ISO 15189:2022 Medical Laboratory PDF
Document Details
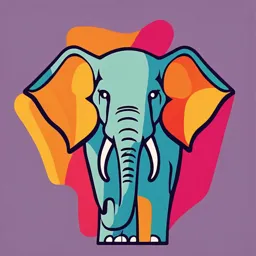
Uploaded by ConscientiousYew
2022
Tags
Summary
This document provides requirements for quality and competence in medical laboratories. It covers general requirements, structural and governance requirements, resource requirements, and process requirements. It is intended for laboratory users, regulatory authorities, and accreditation bodies.
Full Transcript
INTERNATIONAL ISO STANDARD 15189 Fourth edition 2022-12 Medical laboratories — Requirements for quali...
INTERNATIONAL ISO STANDARD 15189 Fourth edition 2022-12 Medical laboratories — Requirements for quality and competence Laboratoires de biologie médicale — Exigences concernant la qualité et la compétence Reference number ISO 15189:2022(E) © ISO 2022 ISO 15189:2022(E) COPYRIGHT PROTECTED DOCUMENT © ISO 2022 All rights reserved. Unless otherwise specified, or required in the context of its implementation, no part of this publication may be reproduced or utilized otherwise in any form or by any means, electronic or mechanical, including photocopying, or posting on the internet or an intranet, without prior written permission. Permission can be requested from either ISO at the address below or ISO’s member body in the country of the requester. ISO copyright office CP 401 Ch. de Blandonnet 8 CH-1214 Vernier, Geneva Phone: +41 22 749 01 11 Email: [email protected] Website: www.iso.org Published in Switzerland ii © ISO 2022 – All rights reserved ISO 15189:2022(E) Contents Page Foreword........................................................................................................................................................................................................................................ vi Introduction..............................................................................................................................................................................................................................vii 1 Scope.................................................................................................................................................................................................................................. 1 2 Normative references...................................................................................................................................................................................... 1 3 Terms and definitions..................................................................................................................................................................................... 1 4 General requirements..................................................................................................................................................................................... 8 4.1 Impartiality................................................................................................................................................................................................ 8 4.2 Confidentiality......................................................................................................................................................................................... 8 4.2.1 Management of information...................................................................................................................................... 8 4.2.2 Release of information................................................................................................................................................... 9 4.2.3 Personnel responsibility.............................................................................................................................................. 9 4.3 Requirements regarding patients.......................................................................................................................................... 9 5 Structural and governance requirements................................................................................................................................. 9 5.1 Legal entity................................................................................................................................................................................................. 9 5.2 Laboratory director......................................................................................................................................................................... 10 5.2.1 Laboratory director competence....................................................................................................................... 10 5.2.2 Laboratory director responsibilities.............................................................................................................. 10 5.2.3 Delegation of duties....................................................................................................................................................... 10 5.3 Laboratory activities....................................................................................................................................................................... 10 5.3.1 General...................................................................................................................................................................................... 10 5.3.2 Conformance with requirements...................................................................................................................... 10 5.3.3 Advisory activities.......................................................................................................................................................... 10 5.4 Structure and authority............................................................................................................................................................... 11 5.4.1 General...................................................................................................................................................................................... 11 5.4.2 Quality management..................................................................................................................................................... 11 5.5 Objectives and policies.................................................................................................................................................................. 11 5.6 Risk management............................................................................................................................................................................... 12 6 Resource requirements..............................................................................................................................................................................12 6.1 General......................................................................................................................................................................................................... 12 6.2 Personnel................................................................................................................................................................................................... 12 6.2.1 General...................................................................................................................................................................................... 12 6.2.2 Competence requirements...................................................................................................................................... 12 6.2.3 Authorization...................................................................................................................................................................... 13 6.2.4 Continuing education and professional development..................................................................... 13 6.2.5 Personnel records........................................................................................................................................................... 13 6.3 Facilities and environmental conditions....................................................................................................................... 13 6.3.1 General...................................................................................................................................................................................... 13 6.3.2 Facility controls................................................................................................................................................................. 14 6.3.3 Storage facilities............................................................................................................................................................... 14 6.3.4 Personnel facilities......................................................................................................................................................... 14 6.3.5 Sample collection facilities...................................................................................................................................... 14 6.4 Equipment................................................................................................................................................................................................. 15 6.4.1 General...................................................................................................................................................................................... 15 6.4.2 Equipment requirements.......................................................................................................................................... 15 6.4.3 Equipment acceptance procedure.................................................................................................................... 15 6.4.4 Equipment instructions for use.......................................................................................................................... 15 6.4.5 Equipment maintenance and repair............................................................................................................... 15 6.4.6 Equipment adverse incident reporting......................................................................................................... 16 6.4.7 Equipment records......................................................................................................................................................... 16 6.5 Equipment calibration and metrological traceability....................................................................................... 17 6.5.1 General...................................................................................................................................................................................... 17 6.5.2 Equipment calibration................................................................................................................................................. 17 © ISO 2022 – All rights reserved iii ISO 15189:2022(E) 6.5.3 Metrological traceability of measurement results............................................................................ 