Tablet Manufacturing Lecture Notes PDF
Document Details
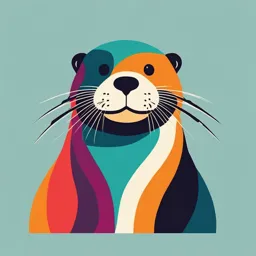
Uploaded by GallantAmericium2685
2024
Tags
Related
- Crystal Properties and Tablet Compaction PDF
- Manufacturing Pharmacy M5.4 PDF
- L1. Introduction to Solid Pharmaceutical Formulations (AY24/25.S1)
- Sesión de Aprendizaje 06 - Buenas Prácticas de Elaboración, rotulado y Envasado de Fármacos y Productos Orales PDF
- Tablet Dosage Form PDF
- Industrial Pharmacy Lec 2 PDF
Summary
This document is a lecture or presentation on tablet manufacturing. It covers various methods like direct compression, wet granulation, and dry granulation, and details the processes involved and associated advantages and disadvantages.
Full Transcript
Tablet manufacturing https://www.youtube.com/watch?v=Ls6YEw0I7QY 10/20/2024 1 Tablet manufacturing The tablet is made by compressing a carefully formulated mixture of drug and excipients in a cylindrical steel die between steel punches (pre...
Tablet manufacturing https://www.youtube.com/watch?v=Ls6YEw0I7QY 10/20/2024 1 Tablet manufacturing The tablet is made by compressing a carefully formulated mixture of drug and excipients in a cylindrical steel die between steel punches (pressure is typically 5-10 tons per square centimetre) Methods of tablet manufacturing: Direct compression Wet granulation Dry granulation (preliminary compression) 10/20/2024 2 Generally, tablet formulation consists of following main processes: 1. weighing , mixing 2. Granulation 3. Milling and mixing 4. Compression 10/20/2024 3 Mixing Mixing allows uniform distribution of tablet constituents throughout the formulation Allows for adequate distribution of lubricants around tablet granules. Mixing step should be validated in a way that adequate mixing is obtained 10/20/2024 4 Direct compression The term “direct compression” is defined as the process by which tablets are compressed directly from powder mixture of API and suitable excipients. It involves only two unite operations: powder mixing and tabletting. 10/20/2024 5 Advantages of Direct Compaction: Reduced production time &cost. product stability can be improved. less number of equipment are required Elimination of heat and moisture, thus increasing the stability and the suitability of the process for thermolabile and moisture sensitive API’s. The chances of batch-to-batch variation are negligible 10/20/2024 6 Disadvantages of Direct Compaction 1. Many active ingredients are not compressible either in crystalline or amorphous forms. 2. Needs directly compressible filler that is usually expensive, e.g. microcrystalline cellulose (Avicel), spray dried lactose 3. Problems in the uniform distribution of low dose drugs. 4. High dose drugs having high bulk volume, poor flowability and poor compressibility are not suitable for direct compression. For example, Aluminium Hydroxide, Magnesium Hydroxide 5. Non-uniform distribution of color, especially in tablets of deep colors 10/20/2024 7 Granulation https://www.youtube.com/watch?v=wbuC6bpWQM8 10/20/2024 8 Wet Granulation Reasons for granulation Improve flowability Improve mixing homogeneity and reduce segregation Improve compactability by adding a binder Ensure a homogeneous colour Affect the dissolution process for hydrophobic poorly soluble particles by using a hydrophilic binder Avoid the hazard of generation of toxic dust. 10/20/2024 9 WG Process description It involves massing of a mix of dry primary powder particles using a granulating fluid. Once the granulating liquid has been added, mixing continues until uniform dispersion is attained (15 min. to an hour). The fluid contain a solvent that must be volatile and non- toxic e.g water, or organic solvent. The granulating solvent may contain a binding agent to ensure particle adhesion after drying. Poly vinyl pyrolidone (PVP) is dissolved in water or solvent and added to the process. 10/20/2024 10 The moist mass is broken up into coarse, granular aggregates (using screens with large perforations). The purpose is to increase surface area to facilitate removal of moisture. Mixing with other tablet excipients (lubricant, glidant, remaining of disintegrant) and then compaction. 10/20/2024 11 Typical liquids include 1. Water : may adversely affect drug stability, causing hydrolysis, it needs a longer drying time. The advantage: non-flammable and economic. 2. Ethanol, Isopropanol ,or combination (organic solvents) used with water sensitive drugs, when rapid drying time is required. 