Chapter 5 - Temperature and Heat PDF
Document Details
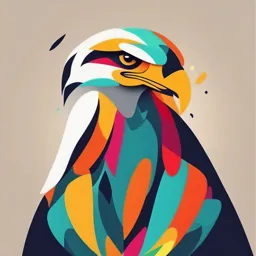
Uploaded by RewardingFluorine
Palawan State University
Tags
Summary
This document is a chapter on temperature and heat, likely from a physics textbook. It covers the differences between temperature and heat, various temperature scales (Fahrenheit, Celsius, Rankine, Kelvin), fundamental formulas, and methods of heat transfer such as conduction, convection, and radiation. Important concepts like specific heat and thermal expansion are also included.
Full Transcript
CHAPTER 5 TEMPERATURE AND HEAT Chapter Objectives This chapter will help you understand the difference between temperature and heat, the units used for their measurement, thermal time constants, and the most common methods used to measure temperature and heat and their standards. Topics covered...
CHAPTER 5 TEMPERATURE AND HEAT Chapter Objectives This chapter will help you understand the difference between temperature and heat, the units used for their measurement, thermal time constants, and the most common methods used to measure temperature and heat and their standards. Topics covered in this chapter are as follows: The difference between temperature and heat The various temperature scales Temperature and heat formulas The various mechanisms of heat transfer Specific heat and heat energy Coefficients of linear and volumetric expansion The wide variety of temperature measuring devices Introduction to thermal time constants Introduction Similar to our every day needs of temperature control for comfort, almost all industrial processes need accurately controlled temperatures. Physical parameters and chemical reactions are temperature dependent, and therefore temperature control is of major importance. Temperature is without doubt the most measured variable, and for accurate temperature control its precise measurement is required. This chapter discusses the various temperature scales used, their relation to each other, methods of measuring temperature, and the relationship between temperature and heat. Basic Terms Temperature definitions Temperature is a measure of the thermal energy in a body, which is the relative hotness or coldness of a medium and is normally measured in degrees using one of the following scales; Fahrenheit (F), Celsius or Centigrade (C), Rankine (R), or Kelvin (K). Absolute zero is the temperature at which all molecular motion ceases or the energy of the molecule is zero. Basic Terms Fahrenheit scale was the first temperature scale to gain acceptance. It was proposed in the early 1700s by Fahrenheit (Dutch). The two points of reference chosen for 0 and 100° were the freezing point of a concentrated salt solution (at sea level) and the internal temperature of oxen (which was found to be very consistent between animals). This eventually led to the acceptance of 32° and 212° (180° range) as the freezing and boiling point, respectively of pure water at 1 atm (14.7 psi or 101.36 kPa) for the Fahrenheit scale. The temperature of the freezing point and boiling point of water changes with pressure. Celsius or centigrade scale (C) was proposed in mid 1700s by Celsius (Sweden), who proposed the temperature readings of 0° and 100° (giving a 100° scale) for the freezing and boiling points of pure water at 1 atm. Rankine scale (R) was proposed in the mid 1800s by Rankine. It is a temperature scale referenced to absolute zero that was based on the Fahrenheit scale, i.e., a change of 1°F = a change of 1°R. The freezing and boiling point of pure water are 491.6°R and 671.6°R, respectively at 1 atm, see Fig. 8.1. Kelvin scale (K) named after Lord Kelvin was proposed in the late 1800s. It is referenced to absolute zero but based on the Celsius scale, i.e., a change of 1°C = a change of 1 K. The freezing and boiling point of pure water are 273.15 K and373.15 K, respectively, at 1 atm, see Fig. 8.1. The degree symbol can be dropped when using the Kelvin scale. Heat definitions Heat is a form of energy; as energy is supplied to a system the vibration amplitude of its molecules and its temperature increases. The temperature increase is directly proportional to the heat energy in the system. A British Thermal Unit (BTU or Btu) is defined as the amount of energy required to raise the temperature of 1 lb of pure water by 1°F at 68°F and at atmospheric pressure. It is the most widely used unit for the measurement of heat energy. A calorie unit (SI) is defined as the amount of energy required to raise the temperature of 1 gm of pure water by 1°C at 4°C and at atmospheric pressure. It is also a widely used unit for the measurement of heat energy. Joules (SI) are also used to define heat energy and is often used in preference to the calorie, where 1 J (Joule) = 1 W (Watt) × s. This is given in Table 8.1 that gives a list of energy equivalents Specific heat is the quantity of heat energy required to raise the temperature of a given weight of a material by 1°. The most common units are BTUs in the English system, i.e., 1 BTU is the heat required to raise 1 lb of material by 1°F and in the SI system, the calorie is the heat required to raise 1 g of material by 1°C. Thus, if a material has a specific heat of 0.7 cal/g °C, it would require 0.7 cal to raise the temperature of a gram of the material by 1°C or 2.93 J to raise the temperature of the material by 1 k. Table 8.2 gives the specific heat of some common materials; the units are the same in either system. Thermal conductivity is