Complete Engineering Theory Book PDF
Document Details
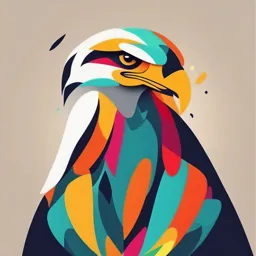
Uploaded by GlimmeringMachuPicchu7010
Ballyhaunis Community School
Tags
Summary
This textbook covers various engineering topics, including metallurgy, materials science, polymers, welding, Iron-Carbon diagrams, and machining. It's designed for Leaving Certificate Engineering students in Ireland, outlining concepts and principles of the subject.
Full Transcript
Ballyhaunis Community School Leaving Certificate Engineering Textbook Metallurgy Where Metals Come From The Periodic Table of Eements........................................................................................... 5 The Atom................................................
Ballyhaunis Community School Leaving Certificate Engineering Textbook Metallurgy Where Metals Come From The Periodic Table of Eements........................................................................................... 5 The Atom........................................................................................................................... 5 States of Matter................................................................................................................ 6 Atomic Bonding................................................................................................................. 6 Crystal Structures.............................................................................................................. 7 Metal Defects.................................................................................................................... 8 Metal Ore Extraction......................................................................................................... 9 Metal Ore Concentration................................................................................................. 12 Materials Science Where Metals Come From Understanding Materials................................................................................................. 14 Non Destructive Testing (NDT)........................................................................................ 17 Mechanical Testing (Destructive Testing)......................................................................... 20 Polymers Where Metals Come From Polymer Materials Science............................................................................................... 28 Manufacturing with Plastics............................................................................................ 35 2 Welding Where Metals Introduction Come From.................................................................................................................... 40 Gas Welding.................................................................................................................... 40 Electric Arc Welding......................................................................................................... 42 Resistance Welding......................................................................................................... 45 Power Control................................................................................................................. 46 Iron Carbon Diagrams Where Metals Come From What is Steel................................................................................................................... 49 Understanding the Iron Carbon Diagram......................................................................... 49 Heat Treatments.............................................................................................................. 52 Pyrometers...................................................................................................................... 55 Cast irons......................................................................................................................... 56 Alloy Steels...................................................................................................................... 57 Machining Where Metals Come From Introduction.................................................................................................................... 59 Turning............................................................................................................................ 59 Milling............................................................................................................................. 65 Precision Grinding........................................................................................................... 69 3 Metallurgy Where Metals Come From Contents The Periodic Table of Eements..............................................................................................................................5 The Atom.............................................................................................................................................................5 States of Matter...................................................................................................................................................6 Atomic Bonding....................................................................................................................................................6 Crystal Structures.................................................................................................................................................7 Metal Defects.......................................................................................................................................................8 Point Defects.................................................................................................................................................................8 Line Defect.....................................................................................................................................................................9 Metal Ore Extraction............................................................................................................................................9 Open Cast Mining........................................................................................................................................................10 Open Pit Mining...........................................................................................................................................................10 Underground Mining...................................................................................................................................................11 Dredging......................................................................................................................................................................11 Solution Mining...........................................................................................................................................................11 Metal Ore Concentration.................................................................................................................................... 12 Magnetic Separation...................................................................................................................................................12 Floatation Separation..................................................................................................................................................12 Pyrometallurgy............................................................................................................................................................13 4 The Periodic Table of Elements Everything that exists today is made up of a variety of different elements. Sometimes these elements are mixed together as is seen in alloy metals or something as simple as the air that we breathe. The periodic table of elements outlines all the elements that we have discovered so far in our world. Many of these elements are metals which are vital to the progression of engineering in modern times. Some of these include; iron, aluminium, chromium, nickel and cobalt. These materials provide a variety of properties that are suited to different tasks whether it be the iron in shipbuilding or tungsten in a light-bulb filament. We can only begin to understand metals when we understand their construction at the smallest possible level. The Atom The atom is the smallest thing that any element can be broken down into. It is made up of what we call a nucleus surrounded by electrons. The nucleus contains positively charged protons and neutrons. Orbiting these are negatively charged particles which we know as electrons. Atoms follow a few simple rules which effect how they behave and combine with other atoms, these are; 1. All atoms are neutral when their quantity of electrons matches the quantity of protons. If electrons are lost the atom will become overall positively charged due to the loss of negative particles. Likewise if electrons are gained the atom will have an overall negative charge. 