10/20/2024 12 Dry Granulation The dry granulation process is used to form granules without using a liquid solution because the product to be granulated may be sensitive to moisture and heat. In this process the primary powder particles are aggregated under high pressure. 10/20/2024 13 Methods of dry granulation A. Slugging technique The blend of finely divided powders is forced into the dies of a large capacity tablet press. Then, compacted by means of flat faced punches (Compacted masses are called slugs and the process is slugging) 10/20/2024 14 B. Roll compactor to produce sticks or sheets. Slugs or sheets are then milled/screened to produce granules (flow more than the original powder mixture). 10/20/2024 15 Tablet press 1- Single Punch press (Eccentric Press): bench-top models that make one tablet at a time (single- station presses) Disadvantages: Production of small batches of tablets (200 tablets per minute). 10/20/2024 16 2- Rotary Press ( Multi station Press): It was developed to increase the output of tablets (10 000 tablets per minute), used for Large scale production. It consists of a number of dies and sets of punches The dies are mounted in a circle in the die table and both the die table & the punches rotate together during operation of the machine. 10/20/2024 17 Tablet Compression Machine 1. Hopper(s) for holding and feeding tablet component 2. Dies that define the size and shape of the tablet 3. Punches for compressing the granulation within the dies 4. Cam tracks for guiding the movement of the punches 10/20/2024 18 10/20/2024 19 Caplet Shape Dies Star Shapes Dies Oval Shapes Dies Round Shapes Dies 10/20/2024 20 Tablet compression process 10/20/2024 21 Granulation technology by various technique 10/20/2024 22 Table 1. Typical unit operation involved in Wet granulation, Dry granulation and Direct compression Wet granulation Dry granulation Direct compression Milling and mixing of drugs and Milling and mixing of drugs and Milling and mixing of excipients excipients drugs and excipients Preparation of binder solution Compression into slugs or roll Compression of tablet compaction Wet massing by addition of Milling and screening of slugs and binder solution or granulating compacted powder solvent Screening of wet mass Mixing with lubricant and disintegrant Drying of the wet granules Compression of tablet Screening of dry granules Blending with lubricant and disintegrant to produce Compression of tablet 10/20/2024 23 Tablet coating Coating is the process by which a dry outer layer of coating material is applied to the surface of the tablet Why? Protect drug from destructive exposure to humidity and/or air To mask the taste of the drug To provide easiness of swallowing for patients To provide special characteristics of drug release (e.g., enteric coating) To provide distinction and appealing to the product by colouring To enable easier handling 10/20/2024 24 Coating types: Sugar coating Film coating Enteric coat 10/20/2024 25 Sugar coating Involve many processes: sealing, drying, sub-coating , smoothing , colouring, imprinting and polishing Processes are conducted in a series of mechanically operated coating pans of stainless steel During operation, pan is rotated while making contact with the coating solution which is sprayed or poured gently and in portions Disadvantages: time consuming (8 hours), require expertise of skilled technician, it results in almost twice the size of the original tablet and may have weight and size variation 10/20/2024 26 Fluid bed coating and pan coating 10/20/2024 27 Fluid bed coating and pan coating 10/20/2024 28 Film coating It places a thin, skin-tight coating of a plastic like material over the compressed tablet by spraying method It is the most common used type of coating Classification: Immediate-release film coating Modified-release film (delayed-release or enteric film coating) Advantages: Usually one stage Less time (1.5-2 hours) Does not change the size and weight of tablet Can control the release of the drug More resistant to destruction compared to sugar coating 10/20/2024 29 Modified release film coating (Enteric coat) Is intended to pass through the stomach intact to disintegrate and release the drug content for absorption in the intestines How it can be achieved? Coating of sufficient thickness Usually through applying coating that resist dissolution in high acidic medium (stomach) but dissolving in less acid environment of pH = 6 and greater (intestines) Examples: hydroxypropyl methylcellulose phthalate and polyvinyl acetate phthalate 10/20/2024 30