Manufacturing Processes - L1 Fundamental PDF
Document Details
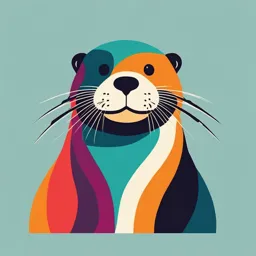
Uploaded by SecureTuring
Production and Robotics Engineering
Komkamol Chongbunwatana (KMC)
Tags
Summary
This document provides an overview of manufacturing processes, focusing on the fundamental principles of cutting. Key topics discussed include cutting terminology, chip formation mechanisms, forces during cutting, tool designs, and tool wear. Detailed cutting parameters and chip formation mechanisms are explored.
Full Transcript
Manufacturing Processes Fundamental of cutting Lecture 1 Komkamol Chongbunwatana (KMC) PRODUCTION AND ROBOTICS ENGINEERING Lecture Outline Terminology of the cutting part Chip formation Loads on the cutting part...
Manufacturing Processes Fundamental of cutting Lecture 1 Komkamol Chongbunwatana (KMC) PRODUCTION AND ROBOTICS ENGINEERING Lecture Outline Terminology of the cutting part Chip formation Loads on the cutting part Designs of the cutting part Tool wear PRODUCTION AND ROBOTICS ENGINEERING PAGE | 2 Lecture Outline Terminology of the cutting part Chip formation Loads on the cutting part Designs of the cutting part Tool wear PRODUCTION AND ROBOTICS ENGINEERING PAGE | 3 Definition of Machining Cutting, in which layers of material are mechanically separated from a workpiece in the form of chips by means of a relative motion between the tool and the workpiece [DIN8580, DIN8589] Source: Sandvik Coromant PRODUCTION AND ROBOTICS ENGINEERING PAGE | 4 Cutting Part – Speeds in Machining Translating cutting tool Cutting velocity, 𝑣𝑣𝑐𝑐 (primary cut direction) Effective cutting 𝑣𝑣𝑓𝑓 velocity, 𝑣𝑣𝑒𝑒 𝑣𝑣𝑐𝑐 Feed velocity, 𝑣𝑣𝑓𝑓 (feed direction) Rotating machined workpiece Source: Sandvik Coromant PRODUCTION AND ROBOTICS ENGINEERING PAGE | 5 Cutting Part – Terms Tool shank Rake face, 𝐴𝐴𝛾𝛾 Major cutting edge, 𝑆𝑆 (turned towards the cut surface) Major flank, 𝐴𝐴𝛼𝛼 Cutting edge corner (nose) Minor cutting edge, 𝑆𝑆 ′ (turned Minor flank, 𝐴𝐴′𝛼𝛼 towards the machined surface) PRODUCTION AND ROBOTICS ENGINEERING PAGE | 6 Cutting Part – Tool-in-Hand System Tool reference plane, 𝑷𝑷𝒓𝒓 (⊥ 𝑣𝑣𝑐𝑐 and Tool back containing the tool (passive) rotational axis) plane, 𝑷𝑷𝒑𝒑 /// 𝑃𝑃𝑟𝑟 (⊥ 𝑃𝑃𝑟𝑟 and 𝑃𝑃𝑝𝑝 Cutting point ⊥ 𝑣𝑣𝑓𝑓 ) 𝑣𝑣𝑐𝑐 Assumed 𝑃𝑃𝑓𝑓 𝑣𝑣𝑓𝑓 working (feed) plane, 𝑷𝑷𝒇𝒇 Tool cutting edge plane, 𝑷𝑷𝒔𝒔 (⊥ 𝑃𝑃𝑟𝑟 and ∥ 𝑣𝑣𝑓𝑓 ) (⊥ 𝑃𝑃𝑟𝑟 and tangential to 𝑆𝑆) Tool orthogonal plane, 𝑷𝑷𝒐𝒐 (⊥ 𝑃𝑃𝑠𝑠 ) Tool cutting edge normal plane, 𝑷𝑷𝒏𝒏 (⊥ 𝑆𝑆) PRODUCTION AND ROBOTICS ENGINEERING PAGE | 7 Cutting Part – Parameters on 𝑷𝑷𝒓𝒓 Tool reference plane, 𝑷𝑷𝒓𝒓 (⊥ 𝑣𝑣𝑐𝑐 and Bound cut (both 𝑆𝑆 and 𝑆𝑆 ′ ) ≠ free cut (only 𝑆𝑆 or 𝑆𝑆 ′ ) containing the tool 𝑃𝑃𝑝𝑝 𝑓𝑓 rotational axis) Cut surface /// 𝑃𝑃𝑟𝑟 𝑆𝑆 𝜿𝜿𝒓𝒓 𝑃𝑃𝑓𝑓 𝜺𝜺𝒓𝒓 𝑎𝑎𝑝𝑝 Machined 𝑆𝑆 ′ 𝑏𝑏 surface ℎ 𝜿𝜿𝒓𝒓 : tool cutting edge angle [°] 𝑏𝑏 : undeformed chip width [mm] 𝑎𝑎𝑝𝑝 𝜺𝜺𝒓𝒓 : tool included angle [°] ℎ: undeformed chip thickness [mm] 𝑏𝑏 = 𝑟𝑟𝜀𝜀 : corner radius [mm] sin 𝜅𝜅𝑟𝑟 𝑎𝑎𝑝𝑝 : depth of cut (infeed) [mm] ℎ = 𝑓𝑓 sin 𝜅𝜅𝑟𝑟 cross-sectional area of chip [mm2] 𝑓𝑓 : feed [mm] 𝑎𝑎𝑝𝑝 𝑓𝑓 = 𝑏𝑏 ℎ PRODUCTION AND ROBOTICS ENGINEERING PAGE | 8 Cutting Part – Parameters on 𝑷𝑷𝒐𝒐 ℎ 𝑃𝑃𝑟𝑟 /// 𝑃𝑃𝑜𝑜 𝜸𝜸𝒐𝒐 𝑃𝑃𝑠𝑠 𝜷𝜷𝒐𝒐 𝜶𝜶𝒐𝒐 𝜶𝜶𝒐𝒐 : tool orthogonal clearance angle [°] 𝜷𝜷𝒐𝒐 : tool orthogonal wedge angle [°] 𝜸𝜸𝒐𝒐 : tool orthogonal rake angle [°] 𝑟𝑟𝛽𝛽 : cutting edge radius (dull/sharp) [mm] (< ℎ⁄2 to avoid dull cutting edges, which Tool orthogonal plane, 𝑷𝑷𝒐𝒐 (⊥ 𝑃𝑃𝑠𝑠 ) plastically form burrs on the uncut surface) PRODUCTION AND ROBOTICS ENGINEERING PAGE | 9 Cutting Part – Parameters on 𝑷𝑷𝒏𝒏 𝑃𝑃𝑟𝑟 /// 𝑃𝑃𝑛𝑛 𝜸𝜸𝒏𝒏 𝑃𝑃𝑠𝑠 𝜷𝜷𝒏𝒏 𝜶𝜶𝒏𝒏 𝜶𝜶𝒏𝒏 : tool normal clearance angle [°] 𝜷𝜷𝒏𝒏 : tool normal wedge angle [°] 𝜸𝜸𝒏𝒏 : tool normal rake angle [°] Tool cutting edge normal plane, 𝑷𝑷𝒏𝒏 (⊥ 𝑆𝑆) PRODUCTION AND ROBOTICS ENGINEERING PAGE | 10 Cutting Part – Parameters on 𝑷𝑷𝒇𝒇 𝑃𝑃𝑟𝑟 /// 𝑃𝑃𝑓𝑓 𝜸𝜸𝒇𝒇 𝑃𝑃𝑠𝑠 𝜷𝜷𝒇𝒇 Assumed 𝜶𝜶𝒇𝒇 working 𝜶𝜶𝒇𝒇 : feed clearance