Water Softening Processes PDF
Document Details
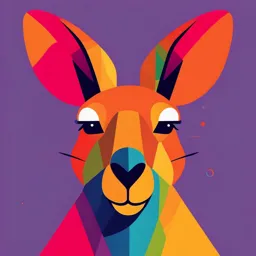
Uploaded by TrustySurrealism
Poornima College of Engineering
Tags
Summary
This document describes various water softening processes, including the lime-soda method, zeolite process, and ion exchange. It details chemical reactions involved and compares the different techniques. The chapter also includes boiler troubles and their prevention.
Full Transcript
# Chapter 2: Water Softening ## Objectives: - Introduction - Lime Soda Process - Zeolite or Permutit Process - Ion-Exchange or De-Ionization or De-Mineralization Process - Boiler Troubles - Sludge - Scales - Boiler Corrosion - Caustic Embrittlement - Priming and Foaming - Numerical based on Lime So...
# Chapter 2: Water Softening ## Objectives: - Introduction - Lime Soda Process - Zeolite or Permutit Process - Ion-Exchange or De-Ionization or De-Mineralization Process - Boiler Troubles - Sludge - Scales - Boiler Corrosion - Caustic Embrittlement - Priming and Foaming - Numerical based on Lime Soda Process ## 2.1: Introduction The process of removing the hardness causing salts (Ca+2, Mg+2 and other heavy metal ions) from water is known as "Softening of water". It is very essential since hard water is unsuitable for domestic as well as industrial use. The hardness causing salts can be removed from water by the following two ways: - **External treatment:** This is carried out before the water enters the boiler. It is aimed at preventing boiler problems. - **Internal treatment:** This refers to the conditioning of water in the boiler itself by the addition of chemicals. It essentially is a corrective method to remove those salts which are not completely removed by external treatments. ### Water Softening: | External Treatment | Internal Treatment | |---|---| | Lime-soda process | Carbonate Conditioning | | Zeolite process | Phosphate Conditioning | | Ion-exchange process | Colloidal Conditioning | | | Calgon Conditioning | ## 2.1.1: Lime Soda Process In this process, a calculated amount of lime [Ca(OH)2] and Soda [Na₂CO₃] are added to raw water. These react with the calcium and magnesium salts to form insoluble precipitates of calcium carbonate and magnesium hydroxide. Here are the chemical reactions taking place during this treatment: | S.No. | Constituent | Reactions | Need | |---|---|---|---| | 1 | Ca(HCO3)2 (Temp. Ca) | Ca(HCO3)2 + Ca(OH)2 → 2CaCO3 + H₂O | L | | 2 | Mg(HCO3)2 (Temp. Mg) | Mg(HCO3)2 + 2Ca(OH)2 → 2CaCO3 + Mg(OH)2 + 2H2O | 2L | | 3 | Mg2+ (Perm. Mg from MgCl2 or MgSO4) | Mg2+ + Ca(OH)2 → Mg(OH)2 + Ca²+ <br> Ca2+ + Na2CO3 → CaCO3 + 2Na+ <br> MgCl2 + Ca(OH)2 → Mg(OH)2++CaCl2 <br> CaCl2 + Na2CO3 → CaCO3 + 2NaCl <br> MgSO2 + Ca(OH)2 → Mg(OH)2 +CaSO4 <br> CaSO4 + Na2CO3→ CaCO3 + Na2SO4 | L <br> S <br> (L+S) | | 4 | HCO3 (e.g., NaHCO3) | 2NaHCO3 + Ca(OH)2 → CaCO3+H2O + Na2CO3 | (L-S) | | 5 | Ca2+ (Perm. Ca From CaCl₂ or CaSO4) | Ca2+ + Na2CO3 → CaCO3 + 2Na+ <br> CaCl2 + Na2CO3→ CaCO3 + 2NaCl <br> CaSO4 + Na2CO3→ CaCO3↓ + Na2SO4 | S <br> S | | 6 | CO2 | CO2 + Ca(OH)2→ CaCO3 + H2O | L | | 7 | H+ (free acid like HCI, H2SO4, etc.) | 2H+ + Ca(OH)2→ Ca²+ + 2H2O <br> 2HCI + Ca(OH)2→ CaCl2 + 2H2O <br> H2SO4 + Ca(OH)2→ CaSO4 + 2H2O <br> CaCl2 + Na2CO3→ CaCO3 + 2NaCl <br> CaSO4 + Na2CO3→ CaCO3 + Na2SO4 | (L+S) <br> L <br> L <br> S <br> S | | 8 | FeSO4 | FeSO4 + Ca(OH)2 → Fe(OH)2 + CaSO4 <br> 2 Fe(OH)2 + H2O + O2→ 2Fe(OH)3 <br> CaSO4 + Na2CO3→ CaCO3 +2Na+ | (L+S) | | 9 | Al2 (SO4)3 | Al2(SO4)3 + 3Ca(OH)2 → 2Al(OH)3 +3CaSO4 <br> 3CaSO4 + 3Na2CO3→ 3CaCO3 + 3Na2SO4 | (L+S) | | 10 | NaAlO2 | NaAlO2 + 2H2O → Al(OH)3 + NaOH | L | **Note**: - Aluminum and iron salts may be present in water as contributors to permanent hardness, or they may be added as coagulants. - There is no consideration of substances like NaCl, KCl, Na₂SO₄, SiO₂, Fe₂O₃ etc. for calculating the lime and soda requirement as they do not impart any hardness. - If there are OH- and CO3-2 ions are present in treated water, it indicates that excess of [Ca(OH)2 + Na2CO3] and