Air Compressor Clasification PDF
Document Details
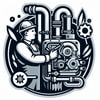
Uploaded by SmootherEpitaph1188
CFP des Moulins
Tags
Summary
This document provides a comprehensive overview of different air compressor types, including their applications and operating principles. It discusses volumetric and dynamic compressors along with various specific compressor types like reciprocating, rotary, and liquid piston compressors. The text details how different types manage various applications in industry.
Full Transcript
# QUATRIÈME PARTIE SERVICES AUXILIAIRES ## COMPRESSION DE L'AIR - We have chosen the title "Compression of the air" because the most common application of compressors in a power plant is to produce high-pressure air. - The compression of other gases is often used in industry, and we mention it in...
# QUATRIÈME PARTIE SERVICES AUXILIAIRES ## COMPRESSION DE L'AIR - We have chosen the title "Compression of the air" because the most common application of compressors in a power plant is to produce high-pressure air. - The compression of other gases is often used in industry, and we mention it in the lesson. - The basic principles are the same regardless of the gas, and the examples of calculations represent the compression of air. ## UTILISATIONS DES COMPRESSEURS - Compressors have many diverse applications in everyday life, at home or in industry. - For example, they are used in service stations where compressed air is used for the operation of lifting devices, grease guns and paint guns, as well as for inflating vehicle tires. - Other well-known applications are refrigerators and air conditioners where the heat absorption properties of a gas that expands or a liquid that evaporates are used. - In the construction industry, air compressors provide the drive for jackhammers, riveters, chipping hammers, impact wrenches, grinders, and more. - Compressors serve several purposes in the chemical and petrochemical industries. - Gases are brought to pressures higher than atmospheric pressure and used to promote chemical reactions that do not easily occur at atmospheric pressure. - The separation of components in a gas mixture is also accomplished by compression. This process, called liquefaction, often requires very high pressures. - Separation normally occurs by pressurizing the gas mixture to the critical pressure of the component with the highest boiling point. - The temperature is then lowered to condense the mixture into a liquid form. - The oil industry uses a large number of compressors to recover volatile fractions of gasoline from natural gas, force natural gas into transmission lines, cool the oils before de-waxing, and charge the gases into refining processes. ## LES COMPRESSEURS SONT SOUVENT UTILISÉS AVEC DES MOTEURS À COMBUSTION INTERNE, PARTICULIÈREMENT DIESELS, POUR BALAYER LES GAZ D'ÉCHAPPEMENT DES CYLINDRES DE GROS MOTEURS À DEUX CYCLES, POUR SURCHARGER ET POUR ATOMISER LE COMBUSTIBLE DANS LES MOTEURS À INJECTION D'AIR. - Compressed air is useful for starting fixed, low-speed engines and marine diesel engines using air starting valves that supply compressed air to the cylinders during a portion of their expansion strokes until the start of ignition. ## CLASSIFICATION DES COMPRESSEURS - All compressors are divided into two groups: - Volumetric - Dynamic - Compressors and pumps do similar jobs. The differences between them are primarily due to the fluids that they handle. - Pumps are designed to handle relatively incompressible, viscous liquids. Increasing the pressure on a liquid does not significantly reduce its volume. - On the other hand, compressors handle non-viscous vapors or gases that are significantly reduced in volume by an increase in pressure. These fluids can even liquefy when enough pressure is applied and the temperature is reduced below the critical value of the gas in question. ## COMPRESSEURS VOLUMÉTRIQUES - This type of compressor draws in a quantity of air, traps it, and then compresses it using a reciprocating piston or a rotating element before discharging it against the discharge pressure. - This category includes reciprocating compressors and rotary compressors of the lobe, vane, and liquid-piston types. ## TYPES DE COMPRESSEURS VOLUMÉTRIQUES - Reciprocating compressors are the oldest and by far the most common type; they always provide the best efficiency. There are several designs and arrangements, some of which are illustrated below. - The cylinders are arranged in several different ways to suit the drive used and the purpose of the compressor. Figures 1-5 show arrangements for single-stage compressors. - Figure 1 shows the simplest form of compressor, with a single cylinder driven by a crank. It