angle [°] (feed) plane, 𝑷𝑷𝒇𝒇 𝜷𝜷𝒇𝒇 : feed wedge angle [°] (⊥ 𝑃𝑃𝑟𝑟 and ∥ 𝑣𝑣𝑓𝑓 ) 𝜸𝜸𝒇𝒇 : feed rake angle [°] PRODUCTION AND ROBOTICS ENGINEERING PAGE | 11 Cutting Part – Parameters on 𝑷𝑷𝒑𝒑 Tool back (passive) plane, 𝑷𝑷𝒑𝒑 𝜸𝜸𝒑𝒑 /// 𝑃𝑃𝑝𝑝 𝑃𝑃𝑠𝑠 (⊥ 𝑃𝑃𝑟𝑟 and ⊥ 𝑣𝑣𝑓𝑓 ) 𝑃𝑃𝑟𝑟 𝜷𝜷𝒑𝒑 𝜶𝜶𝒑𝒑 𝜶𝜶𝒑𝒑 : tool back clearance angle [°] 𝜷𝜷𝒑𝒑 : tool back wedge angle [°] 𝜸𝜸𝒑𝒑 : tool back rake angle [°] PRODUCTION AND ROBOTICS ENGINEERING PAGE | 12 Cutting Part – Parameters on 𝑷𝑷𝒔𝒔 Major cutting edge, 𝑆𝑆 /// 𝑃𝑃𝑠𝑠 Tool cutting edge plane, 𝑷𝑷𝒔𝒔 𝝀𝝀𝒔𝒔 𝑃𝑃𝑟𝑟 (⊥ 𝑃𝑃𝑟𝑟 and tangential to 𝑆𝑆) 𝝀𝝀𝒔𝒔 : tool cutting edge inclination [°] PRODUCTION AND ROBOTICS ENGINEERING PAGE | 13 Lecture Outline Chip formation Loads on the cutting part Designs of the cutting part Tool wear PRODUCTION AND ROBOTICS ENGINEERING PAGE | 14 Mechanism of Chip Formation 𝑣𝑣𝑐𝑐 : 100 m/min Shear a : preliminary deformation Workpiece 𝑣𝑣 plane 𝑎𝑎𝑝𝑝 : 2 mm structure 𝑐𝑐 zone 𝑓𝑓 : 0.3 mm Chip structure b : primary shear zone a b c : viscous flow zone Shear e 𝑣𝑣𝑐𝑐𝑐 (great shear zone d c deformation) d : secondary shear zone Flow Rake face zone e : detachment zone Cut surface (initial split for ductile Cut surface Flank material) Source: Manufacturing Processes 1 - Cutting (RWTH edition), F. Klocke, Springer (2011) PRODUCTION AND ROBOTICS ENGINEERING PAGE | 15 Stress and Strain in Chips ℎ Average yield strength of stainless steel [MPa] Workpiece 𝑢𝑢𝑥𝑥 𝜏𝜏 Φ Compressive Tensile Bending Shear 𝛾𝛾𝑜𝑜 𝜓𝜓 Chip 1080 671 479 358 𝜏𝜏 𝜎𝜎 𝜎𝜎 ℎ𝑐𝑐𝑐 𝑣𝑣𝑐𝑐 Tool ℎ 𝜎𝜎 𝜎𝜎 normal 𝜏𝜏 𝑥𝑥 𝜏𝜏 𝑥𝑥𝑐𝑐𝑐 𝑣𝑣𝑐𝑐𝑐 strain shear strain ℎ𝑐𝑐𝑐 𝑥𝑥𝑐𝑐𝑐 − 𝑥𝑥 tan 𝛷𝛷 + 𝛹𝛹 − 𝛾𝛾𝑜𝑜 where 𝑥𝑥 2 1 𝑢𝑢𝑥𝑥 𝑢𝑢𝑦𝑦 1 𝑢𝑢𝑥𝑥 𝜀𝜀𝑖𝑖𝑖𝑖 = 𝜀𝜀𝑥𝑥𝑥𝑥 = + = 2 ℎ𝑐𝑐𝑐 𝑥𝑥𝑐𝑐𝑐 2 ℎ𝑐𝑐𝑐 tan 𝛷𝛷 + 𝛹𝛹 − 𝛾𝛾𝑜𝑜 ℎ𝑐𝑐𝑐 − ℎ tan 𝛷𝛷 + 𝛹𝛹 − 𝛾𝛾𝑜𝑜 𝛾𝛾𝑥𝑥𝑥𝑥 2 ℎ = = 2 2 Source: The application of viscoplasticity in predictive modelling, J. Leopold, 3rd CIRP-International Workshop (2000) PRODUCTION AND ROBOTICS ENGINEERING PAGE | 16 Phenomenological Classification of Chip Formation Varying shapes of chips, typically taking place in machining processes, influenced by a combination of workpiece material and cutting conditions Discontinuous Continuous chip Lamellar chip Segmented chip chip Source: Basics of Cutting and Abrasive Processes, H.K. Toenshoff, Springer (2013) PRODUCTION AND ROBOTICS ENGINEERING PAGE | 17 Form-Influencing Factors Workpiece material’s mechanical properties 𝜀𝜀𝑈𝑈 Shear stress, 𝜏𝜏 [MPa] 𝜀𝜀𝑐𝑐𝑐 : shear (cutting) strain developed in chips [-] 𝜀𝜀𝐹𝐹 𝜀𝜀𝑌𝑌 Continuous chip 𝜀𝜀𝑌𝑌 : Yield shear strain [-] Lamellar chip 𝜀𝜀𝑈𝑈 : Ultimate shear strain [-] Segmented chip 𝜀𝜀𝐹𝐹 : Fracture shear strain [-] Discontinuous chip 𝜀𝜀𝑐𝑐𝑐 Shear strain, 𝜀𝜀 [-] Workpiece material’s microstructural homogeneity Degree of friction between the tool’s rake face and chips Vibration during machining operation Rake angle Other cutting conditions such as the cutting speed, feed and depth of cut Source: Zerspannung der Eisenwerkstoffe, G. Vieregge, Strahleisen GmbH (1970) PRODUCTION AND ROBOTICS ENGINEERING PAGE | 18 Continuous Chip Characteristics Chipping Behaviour: chips sliding off along the rake face at a constant speed in a stationary flow Encouraging Factors: Ductile material with 𝜀𝜀𝑈𝑈 > 𝜀𝜀𝑐𝑐𝑐 Uniform microstructure Low tool-chip friction (small shear strain) 𝑟𝑟 Neutral High 𝑣𝑣𝑐𝑐 (softening → tough) axis 𝜃𝜃 Small 𝑓𝑓 (small ℎ → low bending strain) Large 𝑎𝑎𝑝𝑝 (big 𝑏𝑏 → big shear-bearing chip ℎ𝑐𝑐𝑐 ∆𝑙𝑙 𝑙𝑙 = = 𝜀𝜀𝑐𝑐𝑐 cross-section area), much less influence than 𝑓𝑓 2𝑟𝑟 𝑙𝑙 Large positive 𝛾𝛾𝑜𝑜 (small shear strain) 𝜀𝜀𝑐𝑐𝑐,1 ℎ𝑐𝑐𝑐,1 ∆𝑙𝑙 = 𝜀𝜀𝑐𝑐𝑐,2 𝜀𝜀𝑐𝑐𝑐,2 ℎ𝑐𝑐𝑐,2 𝜀𝜀𝑐𝑐𝑐,1 Source: Manufacturing Processes 1 - Cutting (RWTH edition), F. Klocke, Springer (2011) PRODUCTION AND ROBOTICS ENGINEERING PAGE | 19 Lamellar Chip Characteristics Chipping Behaviour: chips formed continuously but unevenly deformed resulting in periodic concentrated shear bands Encouraging Factors: Ductile material with 𝜀𝜀𝑈𝑈 < 𝜀𝜀𝑐𝑐𝑐 < 𝜀𝜀𝐹𝐹 