Exam 2 Study Guide - Filled PDF
Document Details
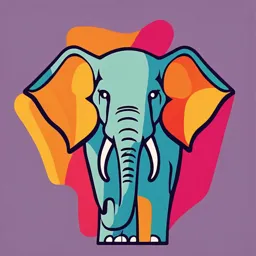
Uploaded by CaptivatingBeryllium
Iowa State University
Tags
Related
Summary
This document provides a study guide for an exam, focusing on mechanical properties. It explains concepts like stress, strain, elastic and plastic behavior, and the stress-strain curve. Additionally, it discusses toughness, ductility, and the behavior of materials like ceramics.
Full Transcript
Topics Mechanical properties o Concepts § Stress (! = # ⁄$! ) Force per area. Force # is perpendicular to an area $!. Units: N⁄m" = Pa (Pascal), lb⁄in" = psi § Strain (0 = ∆2 ⁄2! = (2 − 2! )⁄2! )...
Topics Mechanical properties o Concepts § Stress (! = # ⁄$! ) Force per area. Force # is perpendicular to an area $!. Units: N⁄m" = Pa (Pascal), lb⁄in" = psi § Strain (0 = ∆2 ⁄2! = (2 − 2! )⁄2! ) Change of length per original length after applying a force #. Initial length of the sample is 2! , final length after applying the force is 2. When applying tension, the part elongates, thus 0 is positive, when applying compression, the part shortens, thus 0 is negative. o The measurement of the lateral contractions/dilations in the cross section can be obtained with Poisson's ratio! = −$! /$" = −$# /$" (in tension) and (in compression) § Shear stress The force is parallel to the area, instead of perpendicular. Stress has the same formula. Strain is calculated with 6 = tan 8, with 8 being the angle of deformation. § Elastic behavior Low levels of stress and strains can have elastic (non-permanent) deformation. Meaning when removing the load/force the part returns to its original shape and size. This deformation is linear and proportional. Follows Hooke’s law ! = 90, where 9 is the elastic modulus or Young’s modulus, also known as stiffness o 9 is also proportional to the slope of the interatomic force-separation curve at the equilibrium spacing o In other words, is a measure of the strength of interatomic bonding forces If applying shear forces, the stress-strain expression is : = ;6, with ; being the shear modulus. § Plastic behavior Deformations to a part are permanent or cannot recover its original shape/size § Stress-strain curve Tensile test: load a sample into a universal testing machine and move the crosshead at constant speed elongating the sample until it breaks Tensile test data is Force-displacement. o Divide each force data point by the initial cross section area to obtain stress o Divide each displacement data point by the initial length of the gauge section The point where a material stops behaving elastically is known as yield point (the material “yields” to the stresses and deforms) o Obtaining yield stress convention: § Draw a straight line, parallel to the initial elastic behavior, starting at a strain of 0.002 or 0.2% § Where the parallel line crosses the stress-strain curve is the value we use for yield stress (&# ) The maximum point in the engineering stress-strain curve is the ultimate tensile strength o In tests, this point is also the onset of the formation of a neck in the tensile specimen o In compression there is no necking The curve ends at the fracture point. True stress-true strain curve o Engineering stress-strain does not consider the actual changes of the gauge section o True stress uses the instantaneous area instead of the initial area, to ease the calculations &$ = &(1 + $) o True strain is calculated by $$ = ln(1 + $) § Toughness Resistance of a material to fracture when a crack is present Ability of a material to absorb energy and plastically deform before fracture The area below the curve of an engineering stress-strain curve § Ductility Measure of degree of the amount of plastic deformation before fracture o Calculated with % of elongation or % of reduction in area cross section % &% '" &'! o %./ = 0 !% " 1 or %23 = 0 '" 1 " o Ceramics § More brittle than metals Metals: slip occurs by dislocation motion on close-packed planes and direction Ceramics: dislocation motion is difficult over repeat distances, few slip systems, there is resistance to motion of ions of similar charge past one another § Bending test-flexural strength Three- or four-point bending test Necessary as ceramics often break when being placed into other grips/test configurations. *+ , *+ , Stress at fracture is the flexural strength &() = -./! #or &() = 01!