CMV Training PDF
Document Details
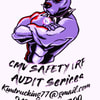
Uploaded by KEEPITMOVING
Keep It Moving Safety & Compliance
Tags
Summary
This document provides an overview of CMV training, focusing on updated Hours of Service (HOS) regulations, electronic logging devices (ELDs), and exemptions. It details provisions for adverse driving conditions, sleeper berth exceptions, and other crucial aspects of the regulations.
Full Transcript
CMV TRAINING CMV Training KIMSCLLC Keep It Moving Safety HOS S Updatess Expands the driving window during adverse driving conditions by up to an additional 2 hours. Requires break of at least thirty consecutive minutes after 8 cumulative hours o...
CMV TRAINING CMV Training KIMSCLLC Keep It Moving Safety HOS S Updatess Expands the driving window during adverse driving conditions by up to an additional 2 hours. Requires break of at least thirty consecutive minutes after 8 cumulative hours of driving time (instead of on duty time) and allows an on-duty/not driving period to qualify as the required break. image of snoring Sleeper Berth Provision Modifies the sleeper berth exception to allow a driver to meet the 10-hour minimum off-duty requirement by spending at least 7 hours of that period in the berth combined with a minimum off-duty period of at least 2 hours spent inside or outside the berth, provided the two periods total at least 10 hours. When used together as specified, neither qualify period counts against the 14-hour driving window. FMCSA revises the hours of service (HOS) regulations to provide greater flexibility for drivers subject to those rules without adversely affecting safety. The Agency expands the short-haul exception to 150 airmiles and allows a 14-hour work shift to take place as part of the exception; expands the driving window during adverse driving conditions by up to an additional 2 hours; requires a 30-minute break after 8 hours of driving time (instead of on-duty time) and allows an on-duty/not driving period to qualify as the required break; and modifies the sleeper berth exception to allow a driver to meet the 10-hour minimum off-duty requirement by spending at least 7, rather than at least 8 hours of that period in the berth and a minimum off-duty period of at least 2 hours spent inside or outside of the berth, provided the two periods total at least 10 hours, and that neither qualifying period counts against the 14-hour driving window. DOT Hours of Service Explained: HOS, ELD, and AOBRD for 2022 meant to provide a general overview of Hours of Service. None of this is intended as legal advice. Check with your local DOT office to ensure that you fully understand What Are the HOS Regulations For? The point of the Hours of Service (HOS) regulations is to keep tired drivers off the road. [Whether these rules do their job or not is up for debate, but for now it looks like they are here to stay. Since each driver is legally responsible for his own logs, it is worth brushing up on the rules to remain compliant and keep your compliance, safety, and accountability (CSA) scores up.] The HOS rules cap the number of hours a driver can be on the road in any given duty cycle so that—in theory— tired drivers are given enough time to rest, eat, sleep, and otherwise be refreshed before they get back on the road. Who’s Required to Use ELDs In short, if you are required to keep Records of Duty Status (RODS), you are probably required to have an ELD. There are some exemptions to this for: Short-haul drivers Drivers who keep RODS for fewer than 8 days in a 30-day period Drive-away-tow-away operations (where you’re delivering the vehicle you’re driving) Vehicles made before the year 2000 Read more about it on the FMCSA’s page here. All drivers in the United States are required to follow these rules, including Canadian and Mexican drivers who cross the United States border to make deliveries. Exemptions With ELDs we got some new exemption statuses. Whereas you may have been able to record your personal driving on the OFF line on paper logs, or considered yourself ON or OFF while in a yard, there’s now the added data with ELDs to show whenever you’ve been driving, and you have to account for this time. Exemption Statuses One of the main things to remember when applying an exemption on an ELD is that you cannot apply one retroactively. Example: You drive on your company’s yard as “Yard Move” time, but forget to change your status to “Yard Move”. You can’t go back and add a “Yard Move” status to those logs, instead you will have to annotate them to explain that they are in error. This rule exists to help avoid cheating on logs. Make sure you apply exemptions when you are supposed to be because a continuous pattern of annotations explaining these kinds of mistakes may look like cheating or loghiding to an officer inspecting your logs. Yard Move (YM) Yard Move (YM) can be applied any time you’re driving off of public roads. This exemption will keep you ON duty while you are driving over 5 MPH so you aren’t losing any of your Drive time while maneuvering your vehicle around a company’s lot. Personal Conveyance (PC)/Personal Use Personal Conveyance (PC) can be applied any time you’re driving for personal reasons and not advancing the load you’re hauling. This would be for driving to and from dinner after you’ve checked into a hotel, finding the nearest safe place to park for a break after your delivery, etc. This was redefined by the FMCSA in 2019 to make it more flexible than it was originally when written for the 2017 ELD Mandate. Although no specifications have been given as to what is a “reasonable distance” traveled under PC (the legal terminology used to explain how far you’re allowed to drive under the exemption), you need to ensure that you annotate your logs to explain where you went under this exemption and why. In other words, if you traveled 250 miles on PC, that could be easily seen in an audit, and you’d better have a really good reason for it! Depending on your ELD provider’s features, your company may be able to set a maximum distance you can drive in PC on a given day. In these cases, your ELD may switch you back into Drive automatically if you exceed the limit set by your company. Geotab’s ELD solution allows administrators to set a maximum PC distance for all drivers, and will automatically switch drivers back into D status if they exceed that limit. The other thing to keep in mind is that PC stops as soon as you cut the ignition on your vehicle. So, if you drive to a restaurant in PC, turn off your vehicle and go eat a meal, and then come back to drive to your hotel for the night, you’ve gotta make sure that you put yourself back into PC before you start driving or you’ll be put into Drive status. This could seriously impact your time if you are on a 10-hour break! Adverse Weather CMV Training KIMSCLLC Keep It Moving Safety This exemption extends your Drive time from 11 hours to 13 hours and your workday from 14 to 16 hours in cases where you encounter weather (e.g. rain, snow, sleet) or traffic conditions that were not known to exist ahead of time. REMINDER: This is for the US Hours of Service rules; the Adverse Weather exemptions for Canada are different. What if You Forget to Apply an HOS Exemption on Your ELD? In short, don’t panic. If you forgot to apply an exemption, you can simply annotate your D and ON logs to explain that you should have been in whichever exemption status you should have chosen. NOTE: Do not do this unless you *really* should have been in an exemption status; if you try to cheat on your logs, this is usually pretty easy to determine based off of your GPS-location records. Sample Log The one downside to messing up your exemption statuses is that it may show up on your time clock and show that you are still out of hours until you take a full 10-hour break. In these cases, you may have to manually keep track of your hours outside of your ELD. Depending on your ELD provider, you may have the ability to ignore erroneous logs so that your time clock isn’t messed up. Geotab has an “Ignore” feature for logs that lets an administrator mark logs to be ignored. The logs still show the violations (along with any annotations you’ve made to explain why they shouldn’t be counted as violations), but the time clock will ignore these so that your ELD will continue to count down your hours without your having to do it manually. Industry Exemptions There are many different industry exemptions for HOS. Here we cover just a couple of the more common ones you may come across. Short-Haul Exemption If you stay within a 150 air-mile radius of your home terminal, you may qualify to run on this exemption. This ruleset limits you to 11 hours of driving within a 14-hour day, requires no break and no paperwork. NOTE: If you leave the 150 air-mile radius or go over the 14-hour workday limit, you are required to keep logs. 16-Hour Exemptions If you’re not longhaul or over-the-road (OTR), the 16-hour exemption may be available to you. This allows one 16-hour workday every duty cycle if you’ve started and ended your day at the same terminal for the previous 5 days. What’s the Takeaway Here? The ELD Mandate looks like it is here to stay. Knowing the rules when it comes to HOS is important for keeping yourself compliant and on the road making money. For further reading, check out some of these other resources: Hours of Service on Wikipedia FMCSA’s ELD FAQs FMCSA’s 2016 Interstate Truck Driver’s Guide to Hours of Service The 14-Hour Window You’ve got 24 hours in a day for: a 14-hour workday, and a 10-hour break. Within your 14-hour workday, you can drive for up to 11 hours. (The extra 3 hours are for breaks, meals, showers, etc.) Once you start your workday (ON or D status), your clock officially begins counting down and cannot be stopped (except under the updated split-sleeper berth provision explained in the Exemptions section below). So, your 14-hour window might look something like this: Example: If you start your workday at 8 AM, you must have all your driving finished by 10 PM. If you start at 8 AM and drive after 10 PM, you will be in violation. Beyond that 14-hour window, you can still work (ON-duty time) but you can’t legally drive again until you take a 10-hour break. The 30-Minute Break Depending on your ruleset, you may be required to take a 30-minute break after 8 cumulative hours of driving time. As of September 29th, 2020, the 30-minute break time must be 30 consecutive minutes of time in an OFF- or ON-duty status. CMV Training KIMSCLLC Keep It Moving Safety Example: If