Compass Health AI SOP: Control of Non-conforming Products PDF
Document Details
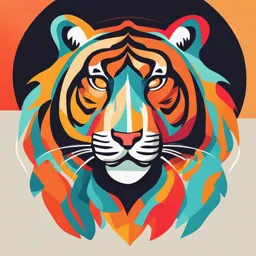
Uploaded by WorkableSteelDrums5546
Tenzin Yangzom , James Baskin
Tags
Summary
This document is a Standard Operating Procedure (SOP) for controlling non-conforming products at Compass Health AI. It details processes for identifying, handling, and disposing of non-conforming medical devices, likely related to medical device manufacturing or quality control. The document covers aspects like rework, scrap, and return to supplier.
Full Transcript
s Compass Health AI SOP: Control of Non-conforming Products Approvals Author Position Role Signature Date DD-MMM-YYYY Tenzin Head of Author 02-Jan-2024 Yangzom QA/RA James Approver...
s Compass Health AI SOP: Control of Non-conforming Products Approvals Author Position Role Signature Date DD-MMM-YYYY Tenzin Head of Author 02-Jan-2024 Yangzom QA/RA James Approver 02-Jan-2024 Baskin COO Revision History Version Date Description 1.0 03-Jan- Initial Release 2024 1 Introduction Safety and effectiveness of our products is paramount at Compass Health Inc. (“Compass”). The ability of a product to conform with required specifications is an important element of achieving that safety and effectiveness. In conjunction, the identification of non-conforming products from the beginning of the process is also key in driving the production of safe and effective medical devices. 1.1 Scope This SOP governs the handling of non-conforming products, both produced by Compass, as well as received by Compass either for input into production, or for elements that may affect product quality, such as test equipment. 2 Applicable and Reference Documents 2.1 Applicable Standards The following standards and regulations are intended to be met by this procedure: ISO 13485:2016 Section 8.3 Control of Nonconforming Product FDA QSR § 820.90 Nonconforming product TG(MD)R Sch1 P1 2, Sch3 P1 1.4(3)(a),(b),(5)(b)(iii), (f) 2.2 Reference Documents Document Title Document # Non-Conformance Form QMS-FRM-0014 Supplier Non-Conformance Report QMS-FRM-0015 SOP: Control of Records QMS-SOP-0003 SOP: Supplier Evaluation and Monitoring QMS-SOP-0016 3 Acronyms and Definitions Table 1: Acronyms Acronym Description WIP Work In Progress MRB Material Review Board DHR Device History Record LHR Lot History Record QA-RA Quality Assurance-Regulatory Affairs Table 2: Definitions Term Meaning A request to permit acceptance of a product that has been Concession manufactured outside specified limits, yet still meets customer Request specifications and can be used without any rework. Non-conforming Product(s) that does not fulfill a specified requirement product Quarantine Area A designated place of isolation for non-conforming products Action taken on a nonconforming product so that it will fulfill the Rework specified DMR requirements before it is released for distribution. 4 Process Roles Role Description Performs initial evaluation to determine the conformance of the product. Commits a final disposition recommendation for QA-RA management approval Reports any open Non-Conformances and active Concessions at each scheduled Quality Management System Review If the product is to be rejected against the supplier, QA-RA will review such rejections and determine whether to raise a Supplier Non-Conformance Report Responsible for notifying customer (or cause customer to be notified) if the concession request impacts the Customer The manager of the department of which the non-conformance is related to. The Responsible Manager is responsible for: Responsible Overseeing the recommended rework to review the method Manager of rework with the QA-RA Verifying that the rework is complete and meets the specification. Determine the validity of, and approve or reject each concession request 5 Control of Non-Conforming Product 5.1 Identification of Non-Conforming Product Any product or material that is found to be suspect, nonconforming and/or contaminated at any point during the manufacturing process is removed from WIP and will be clearly identified with a HOLD Label (Yellow label), either on the product itself, or a containing box as appropriate. QA-RA shall move the product or material to the Quarantine Area, where it will be held awaiting disposition. Product labeled as HOLD shall not be released for sale. 5.2 Disposition of Non-Conforming Product Following detection, identification, and quarantine of product, a Material Review Board (MRB) meeting is convened. The MRB comprises personnel from QA-RA, Management, and, as appropriate to the non-conformance, Engineering, Marketing, and Operations. Initial evaluation by QA-RA is performed to determine whether product or batch should be scrapped. If further discussion is warranted, the MRB shall discuss the issue. A risk assessment shall be performed and specific consideration shall be given to the effect on safety, quality, and effectiveness. The MRB members shall provide recommended disposition. QA-RA shall commit a final disposition recommendation for management approval. Disposition of non-conforming product, described in sections below, will be one of: Rework Scrap Return to supplier Accept by Concession Further investigation and notification of any external party responsible, if applicable 5.3 Rework The Responsible Manager overseeing the recommended rework will review the method of rework with the QA-RA. If it is agreed that the product can be reworked, the REWORK Label (Blue label) is placed on top of the HOLD Label (Yellow label), in such way that it is