G650ER™ Operating Manual Flight Controls General (PDF)
Document Details
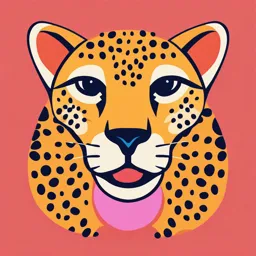
Uploaded by PhenomenalNumber
2023
Tags
Summary
This document provides a detailed description of the Aircraft Flight Control Systems, including the primary FCS (Flight Control System), flap system and horizontal stabilizer system for the G650ER aircraft. The document also covers power sources, system comparisons, and self-test (SPOST) procedures.
Full Transcript
G650ER™ OPERATING MANUAL A2 72- 0- :0 Flight Controls 2A-27-10: General 1. REVISION152023-09-15 General Description: (See Figure 1. Flight Controls System: Control Surface Nomenclature, Figure 3. Flight Control Mode Comparison, and Figure 2. Flight Control Power Sources.) The flight control system c...
G650ER™ OPERATING MANUAL A2 72- 0- :0 Flight Controls 2A-27-10: General 1. REVISION152023-09-15 General Description: (See Figure 1. Flight Controls System: Control Surface Nomenclature, Figure 3. Flight Control Mode Comparison, and Figure 2. Flight Control Power Sources.) The flight control system consists of the primary Flight Control System (FCS), the flap system and the horizontal stabilizer system. The primary FCS includes the components that control the two ailerons, six spoilers, two elevators and one rudder. These surfaces are hydraulically actuated and electrically controlled with fly-by-wire technology. The flap actuation system includes the Flap Electronic Control Unit (FECU) and the drive system. The horizontal stabilizer system includes a Horizontal Stabilizer Control Unit (HSCU) and a Horizontal Stabilizer Trim Actuator (HSTA). Note Nosewheel steering and brakes are not considered to be part of the FCS in this document. The pilot and copilot primary flight controls include control wheels, columns and rudder pedals. Each primary control is connected to position sensors and artificial feel mechanisms. The position sensors provide the position of the respective control device to the Flight Control Computers (FCCs) and Backup Flight Control Unit (BFCU). The artificial feel mechanisms provide tactile cues to the pilots. The pilot and copilot flight controls are mechanically linked and are designed to operate in unison. They have springs and dampers to provide appropriate "feel" forces and mechanical stops to limit their maximum displacement. The wheel and column (but not the rudder pedals) are linked by bungee rods to allow control in the event of a mechanical jam on the pilot or copilot side. The bungee rods act as a solid link unless the forces on the pilot and copilot side differ by a large amount due either to a jam or opposing inputs from the pilots. The pilot and copilot rudder pedals are mechanically connected with a hard link which cannot be overridden. In the event of a rudder pedal jam, the aircraft can be safely flown with rudder trim. Trim switches are provided for pitch, roll, and yaw axes. There are two dual-channel FCCs and a Backup Flight Control Unit (BFCU) which generate commands for the control surface actuators. The FCCs house the operational logic (also known as Control Laws) for control of the flight control surfaces. Any one of the four FCC channels is independently fully capable of safely operating the entire aircraft FCS. In the event that both FCCs (all four channels) are inoperative, the BFCU controls the elevators, ailerons, outboard spoilers (roll control only, no speed brakes), and rudder. The aircraft may be dispatched (with restrictions) with one FCC channel inoperative or the BFCU inoperative with restriction. See MMEL for dispatch requirements. OEM Provided Data Flight Controls Revision 15 2023-09-15 2A-27-00: 1 of 76 G650ER™ OPERATING MANUAL The primary FCS actuators provide a damping feature to protect the primary control surfaces from potential damage caused by wind gusts (up to 65 knots) while the aircraft is on the ground with hydraulic systems depressurized. There is no “gust lock” mechanism. The primary and secondary flight controls are discussed in the following subsections: 2. 2A-27-20: Aileron and Roll Spoiler Control System 2A-27-30: Rudder Control System 2A-27-40: Elevator Control System 2A-27-50: Horizontal Stabilizer System 2A-27-60: Wing Flaps System 2A-27-70: Speed Brake and Ground Spoilers System System Power On Self-Test (SPOST): Note The Cockpit Preflight Inspection checklist (AFM 02-01-10) and the Before Starting Engines checklist (AFM 02-03-20) both have distinct SPOST executions. a. When performing the 'Cockpit Preflight Inspection' checklist (AFM 02-01-10): During the first flight of the day, a separate FCC SPOST is performed with the MAIN BATTERIES selected ON without APU GEN power. FCC 1B and 2A are powered by the Main Batteries. When the EBHA and then the UPS switches are selected ON, the SPOST will exercise the system without having the FCC Batteries receiving power from the EBHA and UPS Battery chargers in order to accurately check battery health. The SPOST will exercise the powered systems, associated with flashing indications on the pedestal in the cockpit and 8 cycles of the pilot side stick shaker. Additionally, at the end of the cockpit preflight check initiated SPOST, both the FCC Alternate Mode (caution) and the FCS Maintenance Required (caution) CAS messages will be present, the Flight Control synoptic will be stable (not flashing), and the FLT CTRL Battery voltage should be within acceptable voltage parameters as indicated in the preflight checklists. The FCS Maintenance Required (caution) CAS message is due to the fact that the Flight Control System is not receiving inputs from the IRUs, ADS, and other unpowered systems. If the SPOST is in progress and does not successfully finish (indicated by less than eight stick shaker momentary activations and the presence of the FCS Maintenance Required (caution) CAS) then the FCC reports the SPOST as failed and posts an FCS Test Fail (caution) CAS. The most likely reason for this failure is removing power to any FCC channels while the SPOST is in progress. Once an FCC channel reports the SPOST as failed, it is latched until power is cycled to the FCC channels twice. Thus, if during the Cockpit Preflight checks the crew were to remove power OEM Provided Data Flight Controls Revision 15 2023-09-15 2A-27-00: 2 of 76 G650ER™ OPERATING MANUAL during the SPOST by prematurely deselecting FCS or Main battery power, then the SPOST will not run during the normal Before Starting Engines sequence and the FCS Maintenance Required (caution) CAS will post. To reset a latched FCC SPOST failure, power must be totally removed for one minute before the next aircraft power up attempt. b. When performing the normal 'Before Starting Engines' checklist (AFM 02-03-20): The SPOST is a feature of the FCC channels that runs when power is first applied by selecting the FLT CTRL BATTERIES (EBHA/UPS) switches to the ON position. During the SPOST, the FCC runs through a series of checks and the pilots will observe multiple flight control capsule lights on the center pedestal flashing as well as both stick shakers momentarily running for a total of eight cycles. A successful SPOST will terminate with the FCC Alternate Mode (caution) CAS and no FCS Maintenance Required (caution) CAS approximately 45-50 seconds after UPS power and about 10 seconds after the last stick shaker vibrates. An unsuccessful SPOST will be indicated by an FCS Maintenance Required (caution) CAS and this will require a complete removal of power for a minute to reset the FCCs The APU GEN powers both the Essential DC and the Main DC busses. When this happens, FCC channels 1B and 2A are powered along with all of the normal associated Flight Control System busses. When the EBHA switch is selected ON, the MCEs are powered. Subsequent selection of the UPS switch to ON powers the remaining two FCC channels (1A and 2B) and the SPOST will initiate within 10 seconds with all the FCS components electrically powered. At the conclusion of the SPOST, approximately 45 seconds after initiation, the FCC Alternate Mode (caution) CAS should be the only FCS CAS message. It will extinguish when the four 'ANTI ICE HTR AIR DATA PROBE' heaters are selected ON after Engine Start is complete. 