you start your workday at 10 AM and go ON duty for about 20 minutes in total during short increments throughout your drive time, you still need to take a 30-minute break at some point before you have driven for a total of 8 hours. In the picture above, the driver has satisfied the 30-minute break requirement because he went ON duty for 35 minutes before going back to driving. Duty Cycles There are numerous rulesets under the HOS laws for different types of drivers, and which ruleset you’re following will determine your duty cycle. Two of the more common rulesets for property-carrying drivers are the 60-hour/7-day and 70-hour/8-day, and how their cycles work is almost identical. For the 60-hour/7-day ruleset, you can have a total of 60 hours of ON-duty and Drive time within a 7-day period. For the 70-hour/8-day ruleset, you can have a total of 70 hours of ON-duty and Drive time within an 8-day period. Since the main variation between these two rulesets is the number of days in a cycle, and the 60-hour/7-day rule is probably the easiest to understand, we’ll explain a few main points about cycles in more detail using the 60-hour/7-day as our model. The 34-Hour Restart Once every 7 days you can perform a 34-hour restart. This just means that you are OFF duty for a full 34 hours. Once you have spent this time OFF, you will gain your full 60 hours back to start a new 60-hour duty cycle. Rolling Days in a Duty Cycle If you prefer not to take 34 hours OFF, you can use rolling days instead. To understand this, consider the following graph. Let’s say it’s Saturday night, and these are the hours you’ve worked all week: Once midnight on Sunday hits, you will gain back the hours you used the previous Sunday. In this example, that means that you would have 8 hours back on Sunday, plus the 1 hour you had left on your cycle from the week before. On Monday at midnight, you would gain 11 hours back. On Tuesday at midnight, you would gain 5 hours back. And so on… NOTE: Just because you gain hours back at midnight does not mean that you can begin driving again at midnight. For example, if you ended your shift at 8 PM on Saturday night, you would still need your full 10-hour break to be able to start driving again at 6 AM on Sunday morning. CMV Training KIMSCLLC Keep It Moving Safety Sample Countdown Timer with Cycle Time Left from the Geotab Drive App Duty Statuses You’ve got four different duty statuses, each logged on one of four lines: D (Drive) ON OFF SB (Sleeper Berth) RODS Graph in the Geotab Drive App D (Drive) This status is for when you are behind the wheel driving faster than 5 MPH (which is pretty much any time you’re driving). ON This is any time you are working but not behind the wheel going over 5 MPH. So, this can be if you’re: Filing paperwork Loading or unloading Supervising loading or unloading Responsible for a load in general Working at another job These are just a few examples of what is considered ON-duty time. One of the more interesting “gotchas” for an ON-duty status is that ON is technically any time you are working: If you have a side gig outside of your trucking job, any time at your other job counts as ON-duty time. Of course, this makes sense, since the point of the HOS rules is to keep tired truckers off the road. OFF This is any time you spend that you do not meet the requirements for any of the other statuses (that is, whenever you’re not ON, Driving, or in the Sleeper Berth). SB (Sleeper Berth) This is any time that you are in the sleeper berth. Duty-Status Buttons in the Geotab Drive App Exemptions With ELDs we got some new exemption statuses. Whereas you may have been able to record your personal driving on the OFF line on paper logs, or considered yourself ON or OFF while in a yard, there’s now the added data with ELDs to show whenever you’ve been driving, and you have to account for this time. Exemption Statuses One of the main things to remember when applying an exemption on an ELD is that you cannot apply one retroactively. Example: You drive on your company’s yard as “Yard Move” time, but forget to change your status to “Yard Move”. You can’t go back and add a “Yard Move” status to those logs, instead you will have to annotate them to explain that they are in error. CMV Training KIMSCLLC Keep It Moving Safety This rule exists to help avoid cheating on logs. Make sure you apply exemptions when you are supposed to be because a continuous pattern of annotations explaining these kinds of mistakes may look like cheating or log hiding to an officer inspecting your logs. Yard Move (YM) Yard Move (YM) can be applied any time you’re driving off of public roads. This exemption will keep you ON duty while you are driving over 5 MPH so you aren’t losing any of your Drive time while maneuvering your vehicle around a company’s lot. Personal Conveyance (PC)/Personal Use Personal Conveyance (PC) can be applied any time you’re driving for personal reasons and not advancing the load you’re hauling. This would be for driving to and from dinner after you’ve checked into a hotel, finding the nearest safe place to park for a break after your delivery, etc. This was redefined by the FMCSA in 2019 to make it more flexible than it was originally when written for the 2017 ELD Mandate. Although no specifications have been given as to what is a “reasonable distance” traveled under PC (the legal terminology used to explain how far you’re allowed to drive under the exemption), you need to ensure that you annotate your logs to explain where you went under this exemption and why. In other words, if you traveled 250 miles on PC, that could be easily seen in an audit, and you’d better have a really good reason for it! Depending on your ELD provider’s features, your company may be able to set a maximum distance you can drive in PC on a given day. In these cases, your ELD may switch you back into Drive automatically if you exceed the limit set by your company. Geotab’s ELD solution allows administrators to set a maximum PC distance for all drivers, and will automatically switch drivers back into D status if they exceed that limit. The other thing to keep in mind is that PC stops as soon as you cut the ignition on your vehicle. So, if you drive to a restaurant in PC, turn off your vehicle and go eat a meal, and then come back to drive to your hotel for the night, you’ve gotta make sure that you put yourself back into PC before you start driving or you’ll be put into Drive status. This could seriously impact your time if you are on a 10-hour break! Adverse Weather This exemption extends your Drive time from 11 hours to 13 hours and your workday from 14 to 16 hours in cases where you encounter weather (e.g. rain, snow, sleet) or traffic conditions that were not known to exist ahead of time. REMINDER: This is for the US Hours of Service rules; the Adverse Weather exemptions for Canada are different. What if You Forget to Apply an HOS Exemption on Your ELD? In short, don’t panic. If you forgot to apply an exemption, you can simply annotate your D and ON logs to explain that you should have been in whichever exemption status you should have chosen. NOTE: Do not do this unless you *really* should have been in an exemption status; if you try to cheat on your logs, this is usually pretty easy to determine based off of your GPS-location records. The one downside to messing up your exemption statuses is that it may show up on your time clock and show that you are still out of hours until you take a full 10-hour break. In these cases, you may have to manually keep track of your hours outside of your ELD. Depending on your ELD provider, you may have the ability to ignore erroneous logs so that your time clock isn’t messed up. Geotab has an “Ignore” feature for logs that lets an administrator mark logs to be ignored. The logs still show the violations (along with any annotations you’ve made to explain why they shouldn’t be counted as violations), but the time clock will ignore these so that your ELD will continue to count down your hours without your having to do it manually. Industry Exemptions There are many different industry exemptions for HOS. Here we cover just a couple of the more common ones you may come across. Short-Haul Exemption If you stay within a 150 air-mile radius of your home terminal, you may qualify to run on this exemption. This ruleset limits you to 11 hours of driving within a 14-hour day, requires no break and no paperwork. NOTE: If you leave the 150 air-mile radius or go over the 14-hour workday limit, you are required to keep logs. 16-Hour Exemptions If you’re not longhaul or over-the-road (OTR), the 16-hour exemption may be available to you. This allows one 16-hour workday every duty cycle if you’ve started and ended your day at the same terminal for the previous 5 days. What’s the Takeaway Here? The ELD Mandate looks like it is here to stay. Knowing the rules when it comes to HOS is important for keeping yourself compliant and on the road making money. For further reading, check out some of these other resources: A portable ELD must be mounted in a fixed position during commercial motor vehicle (CMV) operation (CMV) and visible to the driver from a normal seated driving position. This information can be found in the ELD Rule section 395.22(g). CMV Training KIMSCLLC Keep It Moving Safety DRIVER’S TIME RECORD Driver’s Name (print) __________________________ Employee No. ___________ Month _______________ Year _________ DRIVERS MAY PREPARE THIS REPORT INSTEAD OF “DRIVERS DAILY LOG” IF INTERMITTENT DRIVERS THE FOLLOWING APPLIES: Shall complete this form for 7 Operates within 100 air-mile radius for CDL or 150 mile radius for non CDL days preceding any day driving drivers. is performed. Returns to headquarters and is released from work within 12 consecutive This includes the preceding hours. month. At least 8 consecutive hours off duty separate each 12 hours of duty. Start End Time Total Driving Truck Date Time “All “All Hours Hours Number Headquarters Duty” Duty” 1 2 3 4 5 6 7 8 9 10 11 12 13 14 15 16 17 18 19 20 21 22 HOS QUESTIONS ASKED AND ANSWERED 1) May a driver, who drops his or her last load at a receiver’s facility use personal conveyance to return to their normal work location (i.e. home or terminal?) No. Returning home or to the terminal from a dispatched trip is a continuation of the trip, and therefore cannot be considered personal conveyance. 