Forensic Examination of Fibres, Third Edition PDF
Document Details
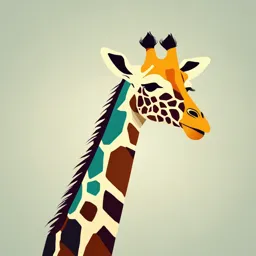
Uploaded by RemarkableIllumination1432
Bundelkhand University
James Robertson, Claude Roux, and Kenneth G. Wiggins
Tags
Summary
This book provides a comprehensive examination of fiber evidence, techniques, and casework. It covers topics such as fiber types, microscopic examination, and advanced methods. This edition focuses on applications of forensic science to real cases and situations in addition to addressing crucial aspects of quality assurance and interpretation techniques.
Full Transcript
Forensic Examination of Fibres International Forensic Science and Investigation Series Series Editor: Max Houck Forensic Examination of Hair James Robertson ISBN 978074840567...
Forensic Examination of Fibres International Forensic Science and Investigation Series Series Editor: Max Houck Forensic Examination of Hair James Robertson ISBN 9780748405671 · 1999 Forensic Examination of Fibres, 2nd edition J. Robertson and M. Grieve ISBN 9780748408160 · 1999 Forensic Examination of Glass and Paint: Analysis and Interpretation B. Caddy ISBN 9780748405794 · 2001 Forensic Speaker Identification P. Rose ISBN 9780415271827 · 2002 Bitemark Evidence B. J. Dorion ISBN 9780824754143 · 2004 The Practice of Crime Scene Investigation J. Horswell ISBN 9780748406098 · 2004 Fire Investigation N. Nic Daéid ISBN 9780415248914 · 2004 Forensic Computer Crime Investigation Thomas A. Johnson ISBN 9780824724351 · 2005 Analytical and Practical Aspects of Drug Testing in Hair Pascal Kintz ISBN 9780849364501 · 2006 Nonhuman DNA Typing: Theory and Casework Applications Heather M. Coyle ISBN 9780824725938 · 2007 Chemical Analysis of Firearms, Ammunition, and Gunshot Residue James Smyth Wallace ISBN 9781420069662 · 2008 Forensic Science in Wildlife Investigations Adrian Linacre ISBN 9780849304101 · 2009 Scientific Method: Applications in Failure Investigation and Forensic Science Randall K. Noon ISBN 9781420092806 · 2009 Forensic Epidemiology Steven A. Koehler and Peggy A. Brown ISBN 9781420063271 · 2009 Ethics and the Practice of Forensic Science Robin T. Bowen ISBN 9781420088939 · 2009 Introduction to Data Analysis with R for Forensic Scientists James Michael Curran ISBN: 9781420088267 · 2010 Forensic Investigation of Explosions, Second Edition A. Beveridge ISBN 9781420087253 · 2011 Firearms, the Law, and Forensic Ballistics, Third Edition Tom Warlow ISBN 9781439818275 · 2011 The Neuroscience of Handwriting: Applications for Forensic Document Examination Michael P. Caligiuri and Linton A. Mohammed ISBN 9781439871409 · 2012 Forensic Metrology: Scientific Measurement and Inference for Lawyers, Judges, and Criminalists Ted Vosk and Ashley F. Emery ISBN 9781439826195 · 2015 Fingerprints and Other Ridge Skin Impressions, Second Edition C. Champod, C. Lennard, P. Margot, and M. Stoilovic ISBN 9781498728935 · 2016 Forensic Examination of Fibres, Third Edition James Robertson, Claude Roux, and Kenneth G. Wiggins ISBN 9781439828649 · 2017 Forensic Examination of Fibres Third Edition Edited by James Robertson, Claude Roux and Kenneth G Wiggins CRC Press Taylor & Francis Group 6000 Broken Sound Parkway NW, Suite 300 Boca Raton, FL 33487-2742 © 2018 by Taylor & Francis Group, LLC CRC Press is an imprint of Taylor & Francis Group, an Informa business No claim to original U.S. Government works Printed on acid-free paper International Standard Book Number-13: 978-1-4398-2864-9 (Hardback) This book contains information obtained from authentic and highly regarded sources. Reasonable efforts have been made to publish reliable data and information, but the author and publisher cannot assume responsibility for the validity of all materials or the consequences of their use. The authors and publishers have attempted to trace the copyright holders of all material reproduced in this publication and apologize to copyright holders if permission to publish in this form has not been obtained. If any copyright material has not been acknowledged please write and let us know so we may rectify in any future reprint. Except as permitted under U.S. Copyright Law, no part of this book may be reprinted, reproduced, transmitted, or utilized in any form by any electronic, mechanical, or other means, now known or hereafter invented, including photocopying, microfilming, and recording, or in any information storage or retrieval system, without written permission from the publishers. For permission to photocopy or use material electronically from this work, please access www.copyright.com (http://www. copyright.com/) or contact the Copyright Clearance Center, Inc. (CCC), 222 Rosewood Drive, Danvers, MA 01923, 978-750- 8400. CCC is a not-for-profit organization that provides licenses and registration for a variety of users. For organizations that have been granted a photocopy license by the CCC, a separate system of payment has been arranged. Trademark Notice: Product or corporate names may be trademarks or registered trademarks, and are used only for identification and explanation without intent to infringe. Library of Congress Cataloging-in-Publication Data Names: Robertson, J. (James), 1950- editor. | Roux, Claude (Forensic scientist) editor. | Wiggins, Kenneth G., editor. Title: Forensic examination of fibres / edited by James R. Robertson, Claude Roux, and Kenneth G. Wiggins. Description: Third edition. | Boca Raton : CRC Press, | Includes bibliographical references and index. Identifiers: LCCN 2017021297| ISBN 9781439828649 (hardback : alk. paper) | ISBN 9781315156583 (ebook) Subjects: LCSH: Criminal investigation. | Textile fibers–Identification. Classification: LCC HV8077.5.C6 F67 2018 | DDC 363.25/62–dc23 LC record available at https://lccn.loc.gov/2017021297 Visit the Taylor & Francis Web site at http://www.taylorandfrancis.com and the CRC Press Web site at http://www.crcpress.com Contents Preface to second edition ix Preface to the third edition xi Editors xiii Contributors xv 1 Fibres, Yarns and Fabrics: An Introduction to Production, Structure and Properties 1 STANLEY MACARTHUR FERGUSSON AND JANE HEMMINGS 2 Textile Damage Interpretation 61 JANE HEMMINGS, DEBRA CARR AND JAMES ROBERTSON 3 Ropes and Cordages 89 KENNETH G WIGGINS 4 From Crime Scene to Laboratory 99 JAMES ROBERTSON AND CLAUDE ROUX 5 Microscopic Examination of Fibres 145 SAMUEL J PALENIK 6 Colour Analysis of Fibres 179 THOMAS W BIERMANN AND KENNETH G WIGGINS 7 Infrared Microspectroscopy of Fibres 245 K PAUL KIRKBRIDE 8 Raman Spectroscopy of Fibres 289 JANE HEMMINGS 9 Other Instrumental Approaches to Fibre Examination 309 CLAUDE ROUX, RACHEL MORISON AND PHILIP MAYNARD 10 Interpretation of Fibre Evidence 345 MICHAEL GRIEVE, CLAUDE ROUX, KENNETH G WIGGINS, CHRISTOPHE CHAMPOD AND FRANCO TARONI vii viii Contents 11 Future Trends for Forensic Fibre Examination 427 KORNELIA NEHSE, SANDRA KOCH, MICHAEL GRIEVE, MAX M HOUCK AND JAMES ROBERTSON Index 455 Preface to second edition By the time this volume is published, it will have been seven years since the first edition of Forensic Examination of Fibres appeared in print. This new volume contains material based on some of the content of that edition, and contributions from many new authors. The subject material covered has been considerably expanded, and all material, at the very minimum, has been revised and brought up to date. The past seven years have seen the introduction of several new fibres into the marketplace, yet the fibre types likely to be seen in the routine life of a forensic scientist remain relatively few. The content of this volume reflects an increased understanding of the importance of the interpretation of fibre find- ings and of the critical content-type of quality assurance in ensuring the reliability of the technical observations and results. It is our hope that this volume will remain relevant for another seven years. To our contributing authors, our sincere and warm thanks for their efforts. To our various helpers in bringing this project to fruition and to our Commissioning Editor, Dilys Alam, thanks for your patience and understanding. James Robertson Canberra Mike Grieve Wiesbaden ix Preface to the third edition In the preface to the second edition my co-editor, Mike Grieve, and I hoped the second edition would remain relevant for another seven years. In fact, it will be closer to 17 years between editions with this third edition. Sadly, the passage of time has seen the sad loss of Mike Grieve and Ken Wiggins, both giants in the forensic fibre world. The content of this new edition sees some new authors, again reflecting the passage of time, but we very much want to preserve the contributions by Mike and Ken for at least one more edition. We hope that this edition continues to be of value to students and forensic practitio- ners around the world whether new to the field or experienced forensic scientists. This will be the final edition for one of us (JR) as it is time to hand on the baton to a younger generation. Finally, to our authors, your patience with us has been nothing short of remarkable! To Taylor & Francis Group, once again, our thanks for not losing faith. James Robertson Canberra Claude Roux Sydney xi Editors James Robertson of the National Centre for Forensic Studies (NCFS) at the University of Canberra graduated with a BSc (Hons) in 1972 and PhD in 1976 from the University of Glasgow. He lectured in forensic science at the University of Strathclyde from 1976 to 1985 before moving to Australia. After five years at the State Forensic Science Centre in Adelaide, he completed twenty years as the head of the forensic group with the Australian Federal Police (AFP), in the process developing a world class and respected forensic group from modest beginnings. He returned to an academic role as a Professorial Fellow on his retirement from the AFP in 2010. He is currently also the Director of the NCFS. He is also an Honorary or Adjunct Professor at several Australian and overseas uni- versities. He has published well over 100 scientific papers and book chapters, edited or coedited four textbooks, is the Editor of the Australian Journal of Forensic Sciences and is a member of the editorial boards of several journals. He has held senior positions on all forensic advisory groups and organisations in Australia, including being the current President of the Australian Academy of Forensic Sciences (AAFS), Vice-President of the Australian and New Zealand Forensic Science