Composite Material Preparation - Level 2 PDF
Document Details
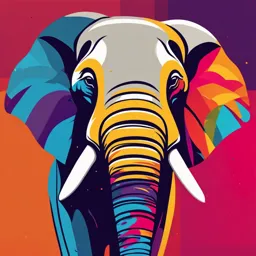
Uploaded by PanoramicSerpentine4424
Kolej Kemahiran Tinggi MARA Masjid Tanah
Tags
Summary
This document provides preparation requirements for composite materials. It covers storage, materials requisition procedures, and tool/equipment information. It also includes details on the different types of equipment used in composite material preparation.
Full Transcript
LEVEL 2 COMPOSITE MATERIAL PREPARATION 02- PREPARE COMPOSITE MATERIALS PREPARATION WORKS REQUIREMENTS Learning Objective 1. Storage area and condition 2. Materials stocks and condition (expiry date/shelf life) 3. Materials requisition procedure 4. Materials requisit...
LEVEL 2 COMPOSITE MATERIAL PREPARATION 02- PREPARE COMPOSITE MATERIALS PREPARATION WORKS REQUIREMENTS Learning Objective 1. Storage area and condition 2. Materials stocks and condition (expiry date/shelf life) 3. Materials requisition procedure 4. Materials requisition form information 5. Tools/equipment/machine 6. Tool/equipment operation checking method and condition 7. Liquid materials weighing method 1. STORAGE AREA AND CONDITION ▪Use kit stopper to endure stacked kits from falling or slide down. Stack kits while not exceeding height limit. ▪Do not let kit in vertical condition. Do not stack kits exceeding height limit. ▪Impact to material if not follow the procedures. Storage of Kits Material ▪ All kitted material that is not for immediate use in the lay up operation shall be placed into a bag with at least one desiccant. The bag shall be heat-sealed. ▪ Kitting personnel must ensure all kitted material must be properly stored and used proper regulator or table (not folded or hanging). ▪ Where kits are to be used at a later date, with consideration of the out time remaining, the kits shall be kept in the freezer until required for use. ▪ Kitting personnel must record and monitor the accumulated in/out time into the freezer to keep track time for out life in the WOP/Kit Stock In Freezer form. ▪ For paperwork that ends at Kitting, Kitting personnel shall transfer material information into Material Data form. This form must be attached together with the kit prior sending to Layup. Storage of Remaining Material ▪ Upon cutting the required amount of material, the remaining of the roll material shall be placed back into the bag with a desiccant, seal the bag (with heat seal or taping the folded end of the bag) and return to freezer. ▪ Kitting personnel shall check for any hole or puncture of the bag and ensure the material is stored and supported at both ends in the freezer. ▪ Kitting personnel must record the accumulated out time and time in into the freezer to keep track time for out life on Material Log and Material Log. ▪ Quality personnel shall verify the bag condition and ensure it is tagged with Material Log and Serviceable tag. The Material Log shall be stamped for bagging condition acceptance prior to roll material being put back into the freezer. ▪ For any balanced material in the Kitting room, shall be stored and supported at both ends on rack. ▪ Remaining roll or return kit material from Lay up personnel shall do the same exercise and all the material is under their responsibility. ▪ Action to be taken for any non compliant of environmental condition if any non compliant occurred due to humidity and temperature exceeded the specification, in Contaminated Controlled Area(CCA) and Freezer personnel must take immediate action as per below details: CERTIFICATION TOLERANCES CHARACTERISTICS DANGEROUS GOODS STORE REFRIGERATOR The minimum and maximum test thermocouple (STD) temperature 5°C Below 10°C Below reading at material and temperature controller setting Recorder (Instrumentation) ± 1.1°C N/A Recorder + Thermocouple sensor ± 2.0°C N/A with STD (combine Accuracy). 24 Hours test, temperature 24 Hours test, temperature Capability of maintaining shall within ranges shall within ranges Elapsed Time for Measurement ± 4 % of 24 Hours N/A REFRIGERATOR & DANGEROUS GOODS STORE 2. MATERIALS STOCKS AND CONDITION ▪Upon cutting the required amount of material, the remaining of the roll material shall be placed back into the bag. The production personnel shall seal the bag ends using the heat sealing roller. ▪The Production personnel shall check for any hole or puncture of the bag. If any opening if observed, the personnel shall seal it with the sealer. ▪Quality personnel shall verify the bag condition and stamp the MIT(Material Identification Tag) log for bagging condition acceptance prior to roll material being put back into the freezer. 