17 6.6 Reagents and consumables....................................................................................................................................................... 18 6.6.1 General...................................................................................................................................................................................... 18 6.6.2 Reagents and consumables — Receipt and storage.......................................................................... 18 6.6.3 Reagents and consumables — Acceptance testing............................................................................ 18 6.6.4 Reagents and consumables — Inventory management................................................................. 18 6.6.5 Reagents and consumables — Instructions for use.......................................................................... 19 6.6.6 Reagents and consumables — Adverse incident reporting....................................................... 19 6.6.7 Reagents and consumables — Records....................................................................................................... 19 6.7 Service agreements.......................................................................................................................................................................... 19 6.7.1 Agreements with laboratory users.................................................................................................................. 19 6.7.2 Agreements with POCT operators.................................................................................................................... 19 6.8 Externally provided products and services............................................................................................................... 20 6.8.1 General...................................................................................................................................................................................... 20 6.8.2 Referral laboratories and consultants.......................................................................................................... 20 6.8.3 Review and approval of externally provided products and services................................ 20 7 Process requirements.................................................................................................................................................................................. 21 7.1 General......................................................................................................................................................................................................... 21 7.2 Pre-examination processes....................................................................................................................................................... 21 7.2.1 General...................................................................................................................................................................................... 21 7.2.2 Laboratory information for patients and users.................................................................................... 21 7.2.3 Requests for providing laboratory examinations............................................................................... 21 7.2.4 Primary sample collection and handling.................................................................................................... 22 7.2.5 Sample transportation................................................................................................................................................ 23 7.2.6 Sample receipt.................................................................................................................................................................... 24 7.2.7 Pre-examination handling, preparation, and storage.................................................................... 24 7.3 Examination processes................................................................................................................................................................. 25 7.3.1 General...................................................................................................................................................................................... 25 7.3.2 Verification of examination methods............................................................................................................. 25 7.3.3 Validation of examination methods................................................................................................................ 25 7.3.4 Evaluation of measurement uncertainty (MU)..................................................................................... 26 7.3.5 Biological reference intervals and clinical decision limits......................................................... 26 7.3.6 Documentation of examination procedures............................................................................................ 27 7.3.7 Ensuring the validity of examination results......................................................................................... 27 7.4 Post-examination processes..................................................................................................................................................... 30 7.4.1 Reporting of results....................................................................................................................................................... 30 7.4.2 Post-examination handling of samples........................................................................................................ 32 7.5 Nonconforming work...................................................................................................................................................................... 33 7.6 Control of data and information management......................................................................................................... 33 7.6.1 General...................................................................................................................................................................................... 33 7.6.2 Authorities and responsibilities for information management............................................. 33 7.6.3 Information systems management.................................................................................................................. 34 7.6.4 Downtime plans................................................................................................................................................................ 34 7.6.5 Off site management..................................................................................................................................................... 34 7.7 Complaints............................................................................................................................................................................................... 34 7.7.1 Process...................................................................................................................................................................................... 34 7.7.2 Receipt of complaint...................................................................................................................................................... 35 7.7.3 Resolution of complaint.............................................................................................................................................. 35 7.8 Continuity and emergency preparedness planning............................................................................................ 35 8 Management system requirements............................................................................................................................................... 35 8.1 General requirements.................................................................................................................................................................... 35 8.1.1 General...................................................................................................................................................................................... 35 8.1.2 Fulfilment of management system requirements.............................................................................. 36 8.1.3 Management system awareness......................................................................................................................... 36 8.2 Management system documentation............................................................................................................................... 36 8.2.1 General...................................................................................................................................................................................... 36 8.2.2 Competence and quality............................................................................................................................................ 36 iv © ISO 2022 – All rights reserved ISO 15189:2022(E) 8.2.3 Evidence of commitment........................................................................................................................................... 36 8.2.4 Documentation.................................................................................................................................................................. 36 8.2.5 Personnel access............................................................................................................................................................... 36 8.3 Control of management system documents............................................................................................................... 37 8.3.1 General...................................................................................................................................................................................... 37 8.3.2 Control of documents................................................................................................................................................... 37 8.4 Control of records.............................................................................................................................................................................. 37 8.4.1 Creation of records......................................................................................................................................................... 37 8.4.2 Amendment of records............................................................................................................................................... 37 8.4.3 Retention of records...................................................................................................................................................... 38 8.5 Actions to address risks and opportunities for improvement................................................................... 38 8.5.1 Identification of risks and opportunities for improvement....................................................... 38 8.5.2 Acting on risks and opportunities for improvement....................................................................... 