2) The guidance allows for “authorized use of a CMV to travel home after working at an offsite location.” What is meant by the term “offsite” when used in this context? The term refers to a location, other than a carrier’s terminal or a shipper’s or receiver’s facility, where a driver works for a temporary period for a particular job. Specifically, this term is intended for construction and utility companies that set up base camps near a major job and operate from there for days or weeks at a time. These remote locations are considered “offsite” locations. Therefore, travel between home and that offsite location is considered commuting time, and qualifies as personal conveyance. 3) Is personal conveyance treated any differently when the driver is hauling hazardous materials? No. There is no restriction on personal conveyance regarding hazardous materials transportation, provided that the driver complies with provisions of 49 CFR parts 177 and 397. 4) Can a driver who claims the short haul exception use personal conveyance? Yes, there is no connection between personal conveyance and the short-haul exception. As always, off-duty time does not extend the 12-hour duty time limitation. 5) How is personal conveyance time calculated in the hours-of-service rules? Time spent under personal conveyance is off-duty time. 6) May a driver use personal conveyance when they run out of available (driving/on-duty) hours? No, except for the one exception described in the guidance where a driver who runs out of hours while at a shipper’s or receiver’s facility may drive from that facility to a nearby, safe location to park, provided that the driver allows adequate time to obtain rest in accordance with daily minimum off-duty periods under the Hours of Service rules before beginning to drive. Personal conveyance is those times where a driver is operating solely for a non-business purpose and cannot be used to extend the duty day. 7) Are there maximum distance time or distance limits for the use of personal conveyance? No. However, it is important to note that the provision in §392.3 of the FMCSRs, prohibiting the operation of a commercial motor vehicle while fatigued, continues to apply. Therefore, a driver must get adequate rest before returning to driving. CMV Training KIMSCLLC Keep It Moving Safety 8) If a driver picks up the commercial motor vehicle from a repair facility once repairs are complete, would the driver be allowed to use personal conveyance to their residence from the repair shop? No, travel for repair and maintenance work is being done in the furtherance of the business and is considered on-duty time. 9) Can a loaded vehicle be used as personal conveyance? Yes. Determining personal conveyance is based on the nature of the movement, not whether the vehicle is laden. 10) Can personal conveyance time be combined with other off-duty time to complete a 10 or 34-hour break? Yes, since PC is off-duty time. However, it is important to note that the provision in §392.3 of the FMCSRs, prohibiting the operation of a commercial motor vehicle while ill or fatigued continues to apply. 11) Can a driver be inspected during personal conveyance? If so, what is the driver’s duty status during the inspection? Yes. Since the driver is still subject to the FMCSRs, the driver or vehicle can be inspected. The driver’s duty status would be “on-duty, not driving.” during the inspection. 1) The guidance allows for “authorized use of a CMV to travel home after working at an offsite location.” What is meant by the term “offsite” when used in this context? May a driver, who drops his or her last load at a receiver’s facility use personal conveyance to return to their normal work location (i.e. home or terminal?) No. Returning home or to the terminal from a dispatched trip is a continuation of the trip, and therefore cannot be considered personal conveyance. 2) The guidance allows for “authorized use of a CMV to travel home after working at an offsite location.” What is meant by the term “offsite” when used in this context? The term refers to a location, other than a carrier’s terminal or a shipper’s or receiver’s facility, where a driver works for a temporary period for a particular job. Specifically, this term is intended for construction and utility companies that set up base camps near a major job and operate from there for days or weeks at a time. These remote locations are considered “offsite” locations. Therefore, travel between home and that offsite location is considered commuting time, and qualifies as personal conveyance. 3) Is personal conveyance treated any differently when the driver is hauling hazardous materials? No. There is no restriction on personal conveyance regarding hazardous materials transportation, provided that the driver complies with provisions of 49 CFR parts 177 and 397. 4) Can a driver who claims the short haul exception use personal conveyance? Yes, there is no connection between personal conveyance and the short-haul exception. As always, off-duty time does not extend the 12-hour duty time limitation. 5) How is personal conveyance time calculated in the hours-of-service rules? Time spent under personal conveyance is off-duty time. 6) May a driver use personal conveyance when they run out of available (driving/on-duty) hours? No, except for the one exception described in the guidance where a driver who runs out of hours while at a shipper’s or receiver’s facility may drive from that facility to a nearby, safe location to park, provided that the driver allows adequate time to obtain rest in accordance with daily minimum off-duty periods under the Hours of Service rules before beginning to drive. Personal conveyance is those times where a driver is operating solely for a non-business purpose and cannot be used to extend the duty day. 7) Are there maximum distance time or distance limits for the use of personal conveyance? No. However, it is important to note that the provision in §392.3 of the FMCSRs, prohibiting the operation of a commercial motor vehicle while fatigued, continues to apply. Therefore, a driver must get adequate rest before returning to driving. 8) If a driver picks up the commercial motor vehicle from a repair facility once repairs are complete, would the driver be allowed to use personal conveyance to their residence from the repair shop? No, travel for repair and maintenance work is being done in the furtherance of the business and is considered on-duty time. 9) Can a loaded vehicle be used as personal conveyance? Yes. Determining personal conveyance is based on the nature of the movement, not whether the vehicle is laden. 10) Can personal conveyance time be combined with other off-duty time to complete a 10 or 34-hour break? Yes, since PC is off-duty time. However, it is important to note that the provision in §392.3 of the FMCSRs, prohibiting the operation of a commercial motor vehicle while ill or fatigued continues to apply. 11) Can a driver be inspected during personal conveyance? If so, what is the driver’s duty status during the inspection? Yes. Since the driver is still subject to the FMCSRs, the driver or vehicle can be inspected. The driver’s duty status would be “on-duty, not driving.” during the inspection. 12) The term refers to a location, other than a carrier’s terminal or a shipper’s or receiver’s facility, where a driver works for a temporary period for a particular job. Specifically, this term is intended for construction and utility companies that set up base camps near a major job and operate from there for days or weeks at a time. These remote locations are considered “offsite” locations. Therefore, travel between home and that offsite location is considered commuting time, and qualifies as personal conveyance. CMV Training KIMSCLLC Keep It Moving Safety 13) Is personal conveyance treated any differently when the driver is hauling hazardous materials? No. There is no restriction on personal conveyance regarding hazardous materials transportation, provided that the driver complies with provisions of 49 CFR parts 177 and 397. 14) Can a driver who claims the short haul exception use personal conveyance? Yes, there is no connection between personal conveyance and the short-haul exception. As always, off-duty time does not extend the 12-hour duty time limitation. 15) How is personal conveyance time calculated in the hours-of-service rules? Time spent under personal conveyance is off-duty time. 16) May a driver use personal conveyance when they run out of available (driving/on-duty) hours? No, except for the one exception described in the guidance where a driver who runs out of hours while at a shipper’s or receiver’s facility may drive from that facility to a nearby, safe location to park, provided that the driver allows adequate time to obtain rest in accordance with daily minimum off-duty periods under the Hours of Service rules before beginning to drive. Personal conveyance is those times where a driver is operating solely for a non-business purpose and cannot be used to extend the duty day. 17) Are there maximum distance time or distance limits for the use of personal conveyance? No. However, it is important to note that the provision in §392.3 of the FMCSRs, prohibiting the operation of a commercial motor vehicle while fatigued, continues to apply. Therefore, a driver must get adequate rest before returning to driving. 18) If a driver picks up the commercial motor vehicle from a repair facility once repairs are complete, would the driver be allowed to use personal conveyance to their residence from the repair shop? No, travel for repair and maintenance work is being done in the furtherance of the business and is considered on-duty time. 19) Can a loaded vehicle be used as personal conveyance? Yes. Determining personal conveyance is based on the nature of the movement, not whether the vehicle is laden. 20) Can personal conveyance time be combined with other off-duty time to complete a 10 or 34-hour break? Yes, since PC is off-duty time. However, it is important to note that the provision in §392.3 of the FMCSRs, prohibiting the operation of a commercial motor vehicle while ill or fatigued continues to apply. 