Dimensioning Standards PDF
Document Details
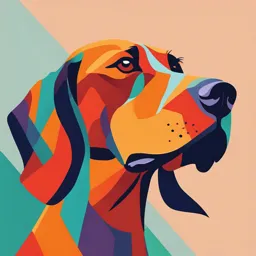
Uploaded by ImmensePoisson
UET Lahore
Tags
Summary
This document offers guidelines and standards for dimensioning in engineering drawings. It covers various aspects, including rules, practices and checklists.
Full Transcript
Dimensioning Standards Rules and Practices Accurate dimensioning is one of the most demanding undertakings when designing parts. Use the checklist to insure you have followed the basic dimensioning rules. Keep in mind there may be a case where the need to break a standard could occur to gi...
Dimensioning Standards Rules and Practices Accurate dimensioning is one of the most demanding undertakings when designing parts. Use the checklist to insure you have followed the basic dimensioning rules. Keep in mind there may be a case where the need to break a standard could occur to give clarity to the part and manufacturer. Standards In order for the drawings to be dimensioned so that all people can understand them, we need to follow standards that every company in the world must follow. Standards are created by these organizations: -ANSI -MIL -ISO -DOD -DIN -CEN -JIS Standards Institutions ANSI - American National Standards Institute - This institute creates the engineering standards for North America. ISO - International Organization for Standardization - This is a world wide organization that creates engineering standards with approximately 100 participating countries. Standards Institutions DIN - Deutsches Institut für Normung - The German Standards Institute created many standards used world wide such as the standards for camera film. JIS - Japanese Industrial Standard - Created after WWII for Japanese standards. CEN - European Standards Organization Standards Institutions The United States military has two organizations that develop standards. DOD - Department Of Defense MIL - Military Standard ANSI/ASME Y14.1 and Y14.5 – international drafting standards for engineering drawings Linear dimensions are comprised of four components: Dimension Text Dimension Lines Arrow Heads Extension Lines Extension Lines Continue 3mm past the dimension line Extended from the view to indicate the edges referenced and hold the dimension line 2mm gap from the view so they are not confused with the visible lines Dimension Lines Horizontal Aligned to a slanted surfaced Vertical When stacked, they are 10mm from the view and 10mm) apart. Dimension Text If the dimension text will not fit between the extension lines, it may be placed outside them. Dimension text is placed in the middle of the line both horizontally and vertically. Dimensioning Methods Dimensions are represented on a drawing using one of two systems, unidirectional or aligned. The unidirectional method means all dimensions are read in the same direction. The aligned method means the dimensions are read in alignment with the dimension lines or side of the part, some read horizontally and others read vertically. Dimension Text Unidirectional vs. Aligned Unidirectional Aligned dimensions are placed dimensions are placed so the horizontal dimensions can so they can be read from be read from the bottom of the the bottom of the drawing sheet and the vertical drawing sheet. This dimensions can be read from the method is commonly right side of the drawing sheet. used in mechanical This method is commonly used in drafting. architectural and structural drafting. Types of Dimensions There are two classifications of dimensions: size and location. Size dimensions are placed in direct relationship to a feature to identify the specific size. Location dimensions are used to identify the relationship of a feature to another feature within an object. Dimensioning Checklist Each dimension should be written clearly with only one way to be interpreted. A feature should be dimensioned only once.(not repeated) Dimension should be in fraction only Dimension and extension lines should not cross. Each feature should be dimensioned. Dimension features or surfaces should be done to a logical reference point. Dimension Checklist Dimension circles should have diameters and arcs with a radius. A center line should be extended and used as an extension line. Dimension features on a view should clearly show its true shape. Enough space should be provided to avoid crowding and misinterpretation. Dimension Checklist Extension lines and object lines should not overlap. Dimensions should be placed outside the part. Center lines or marks should be used on all circles and holes. Total width, depth and height of the object should be mentioned Linear Dimensioning Dimensioning from feature to feature is known as Chain Dimensioning. It is commonly used and easy to lay out. It does have possible consequences in the manufacturing of a part. Tolerances can accumulate, making the end product larger or smaller than expected. Chain Dimensioning This is a general note. It indicates that all two place decimal dimensions have a tolerance of plus or minus.01 inch unless otherwise specified. Chain Dimensioning