38 8.6 Improvement.......................................................................................................................................................................................... 39 8.6.1 Continual improvement............................................................................................................................................. 39 8.6.2 Laboratory patients, user, and personnel feedback.......................................................................... 39 8.7 Nonconformities and corrective actions....................................................................................................................... 39 8.7.1 Actions when nonconformity occurs............................................................................................................. 39 8.7.2 Corrective action effectiveness........................................................................................................................... 40 8.7.3 Records of nonconformities and corrective actions......................................................................... 40 8.8 Evaluations.............................................................................................................................................................................................. 40 8.8.1 General...................................................................................................................................................................................... 40 8.8.2 Quality indicators............................................................................................................................................................ 40 8.8.3 Internal audits.................................................................................................................................................................... 40 8.9 Management reviews...................................................................................................................................................................... 41 8.9.1 General...................................................................................................................................................................................... 41 8.9.2 Review input........................................................................................................................................................................ 41 8.9.3 Review output..................................................................................................................................................................... 41 Annex A (normative) Additional requirements for Point-of-Care Testing (POCT)..........................................43 Annex B (informative) Comparison between ISO 9001:2015 and ISO 15189:2022 (this document)................................................................................................................................................................................................................ 44 Annex C (informative) Comparison between ISO 15189:2012 and ISO 15189:2022 (this document).................................................................................................................................................................................................................54 Bibliography.............................................................................................................................................................................................................................. 61 © ISO 2022 – All rights reserved v ISO 15189:2022(E) Foreword ISO (the International Organization for Standardization) is a worldwide federation of national standards bodies (ISO member bodies). The work of preparing International Standards is normally carried out through ISO technical committees. Each member body interested in a subject for which a technical committee has been established has the right to be represented on that committee. International organizations, governmental and non-governmental, in liaison with ISO, also take part in the work. ISO collaborates closely with the International Electrotechnical Commission (IEC) on all matters of electrotechnical standardization. The procedures used to develop this document and those intended for its further maintenance are described in the ISO/IEC Directives, Part 1. In particular, the different approval criteria needed for the different types of ISO documents should be noted. This document was drafted in accordance with the editorial rules of the ISO/IEC Directives, Part 2 (see www.iso.org/directives). Attention is drawn to the possibility that some of the elements of this document may be the subject of patent rights. ISO shall not be held responsible for identifying any or all such patent rights. Details of any patent rights identified during the development of the document will be in the Introduction and/or on the ISO list of patent declarations received (see www.iso.org/patents). Any trade name used in this document is information given for the convenience of users and does not constitute an endorsement. For an explanation of the voluntary nature of standards, the meaning of ISO specific terms and expressions related to conformity assessment, as well as information about ISO's adherence to the World Trade Organization (WTO) principles in the Technical Barriers to Trade (TBT), see www.iso.org/iso/foreword.html. This document was prepared by Technical Committee ISO/TC 212, Clinical laboratory testing and in vitro diagnostic test systems, in collaboration with the European Committee for Standardization (CEN) Technical Committee CEN/TC 140, In vitro diagnostic medical devices, in accordance with the Agreement on technical cooperation between ISO and CEN (Vienna Agreement). This fourth edition cancels and replaces the third edition (ISO 15189:2012), which has been technically revised. It also replaces ISO 22870:2016. The main changes are as follows: — Alignment with ISO/IEC 17025:2017 resulted in the management requirements now appearing at the end of the document; — Requirements for point-of-care testing (POCT), previously in ISO 22870, have been incorporated; — Increased emphasis on risk management. Any feedback or questions on this document should be directed to the user’s national standards body. A complete listing of these bodies can be found at www.iso.org/members.html. vi © ISO 2022 – All rights reserved ISO 15189:2022(E) Introduction The objective of this document is to promote the welfare of patients and satisfaction of laboratory users through confidence in the quality and competence of medical laboratories. This document contains requirements for the medical laboratory to plan and implement actions to address risks and opportunities for improvement. Benefits of this approach include: increasing the effectiveness of the management system, decreasing probability of invalid results, and reducing potential harm to patients, laboratory personnel, the public and the environment. The requirements for risk management are aligned with the principles of ISO 22367. The requirements for laboratory safety are aligned with the principles of ISO 15190. The requirements for sample collection and transport are aligned with ISO 20658.1) This document contains the requirements for point-of-care testing (POCT) and supersedes ISO 22870, which will be withdrawn upon publication of this document. The format of this document is based on ISO/IEC 17025:2017. The medical laboratory is essential to patient care; activities are provided within an ethical and governance framework, that recognizes the obligations of healthcare providers to the patient. These activities are undertaken in a timely manner to meet the needs of all patients and the personnel responsible for the care of those patients. Activities include arrangements for examination requests, patient preparation, patient identification, collection of samples, transportation, processing of patient samples, selection of examinations that are fit for intended use, examination of samples, sample storage, as well as subsequent interpretation, result reporting and advice to laboratory users. This may also include the provision of results to the patient, arrangements for urgent testing and the notification of critical results. While this document is intended for use throughout the currently recognized medical laboratory disciplines, it can effectively be applied to other healthcare services, such as diagnostic imaging, respiratory therapy, physiological sciences, blood banks and transfusion services. The use of this document facilitates cooperation between medical laboratories and other healthcare services, assists in the exchange of information, and in the harmonization of methods and procedures. The comparability of patient examination results between medical laboratories, regardless of city or country, is facilitated when medical laboratories conform to this document. When a laboratory seeks accreditation, it should select an accreditation body which operates in accordance with ISO/IEC 17011, and which takes into account the particular requirements of medical laboratories. Comparisons between this document, ISO 9001:2015 and ISO/IEC 17025:2017 are in Annex B. The comparison of ISO 15189:2012 to ISO 15189:2022 (this document) is in Annex C. 1) First edition under preparation (previous edition was a Technical Specification). Stage at the time of publication: ISO/DIS 20658:2022. © ISO 2022 – All rights reserved vii INTERNATIONAL STANDARD ISO 15189:2022(E) Medical laboratories — Requirements for quality and competence 1 Scope This document specifies requirements for quality and competence in medical laboratories. This document is applicable to medical laboratories in developing their management systems and assessing their competence. It is also applicable for confirming or recognizing the competence of medical laboratories by laboratory users, regulatory authorities and accreditation bodies. This document is also applicable to point-of-care testing (POCT). NOTE International, national, or regional regulations or requirements can also apply to specific topics covered in this document. 2 Normative references The following documents are referred to in the text in such a way that some or all of their content constitutes requirements of this document. For dated references, only the edition cited applies. For undated references, the latest edition of the referenced document (including any amendments) applies. ISO/IEC Guide 99:2007, International vocabulary of metrology — Basic and general concepts and associated terms (VIM) NOTE ISO/IEC Guide 99 is also known as the Joint Committee for Guides in Metrology (JCGM) 200. ISO/IEC 17000:2020, Conformity assessment — Vocabulary and general principles ISO/IEC 17025:2017, General requirements for the competence of testing and calibration laboratories 3 Terms and definitions For the purposes of this document, the terms and definitions given in ISO/IEC Guide 99 and ISO/IEC 17000 and the following apply. ISO and IEC maintain terminology databases for use in standardization at the following addresses: — ISO Online browsing platform: available at https://w ww.iso.org/obp — IEC Electropedia: available at https://w ww.electropedia.org/ 3.1 bias measurement bias estimate of a systematic measurement error Note 1 to entry: This definition only applies to quantitative measurements [SOURCE: ISO/IEC Guide 99:2007, 2.18, modified — Note 1 to entry has been added.] © ISO 2022 – All rights reserved 1 ISO 15189:2022(E) 3.2 biological reference interval reference interval specified interval of the distribution of values taken from a biological reference population Note 1 to entry: A reference interval is commonly defined as the central 95% interval. Another size or an asymmetrical location of the reference interval could be more appropriate in particular cases. Note 2 to entry: A reference interval can depend upon the type of primary sample (3.25) and the examination procedure (3.9) used. Note 3 to entry: In some cases, only one biological reference limit is important, usually an upper limit, “x”, so that the corresponding biological reference interval would be less than or equal to “x”. Note 4 to entry: Terms such as ‘normal range’, ‘normal values’, and ‘clinical range’ are ambiguous and therefore discouraged. [SOURCE: ISO 18113-1:2022, 3.1.9, modified — The EXAMPLE has been removed.] 