Na2CO3 are used, respectively, for the treatment. So these excess amounts should be added (in terms of CaCO3 equivalent) to the calculation. - The equivalent weight of NaAlO2 is equal to its molar mass. - When the impurities are given as CaCO3 and/or MgCO3, these should be considered due to bicarbonates of calcium and/or magnesium, respectively. ### Formula for Lime and Soda Requirement: As 100 parts by mass of CaCO3 are equivalent to (i) 74 parts of Ca(OH)2 and (ii) 106 parts of Na2CO3. (As the molecular weight of Ca(OH)2 = 74 and Mg(OH)2 = 106). **Lime requirement:** = 74/100 [Tem. (Ca+2 + 2xTem. Mg+2 + Per. (Mg+2 + Fe+2 + Al+3) + H+ + CO₂ + HCO3 - NaAlO2)] all in terms of CaCO3 eq. X Vol. of water. **Soda requirement:** = 106/100 [Per. (Ca+2 + Mg+2 + Al+3 + Fe+2) + H+ - HCO3] all in terms of CaCO3 equivalent × Vol. of water.. ## 2.1.2: Zeolite or Permutit Process: - Zeolites are hydrates of sodium aluminum orthosilicate and it is represented as: Na2O. Al2O3. XSiO2. yH2O(x = 2-10 and y = 2-6). - Zeolites are two types: - **Natural Zeolite**: It is non-porous and derived from green sand. For example, Natrolite. - **Synthetic Zeolite**: It has a gel structure and is more efficient than natural zeolite. Therefore, it's more commonly used. - The process involves placing the zeolite in a suitable column, as shown in Figure 2.3. Hard water is percolated through it. The permutit can be represented as Na₂Z. After base exchange, it is converted into CaZ and MgZ (meaning sodium present in the zeolite is replaced by an equivalent amount of Ca+2 and Mg+2 ions). The hardness causing Ca+2 and Mg+2 ions are retained by the zeolite bed, and an equivalent amount of Na+ ions are released into the water. - Water is thus softened because sodium salts do not cause hardness. But total dissolved solids increase as Ca (atomic wt. = 40) and Mg (atomic wt. = 24) are replaced by 2Na (Wt. = 46). - The following reactions take place during this process: Na2Z + Ca(HCO3)2 → 2NaHCO3 + CaZ Na2Z + Mg(HCO3)2 → 2NaHCO3 + MgZ Na2Z + CaSO4 → Na2SO4 + CaZ Na₂Z + MgCl2 → 2NaCl + MgZ ### Regeneration: When the zeolite bed is completely converted into calcium and magnesium zeolites and it no longer works as a softener, it gets exhausted. At this stage, the supply of feed water is stopped and the exhausted zeolite is regenerated by treating with a concentrated (10%) brine (NaCl) solution. CaZ/MgZ + 2NaCl → Na₂Z + CaCl₂/MgCl2 **Exhausted Brine Zeolite Washings reclaimed Zeolite** The regenerated zeolite bed thus obtained is used again for softening operations. Figure 2.4 shows a diagram of the zeolite regeneration cycle. ### Zeolite Process: - Zeolite process reduces hardness to 0-15 ppm. - Hardness (mg/lit.) = mxv2×50×10³ /Vx58.5 - m = Amount of NaCl present in vol. V₂ (gm/lit). - V₂ = Total vol. of NaCl used for regeneration (lit) - V₁ = Total vol. of water softened. ### Limitations: - Hard water should be turbidity free; otherwise, impurities will clog the pores. - If mineral acids are present in feed water, they must be removed because they destroy the zeolites. - If Mn or Fe present into feed water, it must be removed first, otherwise they form MnZ or FeZ which cannot be removed easily during regenerations. ## 2.1.3: Ion-Exchange or De-Ionization or De-Mineralization Process: - Ion exchange is a process by which ions held on a porous, essentially insoluble solid are exchanged from ions in solution that is brought in contact with it. - All the cations and anions are removed in these processes; therefore, it is known as complete deionization. - Ion exchange resins are organic cross-linked insoluble polymers carrying functional groups that are responsible for the ion-exchanging properties. - Ion exchange resins can be classified as: - **Cation exchange resins (RH+):** These resins have acidic functional groups such as COOH, SO3H, etc., and are capable of exchanging their H+ ions with other cations which come into contact with them. They are mainly derivatives of styrene divinyl benzene copolymers which, on sulphonation or carboxylation, acquire the ability to exchange their H+ ions with other cations present in the water. - **Anion exchange resins (R+ OH-):** These resins contain basic functional groups, such as amino or quaternary ammonium, and are capable of exchanging their anions with other anions that come into contact with them. **Softening Process**: - The hard water is first passed through a 'cation exchange resin' chamber which removes all the cations present (e.g., Ca+2 and Mg+2) from it, and an equal amount of H+ ions are released from its column to water. 