21) Can a driver be inspected during personal conveyance? If so, what is the driver’s duty status during the inspection? Yes. Since the driver is still subject to the FMCSRs, the driver or vehicle can be inspected. The driver’s duty status would be “on-duty, not driving.” during the inspection. Vehicle Maintenance Inspection Basics A maintenance inspection should check the obvious components, such as lights and wipers, as well as hard-to-see components that drivers overlook or cannot check. The key is for the carrier to ensure that when their vehicle goes on the road, it’s 100 percent compliant and safe. Check all lights for function and address any light-related complains from the driver. Gauge and measure the tread depth on all tires. Repair or replace any tire with a defect or reported as having a defect by the driver. Check all brake lines on the vehicle for rubbing and damage. Check the brake components at each wheel end, including: Brake lines: Look at line conditions, connections, rubbing, etc. Brake chamber (or brake cylinder if the vehicle has hydraulic brakes): Look at the condition, mounting, connections, and check for evidence of leakage. Connecting hardware: Look at all that is applicable, including pushrod, clevis, pins, slack adjuster, S-cam and bushings, mounting “spider,” rollers, shoes, linings, and drum. Look at the condition, mounting, connections, presence of locking pins, etc. Check the brake adjustment on all wheels. Check the frame for cracks, damage, loose fasteners, and other problems. Check all of the driveline components, such as the transmission, differentials, yokes, u-joints, driveshafts, retainers, etc., for any damage, looseness, or excessive wear. Inspecting the Brake System Conduct a full system check on the brake system, which includes: Leaks: Chock the wheel and release the parking brakes. Apply the service brakes and turn the engine off. Watch the gauge and listen for any air leaks. If a leak is present, the technician should locate and repair it. Air warning: Turn the key on and pump the brake down until the low-air warning light activates. The light should activate by 60 psi. Button pop out: Pump the brakes until the parking and trailer supply button pops out. Close the tractor protection valve and activate the spring brakes, which are acting as the emergency brakes in this case. Parking/emergency brakes: With the button still out and chocks removed, attempt to move the vehicle by placing it in the lowest gear and trying to ease it forward. With a tractor-trailer, once air pressure has returned to normal, also check the tractor and trailer separately by applying the parking brakes to one unit while the other is released. Service brakes: Release all parking brakes and make sure the vehicle rolls freely. Apply the service brakes when five miles per hour is reached and then release the brakes. This should allow the vehicle to roll freely. ABS key on check: Turn the vehicle off for 30 to 60 seconds. Turn the key on and verify the ABS warning lights on the vehicle are activated and then turn them off. This indicates the warning lights are working and the self-check was passed. If the vehicle has hydraulic brakes: Leaks: Pump the brake pedal three times and keep the brakes applied. After the third pump, the pedal should not “fade”, remaining firm and in place. Warning: Turn the key on and verify that the brake warning light is not on. Power assist backup: If the vehicle is equipped with a power brake assist unit, verify that the backup motor is activated when the key is turned on. Parking brake: Apply the parking brake, if not already applied, and attempt to move the vehicle by placing it in the lowest gear and easing forward. CMV Training KIMSCLLC Keep It Moving Safety Service brakes: Release all parking brakes and make sure the vehicle rolls freely (brakes all released). Apply the service brakes when five miles per hour is reached and the release the brakes, verifying the service brakes release and the vehicle once again rolls freely ABS key on check: Turn the vehicle off for 30 to 60 seconds. Turn the key on and verify the ABS warning lights on the vehicle activate and then turn off. This indicates the warning lights are working and the self-check was passed. Customer Name: Unit # Mechanic: Date: Next PM Due On: ¾ Vehicle Maintenance Requirements The following frequently asked questions (FAQs) were developed to highlight vehicle maintenance requirements for foreign motor carriers operating in cross-border transportation in the United States. The FMCSA has published a significant number of vehicle maintenance related FAQs for all motor carriers operating a commercial motor vehicle in the United States, therefore please refer to the FMCSA website for additional vehicle maintenance related FAQs. PERIODIC VEHICLE INSPECTION Q1: Do vehicles inspected under a periodic Canadian or Mexican inspection program comply with the FMCSA periodic inspection standards? A1: Yes. The FMCSA has determined that the periodic inspection programs required by all of the Canadian Provinces and Mexico's Secretaría de Comunicaciones y Transportes (SCT) defined in the Norma Oficial Mexicana (NOM, or Official Mexican Standard) NOM-068-SCT-2-2014 are comparable to, or as effective as, the periodic inspection requirements contained in the FMCSRs - Appendix G. DRIVER VEHICLE INSPECTION REQUIREMENTS Q1: How does the Final Rule published on December 18, 2014, by the FMCSA that rescinded the requirement that commercial motor vehicle (CMV) drivers operating in the United States in interstate commerce, except drivers of passenger-carrying CMVs, submit, and motor carriers retain, the driver vehicle inspection reports (DVIR) when the driver has neither found nor been made aware of any vehicle defects or deficiencies (no-defect DVIR) impact U.S drivers operating in Canada? A1: This change only applies to operations in the United States only. To continue to comply with Canadian National and Provincial regulations, U.S.-based motor carriers need to complete and retain DVIRs when operating in Canada regardless of whether or not defects are noted. Commercial Motor Vehicle Maintenance and Inspection Program Maintenance and Inspection Program Index 1. Maintenance and Inspection Program a. Appendix 1 – Daily Vehicle Inspection Report (DVIR) b. Appendix 2 – Preventative Maintenance Inspection Report c. Appendix 3 – Annual CMV Inspection Form (also known as appendix G) d. Appendix 4 – CMV Maintenance File (one used for each CMV) e. Appendix 5 – CMV Maintenance Work Order (one used each time CMV work is performed by our “in house” Maintenance Department) f. Appendix 6 – Brake Inspector Qualification Sign Off Form (required for every “in house” mechanic working on brakes) g. Appendix 7 – Vehicle Service Due Status Report h. Appendix 8 – Annual Inspector Qualification Sign Off Form (required for every “in house” mechanic performing CMV annual inspections) i. Appendix 9 – DVIR Ispection Procedure – North America CMV Training KIMSCLLC Keep It Moving Safety MAINTENANCE AND INSPECTION PROGRAM TRUCKS, TRUCK-TRACTOR AND TRAILERS Introduction: Sample Trucking’s Commercial Motor Vehicle (CMV) Maintenance and Inspection program is critical in meeting the expectations of our customers, the motoring public, the Federal Motor Carrier Safety Regulations and our bottom line profitability goals. Management understands that investing in proper CMV preventative maintenance provides many benefits. These include: Reduced Crashes – Proper CMV maintenance will substantially reduce accidents caused by brake, tire, steering, and other mechanical component failures. Reduced Breakdowns – Preventive maintenance minimizes equipment failure, increases equipment uptime and customer satisfaction as on time delivery’s increase. Reduced Maintenance – Properly scheduled CMV maintenance inspections provide opportunities to make minor repairs and adjustments that will help prevent premature wear and identify mechanical failures before they become catastrophic failures. This attention will reduce maintenance costs significantly to the Company. Improved Driver Morale – Sample Trucking takes pride in keeping our equipment safe and in top operating condition for our people. As a result, our driver’s take pride and responsibility in driving safely and handling the equipment with care and professionalism. CSA Scores and Public Perception – CSA Program/SMS scores are critical in fostering a public perception that Sample Trucking offers safe and reliable transportation services. This is fostered by our requirement of keeping clean and well maintained equipment. In addition, our employees and equipment represent our company image and reflect our safety minded company culture. To better understand CMV maintenance it is important to recognize there exists three basic types of vehicle maintenance in use today. These are: 1. Demand Maintenance- where repairs and service are given only when a problem arises, has high costs due to premature failure. 2. Crisis Maintenance- that is applied when a vehicle has “broken down” while in service, thus requiring management to act swiftly and represents the highest cost of maintenance as repairs are unscheduled and work is completed in outside shops at higher costs with unknown quality. 3. Preventive Maintenance- where services and repairs are provided before operational problems interfere with our daily business responsibilities. This has the lowest costs as equipment is maintained in a reliable state with work being performed “in house”. As a result, Sample Trucking focuses on Preventive Maintenance and supports it as a critical component necessary to our fleets operation. Components of a Preventative Maintenance Program The preventive maintenance and inspection program will address the following areas: ¾ Driver Daily Vehicle Inspection Reports (DVIR); ¾ Greasing Interval/Visual Inspections; ¾ Preventative scheduled maintenance; ¾ Annual inspections; ¾ Record keeping of all inspections, repairs and maintenance performed Any component identified as being in need of adjustment, repair and/or maintenance will be maintained and/or repaired as required. The records documenting the repairs and/or maintenance will be submitted to the maintenance manager and retained within the appropriate CMV maintenance file. Sample Trucking will conduct regular and continuous maintenance inspections and repairs in accordance with the following schedule: Inspection Type Vehicle Inspection Interval Comments Type (State Mileage, Time or Hours) Daily Trip Trucks, Complete written Daily Trip Inspection: Tractors, Every 24 hours Inspection form as required. Trailers Record all defects and document all repairs. Greasing Trucks: Every Week Use Mobil 1 Synthetic/Visual Interval/Visual Inspect Inspection: Tractors: Every Week Use Mobil 1 Synthetic/Visual Inspect Trailers: Every Week Use Mobil 1 Synthetic/Visual Inspect Oil Change Trucks: Every 18k MI ~ 2 Use Mobil 1 Semi Synthetic Interval: months 15w/40 Tractors: Every 18k MI ~ 2 Use Mobil 1 Semi Synthetic months 15w/40 Trailers: NA - *Except Reefers *Use Mobil 1 Semi Synthetic 15w/40 PM Scheduled