes with the exception of the undercarriage. It is easier nowadays to inspect the tracks as the drive system is hydraulic rather than mechanical. Notes: 18 Page © LEEA MOB (GLOBAL) v1 2023 AW 3d. Types of Examination Note: whilst this Diploma is based upon LEEA’s COPSULE and global best practice, references are made to certain standards throughout; these standards, where specified, have been adopted in the formulation of LEEA guidance. The following is based upon BS7121-2-1 and BS7121-2-3. It is to be noted that ISO9927-1 and ISO9927-5 also provide similar criteria for the inspection of cranes. It is therefore important that the examiner uses the specific National or International standards used or adopted in their region of operation. We will look at 3 specific levels of inspection: 1. Pre-use inspection The pre-use inspection is normally carried out by the operator of the equipment prior to use. The operator will visually check for any signs of obvious defect, damage or failure that give cause for concern, and that it is safe to use. The functionality of the crane should also be included in any pre-use check, it is essential that this is carried out from a position of safety, and if any such issue is found, the operator must report their findings to the appropriate maintenance/inspection personnel for further investigation before operating the equipment. Pre-use checks of cranes should be carried out by people who have been deemed competent to do so. Competence should involve elements of training and assessment. (Ref: BS7121-2-1) 19 Page © LEEA MOB (GLOBAL) v1 2023 AW 2. Interim inspection The interim inspection (sometimes referred to as the ‘In-Service inspection) is determined by risk assessment as to how often, and to what extent the inspection is performed. This level of inspection normally focuses on critical components that may become problematic prior to the next periodic thorough examination. The number and frequency of these inspections is also determined by the risk assessment and the manufacturers literature. Interim Inspections are often done at the same time as planned maintenance or following a repair. 3. Thorough examination These examinations are performed at specified intervals; before putting the crane into service for the first time, following major refurbishment, repair or alteration and following an exceptional occurrence which may have affected the safety and integrity of the crane. The competent person will decide if any supplementary testing should be carried out as part of the thorough examination. For example, this could include non-destructive testing, overload testing and magnetic wire rope examination. a. Scope of thorough examination before the crane is put into use for the first time (Ref: BS7121-2-3. 8.3) The scope of this examination is decided by the competent person Risks, likelihood and consequences of failure(s) should be in included in the scope Account for the age of the crane and likely deterioration which may increase risk of failure Manufacturer’s records of inspections and tests should be considered b. Scope of thorough examination following installation (Ref: BS7121-2-3. 8.4) The scope of this examination is decided by the competent person The scope should confirm that the crane has been installed, checked, and tested in accordance with the manufacturer’s instructions The complexity of the crane installation will determine the scope of the examination and all previous thorough examinations should be considered c. Scope of periodic examination (Ref: BS7121-2-3. 8.5) (General) The competent person should carry out a thorough examination aligned to the specific scope of examination for the particular crane The defined scope of thorough examination will have been drawn up by a competent person in advance and will identify the parts of the crane that require examination Requirements of supplementary reports and tests should be included in the defined scope, to include: o Witnessing requirements for supplementary testing 20 o Details of any NDT requirements for the crane structure and mechanisms The person carrying out the thorough examination can add items to the defined Page scope but cannot remove any items © LEEA MOB (GLOBAL) v1 2023 AW Dedicated ancillary equipment must be included in the defined scope with particular attention paid to the wire rope(s) The defined scope should be checked periodically to ensure it is current and fit for purpose A copy of the defined scope of thorough examination should be kept in the machine history file As a minimum requirement, the defined scope should include: o An operational check in all motions observing movement and sounds that may indicate issues o Inspection of the components listed o Relevant criteria for component assessment o The path of the load through the cranes structure and mechanisms The defined scope should be risk-based, accounting for any probable failures of the crane A thorough examination should be carried out systematically, logically, and critically ensuring all components and structures are examined A common misconception regarding the thorough examination of mobile cranes is that their supporting chassis and tyres are not included in the scope of work. Mobile cranes rely on their chassis and tyres for safe functioning and therefore they are integral to the safety of the entire crane system. They should therefore be thoroughly examined. Components to be included The defined scope of examination should include the following components where applicable. This list is not exhaustive: Manufacturer’s information plate/label and duty charts Tyres and wheels Axle locking systems Crawler track Crane chassis Outrigger jacks and beams Chassis braking system All bolts, pins, and other fastenings (visual inspection) Slew section structure, including fasteners and slew ring Slewing mechanism (examination throughout its full range of movement with jib at maximum radius) All pipe work and connections (including rigid and flexible hoses) (visual inspection) Hydraulic cylinder fittings (visual inspection) Oil and fluids (visual inspection) Superstructure and jib (visual inspection) Fly jib and mounting attachment (visual inspection) All pivoting joints on the jib and attachments of the crane (visual inspection) Telescoping extensions on the crane (operation and visual inspection) Wire running and static ropes, including terminations Pulleys/sheaves and drums, including guards Cab, including controls, markings, indicators, seating, windows, heating Falling object protection structure (FOPS) bars, wipers, and load charts 21 Limiting and indicating devices including Page o Rated capacity system (measurement of load, movement, and radius) © LEEA MOB (GLOBAL) v1 2023 AW o Anemometer o Devices indicating Over hoist and over lower limits Luffing limits Trolley limits Slack rope limits Rail Travel Limits Hook blocks, including sheaves, hook, safety catch and swivel bearing Counterweights, including pendants, fasteners, lifting and locking mechanisms Hoist and luffing winches and brakes, including hydraulic systems Power and control cables and slip rings (visual inspection) Control cabinets and wiring Marking and labels/instruction notices 3e. Assessment Criteria The thorough examination focuses on defect in any part of the crane or its supporting structure that will affect its strength or functionality. When considering the components defined in the scope of examination, the criteria for assessment should include the following. This list is not exhaustive: Accuracy of limiting and indicating devices – within manufacturer’s tolerance Adjustment – as specified by manufacturer Alignment – within manufacturer’s tolerance Backlash – within manufacturer’s tolerance Bearing play – within manufacturer's tolerance Brake performance - within manufacturer's tolerance