3.3 clinical decision limit examination (3.8) result that indicates a higher risk of adverse clinical outcomes, or is diagnostic for the presence of a specifc disease Note 1 to entry: Clinical decision limits for therapeutic drugs are called "therapeutic range". Note 2 to entry: It is used to determine risk of disease, to diagnose or to treat. 3.4 commutability of a reference material commutability property of a reference material, demonstrated by the closeness of agreement between the relation among the measurement results for a stated quantity in this material, obtained according to two given measurement procedures and the relation obtained among the measurement results for other specified materials Note 1 to entry: The reference material in question is usually a calibrator and the other specified materials are usually routine samples. Note 2 to entry: It is typical that there are more than two measurement procedures available and comparison among all applicable measurement procedures is desirable. Note 3 to entry: Closeness of agreement of measurement results is defined in terms of fitness for purpose as appropriate for the intended use of the reference material. Note 4 to entry: A commutability statement is restricted to the measurement procedures as specified in a particular comparison. [SOURCE: ISO 17511:2020 3.10, modified — Note 2 to entry has been replaced by a new Note 2 to entry.] 3.5 competence demonstrated ability to apply knowledge and skills to achieve intended results [SOURCE: ISO/IEC 17021-1:2015, 3.7, modified — "demonstrated" added to the beginning of the definition.] 2 © ISO 2022 – All rights reserved ISO 15189:2022(E) 3.6 complaint expression of dissatisfaction by any person or organization to a laboratory (3.20), relating to the activities or results of that laboratory, where a response is expected [SOURCE: ISO/IEC 17000:2020, 8.7, modified — The words “other than appeal” have been deleted, and the words “a conformity assessment body or accreditation body, relating to the activities of that body” have been replaced by “a laboratory, relating to the activities or results of that laboratory”.] 3.7 consultant person who provides expert advice professionally 3.8 examination set of operations having the objective of determining the numerical value, text value or characteristics of a property Note 1 to entry: An examination may be the total of a number of activities, observations or measurements required to determine a value or characteristic. Note 2 to entry: Laboratory examinations that determine a numerical value of a property are called "quantitative examinations"; those that determine the characteristics of a property are called "qualitative examinations". Note 3 to entry: Laboratory examinations are also called "assays" or "tests". 3.9 examination procedure specifically described set of operations used in the performance of an examination (3.8) according to a given method Note 1 to entry: In the IVD medical device industry and in many laboratories that use IVD medical devices, an examination procedure for an analyte in a biological sample is commonly referred to as an analytical method, analytical procedure or test procedure. [SOURCE: ISO 15198:2004, 3.7, modified — “set of operations described specifically” changed to “specifically described set of operations”.] 3.10 external quality assessment EQA evaluation of participant performance against pre-established criteria by means of interlaboratory comparisons Note 1 to entry: Also known as proficiency testing (PT) [SOURCE: ISO/IEC 17043:2010, 3.7 modified — The term “external quality assessment”, which was given in Note 2 to entry, is used as the main term. Notes to entry 1 and 2 have been omitted and a new Note 1 to entry added.] 3.11 impartiality objectivity with regard to the outcome of tasks performed by the medical laboratory (3.20) Note 1 to entry: Objectivity can be understood as freedom from bias or freedom from conflicts of interest. Note 2 to entry: Other terms that are useful in conveying the element of impartiality include “independence”, “lack of prejudice”, “neutrality”, “fairness”, “open-mindedness”, “even-handedness”, “detachment”, “balance”. [SOURCE: ISO/IEC 17000:2020 5.3 modified — “outcome of a conformity assessment activity” has been changed to “tasks performed by the medical laboratory”. Note 2 to entry has been added.] © ISO 2022 – All rights reserved 3 ISO 15189:2022(E) 3.12 interlaboratory comparison organization, performance and evaluation of measurements or examinations (3.8) on the same or similar materials by two or more independent laboratories in accordance with pre-determined conditions [SOURCE: ISO/IEC 17043:2010 3.4, modified — "tests" has been replaced by "examinations". "items" has been replaced by "materials". "laboratories" has been replaced by "independent laboratories".] 3.13 internal quality control IQC quality control QC internal procedure which monitors the testing process to verify the system is working correctly and gives confidence that the results are reliable enough to be released [SOURCE: ISO/TS 22583:2019 3.9, modified — “decide” has been replaced by “verify”. Note 1 to entry has been removed. ] 3.14 in vitro diagnostic medical device IVD medical device device, whether used alone or in combination, intended by the manufacturer for the in vitro examination of specimens derived from the human body solely or principally to provide information for diagnostic, monitoring or compatibility purposes and including reagents, calibrators, control materials, specimen receptacles, software, and related instruments or apparatus or other articles [SOURCE: ISO 18113-1:2022, 3.1.33, modified — "medical" has been removed from the beginning of the definition. "and including reagents, calibrators, control materials, specimen receptacles, software, and related instruments or apparatus or other articles" has been added to the end of the definition. Notes 1 and 2 to entry have been removed.] 3.15 laboratory management person(s) with responsibility for, and authority over a laboratory (3.20) Note 1 to entry: Laboratory management has the power to delegate authority and provide resources within the laboratory. Note 2 to entry: The laboratory management includes the laboratory director(s) and delegates together with individuals specifically assigned to ensure the quality of the activities of the laboratory. 3.16 laboratory user individual or entity requesting services of the medical laboratory (3.20) Note 1 to entry: Users can include patients, clinicians, and, other laboratories or institutions that send samples for examination. 3.17 management system set of interrelated or interacting elements of an organization to establish policies and objectives, and processes to achieve those objectives Note 1 to entry: This was formerly referred to and is synonymous with “quality management system”. Note 2 to entry: The management system elements establish the organization’s structure, roles and responsibilities, planning, operation, policies, practices, rules, beliefs, objectives, and processes to achieve those objectives. [SOURCE: ISO 9000:2015, 3.5.3 modified — Notes to entry 1, 3 and 4 have been removed and a new Note 1 to entry has been added.] 4 © ISO 2022 – All rights reserved ISO 15189:2022(E) 3.18 measurement accuracy accuracy of measurement accuracy closeness of agreement between a measured quantity value and a true quantity value of a measurand Note 1 to entry: The concept ‘measurement accuracy’ is not a quantity and is not given a numerical quantity value. A measurement is said to be more accurate when it offers a smaller measurement error. Note 2 to entry: The term “measurement accuracy” should not be used for measurement trueness and the term measurement precision should not be used for ‘measurement accuracy’, which, however, is related to both these concepts. Note 3 to entry: ‘Measurement accuracy’ is sometimes understood as closeness of agreement between measured quantity values that are being attributed to the measurand. [SOURCE: ISO/IEC Guide 99:2007, 2.13] 3.19 measurement uncertainty MU non-negative parameter characterizing the dispersion of the quantity values being attributed to a measurand, based on the information used Note 1 to entry: MU includes components arising from systematic effects, as in the case of corrections to the assigned quantity values of measurement standards. Sometimes estimated systematic effects are not corrected for, but instead, the associated MU components are incorporated. Note 2 to entry: The parameter may be, for example, a standard deviation (SD) called standard MU (or a specified multiple of it), or the half-width of an interval, having a stated coverage probability. Note 3 to entry: MU comprises, in general, of many components. Some of these may be evaluated by Type A evaluation of MU from the statistical distribution of the quantity values from series of measurements and can be characterized by SD. The other components, which may be evaluated by Type B evaluation of MU, can also be characterized by SD or evaluated from probability density functions based on experience or other information. Note 4 to entry: In general, for a given set of information, it is understood that the MU is associated with a stated quantity value attributed to the measurand. A modification of this value may result in a modification of the associated uncertainty. Note 5 to entry: All measurements have bias (3.1) and imprecision. For example, replicate measurements of a sample performed under repeatability conditions generally produce different values for the same measurand. Because the different values could all be reasonably attributed to the same amount of measurand, there is uncertainty as to which value should be reported as the value of the measurand. Note 6 to entry: Based on available data about the analytical performance of a given measurement procedure, an estimation of MU provides an interval of values that is believed to include the actual value of the measurand, with a stated level of confidence. Note 7 to entry: Available data about the analytical performance of a given measurement procedure typically comprise uncertainty of calibrator assigned values and long-term imprecision of IQC materials. Note 8 to entry: In medical laboratories, most measurements are performed in singleton, and are taken to be an acceptable estimate of the value of the measurand, while the MU interval indicates other results that are also possible. [SOURCE: ISO/IEC Guide 99:2007 2.26, modified — Notes to entry 5 to 8 have been added from ISO/TS 20914:2019 3.26.] © ISO 2022 – All rights reserved 5 ISO 15189:2022(E) 3.20 medical laboratory laboratory entity for the examination (3.8) of materials derived from the human body for the purpose of providing information for the diagnosis, monitoring, management, prevention and treatment of disease, or assessment of health Note 1 to entry: The laboratory can also provide advice covering all aspects of examinations including appropriate selection, the interpretation of results and advice on further examinations. Note 2 to entry: Laboratory activities include pre-examination (3.24), examination (3.8) and post-examination processes (3.23). Note 3 to entry: Materials for examination (3.8) include but are not limited to, microbiological, immunological, biochemical, immunohaematological, haematological, biophysical, cytological, tissue and cells, and genetic material. 