Inhomogeneous microstructure Temporally highly altered friction (stick-slip in the mixed/boundary friction region) Vibration in the feed direction with a high frequency in the range of kilohertz (variation in chip thickness) High 𝑣𝑣𝑐𝑐 (softening → tough) Large 𝑓𝑓 (big ℎ → large bending strain) Source: Manufacturing Processes 1 - Cutting (RWTH edition), F. Klocke, Springer (2011) PRODUCTION AND ROBOTICS ENGINEERING PAGE | 20 Segmented Chip Characteristics Chipping Behaviour: chips regularly breaking in the primary shear zone (over fracture limit) and fusing again, leading to saw-tooth like chips Encouraging Factors: Semi-ductile material with 𝜀𝜀𝐹𝐹 < 𝜀𝜀𝑐𝑐𝑐 High tool-chip friction (large shear strain) Vibration in the feed direction with a high frequency in the range of kilohertz (variation in chip thickness) Low 𝑣𝑣𝑐𝑐 (no softening → brittle) Large 𝑓𝑓 (big ℎ → large bending strain) Small 𝑎𝑎𝑝𝑝 (small 𝑏𝑏 → small shear-bearing chip cross-section area) Negative 𝛾𝛾𝑜𝑜 (large shear strain) Source: 1. Manufacturing Processes 1 - Cutting (RWTH edition), F. Klocke, Springer (2011), 2. Sandvik Coromant PRODUCTION AND ROBOTICS ENGINEERING PAGE | 21 Discontinuous Chip Characteristics Chipping Behaviour: chips ripping off the surface with no plastic deformation (right within the primary shear zone without initial detachment in the detachment zone), thus leaving spalling traces on the surface Encouraging Factors: Brittle material with 𝜀𝜀𝐹𝐹 < 𝜀𝜀𝑐𝑐𝑐 Inhomogeneous microstructure High tool-chip friction (large shear strain) Low 𝑣𝑣𝑐𝑐 (no softening → brittle) Large 𝑓𝑓 (big ℎ → large bending strain) Small 𝑎𝑎𝑝𝑝 (small 𝑏𝑏 → small shear-bearing chip cross-section area) Source: 1. Manufacturing Processes 1 - Cutting (RWTH edition), F. Klocke, Springer (2011), 2. Sandvik Coromant PRODUCTION AND ROBOTICS ENGINEERING PAGE | 22 Conventional Chip Forms 1 2 3 4 5 6 7 8 9 10 Angular Short Conical Ribbon Snarled Flat helical Tabular Spiral Short spiral Discontinuous helical tabular tabular Chip Form Chip volume ≥ 90 ≥ 90 ≥ 50 ≥ 50 ≥ 50 ≥ 25 ≥ 25 ≥8 ≥8 ≥3 ratio Greater 𝑅𝑅𝑧𝑧 ⇒ greater required spaces for chip accommodation in the machine tool and chip evacuation from the cutting zone 𝑹𝑹𝒛𝒛 = 𝑽𝑽𝒄𝒄𝒄𝒄 ⁄𝑽𝑽𝑾𝑾 Longer chips ⇒ greater risk of endangering tools, machine tools, workpieces and operators Drifting over the flank Additional Highly scattering (injuring cutting edges and damages (injuring operators) tool holders) Rating Unfavorable Favorable Good Favorable Source: 1. Manufacturing Processes 1 - Cutting (RWTH edition), F. Klocke, Springer (2011), 2. Sandvik Coromant PRODUCTION AND ROBOTICS ENGINEERING PAGE | 23 Cutting-Condition Dependent Chip Forms Workpiece 𝒗𝒗𝒄𝒄 𝜸𝜸𝒐𝒐 𝜿𝜿𝒓𝒓 𝝀𝝀𝒔𝒔 𝜺𝜺𝒓𝒓 𝒓𝒓𝜺𝜺 Rhombic-shape insert: ISO CNMG Austenitic 316L 100 m/min -6° 95° -6° 80° 0.794 mm 120408-MM 2025 Chip volume ratio 𝑅𝑅𝑧𝑧 3.5 3.5 3.0 3.0 Chip breaker (more bending by radius Depth of cut [mm] 2.5 2.5 reduction of the chip curling curvature) 2.0 2.0 1.5 1.5 1.0 1.0 0.5 Greater 𝑓𝑓 → smaller 𝑅𝑅𝑧𝑧 (shorter chips) 0.5 0.1 0.2 0.3 Feed rate [mm/rev] 0.4 0.1 0.175 0.25 0.325 0.4 Feed rate [mm/rev] Greater 𝑎𝑎𝑝𝑝 → bigger 𝑅𝑅𝑧𝑧 (longer chips) Source: Machining of stainless steels: a comparative study, R.D. Koyee, International Conference on Advanced Manufacturing Engineering and Technologies (2013) PRODUCTION AND ROBOTICS ENGINEERING PAGE | 24 Lecture Outline Loads on the cutting part Designs of the cutting part Tool wear PRODUCTION AND ROBOTICS ENGINEERING PAGE | 25 Forces on the Cutting Part 𝐹𝐹 : total machining 𝑣𝑣𝑒𝑒 force [N] 𝑣𝑣𝑐𝑐 𝐹𝐹𝑐𝑐 : cutting force [N] Feed direction 𝐹𝐹𝑓𝑓 : feed force [N] (tool) 𝑣𝑣𝑓𝑓 𝐹𝐹𝑓𝑓 𝐹𝐹𝑝𝑝 : passive force [N] 𝐹𝐹𝑝𝑝 𝑣𝑣𝑐𝑐 : cutting speed [mm/s] 𝐹𝐹𝑐𝑐 𝑣𝑣𝑓𝑓 : feed velocity [mm/s] Primary motion 𝑣𝑣𝑒𝑒 : effective cutting 𝐹𝐹 (workpiece) speed [mm/s] PRODUCTION AND ROBOTICS ENGINEERING PAGE | 26 Effect of Feed Rate on Forces 𝑓𝑓 𝑓𝑓 𝑓𝑓 𝑎𝑎𝑝𝑝 𝐹𝐹𝑓𝑓 𝜅𝜅𝑟𝑟 𝐹𝐹𝑐𝑐 Force, 𝐹𝐹 [N] 𝐹𝐹𝑝𝑝 𝑏𝑏 ℎ ∝ 𝑓𝑓 𝐹𝐹𝑓𝑓 𝐹𝐹𝑝𝑝 Feed, 𝑓𝑓 [mm] PRODUCTION AND ROBOTICS ENGINEERING PAGE | 27 Effect of Depth of Cut on Forces 𝑎𝑎𝑝𝑝 Longer cutting edge 𝑓𝑓 𝑎𝑎𝑝𝑝 engaging with the cut 𝑏𝑏 surface!!!! 