3. MATERIALS REQUISITION PROCEDURE ▪ Definition: A material requisition form lists the items to be picked from inventory and used in the production process or in the provision of a service to a customer, usually for a specific job. The form usually has three purposes: i. To pick items from stock ii. To relieve the inventory records in the amount of the items picked iii. To charge the targeted job for the cost of the items requisitioned ▪ The form can also be used as the basis for the reordering of any inventory items that are not currently in stock. ▪ The information most commonly found on a material requisition form procedures includes: i. Header section: Job number to be charged ii. Header section: Date of requisition iii. Header section: Date by which inventory is required iv. Main body: Item number or description to be pulled from stock v. Main body: Unit quantity to be pulled from stock vi. Footer section: Authorization signature line ▪ If the materials are to be delivered to a specific location, there may also be space in the header in which to identify the delivery location. ▪ Unless a service invoice is to be prepared from this document, it usually does not include item costs or prices. ▪ The requesting person retains a copy of the material requisition form, as does the warehouse staff. Another copy accompanies the picked goods to their eventual destination. If items listed on the form are not in stock, another copy may be sent to the purchasing department for ordering purposes. ▪ Auditors may trace the flow of material requisition forms through a company, to see if inventory items are being appropriately used and recorded as mandated by company materials handling procedures. If not, the auditors may conclude that they cannot rely upon certain aspects of a company's control systems as part of their audit activities, and so will bolster other audit activities. ▪ The material requisition form is not used in a computerized production planning environment, where this picking information is instead sent to the warehouse as an electronic message. 4. MATERIALS REQUISITION FORM INFORMATION Material descriptions Quantity Job order details SAMPLE OF MRN 5. TOOLS/EQUIPMENT/MACHINE Cutting tools/machine templates/tracing paper, Measuring instruments Weighing scales Lay material on bed (S91 and DCS) Lay roll material on bed, using non silicon glove in handling material to prevent contamination. During lay material operator need to check material must 0° orientation. 0° Orientation Press the Servo Power button, the Operator Control Console will go functional and the screen will display press Enter or Return to engage motors Press Enter and the screen will display ‘S91’ and this servo will lock up. Lay the materials on the work surface and cover the material with plastic. Make sure the materials are inline with table’s white line. Press INIT button on the OCC to initialized the machine Press VAC ON/OFF button to turn on the vacuum Use the arrow button to moved the cutter to origin Check straight edge with origin light. If material are straight, type MO (manual origin) and press ENTER to return to origin Search file to be cut. “A: ” and press ENTER. Make sure the diskette already inserted before searching the cut file Knife ON/OFF button Tool button DRY RUN button Turn the knife on, switch tool to Auto. If dry run is required, turn on DRY RUN and press START. If dry run is not required, just press START. Allow the machine to complete the cutting process. After the cutting completed, the machine will display ‘Processing is complete”. Turn off the vacuum, switch the knife up and switch the servo power off. Measuring Equipment /Instrument Thermohygrograph A Thermo-Hygrograph is a chart recorder that measures and records both temperature and humidity (or dew point). Similar devices that record only one parameter are a thermograph for temperature and hygrograph for humidity. Uses a bi-metallic strip for temperature and one human hair bundle for humidity. Includes one red and blue felt–tipped pen to record the reading. A thermograph is usually configured with a pen that records temperature on a revolving cylinder. The pen is at the end of a lever that is controlled by a bi-metal strip of temperature- sensitive metal which bends as the temperature changes. Digital Weighing scale A digital scale is a measurement device used to measure the weight or mass of an object or substances. Digital scales are often more compact, durable, and precise than other kinds of scales, such as spring scales