Cargo Handling and Stowage (NDG) - University of Perpetual Help - PDF
Document Details
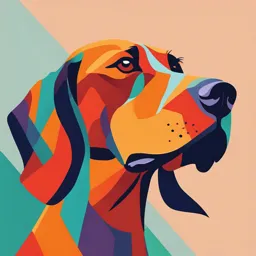
Uploaded by FlatteringVorticism4042
University of Perpetual Help
Belen | Gutierrez | Estoque | De Leon | Hernandez | Reyes | Beronilla | Bredonia | Duenas
Tags
Related
- Master < 45m NC Examination Checklist (Aide Memoire) PDF
- Lyceum International Maritime Academy - Seamanship 4 PDF
- IMSBC Code - Solid Bulk Cargo PDF
- Cargo Handling and Stowage (NDG) Past Paper - NAMEI Polytechnic Institute
- Safety Alert: Hand Injury After Tubular Cargo Shifted PDF
- INS FINALLLLL (Capt Tortora) Past Paper PDF
Summary
This document provides a comprehensive overview of cargo handling, stowage, and preparations prior to inspections. It outlines crucial components for maintaining ship safety and focuses on the importance of thorough inspections for cargo areas, hatch covers, and ballast tanks, highlighting the necessity of maintaining ship integrity. The document also includes a crucial checklist for effective inspections and preparation.
Full Transcript
Cargo Handling and Stowage (NDG) Preparations Prior to Inspections (including Checklist) Belen | Gutierrez | Estoque | De Leon | Hernandez | Reyes | Beronilla | Bredonia | Duenas Course Outcome/Learning Outcomes At the end of the lesson, the students should be able...
Cargo Handling and Stowage (NDG) Preparations Prior to Inspections (including Checklist) Belen | Gutierrez | Estoque | De Leon | Hernandez | Reyes | Beronilla | Bredonia | Duenas Course Outcome/Learning Outcomes At the end of the lesson, the students should be able to: Apply theoretical knowledge practically while emphasizing the importance of thorough inspections in maintaining ship safety and integrity. Introduction Onboard inspections are an essential part of marine safety and operational integrity. These inspections are systematic assessments of a vessel's compliance with safety requirements, maintenance processes, and operational standards. With the maritime industry under growing scrutiny from regulatory organizations, it is critical that vessels operate within legal and safety standards. Introduction Inspections of cargo spaces, hatch covers, and ballast tanks are vital to maritime safety and operational efficiency. Regular inspections help identify defects and damages that could compromise vessel integrity, safety, and compliance with regulations. Gas freeing procedures and the entry into enclosed spaces are critical components of maritime safety. As vessels transport various cargoes and operate in complex environments, ensuring the safety of crew members during these operations is paramount. Preparations Prior to Cargo Spaces: Inspections Effective cargo space inspections involve a systematic examination of the cargo area before, during, and after loading. This process not only protects the integrity of the cargo but also enhances overall safety for personnel and equipment. Items to be inspected: Check that the designated compartments are clean and ready to receive cargo. Check that the drainage and bilge suctions are working effectively and that bilge wells are dry. Bilges to be sweetened for some particular cargoes and covered with burlap and cemented. No leakage from ballast tanks present. Sounding pipes and air pipes passing from holds are clean and rust free. Ensure that cargo battens (spar ceiling) is in position and not damaged Preparations Prior to Inspections Check that the hatch lighting’s are in good order. Isolate lights if it poses fire hazard for the intended cargo. Inspect and ensure all means of access to the compartments are safe. Guard rails and safety barriers should be seen to be in place. Ensure all necessary fixed and portable fire-fighting arrangements are ready for immediate use. Blow through CO2/Halon lines with compressed air. Inspect Cargo Hold Ventilation system. Inspect and ensure hatch covers are weather tight and that all the securing devices are in good working condition. Preparations Prior to Hatch coversInspections inspection Hatch covers are the most vulnerable part of the vessel when it comes to water ingress during the voyage and can endanger the safety of both the vessel and the crew. Visually inspect hatch covers at departure and arrival for water tightness and proper operation. Look for obvious damage, holes and leak points that may jeopardize the quality of the cargo. Conduct Chalk, Hose and Ultrasonic Leak Detection (ULD) tests for objective assessment and verification. Preparations Prior to Inspections Ballast tanks inspection A ballast tank inspection is a critical procedure to ensure the safety, integrity, and functionality of a vessel's ballast system. Ballast tanks play a vital role in controlling a ship's buoyancy, stability, and trim by taking in