ICTM Finals Lesson 11: Other Hospital Information System PDF
Document Details
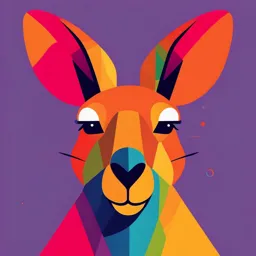
Uploaded by NimbleConcertina
Tags
Summary
This document outlines concepts related to Cardiology Information Systems (CIS) and Radiology Information Systems (RIS). It discusses the definition, functionalities, and advantages of CIS and RIS, along with their integration with other systems like Electronic Health Records (EHR). The document also mentions aspects related to patient management, scheduling, and billing.
Full Transcript
ICTM FINALS may be managed on a single platform with the help of Lesson 11: Other Hospital Information the CIS. System Remote Access–the use of networks and integrated...
ICTM FINALS may be managed on a single platform with the help of Lesson 11: Other Hospital Information the CIS. System Remote Access–the use of networks and integrated information systems, coupled with the availability of the internet and tablets and smart phones offer flexibility to CARDIOLOGY INFORMATION SYSTEM (CIS) Cardiology Information Systems. Visualization and Reporting Capabilities– one of the 11. 1 CARDIOLOGY INFORMATION SYSTEM (CIS) main benefits of Cardiology Information Systems is the ease and consistency of reporting. Virtually real-time 11.1.1. Definition information retrieval is possible with just a couple of Cardiology Information Systems (CIS) are mainly clicks and queries, and is possible from multiple focused on the storage and retrieval of Cardiology- locations. centric images. CIS usually receive an order with patient EHR Integration – since a CIS may be integrated with demographics from other information management existing Electronic Health Record Systems, it can systems, and once the images are acquired from enhance the quality of services, offered by health imaging modalities, they are profiled against the order professionals by offering a more comprehensive view of and stored for further distribution, viewing, and long the patient care spectrum. term archive (Katipula and Ireland, 2013). 11.2. RADIOLOGY INFORMATION SYSTEM The information used by cardiologists for diagnosis 11.2.1. What is a Radiology Information System? and treatment of their patients varies from A Radiology Information System (RIS) is a networked A. personal notes (history, physical examination), software system for managing medical imagery and to signals (electrocardiograms), associated data. An RIS is especially useful for tracking B. images (echocardiograms, angiograms, CT, MRI) radiology imaging orders and billing information, and is and often used in conjunction with Picture Archiving and C. reports from investigations and from Communication Systems (PACS) and Vendor Neutral procedures. All this information can currently Archivals (VNA) to manage image archives, record- be provided in digital format, and Cardiology keeping and billing within a Hospital Information System Information Systems serve as a repository (HIS) (Rouse, 2017). which houses these forms of imagery. Unfortunately, most CIS are limited to their Hospital Information Systems (HIS) storage capabilities and do not include post- - A hospital management information system or processing functions. hospital information system (HIS) is an element of health informatics that focuses mainly on the 11.1.3. Benefits and Features administrational needs of hospitals. Different vendors have varying degrees of available features. Picture Archiving and Communication System (PACS) However, the following are the most common - It is a healthcare technology for short and long benefits they enumerate: term storage, retrieval, management, distribution 1. Ease of access while maintaining data security and presentation of images. 2. Flexibility in the workflow 3. Enhanced Comparability Vendor Neutral Archival (VNA). - In a health information technology context, it is as 11.1.4. Functionalities medical imaging used by the healthcare Editing, Viewing and Storing Multi-Modal Cardiology professionals that stores images in a standard Data– different types of data, including computed format and interface, making medical imaging data tomography (CT), cardiac ultrasound accessible through different picture archiving and (echocardiography), magnetic resonance imaging (MRI), communication systems (PACS). nuclear imaging (PET and SPECT), and angiography, 11.2.2. Advantages of using an RIS Results reporting - A RIS can generate statistical reports for a single Better communication with referring doctors patient, group of patients or particular procedures. An RIS can integrate with the referring doctor’s electronic health record or EHR system, so you can Image tracking access patient data easily and quickly. The result is a - Traditionally, radiology providers use RIS to track better experience for referring doctors, which individual films and their data associated. But as dramatically increases the likelihood they’ll refer more EHRs have become standard across the healthcare patients to you. industry and digitized images and PACS have been widely adopted, radiology departments and their Faster payments RIS-PACS systems have been more drawn into the A chief benefit of a RIS is