EASA Module 09 Human Factors PDF
Document Details
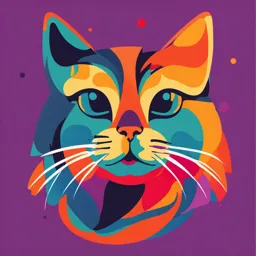
Uploaded by EruditeFreesia
EASA
Nancy Gold
Tags
Summary
This document is a module on human factors for aviation maintenance technicians. It includes details of general factors, human performance, social psychology, and factors affecting performance, among other topics. The module is part of the EASA Aviation Maintenance Technician Certification Series. It also includes sections regarding communication, human error, and hazards in the workplace.
Full Transcript
Module 09 FOR LEVEL B-1 AND B-2 CERTIFICATION HUMAN FACTORS Aviation Maintenance Technician Certification Series Hey Ken Here is a sample RFP that we would send out: EASA Module 5 B2 Quantities: 400, 1000 Trim Size/Pages: 8-3/8 x 10-7/8 with 180 pages + 4-page cover – General Factors – Human Perform...
Module 09 FOR LEVEL B-1 AND B-2 CERTIFICATION HUMAN FACTORS Aviation Maintenance Technician Certification Series Hey Ken Here is a sample RFP that we would send out: EASA Module 5 B2 Quantities: 400, 1000 Trim Size/Pages: 8-3/8 x 10-7/8 with 180 pages + 4-page cover – General Factors – Human Performance and Limitation – Social Psychology – Factors Affecting Performance – Physical Environment – Tasks – Communication – Human Error – Hazards in the Workplace EASA Part-66 Aviation Maintenance Technician Certification Series NO COST REVISION/UPDATE SUBSCRIPTION PROGRAM Complete EASA Part-66 Aviation Maintenance Technician Certification Series NO COST REVISION/UPDATE PROGRAM Aircraft Technical Book Company is offering a revision/update program to our customers who purchase an EASA Module from the EASA Aviation Maintenance Technician Certification Series. The update is good for two (2) years from time of registration of any EASA Module or EASA bundled kits. If a revision occurs within two (2) years from date of registration, we will send you the revised pages FREE of cost to the registered email. Go to the link provided at the bottom of this page and fill out the form to be included in the EASA Revision/Update Subscription Program. In an effort to provide quality customer service please let us know if your email you register with changes so we can update our records. If you have any questions about this process please send an email to: [email protected] HERE’S HOW IT WORKS 1. All EASA Module Series textbooks contain an EASA subscription page explaining the subscription update process and provide a web site link to register for the EASA Revision/Update Subscription Program. 2. Go to the link provided below and fill out the web based form with your first and last name, current email address, and school if applicable. 3. From the time of purchase, if a revision occurs to the Module you have registered for, a revised PDF file containing the pages with edits will be sent to the registered email provided. 4. Please note that we try to keep our records as current as possible. If your email address provided at time of registration changes please let us know as soon as possible so we can update your account. 5. This service is FREE of charge for two (2) years from date of registration. LINK TO REGISTER FOR REVISION/UPDATE PROGRAM http://www.actechbooks.com/easasub/m09 MODULE 09 FOR LEVEL B1 AND B2 CERTIFICATION HUMAN FACTORS Aviation Maintenance Technician Certification Series 72413 U.S. Hwy 40 Tabernash, CO 80478-0270 USA www.actechbooks.com +1 970 726-5111 +1 970 726-5115 fax AVAILABLE IN Printed Edition and Electronic (eBook) Format AVIATION MAINTENANCE TECHNICIAN CERTIFICATION SERIES Author Nancy Gold Contributor James W. Allen, MF, MPH - Working Healthy - Always Layout/Design Shellie L. Hall Government Resources Australian Government - Civil Aviation Safety Authority - Safety Behaviors - Human Factors Resource Guide for Engineers Federal Aviation Administration - Dr. William B. Johnson (FAA) Occupational Safety and Health Administration (OSHA) https://www.osha.gov Other Resources chirp-mems.co-uk - Learning from Experience #2 Copyright © 2015 — Aircraft Technical Book Company. All Rights Reserved. No part of this publication may be reproduced, stored in a retrieval system, transmitted in any form or by any means, electronic, mechanical, photocopying, recording or otherwise, without the prior written permission of the publisher. To order books or for Customer Service, please call +1 970 726.5111. www.actechbooks.com Printed in the United States of America WELCOME The publishers of this Aviation Maintenance Technician Certification Series welcome you to the world of aviation maintenance. As you move towards EASA certification, you are required to gain suitable knowledge and experience in your chosen area. Qualification on basic subjects for each aircraft maintenance license category or subcategory is accomplished in accordance with the following matrix. Where applicable, subjects are indicated by an "X" in the column below the license heading. For other educational tools created to prepare candidates for licensure, contact Aircraft Technical Book Company. We wish you good luck and success in your studies and in your aviation career! EASA LICENSE CATEGORY CHART Module number and title A1 Airplane Turbine B1.1 Airplane Turbine B1.2 Airplane Piston B1.3 Helicopter Turbine B2 Avionics 1 Mathematics X X X X X 2 Physics X X X X X 3 Electrical Fundamentals X X X X X 4 Electronic Fundamentals X X X X 5 Digital Techniques / Electronic Instrument Systems X X X X X 6 Materials and Hardware X X X X X 7A Maintenance Practices X X X X X 8 Basic Aerodynamics X X X X X 9A Human Factors X X X X X 10 Aviation Legislation X X X X X 11A Turbine Aeroplane Aerodynamics, Structures and Systems X X 11B Piston Aeroplane Aerodynamics, Structures and Systems 12 Helicopter Aerodynamics, Structures and Systems 13 Aircraft Aerodynamics, Structures and Systems X 14 Propulsion X 15 Gas Turbine Engine 16 Piston Engine 17A Propeller X X X X X X X X X FORWARD PART-66 and the Acceptable Means of Compliance (AMC) and Guidance Material (GM) of the European Aviation Safety Agency (EASA) Regulation (EC) No. 1321/2014, Appendix 1 to the Implementing Rules establishes the Basic Knowledge Requirements for those seeking an aircraft maintenance license. The information in this Module of the Aviation Maintenance Technical Certification Series published by the Aircraft Technical Book Company meets or exceeds the breadth and depth of knowledge subject matter referenced in Appendix 1 of the Implementing Rules. However, the order of the material presented is at the discretion of the editor in an effort to convey the required knowledge in the most sequential and comprehensible manner. Knowledge levels required for Category A, B1, B2, B2 and B3, and B3 aircraft C aircraft maintenance maintenance licenses licenses remain remain unchanged unchangedfrom fromthose thoselisted listedininAppendix Appendix11 Basic Knowledge Requirements. Tables from Appendix 1 Basic Knowledge Requirements are reproduced at the beginning of each module in the series and again at the beginning of each Sub-Module. How numbers are written in this book: This book uses the International Civil Aviation Organization (ICAO) standard of writing numbers. This methods displays large numbers by adding a space between each group of 3 digits. This is opposed to the American method which uses commas and the European method which uses periods. For example, the number one million is expressed as so: ICAO Standard 1 000 000 European Standard 1.000.000 American Standard 1,000,000 SI Units: The International System of Units (SI) developed and maintained by the General Conference of Weights and Measures (CGPM) shall be used as the standard system of units of measurement for all aspects of international civil aviation air and ground operations. Prefixes: The prefixes and symbols listed in the table below shall be used to form names and symbols of the decimal multiples and submultiples of International System of Units (SI) units. MULTIPLICATION FACTOR 1 000 000 000 000 000 000 1 000 000 000 000 000 1 000 000 000 000 1 000 000 000 1 000 000 1 000 100 10 0.1 0.01 0.001 0.000 001 0.000 000 001 0.000 000 000 001 0.000 000 000 000 001 0.000 000 000 000 000 001 = 101⁸ = 101⁵ = 1012 = 10⁹ = 10⁶ = 103 = 102 = 101 =10-1 = 10-2 = 10-3 = 10-⁶ = 10-⁹ = 10-12 = 10-1⁵ = 10-1⁸ PReFIx SyMbOL exa peta tera giga mega kilo hecto deca deci centi milli micro nano pico femto atto E P T G M k h da d c m µ n p f a International System of Units (SI) Prefixes PREFACE This module includes an examination of the discipline known as Human Factors. In many senses, as human error is cited as the primary cause of almost all aviation incidents and accidents, this subject may be considered the most important of your entire study. Interpersonal communications, a shared sense of a company culture, and a good understanding of personal and workplace stresses are absolutely critical to aviation safety for you, your teammates, and the tens of thousands of people who will fly in the aircraft you maintain. The other aspect of human factors is your own personal safety. Your education, experience, and professional goals will mean little if struck down by an injury or other workplace hazard. While this module covers each of these aspects and more, it is most important to understand that human factors is not just something to learn and test for during a couple of weeks in class. It is a way of life affecting everything you do and every day you do it. Learning to incorporate these concepts in your day-to-day work will ensure a long, rewarding, and successful professional career. Module 09 Syllabus as outlined in PART-66, Appendix 1. CERTIFICATION CATEGORY ¦ Sub-Module 01 - General The need to take human factors into account; Incidents attributable to human factors/human error; Murphy's Law. Sub-Module 02 - Human Performance and Limitations Vision; Hearing; Information processing; Attention and perception; Memory; Claustrophobia; Physical access. Sub-Module 03 - Social Psychology Responsibility; Individual and group; Motivation and demotivation; Peer Pressure; Culture issues; Team working; Management, supervision and leadership. Sub-Module 04 - Factors Affecting Performance Fitness and health; Stress: domestic and work related; Time pressure and deadlines; Workload: overload and underload; Sleep and fatigue, shiftwork; Alcohol, medication, drug abuse. Module 09 - Human Factors LEVELS A B1 B2 1 2 2 1 2 2 1 1 1 2 2 2 v LEVELS CERTIFICATION CATEGORY ¦ Sub-Module 05 - Physical Environment Noise and fumes; Illumination; Climate and Temperature; Motion and Vibration; Working Environment. Sub-Module 06 - Tasks Physical work; Repetitive Tasks; Visual inspection; Complex systems. Sub-Module 07 - Communication Within and between teams; Work logging and recording; Keeping up to date; Currency; Dissemination of information. Sub-Module 08 - Human Error Error models and theories; Types of error in maintenance tasks; Implications of errors (i.e. accidents); Avoiding and managing errors. Sub-Module 09 - Hazards in the Workplace Recognizing and avoiding hazards; Dealing with Emergencies. vi A B1 B2 1 1 1 1 1 1 2 2 2 1 2 2 1 2 2 Module 09 - Human Factors Module 09 - Human Factors vii REVISION LOG VERSION ISSUE DATE 001 2016 01 DESCRIPTION OF CHANGE MODIFICATION DATE Module Creation and Release ACKNOWLEDGMENTS 1 2 3 4 James W. Allen, MF, MPH – Working Healthy – Always Australian Government - Civil Aviation Safety Authority - Safety Behaviors – Human Factors Resource Guide for Engineers Federal Aviation Administration – Dr. William B. Johnson (FAA) Occupational Safety and Health Administration (OSHA) https://www.osha.gov Sub-Module 01 – General 1 Latent Medical and Environmental Conditions (LMEC) 2 737-300 accident 3 PEAR Sub-Module 02 – Human Performance and Limitations 1 Aging Eyes Symptoms 1 Hearing Protection 1 Hearing Loss Studies 2 Information Processing 2 Memory Sub-Module 04 – Factors Affecting Performance Case Study: Taking It For Granted – CASA 2 Teamwork 2 What Leadership Is Not 2 Leadership Under Stress 2 Consider The Following Scenario 2 Stress: Domestic and Work Related 2 Workload – Overload and Under load viii 2 2 Sleep and Fatigue Alcohol, Medication, Drug Abuse Sub-Module 05 – Physical Environment 1 Fumes, Chemicals, Toxic Metals and Solvents 1 Climate and Temperature Sub-Module 06 – Tasks Lack of Resources … Not a Problem – CASA Sub-Module 07 – Communication 2 Communication Channels 2 Within and Between Teams 2 An Accident Related to a Shift Handover - CASA 2 Four Ways to Improve Shift Handover - CASA 2 Effective and Ineffective Handovers - CASA Sub-Module 08 – Human Error 2 Introduction 3 The Dirty Dozen 3 Avoiding and Managing Errors 3 PEAR 2 Types of Errors Sub-Module 09 – Hazards In The Work Place 4 Recognizing and Avoiding Hazards Module 09 - Human Factors CONTENTS HUMAN FACTORS Welcome‥‥‥‥‥‥‥‥‥‥‥‥‥‥‥‥‥‥‥‥‥‥‥‥‥‥‥‥‥‥‥‥‥‥‥‥‥ Forward‥‥‥‥‥‥‥‥‥‥‥‥‥‥‥‥‥‥‥‥‥‥‥‥‥‥‥‥‥‥‥‥‥‥‥‥‥‥ Preface‥‥‥‥‥‥‥‥‥‥‥‥‥‥‥‥‥‥‥‥‥‥‥‥‥‥‥‥‥‥‥‥‥‥‥‥‥‥‥ Revision Log‥‥‥‥‥‥‥‥‥‥‥‥‥‥‥‥‥‥‥‥‥‥‥‥‥‥‥‥‥‥‥‥‥‥ Acknowledgments‥‥‥‥‥‥‥‥‥‥‥‥‥‥‥‥‥‥‥‥‥‥‥‥‥‥‥‥‥ Contents‥‥‥‥‥‥‥‥‥‥‥‥‥‥‥‥‥‥‥‥‥‥‥‥‥‥‥‥‥‥‥‥‥‥‥‥‥ iii iv v viii viii ix SUB-MODULE 01 GENERAL Knowledge Requirements‥‥‥‥‥‥‥‥‥‥‥‥‥‥‥‥‥‥‥‥‥‥‥ General‥‥‥‥‥‥‥‥‥‥‥‥‥‥‥‥‥‥‥‥‥‥‥‥‥‥‥‥‥‥‥‥‥‥‥‥‥‥ The need to take Human Factors into account‥‥‥‥‥ The PEAR model of human factors in maintenance‥ People: The human and the interactions between people‥‥‥‥‥‥‥‥‥‥‥‥‥‥‥‥‥‥‥‥‥‥‥‥‥ Environment: Physical and organizational‥‥ Action: Procedures, paperwork and poor design‥‥‥‥‥‥‥‥‥‥‥‥‥‥‥‥‥‥‥‥‥‥‥‥‥‥‥‥ Resources: A lack of, or deficient‥‥‥‥‥‥‥‥‥‥ The organizational environment‥‥‥‥‥‥‥‥‥‥‥‥‥‥‥‥ The Dirty Dozen‥‥‥‥‥‥‥‥‥‥‥‥‥‥‥‥‥‥‥‥‥‥‥‥‥‥‥‥ Incidents related to Human Factors‥‥‥‥‥‥‥‥‥‥‥‥‥‥‥‥ Case Study: Aloha Airlines Flight 243‥‥‥‥‥‥‥‥‥‥‥ Investigation‥‥‥‥‥‥‥‥‥‥‥‥‥‥‥‥‥‥‥‥‥‥‥‥‥‥‥‥‥ Safety Recommendations‥‥‥‥‥‥‥‥‥‥‥‥‥‥‥‥‥‥‥ Some of “The Dirty Dozen” Human Factors specific to this accident‥‥‥‥‥‥‥‥ Case Study: British Airways BAC-111 Windscreen Blowout‥‥‥‥‥‥‥‥‥‥‥‥‥‥‥‥‥‥‥‥‥‥‥‥‥ Investigation‥‥‥‥‥‥‥‥‥‥‥‥‥‥‥‥‥‥‥‥‥‥‥‥‥‥‥‥‥ Safety Recommendations‥‥‥‥‥‥‥‥‥‥‥‥‥‥‥‥‥‥‥ Some of “The Dirty Dozen” Human Factors specific to this accident‥‥‥‥‥‥‥‥ Case Study: Nose Wheel Jammed on DASH-8‥‥‥‥ Investigation‥‥‥‥‥‥‥‥‥‥‥‥‥‥‥‥‥‥‥‥‥‥‥‥‥‥‥‥‥ Some of “The Dirty Dozen” Human Factors specific to this accident‥‥‥‥‥‥‥‥ Case Study: Failure to Pressurize After Outflow Valve Left in Open Position‥‥‥‥‥‥‥‥‥‥‥‥ Investigation‥‥‥‥‥‥‥‥‥‥‥‥‥‥‥‥‥‥‥‥‥‥‥‥‥‥‥‥‥ Safety Recommendations‥‥‥‥‥‥‥‥‥‥‥‥‥‥‥‥‥‥‥ Some of “The Dirty Dozen” Human Factors specific to this accident‥‥‥‥‥‥‥‥ Case Study: Main Wheel Incorrectly Fitted‥‥‥‥‥‥ Investigation‥‥‥‥‥‥‥‥‥‥‥‥‥‥‥‥‥‥‥‥‥‥‥‥‥‥‥‥‥ Module 09 - Human Factors 1.1 1.2 1.2 1.4 1.6 1.6 1.6 1.7 1.7 1.7 1.8 1.8 1.9 1.9 1.10 1.10 1.10 1.11 1.11 1.12 1.12 1.12 1.13 1.13 1.14 1.14 1.14 1.14 Safety Recommendations‥‥‥‥‥‥‥‥‥‥‥‥‥‥‥‥‥‥‥ Some of “The Dirty Dozen” Human Factors specific to this accident‥‥‥‥‥‥‥‥ Case Study: Torch left in nose wheel steering cable run‥‥‥‥‥‥‥‥‥‥‥‥‥‥‥‥‥‥‥‥‥‥‥‥‥‥‥‥ Investigation and Recommendations‥‥‥‥‥‥‥‥‥‥ Some of “The Dirty Dozen” Human Factors specific to this accident‥‥‥‥‥‥‥‥ Murphy’s Law‥‥‥‥‥‥‥‥‥‥‥‥‥‥‥‥‥‥‥‥‥‥‥‥‥‥‥‥‥‥‥‥‥ Questions‥‥‥‥‥‥‥‥‥‥‥‥‥‥‥‥‥‥‥‥‥‥‥‥‥‥‥‥‥‥‥‥‥‥‥‥ Answers‥‥‥‥‥‥‥‥‥‥‥‥‥‥‥‥‥‥‥‥‥‥‥‥‥‥‥‥‥‥‥‥‥‥‥‥‥ 1.15 1.15 1.15 1.16 1.16 1.17 1.19 1.20 SUB-MODULE 02 HUMAN PERFORMANCE AND LIMITATIONS Knowledge Requirements‥‥‥‥‥‥‥‥‥‥‥‥‥‥‥‥‥‥‥‥‥‥‥ 2.1 Introduction‥‥‥‥‥‥‥‥‥‥‥‥‥‥‥‥‥‥‥‥‥‥‥‥‥‥‥‥‥‥‥‥‥‥ 2.2 Vision‥‥‥‥‥‥‥‥‥‥‥‥‥‥‥‥‥‥‥‥‥‥‥‥‥‥‥‥‥‥‥‥‥‥‥‥‥‥‥ 2.2 The Basic Function of the Eye‥‥‥‥‥‥‥‥‥‥‥‥‥‥‥‥‥‥ 2.2 Components of the Eye‥‥‥‥‥‥‥‥‥‥‥‥‥‥‥‥‥‥‥‥‥‥‥ 2.2 The Cornea‥‥‥‥‥‥‥‥‥‥‥‥‥‥‥‥‥‥‥‥‥‥‥‥‥‥‥‥‥‥ 2.2 The Iris and Pupil‥‥‥‥‥‥‥‥‥‥‥‥‥‥‥‥‥‥‥‥‥‥‥‥‥ 2.3 The Lens‥‥‥‥‥‥‥‥‥‥‥‥‥‥‥‥‥‥‥‥‥‥‥‥‥‥‥‥‥‥‥‥ 2.3 The Retina:‥‥‥‥‥‥‥‥‥‥‥‥‥‥‥‥‥‥‥‥‥‥‥‥‥‥‥‥‥‥ 2.3 Factors Affecting Clarity of Sight‥‥‥‥‥‥‥‥‥‥‥‥‥‥‥ 2.3 Blind Spot‥‥‥‥‥‥‥‥‥‥‥‥‥‥‥‥‥‥‥‥‥‥‥‥‥‥‥‥‥‥‥ 2.3 Refractive Errors‥‥‥‥‥‥‥‥‥‥‥‥‥‥‥‥‥‥‥‥‥‥‥‥‥‥ 2.4 Other visual problems include‥‥‥‥‥‥‥‥‥‥‥‥‥‥‥ 2.4 Foreign Substances‥‥‥‥‥‥‥‥‥‥‥‥‥‥‥‥‥‥‥‥‥‥‥‥ 2.5 Environmental Factors‥‥‥‥‥‥‥‥‥‥‥‥‥‥‥‥‥‥‥‥‥ 2.5 The Nature of the Object Being Viewed‥‥‥‥‥‥‥ 2.5 Color Vision‥‥‥‥‥‥‥‥‥‥‥‥‥‥‥‥‥‥‥‥‥‥‥‥‥‥‥‥‥ 2.5 Night Vision and Color Loss‥‥‥‥‥‥‥‥‥‥‥‥‥‥‥‥ 2.6 Vision and the Aging Eyes‥‥‥‥‥‥‥‥‥‥‥‥‥‥‥‥‥‥‥‥ 2.6 What can be done?‥‥‥‥‥‥‥‥‥‥‥‥‥‥‥‥‥‥‥‥‥‥‥‥‥‥ 2.7 Hearing‥‥‥‥‥‥‥‥‥‥‥‥‥‥‥‥‥‥‥‥‥‥‥‥‥‥‥‥‥‥‥‥‥‥‥‥‥‥ 2.8 The Basic Function of the Ear‥‥‥‥‥‥‥‥‥‥‥‥‥‥‥‥‥‥ 2.8 Outer Ear‥‥‥‥‥‥‥‥‥‥‥‥‥‥‥‥‥‥‥‥‥‥‥‥‥‥‥‥‥‥‥ 2.8 Middle Ear‥‥‥‥‥‥‥‥‥‥‥‥‥‥‥‥‥‥‥‥‥‥‥‥‥‥‥‥‥‥ 2.8 Inner Ear‥‥‥‥‥‥‥‥‥‥‥‥‥‥‥‥‥‥‥‥‥‥‥‥‥‥‥‥‥‥‥‥ 2.8 Performance and Limitations of the Ear‥‥‥‥‥‥‥‥‥‥ 2.8 Impact of Noise on Performance‥‥‥‥‥‥‥‥‥‥‥‥‥ 2.9 High and Low Tone Deafness‥‥‥‥‥‥‥‥‥‥‥‥‥‥‥ 2.9 Hearing Protection‥‥‥‥‥‥‥‥‥‥‥‥‥‥‥‥‥‥‥‥‥‥‥‥ 2.9 Hearing Loss Studies‥‥‥‥‥‥‥‥‥‥‥‥‥‥‥‥‥‥‥‥‥‥‥‥ 2.10 Information Processing‥‥‥‥‥‥‥‥‥‥‥‥‥‥‥‥‥‥‥‥‥‥‥‥‥ 2.11 Information Processing Model ‥‥‥‥‥‥‥‥‥‥‥‥‥‥‥‥‥ 2.11 ix CONTENTS Stage 1: Gathering information‥‥‥‥‥‥‥‥‥‥‥‥‥‥ Stage 2: Perception or assessment‥‥‥‥‥‥‥‥‥‥‥‥‥ Stage 3: Evaluation and decision making‥‥‥‥‥‥‥ Stage 4: Action/response‥‥‥‥‥‥‥‥‥‥‥‥‥‥‥‥‥‥‥ Stage 5: Feedback‥‥‥‥‥‥‥‥‥‥‥‥‥‥‥‥‥‥‥‥‥‥‥‥‥ Attention and Perception‥‥‥‥‥‥‥‥‥‥‥‥‥‥‥‥‥‥‥‥‥ Attention‥‥‥‥‥‥‥‥‥‥‥‥‥‥‥‥‥‥‥‥‥‥‥‥‥‥‥‥‥‥‥‥ Perception‥‥‥‥‥‥‥‥‥‥‥‥‥‥‥‥‥‥‥‥‥‥‥‥‥‥‥‥‥‥‥ Examples of the perceptual process:‥‥‥‥‥‥‥‥ Memory‥‥‥‥‥‥‥‥‥‥‥‥‥‥‥‥‥‥‥‥‥‥‥‥‥‥‥‥‥‥‥‥‥‥‥‥‥ Claustrophobia‥‥‥‥‥‥‥‥‥‥‥‥‥‥‥‥‥‥‥‥‥‥‥‥‥‥‥‥‥‥ Fear of Heights ‥‥‥‥‥‥‥‥‥‥‥‥‥‥‥‥‥‥‥‥‥‥‥‥‥‥‥‥‥ Conclusion‥‥‥‥‥‥‥‥‥‥‥‥‥‥‥‥‥‥‥‥‥‥‥‥‥‥‥‥‥‥ Questions‥‥‥‥‥‥‥‥‥‥‥‥‥‥‥‥‥‥‥‥‥‥‥‥‥‥‥‥‥‥‥‥‥‥‥‥ Answers‥‥‥‥‥‥‥‥‥‥‥‥‥‥‥‥‥‥‥‥‥‥‥‥‥‥‥‥‥‥‥‥‥‥‥‥‥ 2.11 2.12 2.12 2.12 2.13 2.13 2.13 2.14 2.14 2.16 2.17 2.18 2.18 2.19 2.20 SUB-MODULE 03 SOCIAL PSYCHOLOGY Knowledge Requirements‥‥‥‥‥‥‥‥‥‥‥‥‥‥‥‥‥‥‥‥‥‥‥ Introduction‥‥‥‥‥‥‥‥‥‥‥‥‥‥‥‥‥‥‥‥‥‥‥‥‥‥‥‥‥‥‥‥‥‥ Responsibility‥‥‥‥‥‥‥‥‥‥‥‥‥‥‥‥‥‥‥‥‥‥‥‥‥‥‥‥‥‥‥‥‥ Individual Responsibility‥‥‥‥‥‥‥‥‥‥‥‥‥‥‥‥‥‥‥‥‥‥ Case Study: Taking it For Granted‥‥‥‥‥‥‥‥‥‥‥‥‥‥ Key Lessons‥‥‥‥‥‥‥‥‥‥‥‥‥‥‥‥‥‥‥‥‥‥‥‥‥‥‥‥‥‥ Key Points‥‥‥‥‥‥‥‥‥‥‥‥‥‥‥‥‥‥‥‥‥‥‥‥‥‥‥‥‥‥‥ Group or Team Responsibility‥‥‥‥‥‥‥‥‥‥‥‥‥‥‥‥‥ Intergroup Conflict ‥‥‥‥‥‥‥‥‥‥‥‥‥‥‥‥‥‥‥‥‥‥‥ Group Polarization / Groupthink‥‥‥‥‥‥‥‥‥‥‥‥ Social Loafing‥‥‥‥‥‥‥‥‥‥‥‥‥‥‥‥‥‥‥‥‥‥‥‥‥‥‥‥ Motivation and Demotivation‥‥‥‥‥‥‥‥‥‥‥‥‥‥‥‥‥‥‥‥ Motivation‥‥‥‥‥‥‥‥‥‥‥‥‥‥‥‥‥‥‥‥‥‥‥‥‥‥‥‥‥‥‥‥‥ Reward and Punishment: Effects on Behavior‥‥‥‥‥ Maslow’s Hierarchy of Needs‥‥‥‥‥‥‥‥‥‥‥‥‥‥‥‥‥‥ Demotivation‥‥‥‥‥‥‥‥‥‥‥‥‥‥‥‥‥‥‥‥‥‥‥‥‥‥‥‥‥‥‥ Peer Pressure‥‥‥‥‥‥‥‥‥‥‥‥‥‥‥‥‥‥‥‥‥‥‥‥‥‥‥‥‥‥‥‥‥‥ Experiment to illustrate conformity (S. Asch 1951)‥‥‥‥‥‥‥‥‥‥‥‥‥‥‥‥‥‥‥‥‥‥‥‥‥‥‥‥ Culture and Safety Culture‥‥‥‥‥‥‥‥‥‥‥‥‥‥‥‥‥‥‥‥‥‥ How does the organizational culture affect the work of an AMT?‥‥‥‥‥‥‥‥‥‥‥‥‥‥‥‥‥ The influence of organizational culture on safety‥‥‥ Role in developing the culture of safety‥‥‥‥‥‥‥‥ How do you recognize an organization with a good safety culture?‥‥‥‥‥‥‥‥‥‥‥‥‥‥‥‥‥‥ Teamwork‥‥‥‥‥‥‥‥‥‥‥‥‥‥‥‥‥‥‥‥‥‥‥‥‥‥‥‥‥‥‥‥‥‥‥‥ Characteristics of teams‥‥‥‥‥‥‥‥‥‥‥‥‥‥‥‥‥‥‥‥‥‥‥ Conditions for effective teamwork‥‥‥‥‥‥‥‥‥‥‥‥‥‥ x 3.1 3.2 3.2 3.2 3.3 3.3 3.3 3.4 3.4 3.4 3.4 3.5 3.5 3.5 3.6 3.6 3.7 3.8 3.9 3.9 3.9 3.10 3.10 3.10 3.11 3.11 A shared and understood goal‥‥‥‥‥‥‥‥‥‥‥‥‥‥‥ Effective leadership and followership‥‥‥‥‥‥‥‥‥‥ A shared mental model‥‥‥‥‥‥‥‥‥‥‥‥‥‥‥‥‥‥‥‥‥ Practice Clear and Effective Communication‥‥‥ Clear delegation & Role definition‥‥‥‥‥‥‥‥‥‥‥‥ Clear operating procedures‥‥‥‥‥‥‥‥‥‥‥‥‥‥‥‥‥‥ Appropriate allocation of workload‥‥‥‥‥‥‥‥‥‥‥ Appropriate authority gradient‥‥‥‥‥‥‥‥‥‥‥‥‥‥‥ Conflict resolution‥‥‥‥‥‥‥‥‥‥‥‥‥‥‥‥‥‥‥‥‥‥‥‥ Key Points‥‥‥‥‥‥‥‥‥‥‥‥‥‥‥‥‥‥‥‥‥‥‥‥‥‥‥‥‥‥‥‥‥ Management, Supervision and Leadership‥‥‥‥‥‥‥‥‥‥ The Management Role‥‥‥‥‥‥‥‥‥‥‥‥‥‥‥‥‥‥‥‥‥‥‥ The Supervisory Role‥‥‥‥‥‥‥‥‥‥‥‥‥‥‥‥‥‥‥‥‥‥‥‥‥ Leadership‥‥‥‥‥‥‥‥‥‥‥‥‥‥‥‥‥‥‥‥‥‥‥‥‥‥‥‥‥‥‥‥‥ Characteristics of a Good Leader‥‥‥‥‥‥‥‥‥‥‥‥‥ What is leadership‥‥‥‥‥‥‥‥‥‥‥‥‥‥‥‥‥‥‥‥‥‥‥‥ Motivating the Team:‥‥‥‥‥‥‥‥‥‥‥‥‥‥‥‥‥‥‥ Reinforcing Good Attitudes and Behavior:‥‥ Demonstrating by Example: ‥‥‥‥‥‥‥‥‥‥‥‥‥‥ Maintaining the Group:‥‥‥‥‥‥‥‥‥‥‥‥‥‥‥‥‥‥ Fulfilling a Management Role:‥‥‥‥‥‥‥‥‥‥‥‥ What leadership is not‥‥‥‥‥‥‥‥‥‥‥‥‥‥‥‥‥‥‥‥‥ Leadership under stress‥‥‥‥‥‥‥‥‥‥‥‥‥‥‥‥‥‥‥‥ Consider the following scenario‥‥‥‥‥‥‥‥‥‥‥‥‥‥ Conclusion‥‥‥‥‥‥‥‥‥‥‥‥‥‥‥‥‥‥‥‥‥‥‥‥‥‥‥‥‥‥‥‥‥ Questions‥‥‥‥‥‥‥‥‥‥‥‥‥‥‥‥‥‥‥‥‥‥‥‥‥‥‥‥‥‥‥‥‥‥‥‥ Answers‥‥‥‥‥‥‥‥‥‥‥‥‥‥‥‥‥‥‥‥‥‥‥‥‥‥‥‥‥‥‥‥‥‥‥‥‥ 3.11 3.11 3.11 3.11 3.12 3.12 3.12 3.13 3.13 3.13 3.14 3.14 3.14 3.14 3.14 3.15 3.15 3.15 3.15 3.15 3.15 3.15 3.16 3.16 3.16 3.17 3.18 SUB-MODULE 04 FACTORS AFFECTING PERFORMANCE Knowledge Requirements‥‥‥‥‥‥‥‥‥‥‥‥‥‥‥‥‥‥‥‥‥‥‥ Introduction‥‥‥‥‥‥‥‥‥‥‥‥‥‥‥‥‥‥‥‥‥‥‥‥‥‥‥‥‥‥‥‥‥‥ Fitness and Health‥‥‥‥‥‥‥‥‥‥‥‥‥‥‥‥‥‥‥‥‥‥‥‥‥‥‥‥‥ Pre-employment Physical‥‥‥‥‥‥‥‥‥‥‥‥‥‥‥‥‥‥‥‥‥ Day to Day Fitness and Health‥‥‥‥‥‥‥‥‥‥‥‥‥‥‥‥‥ Positive Measures‥‥‥‥‥‥‥‥‥‥‥‥‥‥‥‥‥‥‥‥‥‥‥‥‥‥‥‥ Stress: Domestic and Work Related‥‥‥‥‥‥‥‥‥‥‥‥‥‥‥ Introduction‥‥‥‥‥‥‥‥‥‥‥‥‥‥‥‥‥‥‥‥‥‥‥‥‥‥‥‥‥‥‥‥ Characteristics of Stress‥‥‥‥‥‥‥‥‥‥‥‥‥‥‥‥‥‥‥‥‥‥‥ Stress is Cumulative‥‥‥‥‥‥‥‥‥‥‥‥‥‥‥‥‥‥‥‥‥‥‥‥‥‥ Causes of Stress‥‥‥‥‥‥‥‥‥‥‥‥‥‥‥‥‥‥‥‥‥‥‥‥‥‥‥‥‥ Stressors‥‥‥‥‥‥‥‥‥‥‥‥‥‥‥‥‥‥‥‥‥‥‥‥‥‥‥‥‥‥‥‥‥‥‥ Symptoms of Stress‥‥‥‥‥‥‥‥‥‥‥‥‥‥‥‥‥‥‥‥‥‥‥‥‥‥ Consequences for AMTs‥‥‥‥‥‥‥‥‥‥‥‥‥‥‥‥‥‥‥‥‥‥ Domestic Stress‥‥‥‥‥‥‥‥‥‥‥‥‥‥‥‥‥‥‥‥‥‥‥‥‥‥‥‥‥ Work Related Stress‥‥‥‥‥‥‥‥‥‥‥‥‥‥‥‥‥‥‥‥‥‥‥‥‥ Managing Stress‥‥‥‥‥‥‥‥‥‥‥‥‥‥‥‥‥‥‥‥‥‥‥‥‥‥‥‥ 4.1 4.2 4.2 4.2 4.2 4.3 4.3 4.3 4.3 4.3 4.3 4.4 4.4 4.4 4.4 4.4 4.5 Module 09 - Human Factors CONTENTS Stress Coping Strategies‥‥‥‥‥‥‥‥‥‥‥‥‥‥‥‥‥‥‥‥‥‥ 4.5 Achieving relaxation‥‥‥‥‥‥‥‥‥‥‥‥‥‥‥‥‥‥‥‥‥‥‥ 4.5 How stressed are you?