3.21 patient person who is the source of material for an examination (3.8) 3.22 point-of-care testing POCT examination (3.8) performed near or at the site of a patient (3.21) [SOURCE: ISO/TS 22583:2019, 3.11] 3.23 post-examination processes processes following the examination (3.8) including review of results, formatting, releasing, reporting and retention of examination results, retention and storage of clinical material, sample (3.28) and waste disposal 3.24 pre-examination processes processes that start, in chronological order, from the user’s request and include the examination (3.8) request, preparation and identification of the patient (3.21), collection of the primary sample(s) (3.25), transportation to and within the laboratory (3.20), ending when the examination (3.8) begins 3.25 primary sample specimen discrete portion of a body fluid or tissue or other sample associated with the human body taken for examination (3.8), study or analysis of one or more quantities or characteristics to determine the character of the whole Note 1 to entry: The International Medical Device Regulators Forum (IMDRF) uses the term specimen in its harmonized guidance documents to mean a sample of biological origin intended for examination by a medical laboratory (3.20). [SOURCE: ISO 18113-1:2022, 3.1.65, modified — Note 1 to entry has been modified. Note 2 to entry has been deleted.] 3.26 quality indicator measure of the degree to which a large number of characteristics of an object fulfils requirements Note 1 to entry: Measure can be expressed, for example, as % yield (% within specified requirements), % defects (% outside specified requirements), defects per million occasions (DPMO) or on the Six Sigma scale. 6 © ISO 2022 – All rights reserved ISO 15189:2022(E) Note 2 to entry: Quality indicators can measure how well an organization meets the needs and requirements of users and the quality of all operational processes. 3.27 referral laboratory external laboratory (3.20) to which a sample or data is submitted for examination (3.8) Note 1 to entry: A referral laboratory is one to which laboratory management chooses to submit a sample or sub- sample for examination, data for analysis or interpretation, or when routine examinations cannot be carried out. Note 2 to entry: This differs from a laboratory to which submission of samples is required by regulation, or a so called reference laboratory, e.g. public health, forensic, tumour registry, or a central (parent) facility to which submission of samples is required by structure. 3.28 sample one or more parts taken from a primary sample (3.25) 3.29 trueness measurement trueness closeness of agreement between the average of an infinite number of replicate measured quantity values and a reference quantity value Note 1 to entry: Measurement trueness is not a quantity and thus cannot be expressed numerically, but measures for closeness of agreement are given in ISO 5725-1. Note 2 to entry: Measurement trueness is inversely related to systematic measurement error, but is not related to random measurement error. Note 3 to entry: ‘Measurement accuracy” should not be used for ‘measurement trueness’. Note 4 to entry: For qualitative examinations, trueness of measurement (closeness of agreement) can be expressed in terms of concordance (i.e. percent agreement with a reference examination). Note 5 to entry: Trueness is a property of the examination procedure (3.9) that reflects the bias (3.1) of the measurements from the expected or target value. It is described qualitatively as good or bad. An examination procedure (3.9) has good trueness if the bias (3.1) of the measurements is acceptable. [SOURCE: ISO/IEC Guide 99:2007, 2.14, modified — Notes to entry 4 and 5 have been added.] 3.30 turnaround time elapsed time between two specified points through pre-examination (3.24), examination (3.8), and post- examination processes (3.23) 3.31 validation confirmation of plausibility for a specific intended use or application through the provision of objective evidence that specified requirements have been fulfilled Note 1 to entry: Objective evidence can be obtained through observation, measurement, examination or by other means. Note 2 to entry: The word “validated” is used to designate the corresponding status. Note 3 to entry: Specified requirements of an examination method may include the following performance specifications: measurement trueness, measurement precision including measurement repeatability, and measurement intermediate precision, analytical specificity, including interfering substances, detection limit and quantitation limit, measuring interval, clinical relevance, diagnostic specificity and diagnostic sensitivity. [SOURCE: ISO/IEC 17000:2020, 6.5, modified — Notes 1 to 3 to entry have been added.] © ISO 2022 – All rights reserved 7 ISO 15189:2022(E) 3.32 verification confirmation of truthfulness, through the provision of objective evidence that specified requirements have been fulfilled EXAMPLE 1 Confirmation that performance specifications of a measuring system are achieved. EXAMPLE 2 Confirmation that a target measurement uncertainty can be met. Note 1 to entry: Verification is the process by which the laboratory confirms that the established performance claims of a measuring system, e.g. trueness, precision, reportable range, can be replicated in the laboratory before human sample examination is performed. Note 2 to entry: The objective evidence needed for a verification can be the results of an inspection, or other forms of determination, such as performing alternative calculations or reviewing documents. Note 3 to entry: Verification may be sufficient to implement a new IVD device under circumstances where the examination (3.8) is performed and used in the manner as directed in the package insert. Note 4 to entry: The word “verified” is used to designate the corresponding status. [SOURCE: ISO/IEC 17000:2020, 6.6 modified — EXAMPLES 1 and 2 have been added. Notes to entry 1 to 4 have been added.] 4 General requirements 4.1 Impartiality a) Laboratory activities shall be undertaken impartially. The laboratory shall be structured and managed to safeguard impartiality. b) The laboratory management shall be committed to impartiality. c) The laboratory shall be responsible for the impartiality of its laboratory activities and shall not allow commercial, financial or other pressures to compromise impartiality. d) The laboratory shall monitor its activities and its relationships to identify threats to its impartiality. This monitoring shall include relationships of its personnel. NOTE A relationship that threatens the impartiality of the laboratory can be based on ownership, governance, management, personnel, shared resources, finances, contracts, marketing (including branding), and payment of a sales commission or other inducement for the referral of new laboratory users, etc. Such relationships do not necessarily present the laboratory with a threat to impartiality. e) If a threat to impartiality is identified, the effect shall be eliminated or minimized so that the impartiality is not compromised. The laboratory shall be able to demonstrate how it mitigates such threat. 4.2 Confidentiality 4.2.1 Management of information The laboratory shall be responsible, through legally enforceable agreements, for the management of all patient information obtained or created during the performance of laboratory activities. Management of patient information shall include privacy and confidentiality. The laboratory shall inform the user and/or the patient in advance, of the information it intends to place in the public domain. Except for information that the user and/or the patient makes publicly available, or when agreed between the laboratory and the patient (e.g. for the purpose of responding to complaints), all other information is considered proprietary information and shall be regarded as confidential. 8 © ISO 2022 – All rights reserved ISO 15189:2022(E) 4.2.2 Release of information When the laboratory is required by law or authorized by contractual arrangements to release confidential information, the patient concerned shall be notified of the information released, unless prohibited by law. Information about the patient from a source other than the patient (e.g. complainant, regulator) shall be kept confidential by the laboratory. The identity of the source shall be kept confidential by the laboratory and shall not be shared with the patient, unless agreed by the source. 4.2.3 Personnel responsibility Personnel, including any committee members, contractors, personnel of external bodies, or individuals with access to laboratory information acting on the laboratory’s behalf, shall keep confidential all information obtained or created during the performance of laboratory activities. 4.3 Requirements regarding patients Laboratory management shall ensure that patients’ well-being, safety and rights are the primary considerations. The laboratory shall establish and implement the following processes: a) opportunities for patients and laboratory users to provide helpful information to aid the laboratory in the selection of the examination methods, and the interpretation of the examination results; b) provision of patients and users with publicly available information about the examination process, including costs when applicable, and when to expect results; c) periodic review of the examinations offered by the laboratory to ensure they are clinically appropriate and necessary; d) where appropriate, disclosure to patients, users and any other relevant persons, of incidents that resulted or could have resulted in patient harm, and records of actions taken to mitigate those harms; e) treatment of patients, samples, or remains, with due care and respect; f) obtaining informed consent when required; g) ensuring the ongoing availability and integrity of retained patient samples and records in the event of the closure, acquisition or merger of the laboratory; h) making relevant information available to a patient and any other health service provider at the request of the patient or the request of a healthcare provider acting on their behalf; i) upholding the rights of patients to care that is free from discrimination. 