2R H+ + Ca+2/Mg+2 → R₂Ca/R2Mg + 2H+ **Hard water in (Cation exchange reaction)** - After passing the cation exchange chamber, the hard water is now pumped to the 'anion exchange resin' chamber where all anions, like Cl, SO4-2, etc., are reversed, and equal amounts of OH- ions are released from this resin bed to water. ROH + Cl →R+CI + OH 2R+OH + CO32 → R2CO3 + 2OH 2R+OH+SO₄ → R2SO4 + 2OH **Anion exchange reactions** - H and OH- ions released from the reaction in equivalent amounts, get combined to produce water molecules. H+ + OH- → H2O - Thus, the treated water is completely free from cations as well as anions so it is known as demineralized or deionized water. ### Regeneration: When the cation exchangers and anions exchangers are fully saturated by the absorption of cations and anions, respectively, they lose their further exchanging capacity and become exhausted. The exhausted anion exchange column is regenerated by passing dil. NaOH through it. R2SO4 + 2OH → 2ROH + SO4-2 Both the columns are washed with deionized water and washing is passed to the sink. ### Merits of Ion Exchange Process: - It is very economical. - It can be used to soften highly acidic or alkaline water. - It produces water of very low hardness (e.g., 0-2 ppm). So, the treated water is very good for use in high-pressure boilers. ### Demerits of Ion Exchange Process: - The equipment required is very costly. - Expensive chemicals are required. - If water is turbid, the effectiveness of the process is reduced. ## Table 2.3: Comparison of lime-soda, Zeolite and Ion-exchange process: | S.No. | Lime Soda Process | Zeolite Process | Ion-exchange Process | |---|---|---|---| | 1. | Treated water contains 10-15 ppm residual hardness. | Treated water contains residual harness of 0-15 ppm. | Treated water contains residual harness of 0-12 ppm. | | 2. | Low capital cost process. | Cost of material plant is high. | Cost of material plant is highest. | | 3. | Acidic water can be treated. | Acidic water cannot be treated. | Resins are very inert. Acidic water is well treated. | | 4. | Raw water can have suspended impurities. | Water must be free from suspended impurities. | Water should be free from suspended impurities. | | 5. | Coagulation filtration removal of sludge is required. | No removal and disposal is required. | Not required. | | 6. | Treated water contains lesser amount of dissolved solids. | Treated water contains more dissolved solids. | No dissolved solids. | | 7 | Economic process. | Automatic process, easy cheap. Plant occupies less space. | Can be used for acidic and alkaline water. Plant occupies less space. | | 8 | Plant occupies more space. | | | ## 2.1.4: Mixed Bed Deionizer: - It consists of a single cylindrical vessel containing an intimate mixture of cation exchange resins and anion exchange resins. The mixture is passed through the mixed bed; it comes in contact, a number of times, with the two kinds of exchangers alternatively. - Its net effect is equivalent to the removal of several cations and anions again and again. The method is very effective and the residual hardness of the treated water is about 0-1 ppm. **Regeneration**: When the resins are exhausted, the mixed bed is backwashed, and the lighter anion exchanger forms an upper layer above the heavier cation exchanger. Thereafter, the anion exchanger is regenerated by passing dil. NaOH from the top and then is rinsed. The lower cation exchange resin is then