Society (ANZFSS), Chair of the Advisory Forum to the National Institute of Forensic Sciences (NIFS), Chair of Standards Australia (SA) Forensic Committee and a past Chair of the Senior Managers Australian and New Zealand Forensic Laboratories (SMANZFL). His contributions to the forensic sciences and education have been recognised with the awards of a Doctor of the University by the University of Canberra, the Australian Public Service Medal (PSM) and a Member of the Order of Australia (AM). James continues his active interest in, and passion for, the forensic aspects of trace evidence, especially fibres and hairs. Claude Roux completed his undergraduate and PhD studies in forensic science at the University of Lausanne, Switzerland, then migrated to Australia in 1996, where he was appointed as a lecturer at the University of Technology Sydney (UTS). His PhD thesis focused on fibre evidence interpretation. Since then, Claude has been pivotal to the devel- opment of forensic science in his adopted country over the past 21 years by developing and leading the first undergraduate degree and PhD programs in forensic science in Australia. In 2002, he became the founding Director of the UTS Centre for Forensic Science, being Professor of Forensic Science since 2004. His professional motivation has been largely driven by his vision of forensic science as a distinctive academic and holistic research- based discipline. Throughout his career, Claude has published more than 160 refereed papers and 25 book chapters and a large number of conference presentations. Although his research activities cover a broad spectrum of forensic science across social and experimental sci- ences, he remains active in the area of fibres, being a member of the European Fibres Group xiii xiv Editors (now ENFSI Textile and Hair Group) since its inception in 1993. Claude is a member of the editorial board of six scientific journals and of a number of working and advisory groups. He is the immediate past President of the Australian and New Zealand Forensic Science Society (ANZFSS), the current Vice-President of the Australian Academy of Forensic Sciences and a Fellow of the Royal Society of New South Wales. Between 2014 and 2016, he also served on the Scientific Advisory Board of the International Criminal Court, The Hague, the Netherlands. Kenneth G Wiggins joined the then Metropolitan Police Forensic Science Laboratory (MPFSL) in London in 1970. Moving from the Biochemistry section, Ken specialised in the forensic examination of fibres. With the merger of the MPFSL into the Forensic Science Service (FSS) in 1996, he moved to the Analytical Services group before a move to the Research and Development Division as an advisor and consultant dealing with fibres. Ken published a number of key papers especially in the areas of fibre dye analysis, and he was the author of the chapter on ropes and cordage in the second edition of the Forensic Examination of Fibres which has been retained in this third edition. Ken formed a close professional relationship with Mike Grieve that saw them work on a number of major stra- tegic projects such as the establishment of the European Fibres Group (EFG), with Mike and Ken taking on the executive roles in this group and developing it into one of the most successful ENSFI (European Network of Forensic Institutes ) working groups. Ken was to be a co-editor of this third edition, but sadly he passed away in 2009 from motor neurone disease. As with the contributions to the second edition from Mike Grieve, the contribu- tions from Ken have also been retained and updated, where appropriate, to recognise the substantial contribution he made to the forensic examination of fibres over a forty-year time span in forensic science. Contributors Thomas W Biermann is currently with the Forensic Science Institute in Wiesbaden, Germany. Thomas graduated from the University of Frankfurt with a BSc in Biology in 1983. In 1988 he gained his PhD after completing research dealing with the impact of UV-B radiation on lipid metabolism and on fatty acid patterns in synchronously growing marine diatoms. Thomas then joined the Forensic Science Institute in the Bundeskriminalamt and specialized in the examination of fibres and textiles. His special interests included the development of software for databases and for the evaluation of fibre and textile frequen- cies in clothing. From 1999 to 2006 Thomas was the head of the Fibres Section. He lectured in Europe and the United States of America and he has been the author and co-author of many publications concerning fibre and colour frequencies. He was awarded the PW Allen Award of the Forensic Science Society (now The Chartered Society of Forensic Sciences) for the most meritorious paper published in Science & Justice in 1997 and 2001 with Mike Grieve and in 2007 as a sole author. In 2006, Thomas won the Michael C. Grieve Award for the best presentation given on the Meeting of the European Fibres Group at Rome. Thomas was a member of the steering committee of the European Fibres Group and together with Ken Wiggins a member of the Scientific Working Group for Materials (SWGMAT) Fibers Section in the United States. After almost 20 years of reporting in court and research deal- ing with the evidential value of fibres and colours, since November 2006, he has been the head of the Drugs Section of the Forensic Science Institute at the Bundeskriminalamt. From 2013 on, Thomas has been the head of Biometrics Department and vice president of the Forensic Science Institute at the Bundeskriminalamt. Debra Carr has a BSc(Hons) in Materials Science and a PhD in Engineering. Debra is a Reader in Impact and Armour at Cranfield University at The Defence Academy of the UK. Debra is a Chartered Engineer, a Fellow of The Institute of Materials, Minerals and Mining and a Professional Member of The Chartered Society of Forensic Science. In 2012, Debra was a Winston Churchill Travelling Fellow in Forensic Textile Science. Debra has published over 60 articles in peer-reviewed journals and over 50 conference papers. Debra's research interests include: forensic textile science, body armour and helmet optimisation, wound ballistics and clothing and textile sciences. Christophe Champod received his MSc and PhD (summa cum laude), both in Forensic Science, from the University of Lausanne, in 1990 and 1995, respectively. He remained in academia until holding the position of assistant professor in forensic science. From 1999 to 2003, he led the Interpretation Research Group of the Forensic Science Service (UK), before taking a full professorship position at the School of Criminal Justice (ESC) of the University of Lausanne. He is in charge of education and research on identification methods and maintains an activity as an expert witness in these areas. He is a Steering Committee mem- ber for the International Fingerprint Research Group (IFRG), past member of SWGFAST xv xvi Contributors (Scientific Working Group on Friction Analysis, Study and Technology) and, since 2014, an invited member of Friction Ridge subcommittee (part of the Physics and Pattern Evidence Scientific Area Committee) of the Organization for Scientific Area Committees (OSAC). In 2015, he received the Distinguished ENFSI (European Network of Forensic science) Scientist award for his contribution to forensic science. His research is devoted to the infer- ential aspects associated with forensic identification techniques. Stanley (“Mac”) MacArthur Fergusson graduated from Leeds University with a diploma in Textile Industries in 1963. His early employment was as a dyer in both wool and syn- thetic fibres in the United Kingdom. Upon his return to Australia in 1966, Mac worked for Yorkshire Chemicals Pty Ltd as technical representative in both leather and textile dyeing, covering Australia and the Asia Pacific regions. Mac also spent over 4 years in Indonesia as CEO of PT Yorkshire Indonesia. He joined RMIT after a short time with the Melbourne College of Textiles. In 1970, Mac was awarded chartered Textile Technologist (C.Tex.ATI) from the Textile Institute Manchester. He is also a Chartered Colourist (C.Col ASDC) from the Society of Dyers & Colourists, Bradford, Yorkshire. In 2009, Mac graduated with a masters of technology (MTech) from RMIT University, where his research focused on the effect of residual detergents on the light fastness of certain reactive dyes on cotton. Currently, his major areas of research are in dye performance and the forensic aspects of textile materials. Michael Grieve. Sadly, this bio for Michael Grieve recognises the significant contribution made by Mike to the advancement of forensic fibre examination over a close to 40-year period before his untimely and sudden death in 2002. His contribution is more fully recog- nised in the addendum to chapter 11, which deals with the future of forensic fibre examina- tion. He is retained as an author in this third edition with his previous contributions being updated where appropriate. Included in his many achievements, along with Ken Wiggins, he established the European Fibres Group (EFG) that continues its work today as part of the ENFSI (European Network of Forensic Institutes) Textile and Hair Group (ETHG). Mike was the driving force behind the production of a Manual of Best Practice for the Forensic Examination of Fibres. In 2003 he was awarded the ENSFI Distinguished Scientist Award posthumously. Mike published the results of his research throughout his career and unselfishly shared his knowledge. His only goal was to promote the best use of fibre evidence. He was a friend, colleague and mentor to many, and it is a privilege to retain his contribution to this book which he had such a strong influence in developing in the second edition as co-editor. Jane Hemmings is currently working in the Capability Development Office of the Australian Federal Police and prior to this was a Senior Scientist with the Chemistry team in the Forensics portfolio. Jane started work in the AFP Chemical Criminalistics team in 2005 after graduating with a PhD from the University of Technology Sydney, focusing on the use of Raman spectroscopy in forensic fiber examinations. As a qualified fiber and textile dam- age examiner, Jane has been involved in major homicide investigations that have required scene attendance, laboratory examination and the provision of expert evidence. Following a homicide in 2005, Jane reinvigorated textile damage