5 Structural and governance requirements 5.1 Legal entity The laboratory or the organization of which the laboratory is a part shall be an entity that can be held legally responsible for its activities. NOTE For the purposes of this document, a government laboratory is deemed to be a legal entity on the basis of its government status. © ISO 2022 – All rights reserved 9 ISO 15189:2022(E) 5.2 Laboratory director 5.2.1 Laboratory director competence The laboratory shall be directed by a person, or persons however named, with the specified qualifications, competence, delegated authority, responsibility, and resources to fulfil the requirements of this document. 5.2.2 Laboratory director responsibilities The laboratory director is responsible for the implementation of the management system, including the application of risk management to all aspects of the laboratory operations so that risks to patient care and opportunities to improve are systematically identified and addressed. The duties and responsibilities of the laboratory director shall be documented. 5.2.3 Delegation of duties The laboratory director may delegate either selected duties or responsibilities, or both, to qualified and competent personnel and such delegation shall be documented. However, the laboratory director shall maintain the ultimate responsibility for the overall operation of the laboratory. 5.3 Laboratory activities 5.3.1 General The laboratory shall specify and document the range of laboratory activities, including laboratory activities performed at sites other than the main location (e.g. POCT, sample collection) for which it conforms with this document. The laboratory shall only claim conformity with this document for this range of laboratory activities, which excludes externally provided laboratory activities on an ongoing basis. 5.3.2 Conformance with requirements Laboratory activities shall be carried out in such a way as to meet the requirements of this document, the users, regulatory authorities and organizations providing recognition. This applies to the complete range of specified and documented laboratory activities, regardless of where the service is provided. 5.3.3 Advisory activities Laboratory management shall ensure that appropriate laboratory advice and interpretation are available and meet the needs of patients and users. The laboratory shall establish arrangements for communicating with laboratory users on the following when applicable: a) advising on choice and use of examinations, including required type of sample, clinical indications and limitations of examination methods, and the frequency of requesting the examination; b) providing professional judgments on the interpretation of the results of examinations; c) promoting the effective utilization of laboratory examinations; d) advising on scientific and logistical matters such as instances of failure of sample(s) to meet acceptability criteria. 10 © ISO 2022 – All rights reserved ISO 15189:2022(E) 5.4 Structure and authority 5.4.1 General The laboratory shall: a) define its organization and management structure, its place in any parent organization, and the relationships between management, technical operations and support services; b) specify the responsibility, authority, lines of communication and interrelationship of all personnel who manage, perform or verify work affecting the results of laboratory activities; c) specify its procedures to the extent necessary to ensure the consistent application of its laboratory activities and the validity of the results. 5.4.2 Quality management The laboratory shall have personnel who, irrespective of other responsibilities, have the authority and resources needed to carry out their duties, including: a) implementation, maintenance and improvement of the management system; b) identification of deviations from the management system or from the procedures for performing laboratory activities; c) initiation of actions to prevent or minimize such deviations; d) reporting to laboratory management on the performance of the management system and any need for improvement; e) ensuring the effectiveness of laboratory activities. NOTE These responsibilities can be assigned to one or more persons. 5.5 Objectives and policies a) Laboratory management shall establish and maintain objectives and policies (see 8.2) to: 1) meet the needs and requirements of its patients and users; 2) commit to good professional practice; 3) provide examinations that fulfil their intended use; 4) conform to this document. b) Objectives shall be measurable, and consistent with policies. The laboratory shall ensure that the objectives and policies are implemented at all levels of the laboratory organization. c) Laboratory management shall ensure that the integrity of the management system is maintained when changes to the management system are planned and implemented. d) The laboratory shall establish quality indicators to evaluate performance throughout key aspects of pre-examination, examination, and post-examination processes and monitor performance in relation to objectives (see 8.8.2). NOTE Types of quality indicators include the number of unacceptable samples relative to the number received, the number of errors at either registration or sample receipt, or both, the number of corrected reports, the rate of achievement of specified turnaround times. © ISO 2022 – All rights reserved 11 ISO 15189:2022(E) 5.6 Risk management a) Laboratory management shall establish, implement, and maintain processes for identifying risks of harm to patients and opportunities for improved patient care associated with its examinations and activities, and develop actions to address both risks and opportunities for improvement (see 8.5). b) The laboratory director shall ensure that these processes are evaluated for effectiveness and modified, when identified as being ineffective. NOTE 1 ISO 22367 provides details for managing risk in medical laboratories. NOTE 2 ISO 35001 provides details for laboratory biorisk management. 6 Resource requirements 6.1 General The laboratory shall have available the personnel, facilities, equipment, reagents, consumables and support services necessary to manage and perform its activities. 6.2 Personnel 6.2.1 General a) The laboratory shall have access to a sufficient number of competent persons to perform its activities. b) All personnel of the laboratory, either internal or external, that could influence the laboratory activities shall act impartially, ethically, be competent and work in accordance with the laboratory’s management system. NOTE ISO/TS 22583 provides guidance for supervisors and operators of POCT equipment. c) The laboratory shall communicate to laboratory personnel the importance of meeting the needs and requirements of users as well as the requirements of this document. d) The laboratory shall have a programme to introduce personnel to the organization, the department or area in which the person will work, the terms and conditions of employment, staff facilities, health and safety requirements, and occupational health services. 6.2.2 Competence requirements a) The laboratory shall specify the competence requirements for each function influencing the results of laboratory activities, including requirements for education, qualification, training, re-training, technical knowledge, skills and experience. b) The laboratory shall ensure all personnel have the competence to perform laboratory activities for which they are responsible. c) The laboratory shall have a process for managing competence of its personnel, that includes requirements for frequency of competence assessment. d) The laboratory shall have documented information demonstrating competence of its personnel. NOTE Examples of competence assessment methods that can be used in any combination include: — direct observation of an activity, — monitoring the recording and reporting of examination results, 12 © ISO 2022 – All rights reserved ISO 15189:2022(E) — review of work records, — assessment of problem-solving skills, — examination of specially provided samples, e.g. previously examined samples, interlaboratory comparison materials, or split samples. 6.2.3 Authorization The laboratory shall authorize personnel to perform specific laboratory activities, including but not limited to, the following: a) selection, development, modification, validation and verification of methods; b) review, release, and reporting of results; c) use of laboratory information systems, in particular: accessing patient data and information, entering patient data and examination results, changing patient data or examination results. 6.2.4 Continuing education and professional development A continuing education programme shall be available to personnel who participate in managerial and technical processes. All personnel shall participate in continuing education and regular professional development, or other professional liaison activities. The suitability of the programmes and activities shall be periodically reviewed. 6.2.5 Personnel records The laboratory shall have procedures and retain records for: a) determining the competence requirements specified in 6.2.2 a); b) position descriptions; c) training and re-training; d) authorization of personnel; e) monitoring competence of personnel. 6.3 Facilities and environmental conditions 6.3.1 General The facilities and environmental conditions shall be suitable for the laboratory activities and shall not adversely affect the validity of results, or the safety of patients, visitors, laboratory users, and personnel. This shall include pre-examination related facilities and sites other than the main laboratory premises where examinations are performed, as well as POCT. The requirements for facilities and environmental conditions necessary for the performance of the laboratory activities shall be specified, monitored, and recorded. NOTE 1 ISO 15190 provides details for facility and environmental conditions. NOTE 2 Environmental conditions that can adversely affect the validity of results include, but are not limited to: adventitious amplified nucleic acid, microbial contamination, dust, electromagnetic disturbances, radiation, lighting conditions (illumination), humidity, electrical supply, temperature, sound and vibration. © ISO 2022 – All rights reserved 13 ISO 15189:2022(E) 6.3.2 Facility controls Facility controls shall be implemented, recorded, monitored, periodically reviewed, and shall include: a) control of access, taking into consideration safety, confidentiality, quality, and safeguarding medical information and patient samples; b) prevention of contamination, interference, or adverse influences on laboratory activities that can arise from energy sources, lighting, ventilation, noise, water and waste disposal; c) prevention of cross-contamination, where examination procedures pose a risk, or where work can be affected or influenced by lack of separation; d) provision of safety facilities and devices, where applicable and regularly verifying their functioning; EXAMPLES The operation of emergency release, intercom and alarm systems for cold rooms and walk-in freezers, accessibility of emergency showers, eyewash and resuscitation equipment. e) maintenance of laboratory facilities in a functional and reliable condition. 6.3.3 Storage facilities a) Storage space, with conditions that ensure the continuing integrity of samples, equipment, reagents, consumables, documents and records, shall be provided. b) Patient samples and materials used in examination processes shall be stored in a manner that prevents cross contamination and deterioration. c) Storage and disposal facilities for hazardous materials and biological waste shall be appropriate to the classification of the materials in the context of any statutory or regulatory requirements. 