𝑎𝑎𝑝𝑝 𝑏𝑏 𝐹𝐹𝑓𝑓 𝜅𝜅𝑟𝑟 𝐹𝐹𝑐𝑐 Force, 𝐹𝐹 [N] 𝐹𝐹𝑝𝑝 𝑏𝑏 𝐹𝐹𝑓𝑓 𝑏𝑏 ∝ 𝑎𝑎𝑝𝑝 𝐹𝐹𝑝𝑝 Depth of cut, 𝑎𝑎𝑝𝑝 [mm] PRODUCTION AND ROBOTICS ENGINEERING PAGE | 28 Effect of Tool Cutting Edge Angle on Forces 𝐹𝐹𝑓𝑓 𝜅𝜅𝑟𝑟 𝐹𝐹𝑓𝑓 𝜅𝜅𝑟𝑟 𝐹𝐹𝑝𝑝 𝐹𝐹𝑝𝑝 𝑓𝑓 𝑏𝑏 ℎ 𝑏𝑏 𝑎𝑎𝑝𝑝 𝐹𝐹𝑓𝑓 ℎ 𝜅𝜅𝑟𝑟 𝐹𝐹𝑐𝑐 ℎ ∝ 𝜅𝜅𝑟𝑟 Force, 𝐹𝐹 [N] 𝐹𝐹𝑝𝑝 𝑏𝑏 𝐹𝐹𝑓𝑓 1 𝑏𝑏 ∝ 𝜅𝜅𝑟𝑟 𝐹𝐹𝑝𝑝 Tool cutting edge angle, 𝜅𝜅𝑟𝑟 [°] PRODUCTION AND ROBOTICS ENGINEERING PAGE | 29 Effect of Cutting Speed on Forces BUE Built-up Edge (BUE): parts Chip of the workpiece, 𝑓𝑓 atomically bonded (cold BUE welded) to the flank and 𝑎𝑎𝑝𝑝 𝐹𝐹𝑓𝑓 Tool rake face and strain- hardened (plastically deformed) at some low 𝒗𝒗𝒄𝒄 , 𝜅𝜅𝑟𝑟 𝐹𝐹𝑐𝑐 elevating force due to the greater wedge radius (dull) Force, 𝐹𝐹 [N] Blue Brittleness: a strain-aging 𝐹𝐹𝑝𝑝 𝑏𝑏 mechanism in the blue heat 𝐹𝐹𝑓𝑓 temperature range, where ductility drops and strength rises due to 𝐹𝐹𝑝𝑝 diffusion of carbon and nitrogen atoms in material restricting the Cutting speed, 𝑣𝑣𝑐𝑐 [mm/min] movement of dislocations Source: Seco PRODUCTION AND ROBOTICS ENGINEERING PAGE | 30 Force Prediction through the Empirical-Based Kienzle Equation Experiments 𝒃𝒃 = 𝒂𝒂𝒑𝒑 ⁄𝐬𝐬𝐬𝐬𝐬𝐬 𝜿𝜿𝒓𝒓 𝒉𝒉 = 𝒇𝒇 𝐬𝐬𝐬𝐬𝐬𝐬 𝜿𝜿𝒓𝒓 𝑭𝑭′𝒄𝒄 = 𝑭𝑭𝒄𝒄 ⁄𝒃𝒃 𝒇𝒇 [mm] 𝑭𝑭𝒄𝒄 [N] [mm] [mm] [N/mm] 0.13 466.4 2.13 0.12 219 0.32 848 0.3 398 0.45 1,060 0.42 498 0.75 1,484 0.7 697 Specific cutting force 𝑘𝑘𝑐𝑐𝑐.1 = 𝐹𝐹𝑐𝑐 ⁄ 𝑏𝑏 ℎ : force needed to detach a chip with an undeformed cross-section area of 1×1 mm Increment factor (slope): 1 − 𝑚𝑚𝑐𝑐 log 𝐴𝐴𝑦𝑦 − log 𝐵𝐵𝑦𝑦 log 2560 − log 1396 1 − 𝑚𝑚𝑐𝑐 = = = 0.66 log 𝐴𝐴𝑥𝑥 − log 𝐵𝐵𝑥𝑥 log 5 − log 2 Cutting-force linear estimation by the KIENZLE equation log 𝐹𝐹𝑐𝑐′ = 1 − 𝑚𝑚𝑐𝑐 log ℎ + log 𝑘𝑘𝑐𝑐𝑐.1 1−𝑚𝑚𝑐𝑐 log 𝐹𝐹𝑐𝑐 ⁄𝑏𝑏 = log 𝑘𝑘𝑐𝑐𝑐.1 ℎ 𝒃𝒃(𝒂𝒂𝒑𝒑 ) and 𝒉𝒉(𝒇𝒇) as **Kienzle is valid for all force components 𝐹𝐹𝑝𝑝 , 𝐹𝐹𝑐𝑐 and 𝐹𝐹𝑓𝑓 1−𝑚𝑚𝑐𝑐 Source: Manufacturing Processes 1 - Cutting (RWTH edition), F. Klocke, Springer (2011) 𝐹𝐹𝑐𝑐 = 𝑘𝑘𝑐𝑐𝑐.1 𝑏𝑏 ℎ independent variables PRODUCTION AND ROBOTICS ENGINEERING PAGE | 31 Transformation of the Machining Work 𝜎𝜎𝑛𝑛 Distortion Shear work Work 𝑊𝑊𝑒𝑒 work Detachment work 𝜏𝜏 = 𝑊𝑊𝑐𝑐 + 𝑊𝑊𝑓𝑓 Thermal Friction Friction at face energy = 𝐹𝐹𝑐𝑐 𝑙𝑙𝑐𝑐 + 𝐹𝐹𝑓𝑓 𝑙𝑙𝑓𝑓 work Friction at flank 𝑣𝑣𝑐𝑐 𝜎𝜎𝑛𝑛 𝜏𝜏 𝑣𝑣𝑐𝑐ℎ Work, 𝑊𝑊 [Nm] 𝑇𝑇3 Shear work (b) 𝑇𝑇4 Flow zone 𝑇𝑇5 Friction at face (c) Friction at flank (d) + detachment work (e) Source: 1. Zerspannung der Eisenwerkstoffe, G. Vieregge, Strahleisen GmbH (1970) 2. Der Verschleiß an spanenden Werkzeugen, W. König, Materialprüfung (1967) Thickness of cut, ℎ [mm] PRODUCTION AND ROBOTICS ENGINEERING PAGE | 32 Distribution of Heat and Temperature Shear plane 0 Temperature [°C] 700 (Main source of heat) 𝒗𝒗𝒄𝒄 : 60 m/min 5% 𝒉𝒉 : 0.32 mm 75% 𝜸𝜸𝒐𝒐 : 10° 2% “Temperature of 700 up 18% to 1,700 °C expected in the contact zone” Secondary shear zones (2nd sources of heat) Source: 1. Zerspannung der Eisenwerkstoffe, G. Vieregge, Strahleisen GmbH (1959) 2. Source: Grundzüge der Zerspannungslehre vol.1: Einschneidige Zerspannung, M. Kronenberg, Springer (1954) PRODUCTION AND ROBOTICS ENGINEERING PAGE | 33 Lecture Outline Designs of the cutting part Tool wear PRODUCTION AND ROBOTICS ENGINEERING PAGE | 34 Influence of the Tool Cutting Edge Angle on the Machining Process Adjustment of tool 𝜅𝜅𝑟𝑟 𝜅𝜅𝑟𝑟 cutting edge angle 𝜅𝜅𝑟𝑟 𝑏𝑏 𝑏𝑏 𝑃𝑃𝑓𝑓 𝑃𝑃𝑓𝑓 - Less localised wear Less chatter vibration (longer effective engagement of the cutting edge) required + (less passive force) Less cutting force especially to machine high- Better machined surface strength materials quality1 (chips diverted more 𝜅𝜅𝑟𝑟 from the workpiece + less 𝑭𝑭𝒑𝒑 ) Typical value of 𝜅𝜅𝑟𝑟 : 10° to 100° Source: Sandvik Coromant PRODUCTION AND ROBOTICS ENGINEERING PAGE | 35 Influence of the Tool Included Angle on the Machining Process Adjustment of