Productivity Lecture Notes PDF
Document Details
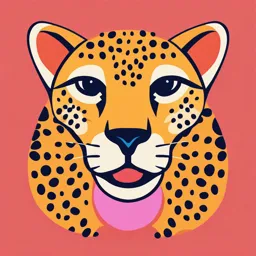
Uploaded by QuaintMesa
Valerie Jane Osuna, Harold Magallanes, Olivia ysip
Tags
Related
- Operations Management: Competitiveness, Strategy, and Productivity PDF
- Chapter 02: Competitiveness, Strategy & Productivity - BUS 2501 PDF
- FINALFINALS3 PDF - Competitiveness and Productivity Update
- OM Teaching Slides - Operations Management Term 1 2024-2025 PDF
- Chapter 15: Managing Operations, Quality, and Productivity PDF
- Operations Management: Creating Value Along the Supply Chain - PDF
Summary
This lecture covers productivity concepts, types of productivity measures, and calculations. It details partial, multifactor, and total factor productivity. Examples of productivity calculations and various applications are included.
Full Transcript
Productivity Compiled by: Valerie Jane Osuna, Harold Magallanes and Olivia ysip Key Ter ms: ❖ Competitiveness – how effectively an organization meets the wants and needs of customers relative to others that offer similar goods or services....
Productivity Compiled by: Valerie Jane Osuna, Harold Magallanes and Olivia ysip Key Ter ms: ❖ Competitiveness – how effectively an organization meets the wants and needs of customers relative to others that offer similar goods or services. ❖ Mission – the reason for the existence of an organization. ❖ Mission statement – states the purpose of an organization. ❖ Goals – provide detail and scope of the mission. ❖ Strategies – plans for achieving organizational goals. ❖ Tactics – the methods and actions taken to accomplish strategies. ❖ Core competencies – are the special attributes or abilities possessed by an organization that give it a competitive edge. ❖ SWOT – analysis of strengths, weaknesses, opportunities, and threats. Key Ter ms: ❖ Order qualifiers – characteristics that customers perceive as minimum standards of acceptability to be considered as a potential for purchase. ❖ Order winners – characteristics of an organization’s goods or services that cause it to be perceived as better than the competition. ❖ Environmental scanning – the monitoring of events and trends that present threats or opportunities for a company. ❖ Operational strategy – the approach, consistent with the organization strategy, that is used to guide the operations function. ❖ Quality-based strategies – strategy that focuses on quality in all phases of an organization. ❖ Time-based strategies – strategy that focuses on reduction of time needed to accomplish tasks. Productivity A measure of how efficiently inputs are being converted into outputs. Productivity is the value of outputs (services and products) produced divided by the values of input resources (wages, cost of equipment, and so on) used. The more efficiently a company uses its resources, the more productive it is: Productivity = output input Current productivity – Previous productivity ❖ Productivity growth = X 100 Previous productivity For ex a mpl e, if p r od uc t i vi t y i n cr ea sed fr om 8 0 t o 8 4, th e g ro wth r ate wou l d b e: 84 – 80 Productivity growth = X 100 80 Productivity growth = 5% ❖ Different Types of Productivity Measures: ① Partial measures ② Multifactor measures ③ Total measure Measures of Productivity 1. Single-factor productivity - (Partial productivity) - Productivity computed as a ratio of output to only one input (e.g., labor, materials, machines). Following are two examples of the calculation of partial productivity: a. A bakery oven produces 345 pastries in 4 hours. What is its productivity? Machine productivity = number of pastries/oven time = 345 pastries / 4 hours = 86.25 pastries/hour b. Two workers paint tables in a furniture shop. If the workers paint 30 tables in 7 hours, what is their productivity? Labor productivity = 30 tables / 2 workers’ / 7 hours = 2.14 tables/hour ❑ Partial Productivity Measures ❖ Some Examples of Partial Productivity Measures: ③ Capital Productivity Units of output per dollar input Dollar value of output per dollar input ④ Energy Productivity Units of output per kilowatt-hour Dollar value of output per kilowatt-hour ❖ The units of output used in productivity measures depend on the type of job performed. Examples of labor productivity: Yards of carpets installed = Yards of carpets installed per labor hour Labor hours Number of motel rooms cleaned = Number of motel rooms cleaned Number of workers per worker Measures of Productivity 2. Multifactor productivity relates output to a combination of inputs, such as (labor + capital) or (labor + capital + energy + materials). is an index of the output provided by more than one of the resources used in production; it may be the value of the output divided by the sum of labor, materials, and overhead costs. For example, let’s say that output is worth $382 and labor and materials costs are $168 and $98, respectively. A multifactor productivity measure of our use of labor and materials would be: Multifactor productivity = output / labor + materials = 382 / 168 + 98 = 1.436 output per dollar Measures of Productivity 3. Total factor productivity compares the total quantity of goods and services produced with all the inputs used to produce them. Productivity computed as a ratio of output to all organizational inputs. For example, let’s say that the weekly dollar value of a company’s output, such as finished goods and work in progress, is $10,200 and that the value of its inputs, such as labor, materials, and capital, is $8600. The company’s total weekly productivity would be computed as follows: Total productivity = output / input = $10,200 / $8600 = $ 1.186 Examples of Productivity Measures Interpreting Productivity Measures For example, if one worker at a pizza shop produces 17 pizzas