Lab 1 – Introduction to Industrial Automation and PLCs PDF
Document Details
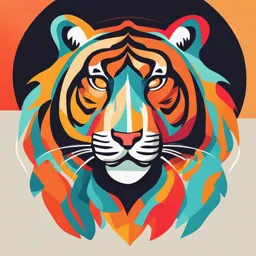
Uploaded by WellMadeAnecdote
UET Lahore
Tags
Summary
This document is a lab manual for an undergraduate course on industrial automation and programmable logic controllers (PLCs). It introduces the concepts of industrial automation and covers the basics of PLCs, including their history, functionality, and applications. It also includes exercises and tasks relating to digital logic design. The document is part of an undergraduate mechatronics engineering course at UET Lahore.
Full Transcript
Lab 1 –Introduction to Industrial Automation and PLCs Name : Date : Regd-No : OBJECTIVES: To get an idea of what Industrial Automation is To have a basic introduction of PLCs...
Lab 1 –Introduction to Industrial Automation and PLCs Name : Date : Regd-No : OBJECTIVES: To get an idea of what Industrial Automation is To have a basic introduction of PLCs Revise few concepts of Digital Logic Design EQUIPMENT AND COMPONENTS: None INDUSTRIAL AUTOMATION Automation is the use of machines, control systems and information technologies to optimize productivity in the production of goods and delivery of services. The correct incentive for applying automation is to increase productivity, and/or quality beyond that possible with current human labor levels so as to realize economies of scale, and/or realize predictable quality levels. PROGRAMMABLE LOGIC CONTROLLERS (PLCs) First Programmable Logic Controller (PLC) was developed by the engineers at General Motors in 1968. Initially PLC was an alternative to complex relay control systems. Any new control system had to meet the following requirements: Simple programming Program changes without system intervention (no internal rewiring) Smaller, cheaper and more reliable than corresponding relay control systems Simple, low cost maintenance In late 80’s process visualization, analogue processing or even the use of a PLC as a controller, were considered as Utopian. Nowadays not only these but various other processes forms the MCT 319- Industrial Automation, Department of Mechatronics and Control Engineering, UET Lahore integral part of the PLCs. Reduction of required memory capacity for program storage initially was a problem but due to advancement of technology it’s not a problem anymore. Also the range of built-in functions available has grown considerably. Controllers can be divided into pneumatic, hydraulic, electrical, electro-mechanical and electronic controller. Differentiation should be made between hard-wired programmable (e.g. wiring of electro-mechanical or electronic components) and programmable logic controllers. The first is used primarily in cases, where any reprogramming by the user is out of the question and the job size warrants the development of a special controller. Typical applications for such controllers can be found in automatic washing machines, video cameras, and cars. However, if the job size does not warrant the development of a special controller or if the user is to have the facility of making simple or independent program changes, or of setting timers and counters, then the use of a universal controller, where the program is written to an electronic memory, is the preferred option. The PLC represents such a universal controller. It can be used for different applications and, via the program installed in its memory, provides the user with a simple means of changing, extending and optimizing control processes. The original task of a PLC involved the interconnection of input signals according to a specified program and, if "true", to switch the corresponding output. Boolean algebra forms the mathematical basis for this operation, which recognizes precisely two defined statuses of one variable: "0" and "1". Accordingly, an output can only assume these two statuses. For instance, a connected motor could therefore be either switched on or off, i.e. controlled. This function has coined the name PLC: Programmable logic controller, i.e. the input/output behavior is similar to that of an electromagnetic relay or pneumatic switching valve controller; the program is stored in an electronic memory. However tasks of a PLC have rapidly multiplied: Timer and counter functions, memory setting and resetting, mathematical computing operations all represent functions, which can be executed by practically any of today’s PLCs. Very soon, it also became necessary to interconnect and harmonize individual systems controlled via PLC by means of automation technology. Hence a master computer facilitates the means to issue higher-level commands for program processing to several PLC systems The networking of several PLCs as well as that of a PLC and master computer is affected via special communication interfaces. To this effect, many of the more recent PLCs are compatible with open, standardized bus systems, such as Profibus to EN 50170. Thanks to the enormously increased performance capacity of advanced PLCs, these can even directly assume the function of a master computer. At the end of 70’s, addition of analogue inputs and outputs to the PLC expanded its market by many folds, since many of today’s technical applications require analogue processing (force measurement, speed setting, and servo-pneumatic positioning systems). The term ’programmable logic controller’ is defined as follows by EN 61131-1 (IEC 61131-1): A digitally operating electronic system, designed for use in an industrial environment, which uses a programmable memory for the internal storage of user-oriented instructions for implementing specific functions such as logic, sequencing, timing, counting and arithmetic, to control, through digital or analogue inputs and outputs, various types of machines or processes. MCT 319- Industrial Automation, Department of Mechatronics and Control Engineering, UET Lahore Both the PC and its associated peripherals are designed so that they can be easily integrated into an industrial control system and easily used in all their intended functions." The program of a PLC can be created in various ways: via assembler type commands in ’statement list’, in higher-level, problem-oriented languages such as structured text or in the form of a flow chart such as represented by a sequential function chart. In Europe, the use of function block diagrams based on function charts with graphic symbols for logic gates is widely used. In America, the ’ladder diagram’ is the preferred language by users. Depending on how the central control unit is connected to the input and output modules, differentiation can be made between compact PLCs (input module, central control unit and output module in one housing) or modular PLCs. Modular PLCs may be configured individually. The modules required for the practical application – apart from digital input/output modules, which can, for instance, include analogue, positioning and communication modules – are inserted in a rack, where individual modules are linked via a bus system. This type of design is also known as series technology. The card format PLC is a special type of modular PLC, developed during the last few years. With this type, individual or a number of printed circuit board modules are in a standardized housing. The hardware design for a programmable logic controller is such that it is able to withstand typical industrial environments as regard signal levels, heat, humidity, and fluctuations in current supply and mechanical impact. The new PLC standard EN 61131 (IEC 61131) This standard consists of five parts: Part 1: General information Part 2: Equipment requirements and tests Part 3: Programming languages Part 4: User guidelines (in preparation with IEC) Part 5: Messaging service specification (in preparation with IEC) Following are some of the companies, which are designing PLCs in exact accordance with EN 61131 standard. ABB, GE Fanuc, Mitsubishi Electric, Moeller, OMRON, Schneider Electric, Siemens Use the knowledge gained in the respective lab session to answer the following tasks in the best possible way. You should submit filled Lab Manual to your instructor before the start of the next lab session. MCT 319- Industrial Automation, Department of Mechatronics and Control Engineering, UET Lahore TASKS (Revision of Digital Logic Design): Numbering Systems Convert following to Decimal numbers. Showing the proper procedure which you’ll follow. a. 111100102 – Decimal Equivalent = _________________________ b. 13428 – Decimal Equivalent = _________________________ c. 2AD5916 – Decimal Equivalent = _________________________ Show your working here Logic Gates Complete the following table by drawing required circuits Hydraulic/ Pneumatic Logic Gate Symbol Electrical Equivalent Electronic Equivalent Equivalent MCT 319- Industrial Automation, Department of Mechatronics and Control Engineering, UET Lahore