5 2. All atoms desire to have 2 electrons in their first shell and eight electrons in their second, third, fourth and subsequent shells. Atoms also desire to fill their outer shells. States of Matter For materials to exist they rely on millions of atoms to bond together with each other. Where atoms are very closely packed solids are created (eg. Steel, timber, plastic). If atoms are able to roll over each other with ease, liquids are produced (eg. water). Where atoms are attracted to each other but not strictly bound together a gas is created. Atomic Bonding There are three different ways in which atoms bond to create a material. They are; Covalent bonding Ionic Bonding Metallic Bonding Covalent Bonding Covalent bonding occurs where two or more atoms will share electrons on their outer shell to satisfy the requirement to fill their outer shell. One example is the molecule of water (H2O). Two hydrogen atoms and one oxygen atom make up this molecule. Hydrogen has 1 electron on its outer shell but as discussed above desires to have 2. Oxygen has 6 electrons on its outer shell but again desires to fill this to 8. By sharing their outer electrons both oxygen and hydrogen fill their outer shells and in the process create what is called a covalent bond which is also known as primary bonding. This type of bonding is very strong and difficult to break down. Ionic Bonding Ionic bonding is a weaker type of bond which occurs where ions are created. An ion is a charged atom, it can be negatively or positively charged. All atoms start out neutral as they have a balance of protons and electrons. If an atom loses one or more electrons it becomes positively charged. The converse is also true with negatively charged atoms being created where atoms gain electrons. Table salt (sodium Chloride, NaCl) is an example of an ionic bond. Sodium starts off with one electron in its outer shell and so requires 7 more electrons to fill its outer shell. Chlorine starts with 7 electrons in its outer shell and requires 1 more electron to satisfy its outer shell. It is easier for sodium 6 to give up its outer electron than find 7 more. As a result sodium is now positively charged whilst chlorine becomes negatively changed by gaining the given up electron. The positively and negatively charged ions now have a natural electrostatic attraction to each other. The bond created is a secondary bond, where it occurs in plastics it can be broken down with the addition of heat. Metallic Bonding Metallic bonding as the name suggests is common with metals. Looking at the periodic table of elements it is clear that all the metals tend to generally have a large number of electrons and therefore more outer shells than most atoms. When an atoms electron is far away from its nucleus, that force of attraction between the electron and nucleus is quite weak and the electron may break free from its atom. When this occurs a cloud/sea of free floating electron is created with positively charged (due to the loss of electrons) atoms suspended within. This type of bond gives metals their ability to conduct as conductivity is defined as the flow of heat or electricity (using the flow of electrons) Crystal Structures A crystal is anything that exists in a solid state where the materials atoms take up a crystalline organised and patterned layout. Metals have crystalline structures which can sometimes change which the application of heat. Three or the many structures include Body Centred Cubic BCC Face Centred Cubic FCC Close Packed Hexagonal CPH Body Centred Cubic BCC This arrangement of atoms is based on an imaginary cube. It consists of 9 atoms in total where the atoms are located at each of the 8 corners of the cubic structure and one additional atom at the centre or body of the structure. This structure is repeated millions of times over to creating a solid material. BCC is regarded as a loose packed structure and can be found in steel known as ferrite Face Centred Cubic FCC Here the atomic arrangement although still based on a cube is more closely packed. Again there is an atom located at each corner of the cubic structure with an additional atom located on the centre of each face of the imaginary cube. There are a total of 14 atoms in this structure. It is found in steel at elevated temperatures which is known as austenite. 7 Hexagonal Close Packed HCP The Close Packed Hexagonal structure is based on an imaginary hexagonal prism. 7 atoms are located on the end of each face of the prism with 3 more atoms separating each of the end faces. The structure has a total of 17 atoms in its structure. It is a very close packed structure and can be found in brass. Slip in Metals The term Slip in metals refers to a situation where layers or rows of atoms within the atomic structure of the material are able to slip or slide over each other. Where slip is allowed to occur it yields a ductile material (ie. A material that can easily be stretched without breaking). As FCC and HCP have a tightly packed structure slip can occur easily. In contrast to this BCC which is loose packed does not enable slip to occur very easily Metal Defects Although Metals desire to have 100% perfect crystal lattice structures this is impossible and all materials will contain defects either at a single point or along a line or row of atoms. These flaws in most cases are acceptable and can be accommodated for but if the flaw is more severe it may lead to a crack forming on the surface of the material or worse still, from within the material where it can’t be seen. Cracks have a tendency to grow and eventually lead to a component breaking. Point Defects Vacancy A vacancy defect occurs where there is one or more atoms missing from the crystal lattice structure. A void is created and the material may distort inwards easily due to the defect. Substitution Defect Here a rogue atom or atoms which are different elements to that of the parent material have somehow entered the lattice structure. This contamination may compromise the materials properties by placing stress on the material where the rogue atom is larger than that of the parent material or creating softness where the rogue atom is smaller than that of the parent material. Interstitial Defect 8 An interstice is a Latin word for free space. As the name suggests this defect occurs where a rogue atom finds its way into the lattice structure of a material. It is normally undesirable as it places stress on the material and can make it harder or more brittle than originally intended. Line Defect Dislocation A dislocation is a line defect. With people, a dislocated shoulder is an injury in which your upper arm bone pops out of the cup-shaped socket that's part of your shoulder blade. With materials a dislocation is similar in principle, a flaw where there is an incomplete row of atoms (a dislocation). This flaw starts inside the material but due to a shear pressure acting on the material the flaw will spread through the material until it reaches the surface where a crack usually forms and will probably lead to the eventual failure of the component Metal Ore Extraction To get a piece of timber you cut a tree down and chop it up into sections, and that is it. Metals are more difficult to obtain. All metals are found in ores which are basically a mix of rock and clay with the metal hidden within. These 9 ores can be difficult to locate and also to extract as they are contained below ground and even under lakes or sea beds. There are several ever evolving methods of ore extraction available. Open Cast Mining The most basic form of mining is used where a metal ore is found close to the surface. Heavy plant is used to remove the topsoil and overburden which is concealing the ore. The ore is then excavated and transported for further refinement. The process is very cost effective as the ore is easy to find and remove. It has the disadvantage that entire landscapes can be permanently destroyed. Open Pit Mining Open pit miming is found where an ore is located than exists close to the surface but also continues deep below ground. Over a period of years the ore is gradually removed with the aid of heavy plant and explosives. This is a very effective type of mining but again has very bad environmental effects on the local landscape. Figure 1 worlds deepest pit The 570 m (1870 ft) deep Fimiston Open Pit (or Super Pit), a gold mine off the Goldfields Highway, Western Australia 10 Underground Mining Not the most cost effective method of mining but if a valuable ore is located deep below the surface underground mining may be utilised. Here a mine shaft is constructed and from here a series or tunnels can be made to remove the ore. The visible effect to the landscape is not as negative as open pit or open cast mining. Safety for the operating personnel has always been a concern due to collapses and gas pockets but this is improving with technological advances in engineering. Dredging Not all ores are to be found are on land. Sometimes rives can flush valuable metal ores from the mountains all the way to lakes or seas. Dredging boats can be used to scoop up a river or sea bed and filter out any valuable ores before returning the unwanted waste. The ore can then be transported to land for further refinement. Dredging usually has a negative impact on aquatic life by silting up the water make it impossible for plant and fish life. Solution Mining Solution mining is used with ores that are soluble in water and are located deep underground. A mining plant on the surface drills two bore holes to a pocket of the ore deposit. Water is pumped down one of the bores. The ore dissolves in this water creating a solution which is then forced up to the surface through the second bore hole. The solution is then further refined at the surface. It can be used for uranium or even something as simple as rock salt. 11 Metal Ore Concentration Following the extraction of ores from the ground or underwater they are still just ores and not pure metal until further refinement occurs. A variety of processes are used to reduce and remove the large quantities of waste material (mainly clay and rock) from the ore. Magnetism, water, and heat are some of the things utilised to help in the ore concentration process Magnetic Separation Magnetic separation is a type of ore concentration that is suited to refining iron ore after mining. Following mining the ore will contain a lot of non-iron including clay and rock. To reduce transportation costs it is desirable to remove as much weight as possible. In the process the mined ore is crushed and sent along a conveyor belt. A magnetised roller at the end of the conveyor belt attracts the iron particles to the right whilst the non magnetised waste (rock and clay) falls into a different container to the left. Floatation Separation Flotation separation is a form of hydrometallurgy. Here the ore is placed in a large container with water and a chemical to assist the process. An agitator breaks up and mixes the ore. Air is pumped into the water and creates bubbles. These bubbles rise to the top and because of the chemical the metal particles of the ore attach themselves to the bubbles. A metal rich froth is created at the top of the tank where it can be collected by skimming it off. It is suitable for the recovery of copper and lead from their ores 12 Materials Testing Pyrometallurgy ‘Pyro’ meaning fire or heat refers to the smelting of ores to obtain pure metals. Here the ore is heated to a high Understanding Materials enough temperature to melt the metal that is trapped within the ore. The molten metal separates itself from Non Destructive Testing (NDT) what is now waste, also known as slag. Slag can be used in construction material for certain types of cement so it is Mechanical Testing (Destructive Testing) not a total waste. The metal obtained after this process is usually quite refined but can be further refined using the full array of furnaces available. The furnaces include the blast furnace, basic oxygen furnace, electric arc furnace and open hearth furnace. Contents _Toc428097081 Understanding Materials.................................................................................................................................... 