the flow or transfer of heat from a high temperature region to a low temperature region. There are three basic methods of heat transfer; conduction, convection, and radiation. Although these modes of transfer can be considered separately, in practice two or more of them can be present simultaneously Conduction is the flow of heat through a material. The molecular vibration amplitude or energy is transferred from one molecule in a material to the next. Hence, if one end of a material is at an elevated temperature, heat is conducted to the cooler end. The thermal conductivity of a material k is a measure of its efficiency in transferring heat. The units can be in BTUs per hour per ft per °F or watts per meter-Kelvin (W/m K) (1 BTU/ft h °F = 1.73 W/mK). Table 8.3 gives typical thermal conductivities for some common materials. Convection is the transfer of heat due to motion of elevated temperature particles in a material (liquid and gases). Typical examples are air conditioning systems, hot water heating systems, and so forth. If the motion is solely due to the lower density of the elevated temperature material, the transfer is called free or natural convection. If the material is moved by blowers or pumps the transfer is called forced convection. Radiation is the emission of energy by electromagnetic waves that travel at the speed of light through most materials that do not conduct electricity. For instance, radiant heat can be felt some distance from a furnace where there is no conduction or convection. Thermal expansion definitions Linear thermal expansion is the change in dimensions of a material due to temperature changes. The change in dimensions of a material is due to its coefficient of thermal expansion that is expressed as the change in linear dimension (a) per degree temperature change. Volume thermal expansion is the change in the volume (b) per degree temperature change due to the linear coefficient of expansion. The thermal expansion coefficients for some common materials per degree fahrenheit are given in Table 8.4. The coefficients can also be expressed as per degree Celsius. Temperature and Heat Formulas Temperature The need to convert from one temperature scale to another is a common everyday occurrence. The conversion factors are as follows: Heat transfer The amount of heat needed to raise or lower the temperature of a given weight of a body can be calculated from the following equation: As always, care must be taken in selecting the correct units. Negative answers indicate extraction of heat or heat loss. Heat conduction through a material is derived from the following relationship: Heat convection calculations in practice are not as straight forward as conduction. However, heat convection is given by It should be noted that in practice the proper choice for h is difficult because of its dependence on a large number of variables (such as density, viscosity, and specific heat ). Charts are available for h. However, experience is needed in their application. Heat radiation depends on surface color, texture, shapes involved and the like. Hence, more information than the basic relationship for the transfer of radiant heat energy given below should be factored in. The radiant heat transfer is given by Thermal expansion Linear expansion of a material is the change in linear dimension due to temperature changes and can be calculated from the following formula: Volume expansion in a material due to changes in temperature is given by In a gas, the relation between the pressure, volume, and temperature of the gas is given by Temperature Measuring Devices There are several methods of measuring temperature that can be categorized as follows: 1. Expansion of a material to give visual indication, pressure, or dimensional change 2. Electrical resistance change 3. Semiconductor characteristic change 4. Voltage generated by dissimilar metals 5. Radiated energy Thermometers Mercury in glass was by far the most common direct visual reading thermometer (if not the only one). The device consisted of a small bore graduated glass tube with a small bulb containing a reservoir of mercury. The coefficient of expansion of mercury is several times greater than the coefficient of expansion of glass, so that as the temperature increases the mercury rises up the tube giving a relatively low cost and accurate method of measuring temperature. Mercury also has the advantage of not wetting the glass, and hence, cleanly traverses the glass tube without breaking into globules or coating the tube. The operating range of the mercury thermometer is from −30 to 800°F (−35 to 450°C) (freezing point of mercury −38°F [−38°C]). The toxicity of mercury, ease of breakage, the introduction of cost effective, accurate, and easily read digital thermometers has brought about the demise of the mercury thermometer. Some thermometer image A thermometer works by measuring temperature, which typically involves a substance that changes in response to temperature fluctuations. Different types of thermometers measure temperature in unique ways, but here are the main types: 1.Mercury and Alcohol Thermometers How it Works: These thermometers use liquids like mercury or colored alcohol that expand and contract with temperature changes. When the temperature rises, the liquid expands and moves up the narrow glass tube, showing the temperature on a calibrated scale. Applications: Commonly used for measuring body, room, or water temperatures. 