or expelling water. Over time, these tanks can suffer from corrosion, leaks, and blockages, which can compromise the vessel's performance and safety. Regular inspections, involving visual checks, non-destructive testing, and leak assessments, help identify potential issues early, ensuring compliance with maritime regulations and preventing costly repairs or operational disruptions. Proper Why is inspection and preparation of cargo spaces, hatch covers, and ballast tank is important? Safety: Ensuring that cargo spaces and tanks are free of hazards reduces the risk of accidents, such as cargo shifting or leaks, which can endanger the crew and the vessel. Cargo Integrity: Proper inspection helps identify issues like contaminants or moisture that could damage the cargo, ensuring it arrives at its destination in good condition. Ensuring Watertight Integrity: Hatch covers must be regularly inspected to ensure they remain watertight. Leaks through damaged or improperly sealed hatch covers can lead to flooding, cargo damage, and even threaten the vessel’s stability. Ensuring Proper Ballast Water Management: Proper management of ballast water is critical for maintaining ship stability and CHECKLIST Cargo Spaces Preparation: Ensure cargo hold spaces are clean and free of debris (dust, dirt, rust, cargo residues). Confirm no water or foreign substances are present that may interfere with inspection. Verify proper ventilation is in place for the cargo spaces. Check that ventilation openings are clear and unobstructed. Inspect for any visible signs of damage to the bulkheads, floors, and sides (dents, cracks, or corrosion). Ensure any sealing between cargo holds and bulkheads is intact. CHECKLIST Hatch Covers Preparation: Check rubber seals for signs of wear, cracks, or damage. Ensure hatch covers are properly aligned and seal correctly when closed. Ensure all hatch covers can be fully closed and securely locked. Test all securing devices (dogs, cleats, etc.) for functionality. Inspect for any structural issues like bends, cracks, or corrosion on the hatch covers or the surrounding coamings. Verify that drainage holes are free of blockages and functioning properly. Inspect the drainage system to prevent water ingress during rain or CHECKLIST Ballast Tanks Preparation: Inspect for any signs of rust, pitting, or corrosion on the tank's internal and external surfaces. Check for any evidence of leaks or abnormal water accumulation. Ensure ballast tanks are free of mud, oil, or any foreign objects. Confirm all ballast tank valves, vents, and associated piping are free of corrosion, blockages, or leaks. Ensure valve operation is smooth and accessible. Verify the ballast tank level indicators are accurate and functional. Confirm all seals around tank openings (manholes, inspection REAL WORLD EXAMPLE A general cargo ship carrying logs in the hold This accident occurred when the stevedores began to enter the fully laden hold, just after the hatches were opened. One of the stevedores slipped and fell into a gap between the logs. Seeing the fall, three other stevedores attempted to rescue him but also became trapped in the log cargo. All four stevedores were brought out from the narrow spaces within the stow, which were 4 to 5m deep, only with great difficulty and with the assistance of shore fire- fighters. All suffered a lack of oxygen and Cargo Handling and Stowage (NDG) Gas Freeing Procedure GAS FREEING PROCEDURE The gas freeing procedure is essential for ensuring that confined spaces, such as ballast tanks, cargo holds, or engine rooms, are safe for entry, maintenance, or inspection. The gas freeing procedure for tank entry begins with creating a work plan that is understood by all necessary personnel. It involves a series of steps to remove or neutralize hazardous gases, ensuring the atmosphere is safe for personnel: Preparation Purging Gas freeing GAS FREEING PROCEDURE GAS FREEING PROCEDURE Preparation for Gas Freeing: Safety Assessment: Identify potential hazardous gases (e.g., methane, hydrogen sulfide, carbon dioxide) that may be present in the confined space. Shut Down Equipment: Ensure that all systems contributing to the generation of hazardous gases (e.g., pumps, engines) are turned off or isolated. Safety Equipment: Verify that safety equipment, such as personal protective equipment (PPE), gas detectors, and ventilation tools, are in place and functional. Isolate the Space: Secure the confined space by closing vents or GAS FREEING PROCEDURE ging (Initial Ventilation) : Introduce Fresh Air: Begin by introducing fresh air into the confined space to push out hazardous gases. This is typically done using mechanical ventilation, blowers, or forced air systems. Flush the Space: Continue ventilation for a specified period to flush out toxic, flammable, or