Connectors for Fixed Partial Dentures PDF 2023
Document Details
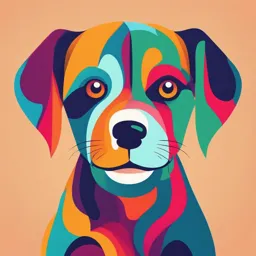
Uploaded by MotivatedAlexandrite
Taibah University
2023
M. Hosny
Tags
Summary
This document provides an overview of connectors for fixed partial dentures (FPDs). It discusses different types of connectors, including rigid and non-rigid connectors, and their applications. It also covers essential aspects of soldering techniques, with detailed information on procedures, materials, and potential issues. The information is presented in a clear manner suitable for dental professionals.
Full Transcript
Connectors for Fixed dental prostheses Presented by Dr. Mohammed Hosny Professor of Fixed Prosthodontics Collage of Dentistry Taibah University 3/18/2023 M.Hosny 2 Outline Definition Types of connectors Soldering Requirement of ideal solder joint Requirements of solder allo...
Connectors for Fixed dental prostheses Presented by Dr. Mohammed Hosny Professor of Fixed Prosthodontics Collage of Dentistry Taibah University 3/18/2023 M.Hosny 2 Outline Definition Types of connectors Soldering Requirement of ideal solder joint Requirements of solder alloy Soldering technique Conclusion 3/18/2023 3 M.Hosny Definition Connectors are those parts of FDP that join retainers and pontics together. 3/18/2023 M.Hosny 4 Types Connectors Rigid Non-Rigid a. Cast connectors b. Soldered connectors c. Welded connectors d. Loop connectors 3/18/2023 a. Precision attachment b. Non precision (rests) M.Hosny 5 Rigid connectors 1. Cast connectors It is a one-piece casting. They are shaped in wax as part of a multiunit wax pattern, before reflowing and investing. 3/18/2023 M.Hosny 6 1. Cast connectors Advantage: Convenient and minimize the number of laboratory steps. Disadvantage: The fit of individual retainers may be affected because distortion more easily results when a multiunit wax pattern is removed from the die. Access to proximal margin is impeded. 3/18/2023 M.Hosny 7 Rigid connectors 2. Soldered connectors Involves the use of intermediate metal with melting temp lower than the parent metal. The parts joined are not melted during soldering. It is indicated in long-span bridge as it is sometimes impossible to transfer the wax pattern without being distorted. 3. Welding connectors The connection is created by melting the adjacent surfaces with heat or pressure. A filler metal with melting temp about the same as that of the parent metal can be used. 3/18/2023 M.Hosny 8 Rigid connectors 4. Loop connectors They are used when an existing diastema is to be maintained. The connector consists of a loop on the palatal of the prostheses connecting adjacent retainers and pontics. 3/18/2023 M.Hosny 9 Non-Rigid Connectors Indication 1. Lone free-standing abutment (pier) with edentulous spaces mesial and distal to it. 2. When it is not possible to prepare two abutments with common path of insertion ( tilted mandibular 2nd molar). 3. Questionable prognosis of an abutment. 3/18/2023 M.Hosny 10 Non-Rigid Connectors 1) Precision attachment They consist of: I. Female component: Prepared within the contours of the retainer. It is placed on the distal surface of the anterior retainer. II. Male component: attached to the pontic. It must be parallel to the path of withdrawal of the distal abutment. Parallelism is achieved by surveyor. 3/18/2023 M.Hosny 11 1) Precision attachment Female component It could be prepared by: a. Free hand in wax pattern b. Using mandrill of a milling machine Male component It could be fabricated of auto polymerizing acrylic resin attached to the pontic wax pattern, then cast. Or use prefabricated plastic components for both female and male component. 3/18/2023 M.Hosny 12 3/18/2023 M.Hosny 13 Non-Rigid Connectors 2) Non precision attachment Occlusal rests, sub-occlusal rests and canine rests (Fixed-supported bridge). They rest either on class II or class III inlay. 3/18/2023 M.Hosny 14 Soldering Uses: 1- Joining components of FDP 2- Building up proximal contacts 3- Repairing casting voids or broken part Requirement of ideal solder joint It should be large enough to prevent distortion or fracture during function. If too large; it will interfere with proper plaque control and may cause metal display. It should be completely concave in peripheral attachment. It should be circular or elliptically shaped in a BL cross-section. It should be centralized by the contact areas, but in anterior teeth they are placed more lingually for esthetic reasons. It should not block the embrasures at interproximal space (hygienic) 3/18/2023 M.Hosny 16 3/18/2023 M.Hosny 17 Principles of Soldering Use solder alloy like parent in terms of composition, carat and color. Wall to soldered should not be less than 0.5mm otherwise deformation will occur. Surface must have adequate metal surface. Gap distance 0.2-0.7mm (business card thickness). All free margins not to be soldered should be covered by the investment. 