2. Digital Thermometers How it Works: Digital thermometers use a sensor, usually a thermistor or a resistance temperature detector (RTD). These sensors change their electrical resistance with temperature, which is then converted to a readable digital output on the thermometer's display. Applications: Widely used in medical, industrial, and home environments. 3. Infrared (IR) Thermometers How it Works: IR thermometers measure temperature by detecting infrared radiation (heat) emitted by an object. An optical lens focuses the infrared energy on a detector, which converts it into an electrical signal, displaying the temperature without needing direct contact. Applications: Useful for measuring the temperature of surfaces, particularly for non-contact readings (like food, machinery, or skin). 4. Thermocouple Thermometers How it Works: Thermocouples consist of two different metals joined together at one end. When heated, they produce a voltage that can be correlated with temperature. The voltage difference between the two metals is measured and used to calculate temperature. Applications: Common in industrial settings and high-temperature environments like ovens and furnaces. Each thermometer type provides a method to convert temperature changes into readable data, whether visually, digitally, or by measuring emitted radiation. Liquid glass thermometers Liquids in glass devices operate on the same principle as the mercury thermometer. The liquids used have similar properties to mercury, i.e., high linear coefficient of expansion, clearly visible, non-wetting, but are nontoxic. The liquid in glass thermometers is used to replace the mercury thermometer and to extend its operating range. These thermometers are accurate and with different liquids (each type of liquid has a limited operating range) can have an operating range of from -300 to 600°F (-170 to 330°C). Bimetallic strip is a type of temperature measuring device that is relatively inaccurate, slow to respond, not normally used in analog applications to give remote indication, and has hystersis. The bimetallic strip is extensively used in ON/OFF applications not requiring high accuracy, as it is rugged and cost effective. These devices operate on the principle that metals are pliable and different metals have different coefficients of expansion. If two strips of dissimilar metals such as brass and invar (copper-nickel alloy) are joined together along their length, they will flex to form an arc as the temperature changes; this is shown in Fig. 8.3a. Bimetallic strips are usually configured as a spiral or helix for compactness and can then be used with a pointer to make a cheap compact rugged thermometer as shown in Fig. 8.3b. Their operating range is from -180 to 430°C and can be used in applications from oven thermometers to home and industrial control thermostats. Pressure-spring thermometers These thermometers are used where remote indication is required, as opposed to glass and bimetallic devices which give readings at the point of detection. The pressure-spring device has a metal bulb made with a low coefficient of expansion material with a long metal tube, both contain material with a high coefficient of expansion; the bulb is at the monitoring point. The metal tube is terminated with a spiral Bourdon tube pressure gage (scale in degrees) as shown in Fig. 8.4a. The pressure system can be used to drive a chart recorder, actuator, or a potentiometer wiper to obtain an electrical signal. As the temperature in the bulb increases, the pressure in the system rises, the pressure rise being proportional to the temperature change. The change in pressure is sensed by the Bourdon tube and converted to a temperature scale. These devices can be accurate to 0.5 percent and can be used for remote indication up to 100 m but must be calibrated, as the stem and Bourdon tube are temperature sensitive. There are three types or classes of pressure-spring devices. These are as follows: Class 1 Liquid filled Class 2 Vapor pressure Class 3 Gas filled Liquid filled thermometer works on the same principle as the liquid in glass thermometer, but is used to drive a Bourdon tube. The device has good linearity and accuracy and can be used up to 550°C. Vapor-pressure thermometer system is partially filled with liquid and vapor such as methyl chloride, ethyl alcohol, ether, toluene, and so on. In this system the lowest operating temperature must be above the boiling point of the liquid and the maximum temperature is limited by the critical temperature of the liquid. Resistance temperature devices Resistance temperature devices (RTD) are either a metal film deposited on a former or are wire-wound resistors. The devices are then sealed in a glass ceramic composite material. The electrical resistance of pure metals is positive, increasing linearly with temperature. Table 8.5 gives the temperature coefficient of resistance of some common metals used in resistance thermometers. These devices are accurate and can be used to measure temperatures from - 300 to 1400°F (-170 to 780°C). The response time of the system is slow, being of the order of 20s. The temperature pressure characteristic of the thermometer is nonlinear as shown in the vapor pressure curve for methyl chloride in Fig. 8.4b. Gas thermometer is filled with a gas such as nitrogen at a pressure range of 1000 to 3350 kPa at room temperature. The device obeys the basic gas laws for a constant volume system [Eq.