6.3.4 Personnel facilities There shall be adequate access to toilet facilities and a supply of drinking water, as well as facilities for storage of personal protective equipment and clothing. Space for personnel activities, such as meetings, quiet study and a rest area, should be provided. 6.3.5 Sample collection facilities Sample collection facilities shall: a) enable collection to be undertaken in a manner that does not invalidate results or adversely affect the quality of examinations; b) consider privacy, comfort and needs (e.g. disabled access, toilet facility) of patients and accommodation of accompanying persons (e.g. guardian or interpreter) during collection; c) provide separate patient reception and collection areas; d) maintain first aid materials for both patients and personnel. NOTE ISO 20658 provides details for sample collection facilities. 14 © ISO 2022 – All rights reserved ISO 15189:2022(E) 6.4 Equipment 6.4.1 General The laboratory shall have processes for the selection, procurement, installation, acceptance testing (including acceptability criteria), handling, transport, storage, use, maintenance, and decommissioning of equipment, in order to ensure proper functioning and to prevent contamination or deterioration. NOTE Laboratory equipment includes hardware and software of instruments, measuring systems, and laboratory information systems, or any equipment that influences the results of laboratory activities, including sample transportation systems. 6.4.2 Equipment requirements a) The laboratory shall have access to equipment required for the correct performance of laboratory activities. b) Where the equipment is used outside the laboratory's permanent control, or equipment manufacturer's functional specification, laboratory management shall ensure that the requirements of this document are met. c) Each item of equipment that can influence laboratory activities shall be uniquely labelled, marked or otherwise identified and a register maintained. d) The laboratory shall maintain and replace equipment as needed to ensure the quality of examination results. 6.4.3 Equipment acceptance procedure The laboratory shall verify that the equipment conforms to specified acceptability criteria before being placed or returned into service. Equipment used for measurement shall be capable of achieving either the measurement accuracy or measurement uncertainty, or both, required to provide a valid result (see 7.3.3 and 7.3.4 for details). NOTE 1 This includes equipment used in the laboratory, equipment on loan, or equipment used in point of care settings, or in associated or mobile facilities, authorized by the laboratory. NOTE 2 The verification of equipment acceptance testing can be, where relevant, based on the calibration certificate of the returned equipment. 6.4.4 Equipment instructions for use a) The laboratory shall have appropriate safeguards to prevent unintended adjustments of equipment that can invalidate examination results. b) Equipment shall be operated by trained, authorized, and competent personnel. c) Instructions for the use of equipment, including those provided by the manufacturer, shall be readily available. d) The equipment shall be used as specified by the manufacturer, unless validated by the laboratory (see 7.3.3). 6.4.5 Equipment maintenance and repair a) The laboratory shall have preventive maintenance programmes, based on manufacturer’s instructions. Deviations from the manufacturer's schedules or instructions shall be recorded. © ISO 2022 – All rights reserved 15 ISO 15189:2022(E) b) Equipment shall be maintained in a safe working condition and working order. This shall include electrical safety, any emergency stop devices and the safe handling and disposal of hazardous materials by authorized personnel. c) Equipment that is defective or outside specified requirements, shall be taken out of service. It shall be clearly labelled or marked as being out of service, until it has been verified to perform correctly. The laboratory shall examine the effect of the defect or deviation from specified requirements and shall initiate actions when non-conforming work occurs (see 7.5). d) When applicable, the laboratory shall decontaminate equipment before service, repair or decommissioning, provide suitable space for repairs and provide appropriate personal protective equipment. 6.4.6 Equipment adverse incident reporting Adverse incidents and accidents that can be attributed directly to specific equipment shall be investigated and reported to either the manufacturer or supplier, or both, and appropriate authorities, as required. The laboratory shall have procedures for responding to any manufacturer's recall or other notice, and taking actions recommended by the manufacturer. 6.4.7 Equipment records Records shall be maintained for each item of equipment that influences the results of laboratory activities. These records shall include the following, where relevant: a) manufacturer and supplier details, and sufficient information to uniquely identify each item of equipment, including software and firmware; b) dates of receipt, acceptance testing and entering into service; c) evidence that equipment conforms with specified acceptability criteria; d) the current location; e) condition when received (e.g. new, used or reconditioned); f) manufacturer's instructions; g) the programme for preventive maintenance; h) any maintenance activities performed by the laboratory or approved external service provider; i) damage to, malfunction, modification, or repair of the equipment; j) equipment performance records such as reports or certificates of calibrations or verifications, or both, including dates, times and results; k) status of the equipment such as active or in-service, out-of-service, quarantined, retired or obsolete. These records shall be maintained and shall be readily available for the lifespan of the equipment or longer, as specified in 8.4.3. 16 © ISO 2022 – All rights reserved ISO 15189:2022(E) 6.5 Equipment calibration and metrological traceability 6.5.1 General The laboratory shall specify calibration and traceability requirements that are sufficient to maintain consistent reporting of examination results. For quantitative methods of a measured analyte, specifications shall include calibration and metrological traceability requirements. Qualitative methods and quantitative methods that measure characteristics rather than discrete analytes shall specify the characteristic being assessed and such requirements necessary for reproducibility over time. NOTE Examples of qualitative methods and quantitative methods that may not allow metrological traceability include red cell antibody detection, antibiotic sensitivity assessment, genetic testing, erythrocyte sedimentation rate, flow cytometry marker staining, and tumour HER2 immunohistochemical staining. 6.5.2 Equipment calibration The laboratory shall have procedures for the calibration of equipment that directly or indirectly affects examination results. The procedures shall specify: a) conditions of use and manufacturer's instructions for calibration; b) recording of the metrological traceability; c) verification of the required measurement accuracy and the functioning of the measuring system at specified intervals; d) recording the calibration status and date of re-calibration; e) ensuring that, where correction factors are used, these are updated and recorded when re- calibration occurs; f) handling of situations when calibration was out of control, to minimize risk to service operation and to patients. 6.5.3 Metrological traceability of measurement results a) The laboratory shall establish and maintain metrological traceability of its measurement results by means of a documented unbroken chain of calibrations, each contributing to the measurement uncertainty, linking them to an appropriate reference. NOTE Information of traceability to a higher order reference material or reference procedure can be provided by an examination system manufacturer. Such documentation is acceptable only when the manufacturer's examination system and calibration procedures are used without modification. b) The laboratory shall ensure that measurement results are traceable to the highest possible level of traceability and to the International System of Units (SI) through: — calibration provided by a competent laboratory; or NOTE 1 Calibration laboratories fulfilling the requirements of ISO/IEC 17025 are considered competent for performing calibrations. — certified values of certified reference materials provided by a competent producer with stated metrological traceability to the SI; NOTE 2 Reference material producers fulfilling the requirements of ISO 17034 are considered to be competent. NOTE 3 Certified reference material fulfilling the requirements of ISO 15194 are considered suitable. © ISO 2022 – All rights reserved 17 ISO 15189:2022(E) c) Where it is not possible to provide traceability according to 6.5.3 a), other means for providing confidence in the results shall be applied, including but not limited to the following: — results of reference measurement procedures, specified methods or consensus standards, that are clearly described and accepted as providing measurement results fit for their intended use and ensured by suitable comparison; — measurement of calibrator by another procedure. NOTE ISO 17511 provides further information on how to manage the compromises in the metrological traceability of measurands. d) For genetic examinations, traceability to genetic reference sequences shall be established. e) For qualitative methods, traceability may be demonstrated by testing of known material or previous samples sufficient to show consistent identification and, when applicable, intensity of reaction. 6.6 Reagents and consumables 6.6.1 General The laboratory shall have processes for the selection, procurement, reception, storage, acceptance testing and inventory management of reagents and consumables. NOTE Reagents include substances which are commercially supplied or prepared in-house, reference materials (calibrators and QC materials), culture media; consumables include pipette tips, glass slides, POCT supplies etc. 6.6.2 Reagents and consumables — Receipt and storage The laboratory shall store reagents and consumables according to manufacturers' specifications and monitor the environmental conditions where relevant. When the laboratory is not the receiving facility, it shall verify that the receiving facility has adequate storage and handling capabilities to maintain supplies in a manner that prevents damage and deterioration. 6.6.3 Reagents and consumables — Acceptance testing Each reagent or new formulation of examination kits with changes in reagents or procedure, or a new lot or shipment, shall be verified for performance before placing into use, or before release of results, as appropriate. Consumables that can affect the quality of examinations shall be verified for performance before placing into use. NOTE 1 Comparative IQC performance of new reagent lots and that of previous lots can be used as evidence for acceptance (see 7.3.7.2). Patient samples are preferred when comparing different reagent lots to avoid issues with commutability of IQC materials. NOTE 2 Verification can sometimes be based on the certificate of analysis of the reagent. 