Trucks: Every Month See it's PM Schedule for CMV Maintenance / Tractors: Every Month See it's PM Schedule for CMV Inspection: Trailers: Every Month See it's PM Schedule for CMV Annual Inspection: All Types Appendix G - Required every 12 (Truck, Annually months before expiration - to be Tractor, completed by a Certified or Trailers) Qualified Inspector Driver Vehicle Inspection Report (DVIR) CMV Training KIMSCLLC Keep It Moving Safety As outlined in Part 396.11, Sample Trucking requires every CMV driver to fill out the DVIR, both Pre- and Post Trip inspection, on all equipment 10,001 lbs. GVW and larger, including the trailer being pulled, if applicable. Sample trucking has elected to continue documenting the written DVIR’s daily. We recognize, going beyond, the FMCSA rescinding the written requirement when no defects are found, is necessary to the safe and reliable operation of our fleets CMVs. As a result, this written DVIR shall include the elements below and cover at least the following parts and accessories as shown in Appendix 1, Driver Vehicle Inspection Report x Operators will fill out the DVIR (Driver Vehicle Inspection Report) book, both Pre- and Post Trip inspection, on all equipment 10,001 lbs. GVW and larger, including the trailer being pulled, as applicable. x At the beginning of each day (Pre-Trip Inspection), the driver should visually inspect the CMV and complete only the header information in the inspection book, i.e. Carrier: address, Date: 1/1/12 and the Truck and Trailer numbers 007. Unless there is a problem found nothing else needs to be done. If a problem is found immediately to report the problem to your dispatcher and the maintenance department, to get the repair work order made, the repairs completed, all prior to using the CMV. x At the end of each day the operator will need to perform a thorough visual inspection (Post Trip Inspection) and complete the remaining fields on the DVIR form. The original (white / top copy) copy of the inspection book will be turned in to the Maintenance Manager so the DVIR completion can be recorded. x Any DVIR that has a defect documented on it must have the white copy go to the Maintenance Department, so repairs can be performed. Maintenance will fill out their work order, leaving the DVIR white copy with the CMV for the driver to review. o If problems are found only check those items that apply, you can make comments in the comment section, at the bottom of the DVIR form, regarding the problems found. Only those problems associated with the safe operations off the CMV and DVIR requirements should be recorded. If needed, place original DVIR form (white / top copy) back in vehicle on the dash or seat of the vehicle so mechanic can find it, make repairs and sign-off on those repairs. o Truck Number, Odometer/mileage and Driver Name are required. x The carbon (yellow) copy will remain in the book. o If no safety items are found or recorded on the DVIR, leave all check boxes blank. Turn in the original (white / top copy) copy for record keeping to clerical along with your normal trip paperwork.. x DVIR repairs will be scheduled and repairs performed immediately, unless a repair required cannot be complete in the time available. If a CMV cannot be repaired in the time available, the CMV will be pulled from service until the resources and repairs can be completed. o When repairs cannot be performed our “in house” personnel or by an external service provider, the CMV will be parked in the “out of service” lot. Only when all repairs have been completed can the vehicle be returned to operation. x Once the repairs are completed, the Maintenance Personnel or external service mechanic will sign off on the DVIR form (white / top copy) and the copy still attached in the inspection book (yellow / carbon copy), and leave the DVIR inspection on the driver’s seat for repair verification and inspection by the next driver. x Once the repairs are complete and noted by a certified mechanic the next driver must verify the repairs are completed. As the driver is starting the Pre-trip inspection, he/she should first check and verify the repair have been completed from the previous day. x If satisfied with the repairs, the driver must sign the DVIR inspection and submit the DVIR form to the Maintenance Manager for review and filing. x If unsatisfied with the repairs, the driver must talk to the Maintenance Manager, Supervisor or on duty mechanic until repairs are made to everyone’s satisfaction or vehicle is safe and legally compliant to operate. x Additional Information o Post-Trip Inspection is the VERY IMPORTANT; all problems found throughout the day that effect the DOT Vehicle inspection should be noted. o Pre-trip should be a review of vehicle condition and to verify all the repairs turned in prior to the per-trip have been resolved. o DVIR completion is only required if the truck or trailer is currently being utilized. o Drivers name/signature must be legible, in case of additional information is required. o Current DVIR Inspection books should remain in the truck at all times. o Completed DVIR books (Yellow Copy) must be kept, until completed, in the vehicle. Once the inspection book is completed and all the original (white / top copy) copies have been turned in the book can be discarded. o Completed DVIR Forms (Original White Copy) must be kept for 3 months plus current. o No repairs other than that defined by the DVIR book should be noted on the DVIR form, unless the repairs needed affect the safe operation of the vehicle. o Sample Trucking Maintenance Manager will inspect the DVIR forms received and maintain a copy of each truck and trailers DVIR (Original White Copy) reports for 3 months plus current. Maintenance and Record Keeping: Sample Trucking will maintain the following records pertaining to each commercial vehicle used in our trucking business. 1. An identification of the vehicle, see Appendix 4, CMV Maintenance File, including; a. The Vehicle Identification Number b. The unit number c. The make of the vehicle, and d. The model of the vehicle CMV Training KIMSCLLC Keep It Moving Safety e. The year of manufacture of the vehicle f. The tire size the vehicle is equipped with 2. A record of the inspection of the CMV will document the repairs, lubrication and maintenance for the vehicle, see Appendix 5 CMV Maintenance Work Order, including; a) The nature of the inspection or work performed on the vehicle, and b) The date on which that inspection or work took place and the odometer or hubometer reading on the vehicle at that time; c) Notices of defect received from the vehicle manufacturer and the corrective work done on the vehicle in relation to those notices; d) DVIR Sample Trucking shall maintain these records at our home terminal. We shall ensure that the records required to be maintained under this section are true, accurate and legible. DVIRs will be retained for the month they are created and an additional 3 months. The other records identified above will be retained for the month they are created and an additional 14 months. All records will be kept for 6 months after the vehicle is retired or disposed of. A person authorized by Sample Trucking to conduct DVIRs shall certify on the DVIR that any major defect has been repaired/corrected or certifies on the report that repair/correction is unnecessary. A truck driver shall not drive or be permitted to drive until all major or safety defects have been repaired. Greasing Interval/Visual Inspection: The Maintenance Department is responsible to ensure the CMV is greased and visually inspected weekly by Sample Trucking maintenance personnel. If any defects or issues are found, complete the CMV Maintenance Work Order, Appendix 5. Once repairs are made, turn into the Maintenance Manager for review and filing into the proper CMV’s maintenance file. Oil Change Interval: The Maintenance Department is responsible to ensure the CMV receives proper oil change and fluid checks by Sample Trucking maintenance personnel. Document the work performed on the CMV Maintenance Work Order, see Appendix 5. Once repairs are made, turn into the Maintenance Manager for review and filing into the proper CMV’s maintenance file. PM Scheduled Maintenance / Inspection: The Maintenance Department is responsible to ensure the CMV is receiving its preventative maintenance (PM) per its unique preventative maintenance schedule or the manufacturer’s recommendations. Optional to use appendix 7, Vehicle Service Due Status Report. If brake adjustment or work is necessary, a Sample Trucking’s certified maintenance personnel authorized to perform brake adjustments and/or repairs must be used. 1. See Appendix 6 - Brake Inspector Qualification Sign Off Form (required for every “in house” mechanic working on brakes) 2. See Appendix 7- Vehicle Service Due Status Report Form. In addition, all PM work is documented using the CMV Maintenance Work Order, Appendix 5. Once repairs are made, turn into the Maintenance Manager for review and filing into the proper CMV’s maintenance file. Annual Inspection: The Maintenance Department is responsible to ensure the CMV receives it’s Annual Inspection, see Appendix G, by Sample Trucking’s certified or authorized maintenance personnel qualified to perform Annual Inspections, 1. Appendix 8 – Annual Inspector Qualification Sign Off Form Document the Annual Inspection on the CMV Maintenance Work Order, Appendix 5. Once repairs are made, turn into the Maintenance Manager for review and filing into the proper CMV’s maintenance file. CMV Training KIMSCLLC Keep It Moving Safety Instructions: Write Initial in Appropriate Boxes Below Repaired Greased Comments & Inspected TASKS TO BE PERFORMED Okay Adjusted Lubed Parts List A Engine 1. Change oil and filter 2. Change fuel lines and tank cap 3. Check fuel filter (25,000 mil) 4. Check air filter if needed 5. Check spark plugs 6. Check distributor cap & rotor 7. Pressure test cooling system 8. Check all hoses under pressure 9. Check all belts & tens loners 10, Check water pump and fan bearing 1 1 0 Check complete exhaust system 12 Check for engine oil leaks B. Under The Hood Fluid Levels 1. Radiatoæ note strength 2 Brake 3. Steering 4. Windshield washer 5. Automatic transmission 6. Rear end fluid 7. Check AC Freon level (blows cold) C. Chassis Repaired Greased Comments & Inspected TASKS TO BE PERFORMED Parts List Okay Adjusted Lubed 1. Check steering play 2. Check power steering hose 3. Check steering pitman arm, drag link & idler arm 4. Check tie rod ends 5. Check front springs 6. Check front shocks 7. Check