3/18/2023 M.Hosny 18 Factors affecting success of soldering Procedure 1.The gap distance between the assembled units should be 0.2 to 0.7mm (business card thickness). This gap is important to provide: Compensation for solidification shrinkage. Capillary attraction for the solder alloy. 2. Solder alloy selection 3. Soldering flux and antiflux 4. Soldering investment 5. Mode of heat application 3/18/2023 M.Hosny 19 3/18/2023 M.Hosny 20 Soldered connectors Connectors to be soldered are waxed to the final shape then sectioned. When the components are cast; the surfaces to be joined will be flat Parallel Controlled gap width 0.25mm If gap width increase → decrease soldering accuracy. If gap width decrease → prevention of proper solder flow → incomplete or weak joint. 3/18/2023 M.Hosny 21 3/18/2023 M.Hosny 22 Requirements of solder alloy 1. Fuse safely below the sag or creep temp. of the casting to be soldered. 2. The solder should possess a fusion temp. that is about 80-100oC below that of the metal being soldered. 3. Resist tarnish and corrosion; depends on the similarity of composition of the parent alloy and the solder alloy; if differ it will cause galvanic corrosion. 4. To be free flowing; flow increase by silver and decrease by copper. 5. To match the color of the units to be soldered. 6. To be strong 3/18/2023 M.Hosny 23 Soldering Flux It is applied on the metal surface to remove oxides and prevent their formation so; the solder can spread over the clean metal surface. 3/18/2023 M.Hosny 24 Soldering Flux Borax glass Used with gold alloy due to its affinity for copper oxides. It composed of borax glass, boric acid and silica. Flux is either powder and liquid or paste. New fluxes are available for nongold-based alloys. All fluxes should be kept from contacting porcelain veneer → will cause pitting and discoloration. 3/18/2023 M.Hosny 25 Soldering Antiflux Used to limit the spreading of the solder. It is placed before the flux application. Example Graphite from a pencil is used, yet it evaporates at high temp. Iron oxide (rouge) in a solvent such as turpentine is brushed on the surface. 3/18/2023 M.Hosny 26 Soldering investment They are like casting investment, yet the refractory component in casting investment creates unwanted thermal expansion → excessively separates the units to be joined. So soldering investment contains fused quartz; the lowest thermally expanding form of silica, as their refractory component. Invested units must be correctly gapped; so, when they expand during heating, they don’t touch. 3/18/2023 M.Hosny 27 If the gap between the units to be soldered was small and the units were allowed to touch → distortion and porous and inadequate joints results. If the gap was big; undersized MD FPD widths will result because of the solder solidification shrinkage. 3/18/2023 M.Hosny 28 Soldering technique 1) According to the materials being soldered Soldering of all metal FPD of type III or IV gold; requires the use of low fusing solder (conventional soldering). Soldering of MC units; we can solder the units either before the ceramic application with high-fusing solder (preceramic soldering), or after the ceramic application with low-fusing solder (postceramic soldering). 3/18/2023 M.Hosny 29 Soldering of All-Metal FDP Type III and IV gold retainers are soldered with gold solder with fineness ranging from 615 to 650. Conventional soldering is done using: Gas-air torch Furnace 3/18/2023 M.Hosny 30 Soldering of MC FdP 1. Preceramic soldering: Adv: Allows the connected prostheses to be tried in the mouth before porcelain application. Disadv: Porcelain is applied to a longer structure; which needs support during firing to prevent high temp. deformation. It requires gas-oxygen torch. 3/18/2023 M.Hosny 31 2. Post ceramic soldering Used to join regular gold with MC units in a single FDP; as regular gold will melt if subjected to porcelain fusion temp. . So, all porcelain adjustment and firing must be completed before soldering. 3/18/2023 M.Hosny 32 Adv: Proximal areas are shaped before soldering → look more natural than cast connectors. Firing supports are not needed because components are short. Disadv: It produces strong but brittle joints; as the solder cannot be quenched after soldering. It requires Furnace or gas-air torch. 3/18/2023 M.Hosny 33 Soldering technique 2) According to the technique of soldering A) Free hand soldering technique It is used for building up of deficient proximal contacts or contours or in repairing casting voids in a single unit restoration. Soldering pliers with modified tip 3/18/2023 Holding crown with soldering pliers M.Hosny Solder on the proximal surface surrounded by an antiflux 34 Soldering technique 2)According to the technique of soldering B) Investment soldering technique It is used for assembling components of an FDP. 3/18/2023 M.Hosny 35 Soldering technique Heat sources 1) Torch soldering: Use the reducing zone of the flame. The flame is never concentrated in one area but kept in constant motion; to prevent uneven heat distribution which could result in fracture. *Adv: Maximum visibility, accessibility of adding more solder, possibility of removing the flame as soon as the solder flow. *Disadv: There is uneven heat distribution and the liability of over heating. 