Manufacturing Management DM202 Semester 2 Lean & Six Sigma
Document Details
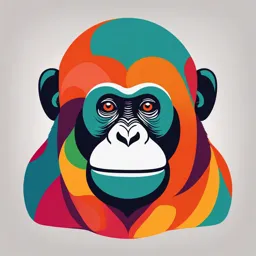
Uploaded by SafeDiscernment
University of Strathclyde
2022
null
Colin Andrews
Tags
Summary
These lecture notes from the University of Strathclyde cover concepts in manufacturing management for a DM202 course, specifically focusing on Lean and Six Sigma methodologies. The notes include introductions to Six Sigma, its origins, key elements, and the role of voice of the customer (VoC) in the framework.
Full Transcript
Manufacturing Management DM202 Semester 2 Lean & Six Sigma Colin Andrews: [email protected] • Six Sigma • Lean • Complementary approaches NOT alternativesAgenda © University of Strathclyde 2020 Introduction to Six Sigma What is Six Sigma? • Vision • Business Strategy • Goal • Metric...
Manufacturing Management DM202 Semester 2 Lean & Six Sigma Colin Andrews: [email protected] • Six Sigma • Lean • Complementary approaches NOT alternativesAgenda © University of Strathclyde 2020 Introduction to Six Sigma What is Six Sigma? • Vision • Business Strategy • Goal • Metric • Benchmark • Philosophy • Vehicle for business excellence “ It is a proven methodology to identify and eliminate defects and reduce variation in processes resulting in financial savings and improved customer satisfaction.” It is neither just a tool nor a technique!! © University of Strathclyde 2020 Six Sigma Origins • 1979: Art Sundry – ‘Our Quality stinks’ • Motorola was spending $700-800m correcting defects; 20% of revenue • Bill Smith : Correlation between a product’s field life and the number of times it was corrected during manufacturing • Popularised by Mikel Harry and Richard Schroeder • 1988: Motorola wins Malcolm Baldrige Award • 1995: GE adopts Six Sigma as ‘the’ strategic initiative © University of Strathclyde 2020 Key Elements (CSFs) 1. Focuses on Customers (VoC) 2. Integrates human & process aspects 3. Uses a disciplined approach to problem solving 4. Organisational project infrastructure 5. Active senior management leadership 6. Significant bottom line financial returns 7. Effective use of statistics 8. Data-driven methodology © University of Strathclyde 2020 ● To reduce and control variation in processes ● This in turn will contribute to ● Reduced defects ● Increased yield ● Improved customer satisfaction ● Higher profitsThe Aim of Six Sigma Lower Specification Upper Specification DefectsDefectsVariation Reduction Variation Reduction © University of Strathclyde 2020 What is Sigma Standard Deviation A symbol traditionally used in statistics to represent the variation about the mean of a normal distribution‘ σ ’ © University of Strathclyde 2020 So what is Six Sigma ‘ 6 σ ’ Level of process performance equivalent to producing only 3.4 defects for every one million opportunities or operations. Six standard deviations represent virtual perfection © University of Strathclyde 2020 Golf Player (3 Sigma vs. 6 Sigma) If you played 100 rounds of golf per year and played at: 3 sigma quality level… you would miss 1 putt per round 4 sigma quality level… you would miss 1 putt every 9 rounds 5 sigma quality level… you would miss 1 putt every 2.3 years 6 sigma quality level… you would miss 1 putt every 163 years!!! © University of Strathclyde 2020 Achieving Six Sigma Performance Complexity Variation 6 σ Customer requirements 1. Understanding Customer needs 2. Reducing variation 3. Simplifying processes © University of Strathclyde 2020 • Input from customers in their own terms • Capture and transform in quantifiable requirements Voice of the customer (VoC) “I want the phone to be answered quickly ” Critical to Quality (CTQ) Number of rings before call is picked up Specification <= 3 rings is acceptable, > 3 is defect © University of Strathclyde 2020 Mechanisms to capture the VoC • One-one Interviews • Surveys • Focus Groups • Market Research • Sales Visits/ Calls • Benchmarking • Quality Scorecards • Customer Brainstorming • Customer Journey Maps © University of Strathclyde 2020 • Variation is natural! It occurs in all activities, in all processes, in all organisations…Understanding variation Mean-Based MeasurementMean-Based Measurement Target 30 daysProcess Av. 25 days Delivery Time (days) “ We’re Good!” Variance-Based MeasurementVariance-Based Measurement Delivery Time (Days) “ We’re Not Good Enough!! 