14 Material Properties.....................................................................................................................................................14 Nature of Forces..........................................................................................................................................................16 Tension (Tensile Force)............................................................................................................................................16 Compression (Compressive Force)..........................................................................................................................16 Bending Force..........................................................................................................................................................16 Torsion (Twisting Force)..........................................................................................................................................16 Shear Force..............................................................................................................................................................16 Non Destructive Testing (NDT)............................................................................................................................ 17 Visual Inspection.........................................................................................................................................................17 Liquid Penetrant Test..................................................................................................................................................17 Magnetic Particle Test.................................................................................................................................................18 Eddy Current Test........................................................................................................................................................18 13 Ultrasonic Test.............................................................................................................................................................19 Radiography Test.........................................................................................................................................................19 Mechanical Testing (Destructive Testing)............................................................................................................ 20 Understanding Materials Material Properties In order to understand what causes a material to strong or weak we must have an in-depth knowledge of material properties. Properties determine how materials behave under certain conditions. They include Hardness ‘The ability of a material to resist scratching or indentation’ Hardness is very important for materials where wear and tear is an important consideration. The gearbox of a car is made of many meshing gears. If these gears are not made of hard materials they will wear away very easily. Hardness also implies that a material is quite brittle and for this reason some materials can be sometimes too hard as they may splinter or even shatter like glass. Figure 2 Diamond - Incredibly Hard Toughness ‘The ability of a material to resist impact’ Almost all engineering components will take impacts of different degrees. The suspension bars under a car or the frame of a bicycle take impacts every time they travel down a rough road. If the material used in these components is no tough it may fail and break. Tough materials are usually softer than hard materials and there can be a trade of between hardness and toughness at times Figure 3 A Simple Toughness Test Ductility ‘The ability of a material to be stretched or drawn into wire’ Most metals are ductile but some more so than others. Copper and aluminium can stretch quite well before they break whilst something like cast iron being more brittle is not as ductile. Material may break in two ways; suddenly where they show brittle fracture (they snap) or sometime they stretch a little be the material gives way and this is called ductile fracture. Ductility is also closely related to another property, Malleability – the ability to hammer a material to shape without it breaking. Figure 4 Deformation Without Fracture Elasticity ‘The ability of a material to return to its original shape after deformation’ Elastic bands are obviously good examples of a material showing elasticity, but all materials show some degree of elasticity, even glass. A steel beam may be allowed to flex when under a load or force but will be expected to automatically spring back or return to its original shape when the force has been removed. Every material also has what is known as an elastic limit. This Figure 5 Elasticity - The Ability To Return To is the point beyond which there is no return. If the elastic limit is exceeded Shape the component is either permanently deformed or breaks. Conductivity 14 ‘The ability of a material to allow heat or electricity to flow’ Conductivity is extremely important when dealing with electricity. Gold is one of the best conductors available but cost prohibits its use. For this reason copper is used as it is more affordable. Sometimes the property of conductivity is not desired. If a material is not a conductor it may be termed an insulator. Polymers tend to be good insulators. The casings of many electrical goods (hand drills, jigsaws, steam irons etc.) are usually made from insulating polymers in order to prevent electrical shock if a fault is present in the item. Tensile Strength ‘The ability of a material to resist a tensile load’ This is the maximum tensile force (see below for definition) that can be applied to a material before it will fail and fracture. It is measured kN/mm2. This is the force that is applied per mm2 for the cross section of the material. Common steels tend to have a reasonably high tensile strength with softer materials like copper and aluminium having lower value tensile strengths Figure 6 Cable Under Tension Fatigue Resistance ‘The ability of a material to resist failure due to repeated loading over a period of time’ A material may resist fracture if a small force is applied. However, if this force is removed and then applied again and again over a long period of time the material may shows signs of a small crack which will grow and eventually lead to fracture. Think of the material failing because it is fatigued or ‘tired’ due to pressure or force acting upon it over time. Creep Resistance ‘The ability of a material to resist failure due to a fixed load over a period of time’ As with fatigue failure time is a major consideration with creep failure. The difference is the nature of the force. Whilst fatigue is caused by a repeated on/off force or load creep occurs where a constant steady load acts on the material over a long period of time. Consider a steel cable that supports a heavy load over a long time. The cable may eventually begin to stretch becoming thinner and as result weaker. This will eventually lead to fracture. Glass Transition Temperature ‘The temperature where a material changes from being brittle and glasslike to being soft and flexible’ All materials will display some level of flexibility and ductility at room temperature. We know that if we raise the temperature most materials will become softer and even more flexible. The opposite also applies if we drop the temperature of the working environment for a material. At lower temperatures all materials will reach a point where they will lose their soft and ductile properties and become much more brittle. This is known as the glass transition temperature of the material. The temperature varies for different materials. It is an important 15 consideration in engineering design if a material is to be used in a cold environment like arctic exploration or aeronautics. Nature of Forces All materials that fail will do so because of a specific force acting on them. Forces will differ firstly in terms of magnitude (how strong the load is) but also in nature (how the force acts). The nature of forces will affect different materials in different ways where some materials will easily resist one type of force but if the nature of the force changes the material can easily fail. The ultimate material would be able to resist all the forces below, but this is impossible and as in all engineering the challenge is to find the best possible compromise. Tension (Tensile Force) Tension occurs where two opposing forces act to create a pulling effect. Metals tend to have a reasonably good resistance to tensile force. Steel for example can be used to make load bearing cables that may be used on cranes for lifting heavy loads. Materials like concrete however are very poor in tension and tend to fracture (break) easily even under minor tensile loads. Compression (Compressive Force) Compression occurs where two opposing forces act to create a squeezing effect. Although poor in tension, concrete is one of the best materials available when put under a compressive load. Load bearing walls of buildings are a simple sign of concretes abilities under compressive loads. Bending Force Bending forces are more complex than both tension and compressive forces yet under closer examination actually incorporate both of the above. In a bending force one side of the material is effectively being squeezed (compression) whilst the opposite side is being stretched. Bending forces can easily been recognised in bridges. The difficulty with bridge construction always lay in material selection. Modern construction of bridges often uses reinforced concrete. Reinforced concrete is an amalgamation of traditional concrete combined with steel rods or mesh running through its core. The concrete manages the tensile loads whilst the steel manages the tensile loads. Torsion (Twisting Force) A torsion force may be defined as two twisting forces that act in different directions on the same piece of material. This force is of particular concern on the area of automobile engineering where drive shafts can be used to transfer rotary power from a car’s engine to its wheels. If there is resistance for example the engine is driving the car up a hill but the car naturally wants to roll back down the hill a