ball joints 8. Check rear springs 9. Check rear shocks 10. Check bel' housing bolts 1 1 * Check transmission mounts 12. Check U-joints & grease 13. Check carrier bearings 14. Check slip joint & grease 15 Check wheels and axle seals E. Brakes 1. Check for fluid leaks 2. Check front pads & rotors 3. Check rear brakes & adjustment 4. Check parking brake operation Wheelchair Lift & ADA Repaired Greased Comments & Inspected TASKS TO BE PERFORMED Okay Adjusted Lubed Parts List Check wheelchair lift & operation CMV Training KIMSCLLC Keep It Moving Safety 2 Check chair lift fluid level 3. Check chair lift control card 4. Check wheelchair tie downs & straps 5M Check seats & seat belts F. Drivability Checks 1. Check window glass and operation 2 Check emergency exits 3. Check mirrors, sport mirrors & brackets 4. Check wiper blades 5 Check if washer fluid sprays 6, Check heater & AC fans 7. Check heater, AC & defrost controls & Check accelerator & linkage 9. Check & lube all hinges, latches & locks 1(). Check & lube passenger doors 1 1 Check fuel tank & mounting 12. Check tire condition & match 13. Check tire rims & lug nuts 14. Check tire inflation 15. Check mud flaps G. Safety I Emergency items Repaired Greased Comments & Inspected TASKS TO BE PERFORMED Okay Adjusted Lubed Parts List l u Fire extinguisher 2. First aid kit 3. Operating flashlight 4. Reflective triangles 5. Ice scraper (season applicable) 6. Blanket 7 s Toolkit H. Wrap-Up 1. Check for leaks 2 Recheck oil level 3, Wash engine & chassis if applicable 4. Install next PM due mileage in pocket 5. Note any other repairs needed PART 396 - INSPECTION, REPAIR, AND MAINTENANCE Authority: 49 U.S.C. 504, 31133, 31136, 31151, 31502; sec. 32934, Pub. L. 112-141, 126 Stat. 405, 830; sec. 5524, Pub. L. 114-94, 129 Stat. 1312, 1560; and 49 CFR 1.87. Source: 44 FR 38526, July 2, 1979, unless otherwise noted. Editorial Note Editorial Note: Nomenclature changes to part 396 appear at 66 FR 49874, Oct. 1, 2001. § 396.1 Scope. (a) Every motor carrier, its officers, drivers, agents, representatives, and employees directly concerned with the inspection or maintenance of commercial motor vehicles must be knowledgeable of and comply with the rules of this part. (b) Every intermodal equipment provider, its officers, agents, representatives, and employees directly concerned with the inspection or maintenance of intermodal equipment interchanged or offered for interchange to motor carriers must be knowledgeable of and comply with the rules of this part. (c) This part does not apply to “covered farm vehicles,” as defined in 49 CFR 390.5, or to the drivers of such vehicles. (d) The rules in this part do not apply to “pipeline welding trucks” as defined in 49 CFR 390.38(b). [73 FR 76823, Dec. 17, 2008, as amended at 78 FR 16195, Mar. 14, 2013; 81 FR 47722, July 22, 2016] § 396.3 Inspection, repair, and maintenance. (a) General. Every motor carrier and intermodal equipment provider must systematically inspect, repair, and maintain, or cause to be systematically inspected, repaired, and maintained, all motor vehicles and interm CMV Training KIMSCLLC Keep It Moving Safety (1) Parts and accessories shall be in safe and proper operating condition at all times. These include those specified in part 393 of this subchapter and any additional parts and accessories which may affect safety of operation, including but not limited to, frame and frame assemblies, suspension systems, axles and attaching parts, wheels and rims, and steering systems. (2) Pushout windows, emergency doors, and emergency door marking lights in buses shall be inspected at least every 90 days. (b) Required records. Motor carriers, except for a private motor carrier of passengers (nonbusiness), must maintain, or cause to be maintained, records for each motor vehicle they control for 30 consecutive days. Intermodal equipment providers must maintain or cause to be maintained, records for each unit of intermodal equipment they tender or intend to tender to a motor carrier. These records must include: (1) An identification of the vehicle including company number, if so marked, make, serial number, year, and tire size. In addition, if the motor vehicle is not owned by the motor carrier, the record shall identify the name of the person furnishing the vehicle; (2) A means to indicate the nature and due date of the various inspection and maintenance operations to be performed; (3) A record of inspection, repairs, and maintenance indicating their date and nature; and (4) A record of tests conducted on pushout windows, emergency doors, and emergency door marking lights on buses. (c) Record retention. The records required by this section shall be retained where the vehicle is either housed or maintained for a period of 1 year and for 6 months after the motor vehicle leaves the motor carrier's control. [44 FR 38526, July 2, 1979, as amended at 48 FR 55868, Dec. 16, 1983; 53 FR 18058, May 19, 1988; 59 FR 8753, Feb. 23, 1994; 59 FR 60324, Nov. 23, 1994; 73 FR 75824, Dec. 17, 2008] § 396.5 Lubrication. Every motor carrier shall ensure that each motor vehicle subject to its control is - (a) Properly lubricated; and (b) Free of oil and grease leaks. § 396.7 Unsafe operations forbidden. (a) General. A motor vehicle shall not be operated in such a condition as to likely cause an accident or a breakdown of the vehicle. (b) Exemption. Any motor vehicle discovered to be in an unsafe condition while being operated on the highway may be continued in operation only to the nearest place where repairs can safely be effected. Such operation shall be conducted only if it is less hazardous to the public than to permit the vehicle to remain on the highway. § 396.9 Inspection of motor vehicles and intermodal equipment in operation. (a) Personnel authorized to perform inspections. Every special agent of the FMCSA (as defined in appendix B to this subchapter) is authorized to enter upon and perform inspections of a motor carrier's vehicles in operation and intermodal equipment in operation. (b) Prescribed inspection report. The Driver Vehicle Examination Report shall be used to record results of motor vehicle inspections and results of intermodal equipment inspections conducted by authorized FMCSA personnel. (c) Motor vehicles and intermodal equipment declared “out-of-service.” (1) Authorized personnel shall declare and mark “out-of-service” any motor vehicle or intermodal equipment which by reason of its mechanical condition or loading would likely cause an accident or a breakdown. An “Out-of-Service Vehicle” sticker shall be used to mark vehicles and intermodal equipment “out-of-service.” (2) No motor carrier or intermodal equipment provider shall require or permit any person to operate nor shall any person operate any motor vehicle or intermodal equipment declared and marked “out-of-service” until all repairs required by the “out-of-service notice” have been satisfactorily completed. The term operate as used in this section shall include towing the vehicle or intermodal equipment, except that vehicles or intermodal equipment marked “out-of-service” may be towed away by means of a vehicle using a crane or hoist. A vehicle combination consisting of an emergency towing vehicle and an “out-of-service” vehicle shall not be operated unless such combination meets the performance requirements of this subchapter except for those conditions noted on the Driver Vehicle Examination Report. (3) No person shall remove the “Out-of-Service Vehicle” sticker from any motor vehicle or intermodal equipment prior to completion of all repairs required by the “out-of-service notice.” (d) Motor carrier or intermodal equipment provider disposition. (1) The driver of any motor vehicle, including a motor vehicle transporting intermodal equipment, who receives an inspection report shall deliver a copy to both the motor carrier operating the vehicle and the intermodal equipment provider upon his/her arrival at the next terminal or facility. If the driver is not scheduled to arrive at a terminal or facility of the motor carrier operating the vehicle or at a facility of the intermodal equipment provider within 24 hours, the driver shall immediately mail, fax, or otherwise transmit the report to the motor carrier and intermodal equipment provider. (2) Motor carriers and intermodal equipment providers shall examine the report. Violations or defects noted thereon shall be corrected in accordance with § 396.11(a)(3). Repairs of items of intermodal equipment placed out-of-service are also to be documented in the maintenance records for such equipment. (3) Within 15 days following the date of the inspection, the motor carrier or intermodal equipment provider shall - (i) Certify that all violations noted have been corrected by completing the “Signature of Carrier/Intermodal Equipment Provider Official, Title, and Date Signed” portions of the form; and (ii) Return the completed roadside inspection form to the issuing agency at the address indicated on the form and retain a copy at the motor carrier's principal place of business, at the intermodal equipment provider's principal place of business, or where the vehicle is housed for 12 months from the date of the inspection. [73 FR 76824, Dec. 17, 2008, as amended at 75 FR 17252, Apr. 5, 2010; 77 FR 28451, May 14, 2012; 78 FR 58485, Sept. 24, 2013; 81 FR 47731, July 22, 2016] § 396.11 Driver vehicle inspection report(s). (a) Equipment provided by motor carrier. (1) Report required. Every motor carrier shall require its drivers to report, and every driver shall prepare a report in writing at the completion of each day's work on each vehicle operated, except for intermodal equipment tendered by an intermodal equipment provider. The report shall cover at least the following parts and accessories: (i) Service brakes including trailer brake connections; (ii) Parking brake; (iii) Steering mechanism; (iv) Lighting devices and reflectors; (v) Tires; (vi) Horn; (vii) Windshield wipers; (viii) Rear vision mirrors; (ix) Coupling devices; (x) Wheels and rims; (xi) Emergency equipment. (2) Report content. (i) The report must identify the vehicle and list any defect or deficiency discovered by or reported to the driver which would affect the safety of operation of the vehicle or result in its mechanical breakdown. If a driver operates more than one vehicle during the day, a report must be prepared for each vehicle operated. Drivers are not required to prepare a report if no defect or deficiency is discovered by or reported to the driver. (ii) The driver must sign the report. On