can be single or double-acting. - Figure 2 shows a single-cylinder compressor with a direct steam drive. When steam cylinders drive compressors directly, the arrangement includes a single piston rod that is common to the steam cylinder piston and the air compressor piston. - Figure 3 illustrates a duplex compressor with a crank drive. - Figure 4 illustrates duplex compressor with a direct steam drive, with two shaft crossheads. - Figure 5 illustrates a radial compressor with three cylinders driven by a crank. - When discharge pressures higher than 550 kPa are required, compression occurs in two or more stages. Figures 6-10 illustrate arrangements for two-stage compressors. The letters H and L indicate the high-pressure cylinder and the low-pressure cylinder, respectively. - Figures 11 and 12 show compressors with three stages and compressors with four stages, respectively. - The illustrations that follow show examples of reciprocating compressors. - Figure 13 shows a small reciprocating compressor. It is the type of compressors used to supply compressed air at gas stations. - Figure 14 shows a vertical reciprocating compressor, with two stages and a single-acting effect. ## FIGURE 15 - This figure shows a cross-sectional view of a horizontal double-acting reciprocating air compressor. - This drawing shows all of the important features of a typical reciprocating air compressor including the cylinder heads, piston, wiper rings, enclosed frame, oil pocket, crosshead pin bushing, split shell bearing, inspection cover, oil gage and drain, oil reservoir, roller bearings, crankshaft, cylinder lubrication, stuffing box, hand hole, crosshead guides, and crosshead. ## FIGURE 16 - This figure shows a cross-sectional view of a balanced opposed, two-stage, horizontal, double-acting reciprocating compressor. ## FIGURE 17 - This figure shows a cross-sectional view of a V-type, double-acting, two-stage, vertical reciprocating compressor. ## FIGURE 18 - This figure shows a cross-sectional view of an opposed horizontal reciprocating air compressor driven by a V12 supercharged two-cycle gas engine. ## FIGURE 19 - This figure shows a cross-sectional view of a large, gas-engine-driven reciprocating compressor. This type is used at natural gas compression stations. - The other volumetric compressors that were mentioned were the rotary types, with either lobes, vanes, or a liquid piston. ## FIGURE 20 - This figure is a schematic of a lobe compressor, with two different types of lobe designs, Lysholm and Roots. - This drawing shows the basic components of the compressor including the impeller, intake manifold, and discharge manifold. - The inlet and outlet are marked on each schematic. ## COMPRESSOR LYSHOLM - Figure 21 shows a Lysholm compressor. - This figure shows a cross-section of a Lysholm compressor. - It is comprised of six female lobe rotors and four male lobe rotors. - The rotors are synchronized in a 3:2 speed ratio using timing gears. - The rotors do not touch, so they do not need lubrication. - As the rotors turn, a compression chamber is created as each male lobe meshes with its corresponding female lobe. - The rotation continuously moves the compression chamber down the length of the rotors until discharge at the opposite end. - The rotors are sealed against the body, which makes the compression process similar to a piston moving in a groove. - Each rotor is bored longitudinally for the flow of cooling oil. - The body is also equipped with a water jacket to remove heat from the compression of the gas. ## COMPRESSOR ROOTS - The bearings and timing gears are normally the only parts of the Roots compressor that require lubrication. However, the rotors need to be lubricated with a special oil. ## FIGURE 22 - This figure shows a cross-sectional view of a Roots-type rotary compressor. - The drawing shows all of the important features of a typical Roots compressor including the impeller, inlet manifold, outlet manifold, timing gears, oil filling plug, oil ring, drain plug, oil cup, oil slusher, outboard bearing, and level cock. - Roots compressors are designed for high capacity and modest discharge pressure. - The capacities can reach 1500 m³/min, with a discharge pressure up to 100 kPa on a single stage. - The operating speed varies with the size of the compressor but can reach 1750 r/min. - Roots compressors are air-cooled. - Because Roots compressors are volumetric, a discharge valve must be incorporated into the inlet piping to prevent over pressurization. ## THE PRINCIPLE OF OPERATION IS AS FOLLOWS - Two rotors turn inside a body that forms two parallel cylindrical bores with a precisely matched set of mating gears to ensure that the rotors turn without touching, while