(8.15), V1 = V2] giving a linear relationship between absolute temperature and pressure. THERMISTOR A thermistor is a type of resistor whose resistance changes significantly with temperature. The word "thermistor" is derived from a combination of "thermal" and "resistor." Thermistors are widely used in temperature sensing and temperature-dependent electrical circuits because of their highly temperature- sensitive nature. Thermistors are a class of metal oxide (semiconductor material) which typically have a high negative temperature coefficient of resistance, but can also be positive. Thermistors have high sensitivity which can be up to 10 percent change per degree Celsius, making them the most sensitive temperature elements available, but with very nonlinear characteristics. The typical response times is 0.5 to 5 s with an operating range from −50 to typically 300°C. Devices are available with the temperature range extended to 500°C. Thermistors are low cost and manufactured in a wide range of shapes, sizes, and values. When in use care has to be taken to minimize the effects of internal heating. There are two main types of thermistors: 1.NTC (Negative Temperature Coefficient) Thermistors: The resistance of NTC thermistors decreases as the temperature increases. They are commonly used in applications where you need to measure or limit temperature, such as in temperature sensors, temperature protection circuits, or as inrush current limiters. 2.PTC (Positive Temperature Coefficient) Thermistors: The resistance of PTC thermistors increases as the temperature increases. PTC thermistors are often used for overcurrent protection and as resettable fuses. When the current passing through a PTC thermistor becomes too high, the temperature rises and causes the resistance to Applications: Temperature sensors: Thermistors are often used in digital thermometers, HVAC systems, and industrial temperature monitoring. Overcurrent protection: PTC thermistors can protect circuits by limiting the flow of current when it exceeds a certain threshold. Temperature compensation: In circuits where temperature variations might affect performance, thermistors help maintain stability by adjusting the circuit's response to temperature changes. Battery chargers: They are used to monitor and protect against overheating in battery charging circuits. Thermistors are valued for their accuracy, sensitivity, and compact size, making them suitable for a wide range of electronic and electrical applications. THERMOCOUPLES Thermocouples are formed when two dissimilar metals are joined together to form a junction. An electrical circuit is completed by joining the other ends of the dissimilar metals together to form a second junction. When the junction of these two metals is heated or cooled, a small voltage (called the Seebeck voltage) is generated, which can be measured and used to determine the temperature at the junction. Thermocouples operate based on the Seebeck effect, which is the phenomenon where a temperature difference between two different conductive materials generates a voltage difference between the materials. This voltage is then correlated to the temperature difference between the junction (called the "hot" or "measuring" junction) and the reference junction (which is kept at a known, constant temperature). Key Features of Thermocouples: 1.Temperature Range: Thermocouples can measure a wide range of temperatures, from very low (around -200°C) to very high temperatures (up to 2000°C, depending on the materials used). 2.Simple Construction: They are easy to make, relatively inexpensive, and rugged, which makes them suitable for a wide range of applications. 3.Wide Application: They are commonly used in industrial processes, furnaces, kilns, engines, and in scientific research. 4.Voltage Output: The voltage produced by a thermocouple is typically in the millivolt range, and it needs to be measured accurately to derive the corresponding temperature. The voltage is proportional to the temperature difference between the two junctions. Types of Thermocouples: Different combinations of metals produce different characteristics and are used in different temperature ranges. The most common thermocouple types include: 1.Type K (Chromel-Alumel): The most widely used type. Temperature range: -270°C to +1372°C. Commonly used for general-purpose measurements in industrial applications. 2.Type J (Iron-Constantan): Temperature range: -40°C to +750°C. Often used in older equipment or specific environments where corrosion- resistant materials are needed. 3. Type T (Copper-Constantan): Temperature range: -200°C to +350°C. Suitable for low-temperature measurements and is highly accurate in the sub-zero range. 4. Type E (Chromel-Constantan): Temperature range: -200°C to +900°C. Offers a high output voltage, making it useful for precise measurements in laboratory settings. 5. Type R, S, and B (Platinum-based): Temperature range: up to 1600°C or higher. These types are used in high-temperature applications like furnaces, and are known for their stability and accuracy. 