two-driver operations, only one driver needs to sign the driver vehicle inspection report, provided both drivers agree as to the defects or deficiencies identified. (3) Corrective action. (i) Prior to requiring or permitting a driver to operate a vehicle, every motor carrier or its agent shall repair any defect or deficiency listed on the driver vehicle inspection report which would be likely to affect the safety of operation of the vehicle. (ii) Every motor carrier or its agent shall certify on the driver vehicle inspection report which lists any defect or deficiency that the defect or deficiency has been repaired or that repair is unnecessary before the vehicle is operated again. (4) Retention period for reports. Every motor carrier shall maintain the driver vehicle inspection report, the certification of repairs, and the certification of the driver's review for three months from the date the written report was prepared. (5) Exceptions. The rules in this section shall not apply to a private motor carrier of passengers (nonbusiness), a driveaway-towaway operation, or any motor carrier operating only one commercial motor vehicle. (b) Equipment provided by intermodal equipment provider. (1) Report required. Every intermodal equipment provider must have a process to receive driver reports of, and each driver or motor carrier transporting intermodal equipment must report to the intermodal equipment provider or its designated agent, any known damage, defects, or deficiencies in the intermodal equipment at the time the equipment is returned to the provider or the provider's designated agent. The report must include, at a minimum, the following parts and accessories: (i) Brakes; (ii) Lighting devices, lamps, markers, and conspicuity marking material; (iii) Wheels, rims, lugs, tires; (iv) Air line connections, hoses, and couplers; (v) King pin upper coupling device; (vi) Rails or support frames; (vii) Tie down bolsters; (viii) Locking pins, clevises, clamps, or hooks; (ix) Sliders or sliding frame lock. (2) Report content. (i) Name of the motor carrier responsible for the operation of the intermodal equipment at the time the damage, defects, or deficiencies were discovered by, or reported to, the driver. (ii) Motor carrier's USDOT number; intermodal equipment provider's USDOT number, and a unique identifying number for the item of intermodal equipment. (iii) Date and time the report was submitted. (iv) All damage, defects, or deficiencies of the intermodal equipment reported to the equipment provider and discovered by, or reported to, the motor carrier or its driver which would (A) Affect the safety of operation of the intermodal equipment, or (B) Result in its mechanical breakdown while transported on public roads. (v) The signature of the driver who prepared the report. (3) Corrective action. (i) Prior to allowing or permitting a motor carrier to transport a piece of intermodal equipment for which a motor carrier or driver has submitted a report about damage, defects or deficiencies, each intermodal equipment provider or its agent must repair the reported damage, defects, or deficiencies that are likely to affect the safety of operation of the vehicle. (ii) Each intermodal equipment provider or its agent must certify on the original driver's report which lists any damage, defects, or deficiencies of the intermodal equipment that the reported damage, defects, or deficiencies have been repaired, or that repair is unnecessary, before the vehicle is operated again. (4) Retention period for reports. Each intermodal equipment provider must maintain all documentation required by this section, including the driver report and the certification of repairs on all intermodal equipment, for a period of three months from the date that a motor carrier or its driver submits the report to the intermodal equipment provider or its agent. [44 FR 38526, July 2, 1979, as amended at 45 FR 46425, July 10, 1980; 53 FR 18058, May 19, 1988; 59 FR 8753, Feb. 23, 1994; 63 FR 33279, June 18, 1998; 73 FR 76824, Dec. 17, 2008; 74 FR 68709, Dec. 29, 2009; 77 FR 34852, June 12, 2012; 77 FR 59828, Oct. 1, 2012; 78 FR 58485, Sept. 24, 2013; 79 FR 75449, Dec. 18, 2014; 83 FR 16227, Apr. 16, 2018; 85 FR 50793, Aug. 18, 2020] § 396.12 Procedures for intermodal equipment providers to accept reports required by § 390.42(b) of this chapter. (a) System for reports. Each intermodal equipment provider must establish a system for motor carriers and drivers to report to it any damage, defects, or deficiencies of intermodal equipment discovered by, or reported to, the motor carrier or driver which would - (1) Affect the safety of operation of the intermodal equipment, or (2) Result in its mechanical breakdown while transported on public roads. (b) Report content. The system required by paragraph (a) of this section must include documentation of all of the following: (1) Name of the motor carrier responsible for the operation of the intermodal equipment at the time the damage, defects, or deficiencies were discovered by, or reported to, the driver. (2) Motor carrier's USDOT number; intermodal equipment provider's USDOT number, and a unique identifying number for the item of intermodal equipment. (3) Date and time the report was submitted. (4) All damage, defects, or deficiencies of the intermodal equipment must be reported to the equipment provider by the motor carrier or its driver. If no defect or deficiency in the intermodal equipment is discovered by or reported to the driver, no written report is required. (5) The signature of the driver who prepared the report. (c) Corrective action. (1) Prior to allowing or permitting a motor carrier to transport a piece of intermodal equipment for which a motor carrier or driver has submitted a report about damage, defects or deficiencies, each intermodal equipment provider or its agent must repair the reported damage, defects, or deficiencies that are likely to affect the safety of operation of the vehicle. (2) Each intermodal equipment provider or its agent must certify on the original driver's report which lists any damage, defects, or deficiencies of the intermodal equipment that the reported damage, defects, or deficiencies have been repaired, or that repair is unnecessary, before the vehicle is operated again. (d) Retention period for reports. Each intermodal equipment provider must maintain all documentation required by this section, including the driver report and the certification of repairs on all intermodal equipment, for a period of three months from the date that a motor carrier or its driver submits the report to the intermodal equipment provider or its agent. [73 FR 76824, Dec. 17, 2008, as amended at 74 FR 68709, Dec. 29, 2009; 77 FR 34852, June 12, 2012; 83 FR 16227, Apr. 16, 2018] § 396.13 Driver inspection. Before driving a motor vehicle, the driver shall: (a) Be satisfied that the motor vehicle is in safe operating condition; (b) Review the last driver vehicle inspection report if required by § 396.11(a)(2)(i); and (c) Sign the report to acknowledge that the driver has reviewed it and that there is a certification that the required repairs have been performed. The signature requirement does not apply to listed defects on a towed unit which is no longer part of the vehicle combination. [44 FR 76526, Dec. 27, 1979, as amended at 48 FR 55868, Dec. 16, 1983; 63 FR 33280, June 18, 1998; 85 FR 50793, Aug. 18, 2020] § 396.15 Driveaway-towaway operations and inspections. (a) General. Every motor carrier, with respect to motor vehicles engaged in driveaway-towaway operations, shall comply with the requirements of this part. Exception: Maintenance records required by § 396.3, the vehicle inspection report required by § 396.11, and the periodic inspection required by § 396.17 of this part shall not be required for any vehicle which is part of the shipment being delivered. (b) Pre-trip inspection. Before the beginning of any driveaway-towaway operation of motor vehicles in combination, the motor carrier shall make a careful inspection and test to ascertain that: (1) The tow-bar or saddle-mount connections are properly secured to the towed and towing vehicle; (2) They function adequately without cramping or binding of any of the parts; and (3) The towed motor vehicle follows substantially in the path of the towing vehicle without whipping or swerving. (c) Post-trip inspection. Motor carriers shall maintain practices to ensure that following completion of any trip in driveaway-towaway operation of motor vehicles in combination, and before they are used again, the tow-bars and saddle-mounts are disassembled and inspected for worn, bent, cracked, broken, or missing parts. Before reuse, suitable repair or replacement shall be made of any defective parts and the devices shall be properly reassembled. [44 FR 38526, July 2, 1979, as amended at 53 FR 49410, Dec. 7, 1988; 53 FR 49968, Dec. 12, 1988; 78 FR 58485, Sept. 24, 2013; 84 FR 51435, Sept. 30, 2019] § 396.17 Periodic inspection. (a) Every commercial motor vehicle must be inspected as required by this section. The inspection must include, at a minimum, the parts and accessories set forth in appendix A to this part. The term commercial motor vehicle includes each vehicle in a combination vehicle. For example, for a tractor semitrailer, full trailer combination, the tractor, semitrailer, and the full trailer (including the converter dolly if so equipped) must each be inspected. (b) Except as provided in § 396.23 and this paragraph, motor carriers must inspect or cause to be inspected all motor vehicles subject to their control. Intermodal equipment providers must inspect or cause to be inspected intermodal equipment that is interchanged or intended for interchange to motor carriers in intermodal transportation. (c) A motor carrier must not use a commercial motor vehicle, and an intermodal equipment provider must not tender equipment to a motor carrier for interchange, unless each component identified in appendix A to this part has passed an inspection in accordance with the terms of this section at least once during the preceding 12 months and documentation of such inspection is on the vehicle. The documentation may be: (1) The inspection report prepared in accordance with § 396.21(a), or (2) Other forms of documentation, based on the inspection report (e.g., sticker or decal), which contains the following information: (i) The date of inspection; (ii) Name and address of the motor carrier, intermodal equipment provider, or other entity where the inspection report is maintained; (iii) Information