Milling 1st Sem 2025 PDF
Document Details
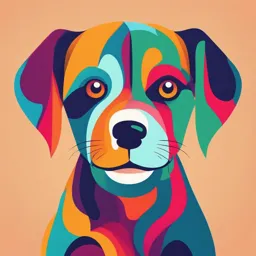
Uploaded by SociableSteelDrums
2025
Tags
Summary
This document is a PowerPoint presentation on milling, covering particle size reduction, crushing, and grinding. It discusses objectives, importance, and energy requirements. The document also introduces various theories and methods for particle size reduction.
Full Transcript
MILLING :Particle Size Reduction (Comminution, Crushing, Grinding) Definition Milling is one of the basic machining processes that allows large amounts of material to be removed quickly. Milling is a very versatile process capable of producing simple two dimensional flat shapes to complex th...
MILLING :Particle Size Reduction (Comminution, Crushing, Grinding) Definition Milling is one of the basic machining processes that allows large amounts of material to be removed quickly. Milling is a very versatile process capable of producing simple two dimensional flat shapes to complex three dimensionalof Objectives interlaced surface Size Reduction To produce smaller particles in the preparation of suspensions or to facilitate the mixing of powders. To increase surface area (eg. to increase adsorptive properties, Expose to heat, moisture, enzymes). In drugs that are crushed to expose cells prior to extraction Reduce the bulk of a material, since shipping charges may be based on volume. Increased Digestibility and Palatability Reduced Sorting & Selective Feeding Preparation for Secondary Operations Importance of Particle size (PS) and lifetime of drug: 1- Determination of PS 2- Crystaline form (polymorphism), invitro dissolution..etc 3- Powder Flow, cmpressibility..etc 4- Invivo dissolution, absorption..etc 5- Some drugs (in nano or micro size) may be absorbedas particles 6- Drug distribution and protein binding. INFLUENCE OF MATERIAL PROPERTIES ON SIZE REDUCTION 1.Toughness: (Brittleness or plasticity) size reduction is carried out by a process of crack propagation, whereby localized stresses produce strains in the particles large enough to cause bond rupture and thus crack. In general, cracks are propagated in regions possess flows or discontinuities and is related to the strain The stress in a material is concentrated at the tip of a crack and the stress multiplier can be calculated from an equation developed by Inglis: where σK is the multiplier of the mean stress in a material around a crack, L is the length of the crack and r is the radius of curvature of the tip of the crack. In the case of a thin disc- shaped crack, shown in cross- section in Figure 10.1, the crack is considered to have occurred at molecular level between atomic surfaces separated by a distance of 2 × 10−10 m for a crack 3 μm long, which gives a stress multiplier of approximately 245. The stress concentration diminishes towards the mean Once crack is initiated its tip propagates at a velocity of 40% of sound speed in solid. This crack propagation is so rapid that excess energy is dissipated through the material and concentrate on other discontinuities where new cracks are propagated. Thus a cascade effect occurs and hence an instantaneous brittle fracture Tougher materials resisit fracture, because they can undergo plastic flow which allows strain energy relaxation without crack propagation. In plastic flow atoms and molecules slip over each other causing deformation without cracking Griffiths’ crack theory account for a fracture stress, σ, which varies inversely with the square root of crack length, L, Ep is the energy required to form unit area of double surface. 2 Surface Hardness: Hardness of a material can be described by its position in Mohs’ scale which is a table of materials: Diamond Hard no > 7......................Talc < 3 Diamond has a surface so hard that can scratch anything below it while talc is so soft that can be scartched by any other material above it. Materials such as rubber, stearic acid gums are capable of absorbing large amount of energy through elastic and plastic deformation without crack initiation. These type of materials can be size reduced by lowering the ambient temp. below their Glass Transition Temp. at which they undergo transition from plastic to brittle materials. 3. Other factors: Moisture content of the material below 5% good for dry grinding above 50% wet grinding is to be carried out. Energy Requirements of the Size Reduction Process Only a very small amount (2%) of the energy utilized by a machine actually used in size reduction. The remainder lost in many ways including: 1. Elastic deformation of particles 2. Plastic deformation of particles without fracture 3. Deformation of metal machine parts 4. Friction between particles and the machine and particles 5. Heat, vibration, and noise A number of hypothesis have been proposed to relate energ input to the degree of size reduction Rittinger’s hypothesis: energy is proportional to the new surface area E=kr(Sn-Si) E: energy input Kr: Rittinger’s constatnt Sn: new surface area Si: initial surface area Kick’s Theory: The energy used in deforming or fracturing a set of particles of equivalent shape is proportional to the ratio of the change in size E= KKlog(di/dn) KK: Kik’s constant di: initial particle diameter dn: the new particle diameter Bond’s Theory: The energy used in crack propagation is proportional to the new crack length produced which is related to the change in particle dimensions: E= 2KB(1/dn-1/di) KB: Bond’s work index and represents the variation in material properties and size reduction method Walker: proposed a generalized differential form of the energy-size relationship which links the upper 3 theories: әE = -k(әd/dn) d is size function that can be characterized by an integrated mean size or weight function n: is an exponent. When n= 1 Kick’s n=2 Rittinger’s n=3/2 Bond’s When designing a milling process for a given particles, the most appropriate energy relationship will be required to calculate energy consumption. It is found that the most appropriate values for n are 1 for coarse particles > 1µm (Kick’s type) n=2 for particles < 1µm (Rittinger’s type) n=3/2 is the average of the above 2 extremes and indicates a possible solution where neither Kick’s nor Rittinger’s theory is appropriater. The efficiency of the milling process is influenced by the nature of force as well as by its magnitude. The rate of application of force is imp. as there is a time lag between the attainment of max. force and fracture. Often materials respond as brittle to fast impact and as plastic to slow force. The greater the rate at which the force is applied, the less effectively the energy is utilized and the higher is the proportion of fine material produced. As the rate of milling is increased more energy is expended. To produce a new surface in milliseconds may require 3-4 times as much energy as the production of the same new surface area in seconds. INFLUENCE OF SIZE REDUCTION ON SIZE DISTRIBUTION During size reduction particles of feed material will undergo different ranges of breakage which leads to change in size distribution towards smaller particle diameter. Heywood showed that the initial normal distribution was transformed to a bimodal population The initial normal size distribution is transformed to bimodal population through differences in the fracture behaviour of coarse and fine particles. - If milling is continued a unimodal population reappears. - The lower particle size limit of a milling operation is dependent on the energy input and material properties. 1. Cutting Method Size reduction range: see fig Principle of operation: -stationary knives - rotating knives - screen High shear rates are useful to produce a coarse dried (powder) and fibrous crude drugs (eg.Roots) for extraction 2. Compression methods Size reduction range: see fig Principle of operation: - On small scale: mortar and pestle - End-runner and edge-runner mills are mechanized forms of mortar pestle - Size reduction occurs by attrition and compression. Alternative: Roller mill: 2 cylindrical rolls mounted horizontally one roll is rotated directly the other by 3.friction Impactduring milling. methods Size reduction range: see fig Principle of operation: a. Hammer mill: series of 4 or more hammers hinged on a central shaft enclosed in rigid metal case. The angular velocity produces a high strain rate to cause brittle fracture. Can produce narrow size range Particles are retained within the mill b. Vibration milling: Filled to 80% of its vol. With steel or porcelain balls During milling the whole body of mill is vibrated and size reduction occurs by repeated impaction. The comminuted particles fall through screen at the base of mill Its efficiency is greater than ball mill 4. Attrition methods Size reduction range: see fig Principle of operation: Roller mills: 2 or 3 metal or porcelain rolls are mounted horizontallye with adjustable gap (eg.20micron). The rolls rotate at different speeds so that the 5.material Combined is sheared impact in andbetween attrition Size reduction range: see fig. Principle of operation: Ball Mill: Consist of a hollow cylinder mounted such that it can be rotated on its horizontal longitu- dinal axis. - Cylinder diameter can be > 3m for large scale and 0.2m for small scale - Ball size depends on mill size. Ex. A mill of 1m diameter 75mm balls Mills usually contain balls with different diameters which helps to improve the product as the large balls tend to break down the coarse feed materials and the smaller balls helps to form the fine product by reducing void spaces between balls. Amount of material in mill is imp.: too much feed produces a cushioning effect and Speedtoooflittle causes rotation: is loss mostofimp. efficiency and abrasive wear of mill parts. A) At low angular velocities the balls move with the drum until the force due to gravity exceeds the frictional force of the bed on the drum then balls slide back to the base. This produce little movement of balls so that size reduction is minimal. B) At high angular velocity balls thrown on mill wall by centrifugal force and no size reduction occur. C) at 2/3 of angular velocity a cascading action produced max size reduction Fluid Energy (Jet) mill (micronizer) Consists of a hollow toroid of 20-200 mm diameter depending on loop hight A fluid (air) is injected as a high pressure jet from bottom nozzles. The high velocity of air gives rise to zones of turbulence which give particles high kinetic energy and lead to impact with each other and fracture. A particle size classifier removes the fine particles while retain the others until they sufficiently milled. SELECTION OF MILLING METHOD - Factors: - 1. The use of the product powder - 2. The cost: increase as size reduction increase - 3. properties of the material (hard, tough, friable, moisture content, m.pt. Flammability - 4. Size of the batch - 5. safety: toxicity, explosivity...