Corrosion – affecting strength or functionality Cracks – affecting strength or functionality Cylinder creep – within manufacturers tolerance Damage – affecting strength or functionality Distortion – affecting strength or functionality Fluid levels – within manufacturer’s tolerance Functionality – as intended by manufacturer Guards – presence and condition Leaks – affecting strength, functionality, and slips Lubrication – adequacy Markings – presence, accuracy, and condition Mode of operation – as intended by manufacturer Obstructions impeding safe access Rope fit, reeving – as specified by manufacturer Rope specification – as specified by manufacturer Rope condition Security – attachment of components and sub-structures, fasteners, welds Seizure – full or partial seizure of rotating components Tidiness – general housekeeping Wear – affecting strength or functionality *Rope condition (in accordance with ISO 4309) *Mobile cranes which operate in areas or conditions where the wire ropes and the 22 equipment they are used with are more liable to damage, e.g., corrosive or abrasive atmospheres will require the assessment of the condition of the rope and the Page © LEEA MOB (GLOBAL) v1 2023 AW equipment to be carefully carried out and the rope removed from service when the damage might affect its safe operation. When carrying out inspections and examinations to assess the fitness of the wire rope for further service, both general deterioration and localized deterioration or damage should be considered. The entire length of the rope is to be examined, with particular attention to the rope near to rope terminations, rope that has been running or stationary over drums, sheaves and deflection pulleys and any other areas likely to sustain damage. Notes: Second-hand (previously used) mobile cranes Note: Anyone purchasing a second-hand mobile crane should ensure that it is fit for service by having it thoroughly examined before it is placed into service. The purchaser will not be aware of any damage or defects that may exist, including poor quality repairs, and these may not be exposed until the mobile crane enters service. The thorough examination of second-hand mobile cranes is to include a full review of maintenance records and previous reports of thorough examination; the manufacturer should also be contacted so that details of any major repairs etc. can be obtained. The contents of any data logging system should be accessed and reviewed by a competent person. The duty to ensure that the thorough examination is completed rests with the user (owner). It is up to the user (owner) to decide who undertakes this work. This may be the mobile crane company tendering for the work or some other provider. Whoever is selected should be sufficiently independent and impartial to allow objective decisions to be made. This does not mean that competent persons must necessarily be employed from a company separate to that undertaking the modifications. If employers and others within their own organisations have the necessary competence, then they can use it. However, if they do, they must ensure that their ‘in-house’ examiners have the genuine authority and independence to ensure that examinations are properly carried out and that the necessary recommendations arising from them are made without fear or favour. The inspection and assessment might require the removal of access covers or removal and dismantling of major components to reveal parts that would not otherwise be seen. Following the inspection and assessment, repairs (where required) should be carried out and an inspection and maintenance regime should be written up. 23 Page © LEEA MOB (GLOBAL) v1 2023 AW Amending the Intervals of Periodic Thorough Examination The recommended, and in some regions, statutory maximum interval between thorough examinations (6 and 12 months), can be reduced if environmental factors, or the crane’s age or condition warrant more frequent examinations. This decision is taken by the crane users, owner and the competent person. Changing the intervals of thorough examination could be required due to the following: 1. When the mobile crane frequently works near or above personnel, both personnel on site and members of the public outside the site 2. When the mobile crane is used for lifting people in exceptional circumstances, including rescue, even if not initially planned 3. When the mobile crane is used in extremely demanding environments, such as extreme temperatures and sandy or dusty atmospheres 4. In cases where a competent person has reviewed an in-service lift plan through risk assessment of method statement etc. to determine the expected load spectrum and frequency of use for the crane (changes in duty) Notes: 3f. Preparation for a Thorough Examination Earlier in this course, we looked at the tools and equipment that the examiner may require to carry out the thorough examination of mobile cranes and their supporting structures. We will now look at the preparation requirements that need to be considered prior to conducting a thorough 24 examination. Page © LEEA MOB (GLOBAL) v1 2023 AW SAFETY The crane should be positioned in an area that is safe and suitable area in which the examination will take place. LIGHTING Try to find a well-lit area; if this isn’t possible then you will need portable lighting. CLEAN The crane must be clean enough for the examination to be conducted without the potential to conceal any defects. Remember that it is not the responsibility of the examiner to clean the crane! ACCESS Ensure that safe access and egress arrangements are in place. This may be a combination of fixed access structures such as walkways, mobile elevated work platforms, or scaffolding. Personnel should be suitably trained and competent to use any portable access equipment and temporary access facilities. PPE requirements must be agreed between the owner and the competent person prior to access. IDENTIFICATION I.D. and rated capacity markings should be present and clearly marked, but these are also to be verified against the crane records. This may include the test certificate, legal documents required in a particular country/region (e.g. a Declaration of Conformity), manufacturer’s instructions/manuals and the previous report of thorough examination. HISTORY The competent person should check to see if any defects or malfunctions have been recorded for the crane, and whether any modifications or alterations have been carried out. The previous thorough examination report, in-service inspections and maintenance log should be viewed. HIDDEN PARTS Where the condition of hidden parts is unknown, these will need to be dismantled prior to the examinations, as required by the competent person. 3g. Competency Competency of personnel carrying out thorough examinations is a critical factor in ensuring that mobile cranes are examined correctly, methodically and thoroughly. All thorough examinations must be carried out by a competent person. The following information provides key elements of competency requirements, but you are advised to revisit your LEEA Foundation Certificate training notes in which the wider scope of competency was visited in depth. Further details can also be found in LEEA’s COPSULE and the BS7121 series of standards. Competent persons should have the necessary attributes, competencies, knowledge and experience to enable them to carry out effective thorough examinations of cranes. These requirements will depend on the purpose of the examination to be undertaken, the complexity of the cranes to be examined and the consequences of failure of those cranes. It is essential that such persons have adequate training, information and independence to 25 carry out the work required. (Ref: BS7121-2-1. 