that you can use it to verify clinical workflow of the entire medical enterprise. insurance before a patient visit. The electronic Billing payments you are now capable of receiving means that - RIS systems provide detailed financial record- you get paid faster. keeping and process electronic payments and automated claims, though these functions are Improved efficiency becoming incorporated into medical organizations' It’s much faster to find, input, and create reports overall EHR systems. from patient data when the records are computerized. With the information digitized and no longer needing to be entered into records a second or third time Rouse (2017) describes the following functions of an RIS: Patient Management - An RIS can track a patient's entire workflow within the radiology department; radiology providers can add images and reports to EHRs and, where they can be retrieved viewed by authorized radiology staff. Scheduling - The RIS allows staff to make appointments for both inpatients and outpatients. Patient Tracking - Using a RIS system, providers can track a patient's entire radiology history from admission to discharge and coordinate the history with past, present and future appointments. ICTM lives of the people are on the line, as well as Lesson 12: Material Management System because medical costs are increasing. Moreover, Johnston details the strategies on how to improve inventory control within healthcare facilities: MATERIALS MANAGEMENT SYSTEM Making Sure Shippers Are Accurate The management function of hospital materials— - Tracking medical inventory must involve checking making sure that services go successfully from one shipments for accuracy. Most medical suppliers use source to an end user—includes several areas of the third-party shippers, and the tracking system must hospital and could drastically affect medical institution ensure that the correct supplies were loaded at the expenses. warehouse. Even if items are ordered correctly, Executing this function in a manner that tracking can catch any errors in filling those orders. – lessens expenses and It can also reveal whether medical supplies have - ensures adequate cash flow been properly handled in transit. *requires effective management of a large amount of Alignment With Sales Projections information from several sources. - In the field of medicine, sales projections can be wildly inaccurate. It is difficult to predict disease and accident patterns, and patients are notoriously reluctant to switch doctors, hospitals and health insurance. Tracking inventory in comparison to actual sales is essential. This prevents waste, frees up cash that would have gone to excess inventory and helps medical companies identify trends they might not have seen before. Compliance With Regulations - The medical field is heavily regulated. A company that routinely fails to serve the best interests of patients can quickly find itself being investigated, PURCHASE REQUEST sued or simply shunned by health-care consumers. A purchase request could be used as a first Tracking inventory can be extremely important in step in the process of purchasing. This is used internally maintaining the responsiveness of a medical to identify a need for an item. company. This applies not only to front-line health A purchase request generally is a document which is providers but also to the suppliers of those made by a user to notify the purchasing department providers. Knowing what inventory is on hand and regarding needed items and services. what items are needed can keep a medical This document specifies company responsive and prevent closer scrutiny by a. quantities, as well as a regulators. b. timeframe for the items requested. c. authorization information needed to proceed with Establishing Buying Cycles the purchase. - Inventory control helps medical companies understand buying cycles. Instead of responding to THINGS TO CONSIDER ONPURCHASINGITEMS: needs for supplies and equipment, inventory Inventory Control personnel can anticipate needs based on previous - Johnston (2014) states that inventory is one of the cycles. Smoothing ordering out to fit predictable biggest expenses for most medical institutions. cycles can eliminate shortages and overages. Inventory control plays an important part in Buying cycles can also be tracked to determine refining the quality of healthcare services, since the whether trends are shifting and need to be adjusted. In this way, tracking inventory can make Some suppliers allow returns of the said goods that inventory ordering into a manageable process that have indents or the like, with a guarantee of is proactive instead of reactive. replacement without any additional payments. This applies to distribution and retail industries where the ITEM MASTER MAINTENANCE- MEDICAL AND NON goods for sale are fast-moving. Normally, damaged MEDICAL INVENTORY ITEMS items are moved to another warehouse for them to be Because the importance of inventory control has monitored. been recognized, the usage of a materials management system could bring an advantage. RE-ORDER LEVEL, RE-ORDER QUANTITY, MINIMUM In Material Management Systems, the “Inventory AND MAXIMUM LEVELS