3. Primary Flight Control System Architecture: The aircraft Fly-By-Wire (FBW) primary FCS is powered by the aircraft electrical and hydraulic systems. The primary FCS utilizes the following equipment: Flight deck controls and displays Flight Control Computers Air Data sensors Inertial sensors Flight Control Actuators Flight control surfaces Analog and digital communications to link the above components The left and right hydraulic systems are connected to the actuators in such a way that if one hydraulic system is lost, all primary flight control surfaces (other than one mid or inboard spoiler pair) remain operational. a. Components: OEM Provided Data Flight Controls Revision 15 2023-09-15 2A-27-00: 3 of 76 G650ER™ OPERATING MANUAL The flight deck control devices include: Conventional control wheel, control column and rudder pedal assembly for each pilot Speed brake handle Trim control switches Flap handle Flight Control Reset Switch Each of the above controls have multiple position sensors that are read by the FCCs The BFCU receives position sensor information from the control wheel, control column and rudder pedal assembly for each pilot and trim control switches (Backup Pitch trim ONLY) The primary FCS includes the following components: Two dual-channel FCCs One BFCU Nine Hydraulic Actuators (HA) - one rudder, two ailerons, two elevators, two mid spoilers and two inboard spoilers Seven Electric Backup Hydraulic Actuators (EBHA) - one rudder, two ailerons, two elevators and two outboard spoilers The Flap Actuation System includes the following components: FECU in the Right Electronics Equipment Rack (REER) Flap Hydraulic Control Module (HCM) in the main wheel well Flap Power Drive Unit (PDU) in the main wheel well Inboard flap actuators (one per wing) Outboard flap actuators (one per wing) Torque shafts (eight per wing) Pillow blocks (six per wing) (1) Flight Control Computers (FCCs): (See Figure 4. LEER Flight Control Computer (FCC) Location and Figure 5. REER Flight Control Computer (FCC) Location.) Two dual-channel FCCs are installed in the aircraft (located in the Left and Right Electronics Equipment Racks [LEER and REER]). Each of the four channels is comprised of a command lane and a monitor lane. The two lanes provide integrity to the system by operating with different software and as a self-checking pair. The monitor lane continuously checks its own computations with the commands transmitted by the command lane. Significant differences between the two lanes cause that channel to be shut down. Any single channel is capable of controlling all flight control surfaces. This configuration provides four redundant dissimilar and independent channels of operation. Each FCC channel contains the operation logic for each flight control surface, previously identified as Control Laws. The FCCs provide OEM Provided Data Flight Controls Revision 15 2023-09-15 2A-27-00: 4 of 76 G650ER™ OPERATING MANUAL Provides BFCU health status and flight deck sensor position data to each FCC (which provides system monitoring of the BFCU to report a failure) Provides surface position commands directly to each of the seven EBHA REUs to allow operation during either normal hydraulic or Electrical Backup operation. The backup mode is not selectable by the flight crew. The BFCU monitors all four FCC channels and will assume control of the FCS within one half of a second if all four channels of the FCCs become unavailable. An FCC channel is unavailable if it is unpowered or is unable to compute in either normal, alternate, or direct modes. The BFCU provides control surface inputs to the EBHAs on the following control surfaces: Both Ailerons Outboard Spoilers Both Elevators Rudder Note When in the BFCU mode of operation, these flight control surfaces have limited travel. This helps to avoid over-controlling or over-stressing the aircraft when operating at high speed. (3) Hydraulic Actuators (HAs) and Electric Backup Hydraulic Actuators (EBHAs): (See Figure 7. Elevator Electrical Backup Hydraulic Actuator (EBHA) and Electro-Hydraulic Servo Actuator (EHSA) Components through Figure 10. Inboard, Mid and Outboard Spoiler Hydraulic Components.) The flight control surfaces are electrically-controlled and hydraulically-powered. There are two types of primary flight control surface actuators: the HA and the EBHA. The EBHAs have the ability to operate normally using the engine-driven-pump hydraulic system supply or in Electric Backup (EB) operation using a built-in motor-pump in the EB manifold powered by 28V DC from the EBHA battery bus. (a) HA: Each HA is controlled by a Remote Electronics Unit (REU) mounted on the actuator manifold. The REU sends commands to a hydraulic valve in the manifold which ports pressure to either the “extend” or “retract” side of the actuator until the desired actuator position is achieved. Each HA REU is powered by a single electrical source on one of the Essential DC buses. The midboard spoiler REUs each have two electrical sources from OEM Provided Data Flight Controls Revision 15 2023-09-15 2A-27-00: 6 of 76 G650ER™ OPERATING MANUAL excitation to and receive inputs from the flight deck control device sensors (and other aircraft sensors and systems). The FCCs use this data to calculate position command signals to the 16 flight control surface actuators. Position sensors at the control surfaces feed the position of the control surface back to the FCC. The FCCs monitor and report the health status of the computing channels, flight deck sensors, air data sensors, inertial data sensors, horizontal stab system, BFCU, and the HA and EBHA actuators. Any abnormal condition is reported through the CAS, FCS Synoptic page, and/or the Central Maintenance Computer (CMC). Functions such as system rigging and system configuration checks can be also be accomplished through the CMC. Communication between the FCCs and the BFCU, HAs, EBHAs, HSTS, FECU and other aircraft systems is primarily through ARINC 429 digital communication buses. The buses from the FCCs to the actuators have redundancy that allows system operation after damage from birdstrikes, tire bursts, engine rotor bursts, etc. The FCS has extensive built-in test capabilities. Some tests are run automatically with each power cycle and others are initiated by maintenance personnel. Each FCC provides the following functions: Flight control surfaces commands as a function of flight conditions and aircraft configuration for pilot and autopilot inputs based on the control laws Secondary command inputs to the FECU based on flaps handle microswitch status Command inputs to the HSTS (based on pitch trim inputs and Control Law commands) Yaw damper Computation of low speed awareness information such as Normalized AOA, pitch limit indicator, and low speed limits for the airspeed tape on the PFD Interface with the surface actuators, FECU and the HSCU by data buses FCS Built-In-Test initiation and fault reporting (2) Backup Flight Control Unit (BFCU): (See Figure 6. Backup Flight Control Unit Architecture.) The BFCU is designed to maintain emergency flight and landing capability in the event all four channels of the FCCs become unavailable. The BFCU is located under the cabin floor aft of the main entrance door. The BFCU interfaces with the following components: OEM Provided Data Provides excitation to and processes signals from flight deck control sensors (one for each wheel, one for each column, and one for rudder pedals) Flight Controls Revision 15 2023-09-15 2A-27-00: 5 of 76 G650ER™ OPERATING MANUAL the Right Essential DC bus with separate wing-leading-edge and trailing-edge routings. The HA has two states – Hydraulically Active or Damped Bypass: Hydraulically Active – HA in normal operation. The aircraft hydraulic system is providing pressurized fluid to position the flight control surface. To be in this state, hydraulic pressure must be available and the actuator REU must electrically hold a solenoid. The REU can force Damped Bypass operation by removing power from the solenoid. Damped Bypass – The actuator is in a passive condition that resists movement proportional to the rate at which the surface is moved by either airflow over the surface or by the other actuator. Hydraulic fluid is trapped within the actuator to prevent control surface flutter in flight. During ground operation, the trapped fluid in the actuator provides gust protection. Pilots may directly experience the behavior of damped bypass actuators by rotating an aileron surface upward or downward with the palms of their hands during preflight when hydraulic pressure is not available to either the left or right system. (b) EBHA: The EBHA has three modes of operation: Hydraulically Active Electric Backup Damped Bypass During normal hydraulic operation, the EBHA has the same inputs and functions as the