oxygen-deficient air. The goal is to reduce the concentration of any harmful gases to safe levels. Open Access Points: Ensure that all hatches, manholes, or other access points are open to allow maximum airflow and ventilation. GAS FREEING PROCEDURE Gas Freeing (Ventilation and Final Monitoring) : Ventilate Continuously: Keep the ventilation systems running to continue circulating fresh air, ensuring that all hazardous gases are cleared from the space. Monitor Oxygen and Gas Levels: Check for oxygen levels (19.5%–23.5%) and flammable gases (below Lower Explosive Limit). Confirm Safe Atmosphere: Once safe, issue a gas-free certificate. GAS FREEING PROCEDURE erting (if necessary) : Inerting the Space: If the space contains highly flammable or explosive gases, inerting may be required. This involves displacing oxygen with an inert gas, such as nitrogen or carbon dioxide, to reduce the oxygen concentration below the level needed for combustion (typically below 8-10%). Monitor Atmosphere: Ensure continuous monitoring of the atmosphere during the inerting process to avoid dangerously low oxygen levels, which could pose asphyxiation risks. IMPORTANCE OF GAS FREEING PROCEDURE Gas freeing onboard chemical tankers is required for entry into cargo tanks, for hot works or washing for clean ballast tanks. Gas Freeing is one of the most hazardous operations routinely undertaken onboard a Chemical Tanker and the additional risk created by cargo gases expelled from the tanks, which may be toxic, flammable and corrosive, cannot be over-emphasised. It is therefore extremely important that all care is exercised during gas freeing operations as the consequences of an GAS FREEING PROCEDURE CHECKLIST Pre-Operation Planning Review work permit and identify required gas freeing. Assign supervisor and ensure personnel are trained. Isolation and Ventilation Isolate the area and lock out/tag out equipment. Set up continuous ventilation (e.g., fans, blowers). Ensure proper air circulation with no blockages. Atmosphere Testing and Monitoring Test for oxygen, flammable gases, and toxic gases. Use calibrated gas detectors and continuously monitor GAS FREEING PROCEDURE CHECKLIST Gas Freeing Equipment and Tools Inspect ventilation equipment, gas detectors, and PPE. Ensure firefighting equipment is available. Gas Freeing Process Begin ventilation and monitor gas concentrations. Continuously check oxygen and hazardous gas levels. Verification of Safe Conditions Ensure oxygen is within safe limits (19.5%-23.5%). Confirm no hazardous gases are present. Perform final atmospheric test before entry. AL WORLD EXAMPLE An oil/chemical tanker was underway. The cargo tanks had been cleaned in preparation for a docking survey and the Chief Officer (CO) had lined up the clean tanks for gas-freeing. The CO gave verbal instructions for completing the gas-freeing operations before retiring to his cabin for rest. At about 23:50, a relieving bridge crew member (lookout) met up with the out-going lookout. They both went on deck to change the portable air chute from one tank to another. About two hours later, the lookout left the bridge to change the portable air chute to the third tank, according to the instructions given by the CO. As the lookout left the accommodation block and went on deck he performed a VHF radio check with the OOW on the bridge, which was AL WORLD EXAMPLE About 20 minutes after the lookout’s last VHF report, the OOW called back to check the status of the task but did not receive a response. Soon after the victim was found lying unconscious on the starboard side main deck. There were no signs of injury on the victim’s body but there were no signs of breathing either and no pulse was detected. CPR was commenced and continued for many hours but the efforts were fruitless. The victim was declared deceased and the vessel proceeded to a nearby port to disembark the body. AL WORLD EXAMPLE After tank cleaning, the tank cleaning hatch (TCH) had been kept open and the oil tight hatch (OTH) was cracked open for the gasfreeing operation. This allowed gas vapours to accumulate on deck (open loop). The victim had likely inhaled remnants of nitrogen gas and/or toxic vapours while changing the portable chute from one tank to another. The victim was not carrying a portable gas detector which could have alerted him of the low oxygen level or presence of toxic gases on deck. But neither had he been instructed to do so. Cargo Handling and Stowage (NDG) Entry to Enclosed Spaces ENTRY TO ENCLOSED SPACES Entry into enclosed spaces, particularly in maritime and industrial settings, requires strict safety procedures due to potential hazards like toxic gases, low oxygen levels, or explosive atmospheres. Before entry, a risk assessment is conducted to identify potential dangers. The