FOR EACH STORE Item Maintenance” screen has many sections. The In a typical material management system, Re-order upper portion contains master information. Additional level is the minimum quantity of an item that a options appear after the selection of an existing item. company has in stock, so when the stock reached the minimum quantity stated, the item must then be re- ordered (Purchase Order/Production Order). A basic re-ordering method implemented in many ERPs and other inventory management software is the Min/Max inventory ordering method. The “Min” value is representative of a stock level that prompts a re-order, and the “Max” value is representative of a new targeted stock level that follows the re-order. The main difference of these two—Max and Min—is often interpreted as Economic Order Quantity (EOQ). Although the Min/Max method is an unpolished ITEM MASTER MAINTENANCE- MEDICAL AND NON- method for inventory ordering, the Min/Max settings MEDICAL INVENTORY ITEMS could be adjusted to provide better inventory “Item Tab” is used for maintenance of the attributes performance (Vermorel, 2014). of an inventory item, such as product type, item class, item type, etc. If the balance and order activity is zero DOCUMENTATION NEEDED IN MMS: (0), items can be deleted using this option. Enquiries Users could set the product type to group similar Enquiries are the start point of a sale or purchase items for sales analysis and inventory reporting. Most of process. Enquiries lead to getting information from a the inventory reports are based on a certain product vendor / supplier for the requirement at hand. Enquiries type. lead to establishing a connection with the right vendor / The “Item Availability” form specifies inventory supplier in order to get a quotation, place the order and levels across all warehouses. receive the requirements. Quotations Quotations consist of various pieces of vital information of a requirement towards a sale /purchase. Quotations state important information such as price, delivery times, delivery details, payment terms, taxation etc. On a quotation being accepted an order is placed for the requirements. ITEM INDENTS AND ISSUES Orders In some cases, there are instances where items In business or commerce, an Order is a stated are damaged either upon receiving from the supplier intention, either spoken or written, to engage in a or during the move from the source to another commercial transaction for specific products or services. location. From a buyer's point of view it expresses the intention PURCHASE REQUESTS, ORDERS CREATION AND to buy and is called a purchase order. From a seller's APPROVAL PROCESS point of view it expresses the intention to sell and is referred to as a sales order. When the purchase order of Purchase Orders the buyer and the sales order of the seller agree, the A Purchase Order, on the other hand, is a document orders become a contract between the buyer and seller. which records a business transaction between the buyer and the seller. A buyer issues his order, and upon seller Invoices acceptance of the order, a legally binding contract is An invoice or bill is a commercial document issued by created between the parties (SAP, 2012). a seller to the buyer, indicating the products, quantities, and agreed prices for products or services the HIS A simple Purchase Order will identify the following seller has provided the buyer. An invoice indicates the basic elements: sale transaction only. Buyer: name, address, and contact info of party giving money for goods COMPARISON OF QUOTATIONS AND PREFERRED Seller: name, address, and contact info of party VENDOR FOR EACH ITEM receiving money for goods Purchase Quotations Order Number: a unique ID number to track each A purchase quotation is a document for requesting business transaction prices and delivery information from a vendor before Item Description: details, quantity of goods, cost per the purchase order. unit, and total price of goods One could create a purchase quotation, then send the Shipping Address: where the goods will be shipped document to a vendor; when a response from the Shipping Date: when the goods will be delivered to vendor is received, with a list of prices and delivery the final location dates, one can enter the information in the purchase Billing Address: location of where the invoice should quotation. This way, one can store in the system the be sent so the Buyer can pay complete history of the sourcing process. Signature: signature of Buyer offering to buy and From the quotation, the information tracked enables signature of Seller accepting one to choose the right vendor for the purchase. Using Order Date: when the business transaction occurred the quotation helps in lessening expenses, improving the quality and increasing on-time delivery. A purchase Approval Process quotation report allows one to compare offers in order The person who creates the document, either a to pick the appropriate vendor for the purchase purchase request or order, is the originator. Upon scenario. Afterwards, one can create the purchase order adding documents to the material management system, from the selected quotation. the system