Arc Welding Study Guide PDF
Document Details
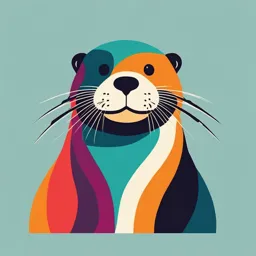
Uploaded by PoeticDidgeridoo2458
National University
Dr Mutlag Shafi Alaythee
Tags
Summary
This document provides a detailed overview of arc welding. It discusses different welding processes, safety protocols, and welding procedures. The document also explores various welding joints and associated equipment. It's a helpful study guide for mechanical and electrical engineering undergraduates.
Full Transcript
EXPERIMENT 4 Dr Mutlag Shafi Alaythee Aim of Exp: To study the process of arc welding and to prepare and weld the given mild steel plates with the following joints Department of Mechanical And Industrial Engineering The fusing of two or more pieces of metal together by using the h...
EXPERIMENT 4 Dr Mutlag Shafi Alaythee Aim of Exp: To study the process of arc welding and to prepare and weld the given mild steel plates with the following joints Department of Mechanical And Industrial Engineering The fusing of two or more pieces of metal together by using the heat produced from an electric arc welding machine. The arc is struck between the electrode and the metal. It then heats the metal to a melting point. The electrode is then removed, breaking the arc between the electrode and the metal. This allows the molten metal to “freeze” or solidify. Welding Processes Fusion welding processes Consumable Electrode SAW – Submerged Arc Welding Oxygen/ Fuel Welding Fusion Welding Processes Non-Consumable Electrode GTAW – Gas Tungsten Arc Welding PAW – Plasma Arc Welding High Energy Beam Electron Beam Welding Laser Beam Welding Department of Mechanical And Industrial Engineering Shielded Metal Arc Welding (AWS)The American Welding Society defines SMAW as Shielded Metal Arc Welding SMAW: – Is commonly known as ‘Stick’ welding or manual arc welding – Is the most widely used arc welding process in the world – Can be used to weld most common metals and alloys An electric current, in the form of either alternating current (AC) or direct current (DC) from a welding power supply, is used to form an electric arc between the electrode and the metals to be joined. Shielded Metal Arc Welding Current flows through the electrode cable, to the electrode holder, through the electrode, and across the arc On the work side of the arc, the current flows through the base material to the work clamp and back to the welding machine Is a consumable - it gets melted during the welding process, and is composed of two parts – Core Rod (Metal Filler) Carries welding current Becomes part of the weld – Flux Coating Produces a shielding gas protect the weld area from atmospheric contamination and can provide additional filler Forms a slag Typically, the equipment used for SMAW consists of a step-down transformer and for direct current models a rectifier, for converting alternating current into direct current The step-down transformer is used to reduce the voltage and increase the current As a result, instead of 230 V at 50 A, for example, the power supplied by the transformer is around 17–45 V at currents up to 600 A The power supply unit used in SMAW has constant current output, ensuring that the current (and thus the heat) remains relatively constant, even if the arc distance and voltage change Department of Mechanical And Industrial Engineering Electric Arc Welding -- Polarity Welding Processes SMAW - DC Polarity Straight Polarity Reverse Polarity (–) (+) (+) (–) Shallow penetration Deeper weld penetration (thin metal) AC - Gives pulsing arc - used for welding thick sections AWS Classification of SMAW Electrodes WELDING EQUIPMENT 1 2 4 Department of Mechanical And Industrial Engineering WELDING JOINTS Department of Mechanical And Industrial Engineering 1. Butt Joint A joint between two members aligned approximately in the same plane Department of Mechanical And Industrial Engineering 2. Lap Joint A joint between two overlapping members Department of Mechanical And Industrial Engineering 3. Tee or T Joint A joint between two members located approximately at right angles to each other Department of Mechanical And Industrial Engineering 4. Corner Joint A joint between two members located at right angles to each other Department of Mechanical And Industrial Engineering 5. Edge Joint A joint between the edges of two or more parallel or nearly parallel members Department of Mechanical And Industrial Engineering EX 3: BUTT AND TEE JOINT Tee joint Butt joint Department of Mechanical And Industrial Engineering Welding Welding Procedure Procedure Clean the surface of the metal pieces to be welded. Mark the lines on the work pieces, as per the drawing, using a steel rule and a scriber. Keep the work pieces together as per the marking on the metal table. Hold the ground clamp on the metal table on which the metal pieces, to be welded, is placed. Set the current as required. Department of Mechanical And Industrial Engineering Arc Welding Safety Rules 1. Never allow any part of the body to become a part of the electrical circuit. 2. Do not harm the welding cables, electrode holder, ground clamp, or welding machine in any way. 3. Stand on a dry surface when welding. 4. Do not watch the electric arc without proper eye protection. Department of Mechanical And Industrial Engineering Arc Welding Safety Rules 5. In order to prevent electrical shock, radiation exposure, and burns when welding, wear leather gloves, leather apron, cotton or wool long pants, and long sleeved shirts or blouses. 6. Always guard your face and eyes when chipping slag. 7. Weld in well ventilated areas to avoid toxic fumes. 8. Before welding, make sure that the welding area is free of flammable materials such as gasoline, paint, rags, and grease. Department of Mechanical And Industrial Engineering Welding Welding Procedure Procedure Insert the correct electrode on to the electrode holder. Bring the electrode straight down to the work piece; then lift slightly to start the arc. Hold the electrode perpendicular to the work piece and move the electrode down the work piece at a uniform speed to perform the weld. Using a chipping hammer and a wire brush, remove the slag. Department of Mechanical And Industrial Engineering ENGINEERING WORKSHOP(EGI00104) LOGO Department of Mechanical And Industrial Engineering