maintaining a specific angle between them. The rotors are timed so that, when one rotor is horizontal, the other is vertical. - As the rotors rotate, air is drawn into the inlet opening, trapped between the rotors and the body, and then is forced into the discharge area against the discharge pressure. - The compressor does not have any valves unless more than one unit discharges into a common manifold. - In this case, a check valve must be used on the discharge piping. - The rotors or impellers turn without touching each other and without any sliding on the body. - There is no wear, and internal lubrication is unnecessary. The air or gas passing through the machine remains dry and free of oil. ## THIS TYPE OF COMPRESSOR IS NORMALLY USED FOR DELIVERING LARGE VOLUMES OF AIR AT LOW PRESSURE. EMPHASIS IS PLACED ON CAPACITY RATHER THAN PRESSURE,SO THAT THE MACHINE IS OFTEN CALLED A BLOWER INSTEAD OF A COMPRESSOR. - Sliding vane compressors are available for higher discharge pressures than typical Roots compressors. They can reach 400 kPa for single-stage machines, and 1000 kPa for two-stage machines. - Capacities range from 180 m³/min for the smaller units, to larger units with motor sizes ranging from 0.09 kW to 375 kW. - Operating speeds typically range from 250 rpm to 3600 rpm, depending on the type of drive and the required free-air capacity. ## FIGURE 23 - This figure is a schematic of a sliding vane compressor. - The drawing shows all of the important features of a typical sliding vane compressor including the rotor, vanes, outlet port, suction port, discharge valve, oil feed lines, oil dose cups, water outlet, force-feed mechanical lubricator, retaining rings, water inlet, and water jacket. Also shown are the oil seal, spring-loaded seal, and feed to oil seal. - Figure 23 shows the mechanism of the sliding vane compressor. The rotor turns eccentrically inside the body and has a number of radial slots in its periphery. - Sliding vanes are inserted into the slots, and they are displaced toward the center of the rotor by centrifugal force or by springs. - The outer edges of the vanes maintain contact with the bearing faces of the body due to centrifugal force, and in some models, they are also held in place by springs. - As the rotor turns, air is drawn through the intake port into the chamber formed between the vanes. - The chamber is sealed by the vanes against the body. ## AS THE ROTOR TURNS, THE AIR IS TRAPPED BETWEEN THE VANES AND THE BODY AND IS COMPRESSED. - The compression process is illustrated in Figure 23. Because of the eccentric rotation of the rotor, the volume of air trapped between the vanes, the rotor, and the body decreases until discharge at the outlet. - Sliding vane compressors often incorporate two concentric rings, free to rotate within the body and around the periphery of the rotor, with a gap between the vanes and the bearing faces. - The rings are perforated to allow air flow, and they reduce wear on the vanes. - This design also decreases the power required to drive the compressor because of reduced friction losses. ## FIGURE 24 - This figure is a schematic of a liquid piston compressor. The drawing shows a sectional end view and a sectional side view of the compressor with all of the major components. - It includes the rotor, cone, shaft packing, water inlet (two), oil cup, inlet port, and discharge port. - In liquid-piston compressors, the vanes do not contact the body of the compressor. Instead, the vanes contact the edge of a rotating ring in a bath of liquid, and they are free to slide within the ring. - The body of the compressor is connected to a water jacket to cool the air during compression. - A small amount of water is constantly supplied to the body to remove heat from the compression process, with any excess water and compressed air being discharged to a separator to remove the water. ## THE LIQUID SEAL ALLOWS CLEAN AIR TO BE DELIVERED WITHOUT A FILTER AND A SEPARATE COOLER. - This is the only type of rotary compressor that requires internal lubrication. - Separators are used in the distribution system to provide clean, dry air. ## COMPRESSEURS DYNAMIQUES - Dynamic compressors transfer kinetic energy to the air using rotating vanes, and then convert that kinetic energy into pressure at the discharge. - Dynamic compressors include centrifugal and axial types. - The development of these compressors was largely due to the development of high-speed drive systems, such as electric motors, steam turbines, and gas turbines. These drive systems enable these compressors to operate at higher speeds (1000 rpm to 20,000 rpm), which is required to achieve the necessary discharge pressure. ## COMPRESSEURS CENTRIFUGES - Figure 25 shows a simple, single-stage, centrifugal compressor. The figure is a cross-sectional view and includes all of the important features of a typical centrifugal compressor including the impeller, inlet manifold, sealing strip, volute casing, grease cup, and diffuser, showing the flow path of the air. - The air is initially drawn into the compressor through the inlet manifold and is then propelled outward by a rotating impeller containing many small vanes. - The rotating impeller accelerates the air towards the outlet. The air exits the impeller at a higher pressure and velocity. - The high-velocity air then enters a diffuser that is designed to slow the air down. The wider cross-section of the diffuser allows for lower air velocity and higher air pressure. ## THE AIR THEN ENTERS A SPIRAL VORTEX HOUSING, WHERE, AGAIN DUE TO THE INCREASING AREA OF FLOW, THERE IS FURTHER REDUCTION IN SPEED AND INCREASED PRESSURE. - The centrifugal compressor is usually mounted on a shaft extension of the driving motor. - For example, in the illustration that follows, a centrifugal compressor is mounted on a shaft extension of a gas turbine. - The shaft extension is often supported by a separate bearing. - The compressor in the illustration uses grease-lubricated anti-friction bearings. - The larger centrifugal compressors have oil lubricated anti-friction bearings or plain bearings, depending on the operating conditions. ## FIGURE 26 - This figure is a cross-sectional view of a double-inlet centrifugal compressor. - The drawing shows all of the major components including the rotor, labyrinth seals, inlet flange, oil supply, oil drain, sight flow fitting, pivoted shoe thrust bearing, and double suction rotor. - Double-inlet centrifugal compressors are inherently balanced against axial thrust, but a thrust bearing is provided to accommodate any residual thrust. - Figure 26 shows the mechanism of the double-inlet type of centrifugal compressor. - Labyrinth seals are located at each end of the rotor to prevent air leakage. - The journal bearings and thrust bearings are provided with a forced lubrication system. - An oil pump (not shown) provides oil at a specific pressure to the bearings through an external oil cooler, with the oil returning to the reservoir by gravity. - The outer housing and bearings are split horizontally to allow access to the rotor and bearings. - The shaft seals at the high pressure end of the compressor are of the labyrinth type, to prevent gas leakage. - The pressure at the low-pressure end of the compressor is the same as the suction pressure, so there is no need to use shaft seals at this end. ## FIGURE 27 - This figure shows a four-stage centrifugal compressor driven by a steam turbine. - All components of the compressor are clearly labeled in this cross-sectional schematic. These major parts include: the compressor, self aligning main bearing, balancing piston, combined main and Kingsbury type thrust bearing, steam turbine, main oil pump, check valve, oil reservoir, relief valve, pressure oil to regulator, drain from regulator, inlet manifold, drain from bearings, pressure oil to bearings, discharge outlet, water cooler, and relief valve to oil reservoir. - Multi-stage centrifugal compressors are best suited for supplying large volumes of air at higher discharge pressures, such as those used at blast furnaces and in the Bessemer process. - They are often driven by steam turbines, but electrical motors can also be used, either directly or through gear reducers. - The turbine is connected directly to the compressor in this illustration, which is a common arrangement. - In another arrangement, the turbine and compressor are connected by a reduction gear box. - The radial thrust is balanced by a balancing piston. - The axial thrust is balanced by a Kingsbury-type thrust bearing. - The rotor bearings and the balancing piston are provided with a forced-feed lubrication system. - An oil pump provides pressurized oil to the bearings through a cooler and back to the reservoir by gravity. - The casings and bearings can be inspected and maintained by removing half of each casing. - Labyrinth seals and carbon face seals are used to prevent the leakage of air, oil, or water. - The space between the compressor body and the impeller or shaft is made gas-tight by labyrinth seals. - The radial thrust of the rotor is balanced by a balancing piston, and a Kingsbury-type thrust bearing is provided to accommodate any residual thrust on the shaft and to position the rotor properly. - The self-aligning bearings for the shaft are housed in external casings. - The bearings are protected from contamination by the compressed air and oil using labyrinth seals, and they