checks for any approval requirements. If the document fails to meet the requisites for an approval, Preferred Vendors the originator is notified that the document needs Companies typically maintain a list of preferred approval. The document is temporarily saved as a draft. vendors, from which inventory items are An internal request is immediately sent to the first usually purchased. Several qualities of a preferred approval stage when the approval process is launched. vendor that a company looks for are: This request is received in the Messages/Alerts On-time performance Overview window, and the approver can access the Reasonable costs document. Approval can be done through a mobile High quality of products and services phone if the devices are integrated. A internal Fully licensed, bonded, and insured notification goes back to the originator with a link to the Good Business practices rejected document should the approver reject the document. The originator can amend the document, and the approval procedures will continue until the approval conditions are adequately satisfied (SAP, 2012). Inspecting a Shipment reworked, returned, or used as it is, a quarantine Persons receiving shipments should, upon location or warehouse can be used to temporarily acknowledging receipt of an order, conduct an house them until a final decision has been reached. inspection to verify the following minimum conditions: Inventory is put into quarantine if initially rejected The products conform to the purchase order during: requirements and other relevant documents (for Production, upon completion of an operation, when example: correct model number, description, size, type, specified as Move Rejected End color, ratings, etc.) Item to Quarantine. The quantity ordered against the quantity shipped or Inbound inspection upon receipt of: delivered. – Manufactured end items There is no damage or breakage. – Purchased items The unit of measurement count is correct (e.g. if the – Sold items on sales return orders unit of measurement on the purchase order is one – Enterprise Planning distribution orders dozen, there should be 12 in the package). – Outbound inspection upon issue of: Delivery documentation (packing list, certifications, – Materials to production (Infor LN Warehousing, 2018). etc.) is acceptable. Perishable items are in good condition and expiration LIFO, FIFO, FEFO ISSUES METHODS: dates have not been exceeded. Inventory management is a crucial function for any Products are operable or functional. product-oriented business. Common inventory handling methods include: Partial Deliveries First In, First Out (FIFO) – Inventory items are sold in Departments should contact the appropriate the order they are purchased. This is the most common Purchasing Agent whenever a purchase is received as a technique. partial delivery without acknowledgement or Last In, First Out (LIFO)– Last to enter the system are notification from the supplier. This information is sold first. This is common among non-perishable items typically noted on the packing list. like petroleum, minerals, and metals. First Expired, First Out (FEFO)– Materials are sold Tracking of Goods based on date they should be consumed, regardless of Goods can be easily tracked /traced when they are when it was purchased. managed by Serial or Batch. Aging of products can also be done if the items are slow moving/stay longer in the PERIODIC PHYSICAL STOCK TAKING AND ADJUSTMENTS warehouse. WITH TRACKING An inventory count is a process where a business EXPIRED STOCK AND QUARANTINE physically counts its entire inventory. A physical Expired Stock/Inventory inventory may be mandated by financial accounting Upon reaching their expiration dates, some goods, rules or the tax regulations to place an accurate value such as food and medicine, can no longer be utilized. In on the inventory, or the business may need to count rare instances, it may be sold to other parties at a lower inventory so component parts or raw materials can be cost. However, as soon as inventory expires and its restocked. Businesses may use several different tactics value falls below its original cost, this must be reflected to minimize the disruption caused by physical inventory. in the financial records so as not to misstate the Inventory services provide labor and automation to financial statements. The amount that reduces quickly count inventory and minimize shutdown time. inventory in your records is recognized as a loss Inventory control system software can speed the that is a reduction in profit (Keythman, 2017). physical inventory process. A perpetual inventory system tracks the receipt and Quarantine Stock/Inventory use of inventory, and calculates the quantity on hand. When undecided about how to handle defective Cycle counting, an alternative to physical inventory, goods, whether to be sold as scrap, may be less disruptive (CTI Reviews, 2016). Fortunately, these are all features and benefits offered by the Material Management System. Barcode and RFID are supplementary technologies that can be used in combination with the Material Management System in order to have more accurate and less burdensome inventory counts.