5.3) Page © LEEA MOB (GLOBAL) v1 2023 AW Continuous Professional Development (CPD) CPD enables individuals to continuously develop their knowledge and skills, maintaining currency with developments in their field of work and the quality and relevance of their skill set. Engaging in a programme of CPD is not onerous and does not necessarily involve additional training courses and time away from work; in fact, CPD is commonly achieved through many elements of our day-to-day work. CPD is, however, a joint responsibility between the competent person and their employer. The employer should maintain a CPD record for each competent person. This record should include details of how CPD is being achieved. There are 3 methods of CPD that may be considered: 1. Active 2. Reflective 3. Self-directed Examples of these are shown in the table below, together with some of the benefits for each method: 26 Page © LEEA MOB (GLOBAL) v1 2023 AW TYPE OF CPD EXAMPLE BENEFITS Attending a training course, conference, workshop, Ensure knowledge, skills and behaviours are up to date ACTIVE seminar, lecture, e-learning course or CPD certified event and relevant to your role. Enable any shortfalls to be such as LiftEx, Technical or Members’ Meetings. corrected whilst developing confidence and competence Increase self-awareness, developing the skills to Reading relevant news articles, podcasts, case studies and REFLECTIVE recognise and articulate what you have learned in industry updates. recording CPD activity. Regular reading of LEEA’s ‘Lifting Engineer’ publication and Diagnosing your learning needs: reading books and SELF News Bulletin, industry standards, guidance notes. Internet articles, internet searches, journals and other sources of DIRECTED browsing for relevant learning material. relevant information. Note: further information is available in BS7121-2-1. 5.3.11 and the LEEA Team are always happy to help answer any questions you may have regarding CPD. Email us at [email protected] 3h. Rated Capacity Indicators and Rated Capacity Limiters (RCIs and RCLs) As an examiner, you are likely to find many different types of RCI (Rated Capacity Indicator) or RCL (Rated Capacity Limiter) in service. You may find that older types of cranes will not have any such devices fitted. RCIs and RCLs should be included in the thorough examination; this should be a thorough visual examination of the individual parts and components. Where reasonably practicable, a calibration check and functional test of RCIs and RCLs to be carried out in addition to testing as part of the thorough examination. A calibration check is to be carried out after any major repairs of modifications have been made to RCIs or RCLs. Calibration is normally carried out by suspending calibrated weights from the crane to a maximum of 110% of rated capacity. Notes: 27 Page © LEEA MOB (GLOBAL) v1 2023 AW 3i. Rated Capacity Indicators and Rated Capacity Limiters (RCIs and RCLs) In the past, mobile cranes in the UK have frequently been subjected to overload testing at 4- yearly intervals in addition to thorough examinations. This is a legacy from older legislation. Legislation in certain areas of the world states that any testing is at the discretion of the competent person carrying out a thorough examination and the competent person will decide on the nature and the method of carrying it out. There are several disadvantages to routine overload testing and very few benefits. Some manufacturers do not recommend overload tests, expect in exceptional circumstances which are mentioned below o Overload o Jib clash o Collision o Use in arduous duties o Failure of a structural component o Subjected to weather in excess of design parameters o Significant modification, repair or change in operational requirements Repeated overloads can cause deterioration of the crane structure Fatigue and such defects may not be revealed by overload testing Authoritative bodies do not recommend it, as there is no defined structural or mechanical benefit If a crane fails during testing it could be dangerous and will certainly be expensive Note: The details and extent of testing should always be made clear in the test report. Notes: 3j. Load Testing Mobile Cranes Sequence for Testing BEFORE THE TEST The competent person should seek advice from the manufacturer (or other suitable design authority) before deciding on the nature of the test and the method of carrying it out, including the magnitude of the load to be applied. A visual examination of the crane and the test area should be carried out prior to commencing the test. Before the application of a load, a thorough examination of the crane should be carried out, 28 including verification that the crane is rigged in accordance with the manufacturer’s instructions. Page © LEEA MOB (GLOBAL) v1 2023 AW The competent person should check the rated capacity specified on the manufacturer’s certificate of test, the load radius indicator, the table of rated capacities displayed in the operator’s cab and those used by the RCI/RCL. The rated capacities should all be identical. FUNCTIONAL TEST A functional test with no load applied should be carried out to determine whether the controls, switches, contactors, and other devices operate correctly. The adjustments of the brakes and limit switches should be checked, and tests carried out to determine whether they are operating correctly. Mobile cranes have a large variety of support systems (for example crawler tracks, tyres and outriggers), jib configurations, counterweights and special attachments, all of which affect stability and strength of the crane. The competent person should take account of all the support systems when determining the conditions for overload testing. Support Systems during Load Testing OUTRIGGERS Certain manufacturers give duties for intermediate extension of outriggers. During functional load testing the competent person should check that the competent person should check that: 1. The intermediate/*Variobase extension position is clearly and durably marked on the outrigger 2. The manufacturer’s duty chart indicates the correct rated capacities applicable to the outrigger extension 3. The duty charts supplied by the manufacturer give the specified intermediate extensions 4. Provision is made by the RCI/RCL to accommodate the specified intermediate extensions *‘Variobase’ is a Liebherr product COUNTERWEIGHT Variations in the counterweight affect the stability of the crane. The manufacturer’s duty charts specify the ratings applicable for each counterweight. Sometimes mobile cranes have additional weights to increase the mass of the counterweight and special rigs to enhance the lifting capacities. JIBS 29 Page © LEEA MOB (GLOBAL) v1 2023 AW Before overload testing, the competent person should check that the jib is fitted to the crane in accordance with the manufacturer’s instructions. Overload testing of cranes with jibs should be carried out in accordance with manufacturer’s instructions. FLY JIBS For overload testing, fly jibs should be erected in accordance with the manufacturer’s instructions for the crane. Overload testing of cranes with fly jibs should be carried out in accordance with the manufacturer’s instructions. LEVELLING The importance of levelling the crane cannot be over-emphasized. The crane should be level to ±0.5% slope. 1. One method of verifying the level of the crane is to use a spirit level 2. A built-in levelling device may also be used to monitor this If the slope is found to exceed the limit given above, testing should be stopped, load removed, and the crane re-levelled. LIFTING FREE ON RUBBER WHEELS Tyre pressures are a critical factor in retaining the necessary stability margin of mobile cranes. 