Each of these steps can range between.490” and.510” wide. Chain Dimensioning The chain dimensioning layout can have an effect on the final length of the part ranging from 1.47 to 1.53. Chain Dimensioning Placing an overall dimension will limit the chain effect of the tolerance build up. Linear Dimensioning The accuracy of the final product is determined by the dimensions on the drawing. If all the dimensions originate from a common corner of the part, the object will be more accurate. This is referred to as Datum Dimensioning. Datums insure the tolerance or errors in manufacturing do not accumulate. Datum Dimensioning The dimensions originate from a common edge (DATUM) of the part. Datum Dimensioning The dimensions originate from a common edge (DATUM) of the part. This is a general note. It indicates that all two place decimal dimensions have a tolerance of plus or minus.01 inch unless otherwise specified. Datum Dimensioning This step can be.490 to.510 wide. This distance can be 1.49 to 1.510 wide. This distance can be.990 to 1.010 wide. Dimensioning Symbols Dimensioning Angles Angled surface may be dimensioned using coordinate method to specify the two location distances of the angle. Angled surfaces may also be dimensioned using the angular method by specifying one location distance and the angle. Dimensioning Angles Coordinate Method Angular Method Dimensioning Arcs and Circles Arcs and circles are dimensioned in views that show the arc or circle. Arcs are dimensioned with a leader to identify the radius; in some cases, a center mark is included. Circles should have a center mark and are dimensioned with a leader to identify the diameter. Dimensioning Curved Features and Arcs The arrow can be inside for small arcs. Use a capital “R” for dimensioning arcs. Small arcs do not need center marks. Arrow can be outside. Large Arcs use center marks. Diameters A full circular object should be dimensioned using its diameter. Holes should use hole notes. This specification calls for a hole with a.5 diameter and 1.00 deep. Diameters Cylindrical parts may show their diameters in this manner. Dimensioning on the right side view could be too crowded. Note that the diameter symbol is used so it is not confused with a linear dimension. Dimensioning Curved Features Points are placed along the contour and are dimensioned from the datum. Datum Reference Dimensions Designates more than one of the same feature. In this case, it is identifying there are two identical holes. Chamfers External chamfer for 45 degree chamfers only. There are two options. Internal chamfers. External chamfer for angles other than 45 degrees. Fillets and Rounds Fillets Rounds Fillets and Rounds Large arcs use center marks. Use a capital “R” for dimensioning the arc. Small arcs do not need center marks. Arrow can be outside the arc. Conical Tapers Slot Dimensioning The two methods shown on the left are the acceptable methods for dimensioning slotted holes. Dimensioning Radial Patterns Angles and radius values are used to locate the centers of radial patterned features, such as the holes on this plate. Keyway and Keyseat Keyway Keyseat Keyways Keyway Dimensions Shaft Hole Dimensioning Holes are specified with numbers and symbols. Reading a Hole Note The Hole Diameter is.25” and will be drilled.75” deep. The Hole will be Counterbored to a.38”diameter and to a depth of.25” Counterbore or Spotface Symbol Depth Symbol Reading a Hole Note The Hole Diameter will be.38” drilled.5 deep. Reading a Hole Note The Hole Diameter will be.38” through the whole block. Reading Thread Notes Threads are dimensioned with the use of local notes. We will discuss two methods: the ISO and the Unified National Thread method. Reading a Unified National Thread Note Identifies coarse or fine Threads per Inch thread. In this case, C for coarse. F is for fine. Major Diameter Reading a ISO Thread Notes This number can be 3,4,5,6,7,8,9. It is the grade of tolerance in the threads from fine to coarse. The H is for allowance: G would be a tight allowance and H is no allowance. Pitch of the threads. Nominal Diameter In Millimeters Prior to THRU, you may have an LH M for Metric for left hand thread. Finally THRU or a depth may be specified. Dimension Guidelines 1. Dimensions should NOT be duplicated, or the same information given in two different ways. Incorrect 1. Dimensions should NOT be duplicated, or the same information given in two different ways. 2. No unnecessary dimensions should be used – only those needed to produce or inspect the part. Incorrect 2. No unnecessary dimensions should be used – only those needed to produce or inspect the part. 3. Dimensions should be attached to the view that best shows the contour of the feature to be dimensioned. Incorrect 3. Dimensions should be attached to the view that best shows the contour of the feature to be dimensioned. 4. Whenever possible, avoid dimensioning to hidden lines and features. Incorrect 4. Whenever possible, avoid dimensioning to hidden lines and features. 5. Avoid dimensioning over or through the object. Incorrect 5. Avoid dimensioning over or through the object. 