twisting force is applied to the drive shaft of the car Shear Force Shear forces occur where two opposing forces act on different. The effect of shear can be a sudden failure through the component concerned. To further understand shear consider a shears or scissors. A scissors works where one blade is pressing the paper down and the other blade is pressing the paper up. If enough force is applied the paper shears (or cuts as its otherwise known. In engineering bolts or shafts may shear due to excessive force acting on them 16 Non Destructive Testing (NDT) Non Destructive testing is used for locating both surface and internal flaws in engineered components. Flaws may include cracks, voids or inclusions that may lead to premature fracture of a component. This has implications for safety. The aeronautical industry is heavily reliant on NDT. Components may be required to have a long service life and for this reason routine inspections are carried out to ensure the safety of a component. Unsafe items may then be replaced before a component in turn preventing potential accidents due to component failure. Visual Inspection Visual inspections are the simplest and most important types of non destructive tests used. There are two main categories. Macroscopic Inspection Macroscopic testing uses the power of the human eye with little or no magnification. It is primarily used in the area of quality control in manufacturing industries. The QC process will identify faults or manufacturing defects such as missing fasteners (nuts, bolts, rivets) or poor workmanship. The simple process is important to prevent faulty goods going to market. Microscopic Inspection Where a detailed examination of a material is required a microscope with high magnification may be used. This enables the engineer to locate tiny surface cracks or flaws that may be invisible to the human eye without magnification. This can be effective for small components but very time consuming on larger items. Liquid Penetrant Test This test is used to highlight surface cracks on components that are difficult to identify using the naked eye. The process is widely used in aircraft maintenance repair and overhaul. Figure 1 below shows the process of the liquid penetrant test. The material being tested must first be cleaned so it is free of oil, grease and dirt particles. A liquid dye is sprayed over the material. This liquid will penetrate into surface cracks on the component. The excess liquid is lightly wiped away. Another spray called a developer is sprayed over the component. The developer draws the colour dye from the crack and helps to show greater contrast in colour between the penetrant dye and the component. If flaws are identified it may be decided to repair, replace or leave the component in service. An alternative to the test shown is to use an ultra violet sensitive liquid penetrant. This will show up brightly in a darkened room using an ultraviolet lamp (blacklight) Figure 7 UV Liquid Penetrant Test 17 Figure 8 Liquid Penetrant Testing Procedure Magnetic Particle Test The magnetic particle test utilises the principle that a magnetised component will create a magnetic field. This magnetic field will always have a clear and identifiable pattern. In Fig.2 an electromagnet is used to magnetise the steel test component. Iron filings/dust is then sprayed or sprinkled over the test piece. These filings will arrange themselves in a pattern due to the presence of the magnetic field. If there is a crack on the surface or even inside the material (but close to the surface) this will interrupt the pattern of the magnetic field. Any interruption in the magnetic field pattern is easily identified by a cluster or small lump of iron filings gathering at the area of the flaw. This test can be used in testing engine blocks, piston heads and crankshafts in the automotive industry. Figure 10 Magnetic Particle Testing Figure 9for surfaceofflaws Principle Magnetic Particle Testing Eddy Current Test Eddy current testing also uses the principle of magnetism but unlike the magnetic particle test it is suitable for testing non-ferrous (non iron based, eg. Aluminium, copper, zinc) components. The test equipment consists of an iron rod with a copper coil wrapped around it. An electrical current travels through the coil and this turns the iron rod into an electromagnet. A magnetic field is created around the rod as a result. An oscilloscope is used to measure the strength of the magnetic field. If the iron rod is passed over the test component the invisible magnetic field will penetrate through the component. The density of the component will lead to some resistance of the magnetic field. The oscilloscope is able to measure this resistance. A certain amount of resistance is expected but if there is a flaw inside the material it will Figure 11 Eddy Current Testing Welded Figure 12 Principle of Eddy Current Testing Joint 18 lead to a fluctuation which can be seen on the oscilloscope. Ultrasonic Test Ultrasonic testing utilises the principle of sound reflection and echo. When sound is emitted it will travel and when it meets a surface it will reflect, this is how an echo occurs. Not all sound can be heard by humans, consider dog whistles which use high frequency sound waves. In ultrasonic testing an inaudible high frequency sound wave is emitted from a transducer in the form of a pulse. The sound will travel through the thickness of the material and reflect back to the transducer. A display unit will show how long it took the sound to travel. If there is a flaw inside the material the sound will be unable to travel through the entire thickness of the material and reflect back early. This will show up on the display monitor as a shorter wave journey thus identifying a fault. Results are sometimes difficult to interpret and for this reason skilled operators are required. Figure 13 Ultrasonic Testing Equipment Figure 14 Ultrasonic Testing can be used to inspect joints in railway lines Radiography Test Radiography or X-ray testing is used to identify internal flaws in various components. A radiation source, created by the rapid movement of electrons in a focused direction, is used to penetrate through the test component. An internal image is created on a photographic sensitive piece of film that is placed under the component. The dark areas identify where the path of the x-rays went unhindered with the brighter areas showing where a dense material resisted the x-rays. Any flaws in the material are easily identified by a tone change on the film. Radiography testing is very effective but extremely expensive to put in place. It also carries a radiation risk to its operators. 19 Destructive Testing Mechanical Testing (Destructive Testing) Figure 15 X-ray testing is widely used in the aeronautical industry Figure 16 Principle of X-ray testing Mechanical testing is used to investigate materials properties and find its ultimate breaking point in various situations. This is done by applying various loads and taking readings until the point of the materials destruction. Engineers need to be sure about the loads and stresses that a material can take so that the correct material is chosen for a particular application. It has implications for safety as well as finance. Over engineering can be costly whilst not using a material that can withstand an intended load can lead to catastrophic component failure. One area of particular importance is the aeronautical industry. Here weight is a major issue and engineers are always developing new materials that can save weight, this leads to better performance and a saving on fuel costs. However engineers must understand the limits that these materials can take. Aiding this is Factor of Safety. If a component is designed to withstand a certain load it may be made even stronger than required. If it is made twice as strong as intended this would be a factor of 2, ten times stronger would be 10 and so on. 20 Impact Testing Impact testing is used to determine the toughness of a material, ‘The ability of a material to resist impact’. The principle of the test involves clamping a pre-sized test piece of material in a vice. A pendulum with a blunt striker at its end is raised to a predetermined height. The pendulum is released. The striker fractures/breaks the test piece and continues to travel. If the material was tough the striker will have used most of its energy and will not travel through far past the test piece but if the material is not tough the striker will still hold a lot of momentum and travel through high past the test piece. The swing of the pendulum past the test piece is measured and this determines the toughness of the material. Other properties like brittleness and ductility can be observed from the test depending on how the test piece breaks. Does it snap suddenly or bend before fracture? Two slightly different types of test exist. The Izod Test holds the test piece vertically in a vice whilst the Charpy Test supports the test piece horizontally between two supports. Both tests do essentially the same thing just in a different way. Figure 17 Impact Testing Principles Figure 18 Ductile Fracture (top) Brittle Fracture (centre) Initial Specimen (bottom) Hardness Testing As suggested by the name this test will investigate the hardness value of a material, ‘The ability of a material to resist scratching or indentation’. A hardness testing machine is used. A small piece of test material called a widget is placed on the machine table. An activating lever forces a pointed or spherical indenter into the material at a pre set force. An indent is left on the surface of the material. The basic principle of the test involves measuring the size of the indent and comparing this to a set of special log tables. A large indent is found on soft materials with a small indent indicating that the material is quite hard. The indenter must always be made from an extremely hard material to ensure test result accuracy two main varieties of the test are used today; 21 Vickers Testing uses a square based pyramid shaped indenter. The indent left here is square in shape. The length of the diagonals on the indent is measured and an average is calculated. From this a VHN is calculated (Vickers Hardness Number). Brinell Testing uses a ball shaped indenter. The indent is circular. The diameter of the indent is measured. From this a BHN is calculated (Brinell Hardness Number) Figure 19 Principles of Vickers and Brinell Hardness Tests Fatigue Testing Due to Fatigue, ‘The ability of a material