are lubricated by a recirculating system. - The lubrication system is usually driven by a gear mounted on the shaft of an electrically driven compressor. - Labyrinth seals are used at the high-pressure end of the compressor, where the shaft passes through the body, to prevent gas leakage. - At the low-pressure end of the compressor, the pressure inside the body is the same as the suction pressure, so these seals are unnecessary. ## COMPRESSORS AXIAUX - Axial compressors are capable of delivering large volumes of air per minute. - They provide better performance than centrifugal compressors when high air volumes are required, especially for higher speeds. - This high efficiency has contributed to the development of the gas turbine. ## FIGURE 28 - The figure shows an axial compressor arrangement with a high-pressure casing, low-pressure casing, an intercooler, and a steam turbine driving the compressor through a gear box. - The compressor is divided into two stages, with an intercooler located between the stages to cool the air. ## FIGURE 29 - This figure is a cross-sectional view of a nine-stage axial compressor, showing all major parts of the compressor. - The major parts include: the case, inlet guide vanes, stator blades, rotor blades, oil inlet (two), thrust bearing, oil scavenge, pilot ring, exit guide vane, rotor disk, tie bolt, seal, and roller bearing. - Figure 29 is a schematic of a typical axial compressor design. The overall design is a single-stage compressor. The rotor and stator each contain rows of airfoil-like blades that direct the air stream, creating a pressure increase and a change in direction of the air. - The diameter of the blades is constant throughout the compressor. The lengths of the blades increase progressively from the impeller to the discharge. - The rotor is mounted on bearings that allow for a slight clearance between the rotor and its surrounding casing to maintain proper clearance between the rotor blades and the stator blades. - The axial thrust of the rotor is balanced by a thrust bearing that might be a ball bearing or a Kingsbury-type bearing. - The rotor blades give the air in the compressor a slight angular rotation. - This rotation increases the air's kinetic energy and pressure. - The stator blades further increase the air's pressure when they straighten the airflow, as the air is passed through the next stage. ## FIGURE 30 - This figure shows the rotor and stator of a nine-stage axial compressor. - The rotor is illustrated separately, and the stator is illustrated separately, and the flow path of the air is shown. ## CALCULS FOR AIR COMPRESSORS ## COMPRESSORS ## WORK ACCOMPLISHED IN COMPRESSION - Figure 31 is a schematic diagram of a single-acting, single-cylinder reciprocating air compressor, showing one complete cycle of compression. - The diagram shows the four critical points in the cycle, a, b, c, and d. - Point a is the beginning of the intake stroke, - point b is the end of the intake stroke, - point c is the end of the compression stroke, and - point d is the end of the discharge stroke. - Line a-b illustrates the intake of air from the air intake manifold, which occurs as the piston moves from the bottom dead center toward the top dead center of the cylinder. - Line b-c illustrates the compression of the air as the piston moves from the top dead center toward the bottom dead center. The intake and discharge valves are closed during this phase. - Line c-d illustrates the discharge of the air into the discharge piping as the piston moves from the bottom dead center to the top dead center. - The area enclosed by the ABCD cycle represents the work done on the air during one complete cycle of compression. ## THE LAW OF THE COMPRESSION CURVE - The amount of work done depends on the volume V; and the increase in pressure Pd-Pa. However, it also depends on the shape of the compression curve bc. - This relationship is shown in Figure 32. - Compression begins at point b in Figure 32, and the curve obeys the law PV"=constant. - This term, P, represents the pressure of the air, and V represents the volume of the air. - The value of n is typically greater than 1.0. Its value depends on the operating conditions. - The value of PV is a constant because the pressure and the volume are inversely proportional. ## THE WORK DONE DURING THE COMPRESSION CYCLE IS GREATER AS THE VALUE OF n IS INCREASED. - If compression takes place without any heat loss, it is adiabatic, and the value of n becomes the ratio of the specific heat at constant pressure to the specific heat at constant volume, or the adiabatic index. - The adiabatic index for air, which is a diatomic gas, is 1.4. - If substantial heat loss occurs during the