Mid Term Revision PDF
Document Details
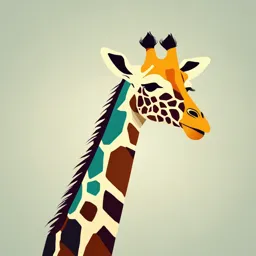
Uploaded by FastestIrony2202
NEOMA Business School
Tags
Summary
This document provides a review of operations management covering topics like goods and services, and productivity. It also includes analysis of operations strategies in a global environment.
Full Transcript
**1. Introduction to Operations Management** - **Definition**: Operations management involves designing, overseeing, and controlling the production processes and redesigning business operations to ensure efficiency. - **Key Concepts** : - **Goods vs. Services**: Understanding th...
**1. Introduction to Operations Management** - **Definition**: Operations management involves designing, overseeing, and controlling the production processes and redesigning business operations to ensure efficiency. - **Key Concepts** : - **Goods vs. Services**: Understanding the distinction between tangible products (goods) and intangible services. - **Productivity**: Measures of efficiency, formula: - **Operations Functions**: Includes production, quality control, inventory management, and supply chain logistics. - **Roles of an Operations Manager**: - Ensuring efficient processes - Managing resources - Balancing costs with customer satisfaction **2. Operations Strategy in a Global Environment** - **Operations Strategy**: Aligning operations with the broader business strategy to gain competitive advantage. - **Globalization**: Operations strategies must adapt to a global market, considering: - **Cultural differences** - **Global supply chain complexity** - **Regulations and compliance** - **Competitive Priorities**: - **Cost leadership**: Competing on low costs. - **Quality**: High-performance, durable goods, or services. - **Flexibility**: Ability to respond to changes in market demand. - **Delivery speed**: Faster processes to ensure prompt delivery. - **Sustainability**: - Focus on eco-friendly and socially responsible operations, including waste reduction and ethical labor practices. **3. Process Strategies and Capacity** - **Process Strategies**: Involves deciding how to organize the production process. **Types of Processes**: - **Job Shop**: Customized, low-volume products. - **Batch**: Producing goods in batches, suited for moderate-volume production. - **Repetitive (Assembly Line)**: Producing standardized goods in high volumes. - **Continuous**: High-volume, continuous production like chemicals, gas, etc. - **Capacity**: - **Definition**: Maximum output a system can produce. - **Capacity Planning**: Balancing capacity with demand to avoid under-utilization or overburdening. - **Key Formulas** : - **Capacity Utilization Rate**: Utilization Rate=Actual Output/Design Capacity×100 **4. Location Strategies** - **Importance of Location** : - Impacts costs, delivery time, labor availability, and customer satisfaction. - **Factors Affecting Location Decisions**: - **Proximity to Markets**: Closer to customers reduces transportation costs. - **Labor Availability**: Skilled vs. unskilled labor and wage costs. - **Infrastructure**: Availability of transportation, utilities, and communication networks. - **Government Regulations**: Tax incentives, zoning laws, and environmental regulations. - **Cost of Living**: Impacts labor costs and attractiveness to employees. - **Techniques** : - **Factor-Rating Method**: Assigning weights to factors affecting the location. - **Center-of-Gravity Method**: Finding a central location to minimize transportation costs. **5. Demand Forecasting** - **Definition**: Predicting future customer demand to plan for production, inventory, and staffing. - **Qualitative Forecasting Methods** : - **Expert Opinion**: Using expert knowledge or judgment. - **Delphi Method**: Group consensus using rounds of expert feedback. - **Market Research**: Customer surveys and focus groups. - **Quantitative Forecasting Methods** : - **Time Series Analysis**: - Moving Average=Sum of Demand in Previous n Periods / n - **Exponential smoothing:** - **Regression Analysis**: Forecasting demand based on the relationship between two or more variables. - **Forecast Accuracy**: - **Mean Absolute Deviation** - **Mean Squared Error** **Key Takeaways** - Operations management optimizes processes, improving productivity and reducing costs. - Strategies must align operations with global competition and sustainability. - Efficient process and capacity strategies are crucial for balancing demand with production. - Choosing the right location affects operational efficiency. - Accurate demand forecasting enables better decision-making for inventory, capacity, and staffing.