to resist failure due to repeated loading over a period of time’, being so common and sometimes unpredictable engineering will often attempt to simulate in a laboratory the forces and repeated loads that a material will undergo over a long period of time. Testing can be quite basic and easy to carry out. At a basic level it involves supporting a test piece in a vice and repeatedly bending it forward and back at a set load whilst counting how many movements it takes for the component to fracture. Engineers will alter the test to suit the expected usage of their own components. Tensile Testing This is probably the most important of the non-destructive tests. The main outcome of a tensile test is to determine the UTS (Ultimate Tensile Strength) for a material. This is the maximum tensile force that a material can withstand before it fractures. By analysing the results of this test many more properties can be observed including, ductility, brittleness, malleability, toughness, hardness and elasticity. Tensile testing is widely carried out on both metals and polymers. A tensile testing machine is used. A test piece of material is prepared; this is usually flat for polymers or cylindrical bars for metals. The test specimen is clamped within the test machine where it is put under a tensile load. As the load increases the test piece will become gradually longer until it will eventually break. During the course of the test the force (kN) is measured against the extension (mm). A graph is constructed to show these results. Understanding these graphs is important for materials scientists so as to better understand the materials that they will select for a variety of applications Figure 20 Tensile Test Specimen 22 Initially a load extension graph is produced. This graph relates to the specific piece of material that has been tested. As test components can vary in size (diameter and length) it is desirable to create more standardised graphs that will relate to the material type as opposed to a specific test piece. In this case a Stress-Strain graph is produced; they are produced by converting the data achieved from a load extension graph. Material Stress is calculated by taking the force used and dividing by the cross sectional area of the component. Stress is measured in units of kN/mm2. Strain is calculated by taking extension and dividing it by the original length. Strain has no units as it is a ratio or comparison of the materials extension to its original length A tensile test is initiated when the test piece is put under a tensile load. This piece will begin to stretch and for a limited duration of the test this extension may be described as elastic deformation. This means that if the force is removed the material will be able to spring back to its original length. This doesn’t last forever though and different materials display different levels of elasticity. A yield point occurs where the straight section of the graph finishes. From here to the highest point on the graph the material continues to extend uniformly (ie. it get thinner as it gets longer) and the region shows plastic deformation. Here the deformation is permanent; even if the force is removed the material will not return to its original length. The top of the graph shows the ultimate tensile strength or maximum stress that the material can take. After the maximum stress has been reached to material will neck. Necking is where the material thins at a single area or weak spot as it continues to be stretched. This significantly and quickly weakens the material and ultimately leads to fracture of the test piece. Ductile materials will tend to display cup and cone fracture due to their ductility whilst harder materials will display brittle fracture. 23 Figure 22 'Cup and Cone' Fracture Material properties related to tensile Figure 23 Brittle Fracture Figure 21 Tensile Specimen, before and after tests The diagram above shows three tensile tests on a variety of materials. From these results it can be deduced that Brass is a hard and brittle material as displays very little extension even when put under a heavy load. Copper may be described as being soft and ductile as it extends very easily without breaking even when the load is low. Mild steel is a tough yet ductile material. A reasonably high load is required to stretch the material and it readily extends with the force without breaking until it has extended considerably. Young’s Modulus of Elasticity Tensile testing also enables materials scientists to investigate the stiffness of a material. Some materials for good or for bad may be more or less flexible than another material. Something like the front wing of an F1 car will require a stiff and rigid material that is not prone to flex as this will aid the cars down-force. High skyscrapers often require materials that allow for the building to flex in situations of high wind or even earthquakes. A measure of a materials stiffness is known as Young’s modulus of elasticity. It’s measured in units of kN/mm2. Young’s modulus is always calculated within the elastic region of a stress strain graph. Young’s modulus =Stress/Strain. It may also be calculated by finding the slope on a stress-strain or load-extension graph. Figure 25 The front wing must be rigid Figure 24 Skyscrapers require a degree of flexibility 24 Constructing a Load-Extension Graph The results shown below were obtained from a tensile test on a non-ferrous alloy with a 10 mm diameter and 50 mm gauge length. Plot the load-extension diagram and determine: (i) The ultimate tensile strength (UTS) (ii) The 0.1% proof stress. Load 15 25 40 60 80 100 107 108 105 96 (kN) Extension 0.06 0.10 0.16 0.26 0.38 0.65 0.90 1.00 1.20 1.40 (mm) 108 (i) U.T.S. = Max.Load (from graph)/C.S.A (Cross sectional Area of the diameter 10 test piece) = 108 / π x 52 = 1.38kN/mm2 (ii) 0.1% proof stress =Proof Load/CSA 25 Proof Load = 0.1% of 50mm(gauge length) = 50x.001 = 0.05mm = Proof load (draw from.05mm on graph parallel to straight line) = 88kN (from graph) 0.1% proof stress = Proof Load/CSA = 88/ π x 52 = 1.12kN/mm2 Constructing a Stress-Strain Graph The results shown below were obtained from a tensile test on a non-ferrous alloy. Plot the Stress-Strain diagram for the alloy and determine: (i) Young’s modulus of elasticity (ii) The 0.1% proof stress. Stress 45 90 135 200 275 308 335 345 340 (N/mm2) Extension 0.50 1.00 1.50 2.25 3.25 4.00 5.00 6.50 7.50 (x1000) (i) Young’s Modulus = Stress/strain (Any point from straight section of graph) = 90 / 1 = 90kN/mm2 (ii) 0.1% proof stress =line drawn from 1 on strain axis =332 N/ mm2 (from graph) 26 Polymers Materials Science of Polymers Manufacturing with Polymers Contents Polymer Materials Science.................................................................................................................................. 28 Introduction.................................................................................................................................................................28 Categories of Polymers................................................................................................................................................28 Natural Polymers.....................................................................................................................................................28 Thermoplastic Polymers (Thermoplastics)..............................................................................................................29 Thermosetting Polymers (Thermosets)...................................................................................................................30 Elastomers...............................................................................................................................................................31 Additives To Polymers.................................................................................................................................................31 Disposal of Polymers...................................................................................................................................................32 Common Polymers used in Engineering......................................................................................................................34 Manufacturing with Plastics............................................................................................................................... 35 Calendering..................................................................................................................................................................35 Compression Moulding...............................................................................................................................................35 Transfer Moulding.......................................................................................................................................................36 Blow Moulding............................................................................................................................................................36 Vacuum Forming.........................................................................................................................................................37 Extrusion Moulding.....................................................................................................................................................37 Injection Moulding......................................................................................................................................................38 Rotational Moulding....................................................................................................................................................39 27 Polymer Materials Science Introduction The familiar word plastic means ‘capable of being re-shaped or re- moulded’. Not all plastics however are capable of this. For this reason Engineers and materials scientists tend not to refer to these materials as Polymers. Poly is a Greek word meaning many whilst a mer means molecule (molecules are clusters of atoms). Polymers are therefore many molecules connected to each other. These molecules are usually inter-connected along long chains in a scattered and random manner. Figure 26 Microscopic view of molecules joining to create a polymer Polymers have been in existence for a relatively short period of time, less than 200 years, but have become incredibly important and we now rely heavily on a lot of these new materials and the unique properties they bring. Popular materials like timber are produced from trees with metals originating from ores in the ground whilst modern polymers are produced from by-products of the gas and oil refining industry. Figure 27 Samples of polymers that we use every day Categories of Polymers 1. Natural Polymers 2. Thermoplastic Polymers (Thermoplastics) 3. Thermosetting Polymers (Thermosets) 4. Elastomers Natural Polymers Natural polymers have always existed and although there has been much advancement over the last century in synthetic (man-made) polymers, it was only through investigating the properties of natural polymers that modern synthetics were developed. Some examples of natural polymers include; Natural rubber Natural Rubber is cultivated by cutting into the bark of the rubber tree to release its sap like material. Latex is the name given to the sap from the rubber tree. Rubber trees only grow in hot climates like. Thailand and Indonesia have an ideal climate for these plantations. Elastic bands can be made from natural rubber. Rubber may be further refined and modified to improve its properties, this will be discussed later. Shellac A simple material collected from a specific species of beetle called the lac bug. The polymer is hard brittle and leaves a high gloss shine on products. It may be used as a French polish for furniture. 