compression process to prevent a temperature increase, the process becomes isothermal. - The compression path is isothermal when n=1, which makes PV=constant. ## THE ISOTHERMAL COMPRESSION PATH IS THE BEST BECAUSE IT REQUIRES THE MINIMUM WORK. - In practical applications, the curve is somewhere in between the isothermal and adiabatic curves. - This condition is illustrated by the line b-d in Figure 32, for which the law is expressed as PV"= constant, where n is greater than 1.0 but less than the adiabatic index for air. ## THE EFFECT OF CLEARANCE VOLUME - The PV diagram in Figure 31 is for a compressor without any clearance volume. - The actual PV diagram for a real reciprocating compressor is shown in Figure 33. - The clearance volume, V3, is the volume of air remaining in the cylinder when the piston is at the bottom dead center. - This is also known as the "dead space". - Line 3-4 illustrates that some of the trapped air expands from the bottom dead center to the top dead center, doing work on the piston in the process. This energy is absorbed by the compressor, so the area under this curve is considered lost work. ## WORK IS DONE BY THE COMPRESSOR AS THE PISTON MOVES FROM THE TOP DEAD CENTER TO THE BOTTOM DEAD CENTER AS THE COMPRESSOR TAKES IN ADDITIONAL AIR. - The work done by the compressor as the piston moves from bottom dead center to top dead center is represented by the volume that is enclosed by line a-b-c-d. ## CLEARANCE VOLUME HAS NO IMPACT ON THE TOTAL AMOUNT OF WORK DONE DURING ONE COMPLETE COMPRESSION CYCLE. - However, its effect on the amount of compressed air delivered during that cycle is significant. - This is because, as the piston moves toward the top dead center during the intake stroke, the volume contained within the cylinder remains unchanged, the air is compressed, and the pressure in the cylinder drops until it equalizes with the intake pressure. - When the pressure equilizes, the intake valve opens, and then air flows into the cylinder during the remainder of the stroke. - No new air is drawn into the cylinder until the pressure drops to equal the intake pressure. ## VOLUMETRIC EFFICIENCY - The volume swept by the compressor piston during the compression cycle is (V1-V3), and the volume of air drawn into the compressor is (V1-V4). - The volumetric efficiency is the ratio of the volume of air drawn into the compressor to the volume swept by the compressor piston: - The higher the compression ratio, the larger the clearance volume and the lower the volumetric efficiency. ## FOR THESE REASONS, THE CLEARANCE VOLUME IN RECIPROCATING COMPRESSORS IS USUALLY KEPT TO A MINIMUM. - The volumetric efficiency is frequently defined as the ratio of the delivered air quantity to the swept volume. - The delivered quantity of air is the actual volume of air that passes through the compressor, and the swept volume is the maximum volume of air that the compressor can draw in on a single stroke, assuming no clearance volume. - The volumetric efficiency is also represented as the ratio of the compressor's intake capacity to the swept volume. ## WORK ACCOMPLISHED PER CYCLE - The clearance volume does not impact the work done per kilogram of air delivered. - The PV diagram in Figure 31 is normally used to illustrate the compression cycle, since the clearance volume is neglected. - This diagram is also known as an indicator diagram. - The area enclosed in the PV diagram represents the work done on the air. ## THE WORK ACCOMPLISHED PER CYCLE IS CALCULATED BY INTEGRATION AS FOLLOWS - The work done during one compression cycle is: - Where V1 and V2 are the volumes of air before and after compression, and they must be in m³. - P1 and P2 are the absolute pressures before and after compression, in kPa. - n is the index of compression. An average value of n is 1.3 for air. - The power required to compress air is simply the work done per cycle multiplied by the cycle speed, or: - This formula can be expressed in a variety of ways using equations of state for the compression process: - These equations are used in accordance with the data in the specific problem. - The expression for the work done per cycle can also be stated as a function of the mass of air compressed per cycle, the gas constant (R), and the temperature change. ## MECHANICAL EFFICIENCY - The power required at the shaft of the compressor drive unit is larger than the power required to compress the air. - The difference in power is due to mechanical friction losses and power required for cooling the compressor. - This difference is between 15% and 35% percent. - However, a value of 17 percent loss is considered a reasonable approximation for air compressors. - The mechanical efficiency of an air