IS 1281 Engineering Measurements Lecture 10 PDF
Document Details
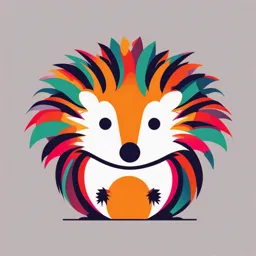
Uploaded by LargeCapacityMossAgate2608
University of Sri Jayewardenepura
S M M H Samarakoon
Tags
Related
- ENGN-3220 Engineering Measurements Introduction PDF
- MEC201 Theory of Measurements and Sensors - Chapter 4 Temperature Measuring Instruments PDF
- Theory of Measurements and Sensors (MEC201) Lecture Notes PDF
- Electrical Instrumentations and Measurements Lecture 4 PDF
- Displacement Measurements PDF
- Vibration Measurements PDF
Summary
This document is a lecture on engineering measurements, covering topics such as sensors, categorization, and characteristics. It details how to measure various physical properties and provides examples of different measurement types.
Full Transcript
IS 1281 ENGINEERING MEASUREMENTS LECTURE 10 S M M H SAM AR AKOON D E PA R T M E N T O F I N T E R D I S C I P L I N A RY S T U D I E S F A C U LT Y O F E N G N E E R I N G U N I V E R S I T Y O F S R I J AY...
IS 1281 ENGINEERING MEASUREMENTS LECTURE 10 S M M H SAM AR AKOON D E PA R T M E N T O F I N T E R D I S C I P L I N A RY S T U D I E S F A C U LT Y O F E N G N E E R I N G U N I V E R S I T Y O F S R I J AY E W A R D E N E P U R A 1 Recap of previous sessions ✓ Introduction to Engineering Measurements ✓ Methods of Measurements ✓ Elements of measurement systems ✓ Measuring Instruments ✓ Characteristics of Measuring Instruments ✓ Error and precision in measurements ✓ Calibration of Measuring Instruments ✓ Linear and angular measurement ✓ Analysis of measured data 2 Introduction to Sensors 3 Learning Outcomes of thissession State and explain what is a sensor and its basic function, requirement. Select proper sensors for measuring physical parameters. State and explain basic working principles of sensors. Explain practical issues concerning with sensors. 4 Introduction What is a sensor and what is a transducer? Sensor Sensor is a device which can measure a physical property or quantity and convert it in to a useable output. Transducer Transducer is generally described as a device which converts one form of energy to another. Thus sensors are often transducers. But other devices can also be transducers. Such as motors. 5 Introduction Sensor categorization Detection or Working Usable measuring of principle output physical parameter Can be categorized depending on, Measuring parameter/ property – what we measure Working principle Type of output – Analogue or digital Active sensors and passive sensors Other methods – ex:- Mechanical sensors, etc… 6 Introduction Active vs Passive sensors? Active sensors Requires an external source of power (excitation voltage) that provides the majority of the output power of the signal. Sensing system simply modulates the value of the external power source and provides the output. Passive sensors Sensor output is produced entirely by the quantity being measured. Direct representation of physical stimuli of light, heat, vibration, etc without the use of an external power source. Note that some sources define active and passive sensors exact oppositeway. 7 Introduction Sensor characteristics Useful criterions for sensor selection Range and span Sensitivity Resolution Accuracy and error Linearity Stability Hysteresis error Precision Dead band 8 Measurements of Physical Parameters Sensor design always involves the application of some law or principle of physics or chemistry that relates the quantity of interest to some measurable event. Position, displacement and speed measurement. Temperature measurement Stress and strain measurement Vibration and acceleration measurement Other – Pressure, Magnetic, etc…. 9 Position, Displacement, and Speed Measurement Position can be measured as, Absolute value or Relative value Linear or angular Displacement values and speed can be calculated. (through the program) But there are sensors to measure velocity without messing with distance values. Commonly used sensors, Potentiometer Proximity sensor Ultrasonic sensor Optical encoder LVDT (linear variable differential transformer) 10 Force and pressure measurement Stress and strain measurement can be indirectly used to measure physical quantities such as force and pressure. Force – by measuring strain of a flexural element Pressure – by measuring in a flexible diaphragm Strain measurement can be taken from a electrical resistance change in a strain gauge. Stress value can be determined from that measurements using the principles in solid mechanics 11 Force and pressure measurement Straingauges Used to measure deformation of solid materials. But can be indirectly used to measure other variables. (Pressure, displacement, acceleration, temperature etc.) Different types of strain gauges (depend on workingprinciple), Piezoresistive strain gauges (foil or wire strain gauges and semiconductor strain gauges) Piezoelectric strain gauges (PVDF film and quartz strain gauges) Other types (fiber optic gauges, birefringement films, etc) 12 Force and pressure measurement Piezoresistive strain gauges Electrical resistance in the material is changed as a result of mechanical deformation (strain) Where Ss is the “Gauge factor” of the strain gauge element There are several types of sub-categories depend on construction, Metal strain gauges Bonded strain gauges Un-bonded strain gauges Sputtered strain gauges Semiconductor strain gauges 13 Force and pressure measurement Load Cell Usually contains an internal flexural element with several strain gauges mounted/ bonded to it. Shape of the flexural element is designed so that the applied force is effectively represented by the voltage output of the strain gauges. Widely used in, Weight scales Integral part of a mechanical structure 14 Force and pressure measurement Load Cell Biaxial stress 15 Pressure sensors Middle range pressure sensors transfer pressure into mechanical deformation and / or stress that is then measured with a proper conversion into electrical signal. Majority of pressure sensors are composite sensors, 16 Pressure sensors Most common pressure sensing element types, Bourdon tube type Diaphragm type Capsule Bellows 17 Flow measurement Different types of techniques used to estimate the flow rate of fluids Coriolis Meters Electromagnetic