1. Some crane manufacturers stipulate higher tyre pressure for free on wheels (static condition fully mobile) duties than for road travel as a vehicle 2. Where the manufacturer permits lift and travel duties these can differ from the free on wheels duties LIFTING CAPACITIES The load ratings marked on mobile cranes and shown on the manufacturer’s rated capacity charts indicate the gross loads. This fact should be considered when the crane is being tested and an allowance should be made for the load imposed by suspended hook blocks, slings and lifting accessories. Certain cranes can become unstable when working with long jibs and fly jibs if the jib angle to the horizontal is reduced below the minimum angle given in the crane manufacturer’s instructions. Notes: 30 Page © LEEA MOB (GLOBAL) v1 2023 AW Supplementary Load Testing 1. The crane should be functionally tested without a load applied to determine whether it is working properly 2. After the functional tests without a load applied, the efficiency of the crane’s hoist brake(s) should be tested with the load that gives the maximum line pull on the hoist rope(s) 3. The load should be lifted clear of the ground and the brake applied by returning the control to neutral 4. There should be no fall back or creep 5. The load should be re-hoisted, and the brake re-applied to check the ability to re- hoist 6. The load should then be lowered, and the control returned to neutral with the load still clear of the ground 7. There should be no over-run or creep 8. At every configuration in the test program the crane should be set up with the test load at a radius/angle within the rated capacity of the crane 9. The test load should then be raised just clear of the ground and the crane derricked out to the radius/angle where the test load is at the overload specified by the manufacturer 10. The load should be raised until every tooth in the train of the hoist gears has been subjected to the overload 11. Then lowered to between 100 mm and 200 mm above the ground and held there for 10 minutes 12. There should be no over-run or creep 13. The load should be slewed at the lowest possible speed in both directions through a small arc to determine the ability of the structure to withstand lateral loadings 14. The test load should then be slewed through the maximum slew angle permitted by the design of the crane Post-Test Examination On completion of the overload test a further thorough examination of the crane should be carried out. Notes: 31 Page © LEEA MOB (GLOBAL) v1 2023 AW 3. Thorough Examination In this module, we will look at the individual components that we looked at earlier in the scope of thorough examination. j. Mobile Crane Carrier/Chassis Manufacturer’s information plate/label and duty charts. The plate would include: Type/Model, Works or Serial number, Year of manufacturer and manufacturers name Any other markings as per legislation Ensure all markings are clear and legible 32 Page © LEEA MOB (GLOBAL) v1 2023 AW Lights Headlights, sidelights, warning lights, indicators, hazards, windscreen wipers/washers, registration plate. Check that all lights function correctly, the condition, function and security of windscreen wipers/ washers and the registration plate is clear, secure, and legible. Reversing alarms/lights: Not all cranes will be fitted with both. What is fitted, however, must work properly. 33 Page © LEEA MOB (GLOBAL) v1 2023 AW Hook Attachment Points Particular attention needs to be paid to the hook attachment point, especially those bolts or welds that are not normally visible, i.e., behind the bumper. Use a torch and mirror to inspect these if necessary. Ensure that all accessories used to attach the hook block are examined and reported on as required for compliance with any local legislation. Operator Cab Carry out examinations of: Housekeeping Control identification Seat and safety belt Condition of operator pedals Check the external condition of the cab, including bodywork, door, window mechanisms and mirrors 34 Page © LEEA MOB (GLOBAL) v1 2023 AW Tyres and Wheels Check the tyre condition, size, type, tyre pressures, valve caps, fixing studs/nuts for correct torque setting. Tyre Pressure is important for any crane, but it is essential that it is correct for cranes that have free on rubber (free on wheels) duties. Manufacturers load calculations and speed of travel are based on the tyre pressures being correct to avoid tipping. If testing on rubber duties, check to see if axle or suspension locks are fitted, or required. Most mobile cranes nowadays are fitted with radial tyres. Although cross-ply tyres are rare, the examiner must ensure that the tyres fitted to a mobile crane are either all radial or all cross ply. Note: a mix between the two types of tyres is not acceptable. Notes: 35 Page © LEEA MOB (GLOBAL) v1 2023 AW Automatic Carrier Levelling and Suspension System Raising and Lowering Observe suspension lowering when setting up and suspension raising when preparing to finish. Further investigation will be needed if any issues are identified. Leaf Spring Suspension Check for security, condition, corrosion and correct type is fitted to the model of crane. (Refer to the original equipment manufacturer's specifications). Notes: 36 Page © LEEA MOB (GLOBAL) v1 2023 AW Hydraulics Check the hydraulic tank oil level is correct before setting up the crane Ensure the cap is fitted to the tank If accessible check the filter Once the P.T.O. (Power Take Off connection) is engaged, listen for any adverse sounds coming from the pump during operation Check all pipes, flexible hoses and connections for leaks and condition 37 Page © LEEA MOB (GLOBAL) v1 2023 AW Hydraulic leaks and burst pipes can be extremely dangerous. It is important that all hydraulic system components are systematically checked by the examiner during the thorough examination. Notes: 38 Page © LEEA MOB (GLOBAL) v1 2023 AW Outrigger Jacks and Beams Outrigger Beams Visually examine the outrigger beams to ensure they are level: beams that are off set could indicate cracked/damaged welds, worn box sections or worn/ missing wear pads. Examine all visible hoses, connections and pipes for cracks, deformation or leaks. If access holes are available on the side of the beam, remove the covers and check the interior of the beam for hydraulic oil presence, this can indicate a leak in the system. Check that the jack ram is dry, a film of oil can indicate a seal is leaking and it will get progressively worse. Use a torch if necessary and check the outer seal cover. 39 Page © LEEA MOB (GLOBAL) v1 2023 AW Whilst the operator is setting up the crane and outriggers, observe for smooth operation Ensure that the locking holes line up and that the locking pins are available and can be inserted Check for deformation in hoses and pipes The image below indicates severe outrigger float: Other forms of outrigger damage. Cracks and damaged or missing components: 40 Page © LEEA MOB (GLOBAL) v1 2023 AW Controls and Level Indicators Check the condition of the operating controls and that they are clearly labelled. Level gauges must be clear and undamaged. Notes: 41 Page © LEEA MOB (GLOBAL) v1 2023 AW Power Take Off Drive Shaft Visually examine to ensure the shaft is secure, the condition of the shaft and if visible the Power Take Off Shaft is engaged. Notes: 42 Page © LEEA MOB (GLOBAL) v1 2023 AW Access Ladders Access ladders are to be checked for damage, missing steps, attachment fixtures, broken welds, and missing bolts etc. 43 Page © LEEA MOB (GLOBAL) v1 2023 AW k. Thorough Examination – Crane Structure The examiner is required to check the following key examination areas, as a minimum: Manufacturers plate, serial number, model, year of manufacture Counterweight and counterweight attachment system Operator cab RCIs Boom cylinder Boom Boom telescoping sections Manufacturer's Identity Plate The information on the manufacturer’s plate is required not just to confirm the identity of the crane, but also to ensure that the correct load charts are available to correctly verify the RCL, so these markings are required to be clear and legible, and the examiner should do so. The serial number on the rated capacity charts should match the serial number on the crane plate. 