compressor (that is, the ratio of the air power to the shaft power) can be stated as: ## THE ABOVE CALCULATION IS FOR THE OPERATION OF A SINGLE-STAGE COMPRESSOR. FOR A MULTI-STAGE COMPRESSOR, THE COMPRESSION WORK IS DISTRIBUTED EVENLY BETWEEN THE STAGES. - Therefore the power rating of the compressor must be adjusted to accommodate the number of stages: - For a multistage compressor, use the following calculation: - The power required for the multistage compressor can be found by multiplying the power for a single-stage compressor by the number of stages. ## EXAMPLE 1 - A single-acting, single-cylinder air compressor has a cylinder diameter of 200 mm and a stroke of 300 mm. It operates at a speed of 180 rpm. The intake air has a pressure of 96 kPa and a temperature of 20 °C. The discharge pressure is 800 kPa. - Calculate the power required to drive this compressor, assuming a mechanical efficiency of 85%. - Neglect the clearance volume. - Use the following compression law: PV1.3 = constant. - Calculate the amount of cooling water required if the air is cooled to 30 °C in an intercooler, assuming a water temperature increase of 5 °C. ## SOLUTION - The PV diagram for the compression process is shown in Figure 34. - The swept volume of the compressor is calculated as: - The swept volume is the same for both the intake and discharge stroke. - The volume after compression is calculated as: - The total work done on the air during each cycle is: - The power required to drive the compressor is: - Since the mechanical efficiency of the compressor is 85%, the power required is: - In order to calculate the required cooling water flow, we need to first calculate the temperature of the air at the end of the compression process: - The amount of heat to be removed from the air for each cycle of compression is: - Since the water temperature increases by 5 °C, the cooling water flow rate is: ## COMPRESSION IN MULTIPLE STAGES - It is not recommended to compress air to pressures greater than 550 kPa in a single stage compressor to avoid high energy losses and the risk of explosion caused by the resulting high temperatures. ## WHENEVER AIR IS COMPRESSED IN A SINGLE-STAGE CYLINDER, WITHOUT INTERCOOLING, TEMPERATURES BETWEEN 250 °C AND 290 °C ARE REACHED. - These high temperatures not only reduce the efficiency and capacity of the compressor, but they are also extremely dangerous, as they can cause an explosion of the compressed air if mixed with oil or other flammable materials. ## IT OFTEN HAPPENS THAT PRESSURES HIGHER THAN THIS ARE DESIRED. TO ACHIEVE THESE HIGHER PRESSURES AND PREVENT THE DANGERS OF EXPLOSION, MULTI-STAGE COMPRESSION IS EMPLOYED. - For these reasons, multi-stage compression is the most common method used today for almost all applications. - The advantage of multi-stage compression is not only in reducing energy losses. It also has mechanical advantages associated with a lower compression ratio per stage. - The main advantages of multi-stage compression, compared with single-stage compression, include the following: - Multi-stage compression provides the opportunity to cool compressed air in an intercooler located between the stages, which reduces the final temperature of the compressed air, reducing the energy required to achieve the target pressure. - Multi-stage compression also reduces the power required to drive the compressor. - It provides a more even load on the compressor drive system. This results in better mechanical balance. This means that a more economical compressor can be used since each stage is designed to handle a lower pressure rise. - The temperature change between the stages is well controlled. The maximum temperature during the compression cycle is maintained at a reasonable level, which makes the compression process safer and more stable. - The performance of a multi-stage compressor is better, especially for applications requiring high capacity and lower discharge pressures. - There is less leakage between the stages due to the lower pressure differential between the stages. - Lubrication is better because the operating temperatures are lower. - The volumetric efficiency is better because of the lower pressure differential between the stages, which minimizes the impact of clearance volume. - The cylinders are often smaller and lighter because it can be designed to withstand a lower maximum operating pressure. ## WORK ACCOMPLISHED IN COMPRESSION IN MULTIPLE STAGES - When air is compressed in multiple stages, the work done on the air is significantly less than in a single-stage compression. - To understand this, let’s look at the PV diagram in Figure 35, which shows a 2-stage compression system. - The first stage compresses the air