examinations in the AFP and in 2008 established the Australian and New Zealand Textile Damage Working Group bringing together experts from across jurisdictions to advance the evidence class in the region. Contributors xvii Max M Houck is an international forensic expert with over 25 years of experience. Houck has experience in the private sector, academia, local government, and worked at the Federal Bureau of Investigation Laboratory Division. He has worked as a forensic anthropologist, a trace evidence analyst, a researcher, and has managed millions of dol- lars in grants and awards. Most recently, he was the inaugural Director of the Department of Forensic Sciences in Washington, D.C., overseeing 150 employees and managing the forensic science laboratory, the public health laboratory, and crime scene sciences for the nation’s capital. Max has worked on a number of mass casualty scenes, including the Branch Davidian Investigation and the September 11, 2001 attack on the Pentagon. He is one of the most published forensic experts in the world. He has dozens of peer-reviewed journal articles and is the author and editor of numerous books. He is co-author of the best-selling Fundamentals of Forensic Science, Science of Crime Scenes, and Success with Expert Testimony, among others. He is the editor of the Advanced Forensic Science series of books. Houck is also founding co-editor of Forensic Science Policy and Management (the official journal of ASCLD), the only journal that addresses the management, policy, and administration of forensic science. K Paul Kirkbride is currently Professor of Forensic Science at Flinders University in Adelaide South Australia. Before entering academia in 2013 he was Chief Scientist with the Forensic and Data Centres portfolio of the Australian Federal Police for five years, and prior to that, he was Manager of Business Programs at the National Institute of Forensic Science in Melbourne. For the other 20 years of his time as a forensic scientist, Paul worked with Forensic Science SA in Adelaide South Australia. With that organization he was a trace evidence examiner, illicit drugs analyst, clandestine drug laboratory investigator and, eventually, Assistant Director – Science. He attributes any success he might have in regards to handling textile fibres under various microscopes to a long and devoted attachment to trout fly-tying. Sandra Koch has worked in the field of forensic trace evidence analysis for over 16 years. She holds a BA in Anthropology and Political Science from University of Michigan, Ann Arbor, an MFS in Forensic Science from George Washington University, an MS in Forensic Anthropology from the Boston University School of Medicine. From 1997 until 2013, she worked for the FBI Laboratory Trace Evidence Unit. During that time she analyzed hairs, fibers, fabric damage, and feathers using a range of instrumentation including light microscopy, polarized light microscopy, fluorescence microscopy, microspectrophotom- etry and infrared spectroscopy. She has taught numerous workshops and short courses on hairs, fibers, crime scene evidence collection and other specialized trace evidence analysis. She is a Fellow of the American Academy of Forensic Sciences, a founding member of the American Society of Trace Evidence Examiners and a Fellow of the American Board of Criminalistics (Hairs and Fibers). Sandy has been a member of the Scientific Working Group for Materials Analysis (SWGMAT) since 1999, served as the chair of the fiber sub- group from 2009 to 2013, and is currently a member of the OSAC Materials (trace) sub- group. She has published in the areas of forensic analysis of hairs, fibers, fabric damage, and feather identification. Currently Sandy is pursuing a PhD in biological anthropology at the Pennsylvania State University, drawing on her background in microscopical analy- sis to integrate forensic and anthropological analysis of hair and has research interests in archaeological textiles. xviii Contributors Philip Maynard is a senior lecturer with the Centre for Forensic Science at the University of Technology Sydney. He teaches the Crime Scene Investigation and Fire and Explosives Investigation subjects at UTS, as well as supporting the other forensic subjects in the foren- sic undergraduate programme. Phil graduated from the University of Sydney in 1992 with a PhD in chemistry, and entered the forensic world in 1995 when he was employed in the Physical Evidence Section at the Division of Analytical Laboratories (FASS). His casework experience includes flammable liquids, explosives, paint, fibres and glass analysis. Phil joined the forensic science programme at UTS in 1998 and has published peer-reviewed research in the fields of fibre evidence, glass evidence, latent fingermark detection, foot- wear impressions and explosives analysis. Rachel Morison of the Centre for Forensic Science is a member of the Faculty of Science staff at the University of Technology Sydney, where she is currently a PhD candidate inves- tigating the detection and identification of acquired characteristics on fibres. She com- pleted a Bachelor of Forensic Science (Honours) in Applied Chemistry in 2012 with her Honours project looking at the effect and identification of unknown chemicals in cases of textile damage. Kornelia Nehse has been working in the field of forensics for more than 25 years. She received her diploma in Textile and Clothing Engineering in 1986 from the University of Applied Sciences in Moenchengladbach, Germany. After teaching in the field of tex- tile technology she moved to forensic science. She is currently the head of the Textiles and Micromorphology department of the Forensic Science Institute (LKA KT) in Berlin, Germany and furthermore the permanent representative within ENFSI (European Network of Forensic Science Institutes) for the Forensic Science Institute in Berlin. She is also the current chairperson of the European Textile and Hair Group (ETHG), a position she has held since 2003. She is a founding member of the European Fibres Group (EFG), now European Textile and Hair Group (ETHG) and member of the Scientific Working Group Material (SWGMAT) in the United States. She recently has also been involved in European projects, e.g. the set up of a Reference Data Base and Fibre Type Information System (FTIS) for the identification of textile fibres. Kornelia has lectured at or been affiliated with numerous universities in the fields of forensic science and textile technology including the HTW University of Applied Sciences and the Berlin University of the Arts (Berlin, Germany), The Brandenburg University of Technology (Cottbus, Germany), and the University of Parma (Parma, Italy). She is also an internationally recognized and invited speaker (e.g. EFG, ETHG, ENFSI, EAFS, SWGMAT, Trace Evidence, ANZFSS, IAFS) and has taught in numerous workshops and short courses from crime scene to court. Samuel J (“Skip”) Palenik has had a lifelong fascination with the microscope that started when he received his first instrument at the age of eight. Since then he has devoted himself to increasing his knowledge of analytical microscopy and microchemistry and applying it to the solution of real world problems, especially those of forensic interest. He was for- tunate in having worked closely with his mentor, Dr Walter McCrone, for over 30 years and to have studied forensic microscopy with Dr Max Frei-Sulzer of Zurich, a disciple of Dr Edmond Locard of Lyon. Skip has been teaching analytical microscopy to forensic Contributors xix scientists for more than 40 years and has published numerous scientific articles and book chapters on the applications of chemical and forensic microscopy. His most recent contri- bution is a chapter on the use of heavy minerals in forensic science published by Elsevier. He has also played a significant content-type in numerous criminal investigations includ- ing the Atlanta child murders, the Air India Bombing, the Jon Benet Ramsey case, the Narita Airport bombing (Tokyo), the Hillside Strangler (Los Angeles) case, the Oklahoma City bombing, the Ivan the Terrible (Jerusalem) case, the assassination of Dr Martin Luther King (reinvestigation by U.S. House Select Committee on Assassinations), the Unabomber case, the disappearance of Helen Brach, the ‘Kiki’ Camarena murder case and the Green River serial murders. He established Microtrace in 1992 to provide a resource for organi- zations and individuals in need of scientific services involving the analysis of microscopic trace evidence. His special research interests are the identification of single small particles, small amounts of complete unknowns and tracing dust and soil back to their origins. He is the 2009 recipient of the Paul L Kirk Award, the highest award given by the criminalistics section of the American Academy of Forensic Sciences, the 2013 Ernst Abbe Award for outstanding contributions to microscopy, the 2013 Edmond Locard Award presented by the American Society of Trace Evidence Examiners, and the Chamot Medal in chemical microscopy in 2010. He is listed in American Men and Women of Science. Franco Taroni is full professor of forensic statistics at the School of Criminal Justice of the University of Lausanne. He received his PhD in forensic science in 1996 from the University of Lausanne. He was awarded two European Community Grants for Training and Mobility of Researchers for a collaboration with Professor Aitken of the Department of Mathematics and Statistics of the University of Edinburgh. He spent four years as a research project manager at the Institutes of Forensic Medicine of the Universities of Lausanne and Zürich (Switzerland). Franco’s main areas of research, casework, and teach- ing are forensic statistics, Bayesian networks, and Bayesian decision-theoretic data analy- ses. He has authored and coauthored several books on these topics (i.e. Statistics and the Evaluation of Evidence for Forensic Scientists (2004), Bayesian Networks and Probabilistic Inference in Forensic Science (2006), Data Analysis in Forensic Science: A Bayesian Decision Perspective (2010) and Bayesian Networks for Probabilistic Inference and Decision Analysis in Forensic Science (2014). He is associate editor of the journal Law, Probability and Risk (Oxford University Press). Fibres, Yarns and Fabrics: An Introduction to Production, Structure and Properties 1 STANLEY MACARTHUR FERGUSSON JANE HEMMINGS Contents 1.1 Introduction 2 1.2 