HA. However, in the event that a surface cannot be powered by an engine-driven hydraulic source, an Electrical Backup (EB) hydraulic pump will provide the EBHA actuator with hydraulic pressure to operate the flight control surface. The EBHA REUs each receive electrical power from two separate circuit breakers. One is located on the UPS bus and the other on one of the Main DC buses except for the rudder which uses two UPS electrical supplies routed through separate rotor burst zones. The Motor Control Electronics (MCE) is used to control the EBHA electric motor-pump when the actuator is in the Electric Backup state due to hydraulic or REU failures. If an EBHA is in the normal hydraulically active state, the MCE is in a standby condition wherein it still processes commands and sends them back to the FCC through its REU to monitor its availability. Normally, the MCE receives commands from its associated REU. As a backup, each FCC has a single MCE bus for direct MCE control. In the event of failure of all REUs on a surface OEM Provided Data Flight Controls Revision 15 2023-09-15 2A-27-00: 7 of 76 G650ER™ OPERATING MANUAL (except inboard and mid spoilers), the MCE bus allows an FCC to retain control of the surface. FCC 1 connects to both aileron MCEs and the right elevator MCE. FCC 2 connects to both outboard spoiler MCEs, the left elevator MCE and the rudder MCE. MCEs each receive electrical power from a single 65 Amp circuit breaker on the 28V DC EBHA bus located in the tail compartment at floor level forward of the ladder. The MCE uses the power for its internal electronics and to power the backup electrical motor. b. Operation: The primary FCS has five modes of operation: Normal Alternate Direct Backup Maintenance Note The FCCs will not allow mixed mode operation. All of the flight controls will be in Normal, Alternate, Direct, or Backup mode. (1) Normal Mode: Under normal conditions, the Flight Control System (FCS) will be in Normal mode. Normal mode has four sub-modes: On-ground, Takeoff and Landing, Cruise, and Angle of Attack (AOA) Limiting. The FCS will be in Normal mode when the following conditions are satisfied: Two or more air data probes are heated and providing consistent data AND At least one IRU is operating and without conflicting data from another IRU or all operating AHRS (standby Attitude Heading Reference Systems) AND The horizontal stabilizer is not reporting to the FCC that it is in Backup Mode (wherein the stabilizer is directly controlled by the center console backup trim switch) (a) On Ground sub-mode: The FCS will be in the On-ground sub-mode when Normal mode conditions are satisfied and at least one of the four conditions is satisfied: OEM Provided Data Flight Controls Revision 15 2023-09-15 2A-27-00: 8 of 76 G650ER™ OPERATING MANUAL WOW from both the left and right main gear indicate weight on wheels OR WOW from the left main gear indicates weight on wheels and the wheel speed from the left wheel is 47 knots or greater OR WOW from the right main gear indicates weight on wheels and the wheel speed from the right wheel is 47 knots or greater OR Both the left and right main gear wheel speeds are 47 knots or greater and Radar altitude is less than 10 feet During a normal takeoff, this last condition will be the last one to cancel as the aircraft climbs through 10 feet AGL allowing transition from On-Ground sub-mode to the Takeoff and Landing sub-mode. During a normal landing, the normal sub-mode will not transition to On-ground until after touchdown. Indications of On-ground sub-mode: The pitch, roll and yaw trim indicators will include a green band when the FCS is in the On-Ground sub-mode While On-ground, AOA limiting is unavailable. Weight off wheels AOA limiting is available Pitch Control – Column deflection translates directly to elevator command. At speeds of approximately 135 KCAS and below, full column will result in full elevator except for a small flap bias described below. As speed increases above approximately 135 KCAS, the amount of elevator deflection per column deflection will decrease so that the pitch response will not be too sensitive. The elevator is biased one degree nose up for each “notch” of flap handle deflection – i.e. one degree for flaps 10, two degrees for flaps 20, and three degrees for flaps 39. Roll Control – Wheel deflection translates directly to aileron and roll spoiler deflection. The amount of roll spoiler deflection will vary with flap position and air speed, and could be as much as full deflection (55°). The outboard and midboard roll spoilers are commanded to move together. Higher speeds and higher flap deflections will tend to a smaller spoiler deflection schedule. Yaw Control – Below 60 KCAS, rudder deflection is only a function of rudder pedal deflection; full pedal will result in full rudder displacement. Between 60 KCAS and 90 KCAS the yaw damper will smoothly transition from 0% to 100% effectiveness. The yaw damper will then be active using simple yaw rate feedback (from the IRS sensors) to the rudder in combination with the rudder pedal input. OEM Provided Data Flight Controls Revision 15 2023-09-15 2A-27-00: 9 of 76 G650ER™ OPERATING MANUAL Pitch Trim – Actuation of any pitch trim switch commands the stabilizer to move at its maximum rate of 0.4 degrees per second in the direction commanded. (b) Takeoff and Landing sub-mode: The FCS will be in the Takeoff and Landing (TL) sub-mode when Normal mode conditions are satisfied and the following conditions are all satisfied: The On-ground logic is not satisfied AND AOA limiting logic is not satisfied AND Autopilot is not engaged AND Landing gear handle is down OR flap handle is greater than 5° Indications of Takeoff and Landing sub-mode: The pitch trim indicator will display the numeric value of stabilizer position without a green band indication Pitch Control – Identical to On-ground sub-mode and repeated here for convenience. Column deflection translates directly to elevator command. At speeds of approximately 135 KCAS and below, full column will result in full elevator except for a small flap bias described below. As speed increases above approximately 135 KCAS the amount of elevator deflection per column deflection will decrease so that the pitch response will not be too sensitive. The elevator is biased one degree nose up for each “notch” of flap handle deflection – i.e. 1 degree for flaps 10, 2 degrees for flaps 20, and 3 degrees for flaps 39. Roll Control – Wheel deflection will command aileron and roll-spoiler deflection. The roll augmentation function may increase or decrease the roll control surface deflections depending on the magnitude of roll rate being realized compared to the amount of roll-rate expected based on the wheel and pedal inputs and normal aircraft response. The roll augmentation function is a safety feature which significantly reduces any roll rate which is not commanded by the pilot (e.g. roll rate caused by wake turbulence or a spoiler panel malfunction). In the event of a spoiler panel malfunction, the roll augmentation feature will deactivate after five seconds and remain so for the duration of the flight. The amount of roll spoiler deflection will vary with flap position and air speed, and could be as much as full deflection (55°). The outboard and midboard roll spoilers are commanded to move together. Higher speeds and higher flap deflections will tend to a smaller spoiler deflection schedule. OEM Provided Data Flight Controls Revision 15 2023-09-15 2A-27-00: 10 of 76 G650ER™ OPERATING MANUAL Yaw Control – The yaw damper will be active using sensor feedback (sideslip rate calculation) to the rudder in combination with the rudder pedal input in order to damp dutch roll oscillations. Pitch Trim – Actuation of any pitch trim switch commands the stabilizer to move at its maximum rate of 0.4 degrees per second in the direction commanded. (c) Cruise sub-mode: The FCS will be in the Cruise sub-mode when Normal mode conditions are satisfied and the following conditions are all satisfied: The On-ground sub-mode logic is not satisfied AND AOA limiting sub-mode logic is not satisfied AND Autopilot engaged OR both the landing gear and flap handles are up Indications of Cruise sub-mode: When the pitch trim indicator does not display the numeric value of the stabilizer position (indicates NOT in On-ground or Takeoff and Landing sub-modes) and there is no FCC AOA Limiting (advisory) CAS message, the FCS is in the Cruise sub-mode Pitch Control – Pitch response is