‥‥‥‥‥‥‥‥‥‥‥‥‥‥‥‥‥‥‥‥‥‥ 4.6 Time Pressure and Deadlines‥‥‥‥‥‥‥‥‥‥‥‥‥‥‥‥‥‥‥‥ 4.7 Time pressure and self imposed pressure‥‥‥‥‥‥‥‥‥ 4.7 How can inappropriate actual or self imposed pressure be managed?‥‥‥‥‥‥‥‥‥‥‥‥‥‥‥‥‥‥‥‥‥‥‥‥‥‥‥‥‥ 4.7 Stress and time pressure in shift and task handovers‥ 4.8 Managing Shift Handovers?‥‥‥‥‥‥‥‥‥‥‥‥‥‥‥‥‥ 4.8 Key Points‥‥‥‥‥‥‥‥‥‥‥‥‥‥‥‥‥‥‥‥‥‥‥‥‥‥‥‥‥‥‥‥‥ 4.8 Workload—Overload and Underload‥‥‥‥‥‥‥‥‥‥‥‥‥‥ 4.9 Factors determining workload‥‥‥‥‥‥‥‥‥‥‥‥‥‥‥‥‥‥ 4.9 Work overload‥‥‥‥‥‥‥‥‥‥‥‥‥‥‥‥‥‥‥‥‥‥‥‥‥‥‥‥‥‥ 4.10 Causes of high workload‥‥‥‥‥‥‥‥‥‥‥‥‥‥‥‥‥‥‥‥ 4.10 Case Study: Short Handed!‥‥‥‥‥‥‥‥‥‥‥‥‥‥‥‥‥‥‥‥ 4.11 Work Underload‥‥‥‥‥‥‥‥‥‥‥‥‥‥‥‥‥‥‥‥‥‥‥‥‥‥‥‥ 4.11 Sleep and Fatigue‥‥‥‥‥‥‥‥‥‥‥‥‥‥‥‥‥‥‥‥‥‥‥‥‥‥‥‥‥‥ 4.12 What is fatigue?‥‥‥‥‥‥‥‥‥‥‥‥‥‥‥‥‥‥‥‥‥‥‥‥‥‥‥‥‥ 4.12 The effects of fatigue‥‥‥‥‥‥‥‥‥‥‥‥‥‥‥‥‥‥‥‥‥‥‥‥‥ 4.12 Think about it!‥‥‥‥‥‥‥‥‥‥‥‥‥‥‥‥‥‥‥‥‥‥‥‥‥‥‥‥‥‥ 4.13 Consider these two imaginary scenarios:‥‥‥‥‥‥‥ 4.13 Scenario 1‥‥‥‥‥‥‥‥‥‥‥‥‥‥‥‥‥‥‥‥‥‥‥‥‥‥‥‥‥ 4.13 Scenario 2‥‥‥‥‥‥‥‥‥‥‥‥‥‥‥‥‥‥‥‥‥‥‥‥‥‥‥‥‥ 4.13 Memory failures‥‥‥‥‥‥‥‥‥‥‥‥‥‥‥‥‥‥‥‥‥‥‥‥ 4.13 Failures to notice defects or problems‥‥‥‥‥‥‥ 4.13 Case Study‥‥‥‥‥‥‥‥‥‥‥‥‥‥‥‥‥‥‥‥‥‥‥‥‥‥‥‥‥‥‥‥‥ 4.14 Are we the best judges of our level of fatigue?‥‥‥‥‥‥‥‥‥‥‥‥‥‥‥‥‥‥‥‥‥‥‥‥‥ 4.14 The Impact of fatigue in the workplace‥‥‥‥‥‥‥‥‥‥‥ 4.14 The Causes of Fatigue‥‥‥‥‥‥‥‥‥‥‥‥‥‥‥‥‥‥‥‥‥‥‥‥ 4.15 Sleep Debt‥‥‥‥‥‥‥‥‥‥‥‥‥‥‥‥‥‥‥‥‥‥‥‥‥‥‥‥‥‥‥ 4.15 Sleep Apnea‥‥‥‥‥‥‥‥‥‥‥‥‥‥‥‥‥‥‥‥‥‥‥‥‥‥‥‥‥‥‥‥ 4.16 When to see a doctor‥‥‥‥‥‥‥‥‥‥‥‥‥‥‥‥‥‥‥‥‥‥ 4.16 Circadian Rhythms‥‥‥‥‥‥‥‥‥‥‥‥‥‥‥‥‥‥‥‥‥‥‥‥‥‥ 4.17 Do shift workers adapt to permanent night shifts?‥‥‥‥‥‥‥‥‥‥‥‥‥‥‥‥‥‥‥‥‥‥‥‥‥‥‥‥‥‥ 4.17 Beware the WOCL!‥‥‥‥‥‥‥‥‥‥‥‥‥‥‥‥‥‥‥‥‥‥‥ 4.17 Factors that increase the impact of fatigue‥‥‥‥‥‥ 4.18 Case Study‥‥‥‥‥‥‥‥‥‥‥‥‥‥‥‥‥‥‥‥‥‥‥‥‥‥‥‥‥‥‥‥‥ 4.18 Managing the risks of fatigue in aviation maintenance‥‥‥‥‥‥‥‥‥‥‥‥‥‥‥‥‥‥‥‥‥‥ 4.19 Sleep inertia (AKA ‘sleep drunkenness’)‥‥‥‥‥‥‥ 4.19 Responsibilities of the employer‥‥‥‥‥‥‥‥‥‥‥‥‥‥ 4.20 Responsibilities of the employee‥‥‥‥‥‥‥‥‥‥‥‥‥‥ 4.20 Strategies to deal with fatigue‥‥‥‥‥‥‥‥‥‥‥‥‥‥‥‥‥‥ 4.20 Get more sleep!‥‥‥‥‥‥‥‥‥‥‥‥‥‥‥‥‥‥‥‥‥‥‥‥‥‥‥ 4.20 Tips for better sleep‥‥‥‥‥‥‥‥‥‥‥‥‥‥‥‥‥‥‥‥‥‥‥ 4.21 Module 09 - Human Factors Controlled naps‥‥‥‥‥‥‥‥‥‥‥‥‥‥‥‥‥‥‥‥‥‥‥‥‥‥‥ Caffeine‥‥‥‥‥‥‥‥‥‥‥‥‥‥‥‥‥‥‥‥‥‥‥‥‥‥‥‥‥‥‥‥‥ Breaks‥‥‥‥‥‥‥‥‥‥‥‥‥‥‥‥‥‥‥‥‥‥‥‥‥‥‥‥‥‥‥‥‥‥ Progressive restrictions‥‥‥‥‥‥‥‥‥‥‥‥‥‥‥‥‥‥‥‥‥ Key Points‥‥‥‥‥‥‥‥‥‥‥‥‥‥‥‥‥‥‥‥‥‥‥‥‥‥‥‥‥‥‥‥‥ Shift Work‥‥‥‥‥‥‥‥‥‥‥‥‥‥‥‥‥‥‥‥‥‥‥‥‥‥‥‥‥‥‥‥‥‥‥ Advantages and Disadvantages of Shift Work ‥‥‥‥ Rolling Shift Patterns‥‥‥‥‥‥‥‥‥‥‥‥‥‥‥‥‥‥‥‥‥‥‥‥ Sleep, Fatigue, Shift Work and the Aviation Maintenance Technician‥‥‥‥‥‥‥‥‥‥‥‥‥‥ Alcohol, Medication, Drug Abuse‥‥‥‥‥‥‥‥‥‥‥‥‥‥‥‥‥ Alcohol‥‥‥‥‥‥‥‥‥‥‥‥‥‥‥‥‥‥‥‥‥‥‥‥‥‥‥‥‥‥‥‥‥‥‥‥ What is alcohol?‥‥‥‥‥‥‥‥‥‥‥‥‥‥‥‥‥‥‥‥‥‥‥‥‥‥ Alcohol and Safety‥‥‥‥‥‥‥‥‥‥‥‥‥‥‥‥‥‥‥‥‥‥‥‥ Alcohol and Sleep‥‥‥‥‥‥‥‥‥‥‥‥‥‥‥‥‥‥‥‥‥‥‥‥‥ Disturbance of paradoxical (REM) sleep/slow wave sleep cycle‥‥‥‥‥‥‥‥‥‥‥‥‥‥‥‥‥‥ Daytime repercussions of alcohol’s effects on sleep‥‥‥‥‥‥‥‥‥‥‥‥‥‥‥‥‥‥‥‥‥‥‥‥‥‥‥ Alcohol and Attention‥‥‥‥‥‥‥‥‥‥‥‥‥‥‥‥‥‥‥‥‥ What would you do?‥‥‥‥‥‥‥‥‥‥‥‥‥‥‥‥‥‥‥‥‥‥‥‥‥ Drugs‥‥‥‥‥‥‥‥‥‥‥‥‥‥‥‥‥‥‥‥‥‥‥‥‥‥‥‥‥‥‥‥‥‥‥‥‥ What is a drug?‥‥‥‥‥‥‥‥‥‥‥‥‥‥‥‥‥‥‥‥‥‥‥‥‥‥‥ How are drugs classified?‥‥‥‥‥‥‥‥‥‥‥‥‥‥‥‥‥‥‥‥‥ Legal drugs‥‥‥‥‥‥‥‥‥‥‥‥‥‥‥‥‥‥‥‥‥‥‥‥‥‥‥‥‥‥ Illegal drugs‥‥‥‥‥‥‥‥‥‥‥‥‥‥‥‥‥‥‥‥‥‥‥‥‥‥‥‥‥ Central nervous system‥‥‥‥‥‥‥‥‥‥‥‥‥‥‥‥‥‥‥‥‥‥‥ How do drugs affect people?‥‥‥‥‥‥‥‥‥‥‥‥‥‥‥‥ Some factors to consider include:‥‥‥‥‥‥‥‥‥‥‥‥‥ Legal Drugs – Prescription and Over the Counter‥‥‥‥‥‥‥‥‥‥‥‥‥‥‥‥‥‥‥‥‥‥‥‥‥ Key Points‥‥‥‥‥‥‥‥‥‥‥‥‥‥‥‥‥‥‥‥‥‥‥‥‥‥‥‥‥‥‥ Conclusion‥‥‥‥‥‥‥‥‥‥‥‥‥‥‥‥‥‥‥‥‥‥‥‥‥‥‥‥‥‥ Questions‥‥‥‥‥‥‥‥‥‥‥‥‥‥‥‥‥‥‥‥‥‥‥‥‥‥‥‥‥‥‥‥‥‥‥‥ Answers‥‥‥‥‥‥‥‥‥‥‥‥‥‥‥‥‥‥‥‥‥‥‥‥‥‥‥‥‥‥‥‥‥‥‥‥‥ 4.21 4.21 4.22 4.22 4.22 4.23 4.23 4.23 4.23 4.24 4.24 4.24 4.25 4.25 4.26 4.26 4.26 4.26 4.27 4.27 4.27 4.27 4.27 4.27 4.28 4.28 4.29 4.29 4.30 4.31 4.32 SUB-MODULE 05 PHYSICAL ENVIRONMENT Knowledge Requirements‥‥‥‥‥‥‥‥‥‥‥‥‥‥‥‥‥‥‥‥‥‥‥ Introduction‥‥‥‥‥‥‥‥‥‥‥‥‥‥‥‥‥‥‥‥‥‥‥‥‥‥‥‥‥‥‥‥‥‥ Noise and Fumes‥‥‥‥‥‥‥‥‥‥‥‥‥‥‥‥‥‥‥‥‥‥‥‥‥‥‥‥‥‥ Noise‥‥‥‥‥‥‥‥‥‥‥‥‥‥‥‥‥‥‥‥‥‥‥‥‥‥‥‥‥‥‥‥‥‥‥‥‥ Protecting Your Hearing‥‥‥‥‥‥‥‥‥‥‥‥‥‥‥‥‥‥‥‥‥‥ Know your work environment.‥‥‥‥‥‥‥‥‥‥‥‥‥‥‥ Select Appropriate Hearing Protection Devices‥ Fumes, Chemicals, Toxic Metals and Solvents‥‥‥‥‥ Gasoline Engine Exhaust (Carbon Monoxide)‥‥ 5.1 5.2 5.2 5.2 5.2 5.2 5.2 5.3 5.3 xi CONTENTS Kerosene Based Fuel‥‥‥‥‥‥‥‥‥‥‥‥‥‥‥‥‥‥‥‥‥‥‥ Kerosene based fuels include jet and diesel fuels.‥‥‥‥‥‥‥‥‥‥‥‥‥‥‥‥‥‥‥‥‥‥‥‥‥‥‥‥ Toxic Metals‥‥‥‥‥‥‥‥‥‥‥‥‥‥‥‥‥‥‥‥‥‥‥‥‥‥‥‥‥‥‥ Cadmium‥‥‥‥‥‥‥‥‥‥‥‥‥‥‥‥‥‥‥‥‥‥‥‥‥‥‥‥‥‥‥ Beryllium‥‥‥‥‥‥‥‥‥‥‥‥‥‥‥‥‥‥‥‥‥‥‥‥‥‥‥‥‥‥‥‥ Preventative actions for toxic metal exposure‥‥‥‥ Paints and Primers‥‥‥‥‥‥‥‥‥‥‥‥‥‥‥‥‥‥‥‥‥‥‥‥‥‥‥ Hydraulic Fluids‥‥‥‥‥‥‥‥‥‥‥‥‥‥‥‥‥‥‥‥‥‥‥‥‥‥‥‥ Solvents‥‥‥‥‥‥‥‥‥‥‥‥‥‥‥‥‥‥‥‥‥‥‥‥‥‥‥‥‥‥‥‥‥‥‥ What are solvents?‥‥‥‥‥‥‥‥‥‥‥‥‥‥‥‥‥‥‥‥‥‥‥‥ Skin Contact‥‥‥‥‥‥‥‥‥‥‥‥‥‥‥‥‥‥‥‥‥‥‥‥‥‥‥‥‥ Eyes and Respiratory System‥‥‥‥‥‥‥‥‥‥‥‥‥‥‥‥ Preventative actions for toxic metal exposure‥‥‥‥ Preventative actions for solvent exposure‥‥‥‥‥‥‥ Illumination‥‥‥‥‥‥‥‥‥‥‥‥‥‥‥‥‥‥‥‥‥‥‥‥‥‥‥‥‥‥‥‥‥‥ Climate and Temperature‥‥‥‥‥‥‥‥‥‥‥‥‥‥‥‥‥‥‥‥‥‥‥ The Body’s Response to Heat‥‥‥‥‥‥‥‥‥‥‥‥‥‥‥‥‥‥ Heat Stress and Major Disorders‥‥‥‥‥‥‥‥‥‥‥‥‥ Working in the Cold‥‥‥‥‥‥‥‥‥‥‥‥‥‥‥‥‥‥‥‥‥‥‥‥‥ Know Your Temperatures‥‥‥‥‥‥‥‥‥‥‥‥‥‥‥‥‥‥‥ Preventing Cold Related Disorders‥‥‥‥‥‥‥‥‥‥‥ Motion and Vibration‥‥‥‥‥‥‥‥‥‥‥‥‥‥‥‥‥‥‥‥‥‥‥‥‥‥‥ Working Environment‥‥‥‥‥‥‥‥‥‥‥‥‥‥‥‥‥‥‥‥‥‥‥‥‥‥ What is a Safety Culture?‥‥‥‥‥‥‥‥‥‥‥‥‥‥‥‥‥‥‥‥‥ Building a safety culture‥‥‥‥‥‥‥‥‥‥‥‥‥‥‥‥‥‥‥‥ Summary‥‥‥‥‥‥‥‥‥‥‥‥‥‥‥‥‥‥‥‥‥‥‥‥‥‥‥‥‥‥‥‥‥‥ Questions‥‥‥‥‥‥‥‥‥‥‥‥‥‥‥‥‥‥‥‥‥‥‥‥‥‥‥‥‥‥‥‥‥‥‥‥ Answers‥‥‥‥‥‥‥‥‥‥‥‥‥‥‥‥‥‥‥‥‥‥‥‥‥‥‥‥‥‥‥‥‥‥‥‥‥ 5.3 5.3 5.4 5.4 5.4 5.4 5.4 5.5 5.5 5.5 5.6 5.6 5.6 5.6 5.7 5.8 5.9 5.9 5.10 5.11 5.11 5.13 5.13 5.13 5.13 5.14 5.15 5.16 SUB-MODULE 06 TASKS Knowledge Requirements‥‥‥‥‥‥‥‥‥‥‥‥‥‥‥‥‥‥‥‥‥‥‥ 6.1 Introduction‥‥‥‥‥‥‥‥‥‥‥‥‥‥‥‥‥‥‥‥‥‥‥‥‥‥‥‥‥‥‥‥‥‥ 6.2 Planning‥‥‥‥‥‥‥‥‥‥‥‥‥‥‥‥‥‥‥‥‥‥‥‥‥‥‥‥‥‥‥‥‥‥‥‥‥ 6.2 Planning of tasks, equipment and spares‥‥‥‥‥‥‥‥‥ 6.2 Lack of resources … not a problem‥‥‥‥‥‥‥‥‥‥‥‥‥‥ 6.2 What would you do?‥‥‥‥‥‥‥‥‥‥‥‥‥‥‥‥‥‥‥‥‥‥‥ 6.3 Is this your preferred decision?‥‥‥‥‥‥‥‥‥‥‥‥‥‥‥ 6.3 Key Points‥‥‥‥‥‥‥‥‥‥‥‥‥‥‥‥‥‥‥‥‥‥‥‥‥‥‥‥‥‥‥ 6.3 Physical Work‥‥‥‥‥‥‥‥‥‥‥‥‥‥‥‥‥‥‥‥‥‥‥‥‥‥‥‥‥‥‥‥‥ 6.4 Repetitive Tasks‥‥‥‥‥‥‥‥‥‥‥‥‥‥‥‥‥‥‥‥‥‥‥‥‥‥‥‥‥‥‥ 6.5 Visual Inspection‥‥‥‥‥‥‥‥‥‥‥‥‥‥‥‥‥‥‥‥‥‥‥‥‥‥‥‥‥‥ 6.5 Complex Systems‥‥‥‥‥‥‥‥‥‥‥‥‥‥‥‥‥‥‥‥‥‥‥‥‥‥‥‥‥‥ 6.6 Questions‥‥‥‥‥‥‥‥‥‥‥‥‥‥‥‥‥‥‥‥‥‥‥‥‥‥‥‥‥‥‥‥‥‥‥‥ 6.9 Answers‥‥‥‥‥‥‥‥‥‥‥‥‥‥‥‥‥‥‥‥‥‥‥‥‥‥‥‥‥‥‥‥‥‥‥‥‥ 6.10 xii SUB-MODULE 07 COMMUNICATION Knowledge Requirements‥‥‥‥‥‥‥‥‥‥‥‥‥‥‥‥‥‥‥‥‥‥‥ Introduction‥‥‥‥‥‥‥‥‥‥‥‥‥‥‥‥‥‥‥‥‥‥‥‥‥‥‥‥‥‥‥‥‥‥ What is Communication‥‥‥‥‥‥‥‥‥‥‥‥‥‥‥‥‥‥‥‥‥‥ Communication channels‥‥‥‥‥‥‥‥‥‥‥‥‥‥‥‥‥‥‥‥‥ Speech‥‥‥‥‥‥‥‥‥‥‥‥‥‥‥‥‥‥‥‥‥‥‥‥‥‥‥‥‥‥‥‥‥‥ Documents‥‥‥‥‥‥‥‥‥‥‥‥‥‥‥‥‥‥‥‥‥‥‥‥‥‥‥‥‥‥ Non verbal communication‥‥‥‥‥‥‥‥‥‥‥‥‥‥‥‥‥‥ Physical cues‥‥‥‥‥‥‥‥‥‥‥‥‥‥‥‥‥‥‥‥‥‥‥‥‥‥‥‥‥ Within and Between Teams‥‥‥‥‥‥‥‥‥‥‥‥‥‥‥‥‥‥‥‥‥‥ Shift Handover‥‥‥‥‥‥‥‥‥‥‥‥‥‥‥‥‥‥‥‥‥‥‥‥‥‥‥‥‥‥‥‥ Concepts‥‥‥‥‥‥‥‥‥‥‥‥‥‥‥‥‥‥‥‥‥‥‥‥‥‥‥‥‥‥‥‥‥‥ Aids to Effective Communication at Shift Handover‥‥‥‥‥‥‥‥‥‥‥‥‥‥‥‥‥‥‥‥‥‥‥‥‥‥‥‥‥ Barriers To Effective Communication at Shift Handover‥‥‥‥‥‥‥‥‥‥‥‥‥‥‥‥‥‥‥‥‥‥‥‥‥‥‥‥‥ Shift Handover Meetings‥‥‥‥‥‥‥‥‥‥‥‥‥‥‥‥‥‥‥‥‥ Walkthroughs‥‥‥‥‥‥‥‥‥‥‥‥‥‥‥‥‥‥‥‥‥‥‥‥‥‥‥‥‥‥ Task Handover‥‥‥‥‥‥‥‥‥‥‥‥‥‥‥‥‥‥‥‥‥‥‥‥‥‥‥‥‥‥ Handing over a task drectly to another person‥‥‥‥‥‥‥‥‥‥‥‥‥‥‥‥‥‥‥‥‥‥‥‥‥‥‥‥ Handing over a task for somebody to complete at a later stage‥‥‥‥‥‥‥‥‥‥‥‥‥‥‥‥‥‥‥‥ An accident related to a shift handover‥‥‥‥‥‥‥‥‥‥‥ Four ways to improve shift handover‥‥‥‥‥‥‥‥‥‥‥‥ Effective and ineffective handovers‥‥‥‥‥‥‥‥‥‥‥‥‥‥ Four types of shift handovers‥‥‥‥‥‥‥‥‥‥‥‥‥‥‥‥ Work Logging and Recording‥‥‥‥‥‥‥‥‥‥‥‥‥‥‥‥‥‥‥‥ Scheduled Task Cards‥‥‥‥‥‥‥‥‥‥‥‥‥‥‥‥‥‥‥‥‥‥‥‥ Non-scheduled Tasks ‥‥‥‥‥‥‥‥‥‥‥‥‥‥‥‥‥‥‥‥‥‥‥‥ Keeping Up-to-Date, Currency‥‥‥‥‥‥‥‥‥‥‥‥‥‥‥‥‥‥‥ Dissemination of Information‥‥‥‥‥‥‥‥‥‥‥‥‥‥‥‥‥‥‥‥ Tips for improving communication and avoiding errors ‥‥‥‥‥‥‥‥‥‥‥‥‥‥‥‥‥‥‥‥‥‥‥‥‥ Conclusion – What you need to know‥‥‥‥‥‥‥‥‥‥‥ Questions‥‥‥‥‥‥‥‥‥‥‥‥‥‥‥‥‥‥‥‥‥‥‥‥‥‥‥‥‥‥‥‥‥‥‥‥ Answers‥‥‥‥‥‥‥‥‥‥‥‥‥‥‥‥‥‥‥‥‥‥‥‥‥‥‥‥‥‥‥‥‥‥‥‥‥ 7.1 7.2 7.2 7.2 7.2 7.3 7.3 7.3 7.4 7.5 7.5 7.5 7.6 7.6 7.7 7.7 7.8 7.8 7.8 7.9 7.9 7.9 7.10 7.10 7.11 7.11 7.12 7.12 7.12 7.13 7.14 SUB-MODULE 08 HUMAN ERROR Knowledge Requirements‥‥‥‥‥‥‥‥‥‥‥‥‥‥‥‥‥‥‥‥‥‥‥ 8.1 Introduction‥‥‥‥‥‥‥‥‥‥‥‥‥‥‥‥‥‥‥‥‥‥‥‥‥‥‥‥‥‥‥‥‥‥ 8.2 Error Models and Theories‥‥‥‥‥‥‥‥‥‥‥‥‥‥‥‥‥‥‥‥‥‥‥ 8.3 The PEAR Model‥‥‥‥‥‥‥‥‥‥‥‥‥‥‥‥‥‥‥‥‥‥‥‥‥‥‥ 8.3 The Dirty Dozen‥‥‥‥‥‥‥‥‥‥‥‥‥‥‥‥‥‥‥‥‥‥‥‥‥‥‥‥ 8.4 Psychological Stressors‥‥‥‥‥‥‥‥‥‥‥‥‥‥‥‥‥‥‥ 8.13 Module 09 - Human Factors CONTENTS Physiological Stressors‥‥‥‥‥‥‥‥‥‥‥‥‥‥‥‥‥‥‥ Additional Models/Theories‥‥‥‥‥‥‥‥‥‥‥‥‥‥‥‥‥‥‥ HFACS-ME Model‥‥‥‥‥‥‥‥‥‥‥‥‥‥‥‥‥‥‥‥‥‥‥ SHEL Model‥‥‥‥‥‥‥‥‥‥‥‥‥‥‥‥‥‥‥‥‥‥‥‥‥‥‥‥ Types of Errors in Maintenance Tasks‥‥‥‥‥‥‥‥‥‥‥‥‥ Unintended Errors‥‥‥‥‥‥‥‥‥‥‥‥‥‥‥‥‥‥‥‥‥‥‥‥‥‥‥ Slips‥‥‥‥‥‥‥‥‥‥‥‥‥‥‥‥‥‥‥‥‥‥‥‥‥‥‥‥‥‥‥‥‥‥‥‥ Lapses‥‥‥‥‥‥‥‥‥‥‥‥‥‥‥‥‥‥‥‥‥‥‥‥‥‥‥‥‥‥‥‥‥‥ Intended Errors‥‥‥‥‥‥‥‥‥‥‥‥‥‥‥‥‥‥‥‥‥‥‥‥‥‥‥‥‥ Mistakes‥‥‥‥‥‥‥‥‥‥‥‥‥‥‥‥‥‥‥‥‥‥‥‥‥‥‥‥‥‥‥‥ Rule Based Mistakes‥‥‥‥‥‥‥‥‥‥‥‥‥‥‥‥‥‥‥‥ Knowledge Based Mistakes‥‥‥‥‥‥‥‥‥‥‥‥‥‥‥ Violations‥‥‥‥‥‥‥‥‥‥‥‥‥‥‥‥‥‥‥‥‥‥‥‥‥‥‥‥‥‥‥ Routine Violations‥‥‥‥‥‥‥‥‥‥‥‥‥‥‥‥‥‥‥‥‥‥ Exceptional Violations‥‥‥‥‥‥‥‥‥‥‥‥‥‥‥‥‥‥‥ Implications of Errors (i.e. accidents)‥‥‥‥‥‥‥‥‥‥‥‥‥‥‥ Avoiding and Managing Errors‥‥‥‥‥‥‥‥‥‥‥‥‥‥‥‥‥‥‥ Error Management Systems (EMS) ‥‥‥‥‥‥‥‥‥‥‥‥‥‥‥ Maintenance Error Decision Aid (MEDA)‥‥‥‥‥‥‥‥‥ The MEDA Philosophy‥‥‥‥‥‥‥‥‥‥‥‥‥‥‥‥‥‥‥‥ The MEDA Process‥‥‥‥‥‥‥‥‥‥‥‥‥‥‥‥‥‥‥‥‥‥‥ Event ‥‥‥‥‥‥‥‥‥‥‥‥‥‥‥‥‥‥‥‥‥‥‥‥‥‥‥‥‥‥‥‥ Decision‥‥‥‥‥‥‥‥‥‥‥‥‥‥‥‥‥‥‥‥‥‥‥‥‥‥‥‥‥‥ Investigation‥‥‥‥‥‥‥‥‥‥‥‥‥‥‥‥‥‥‥‥‥‥‥‥‥‥‥ Prevention Strategies‥‥‥‥‥‥‥‥‥‥‥‥‥‥‥‥‥‥‥‥ Feedback ‥‥‥‥‥‥‥‥‥‥‥‥‥‥‥‥‥‥‥‥‥‥‥‥‥‥‥‥‥ Management Resolve‥‥‥‥‥‥‥‥‥‥‥‥‥‥‥‥‥‥‥‥‥‥ Implementing MEDA‥‥‥‥‥‥‥‥‥‥‥‥‥‥‥‥‥‥‥‥‥ The benefits of MEDA‥‥‥‥‥‥‥‥‥‥‥‥‥‥‥‥‥‥‥‥‥ Conclusion‥‥‥‥‥‥‥‥‥‥‥‥‥‥‥‥‥‥‥‥‥‥‥‥‥‥‥‥‥‥‥‥‥‥‥ Questions‥‥‥‥‥‥‥‥‥‥‥‥‥‥‥‥‥‥‥‥‥‥‥‥‥‥‥‥‥‥‥‥‥‥‥‥ Answers‥‥‥‥‥‥‥‥‥‥‥‥‥‥‥‥‥‥‥‥‥‥‥‥‥‥‥‥‥‥‥‥‥‥‥‥‥ 8.13 8.16 8.16 8.16 8.16 8.16 8.16 8.17 8.17 8.17 8.17 8.17 8.17 8.17 8.18 8.19 8.20 8.21 8.21 8.21 8.22 8.23 8.23 8.23 8.23 8.23 8.23 8.23 8.24 8.24 8.31 8.32 Possible work related accidents or emergencies‥‥‥‥‥ Breathing Emergencies‥‥‥‥‥‥‥‥‥‥‥‥‥‥‥‥‥‥‥‥‥ Rescue Breathing and CPR‥‥‥‥‥‥‥‥‥‥‥‥‥‥‥‥‥ Chemical Burns‥‥‥‥‥‥‥‥‥‥‥‥‥‥‥‥‥‥‥‥‥‥‥‥‥‥ Head Injury ‥‥‥‥‥‥‥‥‥‥‥‥‥‥‥‥‥‥‥‥‥‥‥‥‥‥‥‥‥ Hypothermia‥‥‥‥‥‥‥‥‥‥‥‥‥‥‥‥‥‥‥‥‥‥‥‥‥‥‥‥‥ Spinal Injury‥‥‥‥‥‥‥‥‥‥‥‥‥‥‥‥‥‥‥‥‥‥‥‥‥‥‥‥‥ Strains, Sprains and Broken Bones‥‥‥‥‥‥‥‥‥‥‥ Splintering‥‥‥‥‥‥‥‥‥‥‥‥‥‥‥‥‥‥‥‥‥‥‥‥‥‥‥‥‥‥‥ Conclusion‥‥‥‥‥‥‥‥‥‥‥‥‥‥‥‥‥‥‥‥‥‥‥‥‥‥‥‥‥‥‥‥‥‥‥ Other resources‥‥‥‥‥‥‥‥‥‥‥‥‥‥‥‥‥‥‥‥‥‥‥‥‥‥‥‥‥ First Aid‥‥‥‥‥‥‥‥‥‥‥‥‥‥‥‥‥‥‥‥‥‥‥‥‥‥‥‥‥‥‥‥ Developing a Job Hazard Analysis for Risky Tasks‥‥‥‥‥‥‥‥‥‥‥‥‥‥‥‥‥‥‥‥‥‥‥‥‥‥‥ Other Helpful Sites‥‥‥‥‥‥‥‥‥‥‥‥‥‥‥‥‥‥‥‥‥‥‥‥ Questions‥‥‥‥‥‥‥‥‥‥‥‥‥‥‥‥‥‥‥‥‥‥‥‥‥‥‥‥‥‥‥‥‥‥‥‥ Answers‥‥‥‥‥‥‥‥‥‥‥‥‥‥‥‥‥‥‥‥‥‥‥‥‥‥‥‥‥‥‥‥‥‥‥‥‥ 9.9 9.9 9.9 9.9 9.10 9.10 9.11 9.11 9.12 9.12 9.12 9.12 Acronym Index‥‥‥‥‥‥‥‥‥‥‥‥‥‥‥‥‥‥‥‥‥‥‥‥‥‥‥‥‥‥‥‥ Index‥‥‥‥‥‥‥‥‥‥‥‥‥‥‥‥‥‥‥‥‥‥‥‥‥‥‥‥‥‥‥‥‥‥‥‥‥‥‥‥ A.1 I.1 9.12 9.12 9.13 9.14 SUB-MODULE 09 HAZARDS IN THE WORKPLACE Knowledge Requirements‥‥‥‥‥‥‥‥‥‥‥‥‥‥‥‥‥‥‥‥‥‥‥ Introduction‥‥‥‥‥‥‥‥‥‥‥‥‥‥‥‥‥‥‥‥‥‥‥‥‥‥‥‥‥‥‥‥‥‥ Recognizing and avoiding hazards‥‥‥‥‥‥‥‥‥‥‥‥‥‥‥‥‥ Identifying workplace hazards‥‥‥‥‥‥‥‥‥‥‥‥‥‥‥‥‥ Dealing with Emergencies‥‥‥‥‥‥‥‥‥‥‥‥‥‥‥‥‥‥‥‥‥‥‥ What is an emergency? ‥‥‥‥‥‥‥‥‥‥‥‥‥‥‥‥‥‥‥‥‥‥‥ Preparing for Emergencies‥‥‥‥‥‥‥‥‥‥‥‥‥‥‥‥‥‥‥‥ Planning Ahead‥‥‥‥‥‥‥‥‥‥‥‥‥‥‥‥‥‥‥‥‥‥‥‥‥‥ Attitude of Safety‥‥‥‥‥‥‥‥‥‥‥‥‥‥‥‥‥‥‥‥‥‥‥‥‥ The Right Supplies‥‥‥‥‥‥‥‥‥‥‥‥‥‥‥‥‥‥‥‥‥‥‥‥ Emergency Contacts and Communications‥‥‥‥‥ Responding to an Emergency‥‥‥‥‥‥‥‥‥‥‥‥‥‥‥‥‥‥ Module 09 - Human Factors 9.1 9.2 9.3 9.4 9.7 9.7 9.7 9.7 9.7 9.7 9.7 9.8 xiii xiv Module 09 - Human Factors GENERAL PART-66 SYLLABUS LEVELS A B1 B2 CERTIFICATION CATEGORY ¦ Sub-Module 01 GENERAL Knowledge Requirements 9.1 - General The need to take human factors into account; Incidents attributable to human factors/human error; Murphy's Law. Level 1 A familiarization with the principal elements of the subject. Objectives: (a) The applicant should be familiar with the basic elements of the subject. (b) The applicant should be able to give a simple description of the whole subject, using common words and examples. (c) The applicant should be able to use typical terms. Module 09 - Human Factors 1 2 2 Level 2 A general knowledge of the theoretical and practical aspects of the subject and an ability to apply that knowledge. Objectives: (a) The applicant should be able to understand the theoretical fundamentals of the subject. (b) The applicant should be able to give a general description of the subject using, as appropriate, typical examples. (c) The applicant should be able to use mathematical formula in conjunction with physical laws describing the subject. (d) The applicant should be able to read and understand sketches, drawings and schematics describing the subject. (e) The applicant should be able to apply his knowledge in a practical manner using detailed procedures. 1.1 GENERAL Why are human conditions such as fatigue, complacency, and stress, so important in aviation maintenance? These conditions, along with many others, are called human factors. Human factors directly cause or contribute to many aviation accidents. It is universally agreed that at least 80 percent of maintenance related incidents involve human factors. If they are not prevented, and their causes detected, they can cause injuries, wasted time, and even accidents. (Figure 1.1) THE NEED TO TAKE HUMAN FACTORS INTO ACCOUNT Aviation safety relies heavily on maintenance. When it is not done correctly, it contributes to a significant proportion of accidents and incidents. Some examples of maintenance errors may include; parts installed incorrectly, missing parts, or necessary checks not being performed. In comparison to many other threats to aviation safety, the mistakes of an Aviation Maintenance Technician (AMT) can be more difficult to detect. Often times, these mistakes are present but not visible and have the potential to remain latent, affecting the safe operation of aircraft for long periods of time. AMTs are confronted with a set of human factors unique within aviation. Often times, AMTs are working in Figure 1.1 – The above human factors and how they affect people are very important. Awareness of their influence can help control possible accidents the evening or early morning hours, in confined spaces, on platforms that are up high, or in a variety of adverse temperature/humidity conditions. The work can be physically strenuous, yet also requiring a high degree of attention to detail. (Figure 1.2) Figure 1.2 – Aviation maintenance technicians have many distractions and must focus on detail 1.2 Module 09 - Human Factors GENERAL Figure 1.3 – Factors that affect human performance for AMTs Because of the nature of maintenance tasks, AMTs commonly spend more time preparing for a task than actually carrying it out. Proper documentation of all maintenance work is a key element, and AMTs also typically spend as much time updating maintenance logs as they do performing the work. Human factors and how they affect people are very important to aviation maintenance. Such awareness can lead to improved quality, an environment that ensures continuing worker and aircraft safety, and a more involved and responsible work force. More specifically, the reduction of even minor errors can provide measurable benefits including cost reductions, fewer missed deadlines, reduction in work related injuries, reduction of warranty claims, and reduction in more significant events that can be traced back to maintenance error. Module 09 - Human Factors It is apparent that anticipated or abnormal medical conditions inf luence the AMTs work. Reduction in vision is a signpost of aging that is anticipated in all AMTs over the age of 50 years. It compromises the visual inspection of aircraft. Obesity is an abnormal medical condition that leads to multiple metabolic changes. It produces behaviors described by the Dirty Dozen of human factors. These consequences from normal aging or abnormal medical conditions are classified as Latent Medical or Environmental Conditions (LMEC). Within this book, the many aspects of human factors are discussed in relation to aviation maintenance. (Figure 1.3) The most common of which are introduced along with ways to mitigate the risk to stop them from developing into a problem. 1.3 THE PEAR MODEL OF HUMAN FACTORS IN MAINTENANCE Human factors can be divided into four main topic areas using the memory prompt PEAR. Application of the mnemonic ‘PEAR’ makes recognition of Human Factors (HF) even easier. It prompts recall of the four important considerations for HF programs: People who do the job; Environment in which they work; Actions they perform; Resources necessary to complete the job. The lists within each element are not exhaustive, but help to guide people on the human factor influences that should be considered. People PEAR was developed by Dr. Michael Maddox and Dr. Bill Johnson, specifically with maintenance in mind, as an easy way for aviation maintenance personnel to identify human factors and relate to tasks and conditions within the maintenance environment. PEAR has been used for over a decade by some JAR/ EASA 145-approved organisations and is included by the US Federal Aviation Administration (FAA) in their Maintenance Human Factors training package. Environment Actions Resources P stands for People (the humans in the system), with all our capabilities and limitations. It includes senses such as vision and hearing; physical characteristics such as strength and reach; as well as capabilities such as memory, communication styles, decision making, supervision and teamwork skills (leadership/followership etc.). People relates to the suitability (physical, cognitive and social) of the selected personnel for a particular task. Suitability not only covers technical training but also human factors considerations such as fatigue, stress and motivations. It guides the review of the competency, supervision abilities, briefing needs, leadership skills and requirements of individuals against the task demands. People DOING THINKING INTERACTING Physical capabilities Knowledge Team structure Sensory Capabilities Experience Role definition Health Attitude Leadership Training Motivation Followership Current Confidence Supervision skills/needs Competent Workload Interpersonal relationships Authorized Fatigue Communication Briefed Stress Conflicts E stands for the Environment in which the work is done, not just the physical environment, but also the organization itself. The physical environment includes lighting, temperature, noise level and time of day. The organizational environment covers issues such as supervision (quality and ratios), pressures (time, commercial and production etc.), organization and safety culture and existing organizational norms and how these will affect individual and team performance and the potential for error. The organizational environment also covers the leadership shown and the effectiveness of management in supporting positive safety behaviors. 