$ , where 4( is the load at fracture, / is the distance between supports, if using a rectangular cross section 6 is the base and 7 the height, or if using a circular cross section 2 is the radius Elastic modulus considers the compression force 4 and the midpoint deflection 8 as the plot of these two variables has a linear behavior. + ,$ + ,$ o. = 2 3./$ or. = 2 4-01% (depending on shape of cross section) § Porosity Porosity is common in certain ceramic fabrication techniques, even after treatments to reduce it. Porosity decreases the cross section areas of ceramic parts, thus reduces the modulus and stresses o. =.5 (1 − 1.9; + 0.9;- ) o &() = &5 exp(−@;) o Polymers § Sensitive to strain rate, temperature, environment (chemistry, UV,...) § Modulus of elasticity and ductility – same procedure as for metals § Brittle polymers fracture when deforming elastically (bakelite) § Plastic polymers: elastic initial deformation, then yielding and plastic deformation (PMMA, HDPE,...) Yield strength: max point on the curve just past the linear-elastic region Tensile strength: stress at fracture § Elastomeric polymers: totally elastic, large recoverable strains at low stresses (rubber bands) § Viscoelastic deformation (amorphous polymer – silly putty) Behavior: like glass at low A , rubbery solid at intermediate temps (A > A6 ), viscous fluid at higher A In the intermediate temp (glass transition temp) the polymer behaves both elastically and viscously thus viscoelastically (viscoelasticity) o Other tests § Hardness Resistance to localized plastic deformation (or for cracking in compression in ceramics) Types of tests: Brinell, Vickers, Knoop, Rockwell § Design for safety How to consider uncertainties? Factor of safety (C ) : o &/7)869 = ;& Plastic deformation o Dislocations § Dislocations are 1D defects and can be edge, screw, or mixed § When dislocations move within a material, we term that movement slip § Slip happens on closed/closest packed planes, along closed/closest packed directions § If dislocations can move, the material will be ductile, if not, then it will be brittle § The Schmid factor determines what shear stress acts on the dislocations. If this resolved shear stress exceeds a critical resolved shear stress, dislocations move. § Dislocations are generated (often) at a Frank-Reed Source – which is like a dislocation factory inside the material o Strengthening § Strengthening mechanisms all rely on impeding dislocation movement. This strengthens the material, but also makes it more brittle, a classic trade-off in properties for materials scientists § Focused on four strengthening methods Grain size reduction : reduce grain size -> increase strength Solid solution strengthening : increase solute -> increase strength (up to a point) Precipitation strengthening : smaller, more closely spaced dislocations -> increase strength Strain hardening/Cold working : more dislocations -> increase strength o Undoing deformation §Recovery – Rearrangement of dislocations into lower energy configurations (dislocations spreading out and redistributing) § Recrystallization – Creation of strain-free grains § Grain Growth – Strain-free grains now able to grow, eliminating more defects from the material such as grain boundaries o Deformation in non metals § Strengthening Polymers Increase % Crystallinity (increases amount of secondary bonding) Increase degree of cross-linking (inhibits chain motion) Increase molecular stiffening (add bulky side groups or R groups) Failure o Fundamentals § Ductile Large plastic deformation that causes the material to yield before it breaks Yielding can be seen before failure, giving warning time Tensile samples neck before breaking, making a cup-and-cone shape § Brittle Small amounts of plastic deformation, causing the material to break apart into many pieces Since no or minimal yielding happens before failing, there is no visual warning Tensile samples break cleanly leaving a straight break o Toughness § Toughness is a material property that is a measure of a material’s resistance to brittle fracture when a crack is present § The higher the fracture toughness, Kc, of a material, the harder it is for that crack to propagate § K = Y σ sqrt(aπ) Kc is the Fracture Toughness (this is a specific value of K at which the material fails) Kc is a material