6. A dimension should be attached to only one view; for example, extension lines should not connect two views. Incorrect 6. A dimension should be attached to only one view; for example, extension lines should not connect two views. 7. Whenever possible, locate dimensions between adjacent views. Incorrect 7. Whenever possible, locate dimensions between adjacent views. 8. Avoid crossing extension lines, but do not break them when they do cross. Multiple extension line crossings may be confused for the outside corner of the part. 9. Whenever possible, avoid sending extension lines through object views. Incorrect 9. Whenever possible, avoid sending extension lines through object views. 10. In general, a circle is dimensioned by its diameter and an arc by its radius. 11. Holes are located by their centerlines, which may be extended and used as extension lines. 12. Holes should be located and sized in the view that shows the feature as a circle. Incorrect 12. Holes should be located and sized in the view that shows the feature as a circle. 13. Do not cross a dimension line with an extension line, and avoid crossing dimensions with leader lines. 13. Do not cross a dimension line with an extension line, and avoid crossing dimensions with leader lines. 14. Leader lines point toward the center of the feature, and should not occur horizontally or vertically. 15. Dimension numbers should be centered between arrowheads, except when using stacked dimensions, and then the numbers should be staggered. Incorrect 15. Dimension numbers should be centered between arrowheads, except when using stacked dimensions, and then the numbers should be staggered. 16. Concentric circles are dimensioned in the longitudinal view, whenever practical. Incorrect 16. Concentric circles are dimensioned in the longitudinal view, whenever practical. Tolerances Variation is Unavoidable No two manufactured objects are identical in every way. Some degree of variation will exist. Engineers apply tolerances to part dimensions to reduce the amount of variation that occurs. ANSI/ASME Standard ANSI/ASME Standard Y14.5 Each dimension shall have a tolerance, except those dimensions specifically identified as reference, maximum, minimum, or stock. The tolerance may be applied directly to the dimension or indicated by a general note located in the title block of the drawing. Tolerances A tolerance is an acceptable amount of dimensional variation that will still allow an object to function correctly. Tolerances A tolerance is an acceptable amount of dimensional variation that will still allow an object to function correctly. Tolerances Tolerances Three basic tolerances that occur most often on working drawings are: limit dimensions, unilateral, and bilateral tolerances. Tolerances Three basic tolerances that occur most often on working drawings are: limit dimensions, unilateral, and bilateral tolerances. Limit Dimensions Limit dimensions are two dimensional values stacked on top of each other. The dimensions show the largest and smallest values allowed. Anything in between these values is acceptable. Limit Dimensions These are limit dimensions, because the upper and lower dimensional sizes are stacked on top of each other. Unilateral Tolerance A unilateral tolerance exists when a target dimension is given along with a tolerance that allows variation to occur in only one direction. Unilateral Tolerance This tolerance is unilateral, because the size may only deviate in one direction. Bilateral Tolerance A bilateral tolerance exists if the variation from a target dimension is shown occurring in both the positive and negative directions. General Tolerances If no tolerances are specified at the dimension level, then general tolerances may be applied by deliberately controlling the number of values past the decimal point on each dimension. Linear Dimensions X.X = ±.020 Angles = ±.5° X.XX = ±.010 X.XXX = ±.005 General Tolerances Tolerances X.X = ±.020 X.XX = ±.010 X.XXX = ±.005 Total Tolerance The total tolerance is a value that describes the maximum amount of variation. Tolerance = .010 Total Tolerance =.020.020.490.500.510 Target Dimension Total Tolerance A measuring device should be able to accurately measure within 1/10th of the total blueprint tolerance identified..020.490.500.510 Target Dimension Tolerances and Measuring In this case, a measuring device should be able to take accurate measurements to within two thousandths of an inch. Total tolerance =.020 1 x = 10x =.020 x =.002 10.020 X = the minimum accuracy of the measuring device Three Types of Fit There are three types of fit that should be considered when working with tolerances. Clearance Fit- have limits of size so prescribed that a clearance always results when mating parts are assembled. Interference Fit- have limits of size so prescribed that an interference always results when mating parts are assembled. Transition Fit- have limits of size indicating that either a clearance or an interference may result when mating parts are assembled. Discussion