designed to be conventional, but with additional damping (especially at high altitude). Elevator movement is augmented with sensor feedback to provide a more consistent response to column input with variations in weight and center-of-gravity. Overspeed protection is provided by limiting column authority in the nose down direction if the aircraft exceeds the maximum operating speed. There is no protection against exceeding the maximum mach number. Roll Control – Identical to Takeoff and Landing sub-mode which is repeated here for convenience. Wheel deflection will command aileron and roll-spoiler deflection. The roll augmentation function may increase or decrease the roll control surface deflections depending on the magnitude of roll rate being realized compared to the amount of roll-rate expected based on the wheel and pedal inputs and normal aircraft response. The roll augmentation function is a safety feature which significantly reduces any roll rate which is not commanded by the pilot (e.g. roll rate caused by wake turbulence or a spoiler panel malfunction). In the event of a spoiler panel malfunction, the roll augmentation feature will deactivate after five seconds and remain so for the duration of the flight. The amount of roll spoiler deflection will vary with flap position and air speed, and OEM Provided Data Flight Controls Revision 15 2023-09-15 2A-27-00: 11 of 76 G650ER™ OPERATING MANUAL could be as much as full deflection (55°). The outboard and midboard roll spoilers are commanded to move together. Higher speeds and higher flap deflections will tend to a smaller spoiler deflection schedule. Yaw Control – Identical to Takeoff and Landing sub-mode which is repeated here for convenience. The yaw damper will be active using sensor feedback (sideslip rate calculation) to the rudder in combination with the rudder pedal input in order to damp dutch roll oscillations. Pitch Trim – Pitch trim will initially offset the elevator. In the long term, any persistent elevator offset greater than one degree will be offloaded to the horizontal stabilizer. (d) AOA Limiting: The FCS will be in the AOA limiting sub-mode when Normal mode conditions are satisfied and the following conditions are all satisfied: WOW from both main landing gear indicates weight off wheels AND AOA limiting is available as indicated by the absence of the Stall Protection Unavail (caution) CAS message AND Normalized AOA is greater than the AOA limiting sub-mode entry threshold. During normal maneuvering, this threshold is approximately 0.88-0.93 normalized AOA depending on airspeed deceleration rate. In cases of significant pitch rate and rapid/large aft column input, this entry threshold can be lowered substantially. Entry into the AOA limiting sub-mode can occur at any normalized angle of attack with abrupt nose up control input. Indications of AOA Limiting sub-mode: The FCC AOA Limiting (advisory) CAS message will be displayed. Additionally, the Stall Protection Active (caution) CAS message will be displayed if the AOA is near its limit value of 0.96. Pitch Control – Column commands angle of attack, with full aft column resulting in maximum allowed angle of attack (alpha limit of approximately 0.96 normalized AOA). Reducing angle of attack will exit AOA limiting and return typically to either Cruise or Takeoff-and-Landing sub-mode depending on landing gear and flap handle positions. On-ground conditions have priority and a transition to on-ground sub-mode will occur if the aircraft should touch down while in AOA limiting mode. To protect against unnecessary entry into AOA limiting during landing and flare, approach speed should be increased during strong or gusty wind conditions. In nominal wind conditions, cross the OEM Provided Data Flight Controls Revision 15 2023-09-15 2A-27-00: 12 of 76 G650ER™ OPERATING MANUAL threshold at VREF. In strong wind conditions, cross the threshold at an increased approach speed of VREF plus ½ of the steady state wind plus the full gust increment, not to exceed an approach speed of VREF + 20 KCAS. Landing distance shall be calculated utilizing planned speed at the threshold. Roll Control – Identical to On-ground sub-mode which is repeated here for convenience. Wheel deflection translates directly to aileron and roll spoiler deflection. The amount of roll spoiler deflection will vary with flap position and airspeed, and could be as much as full deflection (55°). The outboard and midboard roll spoilers are commanded to move together. Higher speeds and higher flap deflections will tend to a smaller spoiler deflection schedule. Yaw Control – The yaw damper will be active using sensor feedback to the rudder in combination with the rudder pedal input in order to damp dutch roll oscillations. Pitch Trim – Nose down trim will command the stabilizer in a nose-down direction. Nose up trim has no effect. (2) Alternate Mode: The FCS will be in Alternate mode when one or more of the following conditions are satisfied: Less than two air data probes are heated and providing consistent data OR IRU data is inconsistent, is conflicted by all operating AHRS, or is invalid (all off or malfunctioned) OR The horizontal stabilizer is reporting to the FCC that it is in Backup Mode Indications of Alternate mode: Alternate mode is primarily indicated by an FCC Alternate Mode (caution) CAS message. Since airspeed is not used in Alternate mode, the amount of surface deflection per pilot input (pitch, roll, and yaw) will be greatest when either the flap or gear handle is not up (assumes 250 KCAS); less when both handles are up (assumes 340 KCAS). Pitch Control – Column deflection translates directly to elevator command. Roll Control – Wheel deflection translates directly to aileron and spoiler deflection. The outboard and mid roll spoilers are commanded to move together. OEM Provided Data Flight Controls Revision 15 2023-09-15 2A-27-00: 13 of 76 G650ER™ OPERATING MANUAL Yaw Control – Rudder pedal deflection commands rudder deflection. If IRU #3 data is available, a simplified yaw damper will damp dutch roll oscillations. Pitch Trim – Actuation of any pitch trim switch commands the stabilizer to move at its maximum rate of 0.4 degrees per second. (3) Direct Mode: The FCS will be in Direct mode after all four FCC channels become invalid. The Direct mode behavior is the same as Alternate mode but some of the software and hardware is different and/or simplified to help guarantee its availability. Indications of Direct mode: Direct mode is primarily indicated by an FCC Direct Mode (caution) CAS message. Note While in Direct mode, AOA limiting is unavailable as annunciated by the Stall Protection Unavail (caution) CAS message. The following applies to both Alternate and Direct mode and is repeated here for convenience: Since airspeed is not used in Alternate or Direct mode, the amount of surface deflection per pilot input (pitch, roll, and yaw) will be greatest when either the flap or gear handle is not up (assumes 250 KCAS); less when both handles are up (assumes 340 KCAS). Pitch Control – Column deflection translates directly to elevator command. Roll Control – Wheel deflection translates directly to aileron and spoiler deflection. The outboard and mid roll spoilers are commanded to move together. Yaw Control – Rudder pedal deflection commands rudder deflection. If IRU #3 data is available, a simplified yaw damper will damp dutch roll oscillations. Pitch Trim – Actuation of any pitch trim switch commands the stabilizer to move at its maximum rate of 0.4 degrees per second. (4) Backup Mode: The FCS will be in Backup mode after all four FCC channels have failed (not capable of Normal, Alternate, or Direct Modes). Backup mode behavior is similar to Alternate mode except the only spoiler capability is outboard roll control spoilers. Speed brakes and ground spoilers are not available. Indications of Backup mode: OEM Provided Data Flight Controls Revision 15 2023-09-15 2A-27-00: 14 of 76 G650ER™ OPERATING MANUAL Backup mode is primarily indicated by a BFCU Active (caution) CAS message. Note While in Backup mode, AOA limiting is unavailable as annunciated by the Stall Protection Unavail (caution) CAS message. Since airspeed is not used in Alternate, Direct, or Backup mode, the amount of surface deflection per pilot input (pitch, roll, and yaw) will be greatest when either the flap or gear handle is not up (assumes 250 KCAS); less when both handles are up (assumes 340 KCAS). Pitch Control – Column deflection translates directly to elevator