identifiable that the REWORK (blue) label was placed after the HOLD (yellow) label. The part or lot shall then be placed into the quarantine or other documented area. When the rework method has been agreed, it shall be documented in a work instruction (WI) prior to commencing rework operations. When the rework is complete, the product is re-inspected by the QA-RA and the responsible manager verifying the work is complete and meets the specification. If product is found to be conforming at this time, it is labeled as CLEAR (Green label), and returned to non-segregated storage or inventory. All rework operations shall be documented, including the quantity or identity of reworked product, the personnel conducting the rework, and the date of rework. Product labeled as REWORK shall not be released for sale. Product labeled as CLEAR, may be processed for sale and shipment as with any conforming product. 5.4 Scrap Non-conforming product to be scrapped (destroyed) is affixed with a SCRAP label (Red label). Product for scrap is placed in quarantine until personnel are prepared to conduct scrap operations. All scrap operations shall be documented in the DHR or LHR, including the quantity or identity of scrapped product, the method of product destruction, the personnel conducting the destruction, and the date of destruction. Product labeled as SCRAP shall not be released for sale. 5.5 Return to Supplier If the product is to be rejected against the supplier, QA-RA will review such rejections and determine whether to raise a Supplier Non-Conformance Report (QMS-FRM-0015). Supplier Non-Conformance Reports will serve as input to ongoing SOP: Supplier Evaluation. Some quality problem items will need a Supplier visit to confirm Corrective Actions taken. Product for return to supplier shall be affixed with a RETURN label. Product labeled for RETURN shall not be released for sale. Return of the product shall be documented in the DHR or LHR, including the quantity or identity of product, personnel returning the product, and the date such return was made (i.e. the date the rejected product was shipped from Compass). 5.6 Accept by Concession Acceptance by concession may be permitted when the product has been manufactured outside specified limits, yet performs as intended, is safe and meets all regulatory requirements. 5.6.1 Compass Initiated Concessions Internal requests for acceptance of product into inventory and/or sale under concession shall be reviewed by QA/RA. Such Concession Request shall be documented in the Non- Conformance disposition. QA-RA shall review the nature of the Concession Request with the Responsible Manager, who will determine the validity of, and approve or reject each request. The description of the concession must be concise and accurate, including the period or quantities to be covered. If the request impacts the Customer, the QA-RA shall notify the Customer (or cause customer to be notified), and if required by Customer, submit documentation per their processes. Once final approval has been given by the appropriate signatories the Concession will be distributed to the following as appropriate: Operations Manager Sales Responsible Manager All product manufactured under this Concession must be accompanied by the concession documentation. Product under Concession shall be labeled CONCESSION (Green label with ‘CON’ handwritten on it). Product labeled as CONCESSION, may be processed for sale and shipment as with any conforming product, subject to the additional documentation requirement. 5.6.2 Supplier Initiated Concessions When a supplier requests a Concession, QA-RA shall review the request and decide whether to proceed. If the decision is made to reject the request, QA-RA shall inform the supplier of the decision to reject and dispose of any material affected. If the Concession request is initially accepted, QA-RA will raise a Concession Request per the above process. 6 Returned Medical Devices All medical devices returned from customers will be labeled as HOLD and shall not be released for sale. If a customer identifies a non-conforming product after delivery or use has started, Compass will request the customer to return the device back to the manufacturer’s address. Product returns are considered customer feedback at Compass as per SOP: Feedback and Customer Satisfaction. Further, QA-RA shall determine if further action is warranted in accordance with SOP: Device Recall and Advisory notices and SOP: Medical Device Reporting and Mandatory Problem Reporting. QA-RA shall inspect and determine the final disposition of the returned product as per the dispositions described in this procedure. The investigation and conclusion shall be documented. 8 Process Monitoring QA-RA shall report on any open Non-Conformances and active Concessions at each scheduled Quality System Management Review. 9 Quality Records Record type Description Documentation of all rework operations, including the Rework Operations quantity or identity of reworked product, the personnel Documents conducting the rework, and the date of rework. It is documented in the DHR or LHR Provides all the details of a Concession, including a Concession Request concise description of the Concession and the period or Documentation quantities to be covered. Supplier Non-conformance Raised and completed if a product is to be rejected Record against the supplier All information pertaining to scrapping of any product. Scrap Operations Documents It is documented in the DHR or LHR Non-Conformance Log Log to keep track of all non-conformance records