3/18/2023 M.Hosny 36 3/18/2023 M.Hosny 37 Heat sources 2) Oven soldering: Furnace or oven soldering is performed under vacuum or in air. A piece of solder is placed in the joint space and the casting is heated using an infrared light. Air firing is preferred with post- ceramic soldering. *Adv: It provides more uniform heating and accurate control of temperature level. * Disadv: Lack of visibility in some ovens. 3/18/2023 M.Hosny 38 3/18/2023 M.Hosny 39 Heat sources 3) Infrared soldering Used for both pre and post ceramic connectors. It is a unit that uses an infrared light as a heat source. The connector area is positioned precisely on the focal point of the reflector that concentrates the heat. 3/18/2023 M.Hosny 40 Heat sources 4) Laser welding: Adv: Laser assembly of FPD reported higher strength and reduced corrosion in comparison to conventional soldering. It is used to join cast titanium components. It is a relatively easy and a time saving technique. Disadv: The high cost of the machine and the need for qualified technicians to adjust the laser parameters. 3/18/2023 M.Hosny 41 Soldering technique Steps of soldering technique Occlusal soldering index by plaster or autopolymerizing resin intraorally or on the working cast. The index must accurately maintain the relationship until the parts of the FDP are embedded in soldering investment. 3/18/2023 M.Hosny 42 Auto polymerizing resin soldering index for ant. restorations due to their thin incisal edges → unstable in the plaster index. 3/18/2023 M.Hosny 43 Apply sticky wax to each casting to maintain its position. Because glazed porcelain is damaged by contact with the investment, the porcelain is protected with a layer of wax. 3/18/2023 M.Hosny 44 Flow utility wax into the joint to prevent the joint from being filled with investment. 3/18/2023 M.Hosny 45 Place boxing wax around the index. Apply soldering investment and after it sets remove the boxing wax. 3/18/2023 M.Hosny 46 Run hot water to remove the wax and then separate the index from the investment. 3/18/2023 M.Hosny 47 Cut a V-shaped notch buccal and lingual to the solder joint; as the solder will be fed to the joint from these notches. 3/18/2023 M.Hosny 48 Use a pencil to draw a heavy line adjacent to the solder joint; it will act as an antiflux. While the casting is still warm, add the flux paste. 3/18/2023 M.Hosny 49 Invested castings are preheated to insure even heating. If not preheated → distortion to the joint and cracking in the porcelain veneer. It can be preheated in an oven or on a burner. 3/18/2023 M.Hosny 50 Apply 2 or 3 pieces of the solder to the lingual embrasure of the joint area. 3/18/2023 Apply the heating source M.Hosny 51 After soldering, allow the FDP to bench cool for 4-5 min then it is quenched; leading to increased hardness and strength of the joint (except MC post-ceramic soldering). Immediate quenching → the FDP to wrap. Not quenching → a brittle joint with no ductility. 3/18/2023 M.Hosny 52 3/18/2023 M.Hosny 53 Conclusion Soldering of Metal ceramic units Pre-ceramic Post-ceramic Before porcelain application Solder below melting temp. of parent alloy but above firing temp. of porcelain. After porcelain application Solder below parents and firing temp.of porcelain. 3/18/2023 M.Hosny 54 Conclusion Indications Pre-ceramic Defect in one retainer only When bridge is too big for accurate one-piece casting Post-ceramic Failure to seat unglazed bridge at try in or final Attaching gold units to metal ceramic units Advantages Pre-ceramic Adjustments can be done before porcelain application 3/18/2023 M.Hosny Post-ceramic No sagging of metal as porcelain is fired over shorter segments 55 Conclusion Techniques Pre-ceramic Phosphate bonded invest. Oxyacetylene torch Rapid cooling (quenching) to improve metal properties Post-ceramic Gypsum bonded invest. Gas-air torch No quenching as this will cause porcelain to fracture Problems Pre-ceramic Lack of oxides at connector area for porcelain bonding Proper proximal contouring and embrasures is difficult Liability to sag on firing 3/18/2023 M.Hosny Post-ceramic Incomplete solder joint due to limited access Porcelain discoloration from flux Porcelain roughening/loss of glaze due investment Cracking of porcelain on heating 56 References: Contemporary of Fixed Prosthodontics. 5th edition. Fundamental of fixed Prosthodontics 4th edition. 3/18/2023 M.Hosny 57