tool included angle 𝜀𝜀𝑟𝑟 𝜀𝜀𝑟𝑟 𝜀𝜀𝑟𝑟 𝑃𝑃𝑓𝑓 𝑃𝑃𝑓𝑓 - Greater accessibility Greater cutting-edge stability (able to enter restricted space) Less chatter vibration + As large for the sake of stability as needed but the angle between the (less passive force) minor cutting edge and feed plane at Less cutting force least greater than 2° to avoid the minor cutting edge engaging with the Typical value of 𝜀𝜀𝑟𝑟 : 60° to 120° machined surface PRODUCTION AND ROBOTICS ENGINEERING PAGE | 36 Influence of the Corner Radius on the Machining Process Adjustment of corner 𝑟𝑟𝜀𝜀 radius 𝑟𝑟𝜀𝜀 𝑟𝑟𝜀𝜀 𝑃𝑃𝑓𝑓 𝑃𝑃𝑓𝑓 - Less chatter vibration (less passive force) + Less cutting force 𝑓𝑓 2 𝑅𝑅𝑡𝑡 = 𝑟𝑟𝜀𝜀 − 𝑟𝑟𝜀𝜀2 − 𝑓𝑓 2 ⁄4 ≈ 8𝑟𝑟𝜀𝜀 Better machined surface quality2 Typical value of 𝑟𝑟𝜀𝜀 : 0.4 to 2 mm (low kinematic surface roughness) 𝑎𝑎𝑝𝑝 (< to avoid dull edges plastically forming burrs) Greater cutting-edge stability 2 PRODUCTION AND ROBOTICS ENGINEERING PAGE | 37 Corner-Radius Dependent Surface Roughness Too big cutting edge corner radius (2 mm) adversely leading to great passive and cutting forces and therefore more intense oscillation causing rougher workpiece surface PRODUCTION AND ROBOTICS ENGINEERING PAGE | 38 Influence of Tool Orthogonal Rake Angle on the Machining Process −𝛾𝛾𝑜𝑜 Adjustment of tool 𝑃𝑃𝑟𝑟 orthogonal rake angle 𝛾𝛾𝑜𝑜 𝑃𝑃𝑟𝑟 +𝛾𝛾𝑜𝑜 - Greater cutting-edge stability 1.5 % less 𝐹𝐹𝑐𝑐 per degree Better chip breakage + 5.0 % less 𝐹𝐹𝑓𝑓 per degree 4.0 % less 𝐹𝐹𝑝𝑝 per degree Less wear on the rake face Better machined surface quality3 (less BUE formation due to a sharper cutting edge + chips diverted more Typical value of 𝛾𝛾𝑜𝑜 : -10° to +20° from the workpiece + less 𝑭𝑭𝒑𝒑 ) Source: Sandvik Coromant PRODUCTION AND ROBOTICS ENGINEERING PAGE | 39 Influence of Tool Orthogonal Clearance Angle on the Machining Process Adjustment of tool orthogonal clearance angle 𝛼𝛼𝑜𝑜 𝑃𝑃𝑠𝑠 𝑃𝑃𝑠𝑠 𝛼𝛼𝑜𝑜 𝛼𝛼𝑜𝑜 - Greater cutting-edge stability Less wear on the flank mechanically + (smaller workpiece-tool Greater cutting-edge stability contact area) thermally (bigger heat-absorbing mass, lowering Δ𝑇𝑇 and thus retaining strength) Typical value of 𝛼𝛼𝑜𝑜 : 6° to 12° PRODUCTION AND ROBOTICS ENGINEERING PAGE | 40 Influence of Cutting-Edge Inclination on the Machining Process 𝑃𝑃𝑟𝑟 +𝜆𝜆𝑠𝑠 Adjustment of cutting- −𝜆𝜆𝑠𝑠 edge inclination 𝜆𝜆𝑠𝑠 𝑃𝑃𝑟𝑟 - Greater cutting-edge stability due to an 1.5 % less 𝐹𝐹𝑐𝑐 per degree improved load profile caused by initial workpiece-tool engagement towards the + 1.5 % less 𝐹𝐹𝑓𝑓 per degree 10 % less 𝐹𝐹𝑝𝑝 per degree middle of the cutting edge instead of at Less chatter vibration the nose (less local overloading) (less passive force) Better machined surface quality4 (chips diverted more from the Typical value of 𝜆𝜆𝑠𝑠 : -6° to +6° workpiece + less 𝑭𝑭𝒑𝒑 ) PRODUCTION AND ROBOTICS ENGINEERING PAGE | 41 Tool Designs Indexable Tools (Tools with Inserts) Solid Tools (Tool Bits) T-Max® Q-Cut blade CoroMill® 331 CoroDrill® 860-PM for parting adjustable half side solid carbide drill Possibility and back face disc for custom milling cutter regrinding Wear-resistant CoroMill® single inserts with Plura solid several cutting carbide ball edges clamped or nose end mill screwed onto a CoroMill® 345 face tough tool holder milling cutter Safe, quick insert replacement (indexing) CoroThread® with cutting edges positioned against the CoroTurn® XS solid 266 shank tool carbide tool for tool holder rather than the workpiece for thread turning turning Source: Sandvik Coromant PRODUCTION AND ROBOTICS ENGINEERING PAGE | 42 ISO 1832:2017 Indexable Inserts 1 2 3 4 5 6 7 8 9 4. Fixing and/or chip breakers 3. Tolerance class 8. Cutting edge condition (𝒓𝒓𝜷𝜷 ) Countersink Chip Insert Rounded 𝒅𝒅 [μm] 𝒎𝒎 [μm] 𝒔𝒔 [μm] Chamfered C N M G 12 04 08 Code Code on the hole breaker cross corners Inscribed Nose Thick- F Sharp S /rounded Side Angle on face section Odd side no circle height ness E Rounded