from P1 to P2. - The second stage then compresses the air from P2 to Pd. - A cooler is located between the two stages to cool the air. - This process is illustrated by the line a-b-c-d in the figure. - The area enclosed by the a-b-c-d cycle represents the total work done on the air in the two-stage compression process. - Now, let's consider what would happen if we compressed the air in a single stage from P1 to Pd. - This is represented by the line 1-2-5 in the figure. - The area enclosed by that cycle represents the work done in the single-stage compression process. - The difference in work done between the two compression processes is the area enclosed by the 1-2-5-6 cycle. - Work is saved using a multi-stage compression system. ## CONDITIONS FOR MAXIMUM EFFICIENCY - Multi-stage compressors operate most efficiently if the work done on the air is distributed evenly across the stages. - The work done on the air is distributed evenly when the compression ratio is the same across the stages. - Specifically, the pressure ratio across each stage should be equal. - The pressure ratios in a multi-stage compressor are determined by the following equations: - The pressure ratio across each stage must be the same. - The intermediate pressure is calculated using the geometric means of the inlet and discharge pressures. ## EXAMPLE 2 - A three-stage air compressor draws air from a 90 kPa source. - Calculate the pressure at the end of the first and second stages if the discharge pressure is 2750 kPa? ## SOLUTION - The total compression ratio is calculated as follows: - The pressure ratio for each stage is: - The pressure at the end of the first stage is: - The pressure at the end of the second stage is: ## EXAMPLE 3 - A three-stage air compressor is designed to handle 8.5 m³ of air per minute. The intake air pressure is 90 kPa and the temperature is 15 °C. The discharge pressure is 2750 kPa. - Assuming that the piston speed is 92 m/min, the volumetric efficiency is 85% and the stroke is 380 mm, calculate the required diameter of the cylinders and determine the power required to drive the compressor when the mechanical efficiency is 95% and the compression index is 1.2. ## SOLUTION - The volumetric efficiency is the ratio of the delivered air capacity to the swept displacement. - Therefore, the swept volume is: - For a double-acting compressor, the swept volume is: - The area of the piston is calculated as: - The diameter of the cylinder is calculated as: - The diameter of the high-pressure cylinder is calculated as: - The overall dimensions for the three compression cylinders are: - The speed of the compressor is calculated as: - The work done on the air during one compression cycle is: - Where V is the intake volume, and P is the intake pressure, and P2 is the discharge pressure. - The work done per unit time is: - The power required to drive the compressor is: - The power required to drive a three-stage compressor is: ## THE EFFECT OF ALTITUDE - The atmospheric pressure is caused by the weight of the air above a point of measurement. - The atmospheric pressure is highest at sea level, decreasing with altitude. - The atmospheric pressure decreases by about 11.33 kPa for every 1000 m increase in altitude. - When an air compressor is operating at an altitude above sea level, the volume of air drawn in per minute is less than the volume that is drawn in at sea level, because the density of air decreases with altitude. - The correction that needs to be applied to the capacity of the compressor is a function of the barometric pressure. - The correction value is not a direct relationship due to the effect of altitude on the pressure ratio of the compressor. - The table on page 37 provides an example of altitude correction factors to be used when determining the capacity of an air compressor operating at altitude. The table also includes the change in pressure in kPa for each elevation change, and the multiplier that corresponds to each altitude. - To use the table, enter the table at the altitude of the compressor. - The barometric pressures are directly related to the elevation change. - Multiply the pressure at sea level by the appropriate multiplier for the compressor altitude. This will determine the volume of air that must be taken in at altitude to produce the same volume of air at sea level. ## EXERCISE 1. A) Draw a schematic diagram of a three-stage air compressor, including intercoolers between stages. B) Describe the auxiliary equipment and safety devices that would be included in such a compressor. 2. What effect does clearance volume have on the volumetric efficiency of a compressor? 3. A single-acting, single-cylinder air compressor draws air from a manifold