property (it has been measured) Y is just a scalar multiplier (nominally 1) a is a measurement of crack length o The length of a surface crack is a o The length of an internal crack is 2a K (a stress concentration factor depending upon Y, a, and s) is a mathematically calculated value for the part/crack. If this K is greater than the material property (Kc) the specimen will § Kt = 2(a/p)^0.5 Kt is the stress concentration factor a is the crack length p is the radius of curvature for the tip o This is small for a sharp corner o This is large for a rounded corner o Therefore, the stress concentration for a sharp corner is higher than for a rounded corner o Fatigue § Failure from cyclical loads of stress § Can make parts fail even if the total stress is less than would make a part fail normally § Is the most common mode of mechanical engineering failure (~90%) § Some materials like steel have a fatigue limit, that if a stress is under, no number of cycles will ever cause a fatigue failure § Most materials do not have a fatigue limit, so given enough cycles, most materials can fail through fatigue regardless of stress § Fatigue has three stages Crack initiation Crack undergoes a steady rate of increasing with cycles Crack undergoes rapid propagation leading to failure o Creep § Creep is a time-dependent permanent deformation of materials when under a constant stress § For metals, creep does not happen until heated to or above 0.4 time the melting temperature (in Kelvin! This does not work with C or F!) § This is easily seen with silly putty, under a constant load, the material will slowly and permanently deform through creep § To prevent creep Increase grain size (creep can happen along grain boundaries) Increase the melting temperature or increase the modulus (most material with higher stiffness also have higher melting temp) Precipitation strengthening the material to impede creep movement Environmental damage o Oxidation § Loss of electrons § Oxidation happens at the anode § The anode is corroding away § Anodic materials have a negative electrode potential, or less than that of a cathode o Reduction § Gain of electrons § Reduction happens at the cathode § Cathodic materials have a positive electrode potential, or greater than that of an anode o Types of Corrosion § Galvanic corrosion – Two different metals in contact with each other and water/electrolytes present. § Crevice corrosion – Occurs in crevices or under deposits of dirt/debris where the solution it is in is stagnant at locally depleted of oxygen § Pitting corrosion – Corrosion that causes small pits and holes, going nearly perfectly vertical § Intergranular corrosion – Corrosion that occurs along grain boundaries, especially found in stainless steels § Stress corrosion cracking – Occurs when a sample is under a tensile stress and in a corrosive environment. Causes small cracks to form before failure § Erosion-corrosion – Occurs from a combination of a chemical attack and mechanical abrasion or wear from experiencing a constant fluid motion. Almost all metals are susceptible to this. o P-B ratio § Less than 1, the oxide film is nonprotective § ~1, ideal for creating a protective oxide film § Between 1-2 is normally protective, and above is normally nonprotective again Other properties o Electrical § Band Gaps Conductors – no band gap is seen, small amount of energy can excite electrons to the conduction band Semiconductors – small band gap is seen, when an electron is excited, it leaves an electron hole behind Insulators – a wide/large band gap is seen, taking much more energy to excite an electron to the conduction band o Optical § Intensity of light Summation of transmitted light, absorbed light, and reflected light Materials appear to be the color of light they reflect (whichever colors that are not absorbed or transmitted). o Magnetic § Types of Magnetism Diamagnetic – weak form of magnetism that is not permanent, only exists when in an external field Paramagnetic – weak form of magnetism coming from a permanent dipole in each atom Ferromagnetic – strong form of magnetism that is permanent. Metallic materials such as iron, cobalt, nickel Antiferromagnetism – materials that have no magnetic effect, because they have alternating magnetic poles Freeimagnetism – permanent magnetism seen in ceramics with aligned spins