regenerated by H2SO4 solution treatment and then is rinsed. The two beds are then mixed again by forcing compressed air. Now the regenerated bed is ready for use again. ## 2.2: Boiler Troubles: Water required for steam generation operation i.e., boiler feed water should be of very good quality because it is directly concerned with the safety, economy, and the efficiency of the boiler. Several problems can occur if the quality of water is not suitable for the boiler. These problems are called boiler troubles, which include: - **Scale and sludge** - **Boiler corrosion** - **Caustic embrittlement** - **Priming and foaming** ## 2.2.1: Sludge: - Sludge is a soft, loose, and slimy precipitate formed within the boiler. Sludges are formed by substances which have greater solubilities in hot water than in cold water, e.g., MgCO3, MgCl2, CaCl2, MgSO4 etc. They are formed at comparatively colder portions of the boiler and get collected at places where the flow rate is slow. They can be easily removed (scraped off) with a wire brush. - If sludges are formed along with scales, then the former gets entrapped in the latter, and both get deposited as scales. ### Disadvantages of Sludge Formation: - **Fuel wastage:** As the sludges are poor conductors of heat, they resulting in the loss of heat. - **Working efficiency:** Sludge formation decreases the efficiency of the boilers. - **Chocking of pipes:** Formation of sludge may block the pipelines and plug openings. ### Prevention of Sludge Formation: - By using soft water for boiler feed operations. - By frequently removing a portion of concentrated water and replacing it by fresh water (blow-down operation). ## 2.2.2: Scales: - Scales are hard deposits that adhere firmly to the inner surfaces of the boiler. They are difficult to remove, even with the help of a hammer and chisel, and are the main source of boiler troubles. ### Causes of Scale Formation: - **Decomposition of Calcium Bicarbonate:** In low-pressure boilers, calcium bicarbonate decomposes as: Ca(HCO3)2 Heating → CaCO3↓ + H2O + CO2↑ - **Decrease in Solubility of Salts:** Increasing temperature decreases the solubility of many salts. For example, CaSO4 decreases with increasing temperature. Therefore, when hard water containing CaSO4 is heated in boilers, CaSO4 gets precipitated. - **Hydrolysis of Magnesium Salts:** At high temperatures, dissolved magnesium salts get hydrolyzed and form Mg(OH)2: MgCl2 + 2H2O → Mg(OH)2+2HCI. - **Formation of Magnesium and Calcium Silicates:** If small quantities of SiO₂ are present in water, they form CaSiO3 and MgSiO3, which are completely insoluble in hot water. These deposits stick very firmly on the inner side of the boiler surface and are very difficult to remove. ### Disadvantages of Scale Formation: - **Fuel wastage:** As scales have a low thermal conductivity, to provide a continuous supply of heat to water, overheating is done which results in the wastage of fuel. - **Decrease in efficiency:** Scales deposited in the boiler walls and choke them partially. Therefore, they decrease the efficiency. - **Lowering of boiler safety:** The superheating of the boiler makes the boiler material softer and weaker which causes distortion of the boiler tube. - **Danger of explosion:** The unequal expansion of the scale may lead to the cracking of the scale. Superheated steel plates come in contact with the boiler water. This causes the formation of large amounts of steam suddenly, creating high pressure inside the boiler. When the boiler material is not strong enough to withstand the pressure, it bursts. ### Removal of Scales: - **For Soft Scales:** As they're loosely adhering, they can be removed using a scraper, wire brush, or with the help of a blow-down operation. - **For Brittle Scales:** These can be removed by giving them thermal shocks (heating and then suddenly cooling with water). ### Prevention of Scale Formation: - **External Treatment:** Treatment of water before feeding to the boiler. - **Internal Treatment:** Treating the raw water