15 20 25 30 35 45 50 The Customer Feels Variance - Not the Mean! Dissatisfied Customers? © University of Strathclyde 2020 e.g. Travel time to work © University of Strathclyde 2020But they form a pattern that, if stable, can be described as a distribution Distributions can differ in: TIME TIME TIME TIME TIME TIME TIME TIME TIME TIME … Or any combination of these. SPREAD LOCATION SHAPE Normal Distribution • a bell-shaped curve with a peak around an average value: 68.26% 95.44% 99.74% +1σ +2σ +3σ-3σ -2σ -1σ © University of Strathclyde 2020 • Common Cause (Noise) • Is present in every process and is produced by the process itself • It can be mitigated but requires a fundamental change in the process • Special Cause (Signals) • Exists in most operations/processes • Caused by unique disturbances or a series of them • Can be removed/lessened by basic process control and monitoring Types of Variation © University of Strathclyde 2020B u s in e s s a s u s u a l O p p o rtu n ity fo r im p ro v e m e n t • If only common causes of variation are present, the output of a process forms a predictable (probable) and stable distribution over time • If special causes of variation are present, the output of a process is not stable over time (and not predictable)Common cause vs. Special cause © University of Strathclyde 2020 Variation reduction = Defect reduction Lower Specification Upper Specification DefectsDefects x Sigma Process 6 Sigma Process Variation Reduction Variation Reduction © University of Strathclyde 2020 Performance Level SIGMA % Yield # of Defects per Million Opps (DPMO) A+ 6 99.99966 3.4 A 5 99.9767 233 B 4 99.3790 6,210 C 3 93.3 66,807 D 2 69 308,537 F 1 31 691,462 Cost of Quality % <1% of sales 5 - 15% of sales 15 - 25% of sales 25 - 40% of sales C 93.3 66,8073 Non-competitive Out of BusinessWhat makes Six Sigma World Class? © University of Strathclyde 2020 Who makes Six Sigma work? • Champion – Monitoring the progress of Projects • Master Black Belts – Process Improvement Specialist, Coaching, Mentoring, etc. • Black Belts – Full Time Change Agents; Project Leader • Green Belts – Part-time involvement • Yellow Belts – Part-time involvement © University of Strathclyde 2020Champion Black Belt Black Belt Black Belt Green Belt Green Belt Green Belt Green Belt Green Belt Yellow Belt Yellow Belt Yellow Belt Yellow Belt Master Black Belt Setting Strategic Goals KPIs are linked to the strategy Finance Customer Processes Employees Vision Strategy Critical success factors Key Performance Indicators What do we need to achieve our targets? How do we measure our success?What do we want to achieve? How do we achieve this? Focus of Six Sigma © University of Strathclyde 2020 Vision & Strategy becom es transparent Six Sigma Summary Six Sigma methods answer the question ‘How do we ensure nothing goes wrong in the hands of the customer?’ The approach can only work if: customer requirements are translated into specifications processes are stable / predictable special cause variation is actively searched for The first steps are therefore Understand customer value Stabilise processes Look for problems to solve Introduction to Lean “ The endless transformation of waste into value from the customer’s perspective”. Womack and Jones, Lean Thinking Lean Thinking is about accelerating the velocity of any process by doing only the things that add customer value and eliminating other activities that don’t ( Waste ).What is Lean Thinking? © University of Strathclyde 2020 Customer Order Waste Product / service delivery TimeBusiness as Usual Time (Shorter)Customer Order Waste Lean Manufacturing Product / service deliveryLean Thinking Philosophy © University of Strathclyde 2020 … about eliminating people!! It is about continuous process improvement, NOT cost reduction through headcount cutbacks!Lean is not… © University of Strathclyde 2020 GOAL : Highest quality , Lowest Cost , Shortest Lead Time Just in Time Jidohka TPS Minimum resources req Consistency What is needed ! Right amount where & when needed Detect abnormalities Stop & respond Effective autonomation Heijunka Standardised Work Kaizen Stability Minimum Lead Time Min input Max output Process Method High Quality Muda Mura Muri• Lean thinking began in post-war Japan with the renowned Toyota Production System which transformed the car manufacturing industry. Origins of Lean Production levelling Continuous ImprovementAutonomy / no errors forward Waste, overburden & unevenness © University of Strathclyde 2020 1. Identify value 2. Map value stream 3. Create flow4. Establish pull5. Pursue perfectionLean Principles © University of Strathclyde 2020 © University of Strathclyde 2020Who can benefit from ‘Lean’ Lean tools and methods apply to anyone who… Chases for information in order to complete a task Goes through multiple decision loops to get something done Is constantly interrupted when trying to complete a task Is engaged in expediting reports, purchases, materials, Does work in batches Industries where Lean has worked Automotive Ship-building Pharmaceuticals Electronics Software development Public Services Banking ... Key examples • Throughput Yield & Rolled Throughput Yield • Work in Process • Lead time • Waste • Value Added / Non Value Added (Value added ratio) • Takt timeLean Metrics are ‘absolute’ © University of Strathclyde 2020 Throughput Yield (TPY) “ Throughput Yield (TPY) is the number of acceptable units / transactions at the end of the end of a process divided by the number of starting units / transactions excluding scrap and rework”.?????????????????? = ???????????? . ?????????????????????????????? / ???????????????????????????????????????????????????????????????????????? h ?????????????????? ?????? ?????????????????????????????????????????????????????? ?????????????????????????????? ???????????? . ???????????? ?????????????????????????????? /???????????????????????????????????????????????????????????????????????? © University of Strathclyde 2020 Rules for calculating TPY • The unit of measure must be the same for the numerator and denominator. • Rework should be considered in the TPY calculation. • TPY should only be used to measure a single process. • To calculate a number of processes the rolled throughput yield (RTY) needs to be calculated © University of Strathclyde 2020 Calculate the TPY for the following Process 1, 2 & 3 © University of Strathclyde 2020 Solution Process 1 TPY= 40 / 50 = 80.0% Process 2 TPY = 34 / 46 = 73.9% Process 3 TPY = 37/46 = 80.4% • Rolled throughput yield (RTY) is the probability of the entire process producing zero defects…. RTY = Process 1 TPY * Process 2 TPY * Process 3 TPY RTY = 0.800 * 0.739 * 0.804 RTY = 47%! © University of Strathclyde 2020 Remember OEE! “ Material that has entered the production process but is not yet a finished product. Work in process (WIP) therefore refers to all materials and partly finished products that are at various stages of the production process.” • Manufacturing slang?... • Try number of “things in process”… e.g. how many “things” are sitting in your desk, awaiting in your inbox, or in a programme waiting for you to work on them? This is WIP!WIP – Work in Process © University of Strathclyde 2020 “ Service processes (transactional and manufacturing) are usually slow. Slow processes are expensive. Slow processes are prone to poor quality… which drives cost up…and drives down customer satisfaction…and hence reduce revenue Service processes are slow because there is too much WIP, often the result of unnecessary complexity in the service offering…” (M L George 2003)Why such a big deal about WIP? © University of Strathclyde 2020 • Lead time is how long it takes to deliver a product or service once the order is triggered.Lead Time © University of Strathclyde 2020 • Usual turnaround 15-20 days. • Ideal waiting time for information is 3 days. • System records indicate that the administrative team can close 30 requests for information cases per day in average. • Aim is to a) attract the best students and b) to increase conversion rates for international students. 1. What is the WIP in the current process? 2. What would be the WIP if you were to limit the amount of WIP into the system to meet the customer requirements? 3. What alternatives do you have to decrease the lead-time? 17.5 days * 30 requests per day = 525 requests for information in the system 3 days * 30 requests per day = 90 requests for information in the systeme.g. Dealing with online Information Requests © University of Strathclyde 2020 Mapping the process (value stream) INPUTS PROCESS OUTPUTS SUB PROCESS 1 SUB PROCESS 2 SUB PROCESS 3What is a process? © University of Strathclyde 2020“ Sequence of interdependent and linked procedures which, at every stage, consume one or more resources to convert inputs into outputs. These outputs then serve as inputs for the next stage until a known goal or end result is reached.”INPUTS PROCESS OUTPUTS SUB PROCESS 1 SUB PROCESS 2 SUB PROCESS 3 Eggs, milk, bread, butter, bacon, plates, utensils, cookware, potatoes MAKE BREAKFAST Scrambled eggs, toast, crisp bacon, pan-fried potatoes PREPARE INGREDIENTS COOK INGREDIENTS SERVE INGREDIENTS COOK BACON COOK EGGS TOAST BREAD FRY POTATOES HEAT PAN POUR MIXTURE STIR MIXTURE ADD PEPPER REMOVE EGGS RECIPE (SOIs) Jacka and Keller, 2009Breakfast example © University of Strathclyde 2020Eggs, milk, bread, butter, bacon, plates, utensils, cookware, potatoes MAKE BREAKFAST Scrambled eggs, toast, crisp bacon, pan-fried potatoes PREPARE INGREDIENTS COOK INGREDIENTS SERVE INGREDIENTS COOK BACON COOK EGGS TOAST BREAD FRY POTATOES HEAT PAN POUR MIXTURE STIR MIXTURE ADD PEPPER REMOVE EGGS RECIPE (SOIs) Process flowchart Deployment flowchart• A continuous improvement tool that enables the visual representation of a process Spaghetti diagramWhat is a process map? © University of Strathclyde 2020 Making changes without truly understanding how the process works and why can lead to costly mistakes. Process maps help us to identify,… • Who does what • How tasks are done • What are the inputs and outputs • Where is the waste • Enhance the memory of