44 Page © LEEA MOB (GLOBAL) v1 2023 AW Counterweights Fitting the counterweights as detailed in the load charts will ensure that the crane is working to its maximum boom lengths and radius. It is necessary to observe the counterweight attachment rams whilst they are deploying to ensure that they extend fully and that they engage and lock. Counterweights must be observed when being fitted to ensure that both rams deploy correctly, and both activate (rotate) to lock. By closely observing the hydraulic rams for the counterweights, we can ensure that each ram is extending fully and is locking in position before lifting the counterweight. A further check is to observe the operator’s system display to ensure it is showing the correct sequence of operation. Examine the hydraulic rams and attachments for leaks, loose connections(nuts) or damage. 45 Page © LEEA MOB (GLOBAL) v1 2023 AW Operator and Cab Controls Checks should be made of the entire cab and chassis cab, including: The cab housekeeping – it should be uncluttered and tidy with any rubbish removed The operator’s seat - in good condition and operates in all modes There are no loose wires or panels anywhere in the cab The RCL is fully functional The crane-specific load charts are present in the operator cab There are no obstructions to the operators view The glass in the cab is all safety glass and has not been modified with anything other than the manufacturers specific glass That all the control functions and switches are clearly marked and that they perform as marked The swing brake engages and holds The tilt cab mechanism if applicable operates correctly Lights and windscreen wipers/ washers function correctly Air conditioning/ heater controls operate correctly Check that the tilt cab mechanism if applicable operates correctly, the lights and windscreen wipers/ washers function correctly and the Air conditioning/ heater controls operate correctly. Notes: 46 Page © LEEA MOB (GLOBAL) v1 2023 AW 47 Page © LEEA MOB (GLOBAL) v1 2023 AW Crane Controls Check that all the control functions and switches are clearly marked and that they perform as marked. Rated Capacity Limiter (RCL) and Load Monitoring Indicator To verify that the RCL is operating correctly the following steps should be taken: Check rated capacity (load) charts are correct for model and type of crane Verify closed boom length on RCL against figures on rated capacity chart Pick a configuration and request operator to set boom length accordingly Boom out to a selected radius/angle Verify that the capacity shown on the RCL is the same as shown on the rated capacity chart Physically measure radius to verify it matches RCL Attach a known load, or lift a load using a calibrated load cell and verify RCL Repeat for at least two different radii 48 Page © LEEA MOB (GLOBAL) v1 2023 AW Load Monitoring Indicator Check that the Load Monitoring Indicator (remote bar graph) is functioning and secure. Swing (Slew) Gear Mechanism If internal gearing is used for the swing mechanism the only way, short of dismantling the assembly, to examine this is by using the examiners visual and audible senses. If swing drive is external, it is relatively easy to examine, the points to consider are: Worn gear teeth Noisy drive motor Loose bolts If excessive movement is noted when the crane is under load, then measurements can be taken using a dial test indicator (DTI) and compared with manufacturers readings if available. The examiner will observe the crane whilst slewing and note if there is any discernible rocking movement that would indicate loose bolts or worn gearing, also listening for any grinding of the drive motor. Dial test indicator measurements are a last resort that are seldom utilised, and, unless previous data is available, are non-conclusive. However - it is another tool we can use. Positive Swing Lock 49 Page © LEEA MOB (GLOBAL) v1 2023 AW All mobile telescoping cranes must be fitted with a positive swing lock to ensure that the boom cannot swing when in the locked position. This is essential if the crane is to be moved with the boom in the upright position, (pick and carry duties). Also, while moving/being transported with the boom on the rest, it ensures the boom cannot rotate unexpectedly, (there have been cases of booms swinging whilst travelling and causing accidents to other road users). The example shown on the next page is just one type there are many more different types. Notes: 50 Page © LEEA MOB (GLOBAL) v1 2023 AW Central Rotary Distributor All mobile telescoping cranes are fitted with a central rotary distributor to allow the crane to rotate through a 360° arc. The rotational coupling for hydraulics and electrical connections allows all crane actions to be performed normally even when the cab is rotated. The examiner should ensure that all fastenings are secure, all hydraulic hoses and connections are not leaking and there is no damage to visible wires. On older cranes, a safety chain was attached to ensure the coupling rotated with the crane in case securing bolts sheared. Telescoping Booms The telescopic boom on a mobile telescoping crane is attached to the swivel structure by boom pins and raised by a one or two hydraulic ram system. 51 Page © LEEA MOB (GLOBAL) v1 2023 AW To thoroughly examine the telescoping boom pins, examiners should follow the guidance below: Check upper and lower boom pins paying particular attention to boom derrick ram attachment pins Failure to ensure locking pins are in place can cause the pin to work loose resulting in boom collapse Check all hydraulic connections for loose fittings and leaks Observe derrick piston(s) whilst the boom is being lifted if oil is detected on the piston it can indicate that the seal is leaking Operate boom up and down to clarify if there is actually a leak, as a leak would be more visible whilst the system is under pressure Notes: 52 Page © LEEA MOB (GLOBAL) v1 2023 AW Telescoping Boom Flexing When fully extended and under load modern booms can flex quite extensively, this is normal and allowable. However, if there is a downward bend whilst not under load it may indicate that the bottom and top wear pads may need adjustment or replacement. To verify the allowable deflection, you can measure the maximum radius and check against the rated capacity chart. Wear pad adjustment or replacement is a commonly reported action. Crane owners and mechanics don’t like to hear this as it sometimes means pulling the boom to replace the inner set of wear pads. Looking at a boom like the picture below this would indicate that the side wear pads on the outer section of the boom require adjustment or replacement. A simple method of checking to see if boom wear pads require replacing or adjustment is to fully extend the boom and get the operator to swing a short distance then stop suddenly, any movement in the boom can then be observed. If the whole boom moves, this is expected and acceptable, if individual sections of the boom move sideways, adjustment or replacement of the wear pads in these sections are indicated. 53 Page © LEEA MOB (GLOBAL) v1 2023 AW Some examples of wear pad locations are shown on the next page: The fly jib attachment lugs should also be examined to ensure they have not been damaged or distorted due to boom flexing: Telescoping Systems Older cranes may use a multi ram system for telescoping the boom and in these cases all or most of the boom sections will move at the same time. The modern tendency is to utilise a single ram telescoping system which will telescope the boom section a specific percentage of movement and then lock it in place before returning to its start point and repeating with the next section. 