inside the boiler is called 'internal treatment' or 'internal conditioning' or 'sequestration'. - In internal treatment, appropriate chemicals are added which precipitate the scale-forming substances in the form of loosely adherent sludge which can be removed by blow-down operation. - Alternatively, troublesome cations are converted into highly soluble complexes which remain in dissolved form in boiler water without causing any scale formation and deposition. #### Important Internal Treatment Methods: - **Colloidal Conditioning:** Introducing organic substances like kerosene, tannin, agar-agar (a gel), etc. They surround the minute particles of scale-forming salts and yield non-sticky and loose deposits that can be removed by blow-down operation. - **Carbonate Conditioning:** When sodium carbonate is added to boiler water, it converts CaSO4 to CaCO3, which is a softer sludge that can be removed by blow-down operation. Consequently, no CaSO4 deposits as scale. Carbonate conditioning is only done for low-pressure boilers. In high-pressure boilers, the excess Na2CO3 might be converted into NaOH due to the hydrolysis, which causes caustic embrittlement. CaSO4 + Na2CO3 → CaCO3 + Na2SO4 - **Phosphate Conditioning:** Adding sodium phosphate in boilers forms soft sludge of calcium and magnesium phosphate. 3CaCl2 + 2Na3PO4 → Ca3(PO4)2 + 6NaCl 3MgCl2 + 2Na3PO4 → Mg3(PO4)2 + 6NaCl - **Calgon Conditioning:** When calgon (sodium hexametaphosphate) is added to boiler feed water, it forms soluble complexes with CaSO₄, which remain dissolved in the water. Na₂[Na₄(PO3)6] 2Na+ +[Na₄(PO3)6]^2 2CaSO₄ +[Na₄(PO)]→[Ca₂(PO3)6]² + 2Na2SO4 - **Treatment with Sodium Aluminate (NaAlO2):** Sodium aluminate gets hydrolyzed to form NaOH and a gelatinous precipitate of aluminum hydroxide. NaAlO2 + 2H2O NaOH + Al(OH)3 MgCl2 + 2NaOH→ Mg(OH)2 + 2NaOH The gelatinous precipitate of Al(OH)3 and Mg (OH)2, formed inside the boiler, entraps finely suspended colloidal impurities along with silica and oil drops. The loose slimy precipitate can be easily removed by blow-down operation. - **Electrical Conditioning:** Sealed glass bulbs containing mercury connected to a battery are set rotating in the boiler, where they emit electrical discharges, which prevents scale-forming particles from adhering together to form scale. - **Radioactive Conditioning:** Radioactive salts containing tablets are placed inside the boiler feed water at a few points. The energy radiations emitted by these salts prevent scale formation. - **Complexometric Method:** Using EDTA to prevent the scale-forming cations from forming stable and soluble complexes which inhibits scale and sludge formation. ## 2.2.3: Boiler Corrosion: - Boiler corrosion is the disintegration or decay of boiler material either due to a chemical or electrochemical reaction with its environment. - It's caused by: - The **presence** of dissolved gases in water, like O2, CO2, H2S, etc. - **Acidic salts** ### 1. Corrosion Due to Dissolved Gases: - **Dissolved Oxygen (D.O.):** In the presence of moisture and at high temperatures, it directly attacks the boiler material through the following reactions: 2Fe + 2H2O+O2→ 2Fe(OH)2↓ 4Fe(OH)2+O2→2[Fe2O3.2H2O] ### Removal of Oxygen: - **Preheating:** As the solubility of gases decreases with increasing temperature, at approximately 65°C, the oxygen in water is completely removed. - **Chemical Treatment:** Employing the addition of Na₂SO₃ or Na₂S or hydra (for example Na2SO3 or Na2S): 2Na2SO3 + O2→ 2Na2SO4 Na2S + 2O2 Na2SO4 H₂N-NH2 + O2 → N₂ ↑ + 2H2O - **Mechanical Deaeration:** This involves spraying of raw water through a perforated plate fitted in a tower heated from the sides by a steam jacket. A vacuum pump connected to the tower maintains low pressure inside, with the help of a vacuum pump. - Since the solubility of a gas is directly proportional to pressure and inversely proportional to temperature, the oxygen concentration in water can be reduced by maintaining high temperatures, low pressure, and a large exposed surface.