atmosphere inside the space is tested for oxygen content, flammable gases, and toxic ENTRY TO ENCLOSED SPACES Ventilation is then provided to ensure safe breathing conditions. Workers must wear appropriate *personal protective equipment (PPE)* such as helmets, gloves, and respirators. A permit-to-work system is implemented, granting access only after all safety measures are confirmed. Continuous atmospheric monitoring is essential, along with maintaining effective communication between workers inside and a standby person outside. The standby must be ready to raise an alarm and initiate a rescue plan if necessary. IMPORTANCE OF INSPECTIONS FOR ENTERING ENCLOSED SPACES S 1. Ensuring Worker Safety 2. Compliance with Legal and Regulatory Standards 3. Preventing Accidents and Fatalities 4. Effective Inspections and Maintenance ENTERING ENCLOSED SPACES CHECKLIST 1.Pre-Entry Planning: ⚬ Notify Authorities: Inform relevant parties (e.g., port authorities, vessel management). ⚬ Review Previous Reports: Check past inspections and safety documentation. ⚬ Define Scope: Identify tasks to be performed and ensure all tools/equipment are ready. 2.Personnel Safety: ⚬ Personal Protective Equipment (PPE): Ensure PPE is available (gas detectors, respirators, safety harnesses). ⚬ Training: Ensure all personnel are trained for confined space entry. ⚬ Safety Officer: Assign a supervisor to oversee the operation. 3.Atmospheric Testing: ⚬ Monitor Gases: Test oxygen levels (19.5% - 23.5%) and check for flammable/toxic gases (e.g., H2S, CO). ⚬ ENTERING ENCLOSED SPACES CHECKLIST 5. Isolation of Space: Close Access Points: Seal all doors, hatches, and valves. Lockout/Tagout: Secure any equipment that could pose a risk during entry. 6. Communication Systems: Communication Devices: Ensure two-way communication between personnel inside and outside the space. Emergency Procedures: Review emergency exits, alarms, and rescue plans. 7. Pre-Entry Safety Check: Confirm Safe Entry Conditions: Verify that oxygen levels are safe and hazardous gases are below permissible limits. Issue Gas-Free Certificate: Confirm the space is safe for entry and issue a gas-free certificate. REAL WORLD EXAMPLE UK Marine Insurance P&I Club have published news, dated 20 September 2017 regarding a fatal accident resulting in death of a crew member involved in an enclosed space entry on a bulk carrier. REAL WORLD EXAMPLE DESCRIPTION As discharge of a cargo of coal progressed, the level in one of the cargo holds had lowered to the point where stevedores needed to enter for cargo trimming operations using bulldozers. The cargo hold ladders were completely enclosed within a trunk, with openings at the main deck and at the lower part of the hold only. In accordance with shipboard SMS procedures, it was necessary for the crew to arrange ventilation and testing of the trunk space atmosphere prior to permitting entry of personnel. The third officer instructed two crew members to open the cargo hold access hatch and install a ventilation fan at the REAL WORLD When EXAMPLE the third officer arrived with the portable gas instrument, he saw the hatch open but the fan was not running. He then noticed that both crew members were lying unconscious on the hold ladder platforms within the trunk. The alarm was raised and rescue of the crew members was performed using self-contained breathing apparatus. Unfortunately, one crew member died and the other, although resuscitated, suffered the CONCLU SION Reporting on onboard inspections are an essential part of marine safety and operational integrity. These inspections are systematic assessments of a vessel's compliance with safety requirements, maintenance processes, and operational standards. With the maritime industry under growing scrutiny from regulatory organizations, it is critical that vessels operate within legal and safety standards. The inspections of cargo spaces, hatch covers, and ballast tanks are vital to maritime safety as these inspections help to detect defects and damages that could compromise vessel integrity, safety, and compliance with regulations. The procedures for gas freeing and entry to enclosed spaces requires strict safety procedures due to potential hazards like toxic gasses, low oxygen levels, or explosive REFEREN CES: https://www.slideshare.net/slideshow/inspections-on-board/3067353#4 https://www.sgs.com/en-ph/services/hold-hatch-inspections http://shipsbusiness.com/tank-cleaning-purging-gas-free-check-items.html https://www.iims.org.uk/wp-content/uploads/2014/03/A-Masters-Guide-to-Enclosed-Spa ce-Entry.pdf https://en.wikipedia.org/wiki/MV_Faina#/media/File:Ukrainian_merchant_vessel_MV_Fai na.jpg https://knowledgeofsea.com/gas-freeing/#google_vignette https://www.marineinsight.com/case-studies/four-stevedores-die-on-log-vessel/