54 Because the telescoping rams are internal, it is not always possible to examine them, however some cranes have viewports at the base of the boom that allow a person to observe the rams Page closing. © LEEA MOB (GLOBAL) v1 2023 AW If there is no option for seeing the ram, by examining the boom base for signs of oil we can at least determine whether there are any hydraulic leaks. The condition of the hydraulic hoses on the recoil drum is also a clue as to whether there are any leaks. Single stage ram systems have to be checked on the RCL display to ascertain whether they are operating to their correct configuration and whether the boom pin locking system is functioning. Notes: Boom Furniture Boom furniture may include: Boom length/angle sensor Cable Reeling Drum Limit switches Dynamometer Anti-two block switch Pressure transducers (actual load) Attachments on booms are critical for the correct working of the Rated Capacity 55 Indicator/Limiter. Page © LEEA MOB (GLOBAL) v1 2023 AW Cable Reeling Drum (Power feed to angle sensor and other boom furniture) Ensure that cable is laid flat on the drum, otherwise false length readings may be obtained. The length of cable is mounted to the tip of the boom and transmits the anti-two block signal. The number of turns and the diameter of the cable drum controls the length of the uncoiled cable, thus, the telescopic length is determined. The angle measurement is determined by means of the angle sensor mounted inside the cable reel housing shown below: Fly Jibs and Mounting Structures The difference between a fly jib and a luffing jib is that a fly jib is normally fixed in position during a lift and the main boom moves up and down. A luffing jib, however, is the main mover in luffing configuration and the main boom is normally set at a fixed length and angle. When fly jibs are stowed on the side of the crane boom it is critical to ensure that the jib attachment pins are also stowed on the boom to ensure that the correct pins are available to pin the jib to the boom. 56 Page © LEEA MOB (GLOBAL) v1 2023 AW Boom stowed fly jib extensions, sometimes known as swing-aways, can be examined even when not erected. With the main boom in a horizontal position over the side, the length of the boom can be examined. Because most fly jib extensions are of lattice boom construction, particular attention should be paid to the main cord and lacings. Check for damage such as distortion and cracked welds paying attention also to the attachment lugs and holes. 57 Page © LEEA MOB (GLOBAL) v1 2023 AW Fly Jib Angles The angle of the fly jib may be variable from 0°- 60° and may be manually set or have a powered adjustable system in place. Notes: 58 Page © LEEA MOB (GLOBAL) v1 2023 AW Luffing Jibs Luffing Jibs are used in conditions where it is impractical to boom the main boom up or down, e.g. in close proximity to a building(s) and to offer a greater radius as well as height for the crane. The luffing jib is attached for extra height and extended to clear all obstructions then it can be ‘luffed’ up and down covering a larger horizontal area than a fixed boom. Side-Supported Lifts Old style super lifts normally consisted of additional weights on a platform or wheeled trolley, which then had to be attached to the crane. Modern technology has evolved a method of supporting the boom by rigging extendable boom side-mounted wings which can increase the crane capacity significantly. Some cranes have the side mounted super lift assembly permanently mounted; on others it comes as a separate attachment for road weight restrictions. The images below show a detachable version: 59 Page © LEEA MOB (GLOBAL) v1 2023 AW Boom Tip Sheaves Examine boom tip sheave assemblies: Check for damage to sheaves Check sheaves are free running with no play in the bearings Ensure rope guides are in place and secured Check for wear caused by wire rope rubbing on guide Severe damage can indicate wire rope may have damage too. Notes: 60 Page © LEEA MOB (GLOBAL) v1 2023 AW Wire Rope Anchor The hoist wire operates a hook block and to do this the wire is either attached to the hook block or reeved and attached to the boom tip by a wire rope anchor. It is essential that the correct wire rope anchor is attached and that the wire hoist rope has been inserted correctly and locked in place. Shown here are two methods currently in use to anchor the wire hoist rope, the one on the left is known as a button type anchor and the one on the right is a wedge and socket anchor. If the wire rope fitted with the manufactured end (button) fitting for the easy assembly anchor gets damaged close to the fitting, it cannot be cut and reused in that fitting. The wire rope has to be returned to the manufacturer for a replacement fitting or sent to a manufacturer recognised company for re-terminating. This can be as expensive as buying a new wire rope and often crane owners will just buy new. With the wedge and socket it is imperative that the socket is of the correct size for the diameter 61 of the rope being used and that the wedge and socket are part of the same assembly and not mixed. Page © LEEA MOB (GLOBAL) v1 2023 AW Wedge and Socket Fitting There are a number of ways the wedge and socket can be fitted and shown is the wrong way and the correct way. Also shown is a wedge with rope checker holes in it, that can be used as a guide to check if the wedge and socket are suitable for the wire rope size. A common method of wrongly fitting a wedge and socket anchor is to reeve the live end down the slanting side of the wedge and back up the straight side. This causes the wire rope to sit at an angle and under load the pressure of the load will be concentrated on that small area at the anchor instead of being distributed over the whole diameter of the wire rope. Notes: 62 Page © LEEA MOB (GLOBAL) v1 2023 AW Anti-Two Block System The anti-two block actuator consists of a weight suspended a measured distance from the boom tip by a chain or wire rope attached to the anti-two block switch. When the weight is suspended from the microswitch, a continuous signal is transmitted to the RCL, when the weight is raised by the hook-block, it interrupts the signal causing a warning light and audible alarm to be activated at the operators console and prevents any further upward movement of the hook-block. To test the anti-two block alarm, request the operator to raise the hook block until it is just below the suspended weight then slowly raise the hook block until the alarms activates or the weight is raised so that the alarms should activate. Care must be taken to ensure a block-to-block incident does not occur during this test Ensure that all the assembly and safety pins are present and correctly in place Notes: 63 Page © LEEA MOB (GLOBAL) v1 2023 AW Hook Block The hook block shown below demonstrates the correct information that should be available on all mobile crane hook blocks. In this example the following information is clearly legible: Capacity or SWL: 25T Weight of Hook Block: 360kgs Manufacturer’s plate If the manufacturer’s plate is not on side of the hook block, it can often be found on top of the block. 64 Page © LEEA MOB (GLOBAL) v1 2023 AW Hook Block Examination Examination of the Hook Block should include but not be confined to the following: Check for any visible damage to the hook block Check hook to ensure that it swivels in all directions and there is no excessive play in the bearings Check hook safety latch and throat opening for security and function Check manufacturers plate to find capacity, hook weight, wire rope diameter Confirm wire rope is of the correct diameter 65 Page © LEEA MOB (GLOBAL) v1 2023 AW Additional Information: a hoist rope that twists whilst being hoisted or lowered may indicate that a twist has been introduced when re-reeving, it may also indicate that the wrong lay of rope has been fitted. Using a sheave gauge, check for wear on sheaves. During the thorough examination, as the crane operator booms up, check to see that hook block is reeved correctly. If in doubt consult the load chart or the manufacturer’s recommendations. 