uniquely identifying the vehicle inspected if not clearly marked on the motor vehicle; and (iv) A certification that the vehicle has passed an inspection in accordance with § 396.17. (d) A motor carrier may perform the required annual inspection for vehicles under the carrier's control which are not subject to an inspection under § 396.23(a)(1). An intermodal equipment provider may perform the required annual inspection for intermodal equipment interchanged or intended for interchange to motor carriers that are not subject to an inspection under § 396.23(a)(1). (e) In lieu of the self-inspection provided for in paragraph (d) of this section, a motor carrier or intermodal equipment provider responsible for the inspection may choose to have a commercial garage, fleet leasing company, truck stop, or other similar commercial business perform the inspection as its agent, provided that business operates and maintains facilities appropriate for commercial vehicle inspections and it employs qualified inspectors, as required by § 396.19. (f) Vehicles passing periodic inspections performed under the auspices of any State government or equivalent jurisdiction in the Canadian Provinces, the Yukon Territory, and Mexico, meeting the minimum standards contained in appendix A to this part, will be considered to have met the requirements of an annual inspection for a period of 12 months commencing from the last day of the month in which the inspection was performed. (g) It is the responsibility of the motor carrier or intermodal equipment provider to ensure that all parts and accessories on commercial motor vehicles intended for use in interstate commerce for which they are responsible are maintained at, or promptly repaired to, the minimum standards set forth in appendix A to this part. (h) Failure to perform properly the annual inspection required by this section shall cause the motor carrier or intermodal equipment provider to be subject to the penalty provisions of 49 U.S.C. 521(b). [73 FR 76825, Dec. 17, 2008, as amended at 81 FR 47732, July 22, 2016; 83 FR 22881, May 17, 2018; 86 FR 57077, Oct. 14, 2021] § 396.19 Inspector qualifications. (a) Motor carriers and intermodal equipment providers must ensure that individuals performing annual inspections under § 396.17(d) or (e) are qualified as follows: (1) Understand the inspection criteria set forth in part 393 and appendix A to this part and can identify defective components; (2) Are knowledgeable of and have mastered the methods, procedures, tools and equipment used when performing an inspection; and (3) Are capable of performing an inspection by reason of experience, training, or both as follows: (i) Successfully completed a Federal-or State-sponsored training program or have a certificate from a State or Canadian Province that qualifies the individuals to perform commercial motor vehicle safety inspections, or (ii) Have a combination of training or experience totaling at least 1 year. Such training or experience may consist of: (A) Participation in a commercial motor vehicle manufacturer-sponsored training program or similar commercial training program designed to train students in commercial motor vehicle operation and maintenance; (B) Experience as a mechanic or inspector in a motor carrier or intermodal equipment maintenance program; (C) Experience as a mechanic or inspector in commercial motor vehicle maintenance at a commercial garage, fleet leasing company, or similar facility; or (D) Experience as a commercial motor vehicle inspector for a State, Provincial or Federal government. (b) Motor carriers and intermodal equipment providers must retain evidence of that individual's qualifications under this section. They must retain this evidence for the period during which that individual is performing annual motor vehicle inspections for the motor carrier or intermodal equipment provider, and for one year thereafter. However, motor carriers and intermodal equipment providers do not have to maintain documentation of inspector qualifications for those inspections performed as part of a State periodic inspection program. [73 FR 76825, Dec. 17, 2008, as amended at 81 FR 47732, July 22, 2016; 86 FR 57077, Oct. 14, 2021] § 396.21 Periodic inspection recordkeeping requirements. (a) The qualified inspector performing the inspection shall prepare a report that: (1) Identifies the individual performing the inspection; (2) Identifies the motor carrier operating the vehicle or intermodal equipment provider intending to interchange the vehicle to a motor carrier; (3) Identifies the date of the inspection; (4) Identifies the vehicle inspected; (5) Identifies the vehicle components inspected and describes the results of the inspection, including the identification of those components not meeting the minimum standards set forth in appendix A to this part; and (6) Certifies the accuracy and completeness of the inspection as complying with all the requirements of this section. (b) (1) The original or a copy of the inspection report shall be retained by the motor carrier, intermodal equipment provider, or other entity that is responsible for the inspection for a period of fourteen months from the date of the inspection report. The original or a copy of the inspection report must be retained where the vehicle is either housed or maintained. (2) The original or a copy of the inspection report must be available for inspection upon demand of an authorized Federal, State or local official. (3) Exception. If the motor carrier operating the commercial motor vehicles did not perform the commercial motor vehicle's last annual inspection, or if an intermodal equipment provider did not itself perform the annual inspection on equipment intended for interchange to a motor carrier, the motor carrier or intermodal equipment provider is responsible for obtaining the original or a copy of the last annual inspection report upon demand of an authorized Federal, State, or local official. [73 FR 76825, Dec. 17, 2008, as amended at 86 FR 57077, Oct. 14, 2021] § 396.23 Equivalent to periodic inspection. (a) (1) If a commercial motor vehicle is subject to a mandatory inspection program that is determined by the Administrator to be as effective as § 396.17, the motor carrier or intermodal equipment provider must meet the requirement of § 396.17 through that inspection program. Commercial motor vehicle inspections may be conducted by government personnel, at commercial facilities authorized by a State government or equivalent jurisdiction in the Canadian Provinces, the Yukon Territory, or Mexico, or by the motor carrier or intermodal equipment provider itself under the auspices of a self-inspection program authorized by a State government or equivalent jurisdiction in the Canadian Provinces, the Yukon Territory, or Mexico. (2) Should FMCSA determine that an inspection program, in whole or in part, is not as effective as § 396.17, the motor carrier or intermodal equipment provider must ensure that the periodic inspection required by § 396.17 is performed on all commercial motor vehicles under its control in a manner specified in § 396.17. (b) [Reserved] [83 FR 22881, May 17, 2018] § 396.25 Qualifications of brake inspectors. (a) Motor carriers and intermodal equipment providers must ensure that all inspections, maintenance, repairs or service to the brakes of its commercial motor vehicles, are performed in compliance with the requirements of this section. (b) For purposes of this section, brake inspector means any employee of a motor carrier or intermodal equipment provider who is responsible for ensuring that all brake inspections, maintenance, service, or repairs to any commercial motor vehicle, subject to the motor carrier's or intermodal equipment provider's control, meet the applicable Federal standards. (c) No motor carrier or intermodal equipment provider may require or permit any employee who does not meet the minimum brake inspector qualifications of paragraph (d) of this section to be responsible for the inspection, maintenance, service or repairs of any brakes on its commercial motor vehicles. (d) The motor carrier or intermodal equipment provider must ensure that each brake inspector is qualified as follows: (1) Understands the brake service or inspection task to be accomplished and can perform that task; and (2) Is knowledgeable of and has mastered the methods, procedures, tools and equipment used when performing an assigned brake service or inspection task; and (3) Is capable of performing the assigned brake service or inspection by reason of experience, training, or both as follows: (i) Has successfully completed an apprenticeship program sponsored by a State, a Canadian Province, a Federal agency or a labor union, or a training program approved by a State, Provincial or Federal agency, or has a certificate from a State or Canadian Province that qualifies the person to perform the assigned brake service or inspection task (including passage of Commercial Driver's License air brake tests in the case of a brake inspection); or (ii) Has brake-related training or experience or a combination thereof totaling at least one year. Such training or experience may consist of: (A) Participation in a training program sponsored by a brake or vehicle manufacturer or similar commercial training program designed to train students in brake maintenance or inspection similar to the assigned brake service or inspection tasks; or (B) Experience performing brake maintenance or inspection similar to the assigned brake service or inspection task in a motor carrier or intermodal equipment provider maintenance program; or (C) Experience performing brake maintenance or inspection similar to the assigned brake service or inspection task at a commercial garage, fleet leasing company, or similar facility. (e) No motor carrier or intermodal equipment provider may employ any person as a brake inspector unless the evidence of the inspector's qualifications, required under this section, is maintained by the motor carrier or intermodal equipment provider at its principal place of business, or at the location at which the brake inspector is employed. The evidence must be maintained for the period during which the brake inspector is employed in that capacity and for one year thereafter. However, motor carriers and intermodal equipment providers do not have to maintain evidence of qualifications to inspect air brake systems for such inspections performed by persons who have passed the air brake knowledge and skills test for a Commercial Driver's License.