Injection Molding Materials PDF
Document Details
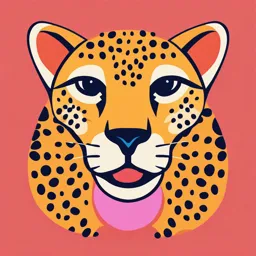
Uploaded by ResponsiveArtNouveau
Tags
Summary
This document provides a comprehensive overview of various materials used in injection molding, including steels, copper alloys, aluminum alloys, and others. It details their properties and applications, including how different materials are used for forming injection molds and cavity inserts. It also touches upon laser surface treatments for improving mold performance.
Full Transcript
P-20 Pre-hard steel (Rc 29-36): A common tool steel used for its durability and machining qualities....
P-20 Pre-hard steel (Rc 29-36): A common tool steel used for its durability and machining qualities. H-13 Air hard steel (Rc 46-54): Great for high production cavities and cores, slide bodies, lifters, and gibs. S-7 Air hard steel (Rc 54-56): Used for many of the same applications as H-13, but somewhat less stable and more prone to cracking. M-2 High speed steel (Rc 60-62): Used where tough rigidity is required, such as tall thin core pins or blades. 420 SS stainless steel (Rc 49-53): Best for Example Materials achieving high polish finishes and for The injection molding technique must corrosive polymers such as PVC. meet the ever-increasing demand for high- quality, economically-priced products. Beryllium Copper: Primarily used for inserting small areas in tools that may be Injection molds are expected to provide prone to overheating. reliable, fully repeatable function and a long service life to offset the high capital investment. 7075 T-6 Aluminum: Generally used for short-run or prototype tooling, but has good hardness, wear resistance, and Injection molds are almost exclusively polishing ability. made of high-strength metals, primarily Introduction steel. Lamina: A bronze over steel laminate material used for wear plates and large Cavity inserts made of materials other locking surfaces. than steel are used for cavities that are difficult to shape, often made by electrodeposition. Laser surface treatments are special Non-metallic materials are growing in finishing procedures that serve as an importance for prototype production due alternative to conventional hardening to fast production, low cost, and the ability techniques for increasing the service life to predict weaknesses and problems of molds with high component costs. during later production. Laser Surface Treatments Thermal: Laser hardening, laser remelting Laser surface treatments can be divided into two groups: Steel is the only material that guarantees Thermochemical: Laser alloying, laser reliably functioning molds with long dispersing, laser coating service life. The selection of the most suitable steel grade and proper heat treatment is crucial The goal of surface treatments is to to develop the required properties. improve surface quality, fatigue and wear resistance, corrosion resistance, sliding ability, and reduce the tendency to form Economical workability material residues and deposits in the mold. Capacity for heat treatment Thermal: Induction hardening, flame hardening, electron beam hardening, impulse hardening, deposit by welding, Sufficient toughness and strength armor plating Steel properties should include: Resistance to heat and wear Surface Treatments Thermochemical: Cementation, nitriding, carbonizing, boriding, sulfidization, High thermal conductivity oxidizing, flame spraying, explosion coating Corrosion resistance Electrochemical: Hard-chromium plating, The most common surface treatments for Case-hardening steels best meet the nickel plating mold steels include: qualifications for mold making, accounting for about 80% of the total steel used. Mechanical: Jet lapping, pressure Comprehensive polishing, rolling Summary of Through case hardening, carburization, or cementization, a mold surface as hard as Depositing in gaseous phase: Chemical Injection Mold glass is generated along with a tough and ductile core. Materials and vapor deposition (CVD), physical vapor Case-Hardening Steels deposition (PVD) Surface Case-hardening steels offer advantages such as ease of machining, good polishing, Copper alloys, such as beryllium copper- Treatments low strength after low-temperature annealing, suitability for hobbing, and cobalt alloys, are important materials for suitability for small cavities and multi- mold cavities due to their high tensile cavity molds. strength, hardness, ductility, polishability, corrosion resistance, and insensitivity to thermal shock. Nitriding is a heat treating process that Copper Alloys diffuses nitrogen into the surface of a steel to create a case-hardened surface. High-grade zinc alloys are used for prototype molds or small production runs Nitriding provides the steel with an due to their inferior mechanical properties, extraordinarily hard and wear-resistant but they are more frequently utilized for surface with a Brinell hardness between blow molding or vacuum forming. 600-800. Zinc and its Alloys Aluminum alloys have gained more use in Advantages of nitriding steels include no recent times due to improvements in their Nitriding Steels need for heating, quenching or annealing, mechanical properties, particularly their freedom from distortion, retention of low density, good machinability, high hardness up to 500°C, and suitability for thermal conductivity, and corrosion processing thermosets and high- resistance. temperature thermoplastics. Non-Ferrous Metallics Aluminum is not suitable for processing Aluminum Alloys Disadvantages include the risk of the hard thermosets due to the high processing layer peeling off under high surface temperatures and associated thermal pressure. stress. Through-hardening steels increase their Bismuth-tin alloys are relatively soft, hardness by the formation of martensite, heavy metals that react to shock in a which results from rapid quenching. brittle manner but exhibit plasticity under constant loading. The hardening process involves preheating, heating to a prescribed They are primarily used for prototype temperature, quenching with formation of molds in injection molding, as well as for a hard martensitic structure, and blow molds, molds for hot forming, high- Bismuth-Tin Alloys Steels normalizing to improve toughness. precision matrices in electrolytic depositing, and as a material for fusible cores. Through-Hardening Steels Through-hardening steels exhibit very good dimensional stability, high compressive strength, good wear resistance, and suitability for molds with shallow cavities and insert molding. Cast steel is a ferrous alloy with a maximum carbon content of approximately 0.75%. However, they have lower toughness, making them more prone to cracking in molds with deep cavities. The production of molds from cast steel is less expensive than forged or rolled steel, Cast Steel as it allows for greater design flexibility These steels are tempered by the and complex shapes with hollow cross- manufacturer and can be used as supplied sections. without further heat treatment. Tempering reduces hardness and strength Heat-Treated Steels while increasing ductility and toughness. Heat-treated steels are preferred for medium-sized and large molds, as corrections are more easily accomplished after a trial run. Martensitic steels combine extreme strength and hardness with the advantage of simple heat treatment. Their structure consists of tough nickel martensite with a strength of 1000-1150 Martensitic Steels MPa. They are recommended for smaller cavity inserts with complex contours and large differences in cross sections or detached thin flanges, as other steel grades would result in distortion. Hard mold alloys are produced by a powder metallurgical process, resulting in a steel matrix with small carbides. They have extremely high wear resistance Hard Mold Alloys due to their high carbide content (50 vol%) and are suitable for processing wear- promoting compounds and various tool parts subjected to increased wear. Corrosion-resistant steels are produced by alloying with chromium to protect the mold against corrosion from chemically aggressive substances released during polymer processing. Corrosion-Resistant Steels Complicated geometries make it difficult to apply uniform protective electroplating coatings, making corrosion-resistant steel a better option. Refined steels are the purest steels currently available, allowing for better polishing and higher surface quality of the mold, particularly important for transparent articles such as lenses. Refined Steels