66 Page © LEEA MOB (GLOBAL) v1 2023 AW Notes: 67 Page © LEEA MOB (GLOBAL) v1 2023 AW Hoist Drums Hoist drums have to be thoroughly examined to ensure that: They are securely fastened to the superstructure There is no visible damage to the drum The hydraulic hoses and connections are secure and not leaking The wire hoist rope is layered on the drum correctly The drum rotates correctly The hoist brake operates There are no detrimental sounds coming from the drum during operation Notes: 68 Page © LEEA MOB (GLOBAL) v1 2023 AW 3l. Examination of wire rope Safe operation of Mobile Cranes incorporating wire rope depends, to a considerable extent, upon the level of detailed examination that is carried out by the Competent Person during the periodic inspection, not with-standing that daily operator checks by the user also have a significant bearing on safety of the machine in use. The Competent Person should firstly refer to instructions provided by the original equipment manufacturer, local or application-specific regulations should always be followed. The aim of the periodic inspection is to determine whether the rope: a) Can safely remain in service, and the latest time on which the next examination is to be carried out b) Needs to be withdrawn immediately, or within a specified time 69 NOTE: Rope should always be clean; if this is not possible, consider electromagnetic wire rope Page examination method, where appropriate. © LEEA MOB (GLOBAL) v1 2023 AW The inspection of wire ropes should be systematic and follow a logical order so that no part of the rope, or the accessories and attachments to which it connects are missed. In manual machines, particular attention is to be taken at the following locations: Rope drum anchorage Check entry of rope into detachable terminations such as wedge sockets for broken wires but also correct orientation of the rope through the socket Rope within the area of a termination point, particularly where it enters the termination point, where it is typical to find broken wires Sections of rope travelling through sheaves Sections of rope travelling through the hook block Sections of rope that spool onto the rope drum, especially in areas where the rope crosses over itself in multi-layer drums Any section of the rope that can be damaged by abrasion in contact with an external fixture such as a hatch opening Any part of the rope that is exposed to heat Spooling/ cross over damage Slippage in ferrules (evidence of the rope pulling through the ferrule) 70 Page © LEEA MOB (GLOBAL) v1 2023 AW Inspection frequency As we know, the periodic inspection for lifting appliances is each 12 months, or 6 months for any people carrying machines. The Competent Person may however decide that more frequent inspections are required for certain appliances due to several factors, which may include: Any specific national statutory requirements in the country of use Type of hoist and the environmental conditions it operates in Classification group of the machine Results of previous inspections Experience of other similar types of hoist in similar use or conditions How long the wire rope has been in service How frequently the hoist is operated Original manufacturers recommendations Inspection record A record of each and every inspection should be made by the Competent Person. ISO 4309 states that a running record of crane rope inspections is maintained. An example of this is available in the standard in Appendix E. Combined effect assessment As we have seen, there are several areas of the rope that need to be checked during the visual examination. There are many faults that may exist in a wire rope, and this is not limited to broken wires! The examiner therefore needs to be aware of the many different defects that will affect a wire rope’s performance and service life, which we will explore in this module. Assessment from the inspection The extent and severity of deterioration is to be assessed and provided as a percentage (% Severity Rating) for example 20%, 40%, 60%, 80%, or 100%, for each individual type of discard criteria. This can be expressed in words as, ‘slight’, ‘medium’, ‘high’, ‘very high’ and ‘discard’. This assessment can be drawn from different visual inspection and/or measurement, and Magnetic Rope Testing (MRT). The combined effect assessment is an overall assessment of the condition of the wire rope. The examiner will record his findings using a report format similar to the one shown on the next page: 71 Page © LEEA MOB (GLOBAL) v1 2023 AW NOTE: the examination record requires the examiner to enter a ‘% severity rating’ in: The number of broken wires (6 x d and 30 x d) Decrease in diameter Corrosion Damage and / or deterioration Having collated this data, the examiner now sums up all the individual severity ratings and determines a total combined severity in the form of a percentage. This is then added to the end column of the *combined assessment table. If the examiner so chooses, the degree of severity may be inserted in the form of a description (words) rather than a percentage. An equivalence table has been provided here to show how percentage and description severity ratings align in the standard: Ultimately, the examiner must determine whether the rope is safe to continue in service. If this is the case, the examiner may wish to reduce the period of time before the next examination is carried out due to the rope’s current condition and level of deterioration. Notes: 72 Page © LEEA MOB (GLOBAL) v1 2023 AW This table shows examples of combined effect assessments (*combined assessment table): Combined Assessment Table NOTE: Where the term MRT (LF) is referred to in the table, this is technically known as a ‘local fault’ or ‘local flaw’, such as a wire break, welded wire (from production), corrosion, pitting or nicked (pinched) strands. Modes of deterioration This table shows the common types of deterioration whether or not they can be either counted or measured, or if visual or MRT inspection would be required for each type: When might a wire rope inspection be carried out, other than periodically? If we consider that mobile cranes are thoroughly examined in the event of exceptional circumstances, and not solely periodically, then surely the load ropes may also need to be thoroughly examined too? Here are two circumstances why a thorough examination of the wire rope should be carried out: 1. Following an accident a. Or: an exceptional circumstance such as an overload or collision 73 2. If the appliance has been out of action for a period in excess of 3 months Page © LEEA MOB (GLOBAL) v1 2023 AW Magnetic Rope Testing (MRT) By giving visibility right through to a wire rope’s core, Magnetic Rope Testing (MRT) can play a vital role in improving lifting safety. MRT is a method used to see into the heart of wire rope used on cranes in order to detect any deterioration that might have occurred during service. The MRT method involves passing the rope through a permanent magnet. This sets up an electromotive force, which is picked up with electronic sensors that can detect any breaks in the rope or any corrosion that occurs throughout the section of the rope, which is known as Loss of Metallic Area (LMA). There are different MRT equipment manufacturers, but the method is exactly the same with each one. To examine the core of the rope under normal examination, without MRT, requires a special tool to open the rope’s strands. But this still only gives visibility of a small percentage of the rope’s length. On multi-strand crane ropes, you can never see the core because the multiple layers can’t be opened up due to the underlying layers being laid in the opposite direction to the outer strands. For high integrity cranes, particularly those used offshore, wire rope manufacturer’s will use MRT to produce a ‘baseline’ as a ‘birth certificate’ for a length of wire rope. So, when it enters service, the competent person knows precisely what that rope is like at the outset and can then accurately monitor any deterioration throughout its service life. Notes: 74 Page © LEEA MOB (GLOBAL) v1 2023 AW ISO 4309 discard criteria Types of deterioration: 75 Page © LEEA MOB (GLOBAL) v1 2023 AW Notes: 76 Page © LEEA MOB (GLOBAL) v1 2023 AW 77 Page © LEEA MOB (GLOBAL) v1 2023 AW 78 Page © LEEA MOB (GLOBAL) v1 2023 AW Notes: 79 Page © LEEA MOB (GLOBAL) v1 2023 AW Notes: 80 Page © LEEA MOB (GLOBAL) v1 2023 AW 81 Page © LEEA MOB (GLOBAL) v1 2023 AW 82 Page © LEEA MOB (GLOBAL) v1 2023 AW 17) Heat or electric arcing damage Can be shown by a ‘bluing’ of the steel in the area affected. MRT is the preferred method for further investigation. 