28 Amber Amber is quite simply fossilised tree resin that has become hardened over the period of being fossilised. Amber has been used over centuries in jewellery making due to its attractive translucent colour. Because amber starts life in a softened state fossilised insects may be found in the amber which may add to its appeal. Figure 30 Shellac Producing Beetle Figure 29 Amber has an (lac bug) attractive appeal Figure 28 Natural Rubber Cultivation Thailand Thermoplastic Polymers (Thermoplastics) Thermoplastics are modern synthetic polymers that have been developed over the past century. They include popular materials like acrylic (Perspex), polythene (used for plastic bags) and polypropylene (used for plastic chairs). They are produced by a process called Addition Polymerisation. Figure 32 shows the polymerisation process for polyethylene (plastic bag material). This process begins with a single mer (molecule) of ethylene, C2H4. A double bond exists within the molecule between the two carbon atoms preventing the mer joining with other mers. A free radical (catalyst), a chemical additive, is introduced. This has the effect of breaking the double bond between the carbon atoms. The mer then bonds to another mer and the breaking down of the double bond is relayed onto the end of the chain. The process rapidly repeats itself creating long slender chains of molecules. These chains commence and terminate at various random locations within the material creating what is called an amorphous structure (a random, scattered and disorganised arrangement). Within the structure the mers along the chains are bonded covalently. This form of primary bonding is very strong and extremely difficult to break down. Between the Figure 32 Addition Polymerisation Process Figure 31 Amorphous Structure of Polyethylene different chains or across overlapping chains a weaker type of bonding is found known as secondary bonding or sometimes called Van Der Wall’s Forces, named after the Dutch scientist who discovered them. These bonds unlike the primary bonds can easily be broken down by heat and reform upon cooling. This principle explains why thermoplastic polymers become flexible when heated and rigid when cooled. 29 Thermoplastics can be further engineered to improve their properties by the following processes; Co-Polymers Mixing and combining different types of molecular chains can improve the material by making it harder, softer, more rigid or flexible depending on what is required. This is similar to making alloys (mixing metals). The newly engineered materials will possess new and unique properties as determined by the required material use. Figure 33 Co-Polymers are similar to alloys Branching A linear molecular chain in an amorphous structure will produce a reasonably flexible material. Where a more rigid or firm material is required a catalyst/chemical may be added during polymerisation causing branches to form from each molecular chain. This creates a much firmer material as the different branches mesh together. Figure 34 Linear and Branched chains Crystalline Regions Thermoplastics by their nature have an amorphous structure. These polymers may be modified to include crystalline regions. Crystalline means organised or patterned, this is in contrast to amorphous, random or scattered. Crystalline regions within the structure will give the material more tensile strength in the direction of the aligned chains. Figure 35 Combining amorphous with crystalline Thermosetting Polymers (Thermosets) Thermosets like thermoplastics are fully synthetic. Some common examples of thermosets are Bakelite and epoxy. Thermosets are produced be the process of condensation polymerisation. The name is derived from the process by-product, water or condensation. Unlike the process of addition polymerisation where a single mer is repeatedly joined to identical mers all thermosets will commence with two distinctly different molecules. Figure 37 shows the production of Bakelite (phenol- Formaldehyde), a hard brittle plastic first developed in the early 20th century. The process begins when two molecules of phenol and one molecule of formaldehyde are mixed together. An irreversible chemical reaction takes place. No long chains of polymer are created but a complex crosslinked or networked structure is the result. There is much more primary bonding with even the secondary bonds being replaced by primary bonding crosslinks between adjacent molecules. As no secondary bonding exists thermosets cannot be reheated or remoulded. Their final shape is set during the curing that takes place in the initial moulding process. Thermosets tend to be quite rigid and brittle in comparison to the more flexible (plastic) thermoplastics. 30 Figure 37 Figure 36 Thermosets have a highly crosslinked Phenol+Formaldehyde+Formaldehyde=Phenolformaldehyde structure with all primary bonding (Bakelite)+Water (by product) Elastomers Elastomers are a small category of polymers. As they name suggests they include polymers that are highly flexible or elastic. These polymers can be excessively distorted out of shape but will always return to their original form. Although rubber is a natural polymer it may also be thought of as an elastomer. The internal structure is similar to a crossover between a thermoplastic and thermoset. The structure is amorphous with a small amount of crosslinking between elastic chains. Figure 38 Elastomers always return to shape Additives to Polymers Central to the evolution of polymers is the ability to manipulate these versatile materials to change what they can do and how they look and even how much they cost. The following are added to polymers to change or improve the final product. Colour Pigments Quite simply this is a dye put into the manufacturing process to control the colour of the finished product. It is extremely common in the production of acrylic (Perspex). Fillers Fillers are non-plastic products that can be added to a polymer for different reasons. Sawdust may be added to increase bulk or volume and bring down the cost where a polymer may be expensive. Glass- Fibre may be used as an ingredient in order to improve the strength properties of a material. This leads into the area of composite materials which has started to boom in recent years. Think of Carbon fibre technology in F1 racing. Figure 39 F1 cars use a lot of carbon fibre Plasticisers Certain additives to polymers will improve the flexibility of the product. A simple example would be the lid of a lunch box which needs to be flexible to aid opening and closing of the product. The word plasticiser comes from the word plastic which again means ‘capable of being moulded’ or being flexible Stabilisers and antioxidants Whilst polymers may seem superior to wood as they do not rot or steel as they do not rust, polymers have their own problems. UV or Sunlight can be very harmful to polymers causing them to degrade crack and 31 break. Think of white kitchen goods like a food processor that started out bright white but turns a yellow colour after years sitting on a kitchen counter and may show cracks or become brittle. Stabilisers and antioxidants are chemical additives which attempt to slow down the material degradation process Flame Retardants All polymers have carbon as their main building blocks as does gas, coal, diesel, petrol, and turf all of which are highly flammable meaning that so too are polymers. Certain chemicals added to polymers will inhibit the flammability if a plastic product. This is particularly important as we use more and more plastic items every day. Shoes, jumpers, coats even plastic foam seating used in airlines or some of mix of carpets used in homes. Figure 40 Foam seats on aircraft were once problematic in fire Lubricants Polymers are meted to allow them to be shaped usually by pressing them into a mould. When melted polymers tend to be a lot more viscous (thick) than something like water which can be a challenge when moulding the polymer. Lubricants improve the mouldability of the polymer. Vulcanised Rubber In 1844 after a few years of experimentation with natural rubber Charles Goodyear discovered that adding sulphur to natural rubber and allowing it to cure by heating gave a dramatic new material which was far superior to natural rubber. The sulphur had the effect of promoting crosslinking within the material’s structure converting rubber from a flimsy elastomer to a true thermoset yet maintaining flexibility. The tough new material was used to make things like wellingtons and coats. John Dunlop later used the new material to Figure 41 Natural develop pneumatic tyres (air filled tyres). Rubber+Sulphur=Vulcanised Rubber Disposal of Polymers The reliance of plastics in everyday day life for simple disposable, throw-away items has lead to issues of concern in the disposal of these materials. As they do not degrade simply like wood and can’t easily be re-melted like metals, new and creative means of disposal may need to be explored. There are currently several ways of disposing plastics. 