Fibres 2 1.2.1 Classification of Textile Fibres 3 1.2.2 Fibre Production 4 1.2.3 Fibre Characteristics 4 1.2.4 Properties of Fibre Forming Polymers 5 1.3 Natural Fibres – Vegetable Fibres 5 1.3.1 Seed Fibres – Cotton, Kapok and Coir 8 1.3.2 Stem Fibres – Flax, Jute, Ramie, Hemp, Kenaf 12 1.3.2.1 Flax 12 1.3.2.2 Jute 13 1.3.2.3 Ramie 13 1.3.2.4 Hemp 14 1.3.3 Leaf fibres – Sisal, Hemp (Manila and New Zealand) 14 1.3.3.1 Hemp-Abaca (or Manila Hemp) and New Zealand Hemp 14 1.3.3.2 Sisal and Henequen 15 1.4 Natural Fibres – Animal Fibres 15 1.4.1 Wool 16 1.4.1.1 Hair fibres or Speciality Wools 17 1.4.2 Silk—Silkworm 19 1.4.2.1 Spider Silk 20 1.5 Mineral Fibres (Asbestos) 20 1.6 Man-made Fibres 20 1.6.1 Fibres Regenerated from Natural Polymers 21 1.6.1.1 Viscose Rayon 21 1.6.1.2 Bamboo 23 1.6.1.3 Improved Forms of Viscose 24 1.6.1.4 Esters of Cellulose 25 1.6.1.5 Regenerated protein fibres 26 1.6.1.6 Alginate Fibres 26 1.6.2 Synthetic Fibres 26 1.6.2.1 Polyesters 28 1.6.2.2 Polyamides 30 1.6.2.3 Polyolefins 32 1 2 Forensic Examination of Fibres 1.6.2.4 Polyvinyl Fibres 34 1.6.2.5 Polyurethane Fibres 35 1.6.2.6 Aramides 36 1.6.2.7 Polyvinyl Alcohol Fibres 37 1.6.2.8 Inorganic Man-Made Fibres 37 1.7 Bicomponent Fibres 38 1.8 New Fibres 39 1.9 From Fibre to Fabric 39 1.9.1 Introduction 39 1.9.2 Yarns 40 1.9.2.1 Types of Yarns 41 1.9.3 Fabrics 41 1.9.3.1 Woven Fabrics 42 1.9.3.2 Knitted Fabrics 47 1.9.3.3 Pilling 52 1.9.4 Non-Woven Materials 53 1.9.4.1 Leather 55 1.10 Conclusions 57 Acknowledgments 58 Bibliography 58 Further Readings 58 Textbooks 58 1.1 Introduction If forensic fibre examiners are to fully exploit fibre and textile evidence during analysis they require not only specialised forensic knowledge but also knowledge of fibres, yarns and fabrics. Production, structure (both chemical and physical) and the properties of these materials is required in order to assess the value of fibre evidence. It is necessary to also know production figures, fashion changes, sudden arrivals of new material/s, dye variabil- ity and other factors that may have a bearing on the information obtained. What follows is a summary of fibres and the textiles that can be constructed from them. Information can also be obtained from catalogues, journals and texts, examples of which are listed at the end of this chapter. 1.2 Fibres The fundamental use of textiles by ancient man was for the purpose of protection and the initial textile used was the animal skin. As man became more sophisticated textiles became a way of showing status in wealth and society. Rapid population growth since World War II and consumerism has seen a rapid expansion of textile products from synthetic sources. Without synthetic textile products world production of natural fibres would be unable to satisfy world consumer demand for fibres and their products. The common misconception is that textiles relate in the main to apparel and home furnishings. There are however many other applications. These applications can be in the Fibres, Yarns and Fabrics 3 Table 1.1 Use of Textiles in Various Industries Industry Uses Medical Bandages, swabs, sutures, absorbent cloths Transport Inflatables, ropes, canvas, sails Mining Conveyor belts, flexible ducting, sacks Sports Windproof fabrics, playing surfaces, Equipment Furniture Upholstery, netting, bedding, wadding Horticulture Netting, shade cloths, hail protection, Twine Clothing Sewing threads, hats, garments, shoes Water Hoses, membranes, filters Chemical Filter fabrics, vat liners, overalls Architecture Awnings, carpets, wall coverings, drapes Aerospace Glider fabric, parachutes, composites Paper Making Filtration aids, conveyors, felts Automotive Deat belts, drive belts, interior trims, insulaion Civil Engineering Road construction, retaining walls, soil separation, slings Agriculture Animal coats & collars, sacks, flexible silos Defence Camouflage, clothing, ballistic vests industrial, medical, aerospace and automotive industries. Fibre types and processing routes vary depending on the industry of application. Table 1.1 lists examples of the wide variety of applications for textile products in the ever-changing world of industry. 1.2.1 Classification of Textile Fibres The basic component of a textile is a fibre. At the basic level all fibres fall into one of two categories: natural fibres and man-made fibres. Natural fibres fall into three chemical classes: Cellulose based fibres (from the seeds, stem and leaf of plants) Protein based fibres (from the hair, wool or silk of animals) Mineral based fibres (the only naturally occurring mineral fibre is asbestos the use of which is banned in many countries) Man-made fibres are manufactured and fall into three classes: Regenerated fibres (those formed from naturally occurring fibre-forming poly- mers, such as viscose from cellulose) Synthetic fibres (those formed from non-renewable sources, such as polyester) Inorganic fibres (those formed from inorganic materials, such as carbon and glass) Classification of fibres at this broad level is summarised in Figure 1.1. A more detailed breakdown within each class will be given as each is considered throughout this chapter. 4 Forensic Examination of Fibres Fibres Natural Man-made Animal Vegetable Organic Inorganic e.g. e.g. e.g. Wool Cotton Carbon Glass Transformation of natural Synthetic polymers e.g. e.g. Acetate Acrylic Lyocell Aramid Modal Modacrylic Figure 1.1 Broad classification of natural and man-made fibres. 1.2.2 Fibre Production Originally all textiles were composed of natural fibres, such as cotton, wool, silk, flax and jute. With the increasing demand for fibres that could perform a variety of functions, the invention and production of man-made fibres emerged. The first man-made fibre intro- duced in 1911 was rayon, which was a transformation of the naturally occurring poly- mer cellulose. The creation of synthetic polymers in 1930 made possible the production of organic synthetic polymer fibres. The first man-made synthetic polymer fibre was nylon in 1939. The development of new fibres continues even today (see Chapter 11) as advancing technical innovations expand fibre and fabric manufacturing processes. These innovations have resulted in more efficient manufacturing processes giving rise to a wider variety of products at lower cost to the consumer. As demand has shaped the quality of fibres manufactured so does demand influence the quantity of fibres produced each year. Global textile fibre production for the years 2000 and 2008 is illustrated in the Table 1.2. These figures show the very large increase in demand for polyester fibre, with relatively stable cotton production. Other natural fibres such as wool, silk and flax show little or no growth and static production. Polypropylene production and use, on the other hand, is growing, mainly due to its less complex manu- facture compared to nylon and polyester. 1.2.3 Fibre Characteristics Fibres used in textiles are fine and thin; the Textile Institute defines a fibre as: Textile raw material, generally characterised by flexibility, fineness and high ratio of length to thickness* Natural fibres, with the exception of silk, exist as staple fibres† with lengths ranging from 2 to 50 cm in length and cross sections ranging from 10 to 40 microns. The limited length of staple fibres means they need to be spun to be converted to a yarn. Synthetic fibres (and silks) are produced as continuous filament yarns. These yarns are sometimes cut to form staple yarns of specified lengths depending on the end use of the fibre. * Textile Terms and Definitions, 11th edition, Textile Institute. † A fibre of relatively short length. Fibres, Yarns and Fabrics 5 Table 1.2 Global Textile Fibre Production, for Major Fibre Types, for the Years 2000 and 2008 Global Textile Fibre Production (Million Tons) – 2000 2008 Cotton 19.7 24.4 Polyester 18.9 30.7 Polyamide 4.1 3.5 Polypropylene 6.0 5.9 Acrylics 2.7 1.9 Wool 1.3 1.2 Silk 0.1 0.2 Total 56.9 67.8 Source: Koslowski, H.-J. and Kassel, F. M., Fasen für Vliesstoffindustrie aktuelle Markttrends, 2008; American Fiber Manufacturers Association, Fibre Organon, 80, 95–112, 2009. The success of a fibre within a textile is significantly influenced by the polymer com- prising the fibre. 1.2.4 Properties of Fibre Forming Polymers Fibre forming polymers, either natural or synthetic, are a series of polymer chains held together by strong bonding with the lengths being several hundred times greater than the width. These polymers must also possess other general traits to make them useful as a fibre for textile purposes such as: 1. A degree of crystallinity of the molecular chains to give longitudinal strength along the fibre axis 2. Molecular chain flexibility to give extensibility and drape, particularly in apparel fabrics 3. High molecular weight giving both a high melting point and low solubility in most solvents Figure 1.2 shows the internal molecular structure of a man-made fibre illustrating the amorphous and crystalline regions. This polymer has all the features listed above, thereby making it suitable as a textile fibre. 1.3 Natural Fibres – Vegetable Fibres Vegetable fibres are divided into three groups based on the section of the plant from which they are produced (refer to Figure 1.3). 