ECBC Code Compliance - Jayesh Vira PDF
Document Details
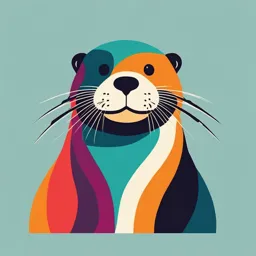
Uploaded by WorldFamousPhosphorus4784
null
Jayesh Vira
Tags
Related
- CE013 Introduction to the Building Code Part 2 PDF
- CE013 Introduction to the Building Code Part 1 to Structural System PDF
- Los Angeles City Wood Frame Prescriptive Provisions 2023
- Los Angeles City Wood Frame Prescriptive Provisions 2023
- IECC International Conservation Code 2021 PDF
- North Carolina State Building Code: Residential Code 2018 PDF
Summary
This document provides a comprehensive overview of ECBC code compliance, covering various aspects like building envelope, HVAC, lighting, and electrical systems. It also discusses the whole building simulation method for energy analysis.
Full Transcript
ECBC – Code Compliance ENVIRO CONSULTANCY SUSTAINABILITY SOLUTIONS Enviro Consultancy LLP Enviro Need for the Code To have World class standards & Essential to have a procedures code...
ECBC – Code Compliance ENVIRO CONSULTANCY SUSTAINABILITY SOLUTIONS Enviro Consultancy LLP Enviro Need for the Code To have World class standards & Essential to have a procedures code Uniformity and Benchmarking Continuous upgradation with the evolving technology Evolution of products and markets Enviro Different Codes Available codes National & International Design Case Base Case Enviro Scope of the Code Code applicable to buildings or building complexes having connected load of 100 kW or greater or a contract demand of 120 kVA or greater Intended to be used for commercial purposes Not Applicable to Residential Projects The provisions of this code do not apply to plug loads, and equipment and parts of buildings that use energy for manufacturing processes, unless otherwise specified in the Code. Performance levels of the Code ECBC Compliant Building - mandatory Increasing levels of ECBC+ Building - voluntary energy Super ECBC Building - voluntary efficiency Enviro Areas of Compliance Building Envelope Parameters for Compliance HVAC Service hot water Lighting Electrical Power & Motors Renewable Systems Enviro How to Read Code? Each area of compliance have some mandatory and some prescriptive requirements Mandatory – Section 4.2, 5.2, 6.2 & 7.2 Prescriptive - Section 4.3, 5.3, 6.3, Section 9 – Mentions the energy performance methodology & requirements Enviro Approach to meet the Code Compliance Prescriptive Approach: Meet all the Mandatory and Prescriptive requirements without any exception. Whole Building Simulation Approach: Meet all the Mandatory requirements and can perform building simulation which enables trade-offs in prescriptive requirements. Enviro Building Envelope Mandatory requirements Fenestration: U-Value, SHGC and VLT determination of the complete fenestration and not only for the Glass (Glass + 4.2.1 Fenestration Frame) 4.2.1.1 U-factors Should be conducted by lab or certified by 4.2.1.2 Solar Heat Gain Coefficient manufacture 4.2.1.3 Visual Light Transmittance Opaque Construction (Roof & Wall): Only U-value 4.2.2 Opaque Construction determination of complete assembly 4.2.3 Daylighting Daylighting (New Requirement): Minimum levels of 4.2.3.1 Daylighting Simulation Method daylight should meet the code requirements for different building 4.2.3.2 Manual Daylighting Compliance Method Building Envelope Sealing – Air leakages 4.2.4 Building Envelope Sealing Enviro Fenestration – Thermal Properties Enviro Building Envelope – Thermal Properties U-VALUE SHADING CO-EFFICIENT ❖ Shading coefficient ❖ U value – (W/m2.deg K) Heat gain thru’ a given glazing (SHGC) --------------------------------------------------- ❖ Heat transfer due to temperature difference Heat gain thru’ 3 mm clear glass (0.87) (conduction) ❖ Solar heat gain coefficient (SHGC) ❖ Typical U values Indicates direct heat gain Single glazed glass (6mm) : 5-6 ❖ Typical values High Performance glass : 1.7 – 3.0 Single glazed 6mm glass : 0.5 – 0.8 (6mm+airgap+6mm) High performance glass : 0.1 – 0.4 Enviro Prescriptive Requirement Maximum allowable Window Wall Ratio (WWR) is 40% Maximum allowable Skylight to Roof Ratio (SSR) is 5% Minimum allowable Visual Light Transmittance (VLT) is 0.27 Table 4-10 Vertical Fenestration effective SHGC Requirements for ECBC buildings Composite Hot and dry Warm and Temperate Cold humid Maximum U-factor (W/m2K) 3.00 3.00 3.00 3.00 3.00 Maximum SHGC Non-North 0.27 0.27 0.27 0.27 0.62 Maximum SHGC North 0.50 0.50 0.50 0.50 0.62 for latitude ≥ 15°N Maximum SHGC North 0.27 0.27 0.27 0.27 0.62 for latitude < 15°N See Appendix A for default values of unrated fenestration. Enviro Building Envelope – Thermal Properties Enviro Opaque Construction – Wall & Roof ❖ RCC Walls WALL OPTIONS U-value: 1.95 W/m2 deg K ❖ Brick wall with insulation Heat Storage higher Extruded polystyrene, Expanded polystyrene (thermocol), Glass wool, etc. Due to high mass ❖ Double wall with air cavity/Insulation ❖ Concrete blocks ❖ Concrete Roof ❖ Flyash bricks ❖ Autoclaved Aerated Concrete Blocks (AAC) U-value: 2.5 – 3.0 W/m2 deg K Efficient roof in a flat building Efficient wall in multi-storied building Enviro Opaque Construction – Wall & Roof TANDOOR TILES ROOF OPTIONS @ 50+° C ❖ Slab with Insulation (Overdeck/Underdeck) Extruded polystyrene, Expanded LANDSCAPE polystyrene (thermocol), Glass wool, etc. @ 40+° C ❖ Slab with brickbat coba ❖ Terrace Garden ❖ High Reflective Paint Original Image of the terrace garden Thermal Image of the terrace garden Thermal Image of Terrace Garden. Vegetated Landscape helps in reducing the Heat Island effect. Enviro Prescriptive Requirement Table 4-4 Roof Assembly U-factor (W/m2.K) Requirements for ECBC Compliant Building Composite Hot and Warm and Temperate Cold dry humid All building types, except 0.33 0.33 0.33 0.33 0.28 below School 10,000 m2 AGA 0.20 0.20 0.20 0.20 0.20 Table 4-7 Opaque Assembly Maximum U-factor (W/m2.K) Requirements for an ECBC compliant Building Composite Hot and dry Warm and Temperate Cold humid All building types, except 0.40 0.40 0.40 0.55 0.34 below No Star Hotel < 10,000 m2 AGA 0.63 0.63 0.63 0.63 0.40 Business < 10,000 m2 AGA 0.63 0.63 0.63 0.63 0.40 School