K Double 1. Insert shape with 𝜺𝜺𝒓𝒓 2. Normal clearance 𝜶𝜶𝒏𝒏 chamfered N – A1 ± 25 ±5 ± 25 Hex H 120° A 3° F 25° Double R – – Single C ± 25 1 ± 13 ± 25 T Chamfered P chamfered/ Equiangular Oct O 135° B 5° G 30° F Both E ± 25 ± 25 ± 25 rounded C 7° N 0° A – F ± 13 1 ±5 ± 25 I Pen P 108° D 15° P 11° M No – Single 9. Direction of feed motion (𝒗𝒗𝒇𝒇 ) G ± 25 ± 25 ± 130 Sq. S 90° E 20° O others G Both Inserts with Even side no H ± 13 ± 13 ± 25 R Right- asymmetrical 60° 5. Insert size (2 digits) W – Equilateral Tri. T Single J1 ± 50–1502 ± 5 ± 25 hand chip breakers T Single or cutting- C 80° Cutting edge length 40–60° K1 ± 50–1502 ± 13 ± 25 Q – edge corners Both Left- Non-equiangular D 55° I U Both L1 ± 50–1502 ± 25 ± 25 L hand (e.g., wiper Rhombic + B – Wiper edge M ± 50–150 ± 80–200 2 2 ± 130 edges) E 75° II Single II H Single N ± 50–1502 ± 80–2002 ± 25 Inserts with 70–90° symmetrical M 86° maximum 𝒂𝒂𝒑𝒑 C – U ± 80–250 ± 130–380 ± 130 N Neu- 2 2 Both V 35° III J Both 1 Inserts with wipers (↑ 𝑓𝑓 but ↓ 𝑅𝑅 ) tral chip breakers or cutting- Length 𝑎𝑎 + of a major Uncommon designs with drawings 2 Depending on the insert size edge corners Trig. W 80° X IV (longer) cutting edge (always for non-equilateral inserts) Roun Code M0 02 16 Preceded by 0 in the case of 1 digit 00 configuration III Rec L 90° Non-equi. E. V Diameter ded 𝒓𝒓𝜺𝜺 [mm] 0.2 1.6 ⋯ Sharp Non-equi. 7. Insert corner A 85° Preceded by 0 if only 1 Code A D E F P Z Parallel. edges Wiper IV B 82° digit is present, the code 𝜿𝜿𝒓𝒓 [°] 45 60 75 85 90 others is a 2-digit dimension Code A B C D E F G N P Z K 55° discarding all decimals ′ 𝜶𝜶𝒏𝒏 [°] 3 5 7 15 20 25 30 0 11 others V Round R – 6. Insert Code 01 T1 02 03 T3 04 05 06 07 09 12 Distance from a base surface up to the 𝜺𝜺𝒓𝒓 : the smaller angle thickness 𝒔𝒔 [mm] 1.59 1.98 2.38 3.18 3.97 4.76 5.56 6.35 7.94 9.52 12.7 edge of its opposing cutting-edge corner PRODUCTION AND ROBOTICS ENGINEERING PAGE | 43 ISO 1832:2017 Indexable Inserts 1 2 3 4 5 6 7 8 9 10 8. Cutting edge condition (𝒓𝒓𝜷𝜷 ) Manufacturers’ 10. Size of cutting-edge condition (5 digits) Chamfered C N M G 12 04 08 designation Code 𝒃𝒃𝜸𝜸 [mm] Code 𝜸𝜸𝒃𝒃 [°] F Sharp S /rounded Double codes e.g., 005 0.05 05 5 E Rounded K chamfered Chamfered cutting edges (T, S) Double chipbreaker 010 0.10 10 10 T Chamfered P chamfered/ CNMG120408-PM4325: designs or 015 0.15 15 15 rounded T-Max® P insert for turning insert grades 020 0.20 20 20 9. Direction of feed motion (𝒗𝒗𝒇𝒇 ) 025 0.25 25 25 Inserts with R Right- asymmetrical hand chip breakers 030 0.30 30 30 or cutting- 050 0.50 Chamfered edge corners Left- L hand 070 0.70 (e.g., wiper edges) 100 1.00 Double Inserts with cham- symmetrical 150 1.50 fered N Neu- tral chip breakers 200 2.00 or cutting- edge corners Code 𝒃𝒃𝜸𝜸𝜸𝜸 [mm] 𝜸𝜸𝒃𝒃𝒃𝒃 [°] 𝒃𝒃𝜸𝜸𝜸𝜸 [mm] 𝜸𝜸𝒃𝒃𝒃𝒃 [°] cutting edges (K, P) Double chamfered 05015 0.50 15 0.10 30 07015 0.70 15 0.15 30 10015 1.00 15 0.20 30 15010 1.50 10 0.25 30 20010 2.00 10 0.25 30 Source: Sandvik Coromant PRODUCTION AND ROBOTICS ENGINEERING PAGE | 44 Application-Dependent Cutting-Edge Geometry Chip control range (geometry of Sharp Cutting area (geometry) Strong cutting edges and chip breakers) Stable Finish (FP) Medium (MP) Rough (RP) for negative inserts to cut steel cutting: Corner Corner Corner Cross section Continuous geometry Flank Flank Flank cutting Constant Good surface finish Good balance of Good balance of depth of cut due to great 𝛾𝛾𝑛𝑛 (sharp) sharpness (great 𝛾𝛾𝑛𝑛 ) strength (wide land) and strength (great possible to remove Rigid Features Good chip breakage 𝛽𝛽𝑛𝑛 from the narrow hard skin and chip RP clamping at small 𝑓𝑓 (small chip land) curling radius) evacuation (wide chip pocket) Unstable Stable FP MP RP Tough Grade Hard NX2525 MC6015 MC6015 cutting: MP Cutting condition Interrupted General CNMG CNMG CNMG cutting 120402-FP 120408-MP 120408-RP FP Irregular MP3025 MC6015 MC6015 