6 Forensic Examination of Fibres The chemical composition of vegetable fibres can vary dramatically, however the principle component in all the vegetable fibres is cellulose. Depending on the fibre, other constituents present consist of: hemi-cellulose; water soluble pectins; lignin as well as fats and waxes (refer to Table 1.3 for typical ratios of fibre constituents for some vegetable fibres). Crystalline region Amorphous region Figure 1.2 Morphology of a synthetic fibre. (Adapted from East, A.J., In J. E. McIntyre (Eds.), Synthetic Fibres: Nylon, Polyester, Acrylic, Polyolefin, Cambridge, Woodhead Publishing and CRC Press, 2005.) Fibres Natural Man-made Animal Vegetable Organic Inorganic Seed Stem (bast) Leaf Cotton Flax Kapok Jute Coir Ramie Hemo Figure 1.3 Sub-classification of vegetable fibres. Table 1.3 Approximate (%) Chemical Composition of Cellulosic Fibres Fibre Cellulose Hemicellulose Pectin Lignin Fat & Wax Cotton 92–95 5.7 1.2 0 0.6 Flax 62–71 16–18 1.8–2.0 2.0–2.5 1.5 Hemp 67–75 16–18 0.8 2.9–3.3 0.7 Ramie 68–76 13–14 1.9–2.1 0.6–0.7 0.3 Jute 59–71 12–13 0.2–4.4 11.8–12.9 0.5 Sisal 66–73 12–13 0.8 9.9 0.3 Abaca 63–68 19–20 0.5 5.1–5.5 0.2 Coir 36–43 0.2 3–4 41–45 Fibres, Yarns and Fabrics 7 OH OH O HO O HO O O OH OH n Figure 1.4 Repeating unit of glucose (units joined between the 1 and 4 carbon atoms). Cellulose is the carbohydrate part of the plant’s cell wall and is a polysaccharide macro molecule consisting of a large number of anhydroglucose units. The number of 1,4-β– glucose units in the cellulose chain can vary from several hundred to several thousand depending on the degree of hydrolysis that the cellulose undergoes. The repeating unit is illustrated in Figure 1.4. The molecular chains in natural cellulose vary in length. Variations in chain length results in differing solubilities in alkali and different viscosities but the same chemical properties. The degree of polymerisation (DP) is a measure of the chain length. Bast fibres have a DP of about 9000; wood cellulose on the other hand has a DP between 7,500 and 10,500. Hemi-cellulose is the name applied to a group of polysaccharides found in the cell walls of plants. The hemi-cellulose found in flax differs in constitution to that found in jute, which is again different to that found in hemp. Whilst hemi-cellulose is similar in structure to cellulose, the typical hemi-cellulose, xylose, does not contain the projecting CH2OH group found in cellulose. Because hemi-cellulose has a much shorter chain length (DP of about 120) it is readily soluble in dilute solutions of alkali. Lignin is an amorphous polymeric material concentrated in the spaces between the cells. Chemically, lignin differs from other natural polymers in being aromatic; destruc- tive distillation yields derivatives of phenyl propane. Lignified tissues are stronger and are more resistant to retting*. The lignin in plant cell walls can be almost completely removed by treatment with chlorine compounds such as sodium hypochlorite or sodium chlorite used in the bleaching process. The presence of large amounts of lignin in cellulosic fibres can result in substantial changes to colour on exposure to light. Jute, for example, a high lignin content fibre, will yellow when exposed to sunlight. Pectins are a complex group of substances of which the principle constituent is polygalaturonic acid in which a large proportion of the carboxyl groups have been meth- ylated. The pectins do not contribute to the overall strength of the fibre, as once removed by boiling in 1.0% solution of sodium hydroxide for 30 minutes in the absence of air, the strength of the fibre and its fluidity † remain unchanged. In mature cells, more rigid bonding between the cells is required and insoluble salts of calcium and magnesium pectinates occur. * Retting is the bacterial decomposition of lignan and hemicellulose. † Fluidity – A measure of the damage to cellulose. 8 Forensic Examination of Fibres 1.3.1 Seed Fibres – Cotton, Kapok and Coir Of all the natural fibres used in textiles, cotton is the most important with 24.4 million tonnes produced in 2008. It is also the most commonly encountered natural fibre in foren- sic examinations. Cotton is a natural vegetable fibre from the seedpod of plants in the genus Gossypium and is grown in subtropical climates. Two species are commonly cultivated; G. hirsutum, or upland cotton, accounts for 94% of world production and, G. barbadense, or Egyptian or Pima type cotton, which accounts for only 3%–4% of world production (Gordon, 2009). Cotton fibres exhibit considerable variability in their chemical and physical properties depending on the country of origin and the conditions under which they are cultivated. Variability can be evident in fibres even from the same seed-pod. Hence consistency in fibre sourcing is required to ensure minimal changes in processing characteristics between production lots. This presents a major challenge to the textile manufacturing industry. Figure 1.5 shows the major features in the cross-section of the cotton fibre. The cellulose content of cotton varies from a low of 88% to a high of about 96%. In the natural harvested state, the average cotton fibre is approximately 90% pure cellulose. This percentage rises to about 96% after industrial scouring and bleaching. Scouring removes naturally occurring waxes, salts and pectins present in the fibre. Bleaching gives the fibre a brighter, cleaner colour and serves to reduce imperfections in fibres from different sources. Depending on the method of yarn manufacture, cotton seed or husk may be present in the final yarn. Combed yarns* contain less cotton seed, as the majority of this is removed during the combing process. Carded yarns† however contain more of the seed, which is bleached during the bleaching process to give a more uniform fabric appearance. Unlike other cellulosic fibres, for example flax, hemp and jute, cotton is unique in that its strength does not decrease when wet. The strength of the cotton fibre increases when wet due to increased hydrogen bonding. This is because water molecules can easily form hydrogen bonds with the free cellulose hydroxyl groups. Water absorption at high humid- ity results in the swelling of the secondary cellular wall, which has little effect on the fibre length. This is unusual, as when swelling takes place there is normally a reduction in length proportional to the degree of swelling. During the scouring of cotton fabrics prior to dyeing, alkalis such as sodium hydrox- ide and sodium carbonate are used. This scouring removes waxes and impurities from the fabric and has an influence on the dye uptake depending on the amount of alkali used. Treatment of cotton with higher quantities of alkali, i.e. 26% sodium hydroxide Cellulose Lumen Wax Figure 1.5 Cross-section of a cotton fibre showing the major features. * Combing is a process that removes short fibres and some vegetable matter. † Carding is a process that straightens the fibres. Fibres, Yarns and Fabrics 9 (mercerising), has a more marked effect on the physical and chemical properties of the cotton fibre. The average regain of the fibre increases by almost 25%–10.5% at 65% relative humidity and 20°C. Mercerising (a permanent treatment) also results in physical changes to the cotton fibre that give added value to the final product. If the fabric is under tension during the sodium hydroxide treatment the fibre is prevented from shrinking during the swelling process. Surface lustre is developed, in part due to the changes that take place in the fibre cross-section. The fibre loses its kidney shape and becomes more circular as shown in Figure 1.6, thus increasing the surface reflective properties. Increased hydro- gen bonding between the molecular chains also occurs, thus giving an increase in fibre strength of approximately 20%. Since the fibre swells dramatically during the treatment, the fibrils in both the crystalline and non-crystalline regions become more accessible to the penetration of moisture. Thus the relative moisture absorbency increases. This increase in moisture absorbency increases the comfort factor of a typical cotton garment. At the (a) (b) Figure 1.6 Scanning electron micrographs of cotton fibre before (a and b) and after (c and d) treatment with 26% sodium hydroxide illustrating the change in cross-section and longitu- dinal aspect. Note – presence of dead cotton not affected by mercerisation process (circled in white). (Courtesy of Dr L. Arnold, RMIT University.) (Continued) 10 Forensic Examination of Fibres (c) (d) Figure 1.6 (Continued) Scanning electron micrographs of cotton fibre before (a and b) and after (c and d) treatment with 26% sodium hydroxide illustrating the change in cross-section and longitudinal aspect. Note – presence of dead cotton not affected by mercerisation process (circled in white). (Courtesy of Dr L. Arnold, RMIT University.) same time the dye-ability of the fibre increases, so that a lower quantity of dye is required for a given shade depth. Not all cotton fabrics are mercerised, however most cotton sewing threads are mercerised to give increased yarn strength. Cotton fibres have a natural twist or convolution which is present during fibre growth. The process of mercerising reduces and in some cases completely removes the convolutions. Figure 1.6a through d show the effect of mercerising on both the cross-section of the fibre and the longitudinal aspect of the fibre. Within any given cotton crop, a percentage of immature and dead fibres will always be present. The percentage of these fibres depends to a large extent on the conditions during the ripening period of the crop. Figure 1.7 illustrates the variability in the fibre cross sec- tion between mature, immature and dead fibres. Immature fibres dye lighter than mature fibres causing colour variation. Dead fibres in a yarn or fabric show as uncoloured or white flecks lowering the appearance of a fabric and thus the final finished quality. Cotton fibres sourced from different growing regions vary widely in fibre length, fine- ness and colour. These variations can result in large fibre losses during spinning and wet processing particularly when immature fibres are present. The presence of short fibres in a yarn can result in pilling, and immature fibres can cause colour variations (due to poor or no dye uptake). Variations between batches can also result in variable uptake of dye by the fibre, also giving rise to colour variations. Fibres, Yarns and Fabrics 11 Mature fibre with a very thick secondary wall. When dyed the secondary wall is dark. Notice the lumen is completely collapsed. Immature fibre secondary wall shows both thick and thin places, so the fibre will dye lighter. Dyeing properties can be improved by mercerising. Dead fibre with very little cell wall, when dyed the fibre appears white. Cannot be improved by mercerising. Figure 1.7 Mature (top), immature (middle) and dead (bottom) cotton fibres. This is particularly so when scouring using sodium hydroxide. Partial mercerisation of the fibre can occur. For this reason, the quantities of chemicals used in scouring and bleaching processes are carefully monitored. Cotton can be dyed with a wide variety of dyes; these include direct, reactive, vat, sul- phur and azoic dyes. Today the most common dye for cotton is the reactive dye. Military fabrics are usually dyed with vat dyes due to their very high performance to light and washing. Many T-shirt garments are printed or dyed using organic pigments, the colour being held on the garment by means of an acrylic resin binder. Kapok is from the seed pods of the kapok tree Celba pentandra, which grows in Malaysia and