6.6.4 Reagents and consumables — Inventory management The laboratory shall establish an inventory management system for reagents and consumables. The system for inventory management shall segregate reagents and consumables that have been accepted for use from those that have been neither inspected nor accepted for use. 18 © ISO 2022 – All rights reserved ISO 15189:2022(E) 6.6.5 Reagents and consumables — Instructions for use Instructions for the use of reagents and consumables, including those provided by manufacturers, shall be readily available. Reagents and consumables shall be used according to the manufacturer's specifications. If they are intended to be used for other purposes see 7.3.3. 6.6.6 Reagents and consumables — Adverse incident reporting Adverse incidents and accidents that can be attributed directly to specific reagents or consumables shall be investigated and reported to either the manufacturer or supplier, or both, and appropriate authorities, as required. The laboratory shall have procedures for responding to any manufacturer's recall or other notice and taking actions recommended by the manufacturer. 6.6.7 Reagents and consumables — Records Records shall be maintained for each reagent and consumable that contributes to the performance of examinations. These records shall include, but not be limited, to the following: a) identity of the reagent or consumable; b) manufacturer's information, including instructions, name and batch code or lot number; c) date of receipt and condition when received, the expiry date, date of first use and, where applicable, the date the reagent or consumable was taken out of service; d) records that confirm the reagent's or consumable's initial and ongoing acceptance for use. Where the laboratory uses reagents prepared, resuspended or combined in-house, the records shall include, in addition to the relevant information above, reference to the person or persons undertaking the preparation, as well as the dates of preparation and expiry. 6.7 Service agreements 6.7.1 Agreements with laboratory users The laboratory shall have a procedure to establish and periodically review agreements for providing laboratory activities. The procedure shall ensure: a) the requirements are adequately specified; b) the laboratory has the capability and resources to meet the requirements; c) when applicable, the laboratory advises the user of the specific activities to be performed by referral laboratories and consultants. Laboratory users shall be informed of any changes to an agreement that can affect examination results. Records of reviews, including any significant changes, shall be retained. 6.7.2 Agreements with POCT operators Service agreements between the laboratory and other parts of the organization using laboratory supported POCT, shall ensure that respective responsibilities and authorities are specified and communicated. NOTE Established multidisciplinary POCT committees can be used to manage such service agreements as described in Annex A. © ISO 2022 – All rights reserved 19 ISO 15189:2022(E) 6.8 Externally provided products and services 6.8.1 General The laboratory shall ensure that externally provided products and services that affect laboratory activities are suitable when such products and services are: a) intended for incorporation into the laboratory's own activities; b) provided, in part or in full, directly to the user by the laboratory, as received from the external provider; c) used to support the operation of the laboratory. It can be necessary to collaborate with other organizational departments or functions to fulfil this requirement. NOTE Services include, e.g. sample collection services, pipette and other calibration services, facility and equipment maintenance services, EQA programmes, referral laboratories and consultants. 6.8.2 Referral laboratories and consultants The laboratory shall communicate its requirements to referral laboratories and consultants who provide interpretations and advice, for: a) the procedures, examinations, reports and consulting activities to be provided; b) management of critical results; c) any required personnel qualifications and demonstration of competence. Unless otherwise specified in the agreement, the referring laboratory (and not the referral laboratory) shall be responsible for ensuring that examination results of the referral laboratory are provided to the person making the request. A list of all referral laboratories and consultants shall be maintained. 6.8.3 Review and approval of externally provided products and services The laboratory shall have procedures and retain records for: a) defining, reviewing, and approving the laboratory's requirements for all externally provided products and services; b) defining the criteria for qualification, selection, evaluation of performance and re-evaluation of external providers; c) referral of samples; d) ensuring that externally provided products and services conform to the laboratory's established requirements, or where applicable to the relevant requirements of this document, before they are used or directly provided to the user; e) taking any actions arising from evaluations of the performance of external providers. 20 © ISO 2022 – All rights reserved ISO 15189:2022(E) 7 Process requirements 7.1 General The laboratory shall identify potential risks to patient care in the pre-examination, examination and post-examination processes. These risks shall be assessed and mitigated to the extent possible. The residual risk shall be communicated to users as appropriate. The identified risks and effectiveness of the mitigation processes shall be monitored and evaluated according to the potential harm to the patient. The laboratory shall also identify opportunities to improve patient care and develop a framework to manage these opportunities (see 8.5). 7.2 Pre-examination processes 7.2.1 General The laboratory shall have procedures for all pre-examination activities and make them accessible to relevant personnel. NOTE 1 The pre-examination processes can influence the outcome of the intended examination. NOTE 2 ISO 20658 provides detailed information for sample collection and transport. NOTE 3 ISO 20186-1, ISO 20186-2, ISO 20186-3, ISO 20166 (all parts), ISO 20184 (all parts), ISO 23118 and ISO 4307 provide detailed information for samples from particular sources and for specific analytes. 7.2.2 Laboratory information for patients and users The laboratory shall have appropriate information available for its users and patients. The information shall be sufficiently detailed to provide laboratory users with a comprehensive understanding of the laboratory's scope of activities and requirements. The information shall include as appropriate: a) the location(s) of the laboratory, operating hours and contact information; b) the procedures for requesting and the collection of samples; c) the scope of laboratory activities and time for expected availability of results; d) the availability of advisory services; e) requirements for patient consent; f) factors known to significantly impact the performance of the examination or the interpretation of the results; g) the laboratory complaint process. 7.2.3 Requests for providing laboratory examinations 7.2.3.1 General a) Each request accepted by the laboratory for examination(s) shall be considered an agreement. b) The examination request shall provide sufficient information to ensure: — unequivocal traceability of the patient to the request and sample; © ISO 2022 – All rights reserved 21 ISO 15189:2022(E) — identity and contact information of requester; — identification of the examination(s) requested; — informed clinical and technical advice, and clinical interpretation can be provided. c) The examination request information may be provided in a format or medium as deemed appropriate by the laboratory and acceptable to the user. d) Where necessary for patient care, the laboratory shall communicate with users or their representatives, to clarify the user's request. 7.2.3.2 Oral requests The laboratory shall have a procedure for managing oral requests for examinations, if applicable, that includes the provision of documented confirmation of the examination request to the laboratory, within a given time. 7.2.4 Primary sample collection and handling 7.2.4.1 General The laboratory shall have procedures for the collection and handling of primary samples. Information shall be available to those responsible for sample collection. Any deviation from the established collection procedures shall be clearly recorded. The potential risk and impact on the patient outcome of acceptance or rejection of the sample shall be assessed, recorded and shall be communicated to the appropriate personnel. The laboratory shall periodically review requirements for sample volume, collection device and preservatives for all sample types, as applicable, to ensure that neither insufficient nor excessive amounts of sample are collected, and samples are properly collected to preserve the analyte. 7.2.4.2 Information for pre-collection activities The laboratory shall provide information and instructions for pre-collection activities with sufficient detail to ensure that the integrity of the sample is not compromised. This shall include: a) preparation of the patient (e.g. instructions to caregivers, sample collectors and patients); b) type and amount of the primary sample to be collected with descriptions of the containers and any necessary additives, and when relevant the order of collecting samples; c) special timing of collection, where relevant; d) provision of clinical information relevant to, or affecting sample collection, examination performance or result interpretation (e.g. history of administration of drugs); e) sample labelling for unequivocal identification of the patient, as well as source and site of sample, and labelling, when several samples from the same patient are to be collected, including multiple pieces of tissue or slides; f) the laboratory’s criteria for acceptance and rejection of samples specific to the examinations requested. 7.2.4.3 Patient consent a) The laboratory shall obtain the informed consent of the patient for all procedures carried out on the patient. 22 © ISO 2022 – All rights reserved ISO 15189:2022(E) NOTE For most routine laboratory procedures, consent can be inferred when the patient willingly submits to the sample collecting procedure, for example, venipuncture. b) Special procedures, including more invasive procedures, or those with an increased risk of complications to the procedure, may need a more detailed explanation and, in some cases, recorded consent. c) If obtaining consent is not possible in emergency situations, the laboratory may carry out necessary procedures, provided they are in the patient’s best interest. 7.2.4.4 Instructions for collection activities To ensure safe, accurate and clinically appropriate sample collection and pre-examination storage, the laboratory shall provide instructions for: a) verification of the identity of the patient from whom a primary sample is collected; b) verification and when relevant, recording that the patient meets pre-examination requirements [e.g. fasting status, medication status (time of last dose, cessation), sample collection at predetermined time or time