32 Landfill Plastics may sometimes be sent to landfill but cause a major problem as they take much longer to degrade when compared to more traditional materials. Many plastics will remain in-tact hundreds and of years after initial disposal Incineration A lot of traditional waste in other European countries is burned and used to aid in power production. Burning plastics however causes the release of toxic fumes which can be extremely harmful if not monitored and managed properly. Recycle Recycling plastics is more preferable to landfill and incineration. Recycling can be problematic as not all polymers can be remoulded and others that can have a limit the number of times this can happen. Where this is the case sometimes shredding is used creating new modern materials like mats and filler materials used in applications like insulation. Reduce/Reuse Reducing/Reusing plastic items is the most environmentally friendly way of dealing with the issue of disposal. Instead of sending away polymers for processing consumers are becoming more conscious of the problems posed and are increasingly finding other uses for plastics. People can now purchase a lot of refill items and more items cut down on packaging by using concentrates. In Ireland the plastic bag levy has had a positive impact in the reduction of waste polythene. Figure 42 Methods used in the disposal of Plastics 33 Common Polymers used in Engineering Figure 43 Common Polymers in use today Natural Polymers Thermoplastics Thermosets Elastomers Shellac Polyethylene PE Bakelite(Phenol- Natural Rubber Hard shiny polymer from LDPE,HDPE Formaldehyde) Soft and flexible beetle dung. Flexible and tough Hard brittle plastic produced from rubber Eg. furniture polish Low density-plastic bags Eg. Frying pan handles, tree sap High Density-lunch box some plugs and light Eg. Elastic bands switches Natural Rubber Polypropylene PP Vulcanised Rubber Silicone Soft and flexible Tough, Hard wearing Natural Rubber+Sulpher Soft, flexible and produced from rubber Eg. Blue rope, Chairs promotes more waterproof. Can be used tree sap crosslinking. as a sealant Eg. Elastic bands Very tough, wear resistant. Eg, Bathroom sealant Eg. Car Tyres Amber Polytetraflourethylene Polyester Hard and translucent PTFE (Teflon) May also be a fossilised material Heat resistant, Non stick thermoplastic.Hardwearing, e.g. Jewellery Eg. non-stick frying pans tough surface Eg. Plastic gears, brush bristles Polymethylmetacrylate Epoxy PMMA (Acrylic/Perspex) Hard and brittle Versatile, corrosion Used in adhesives/glue resistant, where a resin and hardener tough,inexpensive are mixed Eg. Shop Signs Polyvinvlchloride PVC Versatile, inexpensive, easily worked, tough Eg. Window frames, plumbing, cable trunking Polystyrene PS Tough, flexible, versatile. Foaming agent may be added Eg, packaging, foam cups, insulation 34 Manufacturing with Plastics Looking around you will see how widely plastics are used. A massive variety of shapes and forms are possible. To achieve this we a variety of manufacturing processes. These include; 1. Calendering 2. Compression Moulding 3. Transfer Moulding 4. Blow moulding 5. Vacuum Forming 6. Extrusion Moulding 7. Injection Moulding Calendering Calendering is used in the production of large flat thermoplastic sheets or rubber mats. A billet of heated softened polymer (sometimes granulated polymer is used instead) is fed through a series of heated rollers. The rollers flatten the polymer making it gradually thinner as it passes through the manufacturing process. The flattened sheet is either stored on a roll or fed onto a conveyor belt where it can be cut to length. Figure 44 Calendaring is used to make flat sheets and rubber mats Compression Moulding Compression moulding is widely used in the moulding of rubber products and as part of the car tyre manufacturing process. The process is mostly suited to Thermosets. A measured quantity of polymer billet, the charge, is placed inside an open heated mould. The process is simple where the mould is forced close, usually with the aid of hydraulics, whilst the polymer fills the mould cavity. The mould remains closed whilst the polymer is allowed to cure. The mould then opens and ejector pins or manual labour may be used to help in the removal of the product Figure 45 Car Tyres and other rubber products are manufactured using compression moulding 35 Transfer Moulding Transfer moulding is increasingly being replaced by injection moulding (see further down). It is mostly used with thermosets where complex shapes are required. It is similar to the compression moulding process but has the advantage that it is not vital to measure the charge of polymer billet, the system allows for excess polymer. Polymer is placed in the transfer port. A plunger is then used to force the polymer into the closed mould through the narrow opening at the sprue. The polymer is allowed to set. The mould is then opened and the product can then be removed. Transfer moulding can be used to aid the manufacture bushings and bearing units that comprise of plastics with a metal core. The metal core or base can be placed inside the mould cavity before the polymer is injected. Figure 46 Transfer moulding is used for hard plastics Blow Moulding Blow moulding is exclusively uses thermoplastics. The process is used to make containers that can usually hold liquids like soft drinks, milk cartons and household detergents. A split mould is open and a parison is introduced. A parison is a heated hollow tube of thermoplastic polymer. The split mould closes around the parison, pinching the top closed in the process. Air is blown into the parison from the open end (if a parison is not used a preform is used, as in the video clip). The plastic expands like a balloon to meet the mould walls where it cools and hardens. The mould opens and the product is removed. Figure 47 Blow moulding is used to make plastic bottles 36 Vacuum Forming Vacuum forming is used where large flat sheets of thermoplastic need to be formed into complex shapes. It can be used in the manufacture of bathtubs, Jacuzzi tubs, model making and moulded shop signs. A flat sheet of thermoplastic is pre-heated to may it pliable. The sheet is placed over a mould and sealed at the edges with a clamp. The mould is drilled with a series of small holes to allow air to be sucked out from underneath. A vacuum pump is turned on and the air remaining between the polymer sheet and the mould is removed leaving a vacuum (nothingness). Atmospheric pressure (the weight of air) forces the plastic firmly against the mould. The clamp is released and the plastic is carefully pulled from the mould. Talc or other powders are sometimes used to prevent the plastic sticking to the mould. Figure 48 Vacuum Forming can be used when moulding intricate forms Extrusion Moulding Extrusion moulding is used in the manufacture of polymers of continuous length with uniform cross section i.e. round, square, and hex bars, window frames and garden hose. It is most suitable for thermoplastics. The polymer is fed from the hopper into the barrel. Here the screw mixes the pellets of polymer ad forces them along the length of the barrel. Heaters attached to the barrel, along with the friction created by the action of the help to melt the polymer. The Melt is then pushed, under pressure from the screw, through the die at the end of the machine. The die used determines the shape of the product produced. Extrusion is a continuous operations process with the product being cut to required lengths as it cools after exiting the die. 37 Figure 49 Extrusion moulding process with sample products right Injection Moulding Injection moulding is the most widely used plastics manufacturing process today. It is most suited to thermoplastics but more advanced systems can use a double barrel system to cater for thermosets. Most items we come across every day has probably been injection moulded. Pens, rulers, phone covers, keyboards, lunch boxes are a tiny example of the machines products. The process is similar to extrusion with the main difference being the removal of the extrusion die in favour of a cavity mould to aid in the production of finite (fixed shape) product. Polymer pellets are fed at the hopper into the barrel. The screw mixes the polymer and with the aid of heaters that are attached to the barrel the polymer is melted. The mould must be in the closed position before the entire screw is pushed forward inside the barrel by a hydraulic ram. This injects a fixed quantity of polymer into the mould. The screw is retracted whilst the mould remains closed for a few seconds to allow the product to set. The mould is opened and ejector pins help to remove the product. The process is highly automated and is merely supervised by manual labour. Figure 50 Injection moulding is used in the manufacture of countless plastic products. Chairs, toys, pens, rulers, keyboards...... 38 Rotational Moulding Welding Rotational moulding is used for spherical hollow objects like balls or larger hollow objects like kayaks, children’s toys, storage containers and even those red/white road construction barriers. The principle involves placing granulated polymer into a split mould where it melts. The entire mould is then rotated usually about two axes to help the polymer spread evenly around the inner mould wall. The mould is Fusion Joining of Metals then open and the product removed. A solid shell like item is produced. Figure 51 Rotational moulding is used to produce hollow shell-like plastic products Contents Introduction....................................................................................................................................................... 40 Gas Welding....................................................................................................................................................... 40 Oxy-Acetylene Welding...............................................................................................................................................40 Electric Arc Welding........................................................................................................................................... 