Indonesia. The fibre is light weight soft and hollow but brittle and is removed by hand from the seed pods, dried and shaken to remove any seeds. Fibre length is approximately 18–24 mm with a pronounced lumen. Compared to cotton kapok has a much lower cellulose content. The fibre is unsuitable for spinning into yarn due to its brittleness and inflexibility. It is an extremely buoyant fibre and will support more than thirty times its own weight and does not waterlog. Originally used in life vests and safety equipment, mattress and furniture fillings and pillows. Today its use has declined due to the introduction of synthetic fibres such as polyester, which is now widely used as fillings in many furniture applications. Coir is a coarse fibre that comes from the fibre mass between the husk of the coconut and the shell of the kernel. Coconuts are soaked in water to loosen the fibre and remove some of the hemicelluloses and pectins. The raw fibre consists of about 40% cellulose 40% lignin, the bal- ance being hemi-cellulose and pectins. The fibre can be recovered either by hand or machine that tears away the non-fibrous material from the longer fibres. It is dark brown in colour. Individual fibres are 15–30 cm in length. The fibres are combed and then spun into yarn, it can be bleached and dyed and has good resistance to abrasion and weathering. The principle application of coir is in ropes, twines and matting. Fishing nets can be made from coir fibre but to a large extent this application is diminishing and being replaced by fibres of synthetic origin. Coarser fibres are used in brushes, broom and door mats. 12 Forensic Examination of Fibres 1.3.2 Stem Fibres – Flax, Jute, Ramie, Hemp, Kenaf Stem or bast fibres form the fibrous bundles in the inner vascular areas of the stems of dicotyledenous plants. They are thick-walled cells that overlap one another and are cemented together by non-cellulose materials, principally pectin. The fibres are released from the woody bundles by a process of natural decomposition called retting, which could be considered to be controlled rotting. Unlike cotton, bast fibres have a lower cellulose content being only 65%–75% of the fibre. The other components are hemi- cellulose, pectin, and lignins. Of the bast fibres the major material is flax, the source of linen. Other bast fibres of interest are ramie, hemp, jute and kenaf. Blends of linen with synthetic fibres such as polyester are now common in high-class fashion shirtings and blouses. 1.3.2.1 Flax Flax comes from the stem of an annual plant Linum usitatissimum, which grows in both temperate and sub-tropical climates. The seeds of the flax plant are crushed, yielding flax oil known commercially as linseed oil. Within the inner bark there are long, thin, thick walled cells that compose the fibre strands. Only about one quarter of the stem is fibre. The fibres are held together by woody material and cellular tissue that must be removed to liberate the final fibre. Retting of the woody bundles is achieved through several different processes: Dam retting where the bundles of stems are immersed in ponds or dams for about 10 days. Dew retting where the stems are laid on the ground and left for several weeks, where they are continually wetted with dew and rain, which results in the forma- tion of moulds that enhance fermentation. Dew retted flax is darker than fibre that has been dam or tank retted. Tank retting where the stems are mechanically stripped of seed bolls and the straw tied in bundles and packed into a concrete tank filled with water. The water is heated to about 30°C and retting is completed in about 3 days. A second retting may be employed to improve the fibre quality. Chemical retting using alkalis such as sodium hydroxide and sodium carbonate with soap have also been used, but this method is more costly compared to the biological methods previously discussed. The lightest colour and best quality flax is produced by tank retting. The dried retted flax is then ready for breaking and scutching. In this process, the dried retted flax is passed between fluted rollers that break the woody core without damaging the fibres. In scotching, the broken straw is beaten on a scutching machine to separate the individual fibres from the unwanted woody matter. After scotching, the fibres are combed or ‘hackled’ by drawing the fibre through sets of pins, each successive set finer than the previous set. This process separates the coarser fibres and also arranges them parallel ready for spinning into yarn. After boiling and bleaching, flax is almost pure cellulose with a specific gravity of 3.54. Flax is soft with a lustrous appearance, yellowish white in colour, but can vary depending on the retting process used. Fibre length is 6–65 mm, but on average is about 20 mm, and Fibres, Yarns and Fabrics 13 has a fineness of approximately 20 microns. In cross-section the fibre is polyganol with thick cell walls. Immature fibres are more oval in cross-section. A characteristic lumen or canal runs through the centre of the fibre. The fibre is stronger than cotton and has minimal extensibility. It has good resistance to alkalis and will withstand the action of dilute acids. Because of its high moisture absorption properties it is used in table linen and towelling. Other applications of flax are in high quality ladies’ blouses and shirts. The application of blends of linen with synthetic fibres such as polyester greatly improves its easy-care properties. 1.3.2.2 Jute The jute plant Corchorus is an annual that grows in hot damp climatic regions and is culti- vated mainly in India and Bangladesh. Only two species are grown on a commercial scale, G, capoularis and G. olitorius; the first species produces ‘white jute’ and the second ‘Tossa jute’. White jute is a little misleading as the natural fibre is in fact a golden yellow colour. Retting is carried out in a similar manner to that employed for flax. Commercial jute var- ies in colour from yellow to brown. Chemically the dry fibre consists of 71% cellulose, 13% lignin 13% hemicelluloses, 0.2% pectin 0.5% fats and waxes and 2.3% water solubles. The fibre strands can be up to 2 meters in length. Following retting, the fibres are hung to dry in the sun, then compressed into bales ready for spinning. In cross section, the jute fibre is polygonal with five to six sides. The lumen is oval in cross-section but irregular compared to flax, which has a regular lumen. Compared to flax, jute is not as strong due to the uneven thickness in the cell walls. The moisture absorption properties of jute are unusual, being very hygroscopic, able to absorb up to 23% moisture in humid conditions with a normal regain of 13.75%. Prolonged exposure to moisture causes the fibre to lose strength. Jute is more resistant to micro-organisms than either grey cotton or flax; this is due to the pro- tective effect of the lignin. To a large extent, many applications for jute have been replaced by synthetic fibres such as polypropylene and polyester, however jute is still used as the secondary backing in carpets due to its non slip properties. Other applications for jute are ropes, cordage, linings in older style furniture, sackings and bales. Kenaf, Guinea hemp or Mesta from the plant Hibiscus cannabinus grown in Africa, India and Bangladesh, has similar properties to jute and can be used as a substitute but is produced on a much smaller scale on the international market. 1.3.2.3 Ramie Ramie or China grass comes from the plant Boehmeria nivea that belongs to the family of stinging nettles. It is a perennial grown mainly in China. The root sends up many stalks to a height of approximately 1.2–2.0 meters. These are harvested every two to three months when the lower stalks turn yellow and new stalks begin to appear. The fibres are removed from the stalks by decortication which consists of mechanically peeling or beating the bast and bark followed by soaking in water and scraping to free the fibres from the bark. The final fibres vary in length from 2.5–30 cm. The cellulose content of ramie rises from 75% cellulose to 85% cellulose after decortications, and after degumming the cellulose content on dry basis is 96%–98%. Degumming is accomplished by treatment in sodium hydroxide solution followed by bleaching. Ramie fibres are white and lustrous and are unaffected by the action of sunlight and can be blended with other fibres. The fibre has a high resis- tance to bacteria, fungi and mildew. Treatment in strong 26% sodium hydroxide solution (mercerising strength) brings about changes to the fibre similar to that achieved in the 14 Forensic Examination of Fibres mercerising process used on cotton. Fabrics made from ramie are very absorbent and dry quickly and can be used for the manufacture of towels and table linen. 1.3.2.4 Hemp True hemp derived from the plant Cannabis sativa has been in use since ancient times. The term hemp has been used to describe a range of fibres from different species used for the manufacture of ropes and cordages, some being derived from stalks and others from leaves such as Manila hemp and New Zealand hemp. Cannabis sativa is an annual plant grown from seed in temperate climates. The stalks should not exceed 1.8 meters in height if good quality fibre is to be produced. Harvesting takes place when the lower leaves turn yellow and the stalks are pulled from the ground. Retting and scutching are similar to that used for flax. Under microscopic examination hemp resembles flax in appearance; this similar- ity means that some hemp varieties are difficult to distinguish from flax. Hemp is overall a courser fibre than flax, being darker in colour and difficult to bleach. The cross-section of hemp is polygonal and the lumen is broader than that of flax. Dry hemp fibres have high cellulose content, approximately 75%; lignins are lower at 3.6%, compared to jute. Other components are hemi-cellulose about 17%, fats and waxes 0.8%, water solubles 2.0%, pectins 1.0% and lignins 3.6%. The major applications of hemp are in the manufacture of ropes, twines and cordages. More recently however there have been garments manufactured from blends of hemp with cotton. High quality hemp can be used as a substitute for flax. 1.3.3 Leaf fibres – Sisal, Hemp (Manila and New Zealand) The leaves of certain tropical and sub-tropical monocotyledonous plants are held in shape by fibrous cells that run in strands (vascular tissue) through the length of the leaf. These cells help to give the fibre strength and maintain its shape. As a general rule the leaf fibres are courser than fibres that come from dicotyledonous plants, which are the source of the bast fibres. The leaf fibres are often referred to as ‘hard’ fibres being that they are thicker and stiffer than either the bast or seed fibres. The major leaf fibres are sisal, henequin, New Zealand hemp and abaca. Synthetic and regenerated fibres from natural polymers have, to a large extent, taken a substantial share of the market for both the bast and leaf fibres. More recently however, with the rising cost of petroleum, there has been an increased awareness of the advantages of these natural products, particularly in relation to their sustainable production. 