18) Mechanical damage Usually caused by the rope coming into contact with the structure of the crane on which it is fitted or an external structure/load. 19) Decreased rope elasticity This is often caused by: A decrease in the rope’s diameter Elongated ropes Insufficient clearance between strands and wires A decrease in elasticity is normally identified by fine powder coming from the valleys of the rope (known as fretting corrosion) and a notable stiffening of the rope as it is being handled. Deterioration In the case of 6 and 8-strand ropes, broken wires usually occur at the external surface. In the case of rotation-resistant ropes, there is a probability that the majority of broken wires will occur internally and are “non-visible” fractures. It is therefore the reason why the allowable number of visible broken wires for a rotation-resistant rope is less than allowable in a single- layer rope. NOTE: students are reminded that access to relevant standards, such as ISO 4309, is necessary in order to carry out thorough examinations correctly. Broken wires It is usually the number of broken wires developing in a wire rope, which causes its removal from service. It is essential that the entire length of a wire rope be inspected frequently for broken wire(s), excessive wear, and lack of lubrication, with particular attention being paid to those areas adjacent to terminal fittings and where an accelerated rate of wear or corrosion is to be expected, e.g. where a rope passes around sheaves or pulleys, or is particularly exposed to the elements. All examinations must consider these individual factors, recognising the particular criteria: One line of broken wires: One line of broken wires running along the length of the rope would suggest that the rope has insufficient support, generally caused by oversize sheave(s) or drum grooving Fatigue breaks Fatigue induced wire breaks are identified by the flat ends on the broken wires IMPORTANT! Wire ropes are known to increase the rate of broken wires the longer they are in service. Have a look at the following graph which shows examples of this in two different ropes: 83 Page © LEEA MOB (GLOBAL) v1 2023 AW Multi-layer drum spooling Powered lifting machines (mobile cranes) utilising a multi-layer rope drum where the rope is spooling on top of itself, layer after layer tend to suffer from broken wires and deformation where the ropes cross each other. These areas should be the main focus of attention for the examiner. Valley wire breaks The examiner should pay particular attention to broken wires in the valley of a wire rope as these could indicate that internal rope deterioration, particularly in smaller diameter ropes. Such breaks can be exposed by flexing the rope from its natural position under no tension. IMPORTANT: If 2 or more valley breaks are discovered in one lay length, it is likely that the core is no longer supporting the outer strands. An MRT inspection would be able to confirm this. BS ISO 4309 details the discard criteria for the allowable number of broken wires, depending upon the ‘Rope Category Number’ of the rope (RCN). Before determining the discard criteria for load ropes under, it is necessary to identify the ropes RCN. By way of example, we are going to look at an RCN 02: Viewing the example from ISO 4309 above, we can see that it is an ordinary-lay rope, categorized as an RCN 02 (single-layer or parallel-closed rope). The extract from Table 3 in ISO 4309 below shows that an RCN 02 rope of this construction may have a maximum of 3 broken wires over a length of 6 x its diameter, or 6 broken wires over a length of 30 x its diameter, fitted to an electric wire rope hoist, M3 duty, using a single-layer drum. 84 Page © LEEA MOB (GLOBAL) v1 2023 AW Important note 1 – Seale construction ropes with less than 19 wires in each strand: In the example provided above (RCN 02 rope), you may have noticed that the illustration represents a Seale construction rope. The total number of load-bearing outer wires in the outer layer of strands in this rope equals 6 x 19, = 114, therefore ordinarily it would be classed as an RCN 04 in the table above, having between 101 and 120 outer load-bearing wires. However, ISO 4309 states that for Seale construction rope where the number of wires in each strand is 19 or less, they are placed in the table (shown above) 2 places higher than where they would normally be placed for the total number of outer wires, hence it is moved from RCN 04 to RCN 02. Important note 2 - M5 to M8 duty classification: Ropes fitted to machinery having a duty classification of M5 to M8 may have twice the number of broken wires listed in the ISO 4309 tables. RCN (Rope Category Number) If the RCN number of the load rope cannot be found in annex H of ISO 4309, the following method should be used for calculating the number of allowable broken wires: Determine the total number of load-bearing wires in the rope Simply add together all of the wires in the outer layer of strands except for any filler wires and read off the discard values for broken wires over a length of 6d and 30d for the appropriate conditions, in the tables provided Uniform decrease in diameter For wire ropes that are fitted to a single-layer rope drum, ISO 4309 provides guidance to the examiner in the form of suggested % severity rating and discard criteria. The figures in the table below are derived from a calculation which determines the amount of decrease in diameter from the nominal diameter of the rope: 85 Page © LEEA MOB (GLOBAL) v1 2023 AW Notes: 86 Page © LEEA MOB (GLOBAL) v1 2023 AW Load Charts Rated Capacity Charts provide critical information to enable R.C.L.’s (Rated Capacity Limiters) to be calibrated correctly and lifting operations to be planned and carried out safely. Rated Capacity Charts are essential to the crane operator to enable them to input the correct information into his R.C.L. so they can operate safely and within the design parameters of the crane. The technical information contained in Rated Capacity Charts is of importance to the competent person(s) and will assist them in carrying out their examinations. In the following tables and diagrams are pages which will provide an example of a Rated Capacity Chart which shows the type of the information that the competent person may use to carry out a complete thorough examination and functional test of a mobile crane. The weight of the crane is required to ensure that the crane can safely travel to its location without exceeding weight restrictions for roads, bridges, crossings or recent excavations. In the case of rough terrain cranes, the weight is required to ensure appropriate heavy transport is available to relocate the crane from site