or balances, which often wear out and give different readings over time. Digital scales require a power source and may not always be completely accurate, but they are generally quite accurate and consistent even when used over extended periods of time. A digital scale may be used for many different purposes. THAWING PROCESS OF MATERIALS Obtain materials from storage area. Raise Material Request Note (MRN) base on cutting schedule and submit to warehouse for withdrawing of material. Make a visual inspection on boxes of material received for any damage or opening and ensure the material inside the box is supported at both ends. Ensure the materials received are accompanied with Serviceable Tag, Material Log & Material Identification Tag (MIT). Send materials to work area Ensure all information stated in Serviceable Tag, Material Log and Material Identification Tag (MIT) is correct Boxes to be arranged by kitting personnel using pallet at a specific column allocate (standard high of column for each box) as picture shown. Box without racking system can be stack maximum with two boxes with pallet in between the box. Arrange boxes on the racking and attach boxes with Material Identification Tag (MIT), Material Tracking Form (MTF), Material Log and Serviceable Tag complete with item name, part number, date issued and GRR number. OK NOT OK Thaw frozen material prior sending to work area. After removing from cold storage to thawing room, the material must remain sealed until it reaches ambient temperature. (Temp21°± 5 and Humidity 70%). The material is ready for production use when no condensation forms on the outside of the bag when wiped. 6. TOOL/EQUIPMENT OPERATION CHECKING METHOD AND CONDITION Preventative maintenance for S91/C-100 GERBERcutter® machine and AccuPlot™ 300 covers daily, weekly and annually depending on the detail components. Please refer to Table 1 for S91/C-100 GERBERcutter machine (for annual quarterly) for maintenance requirements. Procedures Page Reference Page Major Assembly Assembly Component Action Frequency (Reference 4) (Reference 4) Knife Drive Train Inspect Daily 5-13 5-2 Knife Drive Train Inspect Daily 5-14 5-2 Knife Check Bristle Annually 5-22 5-2, 5-3 Penetration Cover N/A Clean Daily 5-12 5-1 Cutter Head Inspect Weekly 5-21 Air-Cylinder Rod N/A Clean Weekly 5-21 5-2 Lubricate Weekly 5-21 Inspect Weekly 5-22 Round way N/A Clean Weekly 5-20 5-2, 5-3 Lubricate Weekly 5-20 Knife Drive Inspect Weekly 5-22 5-2, 5-3 Table Filter N/A Clean Daily 5-27 5-1 Cutting Table Inspect Daily 5-25 Work Surface Bristle Squares 5-1 Clean Daily 5-24 Inspect Weekly 5-11 Flatway N/A Clean Weekly 5-11 5-1, 5-2 Lubricate Weekly 5-11 Beam Inspect Weekly 5-10 Round way Clean Weekly 5-10 5-1,5-2 Lubricate Weekly 5-10 Arrange Tools/Equipment Machines Poor arrangement can be a cause of accidents, such as: tripping over loose objects on floors, stairs and platforms being hit by falling objects slipping on greasy, wet or dirty surfaces striking against projecting, poorly stacked items or misplaced material cutting, puncturing, or tearing the skin of hands or other parts of the body on projecting nails, wire or steel strapping To avoid these hazards, a workplace must "maintain" order throughout a workday. Although this effort requires a great deal of management and planning, the benefits are many. 7. LIQUID MATERIALS WEIGHING METHOD Estimating material weight Resin usage will vary depending on the type of reinforcement being used. The heavier the fabric, the more resin it will take to wet it out. A good hand laminate consists of about 50% fabric and 50% resin by weight. For example, if an application requires 3 square yards of a 4 ounce-per-square-yard fabric (total fabric weight is 12 ounces), 12 ounces of resin will be needed. However, if 3 yards of 10 ounce-per-square-yard fabric is chosen (total fabric weight is 30 ounces), 30 ounces of resin will be needed. Glass mat requires a minimum of 2 ounces of resin for each ounce of mat. Therefore, it the application calls for 20 square feet of 1.5 ounce-per-square- foot mat, it will require a minimum of 60 ounces of resin. Remember that mat is specified in ounces per square foot, where fabrics are specified in ounces per square yard. Chopped mat at 1.5 ounces-per-square-foot actually weighs 13.5 ounces-per-square-yard! Since there are so many possible combinations of materials, one should calculate the weight and cost of a single layer using a variety of reinforcements. These can then be added or subtracted form the theoretical laminate until the design properties are achieved.