1.3.3.1 Hemp-Abaca (or Manila Hemp) and New Zealand Hemp Musa textilis a member of the banana family indigenous to the Philippines and is the source of manila hemp for the manufacture of high quality ropes and cordages. The fibre is in the form of strands of many fibres held together by natural gums. The length of these strands varies from 1–3 meters and 0.05–0.3 mm in diameter. Final fibre length is 3–12 mm and 16–32 μm in diameter. The fibre has a good natural lustre and is off-white in colour. Chemically abaca fibres contain about 77% cellulose on a dry weight basis and are coated with about 9% lignin. The individual fibres are separated from the soft fleshy material by drawing the strips of the leaf between a knife edge and a wooden block. The repeated scraping in this manner removes the soft cellular matter that surrounds the fibre. Once the fibre is cleaned it is hung up to dry. When dry it is ready for use. The fibre has a Fibres, Yarns and Fabrics 15 variable cross-section that is irregularly circular or oval in shape. One of the advantages of abaca is that it is not affected by salt water; hence it is ideally suited for use in marine cordage. New Zealand hemp is the perennial plant Phormium tenax native to New Zealand. Captain Cook noted that the Maoris produced fine fabrics from the leaves of this plant. Fibres are extracted from the leaves by mechanical scraping. Whilst the fibre is fairly strong and has good resistance to sea water it is weaker and softer than Manila hemp. The individual fibres are smooth with pointed ends with an average length of about 6–7 mm, a near circular cross-section and a narrow circular lumen. Compared to other leaf fibres, the lignin and hemicelluloses is higher and the cellulose content lower. 1.3.3.2 Sisal and Henequen Sisal is the leaf fibre that comes from the plant Agave sisalana. The name is derived from the Yucatan port ‘Sisal’ situated on the Gulf of Mexico. It was from this port that the fibre was first exported. The sisal plant is grown in tropical regions and grows huge leaves almost from ground level. The leaves are harvested when the plants are 2–4 years old. A good plant may yield up to 400 leaves in its lifetime of seven to eight years. The fibres are extracted from the leaves using a decortication process in a machine that scrapes the pulpy matter from the fibres. The fibres are washed, then dried either in the sun where bleaching takes place or in an oven. Fibre strands vary in length from 60–120 cm in length and have an average diameter of 24 μm. The fibre is polygonal in cross-section with a broad lumen which varies in thickness and is often packed with small granules. The fibre ends are blunt and in some cases forked. Sisal is used for the manufacture of ropes, cordages, twines, upholstery, carpet and custom rugs. Yarns have a tendency to shed the fibre and fabrics quickly fade out. Henequen fibre is produced from the plant Agava bourcroydes and is often known as ‘Yucatan sisal’ or ‘Cuban sisal’. The plant has prickly leaves that are grey green in colour. Processing of the leaves is similar to that for conventional sisal. The fibre strands are long and slightly finer than those of sisal. Applications include string and agricultural twine. 1.4 Natural Fibres – Animal Fibres Natural fibres that have an animal source (refer to Figure 1.8 for sub-classification), such as wool or silk, are protein based. Proteins are chain like molecules formed by the union of α-amino acids joined together by the peptide link as shown below. R R NH2 – CH NH2 – C – COOH COOH H The difference between proteins is related to differences in the side group –R pendent to the main chain. Over 20 amino acids are known to exist because of the difference in size, shape and chemical reactivity. The limited number of side groups is sufficient to result in an extremely large number of polypeptides and proteins due to arrangements that are pos- sible. Table 1.4 lists the differing ratios of amino acids in wool and silk fibres. 16 Forensic Examination of Fibres Fibres Natural Man-made Animal Vegetable Organic Inorganic Hair Silk Wool – sheep Bombyx mori – silkworms Goat family – mohair, cashmere Arachnids – spider silk Camel family – camel hair, alpaca, vicuna Hymenotpera – bees, wasps, ants Other – rabbit fur, possum fur Figure 1.8 Sub-classification of animal fibres. 1.4.1 Wool Of the protein fibres, wool is the predominant fibre, with world production being approxi- mately 1.2 million tonnes in 2008. Raw wool after shearing contains impurities, such as grease, swint (sweat), dirt and vegetable matter. The quantities of these impurities will vary depending on the agricultural region where the animal has been grazing. Merino sheep that are raised under shedded conditions show minimal amounts of vegetable matter and dirt present in the fleece. After scouring and removal of vegetable matter under conven- tional grazing conditions the yield will be about 65% of clean wool. It is normal for scoured wool to retain about 0.5% residual grease as this assists in later mechanical processes such as carding and combing to minimise fibre breakage. In a typical wool fibre there are four regions: 1. The epicutical (or outer sheath): A thin hydrophobic membrane and the only non- protein part of the wool fibre. This membrane is water repellent for water droplets but will absorb water vapour through its many microscopic pores (thus absorbing water vapour from the body and releasing into the air); 2. The scale-cell layer (comprising the enzyme resistant exocuticle and enzyme digestible endocuticle): This layer contains the flat scale-like cells which overlap each other (refer to Figure 1.9 for a cross section of wool illustrating the overlapping scales). The number of scales present on a wool fibre is known to vary greatly depending on the quality of the wool with fine wools having significantly more scales than coarse or medium wools. 3. The cortex: This layer comprises some 90% of the wool fibre consisting of millions of spindle shaped cells; and 4. The medulla: Many wool fibres (particularly the coarser ones) have a hollow cen- tral space running longitudinally to the fibre length. The medulla may be either empty or contain a loose network of open cell walls. Coarse and medium wools are generally characterised as having a greater proportion of the fibres medullated. Conversely, in fine wools the medulla is either absent or so fine as to not be visible. The dimension of wool fibres varies considerably depending on the quality of the wool. Fine wool fibres are generally about 3.8–12.7 cm long, medium wools are generally 6.3– 15.2 cm long and long wools are 12.7–38 cm long. The diameter can also vary significantly Fibres, Yarns and Fabrics 17 Table 1.4 Amino Acids Present in Silk and Wool Protein Fibres g- Amino Acid per 100 g Protein Amino Acid Silk Fibroin Wool Keratin Inert acids Glycine 43.8 6.5 Alanine 26.4 4.1 Valine 3.2 5.5 Phenylalanine 1.5 1.6 Isoleucine 1.4 0.0 Leucine 0.8 9.7 Acidic Glutamic Acid 2.0 16.0 Aspartic Acid 3.0 7.3 Basic Histidine 0.5 0.7 Lysine 0.9 2.5 Arginine 1.1 8.6 Hydroxyl Serine 12.6 9.5 Tyronsine 10.6 6.1 Threonine 1.5 6.6 Miscellaneous Proline 1.5 7.2 Cystine 0.0 11.8 Tryptophan 0.0 0.7 Cysteine 0.0 0.1 Methionine 0.0 0.4 with the average diameter for a top-quality merino wool being 17 μm; a medium wool fibre about 24–34 μm and a long wool fibre about 40 μm. Wool fibres have a natural wave or crimp which is a unique characteristic amongst natural fibres. The crimp is not in a single plane but has a three dimensional waviness. This natural waviness allows fibres to hold together when made into a yarn. Once again the quality of the wool will be reflected in the waviness of the fibre. The finest wools can have as many as 12 waves to the centimetre whereas poorer quality wools will have 2 (or even less). Intercellular cement holds the cuticle cells together and separates them from the underlying cortical cells. During the processing of washable wool, i.e. shrink resistant wool, the hydrophobic epicuticle is damaged and the scale structure is significantly changed due to the action of chlorine and a cationic resin. This process is the ‘KROY TM’ process. 