6. Type N (Nicrosil-Nisil): A newer type, known for its resistance to oxidation at high temperatures. Applications: Industrial and Process Control: Thermocouples are used to monitor and control the temperature in industrial processes like metal forging, glass manufacturing, and chemical processing. Ovens and Furnaces: They are widely used for temperature measurement in ovens, kilns, and furnaces. Automotive: Thermocouples are used to monitor engine temperatures and exhaust gas temperatures. Science and Research: Thermocouples are often used in laboratories for experiments requiring temperature measurement in extreme environments. HVAC Systems: Thermocouples are used in heating, ventilation, and air conditioning systems to ensure proper functioning and regulation of temperature. Advantages of Thermocouples: Wide temperature range: Thermocouples can measure very high or very low temperatures. Durability: They are robust and can withstand harsh environmental conditions, such as vibration, pressure, and exposure to corrosive materials. Fast response time: Thermocouples are quick to react to temperature changes, making them ideal for dynamic or fast-changing environments. Disadvantages: Low signal output: The voltage produced is very small (in millivolts), which means the measurement needs to be precise, and the signal may require amplification or conversion. Non-linear output: The relationship between the temperature and the output voltage is not linear, meaning calibration is needed for accurate measurements. Requires a reference junction: The temperature of the reference junction (often at the measuring device) must be known and compensated for. In summary, thermocouples are versatile, durable, and widely used temperature sensors, especially suited for high-temperature environments, though they do require careful calibration and signal conditioning due to their small voltage output and non-linear behavior. Semiconductor temperature sensors Semiconductor temperature sensors are temperature sensing devices that rely on the properties of semiconductor materials (such as silicon or germanium) to measure temperature. These sensors are widely used in electronic circuits because they are compact, inexpensive, and offer good accuracy over a limited temperature range. The key principle behind semiconductor temperature sensors is that the electrical characteristics of semiconductor materials, particularly their voltage, resistance, or current, change with temperature in a predictable way. Types of Semiconductor Temperature Sensors 1.Thermistors: NTC (Negative Temperature Coefficient) thermistors are a type of semiconductor temperature sensor where the resistance decreases as the temperature increases. PTC (Positive Temperature Coefficient) thermistors are another type where the resistance increases with temperature. Thermistors are widely used because of their high sensitivity to temperature changes and relatively low cost. They are suitable for a range of applications such as temperature monitoring in circuits, battery protection, or environmental sensing. 2. Diode-Based Temperature Sensors: A common example of a semiconductor temperature sensor is a diode or a transistor. The forward voltage of a diode (or base-emitter voltage of a transistor) decreases by about 2 mV for every 1°C increase in temperature. This behavior can be used to determine the temperature by measuring the voltage across the diode or transistor. Diodes are often used in integrated circuit (IC) temperature sensors, where the voltage drop across the diode is proportional to the temperature. 3. Silicon-Based Temperature Sensors: Silicon Temperature Sensors are often found in Integrated Circuit (IC) form and provide a linear output voltage or current that is proportional to the temperature. These sensors take advantage of the fact that the bandgap of silicon changes with temperature, which directly affects the electrical properties of the silicon. Silicon-based sensors are available in many forms, from simple analog voltage outputs to more complex digital interfaces. How Semiconductor Temperature Sensors Work: Voltage-Temperature Relationship: In semiconductor materials, the energy band structure changes with temperature, causing a shift in electrical characteristics such as the forward voltage of diodes, the resistance of thermistors, or the current flowing through a transistor. Bandgap Principle: In devices like bandgap reference sensors, the voltage drop across a diode or transistor is measured and used to determine the temperature. The voltage changes in a predictable way with temperature, so it can be calibrated to provide accurate temperature readings. Advantages of Semiconductor Temperature Sensors: 1.Small Size: These sensors are typically very small, often available in IC packages that are easy to integrate into electronic systems. 2.Low Cost: Semiconductor temperature sensors are generally cheaper than other types of sensors (like thermocouples or RTDs), which makes them attractive for mass-produced consumer electronics. 3.Fast Response Time: Semiconductor sensors can respond quickly to temperature changes, making them ideal for applications where rapid temperature monitoring is required. 4.Linear Output: Many semiconductor-based sensors offer a linear output with respect to temperature (especially in IC temperature sensors), which simplifies the process of temperature measurement and calibration. 5.Wide Integration: Semiconductor sensors are often integrated into complex systems, like microcontrollers or other ICs, making them easy to implement in electronic devices. Disadvantages of Semiconductor Temperature Sensors: 1.Limited Temperature Range: Semiconductor sensors typically operate within a limited temperature range compared to thermocouples or RTDs. For example, typical silicon-based sensors work well from around -50°C to +150°C, and are not suitable for very high temperatures. 