principle Ultrasonic flow meters Vortex flow meters Orifice/ Nozzle/ venture type flow meters Traditional method is to measure using a orifice plate – because of the restriction there will be a change in the pressure. Orifice type flow meter 18 Temperature Measurement Most commonly based on, Contraction or expansion of solid, liquid or gas. Change in the electric resistance of a material. Common sensors and techniques, Thermocouples RTD (Resistive temperature devices) Pyroelectric devices Thermal imaging Bimetallic thermometers 19 Temperature Measurement Thermocouples Seebeck effect – is the net source of emf between pair of points in any individual electrically conducting material due to a difference of temperature between them. ∆𝐸= emf between 2 points 𝜎𝑇= Seebeck coefficient In thermocouples – two dissimilar metals in contacts forms a thermo electric junction that produces a voltage which is proportional to the temperature of the junction. 20 Temperature Measurement Thermocouples Thermocouples circuits Thermocouple with dual reference junctions Standard thermocouple configuration A, B – dissimilar metals C, D – extension leads A’, B’ – Internal reference junctiontemperature compensation 21 Temperature Measurement Thermo resistive sensors Resistance of the sensing element changes with temperature. Divided into two basic types, RTD – Resistance temperature devices Thermistors 22 Temperature Measurement Resistance Temperature Device (RTD) Resistance of the device usually increases with temperature. - PTCs RTD – constructed of metallic wire wound around a ceramic/ glass 23 Temperature Measurement Resistance Temperature Device (RTD) In some cases TCR is not a constant Relations have been established based on calculations done through actual measurements. Coefficients are specified by standards measurements. For measurements over large temperature spans, these equations are used. For measurements over small temperature spans, previous equation is acceptable. (minimum error) 24 Temperature Measurement Thermistor Semiconductor metal oxide devices – resistance changes exponentially with temperature Usually resistance decreases with increasing temperature. – NTC thermistors 25 Temperature Measurement Thermistor Different types of thermistors are available (depend on construction and depend on shape) Bead thermistor Chip thermistor Deposited thermistors on ceramic substrate 26 Temperature Measurement Thermistor PTC thermistors are also available – depend on the type of material More sensitive than NTC thermistors Commonly used, In digital thermometers As current limiters In fuses and surge protectors In automobiles Accuracy is better than RTDs Operating range is lower than RTDs 27 Position, Displacement, and Speed Measurement LinearPotentiometer Commercially available forms, Rectilinear potentiometers – For rectilinear motion measurements Rotary potentiometers – For angular motion measurements Electromechanical device that contains a fixed resistive element and a conductive wiper that slides against the element. 28 Position, Displacement, and Speed Measurement LinearPotentiometer General schematic, Output is given by, vo = kx ;where x is displacement But the actual relationship is non-linear due to finite loading impedance at output terminals. 29 Position, Displacement, and Speed Measurement Proximity Sensor Generally consists of an element that changes its state when an close by,but often not actually touching it. Usually provides an analogue signal output Working principle can be, Magnetic Electrical capacitance Inductance Eddy current Other 30 Position, Displacement, and Speed Measurement Proximity Sensor A common form of proximity sensor consists of an infrared light- emitting diode (LED) source and a phototransistor. In this form, Source – is the LED; Emits light Detector – is the phototransistor; triggered into a conducting state by reflected light. 31 Position, Displacement, and Speed Measurement Proximity Sensor Inductive proximity switch, Consists of a coil wound around a core and it generates a changing magnetic field. When a metal object brought closer to this coil end, its inductance changes This change can be monitored by its effect on resonant circuit. This can also be used as a triggering switch, at a preset level. (at preset distance) This sensor can be used for detecting metal objects. 32 Position, Displacement, and Speed Measurement Optical Encoders “A digital optical encoder is a device that converts motion into a sequence of digital pulses.” Both linear and rotary encoders are available. But most common type is rotary. Two basic forms of rotary encoders, Incremental encoder. Absolute encoder. 33 Position, Displacement, and Speed Measurement Optical Encoders Incremental encoder Produces digital pulses as the shaft rotates. From those pulses, relativedisplacement can be measured. Consists of two slightly off-set – sensor pair or tracks Pulse occurring frequency is proportional to the shaftspeed. The lead-lag phase relationship between the signals, yields the direction of rotation. https://www.youtube.com/watch?v=nnk0DV5kgMk 34 Position, Displacement, and Speed Measurement Optical Encoders 35 Position, Displacement, and Speed Measurement Optical Encoders Absolute position encoder A pattern of light and dark strips is printed on to a disk and is detected by a sensor as the disk rotates with the shaft. The pattern takes the form of a series of lines This pattern is arranged so that the combination is unique at each point Sensor is an array of photodiodes. If there are 8 tracks, the encoder is capable of measuring 256 (28) distinct positions. 36 Position, Displacement, and Speed Measurement Optical Encoders Absolute position encoder 37 Position, Displacement, and Speed Measurement Optical Encoders Absolute position encoder 38 Position, Displacement, and Speed Measurement Optical Encoders Absolute position encoder 39 Acceleration and Vibration Measurement Accelerometers are used for measuring acceleration and for high frequency vibration measurements. Accelerometers, Uses MEMS technology. Based on an algorithm which takes the displacement values of a small proof mass etched into a silicon surface of an integrated surface and suspended by small beams. 40 END OFSESSION 41