Maintenance Policies and RCM (Reliability Centered Maintenance) PDF
Document Details
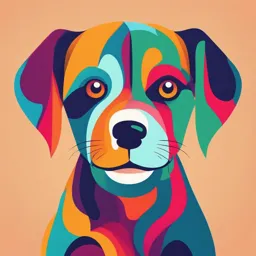
Uploaded by AltruisticMossAgate8880
Jordan University of Science and Technology
Tags
Related
- Fresno City Fire Department Apparatus Maintenance PDF
- Consolidation of Policies of Operation Divisions (2024-2024)
- DS2: Stratégie de Maintenance PDF
- DS2 : Stratégie de Maintenance - BTS La maintenance
- Spring Fire Department Vehicle Use Policy PDF
- Chapitre 2 - Politiques (Méthodes) de la Maintenance - ENSAT-2022 PDF
Summary
This document describes Reliability Centered Maintenance (RCM) principles, goals, and steps. It covers how to assess critical failures, apply decision-making logic, and categorize maintenance requirements in industrial settings. It also discusses applying sustaining engineering based on field experience.
Full Transcript
Reliability and Maintenance Management Reliability Centered Maintenance RCM Dr. Hazem Smadi Dr. Nader Al Theeb Reliability Centered Maintenance RCM RCM is a systematic methodology used to identify the preventive maintenance– related...
Reliability and Maintenance Management Reliability Centered Maintenance RCM Dr. Hazem Smadi Dr. Nader Al Theeb Reliability Centered Maintenance RCM RCM is a systematic methodology used to identify the preventive maintenance– related tasks necessary for realizing the inherent reliability of equipment at the lowest cost. Any organization can benefit from RCM if its breakdowns account for more than 20 to 25% of the total maintenance workload. RCM Goals To develop design-associated priorities that can facilitate PM. To gather information useful for improving the design of items with proven unsatisfactory, inherent reliability. To develop PM-related tasks that can reinstate reliability and safety to their inherent levels in the event of equipment or system deterioration. To achieve the above goals when the total cost is minimal. RCM Principles RCM Principles ❖ RCM is system/equipment focused: RCM is concerned more with maintaining system function as opposed to maintaining individual component function. ❖ Safety and economics drive RCM: Safety is of paramount importance, thus it must be ensured at any cost and then cost effectiveness becomes the criterion. ❖ RCM is function-oriented: RCM plays an instrumental role in preserving system/equipment function, not just operability for its own sake. RCM Principles ❖ Design limitations are acknowledged by RCM: The goal of RCM is to maintain the inherent reliability of the equipment/system design and at the same time recognize that changes in inherent reliability can only be made through design rather than maintenance. Maintenance at the best of times can only achieve and maintain a level of designed reliability. ❖ RCM is reliability-centered: RCM is not overly concerned with simple failure rate, but it places importance on the relationship between operating age and failures experienced. RCM treats failure statistics in an actuarial fashion. RCM Principles ❖ An unsatisfactory condition is defined as a failure by RCM: A failure could be either a loss of acceptable quality or a loss of function. ❖ RCM is a living system: RCM collects information from the results achieved and feeds it back to improve design and future maintenance. ❖ Three types of maintenance tasks along with run-to-failure are acknowledged by RCM. These tasks are defined as failure- finding, time-directed, and condition-directed. The purpose of the failure-finding tasks is to discover hidden functions that have failed without providing any indication of pending failure. Time-directed tasks are scheduled as considered necessary. Condition-directed tasks are conducted as the conditions indicate for their need. Run-to-failure is a conscious decision in RCM. RCM Principles ❖ RCM tasks must be effective: The tasks must be cost-effective and technically sound. ❖ RCM uses a logic tree to screen maintenance tasks: This provides consistency in the maintenance of all types of equipment. ❖ RCM tasks must be applicable: Tasks must reduce the occurrence of failures or ameliorate secondary damage resulting from failure. RCM PROCESS AND ASSOCIATED QUESTIONS What are the functions and associated expected levels of the facility performance in its current operating context? How might it fail to meet its assigned functions? What are the reasons for each functional failure or failure mode? What are the effects of each failure? How does each failure matter? What remedial measures should be taken to prevent or predict each failure? What measures should be taken in the event of not finding a suitable proactive task? RCM Steps 1. Identify important items with respect to maintenance. Usually, maintenance important items are identified using techniques such as failure, mode, effects, and criticality analysis (FMECA) and fault tree analysis (FTA). 2. Obtain appropriate failure data. In determining occurrence probabilities and assessing criticality, the availability of data on part failure rate, operator error probability, and inspection efficiency is essential. These types of data come from field experience, generic failure databanks, etc. Many sources for obtaining failure data are listed in Reference 16. 3. Develop fault tree analysis data. Probabilities of occurrence of fault events— basic, intermediate, and top events—are calculated as per combinatorial properties of the logic elements in the fault tree. 4. Apply decision logic to critical failure modes. The decision logic is designed to lead, by asking standard assessment questions, to the most desirable preventive maintenance task combinations. The same logic is applied to each crucial mode of failure of each maintenance-important item. 5. Classify maintenance requirements. Maintenance requirements are categorized into three classifications: on condition maintenance requirements, condition-monitoring maintenance requirements, and hard-time maintenance requirements. 6. Implement RCM decisions. Task frequencies and intervals are set/enacted as part of the overall maintenance strategy or plan. 7. Apply sustaining-engineering on the basis of field experience. Once the system/equipment start operating, the real-life data begin to accumulate. At that time, one of the most urgent steps is to re-evaluate all RCM-associated default decisions.