depth of cut Unstable FP MP RP Loose MC6025 MC6025 MC6025 Source: Mitsubishi Materials Corporation clamping PRODUCTION AND ROBOTICS ENGINEERING PAGE | 45 Lecture Outline Tool wear PRODUCTION AND ROBOTICS ENGINEERING PAGE | 46 Tool Wear Characteristics Minor flank notch wear Crater wear Plastic deformation Flank wear Major Cutting edge chipping/breakage Layer flaking Rake notch wear (delamination) Wall-like stain (BUE) Major flank notch wear Source: Manufacturing Processes 1 - Cutting (RWTH edition), F. Klocke, Springer (2011) PRODUCTION AND ROBOTICS ENGINEERING PAGE | 47 Measurements of Tool Wear 𝑆𝑆𝑆𝑆𝛼𝛼 : Displacement @𝑉𝑉𝑉𝑉 = 0.5 mm (big contact) 𝑉𝑉𝑉𝑉𝐵𝐵,𝑚𝑚𝑚𝑚𝑚𝑚 of cutting edge 𝑉𝑉𝑉𝑉𝑁𝑁 𝑉𝑉𝑉𝑉𝐵𝐵 towards flank 𝑉𝑉𝑉𝑉𝑐𝑐 𝑆𝑆𝑆𝑆𝛼𝛼 𝐹𝐹𝑝𝑝 100% 𝐹𝐹𝑓𝑓 90% 𝐹𝐹𝑐𝑐 20% 𝑆𝑆𝑆𝑆𝛾𝛾 : Displacement Bigger 𝐾𝐾𝐾𝐾 of cutting edge Poorer chip breakage (bigger γ) towards face 𝑟𝑟𝜀𝜀 𝑏𝑏⁄4 Weaker cutting part (smaller β) 𝑽𝑽𝑽𝑽 : Width of flank Zone 𝐶𝐶 𝐵𝐵 𝑁𝑁 wear land 𝑏𝑏 𝐾𝐾𝐾𝐾 : Crater depth 𝐴𝐴 𝐾𝐾𝐾𝐾 : Crater width 𝐾𝐾𝑀𝑀: Crater centre location 𝑆𝑆𝑆𝑆𝛾𝛾 𝑲𝑲 : Crater ratio 𝐴𝐴 − 𝐴𝐴 𝐴𝐴 Source: Manufacturing Processes 1 - Cutting (RWTH edition), F. Klocke, Springer (2011) 𝑲𝑲 = 𝑲𝑲𝑲𝑲⁄𝑲𝑲𝑲𝑲 PRODUCTION AND ROBOTICS ENGINEERING PAGE | 48 Flank-Wear Dependent Surface Quality Great flank wear adversely influencing the workpiece surface quality5 due to growing cutting edge roughness and more intense oscillation caused by the increasing machining force PRODUCTION AND ROBOTICS ENGINEERING PAGE | 49 Flank-Wear Dependent Residual Stress Residual compressive stress developed under the workpiece surface when cutting with a fresh cutting tool due to the dominant mechanical load Combined residual compressive- tensile stress developed when cutting with a worn cutting tool due to the increasing thermal load as a result of greater friction between the scratched flanks and workpiece surface PRODUCTION AND ROBOTICS ENGINEERING PAGE | 50 Flank-Wear Dependent Form Accuracy A worn cutting edge causing the workpiece temperature to rise greatly as the cutting operation is proceeding, resulting in radial workpiece expansion and, accordingly, increasing effective depth of cut over the path, producing a conical workpiece, whose diameter diminishes in the feed direction Sufficiently-large feed velocity capable of compensating almost completely for such temperature escalation PRODUCTION AND ROBOTICS ENGINEERING PAGE | 51 Determination of Cutting Tool Life Taylor tool-life equation log 𝑇𝑇𝑐𝑐 = 𝑛𝑛 log 𝑣𝑣𝑐𝑐 + log 𝐶𝐶𝑣𝑣 𝛽𝛽 𝑇𝑇𝑐𝑐 = 𝐶𝐶𝑣𝑣 𝑣𝑣𝑐𝑐𝑛𝑛 𝑇𝑇𝑐𝑐 = 𝐶𝐶𝑣𝑣𝑐𝑐𝑛𝑛 𝑓𝑓𝑧𝑧𝛼𝛼 𝑎𝑎𝑝𝑝 log 𝐴𝐴𝑦𝑦 −log 𝐵𝐵𝑦𝑦 log 20⁄3 𝑛𝑛 = = = −6.69 log 𝐴𝐴𝑥𝑥 −log 𝐵𝐵𝑥𝑥 log 72.06⁄95.68 𝑇𝑇𝑐𝑐 72.06 Tool life criterion (𝑽𝑽𝑽𝑽𝒎𝒎𝒎𝒎𝒎𝒎 or 𝐶𝐶𝑣𝑣 = = = 3.7 1010 𝑣𝑣𝑐𝑐𝑛𝑛 20−6.69 𝑲𝑲𝒎𝒎𝒎𝒎𝒎𝒎 ) chosen to fully avoid phase III under any situation Phase I (run-in): rapid wear due to unevenness of new edges quickly smoothed out Phase II (steady wear): steady wear dependent on cutting conditions Phase III (failure): rapid wear until complete failure, difficult to handle due to excessive wear accumulation Source: Tool wear analysis and improvement of cutting conditions using the high-pressure water-jet assistance when machining the Ti17 titanium alloy, Y. Ayed, Precision Engineering, Elsevier (2015) PRODUCTION AND ROBOTICS ENGINEERING PAGE | 52 Wear Mechanisms in Cutting Processes Tool wear Diffusion Abrasion Adhesion Oxidation Cutting temperature Source: Zerspannung der Eisenwerkstoffe, G. Vieregge, Strahleisen GmbH (1970) PRODUCTION AND ROBOTICS ENGINEERING PAGE | 53 Adhesion: Shearing-off of Atomically Bonded Chip/Tool Surfaces (Built-up Edge) Small crater wear due to smaller contact of the rake face with chips lifted off by BUE formation Cutting edge micro-chipping* due to frequently sheared-off BUE particles feasibly leading to delamination Flank* and notch wear + poor surface quality6 due to hard BUE particles scratching both surfaces adhesion wear 