1.4 Module 09 - Human Factors ORGANIZATIONAL Weather Management style Location (inside/outside) Leadership Workspace Staffing levels Lighting Size/complexity Noise Priorities Distractions Pressures Housekeeping Morale Hazards Norms Shift (day/night/late) Culture GENERAL Environment PHYSICAL A represents the Actions people perform. Actions list the requirements of a job to help to identify any specific areas that might increase the risk of error, such as ambiguous information, or complex tasks that need specialist skills and knowledge. Actions Getting Information Communication requirements Preparation Task management Briefing/debriefing Supervision requirements Steps/sequence of activity Inspection requirements Application of Knowledge Documentation Application of skill Certification requirements The list of actions is aligned with a Job Task Analysis (JTA) process which is the standard human factors approach to identifying the knowledge, skills and attitudes necessary to perform each task in a given job. The JTA also helps identify what instructions, preparation and task management are necessary. This may include Accessing / finding task specific information required Preparation and briefing requirements Identifying procedures to be followed Are those procedures clear and easy to follow? Task complexity and application of skill and knowledge Communication requirements (headsets required?) The level of supervision and inspection required (is a dual inspection needed?) The certification and documentation, including the complexity or user-friendly nature of the aircraft maintenance documentation. R is for the Resources necessary to perform the work. Resources are the broadest component of PEAR. They can be defined as anything that the maintenance technician needs to get the job done. Resources details both the tangible items required and available, such as personnel, spares, technical manuals, tooling, and personnel protective equipment (PPE), as well as less tangible (but equally important) elements such as time and training availability. Resources Module 09 - Human Factors Procedures/workcards Technical manuals Personnel Test equipment Tools Computers/software Paperwork/signoffs Ground handling equipment Workstands and lifts Fixtures Materials Task lighting Training Quality system Personal Protective Equipment Interpersonal relationships Confidence Supervision skills/needs Competence Workload Interpersonal relationships 1.5 Time and personnel should be the f irst resources considered, as they are critical to the planning process of any job. An important resources element is focusing on identifying the areas where resources are deficient including: Design (work stands, tools etc.) Application (e.g. available, accurate procedures) Where additional resources (time, personnel, training, lighting, PPE and consumables) are required. PEAR APPLIED TO MAINTENANCE People: The human and the interactions between people The part of PEAR dealing with interactions between humans is particularly important in maintenance. Included are normal human capabilities and limitations in this part; the unaided human eye is still the main tool for inspections, yet the limitations of our vision system sometimes lead to defects being missed. We rely on short term memory each time we have to pay attention to a problem for more than a few seconds, yet the limits of our memory help explain why distractions and interruptions can be so dangerous. Good decision making is an important safety net in aviation, yet we are more likely to make poor decisions when under time pressure or stress. A ‘can do’ attitude is normally a positive characteristic, but in maintenance, if we attempt to operate outside our performance limitations it can lead to danger if not tempered by appropriate caution. Environment: Physical and organizational The maintenance environment presents numerous human factors challenges, including the need to work outside, high noise levels, temperature extremes, and at times poor lighting. All these conditions can increase the probability of error. For example, a three engine aircraft lost oil from all engines after maintenance technicians on night shift fitted magnetic chip detectors without the necessary O-rings. The work was performed outside, using the headlights of a tug for illumination. Furthermore, the technicians had no direct view of the task, and fitted each chip detector by feel, reaching inside the oil service door on each engine. In addition to the physical environment, there is the organizational environment surrounding maintenance. Maintenance tasks are often performed under time pressure. Time pressure is a particular threat when technicians are not used to handling it, and allow it 1.6 to have undue inf luence on their decision making. Other aspects of the organizational environment are management style, organizational culture and workplace ‘norms’ – the unwritten, informal work practices that members of the organization follow. Action: Procedures, paperwork and poor design The actions component of PEAR includes all of the hands on requirements needed to complete a task; from gathering information on tasks, identifying approved data and procedures, the physical and mental demands of the tasks, to finalizing and certifying a job complete. The FA A has estimated that airline maintenance personnel spend between 25 and 40 percent of their time dealing with paperwork. In airlines, technicians frequently deal with maintenance documentation that is difficult to interpret, or that describes procedures in ways that appear to be out of touch with current maintenance practices. In General Aviation, the problem may be that approved documentation for older aircraft is simply not available, or is hard to obtain. Many AMTs use “black books”, personal sources of unapproved technical data that may or may not be up to date. A problem faced by AMTs is a conflict between following procedures and the pressure to “get the job done”. An awareness of human factors associated with the actions required to complete a job by people at all levels of the organization can help to identify areas where the formal procedures can be approved. An accurate knowledge of task demands will help to identify informal work practices developed to meet these demands that need to be brought into alignment with formal procedures. Human factors are not just for technicians but also for managers and writers of technical documents. Module 09 - Human Factors disruptions. AMTs have to deal frequently with lack of resources or equipment. Knowing how to deal with the lack of resources requires judgement that takes years to build. THE ORGANIZATIONAL ENVIRONMENT How does your organization stack up? Positive organizational characteristics 1. There are sufficient staff appropriately licensed to cover the workload 2. The organization never encourages shortcuts or procedure violations 3. Management acts quickly to fix unsafe situations 4. Staff are encouraged to report errors and unsafe situations 5. The company has a ‘just culture’ policy. Incidents are investigated to identify why they occurred, not whom to blame 6. Staff receive human factors training Negative organizational characteristics 7. There is an extreme ‘can-do’ culture. Staff do whatever it takes to get a job done on time 8. Tasks are routinely performed according to ‘norms’ (informal work practices), rather than documented procedures. 9. Staff are often required to work excessive hours 10. Work is done differently when there is time pressure 11. Shortages of spares or equipment often lead to workarounds 12. There is rapid staff turnover, or many inexperienced personnel Yes Yes Yes Yes Yes No No No No No Yes No Yes Yes No No Yes Yes Yes Yes No No No No THE DIRTY DOZEN The Dirty Dozen refers to twelve of the most common human error preconditions or conditions that can act as precursors to accidents or incidents. These twelve elements influence people to make mistakes. The following case studies reference some of the Dirty Dozen factors that contributed to accidents: THE LIST 1. 2. 3. 4. 5. 6. Lack of communication Distraction Lack of resources Stress Complacency Lack of teamwork 7. 8. 9. 10. 11. 12. Pressure Lack of awareness Lack of knowledge Fatigue Lack of assertiveness Norms The Dirty Dozen Model will be discussed in depth in Chapter 8. Module 09 - Human Factors 1.7 GENERAL Resources: A lack of, or deficient Many maintenance incidents begin with a lack of necessary resources, such as time, spares, or specialized tools. Shortages will sometimes lead to work arounds or INCIDENTS RELATED TO HUMAN FACTORS The following are major incidents that have been directly attributed to human factors. CASE STUDY: ALOHA AIRLINES FLIGHT 243 Complacency is identified as one of the “Dirty Dozen” of aircraft maintenance human factors. (Discussed in full in sub module 9.8, along with other error models). The Dirty Dozen are 12 identified human factors that lead to maintenance errors. Complacency is at the top of this list and is the deadliest of the 12. This is demonstrated by the tragic Aloha Flight 243, which took place on April 28, 1988. Complacency with the state of aging aircraft was exposed as the cause of the accident and this event became the watershed accident that would bring much needed change. Aloha Airlines Flight 243 (AQ 243, AAH 243) was a scheduled Aloha Airlines f light between Hilo and Honolulu in Hawaii. On April 28, 1988, a Boeing 737.297 serving the f light suffered extensive damage after an explosive decompression in flight, but was able to land safely at Kahului Airport on Maui. There was one fatality, a member of the flight crew who was swept overboard from the airplane. Another 65 passengers and crew were injured. The safe landing of the aircraft despite the substantial damage inf licted by the decompression established Aloha Airlines Flight 243 as a significant event in the history of aviation, with far reaching effects on aviation safety policies and procedures. (Figure 1.4) The flight departed Hilo at 13:25 HST on 28 April 1988 with six crew members and 89 passengers, bound for Honolulu. No unusual occurrences were noticed during the pre departure inspection of the aircraft. The aircraft had previously completed three round trip flights from Honolulu to Hilo, Maui, and Kauai that day, all which were uneventful. Meteorological conditions were checked but no advisories for weather phenomenon occurred along the air route, per Airman’s meteorological information or significant meteorological information. The captain was an experienced pilot with 8 500 flight hours; 6 700 of those were in Boeing 737s. The first officer had significant experience flying 737s, having logged 3 500 of her total 8 000 flight hours in them. No unusual occurrences were reported during the takeoff and ascent. Around 13:48, as the aircraft reached its normal flight altitude of 24 000 feet (7 300 m) about 23 nautical miles (43 km) south southeast of Kahului, Maui, a small section on the left side of the roof ruptured with a “whooshing” sound. The captain felt the aircraft roll left and right, and the controls went Figure 1.4 – Aloha Airlines Flight 243 – A watershed moment in aviation maintenance history that brought about much needed change in aviation maintenance. It was recognized that complacency in the state of aging aircraft was the main contributing factor to this accident. 