in two hours, the productivity of that worker is 8.5 pizzas per hour. This number by itself does not tell us very much. However, if we compare it to the productivity of two other workers, one who produces 7.2 pizzas per hour and another 6.8 pizzas per hour, it is much more meaningful. We can see that the first worker is much more productive than the other two workers. ❖ Productivity measures are useful on several levels: ① In business organizations, productivity ratios are used for a) planning workforce requirements b) scheduling equipment c) financial analysis d) other important tasks ② For an individual department or organization, productivity measures can be used to track “performance over time”. This allows managers to judge performance and to decide where improvements are needed. ❖ Productivity measures are useful on several levels: ③ Productivity measures also can be used to judge the performance of an entire industry or the productivity of a country as a whole. These productivity measures are aggregate measures. ④ Productivity measurements serve as scorecards of the effective use of resources. Productivity and the Service Sector Service sector companies have a unique challenge when trying to measure productivity. Services primarily produce intangible products, such as ideas and information, making it difficult to evaluate quality. Consequently, accurately measuring productivity improvements can be difficult. Productivity and Competitiveness Productivity is essentially a scorecard of how efficiently resources are used and a measure of competitiveness. Productivity can be measured for individuals, departments, or organizations. Competitiveness - the degree to which a nation can produce goods and services that meet the test of international markets. ❖ Co n dit ion s T h at C au se Hig h R iv alr y A mo n g Com pet in g Fir m s ❖ 1. When the number of competing firms is high 2. When competing firms are of similar size 3. When competing firms have similar capabilities 4. When the demand for the indust ry’s product s is falling 5. When the product or service prices in the industry is falling 6. When consumers can switch brands easily 7. When barriers t o leaving the market are high 8. When barriers t o entering t he market are low 9. When fixed costs are high among compet ing firms 10. When the product is perishable 11. When rivals have excess capacity 12. When consumer demand is falling 13. When rivals have excess invent ory 14. When rivals sell similar products/services 15. When mergers are common in the industry Competition within Industries Increases when: Measures of Competitiveness (among different nations) M a j o r I n f l u e n c e o f O p e r a t i o n s o n C o m p e ti t i v e n e s s : ① Product and service design Should reflect joint efforts of many areas of the firm to achieve a match between financial resources, operations capabilities, supply chain capabilities, and consumer wants and needs. ② Cost of an organization’s output Is a key variable that affects pricing decisions and profits. ③ Location Can be important in terms of cost and convenience for customers. Location near inputs can result in lower input costs. Location near markets can result in lower transportation costs and quicker delivery times. M a j o r I n f l u e n c e o f O p e r a t i o n s o n C o m p e ti t i v e n e s s : ④ Quality Refers to materials, workmanship, design, and service. ⑤ Quick response ≫ is quickly bringing new or improved products or services to the market, ≫ is being able to quickly deliver existing products and services to a customer after they are ordered, ≫ is quickly handling customer complaints. ⑥ Flexibility The ability to respond to changes. M a j o r I n f l u e n c e o f O p e r a t i o n s o n C o m p e ti t i v e n e s s : ⑦ Inventory management Can be a competitive advantage by effectively matching supplies of goods with demand. ⑧ Supply chain management Involves coordinating internal and external operations (buyers and suppliers) to achieve timely and cost-effective delivery of goods throughout the system. ⑨ Service ≫ might involve after-sale activities customers perceive as value- added, such as delivery, setup, warranty work, and technical support. M a j o r I n f l u e n c e o f O p e r a t i o n s o n C o m p e ti t i v e n e s s : ⑨ Service ≫ it might involve extra attention while work is in progress, such as courtesy, keeping the customer informed, and attention to details. ⑩ Managers and workers These are the people at the heart and soul of an organization, and if they are competent and motivated, they can provide a distinct competitive edge by their skills and the ideas they create. Competitive Capabilities - are the cost, quality, time, and flexibility dimensions that a process or supply chain actually possesses and is able to deliver. nine broad competitive priorities that fall into the four capability groups: Low-cost Operations Consistent Quality Delivery Speed Volume Flexibility Definitions, process considerations, and examples of competitive priorities; Definitions, process considerations, and examples of competitive priorities; Definitions, process considerations, and examples of competitive priorities; ❖ Seatwork # 1: Productivity Computation Determine the productivity for these cases: a) Four workers installed 720 square yards of carpeting in eight hours. b) A machine produced 70 pieces in two hours. However, two pieces were unusable. *** Show your solution. ❖ Seatwork # 1: Productivity Computation Determine the multifactor productivity for the combined input of labor and machine time using the following data: Output: 7,040 units Input: Labor: $ 1,000 Materials: $ 520 Output: $ 2,000 *** Show your solution. End of the Slide Thank you and God Bless