𝑣𝑣𝑐𝑐 = 10 m/min 𝑣𝑣𝑐𝑐 = 20 m/min 𝑣𝑣𝑐𝑐 = 30 m/min 𝑣𝑣𝑐𝑐 = 2 m/min 0.24 wear land, 𝑉𝑉𝑉𝑉 [mm] 0.20 Width of flank 0.16 0.12 0.08 0.04 0 Source: 1. Manufacturing Processes 1 - Cutting (RWTH edition), F. Klocke, Springer (2011) 1 2 3 5 10 20 30 50 100 2. Micromachining of Advanced Materials, W.N.P. Hung, Micromachining-IntechOpen (2019) Cutting speed, 𝑣𝑣𝑐𝑐 [m/min] PRODUCTION AND ROBOTICS ENGINEERING PAGE | 54 Cutting-Speed Dependent Flank Wear Given 𝑓𝑓, increasing 𝑣𝑣𝑐𝑐 to avoid BUE formation and thus diminishing the flank wear Given 𝑣𝑣𝑐𝑐 , increasing 𝑓𝑓 to avoid BUE formation and thus diminishing the flank wear Source: Manufacturing Processes 1 - Cutting (RWTH edition), F. Klocke, Springer (2011) PRODUCTION AND ROBOTICS ENGINEERING PAGE | 55 Abrasion (Mechanical Wear) The process, in which intermediate particles from the workpiece, chip, tool or BUE penetrate into the surface of the cutting tool material, make a tangential motion and leave grooves on the surfaces (crater wear & flank wear* & notch wear) Ductile Materials Brittle Materials Micro-plowing Micro-cutting Micro-cracks Plastic deformation Plastic deformation with No plastic deformation but without chips chips cracks with much bigger groove volume Source: Grundlagen des Verschleißes, G. Zum, VDI Report 600.3 (1987) PRODUCTION AND ROBOTICS ENGINEERING PAGE | 56 Diffusion (Chemical Instability) A chemical process, where, under high temperature and pressure, atoms of the tribological partner materials are diffused into each other, potentially weakening certain strength or hardness properties, thus reduction of wear resistance of cutting tools at high temperature (crater wear) (Ti, Ta, Ni, W)C WC-Co X6CrNiMoTi17-12-2 Cemented carbide Austenitic steel 60 Co-W-C binder 50 Mass ratio [%] W Fe Fe 40 Co Cr W 30 Ni 20 Co Tool Chip 10 0 WC dissolved into Fe3W3C, 5 0 5 (FeW)6C and (FeW)23C6 Distance from the contact surface [µm] Source: Manufacturing Processes 1 - Cutting (RWTH edition), F. Klocke, Springer (2011) PRODUCTION AND ROBOTICS ENGINEERING PAGE | 57 Oxidation (Scaling) A chemical reaction of the cutting material with the surrounding medium e.g. oxygen, forming oxidation films (scaled skin), either () enhancing wear resistance e.g. Al2O3 or () easily worn out e.g. WO3 in the form of coating delamination or notch wear* (grooves) on the depth of cut line around the contact zone Rake face Rake face Oxidation zone outside the contact zone where oxygen has access to Minor flank Minor flank Source: Sandvik Coromant PRODUCTION AND ROBOTICS ENGINEERING PAGE | 58 Surface Damage (Excessive Mechnaical and Thermal Loads) Cutting edge failure caused by mechanical and thermal overstress Cutting edge Plastic Cracks by Dynamic Loads chipping/breakage deformation Comp Large cutting force crack Striking chips Impact cutting Parallel crack Too small wedge (𝛽𝛽𝑜𝑜 ) or tool included (𝜀𝜀𝑟𝑟 ) angle Parallel Cracks Comb Cracks Fatigue caused Fatigue along the isotherms due by fluctuating to alternating thermal stress Thermo-mechanical mechanical Potential source of notch wear stress beyond the stress such as resulting from crack growth yield limit of the tool in milling material Cutting fluid favouring cracks Source: 1. Zerspannung der Eisenwerkstoffe, G. Vieregge, Strahleisen GmbH (1959), 2. Sandvik Coromant PRODUCTION AND ROBOTICS ENGINEERING PAGE | 59 Trouble Shooting on Tool Wear Crater ↗ ↓ 𝑣𝑣𝑐𝑐 ↘ Plastic ↗ ↓ 𝑣𝑣𝑐𝑐 → ↓ 𝑇𝑇 ↓ 𝑇𝑇 wear ↘ ↑ 𝑓𝑓 → ↓ chip length ↗ deformation ↘ ↓ 𝑓𝑓 → ↓ 𝐹𝐹 (m/min) Predictable stable flank wear Cutting speed BUE ↗ ↑ 𝑣𝑣𝑐𝑐 ↘ ↗ ↑ 𝑣𝑣𝑐𝑐 → ↑ T ↘ BUE ↓ BUE Chipping ↓ 𝐹𝐹 ↘ ↑ 𝑓𝑓 ↗ ↘ ↓ 𝑓𝑓 ↗ Feed (mm) Source: 1. Zerspannung der Eisenwerkstoffe, G. Vieregge, Strahleisen GmbH (1959), 2. Sandvik Coromant, 3. Seco PRODUCTION AND ROBOTICS ENGINEERING PAGE | 60 Thank Thank You You for So YourMuch for Attention Your Attention PRODUCTION AND ROBOTICS ENGINEERING PAGE | 61