1.8 Module 09 - Human Factors The first officer was flying the plane at the time of the incident. After discovering the damage, the captain took over and steered the plane to the closest airport, on Maui Island. Thirteen minutes later, the crew performed an emergency landing on Kahului Airport’s Runway 2. Upon landing, the crew deployed the aircraft’s emergency evacuation slides and evacuated passengers from the aircraft quickly. In all, 65 people were reported injured, eight seriously. INVESTIGATION The main factor was the failure of the Aloha Airlines maintenance program to detect the presence of significant disbonding and fatigue damage. Contributing causes were the failure of Aloha Airlines management to supervise properly its maintenance force; the failure of the Federal Aviation Administration (FA A) to eva luate properly the A loha A irl ines maintenance program and to assess the airline’s inspection and quality control deficiencies; the failure of the FAA to require Airworthiness Directive 87.2108 inspection of all the lap joints proposed by Boeing Alert Service Bulletin SB 737.53A1039; and the lack of a complete terminating action (neither generated by Boeing nor required by the FAA) after the discovery of early production difficulties in the B-737 cold bond lap joint which resulted in low bond durability, corrosion, and a premature fatigue cracking. SAFETY RECOMMENDATIONS Investigators made 18 Safety Recommendations that were enacted FAA Provide specific guidance and proper engineering support to principal maintenance inspectors to evaluate modifications of airline maintenance programs and operations specifications, which propose segmenting major maintenance inspections. Module 09 - Human Factors Revise the regulation governing the certification of aviation maintenance technical schools and licensing of airframe and power plant mechanics to require that curriculum and testing requirements include modern aviation industry technology. Require formal certification and recurrent training of aviation maintenance inspectors performing nondestructive inspection functions. Formal training should include apprenticeship and periodic skill demonstration. Develop a continuing inspection program for those B-737 airplanes that have incorporated lap joint termination action (protruding head solid fasteners installed in the upper row of all lap splices) to detect any fatigue cracking that my develop in the middle or lower rows of fuselage lap joint fasteners holes (for both the inner and outer skin panels) or the adjacent tear strap fastener holes. Additionally, to define the types of inspections, inspection intervals, and corrective actions needed for continuing airworthiness. Develop a model program for a comprehensive corrosion control program to be included in each operator’s approved maintenance program. Issue an airworthiness directive for B737 airplanes equipped with carbon steel control cables to inspect the cables for evidence of corrosion and if there is evidence, to accomplish the actions set forth in Boeing Service letter 737-SL-76.2-A. Enhance stature and performance of the principal inspectors through; (1) formal management training and guidance, (2) Greater encouragement and backing by headquarters of efforts by principal inspectors to secure the implementation by carriers of levels of safety above the regulatory minimums, (3) Improve accountability for quality of the surveillance; (4) Additional headquarters assistance in standardizing surveillance activities. Discontinue classif ication of fuselage sk in as “malfunction evident” or “damage obvious” on supplemental structurally significant items in the damage obvious category for possible inclusion in the supplementary inspection program. Issue an air carrier operations bulletin for all air carrier f light training departments to review the accident scenario and reiterate the need to assess airplane airworthiness as stated in the operators manual before taking action that my cause further damage or breakup of a damaged airframe. 1.9 GENERAL loose. The first officer noticed pieces of grey insulation floating over the cabin. The door to the cockpit was gone so the captain could look behind him and see blue sky. The resulting explosive decompression tore off a large section of the roof, consisting of the entire top half of the aircraft skin extending from just behind the cockpit to the forewing area. Aloha Airlines Revise the maintenance program to recognize the high time high cycles nature of the fleet operations and initiate maintenance inspection and overhaul concepts based on realistic and acceptable calendar and flight cycle intervals. Initiate a corrosion prevention and control program designed to afford maximum protection from the effects of harsh operating environments (as defined by the airplane manufacturer.) Revise and upgrade the technical division manpower and organization to provide the necessary management, quality assurance, engineering, technical training and production personnel to maintain high level of airworthiness of the fleet. Assist member air carriers to establish maintenance depa r tment eng ineering ser v ices to eva luate maintenance practices including structural repair, compliance with air worthiness directives and service bulletins, performance of inspection and quality assurance sections, and overall effectiveness of continuing airworthiness programs. SOME OF “THE DIRTY DOZEN” HUMAN FACTORS SPECIFIC TO THIS ACCIDENT Complacency with the state of aging aircraft – Complacency Working under pressure – Pressure Inspections done at night – circadian rhy thm upset – Fatigue Inspectors suspended by safety harnesses – Lack of Resources Required to inspect 1 300 rivets – Pressure D o c u m e nt a t i o n c o m p l i c a t e d & s u b j e c t t o interpretation – Lack of Knowledge Engineering Dept was outsourced – Lack of Communication, Lack of Teamwork Hangar lighting designed for DC-3’s – Lack of Resources Lack of adequate manpower – Fatigue Lack of knowledge - just two hours of NDT training – Lack of Knowledge CASE STUDY: BRITISH AIRWAYS BAC-111 WINDSCREEN BLOWOUT The aircraft, captained by 42 year old, who had logged 11 050 flight hours, and copiloted by 39 year old, who had logged 7 500 flight hours, was a BAC One Eleven Series. The aircraft took off at 7:20am local time, with 81 passengers, four cabin crew and two f light crew. Copilot handled a routine takeoff, and relinquished control as the plane established itself in its climb. Both pilots subsequently released their shoulder harnesses, while the pilot loosened his lap belt as well. The plane had climbed to 17 300 feet (5 270 m) over Didcot, Oxfordshire. Suddenly, there was a loud bang, and the fuselage quickly filled with condensation. The left windscreen, on the captain’s side of the cockpit, had separated from the forward fuselage. The Captain was jerked out of his seat by the rushing air and forced head first out of the cockpit, his knees snagging onto the flight controls. The door to the flight deck was blown out onto the radio and navigation console, blocking the throttle control which caused the plane to continue gaining speed as 1.10 they descended, while papers and other debris in the passenger cabin began blowing towards the cockpit. On the flight deck, the flight attendant quickly latched his hands onto the captain’s belt; another flight attendant began to reassure passengers, secure loose objects, and take up emergency positions. The copilot eventually received clearance from air traffic control to land at Southampton. The aircraft had landed safely on Runway 02, where the passengers immediately disembarked from the front and rear stairs, and emergency crews retrieved the captain. INVESTIGATION Accident investigators found that a replacement windscreen had been installed 27 hours before the f light, and that the procedure had been approved by the shift maintenance manager. However, 84 of the 90 windscreen retention bolts were 0.026 inches (0.66 mm) too small in diameter, while the remaining six were 0.1 inches (2.5 mm) too short. (Figure 1.5) Module 09 - Human Factors Investigators found the British Airways Birmingham Airport shift maintenance manager responsible for installing the incorrect bolts during the windscreen replacement, and for failing to follow official British Airways’ policies. They also found fault with British Airways’ policies, which should have required testing or verification by another individual for this critical task. Finally, investigators found the local Birmingham Airport management responsible for not directly monitoring the shift maintenance manager’s working practices. SAFETY RECOMMENDATIONS Investigators made eight safety recommendations in the final accident report: British Airways Review their quality assurance system and encourage technicians to provide feedback. Review the need to introduce job descriptions and terms of reference for different grades Shift Maintenance Manager and above. Review their product sample procedure to achieve independent assessment of standa rds and to conduct an indepth audit into the work practices at Birmingham Airport. Civil Aviation Authority Examine the continued viability of self certification with regards to safety critical tasks on aircraft. Rev iew the pur pose and scope of the FOI 7 