businesses “ Improve understanding with the purpose of eliminating non value adding activities.” Why process mapping? © University of Strathclyde 2020 • Get to know your process a little bit before you start…. • Walk through the process…. Learn to see!Ensuring success © University of Strathclyde 2020 • There is a variety of process mapping techniques. • The most commonly used techniques. • High and low lever flow charts • IDEF family of methods • Deployment charts • Spaghetti diagrams • Post-It Technique • Work flow diagrams • Value stream mappingProcess Mapping Techniques © University of Strathclyde 2020 1. Agree on a process to map (including start and end points) 2. Using post its map the process A single post it note per process activity Dependencies between activities should be represented with arrows Start high level and keep building on it 3. When you have a detailed view of the process highlight areas of waste in the process 4. Think about potential opportunities to remove the wasteBasic Steps to build a Process Map 47© University of Strathclyde 2020 Value Stream Map Manufacturing © University of Strathclyde 2020 Redefined for service • Unnecessary Movement • Incorrect inventory • Delay • Duplication • Unclear communication • Errors in the service transaction • Lost opportunity to retain/win customers Bicheno and Holweg 2009Manufacturing • Transportation • Inventory • Motion • Waiting • Over processing • Over production • DefectsWaste in Lean (The 7 Wastes) © University of Strathclyde 2020 “ As services are intangible , they cannot be subjected to precise specifications for uniform quality and measurement of performance. The inseparability and heterogeneity of services mean that there is less managerial control over quality, since the services cannot be tested and assured before delivery and standardised during the delivery. It is also difficult to predict, and hence influence, how the customer would perceive and evaluate the service quality. The final characteristic of perishability implies that service organisations need to retain excess capacity to meet the fluctuating demands of customers.” Woon, 2000The distinguishing characteristics of services © University of Strathclyde 2020 • Customers – Typically greater involvement of customers in the process. Customers sometimes act as co-producers • Standardisation – Difficult to achieve as services are people-centric. • Quality – An experience, not just a measurement against specifications. The customer’s definition of quality is a perception. • Process visibility – Intangible information flows diminish process visibility • IT systems – They play a bigger role. They enable the process, but can also be a rigid constraint on the process. • WIP & Inventory - Often hidden and ignored, can have the same negative impacts as in a manufacturing environmentWhat this means for Lean in Services © University of Strathclyde 2020 ‘ Lean’ Summary Lean methods answer the question ‘How do we quickly and efficiently meet the needs of the customer?’ The approach can only work if: Customer value is understood and can be related to the actual work being carried out Work is carried out in a consistent way Wasteful activities are always challenged The first steps are therefore Understand customer value Stabilise processes Look for waste to remove Lean vs Six Sigma Elimination of waste Identification of Value stream Achievement of flow Pacing by a pull Pursuit of perfection Define Measure Analyse Improve ControlIm proved Speed Im proved SpeedLean – focuses on dramatically improving flow in the value stream and eliminating waste Six Sigma – focuses on eliminating defects and reducing variation in processes Reduced Variation Reduced VariationLean vs. Six Sigma © University of Strathclyde 2020 • Same Objective: Continuous and Sustainable Business Process Improvement • Focus on business needs defined by the customer (customer focus) • Requires active involvement of all interested! • Practical methods, proven to work • Both include a comprehensive tool box to improve any business processLean vs. Six Sigma - Similarities © University of Strathclyde 2020 Lean • Focused on ‘Flow’ • Removal of ‘Waste’ • Technically simple • Low investment • Typically non-statistical tools • Six Sigma • Focused on problems with unknown solution • Reduction of ‘Defects’ often through reduction of variation • Technically more difficult • More significant investment • Statistical tools typically used (Though not applicable to all cases) • Lean vs. Six Sigma - Differences © University of Strathclyde 2020 Faster creation of value for custom ers at a low er costLean & Six Sigma – Complementary approaches Lean Only Six Sigma Only Lean Six Sigma Low Value High Value CUSTOMER VIEW POINTLow Cost PRODUCER VIEW POINT High Cost © University of Strathclyde 2020