Lesson 1: Introduction to Total Quality Management PDF
Document Details
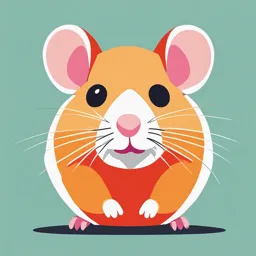
Uploaded by CoolestCurium
University of Peshawar
Saif Ullah Khan
Tags
Related
- Total Quality Management PDF
- Quality Service Management in Tourism & Hospitality PDF
- Introduction to Operations Management & Total Quality Management PDF
- Introduction to Operations Management and Total Quality Management PDF
- Chapter 6 Quality Management PDF
- Chapter 3: Gurus of Total Quality Management PDF
Summary
This document is a lesson on total quality management (TQM), covering definitions, basic approaches, gurus, frameworks, dimensions of quality, obstacles, and Deming's philosophy. The document is from the University of Peshawar in Pakistan.
Full Transcript
LESSON 01: INTRODUCTION TO TOTAL QUALITY MANAGEMENT SAIF ULLAH KHAN IMS – UNIVERSITY OF PESHAWAR DEFINITION Total Made up of the whole Quality Fitness to Purpose Getting things done with and through Management people. “Management of the whole Def...
LESSON 01: INTRODUCTION TO TOTAL QUALITY MANAGEMENT SAIF ULLAH KHAN IMS – UNIVERSITY OF PESHAWAR DEFINITION Total Made up of the whole Quality Fitness to Purpose Getting things done with and through Management people. “Management of the whole Definition organization to achieve a fitness to purpose". BASIC APPROACH 1. A committed and involved management to provide long term top to bottom organizational support. 2. An unwavering focus on customers, both internally and externally. 3. Effective involvement and utilization of the entire workforce. 4. Continuous improvement of the business and production processes. 5. Treating suppliers as partners. 6. Establish performance measures for the processes. GURUS OF TQM Name Contribution Walter Shewhart Spent his career in Western Electrics and Bell Telephone Laboratories Developed Control Chart Theory Developed PSDA Cycle Book: Economic Control of Quality of Manufactured Products Ronald Fisher Developed Design of Experiments Developed the ANOVA technique Books: Statistical Method for the Research Worker Design of Experiments Edward Deming Deming’s 14 Principles Books: Out of Crisis Quality, Productivity and Competitive Position Joseph Juran Juran’s Trilogy. Book: Juran’s Quality Control Handbook Armand Put customer satisfaction at the forefront of quality management Feigenbaum Book: Total Quality Control Kaoru Ishikawa Statistical Process Control Ishikawa Diagram Philip Crosby Zero Defects, do it right for the first time Books: Quality is Free Quality without tears Genichi Taguchi Developed Loss Function “that combines cost, target and variation into one metric”. Taguchi Quality Engineering TQM FRAMEWORK DIMENSIONS OF QUALITY Dimensions Meaning and Example Performance Primary Product Characteristics, such, as the mobile’s ability to send and receive signals. Features Secondary Characteristics of a product, such, camera on a mobile. Conformance Meeting specifications and Industry Standards, such, USB 2.0 Reliability Consistent performance over time, such, same quality of food at a restaurant Durability Useful life of a product, such, the number of kilometers a marker can write Service Resolution of problems and complaint, such, Jockey 777 vs Singer Interaction Human to human interface, such, the courtesy of the Waiter Aesthetics Sensory Characteristics , such, Color and design Reputation Past performance and other intangibles, such, Ranked Number 1, since 1972 OBSTACLES 1. Lack of Management Commitment 2. Inability to Change Organizational Culture 3. Improper Planning 4. Lack of Continuous Training and Education 5. Incompatible Organizational Structure and Isolated Individuals and Departments 6. Ineffective Management Techniques and Lack of Access to Data and Results 7. Paying Inadequate Attention to External and Internal Customers 8. Inadequate Use of Empowerment and Teamwork 9. Failure to Continually Improve This Photo by Unknown author is licensed under CC BY-SA-NC DEMING’S PHILOSOPHY 1. Create and Publish the Aims and Purposes of the Organization. 2. Learn the new Philosophy 3. Understand the purpose of inspection 4. Stop awarding business based on price alone 5. Improve constantly and forever the system 6. Institute Training 7. Teach and Institute Leadership 8. Drive out fear, Create Trust, and Create a Climate for Innovation 9. Optimize the Efforts of Teams, Groups and Staff Areas 10. Eliminate Exhortation for Workforce 11. Eliminate Numerical Quotas and MBO 12. Remove Barriers that rob people of pride of workmanship (next slide) 13. Encourage education and self-improvement for everyone 14. Take action to accomplish the transformation This Photo by Unknown author is licensed under CC BY-SA BARRIERS TO PRIDE IN WORKMANSHIP 1. Workers do not know how to relate to the organization’s mission. 2. They are being blamed for system problems. 3. Poor design leads to the production of “Junk” 4. Inadequate Training 5. Punitive Supervision 6. Inadequate or ineffective equipment is provided This Photo by Unknown author is licensed under CC BY-SA-NC