2.Accuracy: While semiconductor sensors can be quite accurate, their accuracy is generally not as high as thermocouples or RTDs, especially in extreme conditions. 3.Temperature Sensitivity: The electrical properties of semiconductor materials can be more sensitive to factors like supply voltage and noise in the circuit, which can affect the accuracy of the temperature measurement. Common Applications of Semiconductor Temperature Sensors: Consumer Electronics: Used in devices like smartphones, laptops, and refrigerators to monitor and control temperature for safety, efficiency, and comfort. Automotive: Semiconductor sensors are used in engine control systems, cabin temperature regulation, and battery management systems. Industrial: These sensors are found in process control, HVAC systems, and industrial equipment monitoring. Medical Devices: Used in applications like patient temperature monitoring or controlling the temperature of medical equipment. Battery Management Systems: In electric vehicles and portable electronics, semiconductor sensors monitor the temperature of batteries to prevent Examples of Semiconductor Temperature Sensors: 1.LM35: A common IC temperature sensor that provides a voltage output proportional to the temperature (in °C), with a typical scale factor of 10 mV/°C. 2.TMP36: A digital temperature sensor from Texas Instruments, offering high accuracy and a linear digital output that communicates over I2C or SMBus. 3.DS18B20: A popular digital temperature sensor from Maxim Integrated that communicates over a one-wire interface and is widely used in hobbyist and embedded applications. 4.AD22100: A high-accuracy analog output temperature sensor by Analog Semiconductor temperature sensors are versatile, inexpensive, and compact, making them ideal for a broad range of applications, especially in electronic systems. They offer quick response times and can provide a linear output that simplifies the process of temperature measurement. However, they are best suited for moderate temperature ranges and may not be the best choice for high- precision or extreme-temperature environments where other sensors like thermocouples or RTDs are more appropriate. Application Considerations Selection In process control a wide selection of temperature sensors are available. However, the required range, linearity, and accuracy can limit the selection. In the final selection of a sensor, other factors may have to be taken into consideration, such as remote indication, error correction, calibration, vibration sensitivity, size, response time, longevity, maintenance requirements, and cost. The choice of sensor devices in instrumentation should not be degraded from a cost standpoint. Process control is only as good as the monitoring elements. Range and accuracy Table 8.7 gives the temperature ranges and accuracies of temperature sensors. The accuracies shown are with minimal calibration or error correction. The ranges in some cases can be extended with the use of new materials. Table 8.8 gives a summary of temperature sensor characteristics. Thermal time constant A temperature detector does not react immediately to a change in temperature. The reaction time of the sensor or thermal time constant is a measure of the time it takes for the sensor to stabilize internally to the external temperature change, and is determined by the thermal mass and thermal conduction resistance of the device. Thermometer bulb size, probe size, or protection well can affect theresponse time of the reading, i.e., a large bulb contains more liquid for better sensitivity, but this will also increase the time constant taking longer to fully respond to a temperature change. Installation Care must be taken in locating the sensing portion of the temperature sensor, it should be fully encompassed by the medium whose temperature is being measured, and not be in contact with the walls of the container. The sensor should be screened from reflected heat and radiant heat if necessary. The sensor should also be placed downstream from the fluids being mixed, to ensure that the temperature has stabilized, but as close as possible to the point of mixing, to give as fast as possible temperature measurement for good control. A low thermal time constant in the sensor is necessary for a quick response. Compensation and calibration may be necessary when using pressure-spring devices with long tubes especially when accurate readings are required. Calibration Temperature calibration can be performed on most temperature sensing devices by immersing them in known temperature standards which are the equilibrium points of solid/liquid or liquid/gas mixtures, which is also known as the triple point. Some of these are given in Table 8.9. Most temperature sensing devices are rugged and reliable, but can go out of calibration due to leakage during use or contamination during manufacture and should therefore be checked on a regular basis. Protection In some applications, temperature sensing devices are placed in wells or enclosures to prevent mechanical damage or for ease of replacement. This kind of protection can greatly increase the system response time, which in some circumstances may be unacceptable. Sensors may need also to be protected from over temperature, so that a second more rugged device may be needed to protect the main sensing device. Semiconductor devices may have built in over temperature protection. A fail-safe mechanism may also be incorporated for system shutdown, when processing volatile or corrosive materials.