42 Manual Metal Arc M.M.A............................................................................................................................................42 Metal Inerth Gas welding M.I.G..................................................................................................................................43 Tungsten Inerth Gas welding T.I.G..............................................................................................................................44 Submerged Arc Welding S.A.W...................................................................................................................................44 Electro Slag Welding....................................................................................................................................................45 Resistance Welding............................................................................................................................................ 45 Resistance Spot Welding.............................................................................................................................................46 Resistance Seam Welding............................................................................................................................................46 Power Control.................................................................................................................................................... 46 39 Transformers...............................................................................................................................................................47 DC Rectifier..................................................................................................................................................................47 Introduction Welding is a permanent metal joining process. Unlike mechanical joining processes (nuts, bolts, screws) which can easily be undone the welding process is not reversible. Welding is a fusion joining process where both parent metals are melted, usually along with filler metal too, these metals then fuse together creating one new component which cannot be parted without a cutting action. The main requirement for any welding process is a suitable heat source which may come in the form of a flame, electric arc or electrical resistance Categories of Welding 5. Gas Welding 6. Electric Arc Welding 7. Electric Resistance Welding Gas Welding There are a few types of welding available using gas power. Butane and propane can be used alone for low heat applications but the most common type of gas welding is oxy –acetylene welding. Oxy-Acetylene Welding Overview Gas welding involves the use of a flammable gas being mixed with air or better still pure oxygen. The gas mixture is ignited at the welding torch where a flame is created. This flame must be sufficient to give enough heat to melt the parent metal component. Oxy- Acetylene welding is the most widely used gas welding process used around the world today. Equipment Oxygen gas bottle Acetylene gas bottle Hoses Torch Regulators Flash back arrestors Filler rod Process Acetylene and Oxygen, controlled by the pressure 40 regulators (these are like taps) travel from the gas bottles through the hoses to the welding torch where the operator can further adjust the gas mixture to give a flame suitable for the particular type of welding. The work components are heated to allow the metal to melt at the joining area. A filler rod (the same material as the parent metal) is usually used to aid the joining of the two metals. Different types of work will require different flame types; Neutral Flame Used for general welding of mild steel. This flame is an efficient balance of oxygen and acetylene. It is recognised by its blue colour and well defined inner cone. The hottest part of the flame is at the tip of the inner cone. Oxidising Flame Used for specialised welding of copper, bronze and brass. This flame created where there is a deliberate excess supply of oxygen. It is recognised by its blue to bright white colour, its pointed shape and sometimes a hissing sound. Carburising Flame Used for specialised welding of Aluminium or Stainless steel. This flame created where there is a deliberate excess supply of acetylene. It is recognised by its dirty orange colour in the form of what is known as an acetylene feather Safety Aspects Colour Coding for equipment hoses/regulators (Oxygen Blue, Acetylene Red) Flash Back Arrestors (Valve that prevents flame travelling back through hoses to the gas bottle) PPE (Personal Protective Equipment, Boots, Apron, Welding Goggles) Well ventilated Area Dissolved Acetylene (Acetylene is very volatile by itself so acetone liquid is stored in the gas bottle. The acetone absorbs the acetylene making it much less volatile) Screwthreads (Regulators and arrestors have srewthreads. Right hand threads are used for oxygen attachments and left hand threads for acetylene attachments. This prevents accidentally mixing up the welding equipment components) DISSOLVED ACETYLENE : If acetylene is compressed into a cylinder, it would explode under high pressure. Acetylene cylinders are packed with a porous material that is 41 filled with acetone, this can absorb 25 times its own volume of acetylene. Electric Arc Welding Electric arc welding utilises the principle of electricity being able to jump over a small gap. When this happens a spark occurs which produces enough heat to melt steel. We call this an electric arc. There are several types of electric arc welding ranging from manual to fully automatic. Manual Metal Arc M.M.A Manual Metal Arc welding is the most basic and common type of electric arc welding. Electric power is provided by a transformer which is connected to a mains electrical power outlet. The transformer reduces the standard 240V to a safer working voltage of approximately 80-100V. An electrode lead allows current to travel to the welding electrode. The electrode is quite simply a metal rod with a chemical powder coating called flux. An electric arc is created between the tip of the electrode and the workpiece. The heat caused by this arc is sufficient to melt the work material and the electrode. As the electrode is consumed the flux coating vaporises and creates a protective gas shield around the weld pool. This shield is required to prevent atmospheric contamination and porosity (air bubbles) inside the weld. This gas shield eventually solidifies again and creates a coating over the weld called slag. The slag has the advantage of allowing the weld to cool slowly and prevent it becoming brittle. The slag must be chipped away afterwards though using a chipping hammer. The operator moves the electrode in the direction where the weld is required. The ground clamp and return lead are required to complete the electrical circuit without which there would be no electric current flow. The process is a skilled manual operation that is very suitable for the welding of mild steel plate. Applications can include forge and garage work. 42 Safety features that minimise MMA welding electrical hazards: MMA welding machines are protected from electrical surges. Welding stations need to be free from dampness. Cables and electrode holders are covered with plastic insulators. Welding machines are earthed. Power supplied can be adjusted to an appropriate level Metal Inerth Gas welding M.I.G Metal Inerth Gas welding can be described as a semi-automatic welding process. The basic principle of welding using an electric arc is similar to that of MMA. Here we start with a direct current (DC) power supply as this makes welding easier. As in MMA the welding rod is consumed but to make the process quicker and easier this rod is on a round reel where a motor and trigger on the gun control its feed to the weld pool. The welding electrode has no flux coating. The weld pool is protected from atmospheric contamination by a gas shield which is provided through the welding gun from a gas bottle, usually CO2 or Aragon as these are non reactive gases. The process is ideal for working on mild steel and has the advantage that it can be used for lighter applications like car panel assembly where MMA would tend to burn holes in the lighter gauge materials. 43 Tungsten Inerth Gas welding T.I.G Tungsten Inerth gas welding is a specialised type of welding that is used for metal with hard outer oxide layers like Aluminium and Stainless Steel. These metals are normally incredibly difficult to weld as their oxide layers prevent full penetration of the weld pool between the parent metals being welded. Here an Alternating Current (AC) is used as this has a peeling and breaking effect on the oxide layer thus allowing the weld pool to form fully. The electrode used in this process is made from tungsten which has a very high resistance to heat and is therefore not consumed. A filler rod which is normally an off-cut of the metal being welded is used. As in MIG a gas bottle provides for a shield that protects the weld pool from atmospheric contamination. This is a very skilled and timely process. It is used for welding of Aluminium bicycle frames and car exhaust tailpipes. Aluminium oxidises very quickly when heated. This tenacious oxide layer is overcome with the use of an inert gas, such as argon, and the cathodic action of the arc on the work-piece. Aluminium can be welded successfully in this way by TIG welding. Submerged Arc Welding S.A.W Submerged arc welding is a fully automated process. It is similar in nature to MIG welding but the operator is replaced using an automatically driven trolley. The electric arc is created at the tip of the electrode wire which is automatically fed from a spool. Granulated flux (grains of flux) is fed to the weld area from a hopper where it submerges the weld pool. The entire welding unit is usually mounted on a trolley which is motor driven along the length of the work being welded. SAW is widely used in water boiler tank construction as well as the manufacture of structural steel beams. 44 Electro Slag Welding Electro Slag welding is a fully automated welding process. This is used for heavy duty welding of thick steel plate. It is similar to MIG welding with the main difference being that the weld pool is enclosed to prevent spill off and multiple electrodes are used due to the heavy nature of the plates being joined. Te plates being welded are deliberately separated and a cavity area is created using copper shoes to the sides and a starting plate at the bottom. This cavity is then basically filled with molten steel. Multiple consumable electrodes, running through guide tubes, provide the filler for the weld whilst also producing enough heat to melt some of the parent metals, this allows for full fusion welding. To assist the welding process and prevent atmospheric contamination a molten slag pool is created, this pool effectively floats on top of the molten steel and rises up as the weld is bei