Supervisory Visit. Consider the need for the periodic training and testing of technicians. Recognize the need for the use of corrective glasses, if prescribed, in association with aircraft engineering tasks. Ensure that, prior to the issue of an air traffic control rating, a candidate shall undergo an approved course including training in both the theoretical and practical handling of emergency situations. SOME OF “THE DIRTY DOZEN” HUMAN FACTORS SPECIFIC TO THIS ACCIDENT There were staff shortages – Lack Of Resources Time pressures existed – Pressure/Fatigue All the errors occurred at night – Fatigue Shift or task handovers were involved – Lack of Communication They all involved supervisors doing long hands on tasks – Lack of Teamwork There was an element of a “can do” attitude – Complacency Interruptions occurred – Distraction There was some failure to use approved data or company procedures – Lack of Knowledge, Lack of Resources Manuals were confusing – Lack of Resources There was inadequate pre planning, equipment or spares – Lack of Resources Figure 1.5 – Incorrect windscreen retention bolts; (too small) led to the windshield blowout. Module 09 - Human Factors 1.11 GENERAL the bolts on a “like for like” basis without referencing the maintenance documentation. The air pressure difference between the cabin and the outside during the flight proved to be too much, leading to the failure of the windscreen. The incident also brought to attention a design flaw in the aircraft. Securing the windscreen from the outside of the aircraft put a greater pressure on the bolts than if they were secured from the inside. CASE STUDY: NOSE WHEEL JAMMED ON DASH-8 While preparing a Dash-8 aircraft to return to service after major repairs, maintenance technicians noticed that the nose gear was missing a cover plate designed to protect micro switches from dust and stone damage, no spare was available. To help the company meet a deadline, maintenance personnel decided to manufacture a substitute cover plate, without waiting to get engineering approval. The plate was only a protective cover, not a structural component, and this probably led them to believe that manufacturing a similar replacement part would not affect safety. The original plate was shaped to provide clearance between it and the micro switches and was secured using countersunk screws. Because of the limited manufacturing capability at this maintenance facility, the replacement cover was manufactured from a flat plate and spacers were used to provide similar clearance. The holes in the replacement plate were not drilled to accept countersunk screws and it was secured using washers and hexagonal head bolts. The bolt heads protruded beyond the normal position of the counter sunk screw heads. The difference was sufficient to cause the landing gear to jam in the up position during a test flight following the repairs. (Figure 1.6) A retraction test that might have detected the problem was successfully completed before the replacement plate was fitted. INVESTIGATION Positive gravity maneuvers and a touch and go landing failed to shake the nose gear free. The crew decided to land once all other traffic was clear and emergency services were in place. A landing was completed with the aircraft sliding to a stop on its main wheels and nose. The accident investigator noted that a culture of "getting the job done" existed in the company and there was a strong sense of loyalty and motivation among the maintenance staff. The report concluded, "Staff excelled themselves in order to meet deadlines. While this approach is laudable, research and investigation has shown that it can lead to incorrect practices if the appropriate balance is not found". As described in this example, an awareness of how the physical and organizational environment inf luences maintenance tasks is an essential part of human factors. If you can identify error producing conditions in your work environment, you will be better prepared to change those things you can change, and deal with those things that are beyond your control. SOME OF “THE DIRTY DOZEN” HUMAN FACTORS SPECIFIC TO THIS ACCIDENT Corporate culture – get the job done at all costs – Pressure Time saving short cuts – Pressure Lack of spare parts – Lack of Resources Retraction test done before replacement part fitted – Lack of Knowledge, Complacency Figure 1.6 – A retraction test done after the plate was fitted as opposed to prior, would have prevented damage from this accident 1.12 Module 09 - Human Factors Early on the morning of August 14, 2005, a Boeing 737.300 aircraft departed Cyprus for Prague via Athens. About five minutes after takeoff, at an altitude of 12 040 ft. and at a cabin pressure that corresponded to an altitude of 10 000 ft., an aural warning horn sounded. attendant was then seen to enter the cockpit and sit in the captain’s seat. At around 9:00am, the engines flamed out due to fuel exhaustion and the aircraft crashed into hilly terrain northwest of Athens airport. All the 115 passengers and six crew died. On this aircraft, the same aural tone is used to indicate two conditions, Takeoff Configuration Warning and Cabin Altitude Warning. A minute and a half later, with the aircraft still climbing, the captain contacted the company operations center on the company radio frequency and reported that that the crew had a takeoff configuration warning. The operations center put a ground technician on the line to communicate with the captain. The technician later reported a confusing conversation in which the captain mentioned a problem with the ventilation cooling fan lights. INVESTIGATION Since the message from the captain did not make any sense to the technician, he asked the captain to “confirm that the pressurization panel was selected to AUTO.” The captain responded “where are my equipment cooling circuit breakers?” The technician replied “behind the captain’s seat”. During the conversation with the company operations center, the passenger oxygen masks deployed as they were designed to do when the cabin altitude exceeded 14 000 ft. The communication between the ground technician and the captain ended as the aircraft climbed through 28 900 ft. During the previous f light, cabin crew had noticed frozen door seals and noises around the right aft service door, and the flight crew wrote up an entry in the aircraft tech log ‘aft service door requires full inspection’. Between 1:30am – 3:15am, technicians performed a visual inspection of the aft service door and carried out a cabin pressurization leak check. During the leak check, the technician who would later speak with the captain during the flight went to the cockpit to pressurize the aircraft, while another technician stayed in the rear of the aircraft near the R2 door. No defects were found and the log entry was signed off. The maintenance manual procedure for the cabin pressurization check required the pressurization mode selector in the cockpit to be set to the MAN (Manual) position. The investigation board found that after the pressurization test, the pressurization mode selector was not selected back to AUTO (Figure 1.7). As a result, the aircraft’s out flow valve (OFV) remained fixed in the open position, the position it was last left in. Shortly after, the f light crew is believed to have lost useful consciousness as a result of hypoxia, the aircraft leveled off at FL340 and continued on its programmed route, eventually entering a programmed holding pattern near Athens. There was no response to radio calls to the aircraft. F-16 fighters were scrambled to intercept the 737. One of the F-16 pilots observed the aircraft at close range and reported that the captain’s seat was vacant, the first officer’s seat was occupied by someone who was slumped over the controls, the passenger oxygen masks were dangling, and motionless passengers were seen seated wearing oxygen masks in the cabin. A person who appeared to be a flight Module 09 - Human Factors Figure 1.7 – Pressurization Panel was not reset back to auto. 1.13 GENERAL CASE STUDY: FAILURE TO PRESSURIZE AFTER OUTFLOW VALVE LEFT IN OPEN POSITION The investigation board stated ‘Although not a formal omission, it would have been prudent to position the pressurization mode selector back to AUTO’. The board noted that the last action item in the pressurization check procedure stated ‘Put the Airplane Back to its Initial Condition’. SAFETY RECOMMENDATIONS The board considered that these instructions were vague because they did not state specifically that the pressurization mode selector must be returned to the AUTO position, although the procedure explicitly required setting that selector to the MAN (manual) position for the test. During their pref light preparations, the f light crew was required to confirm that all selectors, including the pressurization mode selector, were in their proper positions for flight. The flight crew apparently did not recognize that the pressurization mode selector was set to MAN instead of AUTO, as required. As a result, the out flow valve (OFV) remained fixed in the open position, and the cabin did not pressurize. The off icial accident report provides a much more detailed treatment of the accident and the wider organizational issues that were associated with it, but the vagueness of the maintenance manual instructions was a significant contributing factor. SOME OF “THE DIRTY DOZEN” HUMAN FACTORS SPECIFIC TO THIS ACCIDENT Vag ueness of manua l instr uctions - Lack Of Knowledge, Lack Of Resources CASE STUDY: MAIN WHEEL INCORRECTLY FITTED It’s all too easy to take for granted the support that exists in a main base environment. The following incident serves as a reminder of the some of the issues experienced at some line stations. On arrival at main base, the flight crew of a long haul twin engine aircraft reported that one of the main wheel tire pressures was intermittently reading low. On hubcap removal, the wheel nut was seen to be too far down the axle threads, and the locking bolt was barely engaged with the axle nut. The wheel had been changed at the line station prior to the last sector. The resident line technician discovered a cut in a main wheel tire on his initial walk around and