1.4.1.1 Hair fibres or Speciality Wools Hair fibres or ‘Exotic fibres’ are those that come from other animals such as: 1. Goat family—mohair, cashmere 2. Camel family—camel hair, alpaca, vicuna 3. Rabbit fur and other fur animals such as the possum 18 Forensic Examination of Fibres Figure 1.9 Cross section of 28 micron wool illustrating the overlapping scales. Mohair is from the Angora goat which originated in Turkey, is a lustrous fibre with a staple length of 20–30 cm for a full year’s growth. The fibre’s surface has some similarities to wool; it is covered with epidermal scale anchored much more closely to the body of the fibre compared to wool, there being only about half the number of scales as there are on the wool fibre. The fibre has a circular cross section with an average diameter of about 25 μm for kid mohair and 35 μm for the adult fibre. Chemically, the main constituent is keratin, and its chemical behaviour is very similar to wool. Cashmere was the name originally given to the hair from the Asiatic goat Capra hircus laniger, the Tibetan Cashmere goat, which is raised as a domestic animal in parts of China, Persia and northern India. In Australia, New Zealand and Scotland hair from the selec- tively bred feral goats is also called cashmere. The cashmere fibre varies in length from 5–10 cm with diameter of 14–16 μm. In cross-section the fibre is circular or slightly oval, and in the coloured fibre the natural pigment can be clearly seen in the cortical layer. Because of its softness, cashmere is mainly used in high-quality ladies’ dress wear and knitwear. The fibre is more easily damaged chemically particularly by alkalis due to its fineness and better wetting properties. Camel hair is from the camel Camelus bactrianus. The hair is shed by the animal and collected. The soft inner hair is the finest and is used in high grade men’s over-coatings. Camel hair gives warmth without weight so the fibres are highly prized for quality apparel. The coarser outer hair or guard hair length is approximately 26–30 cm and is used in the manufacture of beltings and interlinings. Alpaca is from the fleece of the Lama pacos from South America. The fleece is coloured brown, fawn, black and sometimes white, with a fibre diameter of 24–26 μm and fibre length of 20–28 cm. Alpaca has a distinctive scale structure with a natural crimp and medullation. Dress fabrics, tropical suiting’s and blends with wool are common. Alpaca is difficult to dye and is usually used in its natural colours. The fibre is noted for its softness, fineness and lustre. Fibres, Yarns and Fabrics 19 Vicuna is the smallest and rarest of the llama family. The undercoat hair fibre from the vicuna is regarded as being the finest wool like fibre with a diameter of 13–14 μm. About 500 g of fibre is obtained from each animal. It is the rarest and most expensive of all fibres and has similar uses to cashmere. Angora fibre is obtained from the pelts of the angora rabbit. After shearing the hair from the pelts is separated by blowing. The fine hair, 6–8 cm in length 13 μm in diameter, is used in the manufacture of felt hats. Angora is difficult to dye and is very slippery and is usually blended with wool and or nylon to facilitate spinning. Other animal fibres may be encountered in textiles including fibres from domestic animals such as cats, dogs, cows, horses, rodents, etc., as well as human body hair. 1.4.2 Silk—Silkworm The silkworm is the caterpillar of a small white moth of the species Bombyx mori from the class of insects Lepitoptera. This caterpillar thrives only on Mulberry leaves and dur- ing the growth stage the worms do nothing but eat except for four periods of sleep, which last about 24 hours. During this resting period the worms shed their skin or moult. After the fourth moult it settles down to a feed lasting about 10 days during which period it eats about twenty times its own weight of leaves. Approximately thirty-five days after hatching the worm begins to spin its cocoon. The liquid silk is from two glands inside the worm. The silk flows in two channels to a common exit point which is the spinneret, in the worm’s head. As it exits the liquid hardens into very fine filaments that are coated and stuck together with a gummy substance called sericin which comes from two other glands nearby. Silk as it emerges from the worm is therefore a twin filament held together as a single strand by the sericin cement. Sericin is an amorphous globular protein and dissolves in hot soap solution. Raw silk contains approximately 75% fibroin and 25% sericin. Sericin remains on the filament surface to protect the fibre from damage during processing. De-gumming during wet processing of both silk yarns and fabrics removes the sericin, leaving a fibre of almost pure fibroin. Silk will dissolve in powerful hydrogen bond-breaking solvents such as cuprammonium hydroxide (as it does not contain the disulphide links present in other animal fibres). Each raw filament of silk is roughly elliptical in cross-section. After de-gumming the fibroin fibre is transparent and uniform in width being 9–12 μm with a smooth surface. Wild silk (Tussah Silk) fibres are darker in colour and coarser, approximately 28 μm, and less uniform in width, with pronounced longitudinal striations. Cross-sections of different silk fibres show significant differences, cultivated Bombyx being roughly triangular with the corners being rounded. Tussah silk on the other hand is wedge shaped, whilst Anaphe silk is roughly triangular and the apex of the triangle is elongated and bent. Because of silk’s outstanding strength, toughness, high regain, soft handle, excellent drape and appearance, it has a wide variety of uses in apparel, in particular high-qual- ity dress goods, lingerie and handkerchiefs. As silk loses about 25% of its weight during de-gumming, manufacturers add weight to the silk with tin salts, so called tin weighting, stannous chloride often being used. 20 Forensic Examination of Fibres 1.4.2.1 Spider Silk The protein fibre spun by spiders has superior mechanical properties compared to those of the silkworm. When compared to synthetic fibres such as polyamide and polyester, spi- der silk is said to be superior in strength, elasticity and resistance to compression. There are many specimens of spider silk, some exhibit elongation as high as 200% whilst oth- ers exhibit strength similar to high-performance fibres such as high tenacity polyamide. Spider silk has better water repellent properties compared to both types of natural silk. The domestication of spiders has not yet been possible, therefore its use in textiles has not been fully exploited. Being predators, the raising of spiders in dense populations is not possible. Compared to the silkworm the amount of silk produced by the spider is small. It has been possible to produce artificial spider silk. Currently DuPont has successfully spun a protein analogue of spider silk using solvent spinning technology and regenerating the fibre in a coagulation bath. Spider silk is sticky and may stick to textiles and could be mistaken for natural silk. 1.5 Mineral Fibres (Asbestos) Of the naturally occurring fibres asbestos is the most peculiar. Unlike other rocks that crystallise during their formation, asbestos is derived from a rock that crystallizes in the form of fibres that are closely packed together giving the surface a grainy appearance. The use of asbestos has been known since ancient times when it was used as wicks in lamps. There are three natural fibrous minerals: Anthophyllite: Magnesium-iron silicate but of least importance for commercial use. Amphibole: There are a number of varieties of this mineral, of which Crocidolite is the most important as it is from this mineral blue asbestos is extracted. Chemically the long flexible fibres are iron sodium silicate and are a blue colour. The average fibre length is 7.5–10 cm, but it is not as resistant to high temperatures as crysotile. Serpentine: Which occurs in two fibre forms is a hydrated silicate of magnesium. The most important of these is crysotile. It is green to brown in colour and the fibres extracted form the major world supply of asbestos. The crysotile fibres are strong, but the ultimate fibrils are very fine, about 25 nm in diameter. Asbestos has been spun into yarns and then woven into fire-resistant fabrics. Asbestos was used in manufacture of construction materials (asbestos cement sheet) but this has now been discontinued in Australia due to health considerations. Aramid polymer fibres such as NomexTM, and glass fibres have replaced asbestos in fire resistant fabrics and yarns. 1.6 Man-made Fibres Man-made fibre can be classified into two groups, those derived from natural polymers such as cellulose (the regenerated fibres) or true synthetic fibres synthesized from simple organic chemicals found in coal and oil. Methods of production vary with the different Fibres, Yarns and Fabrics 21 polymers. Essentially there are three methods of producing fibres from polymeric materi- als. These are; 1. Melt spinning: Applied only to thermoplastic polymers. The concentrated molten polymer is forced through tiny holes in a spinneret. As the polymer cools, the fila- ments are formed. 2. Dry spinning: The polymer is dissolved in a volatile organic solvent and the vis- cous solution pumped through the spinneret into a column of air where the sol- vent evaporates, leaving a continuous filament of fibre. The solvent is recovered for reuse in the process. 3. Wet spinning: The viscous polymer solution, dissolved in either an aqueous or organic solvent, is pumped through the spinneret, which is immersed in a bath containing suitable coagulating chemicals. The polymer precipitates in the bath; the extruded filaments are formed and drawn off ready for further processing. Following extrusion the filaments are stretched or drawn mechanically to orient the molecular chains along the longitudinal axis of the fibre. This stretching maximises the molecular forces between the molecular chains, increasing polymer crystallinity and fibre strength. The degree of crystallinity is a measure of the percentage of polymer present in its crystalline form, the balance being in a disordered or random state. The random state of a polymer is referred to as being an amorphous state. Within the fibre the crystalline and amorphous regions do not have any particular order but are randomly spaced along the fibre axis. The extent to which one or the other predominates will determine the ultimate properties of the fibre. The filaments can be cut into lengths (staple fibres) or remain continuous (continuous filament fibres); they can also be crimped so that they are compatible with the natural fibre yarn spinning system that may be used. Often synthetic fibres are blended with a natural fibre to enhance the properties of the final fabric. A small amount of twist is inserted into a filament yarn to aid in its further processing. Some synthetic fibre yarns are often further processed to increase the bulk and elasticity of the yarn. One such treatment is that of false twisting where high twist is inserted in the filaments as the yarn passes through a heating zone. The heat applied sets the twist, which is then untwisted, giving the yarn an increase in bulkiness in its relaxed state. 1.6.1 Fibres Regenerated from Natural Polymers Man-made fibres regenerated from natural polymers are sub-classified (refer to Figure 1.10) based on the source of the natural polymer (i.e. cellulose based or protein based). 1.6.1.1 Viscose Rayon Of all the regenerated cellulosic fibres viscose is by far the most important. There are many manufacturers throughout the world. In 2006 world production of viscose grew by about 10% to 2.7 million tons, China being the largest consumer at 1.5 million tons*. Viscose rayon is manufactured from wood pulp, usually made from spruce wood. During the * Source: www.worldresearchandmarkets.com. 22 Forensic Examination of Fibres Fibres Natural Man