command. Roll Control – Wheel deflection translates directly to aileron and outboard spoiler deflection. The mid roll spoilers will remain retracted while in Backup mode. Yaw Control – Rudder pedal deflection commands rudder deflection. If IRU #3 data is available, a simplified and reduced authority yaw damper will provide a small amount of additional dutch roll damping. Pitch Trim – The pedestal pitch trim switch commands the stabilizer to move at its Backup rate of 0.15 degrees per second in the direction commanded. The wheel-mounted trim switches will not have any effect. (5) Maintenance Mode: The Maintenance mode is used to rig the FCC and REUs via the CMC. The FCC can only enter Maintenance mode if the aircraft is in the “on-ground stationary” condition (Both MLG WOW = true AND wheel speed is 22° Speed brakes extended with landing gear down PARK / EMERG BRAKE Handle not down L-R Elevator Fail (caution) Both REUs failed. OR Loss of elevator command to both elevators. Elevator Single Actuator Single elevator actuator has failed. (caution) OEM Provided Data Flight Controls Revision 15 2023-09-15 2A-27-00: 43 of 76 G650ER™ OPERATING MANUAL CAS Message Possible Cause(s) Pitch Authority Limit (caution) Pitch axis flight control surfaces approaching maximum displacement. (caution) Pitch Control Miscompare Pilot and copilot pitch control column positions are different. Pitch Trim Nose Down Limit Pitch trim at nose down limit. Pitch Trim Nose Up Limit Pitch trim at nose up limit. (advisory) (advisory) 4. Limitations: There are no limitations established for the elevator control system at the time of this writing. OEM Provided Data Flight Controls Revision 15 2023-09-15 2A-27-00: 44 of 76 G650ER™ OPERATING MANUAL The horizontal stabilizer surface is mounted at the top of the vertical stabilizer. The horizontal stabilizer is supported by an aft hinge and a forward dual-electric-motor jackscrew actuator. The left and right elevator surfaces are mounted on the rear spar of the horizontal stabilizer. 2. Description of Subsystems, Units and Components: a. Horizontal Stabilizer Trim System (HSTS): The HSTS interfaces directly or indirectly with the following systems: Primary Flight Control System Central Maintenance Computer Crew Alerting System Aircraft Electrical Power System Broadband Multilink (Antenna Control Unit) A portion of the pitch trim control is accomplished through a fully trimmable horizontal stabilizer control surface installed as part of the aircraft tail. The stabilizer surface is moved by the Horizontal Stabilizer Trim Actuator (HSTA), which is an electric, dual-load-path actuator. The electric motors and braking system on the HSTA receive electrical power and command inputs from the Horizontal Stabilizer Control Unit (HSCU), installed in the baggage Electronic Equipment Rack (EER). The HSCU normally receives rate commands from the FCCs. The FCC receives inputs from the trim switches on the pilot and copilot control wheels or the pitch trim switch located on the center pedestal. The HSTS has a backup mode of control in which the HSCU receives pilot inputs directly from the backup pitch trim switch located on the center pedestal. (1) HSTS Operation: The HSTS receives rate commands from the FCCs as a function of the FCC-embedded control laws. The maximum stabilizer rate is 0.4°/second. The minimum stabilizer rate is 0.15°/second. The HSCU provides power to the HSTA to move the stabilizer at the commanded rate. The HSCU monitors the HSTA rate and position and provides this data as well as system status to the FCC. When the FCC command is satisfied, the rate command is removed from the HSCU and the stabilizer motion ceases. The HSTS may also be controlled directly by pilot inputs in the event of loss of valid FCC commands. The HSTS receives inputs directly from the backup pitch trim switch located on the center pedestal. The HSCU converts this input to a minimum rate command to the HSTA. The HSTS has four modes of operation: OEM Provided Data Normal Control – The HSCU operates in an active / standby configuration. Both channels receive commands from the FCCs and both channels calculate commands. Only the active channel controls the HSTA. The HSTS operates in Normal mode when the FCCs are available and the HSCU is available. The HSTS operates in Normal mode whenever possible. Flight Controls Revision 15 2023-09-15 2A-27-00: 51 of 76 G650ER™ OPERATING MANUAL Standby Control – The HSTS will operate in standby mode if it is receiving valid commands from one of the FCCs but is not capable of moving the stabilizer as requested. In this case, the HSTS will communicate this status to the FCCs and the FCCs will trim the elevator surfaces as required. Backup Control – Backup control is provided via the BACKUP PITCH switch located on the center pedestal. A Stab Primary Trim Fail (caution) CAS message is posted to alert the crew that the HSTS is in Backup mode. Inputs to the switch are provided directly to the HSCU. The HSCU provides a minimum rate input to the HSTA. The HSTS enters Backup mode if both FCCs are not available on power up. The HSTS enters Backup mode from Normal mode when no valid input is received from either FCC for more than one second. The HSTS enters Normal mode when either FCC provides three consecutive frames of valid data. Maintenance – Maintenance mode is used to perform system rigging, perform Initiated Built-In Test (I-BIT), or perform troubleshooting on the HSTS. The HSTS operates in Maintenance mode only when all interlocks are valid. The interlocks are maintenance requests from the CMC, valid on-ground and stationary interlock from the FCC and valid FCS maintenance switch from the FCC. (2) HSTS Components: The HSTS system consists of the following components: (a) Horizontal Stabilizer Control Unit (HSCU): The HSCU is a dual-channel controller that operates in an active / standby configuration. It interfaces with the primary flight controls system through the FCCs. The HSCU interfaces with CAS and CMC systems through the aircraft MAUs, as well as the flight deck via the BACKUP PITCH switch on the center console. It has two mechanically and electrically separate control channels, each using a hardware and software dissimilar command / monitor architecture. The dual channels of the HSCU are identical with the exception of an additional bus from Channel 2 of the HSCU to the aircraft Antenna Control Unit (ACU) to provide horizontal stabilizer position. (b) Horizontal Stabilizer Trim Actuator (HSTA): (See Figure 21. Horizontal Components.) Stabilizer Electro-Mechanical The HSTA is a dual-load-path, irreversible electro-mechanical actuator incorporating a fail-safe design. The actuator incorporates two independent dual-channel position sensors to provide the HSTS with HSTA position. Two identical and independent electric motor-brake assemblies provide the actuation of the HSTA. The motor-brakes operate in an active / OEM Provided Data Flight Controls Revision 15 2023-09-15 2A-27-00: 52 of 76 G650ER™ OPERATING MANUAL standby configuration. One motor is capable of full performance of the HSTA. The HSTA has fully independent primary and secondary load paths. Under normal conditions, only the primary load path carries the HSTA operating and static loads, while the secondary load path remains unloaded. In case of a structural failure in the primary load path, the secondary load path immediately engages to carry the static loads and the HSTA locks, holding the horizontal stabilizer in the last commanded position for the remainder of the flight. As the locked-up HSTA is commanded to move, the stabilizer system detects the HSTA's failure to move and annunciates the failure to the flight and maintenance crews. The HSTA irreversibility is provided by a mechanical no-back device mounted on the HSTA ballscrew and by electro-mechanical brakes on each motor-brake assembly. Either the no-back device or the motor brake is capable of providing HSTA irreversibility under application of the limit load. 3. Controls and Indications: Note A full description of the Primary Flight Display appears in section 2B-05-00 and a description of the Flight Controls 2/3 synoptic page appears in section 2B-07-00. a. Circuit Breakers (CBs): The following CBs protect the horizontal stabilizer system: Circuit Breaker Name CB Panel Location Power Source STAB 1 DC LEER B-10 L ESS 28V DC STAB 2 DC REER A-7 R ESS 28V DC STAB CH 1 REER E-1 EMER 115V AC STAB CH 2 RPDB RMAC Right Main AC b. Crew Alerting System (CAS) Messages: The following CAS messages are associated with the horizontal stabilizer system: OEM Provided Data Flight Controls Revision 15 2023-09-15 2A-27-00: 53 of 76 G650ER™ OPERATING MANUAL CAS Message Possible Cause(s) Stab Primary Trim Fail (caution) Loss of valid pitch trim communication from the FCCs to the HSCU. NOTE: This message may be accompanied by the FCC Alternate Mode (caution) CAS message. Stabilizer Channel Fail (caution) A horizontal stabilizer control channel has failed. Stabilizer Failed (caution) Horizontal stabilizer not responding to movement commands. OR Surface position information is unreliable or unavailable. Stab Maintenance Required (advisory) A failure within the horizontal stabilizer system has occurred that does not prohibit movement. Stab Rigging Complete (advisory) Rigging is valid for the current aircraft. Message occurs when in Maintenance Mode after Auto Rigging is satisfactorily completed. 4. Limitations: There are no limitations established for horizontal stabilizer system at the time of this writing. OEM Provided Data Flight Controls Revision 15 2023-09-15 2A-27-00: 54 of 76 G650ER™ OPERATING MANUAL The Flap Actuation System (FAS) interfaces with the following aircraft systems: Aircraft Hydraulic System Aircraft Electrical DC Power System Flight Control Computer (FCC) Avionics, Crew Alerting System (CAS) Central Maintenance Computer (CMC) The FAS provides the actuation and control of a Fowler-type, single flap surface on the trailing edge of each wing. When extended, the flap surfaces provide an increase in the wing lift and drag for use primarily during takeoff, approach and landing. The FAS architecture is composed of components performing electrical, mechanical and hydraulic functions. Pilot commands are via the FLAP handle (Figure 23. Flap Handle Assembly). The handle interfaces with the Flap Electronic Control Unit (FECU), as well as the FCC and Backup Flight Control Unit (BFCU). The FECU provides excitation to the FLAP handle position sensors and monitors the handle position. The FECU interfaces via digital data busses with CAS, FCC and CMC systems. The Hydraulic Control Module (HCM), powered by the left, PTU, or AUX hydraulic system, provides hydraulic system pressure and flow to the FAS Power Drive Unit (PDU). The HCM manifold houses the Solenoid Operated Shutoff Valve (SOV) and the Electro-Hydraulic Servo Valve (EHSV) (both controlled by the FECU). The PDU converts hydraulic power into mechanical power, which is then transmitted through the torque shafts to the flap actuators attached to the flap surface. The following redundant design features are incorporated into the flap system: 2. Three electrically-independent position sensors inside the FLAP handle (two Rotary Variable Displacement Transducers [RVDTs] and a set of discrete position switches) FECU powered by two, independent, aircraft-supplied 28V DC power supplies The HCM SOV and EHSV Electrically-duplicated position sensors on the left and right outboard actuators HCM SOV pressure shutoff capability checked by the FECU at every flight System Operation: Flap surface movement only occurs when the FLAP handle is moved from one detent position to another detent position, provided the FECU determines that the command and FAS integrity are valid. The FECU command and monitor paths each excite and demodulate one of the FLAP handle position sensors. Both the command and monitor paths must agree on a valid commanded position before flap movement is allowed. The FECU controls the flap surface rate and direction via the HCM EHSV. The EHSV supplies the PDU hydraulic motor with hydraulic flow. The PDU drives both flap surfaces, via torque shafts and actuators. Aircraft hydraulic system OEM Provided Data Flight Controls Revision 15 2023-09-15 2A-27-00: 57 of 76 G650ER™ OPERATING MANUAL pressure to the EHSV is provided only if the HCM SOV is energized by the FECU. The FECU monitors the flap position, asymmetry, speed and direction based on feedback from the dual-channel position sensors on the left and right outboard actuators. If either FECU channel fails, then the FECU loses the ability to control the flaps, but a remaining healthy channel continues to report flap positions and flap status. Note A FECU failure results in the loss of control of the flap surfaces; however, the flap surfaces will remain in their last position. The FECU interfaces with FCC and avionics systems through digital Buses. The FECU provides the CMC with the flap system fault reporting / isolation and the avionics CAS with the flap system failure annunciation and flap surface position data / indication. Note In instances of total loss of hydraulic or electrical power to the flap system, the flaps will remain in their last position (held by the no-back devices integral with each actuator) when power was lost. Note The FCC angle-of-attack limiting schedule defaults to the ‘clean and protected leading edges’ condition for all flaps settings when ‘on ground stationary’ and remains latched in this condition up to 1500 ft radar altitude. This logic was implemented to support the immediate return scenario where flaps cannot be extended from 0°. In the event of a failure resulting in an uncommanded flap motion (for example, due to a failure in the HCM EHSV), the FECU will immediately detect the failure and arrest the uncommanded motion by de-energizing the HCM SOV, removing hydraulic pressure/flow to the HCM ESHV. In the event of a failure in the flap system that results in loss of PDU control of one flap surface (as for example, due to the mechanical disconnect of the torque shaft between the PDU and the inboard actuator), the FECU detects this failure by continuously monitoring the position feedback signals from the dual-channel position sensors on the left and right outboard actuators. Once a failure occurs, if the flap system is commanded to a new position and the flap surfaces start to move, the FECU will immediately detect the discrepancy between the left and right position sensors. The FECU then disables the flap system for the remainder of the flight by de-energizing the HCM SOV. The failure is annunciated to the flight crew and both flap surfaces remain at the position when the failure was detected. OEM Provided Data Flight Controls Revision 15 2023-09-15 2A-27-00: 58 of 76 G650ER™ OPERATING MANUAL Note In the event of a jam in any component of the flap actuating system, the FECU immediately detects that there is no system motion when commanded. In the event of a flap actuator mechanical disconnect from the flap surface, the unfailed flap actuator attached to the same surface is capable of holding the surface in position for the remainder of the flight. Upon flap system command to move (following the actuator disconnect failure), the unfailed actuator operation results in skewing of the associated flap surface. In this condition, the output forces produced by the unfailed actuator increase rapidly to the point at which the force limiter inside the unfailed actuator engages and locks the flap system. Since the system is locked by the force limiter, the command-response monitor in the FECU immediately detects that there is no system motion when commanded and it disables the flap system for the remainder of the flight. Both left and right wing flap surfaces are simultaneously operated by the flap actuation system to extend or retract according to pilot input. The FAS consists of the following components: 3. Flap Control Handle Flap Electronic Control Unit (FECU) Hydraulic Control Module (HCM) Power Drive Unit (PDU) Torque Drive Shafts and Pillow Blocks Flap Actuators Flap Position Sensors Description of Subsystems, Units and Components: a. Flap Control Handle: (See Figure 23. Flap Handle Assembly.) The FLAP handle is installed on the center console and provides pilot input command to the FECU, which provides excitation and demodulation of the FLAP handle’s two RVDTs. The handle travel is divided by the following four detents: 0 (Flaps Up), 10, 20 (Takeoff / Go Around), and 39 (Flaps Down). Each detent represents a commanded flap surface position. The FCC monitors the FLAP handle’s three micro-switches that indicate the four gate positions of the FLAP handle. b. Flap Electronic Control Unit (FECU): (See Figure 22. Wing Flaps System Schematic.) The FECU, located in the Right Electronics Equipment Rack (REER) provides control and system safety monitoring of the FAS. The FECU performs the control of the flap surface rate and direction of the movement by providing commands to the flap HCM. OEM Provided Data Flight Controls Revision 15 2023-09-15 2A-27-00: 59 of 76 G650ER™ OPERATING MANUAL c. Hydraulic Control Module (HCM): (See Figure 22. Wing Flaps System Schematic and Figure 24. Flap Components.) The HCM is installed on the landing gear center torque box immediately aft of the PDU. The HCM consists of a solenoid, an electro-hydraulic servo valve and a hydraulic manifold. The HCM responds to electrical commands received from the FECU and provides directional control, extend / retract and low / high speed rate control of the PDU. The HCM houses a SOV that stops hydraulic flow when not energized. The SOV is spring-loaded to the closed position. The valve opens when the solenoid coil is energized with 28V DC provided by the FECU. When open, the valve allows hydraulic system flow and pressure supply to the EHSV. The EHSV provides flow control to the PDU. d. Power Drive Unit (PDU): (See Figure 24. Flap Components.) The motion of the left and right flap surfaces are mechanically synchronized by the flap PDU. The PDU consists of a hydraulic motor and a gearbox with splined output shafts on both sides to interface with the flap drive shafts. Located in the main landing gear wheel well, the PDU receives hydraulic power from the flap HCM. The PDU converts hydraulic power into mechanical power in order to simultaneously drive the left and right hand flap surface actuators via torque shafts and pillow blocks. A port located on the bottom of the PDU gearbox provides for any external leakage into an ecological bottle. e. Torque Drive Shafts and Pillow Blocks: (See Figure 24. Flap Components.) 16 rigid drive shafts are installed on both wings and in the torque box area to transfer the torque generated by the PDU to the flap system actuators. Both ends of the drive shafts have universal joints to accommodate the angular misalignment and linear offset between the pillow blocks or flap actuator splines to which the tubes attach. Each end of the torque shafts has an internal spline that mate with the external spline shafts located on the actuators, PDU and pillow blocks. One end of each tube is secured to its mating spline with standard hardware; the remaining end is free to float axially to ensure freedom of motion during wing bending and flap deployment. A total of 12 pillow blocks are installed on both wings to support the torque tube ends. Each pillow block consists of two ball bearings, an aluminum housing and an externally-splined through-shaft (which interfaces with the internally splined end fittings of the torque drive shafts). The pillow block bearings are sealed to prevent FOD and moisture ingress and are packed with grease. f. Flap Actuators: OEM Provided Data Flight Controls Revision 15 2023-09-15 2A-27-00: 60 of 76 G650ER™ OPERATING MANUAL (See Figure 24. Flap Components.) Each flap surface is simultaneously driven by two linear ballscrew flap actuators. The actuators are lubricated with grease and vented to prevent corrosion. Flap actuators perform three basic functions: Conversion of high speed rotary motion at the input shaft to low speed linear motion at the translating nut. Irreversibility (the translating nut cannot be back-driven in normal operation) and/or torque shaft or actuator disconnect system failure mode. System overload protection (by limiting maximum force that each actuator can apply). In a case of a FAS jam or any other condition that results in increased FAS loading, the force-limiting function in each actuator provides overload protection of FAS components and the supporting structure by limiting the maximum actuator output load. Engagement of the force limiting device stalls the actuator. This causes a “trip” in one of the system safety monitors, which completely disengages the FAS. g. Flap Position Sensors: (See Figure 24. Flap Components.) A dual-channel position sensor is installed on each outboard flap actuator. Excitation of the flap position sensor is provided by the FECU. 4. Controls and Indications: Note A full description of the Primary Flight Display appears in section 2B-05-00 and a description of the Flight Controls 2/3 synoptic page appears in section 2B-07-00. a. Circuit Breakers (CBs): The following CBs protect the wing flaps system: Circuit Breaker Name CB Panel Location Power Source FLAP CMD LEER A-10 L ESS 28V DC Bus FLAP MON REER A-8 R ESS 28V DC Bus b. Crew Alerting System (CAS) Messages: The following CAS messages are associated with the wing flaps system: OEM Provided Data Flight Controls Revision 15 2023-09-15 2A-27-00: 61 of 76 G650ER™ OPERATING MANUAL CAS Message Flap Asymmetry (caution) Possible Cause(s) Flap position asymmetry detected. Flaps have stopped moving toward selected position. Flap Command Invalid (caution) Flap handle not in detent, or an RVDT channel has failed. Flaps Failed (caution) No surface movement when flap handle is commanded OR Surface movement in opposite direction OR Uncommanded flap surface movement. Flaps Maintenance Required A failure within the flaps system has occurred that does not prohibit commanded flap movement. Flaps Rigging Complete Rigging is valid for the current aircraft. Message occurs when in Maintenance Mode after Auto Rigging is satisfactorily completed. (advisory) (advisory) 5. Limitations: There are no limitations established for the wing flaps system at the time of this writing. OEM Provided Data Flight Controls Revision 15 2023-09-15 2A-27-00: 62 of 76 G650ER™ OPERATING MANUAL The aircraft has three pairs of spoiler surfaces (three on each wing). Each of the six spoiler panels provides speed brake and ground lift dump functions. Additionally, the midboard and outboard spoiler pairs provide roll control. For the inboard (IB) and midboard (MB) spoiler panels, the actuators are conventional Hydraulic Actuators (HAs). The outboard (OB) spoiler panel actuators use Electric Backup Hydraulic Actuators (EBHAs). In the event the right hydraulic system is lost, the outboard spoiler EBHAs operate in Electric Backup (EB). Note Speed brake and ground spoiler functions are not available when the Primary Flight Control System (PFCS) is in Backup mode (amber BFCU Active). Note Ground spoilers and Speed Brake auto retract are not available in Direct Mode. Note The Flight Control Computers (FCCs) control ground spoiler deployment and speed brakes. The spoiler commands are based on the pilot wheel positions and the speed brake lever. The FCCs perform the necessary control law computations (including command mixing between roll control and speed brake / ground lift dump functions) and send the spoiler position commands via two digital databuses to each of the REUs. In normal operation, each REU averages the position commands from the two FCCs. Actuator ram position feedback is sent back on the databus to the FCC(s) for monitoring. The speed brake function is performed by manually commanding the speed brake lever. The actuation of the speed brake lever will cause the three pairs of spoiler panels to deploy proportionally to the lever displacement. The speed brake handle input is provided to the FCCs through four Rotary Variable Differential Transducers (RVDTs). The control laws resident within the FCCs provide the necessary interlocks and protection for the deployment of speed brakes (simultaneous / symmetric deployment of the spoilers). Ground spoiler deployment is automatically controlled by the FCCs. 2. Description of Subsystems, Units and Components: a. Speed Brakes: All six spoiler panels can be controlled by the speed brake handle located on the left side of the center pedestal (see Figure 27. Speed Brake Handle Assembly). The handle is a fly-by-wire module. The handle module contains four RVDTs to translate the flight crew speed brake commands into analog signals, which are read by the FCCs. An internal friction device contributes to the feel and operation of the lever by the pilots. The handle module has a detent position for the speed brake OEM Provided Data Flight Controls Revision 15 2023-09-15 2A-27-00: 66 of 76 G650ER™ OPERATING MANUAL handle which holds the handle in the stowed position. The detent requires positive handle movement for spoiler deployment. Moving the handle out of the detent position will cause a light in the handle to illuminate and a Speed Brake Extended (advisory) CAS message. If the handle is moved out from the detent position and the throttles are not at idle, the handle will illuminate along with a Speed Brake Extended (caution) message. When the speed brakes are out of the stowed position and the throttles are advanced above 95% Throttle Resolver Angle (TRA), the speed brakes will “auto retract” without the speed brake handle being repositioned. This auto retraction will cause a Speed Brake Auto Retract (caution) CAS message to be displayed. To reset the auto retract, the speed brake handle must be placed back to the stow / retracted position, and then if needed the speed brakes will react to the handle input. The reset of the handle is required even if the throttles are less than 95% TRA. Note b. The speed brake “auto retract” function will only activate in FCC Normal or Alternate modes. Ground Spoilers: All six spoilers are used to reduce lift on the wing to enhance the effectiveness of the main landing gear brakes. When the conditions have been meet for auto ground spoiler deployment, all six spoiler panels will deploy to a full 55°. The ground spoiler deploy requirements are: * GND SPOILER Switch: ARMED AND * Both Throttles at idle AND * One or more of the following conditions: (1) Left MLG WOW AND (left wheel speed > 47 kts) (2) Right MLG WOW AND (right wheel speed > 47 kts) (3) Both WOW AND (radalt < 10 ft OR invalid) (4) (Both wheel speed > 47 kts) AND (radalt < 10 OR invalid) AND (flaps > 22 ORGPWS/GND SPLR FLAP ORIDE switch ON) AND * BFCU is not ACTIVE The ground spoilers are normally armed prior to takeoffs and full-stop landings. During takeoff the ground spoilers will remain stowed provided that the throttles are out of the idle position (>2.5° TRA). If the flight crew elects to abort the takeoff, the ground spoilers will deploy when the throttles are retarded to idle. c. Ailerons as Ground Spoilers: OEM Provided Data Flight Controls Revision 15 2023-09-15 2A-27-00: 67 of 76 G650ER™ OPERATING MANUAL The ailerons deploy as ground spoilers to reduce lift and increase drag after landing or during a rejected takeoff. For the ailerons to function as ground spoilers, the GND SPOILER switch in the cockpit center pedestal must be ARMED. The activation logic is the same as that used for the ground spoilers (i.e., weight-on-wheels or wheel speed, and both throttles at the idle position). When the ailerons deploy as ground spoilers, the Flight Control Computer (FCC) commands them to the full trailing edge-up position; however, aircraft roll control is unaffected, utilizing a single aileron with an approximate doubled displacement ratio with respect to control wheel input. Additionally, to balance the nose-up pitching moment created with the ailerons deploying as ground spoilers, a slight elevator trailing-edge-down displacement is simultaneously commanded by the FCC. Removing the ground spoiler function of the ailerons requires the same pilot actions as stowing the ground spoilers (i.e., selecting the GND SPOILER switch to the OFF position or advancing at least one throttle forward, out of the idle position). The ‘ailerons as ground spoilers’ function is only available when operating in FCC Normal and Alternate modes. d. GND SPOILER and GPWS / GND SPLR FLAP ORIDE Switches: (See Figure 28. Spoiler System Indications and Controls.) (1) GND SPOILER: For automatic ground spoiler deployment, the GND SPLR switch must be placed in the ARMED position. The switch is a split lens with the upper portion labeled OFF (amber), and the lower portion labeled ARMED (blue). When the switch is extended, OFF is illuminated (gear down) or the switch is dark (gear up). When the switch is depressed, ARMED is illuminated. (2) GPWS / GND SPLR FLAP ORIDE: The GPWS / GND SPLR FLAP ORIDE switch serves two functions. The primary function is that it allows the flight crew to inhibit certain EGPWS aural warnings that occur when the aircraft is at lower altitudes (calculated by the EGPWS system based on the flight conditions and local terrain) with flaps not set to a landing configuration. The other function is to allow the use of only wheelspeed logic in the automatic ground spoiler deployment when the flap setting is 20 degrees or less. The presence of both wheelspeed signals by themselves is not allowed to trigger deployment unless the flap setting is greater than 22 degrees (provided the system is armed and throttles at idle). This feature is primarily to remove wheelspeed logic from the take off condition where flaps are normally set at 20 or less and the aircraft is climbing out with the landing gear still extended. In that situation, both wheelspeed signals can remain present as the wheels spin down. If the throttle was brought back to idle for any reason, there could be automatic deployment since the system is normally ARMED on take off. The chances of such an occurrence is further reduced by adding the radar altimeter < 10feet logic. However, if both radar altimeters OEM Provided Data Flight Controls Revision 15 2023-09-15 2A-27-00: 68 of 76 G650ER™ OPERATING MANUAL are invalid, they are removed from the logic -- leaving only the wheelspeed and flap position. (Reference the logic definition above.) If landing with flaps less than 22 degrees, depressing the GPWS GND SPLR / FLAP ORIDE switch to ON enables the combined left and right wheelspeed logic to deploy the spoilers. 3. Controls and Indications: Note A full description of the Primary Flight Display appears in section 2B-05-00 and a description of the Flight Controls 2/3 synoptic page appears in section 2B-07-00. a. Circuit Breakers (CBs): The following CBs protect the spoiler system: Circuit Breaker Name CB Panel Location Power Source L INBD SPLR HA LEER A-7 L ESS 28V DC Bus R INBD SPLR HA LEER A-6 L ESS 28V DC Bus L MID SPLR HA PRI REER B-5 R ESS 28V DC Bus R MID SPLR HA PRI REER B-6 R ESS 28V DC Bus L MID SPLR HA SEC REER C-5 R ESS 28V DC Bus R MID SPLR HA SEC REER C-6 R ESS 28V DC Bus L OUTBD SPLR EBHA PRI REER C-1 UPS 28V DC Bus R OUTBD SPLR EBHA PRI REER C-2 UPS 28V DC Bus L OUTBD SPLR EBHA SEC LEER B-7 L MAIN 28V DC Bus R OUTBD SPLR EBHA SEC LEER B-6 L MAIN 28V DC Bus L OUTBD SPLR EBHA PWR — EBHA PDB EBHA Bus 28V DC L OUTBD SPLR EBHA PWR — EBHA PDB EBHA Bus 28V DC THROT QUAD CPOP D-8 R MAIN 28V DC Bus b. Crew Alerting System (CAS) Messages: The following CAS messages indicate the status of the speed brake / ground spoiler system: OEM Provided Data Flight Controls Revision 15 2023-09-15 2A-27-00: 69 of 76 G650ER™ OPERATING MANUAL CAS Message Possible Cause(s) Aircraft Configuration (warning) On ground: Position of one or more of the following is not correct: FLAP Handle SPEED BRAKE Handle PARK / EMERG BRAKE Handle Landing Gear Control Handle Thrust Reverser Lever(s) GPWS/GND SPLR FLAP ORIDE Switch Pitch, Rudder, and/or Roll Trim Main Door NOTE: Message activation inhibited at speeds greater than V1 - 20 kts. In flight: One or more of the following: Speed brakes extended with Flaps >22° Speed brakes extended with landing gear down PARK / EMERG BRAKE Handle not down Ground Spoiler (warning) Failure of ground spoiler component or deployed ground spoiler panel. NOTE: Not available in FCC Direct mode or BFCU operation. Speed Brake Auto Retract (caution) Speed brakes (flight spoilers) automatically retracted with speed brake handle not in stowed position and TLA ≥90%, or AOA limiting encountered. NOTE: Not available in FCC Direct mode or BFCU operation. Speed Brake Extended (caution) Speed brakes (flight spoilers) are deployed with throttles above idle. NOTE: Not available in FCC Direct mode or BFCU operation. Speed Brake Fail (caution) OEM Provided Data Speed Brake control failed OR At least two pair of spoilers inoperative. Flight Controls Revision 15 2023-09-15 2A-27-00: 70 of 76 G650ER™ OPERATING MANUAL CAS Message Possible Cause(s) Spoiler Panel Fail (caution) REU failure OR Loss of spoiler command to any spoiler panel. Ground Spoiler Unarm (advisory) Ground spoiler system is not armed, with landing gear extended. Speed Brake Extended (advisory) Speed brakes are extended, throttles at idle. NOTE: Not available in FCC Direct mode or BFCU operation. 4. Limitations: a. Speed Brakes: Speed brakes are not approved for extension with flaps at 39° (DOWN) or with landing gear extended in flight. b. Automatic Ground Spoilers: If a touch-and-go landing is to be performed, the GND SPLR switch must be OFF and manual spoiler landing distances must be taken into account. With automatic ground spoilers inoperative, takeoff is permitted on dry and wet runways (less than 3mm of standing water) provided 20° flaps are used. OEM Provided Data Flight Controls Revision 15 2023-09-15 2A-27-00: 71 of 76