after assessment, felt that the tire was within maintenance manual limits. However, subsequent discussions with customer services and the flight crew led to the decision to change the wheel; nightfall was approaching and the clock was ticking. The line station in question supported one resident technician with back up from other airlines. The regular back up technician was contacted at home (1.5 hours away from the airport) while the resident technician conscripted a couple of baggage handlers to help with the manual tasks of a wheel change. Once all the equipment was positioned at the aircraft, 1.14 the technician started to jack the wheel, at which time the baggage handlers ‘disappeared’. The technician then discovered that the jack did not work on air drive and manual jacking was accomplished with support from the refuel technician. By this time the flight crew had arrived and the third flight crewmember was assigned to hold a flashlight through all operations, as the ramp lighting was insufficient. Having sought support from the baggage handlers again, the wheel was removed. After inspecting and regreasing the axle, the new wheel was positioned, minus the spacer, which was still attached to the wheel. The wheel nut was torqued and a spin check carried out. As the cover plate was being fitted, after the tire pressure sensor had been connected, the backup technician arrived to finish the job while the resident technician attended to a further fault on the flight deck. INVESTIGATION The main contributory factors identified during the investigation were: Pressure caused by lone working practices on station. Work area inadequately lit. Pressure of a delay that could have caused crew to go out of hours. No specific cautions or warnings in the maintenance manual to ensure that the spacer was fitted. Module 09 - Human Factors With regards to lone working, the line station reviewed its policy and identif ied that, having one resident technician was sufficient for normal operations as there are plenty of other staff around the aircraft (baggage handlers, refuel technician etc.) to ensure that safety is maintained. What was lacking was a robust process to ensure that when the resident technician required support, it was readily available. (Figure 1.8) T he ot her le s son recom mend at ion w a s one of communication. Operational pressure is always going exist but as long as the technician kept everyone abreast of the situation, there should have been no undue pressure to dispatch a less than serviceable aircraft. Commercial pressures must not play a part when it comes to aircraft maintenance practices. SOME OF “THE DIRTY DOZEN” HUMAN FACTORS SPECIFIC TO THIS ACCIDENT Pressure caused by lone working practices on station – Lack of Resources, Pressure Work area inadequately lit – Lack of Resources Pressure of a delay that could have caused crew to go out of hours – Pressure No specific cautions or warnings in the maintenance manual to ensure that the spacer was fitted – Lack of Knowledge, Lack of Communication Figure 1.8 – Maintenance requires sufficient personnel CASE STUDY: TORCH (FLASHLIGHT) LEFT IN NOSE WHEEL STEERING CABLE RUN Maintenance errors, as we know, can take various forms from panels being installed incorrectly to inadequate surveillance inspections. This incident relates to the consequences of not accounting for all tooling used after a task has been completed. (Figure 1.9) During taxi out to the runway for a return sector from Europe, the f light crew of a Boeing 737 found the aircraft difficult to control through the rudder pedals. The steering tiller would not return to the neutral (self center) making rudder nose wheel steering “impossible”. Inspection of the nose wheel steering mechanism found a torch stuck in the cable run, causing damage to the cable guide wheel bracket and a pulley. Investigation Module 09 - Human Factors Figure 1.9 – All tools need to be accounted for after a task is completed 1.15 GENERAL SAFETY RECOMMENDATIONS identified that the nose wheel spin brake pads had been replaced the night before but why had the engineers involved failed to remove the torch? An engineer and two technicians were tasked to work the B737 but prior to starting their assigned work for the night, they were involved in clearing late evening departure snags. The engineer busied himself with researching a hydraulic leak on an Airbus while the technicians started the spin pad replacement on the B737 at approximately 3:30am. In addition to the spin pad replacement, the B737 also had a toilet leak requiring the toilet dump valve to be replaced, so the technicians split the tasks. The technician arrived at the aircraft, which was parked remotely in the mobile workshop. His original plan was to use separate lighting from the mobile workshop but when he opened the rear doors of the workshop there was a torch lying on the floor. He placed the torch on top of the nose leg and positioned it as best he could to illuminate the task in hand. During completion of the task, the technician inadvertently kicked over a bag of spanners and only after completing the replacement of the spin pads did he pick them up. In doing so, he was momentarily dazzled by the headlamps of the mobile workshop, which was enough to distract from the fact that the torch had not been removed. The technician then assisted his colleague in changing the toilet dump valve as past experience had told him it was a tricky job. INVESTIGATION AND RECOMMENDATIONS The main contributory factors identified during the investigation were: Time pressure; the technician was aware that work was still outstanding on the Airbus and he needed to give his colleague a hand with changing the toilet dump valve. Tool control; there was inadequate control to ensure all tooling was accounted for. Inspection; the engineer failed to inspect the replacement of the spin pads prior to signing for the task in the technical log. Poorly lit work area: It is worth noting that the ‘safety nets’ of an engineering pre service check and two flight crew walkround inspections failed to identify the torch, primarily due to the restricted visibility of the nose wheel area, with doors closed, on the B737. A fundamentally mundane task could have led to a far more serious incident. SOME OF “THE DIRTY DOZEN” HUMAN FACTORS SPECIFIC TO THIS ACCIDENT Time pressure – Pressure To ol cont rol – Lack of Tea mwork , Lack of Awareness Inspection – Lack of Communication, Pressure, Lack of Teamwork Poorly lit work area – Lack of Resources Mundane task could have led to a far more serious incident - Distraction, Complacency After both technicians had completed their work on the B737, they proceeded to the Airbus and began work on a hydraulic pump change. They did not complete this job in the time available and eventually handed it over to the day shift. The engineer never visited the B737 as he considered the technicians to be proficient and the assigned tasks relatively straightforward. 1.16 Module 09 - Human Factors MURPHY’S LAW GENERAL “WHATEVER CAN GO WRONG, WILL GO WRONG” Figure 1.10 – Lt. Colonel John Paul Stapp – Gee Whiz Experiment Yes, there really was a Murphy. He was Captain Edward A. Murphy Jr., an Air Force engineer. The saying came from a 1949 experiment at Edwards Air Force Base in California. The experiment was to determine how many G’s (force of gravity), a pilot could withstand; the test used a rocket sled nicknamed “Gee Whiz” which simulated the force of an airplane crash. (Figure 1.10) Colonel John Paul Stapp was the volunteer who participated in the rocket sled tests. Capta in Mu r phy at tended one of the tests and attached sensors to the colonel. The sensors were capable of measuring the G-force applied when the sled came to a stop, improving the test result data. The first test produced a zero reading; upon examination, it was determined that all four sensors were connected incorrectly. On each of the four sensors, there were two possible ways to connect the wires; and on all four sensors, the wires were hooked up incorrectly! Murphy was very upset and blamed the technician for the foul up. He supposedly said “If there are two ways to do something, and one will result in disaster, he’ll do it that way”. Source: Improbable Research Colonel Stapp recognized the importance of Murphy’s comments, and when talking to the press, attributed the successes and the sled team’s safety record to “Murphy’s Module 09 - Human Factors Figure 1.11 – Whatever can go wrong will go wrong Law”. He explained Murphy’s Law as “whatever can go wrong, will go wrong”, and if you can anticipate problems, disaster can be averted. (Figure 1.11) 1.17 Failures in aviation and space exploration can be extremely costly. In one unmanned orbiting vessel, (ironically) a set of sensors were all connected incorrectly. When the sensors failed to operate as designed, the parachutes that were to slow down the spacecraft didn’t open. Because of costly failures, designers have installed “fail safes”. (Figure 1.12) Fail safes are referred to as “idiot proof ”. But Murphy’s Law always seems to strike, even when precautions have been put in place; resulting in “Grave’s Law”, which states, if you make something idiot proof, the world will create a better idiot”. So what can we learn from this in relation to Human Factors? We can use Murphy’s Law as a tool, if we expect things to go wrong and put maintenance safety culture into action, just like Murphy’s sled team, a good safety record can be maintained. 1.18 Figure 1.12 – Fail safes are designed to be"idiot proof". Module 09 - Human Factors QUESTIONS Question: 1-1 Question: 1-5 Question: 1-2 Question: 1-6 What does the "E" in PEAR Model stand for? Because of costly failures, designers have installed , this is referred to "Idiot Proof". What ever can go wrong, will go wrong refers to ? Corporate culture of get the job done at all costs would fit which Dirty Dozen factor? Question: 1-3 Who supposedly stated "If there are two ways to do something, and one will result in disaster, he'll do it that way."? Question: 1-4 Reduction in near vision is a sign of aging that is anticipated in all AMTs over years of age. Module 09 - Human Factors 1.19 ANSWERS Answer: