Disassembly, Inspection, Repair and Assembly Techniques PDF
Document Details
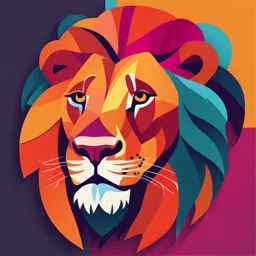
Uploaded by FaultlessMarsh8570
null
CASA
Aviation Australia - David Kingshott
Tags
Related
- Aircraft Maintenance Measuring Tools PDF
- Avionics Assembly and Disassembly Techniques PDF
- Aircraft Maintenance Reviewer Sheet PDF
- Aircraft Maintenance Planning and Control PDF
- ET-PP04 Aircraft Engine Inspection, Maintenance, Operation, and Troubleshooting PDF
- Module 2 Physics for Aircraft Maintenance PDF
Summary
This document provides information on disassembly, inspection, repair, and assembly techniques for aircraft components. It details procedures for complete airframes, major and minor components, and safety precautions. The document includes sections on replacing major components, such as engines and wings, and minor components, such as wheels and tires.
Full Transcript
Disassembly and Re-Assembly Techniques Disassembly and Re-Assembly Disassembly and re-assembly, in terms of aircraft, can range from work on complete airframes down to component maintenance, with several steps in between. The reasons for dismantling and re- assembly may include:...
Disassembly and Re-Assembly Techniques Disassembly and Re-Assembly Disassembly and re-assembly, in terms of aircraft, can range from work on complete airframes down to component maintenance, with several steps in between. The reasons for dismantling and re- assembly may include: Complete airframe disassembly for road/air shipment Replacement of major components/modules Replacement of minor components/modules Disassembly and re-assembly of major components Disassembly and re-assembly of minor components. Complete Airframes It may be necessary to dismantle a complete aircraft for transportation by road or by air. This could be for recovery from an accident site remote from the airfield or for movement of the aircraft when it is totally non-airworthy, due perhaps to severe corrosion or an unknown maintenance history. Because many larger, modern aircraft are manufactured at several different locations, the completed modules are assembled in the final build hall of the primary manufacturer. The joining points are often known as ‘transportation joints’ and in extreme instances can be the points where the aircraft may be dismantled again to allow transportation. Aviation Australia - David Kingshott B18 Takeoff accident 2023-11-16 B1-07d Maintenance Practices Page 304 of 335 CASA Part Part 66 - Training Materials Only Instructions for the dismantling operation will be found either in the Aircraft Maintenance Manual (AMM) or in a special dismantling procedure issued by the manufacturer. During dismantling, precautions must be taken to prevent injury and damage. General precautions include: The aircraft should, if at all possible, be dismantled within a hangar. If this is not possible, then level and firm ground will suffice. Sufficient clearance in the hangar must be available, both to clear the airframe when on jacks and to allow heavy lifting cranes enough room to manoeuvre over the aircraft. All precautions, in accordance with the manufacturer’s instructions, must be taken prior to the aircraft entering the hangar, including de-fuelling and the removal of devices such as emergency oxygen canisters. When the aircraft is jacked up, all trestles must also be placed in position. This allows the aircraft to be climbed on and, later, ensures that it will not overbalance when a major part (such as a wing) is removed. Fuselage sections ready for joining at Boeing plant - Everett 2023-11-16 B1-07d Maintenance Practices Page 305 of 335 CASA Part Part 66 - Training Materials Only While the manufacturer’s instructions give the details for a specific aircraft, the following sequence of dismantling gives an idea of the correct order of disassembly: Main planes Tail unit Undercarriage units Centre section Fuselage. Re-assembly is done in the reverse order of disassembly, and all parts must be cleaned, protected and serviceable before installation. Aircraft during major servicing 2023-11-16 B1-07d Maintenance Practices Page 306 of 335 CASA Part Part 66 - Training Materials Only Replacement of Major Components / Modules Major component replacement is normally completed at a large maintenance base, where all the required equipment is available. An example is the replacement of a engine which has come up for overhaul or wing that has suffered major damage. If the aircraft is positioned away from a maintenance base it is sometimes possible to ferry an aircraft which requires major work to a appropriate place of maintenance. The Aircraft Maintenance Manual (AMM) will be referred to during these tasks. Replacing an engine on a Boeing 727 2023-11-16 B1-07d Maintenance Practices Page 307 of 335 CASA Part Part 66 - Training Materials Only Replacement of Minor Components / Modules Some components have to be repaired by replacement. Repairs to aircraft wheel assemblies (worn tyre), for example, are often done in a dedicated wheel service department. The wheel assembly would normally be replaced on the aircraft by a serviceable item or reinstalled once the repair in the wheel service department has been completed. Other components, which are replaced first and repaired later, might include structural items, such as doors of all types, and most fairings and cowlings. Most of these tasks are simple removal and replacement operations that are covered in the AMM. Boeing B737 MM Example of an aircraft MM 2023-11-16 B1-07d Maintenance Practices Page 308 of 335 CASA Part Part 66 - Training Materials Only Disassembly and Re-Assembly of Major Components Most of the work done during this phase of maintenance is scheduled with normal aircraft maintenance. Not only might the components be removed and reinstalled at different times during the maintenance, but maintenance work might also be done on the items while they are removed. In addition, they may be removed to allow access to other parts of the airframe during maintenance. Items such as engines, propellers, landing gears, hydraulic units and wheels require some form of maintenance. This may include a simple condition check or a full overhaul of its component parts, allowing checks on internal component parts for wear, damage and corrosion. It normally requires the use of a dedicated overhaul facility, which can provide the correct environmental conditions and is equipped with the special test equipment required to carry out maintenance and repair. Work conducted during this type of maintenance is covered in the component maintenance manual (CMM). Front cover of a CMM 2023-11-16 B1-07d Maintenance Practices Page 309 of 335 CASA Part Part 66 - Training Materials Only Disassembly and Re-Assembly of Minor Components A typical passenger aircraft can contain hundreds of small components that work together as parts of a larger system. The wide range of hydraulic and pneumatic components can be mechanical, electromechanical or electrical in operation. Other components might include those installed in fuel, air conditioning, pressurisation, electrical and electronic systems. These components have their own CMMs to allow maintenance and troubleshooting to be done. Some components are removed only once they have failed (On- Condition), while others receive regular maintenance. As with major disassembly and assembly of components they are normally sent to the companies component overhaul facility, which can provide the correct environmental conditions and is equipped with the special test equipment required to carry out maintenance and repair. Operators of smaller aircraft, or those who operate only a few aircraft, usually send components requiring repair or maintenance to a third-party maintenance organisation. Technician calibrating electronic component 2023-11-16 B1-07d Maintenance Practices Page 310 of 335 CASA Part Part 66 - Training Materials Only Basic Disassembly and Re-Assembly Techniques All of the previously mentioned procedures require the use of the correct techniques over a wide range of working practices. These techniques ensure that the components are removed, dismantled, re-assembled and re-installed in accordance with both the relevant manuals and the correct ‘standard practices’. The aircraft, engine and component manufactures AMM and CMM contain the approved procedures for disassembly, inspection and reassembly and must be followed at all times. AMM chapters 20 (Airframe) and 70 (Powerplant) list standard practices used during overhaul. Keep a clean, controlled and well laid out workspace. You may need to cordon off an area around the aircraft and put out signage etc around your work area for safety. "Do Not Operate" tags should be placed around the aircraft and in the flight deck to identify areas and systems which are under maintenance and cannot be operated. If circuit breakers are pulled systems these have dedicated tags which clip over the breaker. Before beginning a task make sure you have the work package, the required tools basic and special to complete the job. Support structures, access stands, ground and pneumatic power may also be required, dependant on the job requirements. Any parts removed must be labelled and stored correctly and safely. Example of an aircraft AMM Pt 1 - Chapter 20 2023-11-16 B1-07d Maintenance Practices Page 311 of 335 CASA Part Part 66 - Training Materials Only When assembling some components, it may be vital to achieve certain alignments, dimensions or profiles. During initial production, most of the airframe and many of the components are assembled in a jig. A jig is a device that allows the manufacture, repair or rigging of components to a high dimensional accuracy. This guarantees consistency over a number of components. The jig holds all of the items securely so that, when assembled, the whole component is exactly the shape that the designer has stipulated. 2023-11-16 B1-07d Maintenance Practices Page 312 of 335 CASA Part Part 66 - Training Materials Only Disassembly / Re-Assembly Safe Work Practices The engineer must be aware of components which pose a threat to their safety as well as that of nearby individuals. For this reason, safe work practices must be implemented. In general, components may contain: Impact or pinch hazards Spring-loaded mechanisms Stored pressure Electrical power either live or stored Falling parts (upon final removal) Moveable components that may require restraint during disassembly and reassembly, e.g. propellers or control surfaces Fluid systems including, High-pressure fluid hydraulic lines (hydraulic leaks under system pressure or flailing of a detached pressurised hose). An example of the latter is an aircraft brake system when the park brake lever is applied. The brake accumulator maintains pressure to the brake units even though the aircraft Engine Driven Pumps (EDPs) have stopped and electric stand-by pumps are de-energised. The assembly and disassembly hazards described above pose a particular risk to an engineer’s hands and face. Park brake schematic 2023-11-16 B1-07d Maintenance Practices Page 313 of 335 CASA Part Part 66 - Training Materials Only To conclude, a wide variety of components exist across the aircraft maintenance environment which are capable of producing impact and pinch hazards. It is not within the scope of this document to specifically list component areas of concern, but to make the engineer aware of safe practices while carrying out maintenance tasks. Small Part and Component Identification When disassembling or removing any component, it is vital that all small items such as bolts, screws, nuts, washers and shims are clearly identified. This involves not only identifying the items by part number, but also recording their correct location and which aircraft they have been removed from as, in some hangars, more than one aircraft may be in a state of disassembly at any one time. Some items may simply be attached to the major assembly using many small ‘tie-on’ bags with identification labels. If a number of different sized fasteners are removed from a component such as a windscreen, they can be located in a locally made holding jig which keeps the different parts in their same relative position to the original item. This should allow all the screws to be returned to their original locations when the screen is reinstalled. Any part which is removed must have its identity and location retained until it is reinstalled. 2023-11-16 B1-07d Maintenance Practices Page 314 of 335 CASA Part Part 66 - Training Materials Only Discarding Parts A number of items, when they are removed from their original position, have to be discarded. The ‘once only’ policy is a combination of the manufacturer’s recommendations and normal engineering practice. Items that are usually discarded at removal are filters, O-rings, seals, gaskets, desiccants, fuels and oils of all types. Expendable parts Many other items have a given ‘life’. This may be counted in flying hours, calendar time or operating cycles, which mean these items have to be replaced throughout the life of the aircraft. If aircraft or their major components have been disassembled, it may be policy to replace components with ‘zero-life’ items prior to re-assembly. This allows the aircraft to fly for considerable time before any parts become due for replacement. 2023-11-16 B1-07d Maintenance Practices Page 315 of 335 CASA Part Part 66 - Training Materials Only Aviation Australia - David Kingshott Overhauled Engine ready for Installation Freeing Seized Components When dismantling any part of an aircraft, it is not unusual for the technician to encounter a seized fastener. Depending on its location, the AMM may recommend a range of actions to assist in the removal of the item(s). Aviation Australia - David Kingshott Mouse Milk Penetrating oil 2023-11-16 B1-07d Maintenance Practices Page 316 of 335 CASA Part Part 66 - Training Materials Only These actions may involve use of penetrating oil, which works its way down through the seized threads, providing both anti-corrosion action and lubrication. Other actions may involve the application of heat or cold to a specific part so that their relative diameters change, lowering the friction between the parts. Use of Correct Tools It is normal for technicians to own a comprehensive tool kit containing the highest quality tools recommended for the work planned. In a number of situations, a technician may use an incorrect tool that appears to be the correct one for the task. It is most important that only the correct tools are used for each and every maintenance task. Six different "cross head" screwdriver heads The removal of nuts from bolts is normally accomplished using a socket and wrench set, and these sockets can be of the 12-point or six-point type. When spanners need to be used, preference should be given to a ring spanner rather than an open-ended spanner. Adjustable spanners or ‘mole grips’ should never be used on aircraft. Use correct tools The manufacturer of the aircraft often specifies special tools when standard tools are unable to complete the task. Unless approved to do so, the technician should never substitute conventional tools for the special tools that are called for in the manual. Damage to the part being worked on will almost always result from the use of incorrect tools. Furthermore, using high-speed pneumatic/power screwdrivers for screw installation creates excessive heat and seizes the screw into the anchor nut. This usually results in screw head damage or may even strip the thread. 2023-11-16 B1-07d Maintenance Practices Page 317 of 335 CASA Part Part 66 - Training Materials Only Never use an electric screwdriver or drill (mains or battery-powered) in or near fuel tanks or in any explosive atmosphere. Use intrinsically safe tools in fuel tanks Murphy’s Law This ‘law’ states that ‘if a part or component can be installed incorrectly, someone, somewhere will install it that way'. There are numerous solutions in the fight against this problem. For example, when a pair of pipes or hoses are to be joined, there is the risk of the two pairs of couplings being ‘cross-connected’. This could result in serious damage if the pipes carry fuel and hydraulic oil. To prevent this happening, pipes and couplings usually have different diameters. Alternatively, the two sets of couplings would be located at different places so the pipes could not be wrongly connected under any circumstances. The same logic is applied to control cables that, of course, must also never be cross-connected. In this instance, the turnbuckles are located at slightly different locations at each cable break, again making it impossible to connect the wrong pair of cables together. 2023-11-16 B1-07d Maintenance Practices Page 318 of 335 CASA Part Part 66 - Training Materials Only